A Blueprint for High-Integrity HPDC: Tackling Porosity in Structural Aluminum & Magnesium Castings
This technical brief is based on the academic paper "Process and Tool Design for the High Integrity Die Casting of Aluminum and Magnesium Alloys" by Varun Nandakumar, presented as a Master's Thesis at The Ohio State University (2014). It is summarized and analyzed for HPDC professionals by the experts at CASTMAN.

Keywords
- Primary Keyword: High Integrity Die Casting
- Secondary Keywords: HPDC porosity, vacuum die casting, aluminum magnesium alloys, chill block design, melt quality, rotary degassing, structural die casting
Executive Summary
- The Challenge: Porosity from entrapped gas and solidification shrinkage is the single biggest defect in High-Pressure Die Casting (HPDC), preventing the use of lightweight alloys in demanding, structural load-bearing components.
- The Method: The research implemented a two-pronged strategy to improve a conventional HPDC cell: 1) Enhancing melt quality through systematic rotary degassing to remove hydrogen, and 2) Designing and validating a complete vacuum-assist die system with custom chill blocks to evacuate air from the cavity.
- The Key Breakthrough: A comprehensive, data-driven process for designing and optimizing a vacuum-capable die was successfully demonstrated. Using simulation and a Designed Experiment (DOE), the study identified that chill block material (copper) and vent gap size were the most critical factors for performance, leading to an optimized, manufacturable design.
- The Bottom Line: By systematically addressing both melt purity and in-cavity gas entrapment, it is possible to upgrade a traditional HPDC process to produce higher-integrity parts suitable for structural applications.
The Challenge: Why This Research Matters for HPDC Professionals
The automotive industry's push for higher efficiency and lower emissions has created a massive demand for lightweight aluminum and magnesium alloys to replace steel in structural components. However, conventional HPDC has historically been sidelined for these critical, load-bearing applications. The reason is simple and one every die caster knows well: porosity.
As a recent NADCA survey cited in the paper confirms, porosity is the single largest contributor to defects in die-cast products (Figure 11). This porosity comes from two main sources:
1. Gas Porosity: Hydrogen dissolved in the molten metal and air entrapped in the shot sleeve and die cavity during the violent injection process.
2. Solidification Shrinkage: Voids left behind as the metal contracts during cooling without sufficient liquid metal to feed them.
These defects compromise mechanical properties, particularly elongation, and prevent parts from being heat-treated, making them unsuitable for crash-worthy or structural use. This research tackles this fundamental challenge head-on, providing a practical framework for upgrading a standard HPDC cell to produce high-integrity castings.
The Approach: Unpacking the Methodology
To combat porosity, the researcher adopted a holistic approach, addressing the problem at its sources. The study was conducted at The Ohio State University's die casting lab using a 250-ton Buhler cold chamber machine.
Improving Melt Quality: The first step was to ensure the molten aluminum was as clean as possible before it even entered the shot sleeve.
- A PYROTEK® STAR 300® Rotary Degasser (Figure 29) was used to bubble inert Argon gas through the melt, removing dissolved hydrogen.
- A Reduced Pressure Tester (Figure 31) and Archimedes density measurements were used to quantify the effectiveness of the degassing process, establishing optimal operating parameters.
Designing a Vacuum-Capable Die: The second, more intensive step was to prevent air from being trapped in the die cavity during injection.
- The study focused on a vacuum-assist system with valve-less chill blocks, a cost-effective and robust solution.
- MAGMA simulation was used to determine the temperature and velocity of the metal at the cavity exit, providing critical boundary conditions for the design.
- An ANSYS simulation model was built to run a 2³ Designed Experiment (DOE) to optimize the chill block design. The experiment tested the effects of three key factors: Material (H13 vs. Copper), Gap Thickness (0.02" vs. 0.04"), and Heat Transfer Coefficient (HTC).
- The final, optimized design was created in 3D CAD software and manufactured.
The Breakthrough: Key Findings & Data
The study yielded clear, actionable results on both fronts of the investigation.
Finding 1: Rotary Degassing is Highly Effective and Quantifiable. The experimental trials on A380 and a similar proprietary alloy demonstrated a significant increase in melt density after degassing. The data showed that degassing for 10-15 minutes was ideal, consistently producing a melt quality sufficient for heat treatment without blistering (Figure 33, Figure 34).
Finding 2: Chill Block Material and Gap are Critical Design Factors. The Analysis of Variance (ANOVA) on the simulation results was unequivocal (Table 6).
- Material: Copper, with its superior thermal conductivity, was significantly better at freezing the metal front than H13 tool steel.
- Gap: A smaller vent gap resulted in a much faster freezing time.
- Interaction: A significant interaction was found between the material and the gap size.
Finding 3: Heat Transfer Coefficient (HTC) was Not a Significant Factor. Perhaps the most non-obvious finding from the DOE was that, for this specific geometry and range of values, the HTC had little statistical influence on the freezing time. This suggests that for initial design purposes, focusing on material and geometry provides the most leverage.
Finding 4: A Complete, Validated Design Process was Established. The research successfully integrated dimensional study, flow simulation, thermal simulation (DOE), and CAD design into a single, cohesive workflow (Figure 44). This process resulted in a final, optimized chill block design: trapezoidal profile, made of copper, with a 0.030-inch vent gap.
Practical Implications for HPDC Products
This thesis moves beyond academic theory to provide a tangible blueprint for improving real-world manufacturing operations.
For Process Engineers: The findings on rotary degassing (Appendix B & C) provide a clear methodology for establishing and verifying melt quality. Implementing a 10-15 minute degassing cycle with Argon and verifying with a Reduced Pressure Test can be a direct path to reducing hydrogen porosity and enabling the production of heat-treatable parts.
For Quality Control: The correlation shown between degassing time and melt density (Figure 32) provides a powerful in-process metric. Monitoring melt density can serve as a leading indicator of potential porosity issues, allowing for corrective action before scrap is produced.
For Die Design: This study provides a powerful, