How Section Thickness Dictates Mechanical Strength in Squeeze Cast AM60
This technical brief is based on the academic paper "Section thickness-dependent tensile properties of squeeze cast magnesium alloy AM60" by Xuezhi Zhang, Meng Wang, Zhizhong Sun, and Henry Hu, published in CHINA FOUNDRY (2012). It is summarized and analyzed for HPDC professionals by the experts at STI C&D.
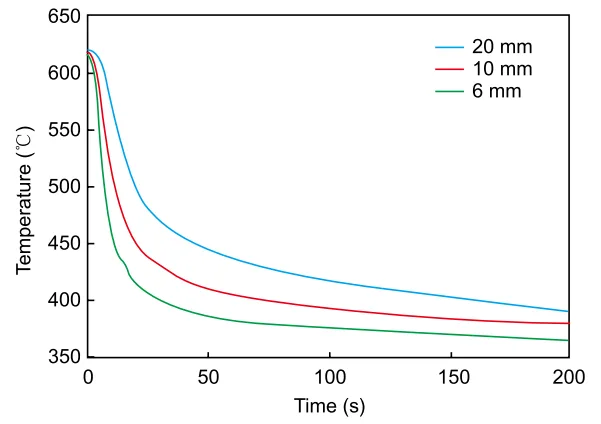
Keywords
- Primary Keyword: Squeeze Cast Magnesium Alloy AM60
- Secondary Keywords: Section thickness effect, Tensile properties, Solidification simulation, Microstructure analysis, Porosity in magnesium casting, Cooling rate
Executive Summary
- The Challenge: The automotive industry's demand for lightweight, complex magnesium components often involves parts with varying wall thicknesses. Traditional high-pressure die casting (HPDC) struggles to produce thick sections without defects like porosity, compromising mechanical integrity.
- The Method: Researchers used squeeze casting (SQC) at 30 MPa to produce magnesium alloy AM60 samples with different section thicknesses (6, 10, and 20 mm). They then conducted tensile testing, porosity analysis, and microstructural examinations, supported by Magmasoft® solidification simulations.
- The Key Breakthrough: The study established a direct and critical inverse relationship: as the section thickness of the squeeze cast AM60 increases, the mechanical properties—including yield strength (YS), ultimate tensile strength (UTS), and elongation—significantly decrease.
- The Bottom Line: For squeeze cast AM60, section thickness is a dominant process variable. Thinner sections achieve superior mechanical performance due to faster cooling rates, which result in a finer grain structure and significantly lower porosity.
The Challenge: Why This Research Matters for HPDC Professionals
The push for greater fuel economy has made magnesium alloys a top choice for automotive lightweighting, with applications expanding from instrument panel beams to steering components. While high-pressure die casting (HPDC) is a cost-effective process for thin-walled parts, it often falls short when producing components with thicker cross-sections. These thicker sections are prone to porosity caused by gas entrapment and solidification shrinkage, which severely degrades mechanical properties like strength and ductility (Ref. [3, 4]).
Squeeze casting (SQC) emerges as a powerful alternative, designed specifically to produce high-integrity, thick-walled parts by applying high pressure during solidification. However, to confidently design and manufacture safety-critical components, engineers must understand precisely how changing the wall thickness affects the final material properties. This study directly addresses that knowledge gap for the widely used AM60 magnesium alloy.
The Approach: Unpacking the Methodology
To isolate the effect of section thickness, the research team employed a straightforward and effective methodology:
- Casting: A step mold made of tool steel was used to fabricate squeeze cast AM60 specimens with three distinct thicknesses: 6 mm, 10 mm, and 20 mm. A constant pressure of 30 MPa was applied during solidification.
- Mechanical Testing: Subsize rectangular tensile specimens were prepared from each thickness step according to ASTM Standard B557M. These were tested at room temperature to determine ultimate tensile strength (UTS), 0.2% yield strength (YS), and elongation to failure (A).
- Porosity and Microstructure Analysis: Porosity was quantified using the Archimedes principle for density measurement. The grain structure and fracture surfaces were examined using optical microscopy and Scanning Electron Microscopy (SEM).
- Numerical Simulation: Magmasoft® simulation software was used to compute the cooling curves and solidification rates for each section thickness, providing a theoretical basis to explain the experimental results.
The Breakthrough: Key Findings & Data
The study revealed a clear and consistent trend: thinner is stronger. The mechanical performance of squeeze cast AM60 is fundamentally tied to its solidification behavior, which is dictated by section thickness.
- Finding 1: Cooling Rate Dictates Grain Size: The simulation results showed a dramatic difference in cooling rates. The 6 mm section cooled at 11.9 °C·s⁻¹, nearly four times faster than the 20 mm section at 2.8 °C·s⁻¹ (Figure 2). This rapid solidification in the thin section prevented extensive grain growth, resulting in a fine average grain size of 16 µm, compared to a coarse 80 µm in the 20 mm section (Figure 4).
- Finding 2: Slower Cooling Increases Porosity: The longer solidification time in thicker sections allowed for the formation of shrinkage porosity. The porosity level increased from a minimal 0.2% in the 6 mm section to 1.3% in the 20 mm section (Figure 6). The optical micrographs in Figure 5 visually confirm the near-absence of pores in the thin sample versus visible porosity in the thick sample.
- Finding 3: Mechanical Properties Degrade with Thickness: The combined effects of coarser grains and higher porosity led to a sharp decline in mechanical properties. As thickness increased from 6 mm to 20 mm (Table 2, Figure 8):
- Ultimate Tensile Strength (UTS) dropped by 40%, from 229.89 MPa to 137.68 MPa.
- Yield Strength (YS) decreased by 30%, from 96 MPa to 67 MPa.
- Elongation (ductility) plummeted by 60%, from 10.19% to just 3.69%.
- Finding 4: Fracture Behavior Shifts from Ductile to Brittle: SEM analysis of the fracture surfaces provided a clear visual of this performance drop. The 6 mm sample showed a ductile fracture with deep dimples, indicating significant energy absorption before failure. In contrast, the 20 mm sample exhibited a brittle fracture characterized by flat, cleavage-like facets, confirming its low ductility (Figure 9).
Practical Implications for Your HPDC Operations
The findings from this paper offer direct, actionable insights for engineers and designers working with magnesium castings.
- For Process Engineers: The direct link between cooling rate and mechanical properties is critical. The data suggests that for thicker sections, process optimization should focus on maximizing heat extraction from the die to promote faster solidification and refine the grain structure.
- For Quality Control: The study confirms that porosity is a primary driver of poor ductility. As shown in Figure 6, density measurement is a reliable non-destructive method to predict the mechanical integrity of a part. A lower-than-expected density in a thick section is a strong indicator of compromised performance.
- For Part and Die Design: Designers must account for the significant "knock-down" factor on mechanical properties in thicker sections. A component designed with a 20 mm wall will have substantially lower strength and ductility than a 6 mm wall of the same AM60 alloy. This research provides the data ( Table 2) to make more informed design trade-offs between geometry and material performance. Furthermore, the solidification simulations (Figure 3) can guide the placement of gates and risers to ensure thick sections are fed properly, minimizing shrinkage porosity.
Paper Details
Section thickness-dependent tensile properties of squeeze cast magnesium alloy AM60
1. Overview:
- Title: Section thickness-dependent tensile properties of squeeze cast magnesium alloy AM60
- Author: Xuezhi Zhang, Meng Wang, Zhizhong Sun, and Henry Hu
- Year of publication: 2012
- Journal/academic society of publication: CHINA FOUNDRY
- Keywords: squeeze casting; magnesium alloy AM60; tensile properties; section thickness
2. Abstract:
The development of alternative casting processes is essential for the high demand of light weight magnesium components to be used in the automotive industry, which often contain different section thicknesses. Squeeze casting with its inherent advantages has been approved for the capability of minimizing the gas porosity in magnesium alloys. For advanced engineering design of light magnesium automotive applications, it is critical to understand the effect of section thickness on mechanical properties of squeeze cast magnesium alloys. In this study, magnesium alloy AM60 with different section thicknesses of 6, 10 and 20 mm squeeze cast under an applied pressure of 30 MPa was investigated. The prepared squeeze cast AM60 specimens were tensile tested at room temperature. The results indicate that the mechanical properties including yield strength (YS), ultimate tensile strength (UTS) and elongation (A) decrease with an increase in section thickness of squeeze cast AM60. The microstructure analysis shows that the improvement in the tensile behavior of squeeze cast AM60 is primarily attributed to the low-gas porosity level and fine grain structure which result from the variation of cooling rate of different section thickness. The numerical simulation (Magmasoft®) was employed to determine the solidification rates of each step, and the simulated results show that the solidification rate of the alloy decreases with an increase in the section thickness. The computed solidification rates support the experimental observation on grain structural development.
3. Introduction:
The use of magnesium in the automotive industry has grown dramatically since the 1990s due to demands for lightweighting and fuel economy. Magnesium is significantly lighter than steel, zinc, and aluminum. However, the dominant manufacturing process, high-pressure die casting (HPDC), is best suited for thin-walled parts. Potential automotive applications often require components with complex shapes and varying wall thicknesses. In thick sections, HPDC parts suffer from porosity, which negatively impacts mechanical properties. Squeeze casting (SQC) is an alternative process designed to produce higher integrity parts by solidifying molten metal under high pressure, making it suitable for thicker-walled components.
4. Summary of the study:
Background of the research topic:
Magnesium alloys are increasingly used in the automotive sector for weight reduction. However, manufacturing processes must be able to produce complex parts with varied thicknesses without compromising mechanical integrity.
Status of previous research:
HPDC is well-established but struggles with porosity in thick sections. Squeeze casting has been shown to be effective for producing high-integrity aluminum components and is a promising technology for magnesium, but more research is needed to understand the process-property relationships. Previous work has shown that porosity strongly influences mechanical properties in magnesium alloys (Ref. [3, 4]).
Purpose of the study:
This study aimed to critically understand the effect of section thickness (6, 10, and 20 mm) on the mechanical properties and microstructure of squeeze cast magnesium alloy AM60.
Core study:
The study involved casting AM60 alloy into a step-mold using the squeeze casting process. The resulting samples of different thicknesses were subjected to tensile testing to measure YS, UTS, and elongation. Porosity was measured via the density method. Microstructure and fracture surfaces were analyzed using optical and scanning electron microscopy. Numerical simulation (Magmasoft®) was used to determine the solidification rates and correlate them with the observed microstructures and properties.
5. Research Methodology
Research Design:
An experimental approach was taken to compare the properties of AM60 magnesium alloy cast into three different section thicknesses (6, 10, and 20 mm) under a constant squeeze pressure of 30 MPa.
Data Collection and Analysis Methods:
- Casting: A step mold made of tool steel was used.
- Tensile Testing: An Instron 8562 universal testing machine was used to test subsize specimens prepared according to ASTM Standard B557M.
- Density/Porosity Measurement: The Archimedes principle (ASTM Standard D3800) was used to determine the actual density, and porosity was calculated relative to the theoretical density of AM60 (1.77 g·cm⁻³).
- Simulation: Magmasoft® was employed to simulate the cooling curves and solidification sequence for each section.
- Microscopy: Optical microscopy was used to examine grain size, and SEM was used for fractography.
Research Topics and Scope:
The research focused exclusively on magnesium alloy AM60 produced by squeeze casting. The primary variable was section thickness (6, 10, and 20 mm). The study investigated the resulting tensile properties, porosity, grain structure, and fracture behavior.
6. Key Results:
Key Results:
The study found a direct and significant correlation between section thickness, cooling rate, microstructure, and mechanical properties. As section thickness increased from 6 mm to 20 mm, the cooling rate decreased from 11.9 °C·s⁻¹ to 2.8 °C·s⁻¹. This slower cooling led to a coarser grain structure (16 µm vs. 80 µm) and higher porosity (0.2% vs. 1.3%). Consequently, all measured mechanical properties deteriorated significantly: UTS decreased by 40%, YS by 30%, and elongation by 60%. The fracture mode transitioned from ductile in the thin section to brittle in the thick section.
Figure Name List:
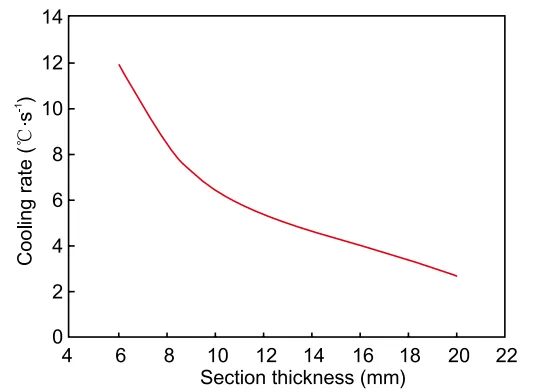
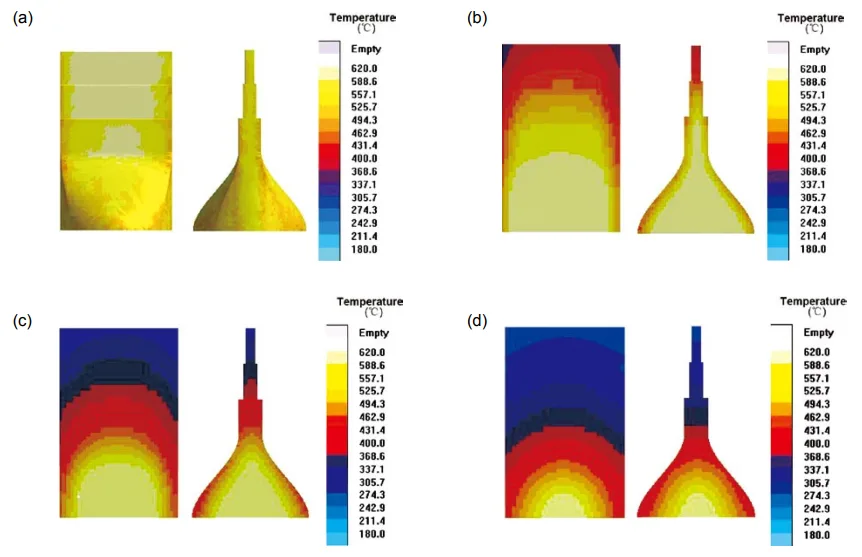
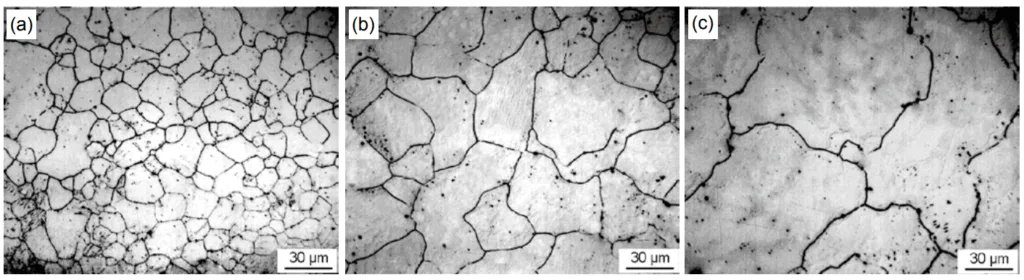
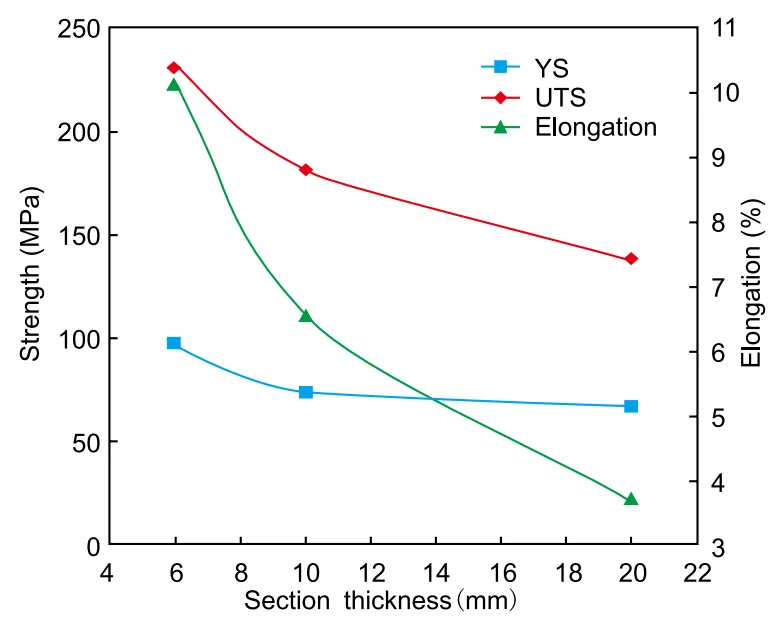
- Fig. 1: Cooling curves of samples with 6, 10 and 20 mm thick sections
- Fig. 2: Cooling rate vs. section thicknesses
- Fig. 3: Simulation on solidification behaviour of AM60 step casting: (a) 20%, (b) 40%, (c) 60%, and (d) 80% solidified
- Fig. 4: Optical micrograph showing grain size of specimens with 6 mm (a), 10 mm (b) and 20 mm (c) section thickness
- Fig. 5: Optical micrographs of squeeze cast AM60 with section thickness of 6 mm (a) and 20 mm (b)
- Fig. 6: Porosity level and density vs. section thickness
- Fig. 7: Engineering stress-strain curve of squeeze cast AM60 alloy
- Fig. 8: Ultimate tensile strength (UTS), yield strength (YS) and elongation vs. section thickness
- Fig. 9: SEM fractographs of 6 mm (a), 10 mm (b), 20 mm (c) thick squeeze cast AM60 samples
7. Conclusion:
The study successfully demonstrated that section thickness has a significant influence on the tensile properties of squeeze cast AM60 alloy. A decrease in section thickness from 20 mm to 6 mm resulted in remarkable increases in elongation (176%), UTS (67%), and YS (43%). This improvement is attributed to the faster solidification rate in thinner sections, which leads to a finer grain structure and a lower level of porosity. The fracture behavior also changes, transitioning from brittle in thick sections to ductile in thin sections. The numerical simulation results supported the experimental findings by confirming that the solidification rate decreases as section thickness increases.
8. References:
- [1] Cole G S. Summary of Magnesium Vision 2020: A North American Strategic Vision for Magnesium. Editor(s) - Randy S. Beals, TMS, 2007 TMS Annual Meeting & Exhibition, Magnesium Technology 2007, 2007: 35-40.
- [2] Herry Hu, Alfred Yu, Naiyi Li and John E Allison. Potential Magnesium Alloys for High Temperature Die Cast Automotive Applications: A Review. Material and Manufacturing Process, 2003, 18(5): 687-717.
- [3] Harvard T, Gjestland Stian Sannes, Hakon Westengen, and Darryl Albright. Effect of Casting Temperature, Section Thickness and Die Filling Sequence on Microstructure and Mechanical Properties of High Pressure Die Castings. NADCA Transactions, 2003: T03-036.
- [4] Ming Zhou, Naiyi Li and Henry Hu. Effect of Section Thicknesses on Tensile Behavior and Microstructure of High Pressure Die Cast Magnesium Alloy AM50. Materials Science Forum, 2005, 475-479: 463-468.
- [5] Kaufmann H and Uggowitzer P J. Metallurgy and Processing of High-Integrity Light Metal Pressure Castings. Schiele & Schon, Berlin, Germany, 2007.
- [6] Yong M S, Clegg A J. Process optimization for a squeeze cast magnesium alloy. J. Mater. Process Technology, 2004, 145: 134-141.
- [7] Zhou M, Hu H, Li N and Lo J. Microstructure and Tensile Properties of Squeeze Cast Magnesium Alloy AM50. Journal of Materials Engineering & Performance, 2005, 14(4): 539-545.
- [8] Yu Alfred, Wang Shuping, Li Naiyi, Hu Henry. Pressurized Solidification of Magnesium Alloy AM50A. Journal of Materials Processing Technology, 2007, 191: 247-250.
- [9] Zhizhong Sun, Henry Hu, Xiaoping Niu. Determination of heat transfer coefficients by extrapolation and numerical inverse methods in squeeze casting of magnesium alloy AM60. Journal of Materials Processing Technology, 2011, 211: 1432-1440.
- [10] Alfred Yu, Shuping Wang, Naiyi Li, and Henry Hu. Mathematical Modeling and Experimental Investigation of Shrinkage Porosity in Squeeze Casting of Magnesium Alloy AM50A. Editor(s) - Randy S. Beals, TMS, 2007 TMS Annual Meeting & Exhibition. Magnesium Technology 2007, 2007: 103-108.
Conclusion & Next Steps
This research provides a valuable roadmap for enhancing component performance in squeeze casting. The findings offer a clear, data-driven path toward improving quality, reducing defects, and optimizing the design of magnesium components with varied cross-sections.
STI C&D is committed to applying cutting-edge industry research to solve our customers’ most challenging technical problems. If the problem discussed in this white paper aligns with your research goals, please contact our engineering team to discuss how we can help you apply these advanced principles to your research.
Expert Q&A:
- Q1: What is the primary effect of increasing section thickness on squeeze cast AM60?
A1: Increasing the section thickness leads to a significant decrease in all key mechanical properties, including yield strength (YS), ultimate tensile strength (UTS), and elongation (ductility). As detailed in the paper "Section thickness-dependent tensile properties of squeeze cast magnesium alloy AM60," this is a direct result of slower solidification. - Q2: Why do thicker sections have worse mechanical properties?
A2: According to the study, thicker sections have a lower cooling rate. This slower cooling allows for the formation of a coarser grain structure and a higher percentage of shrinkage porosity. The combination of larger grains and more defects weakens the material, as supported by the data in Figure 4 (grain size) and Figure 6 (porosity). - Q3: How significant is the drop in performance between a 6 mm and a 20 mm section?
A3: The drop is very significant. The paper reports that the 6 mm section has a 67% higher ultimate tensile strength and a 176% higher elongation compared to the 20 mm section. This data, found in Table 2 and Figure 8, highlights the critical impact of thickness on performance. - Q4: What does the fracture analysis reveal about the material's behavior?
A4: The SEM fractography in Figure 9 shows that the material's failure mode changes with thickness. The thin 6 mm sample fails in a ductile manner, characterized by deep dimples, which is desirable. The thick 20 mm sample fails in a brittle manner, showing flat cleavage facets, indicating low toughness and ductility. - Q5: Can simulation be used to predict these effects?
A5: Yes. The study successfully used Magmasoft® simulation to predict the cooling rates for each section thickness (Figure 1 and Figure 2). These simulated rates provided the theoretical explanation for the experimentally observed differences in microstructure and mechanical properties, demonstrating that simulation is a valuable tool for predicting the outcome of the casting process.
Copyright
Copyright © 2025 STI C&D. All rights reserved.
This material is an analysis of the paper "Section thickness-dependent tensile properties of squeeze cast magnesium alloy AM60" by Xuezhi Zhang, Meng Wang, Zhizhong Sun, and Henry Hu.
Source of the paper: https://core.ac.uk/display/37731215
This material is for informational purposes only. Unauthorized commercial use is prohibited.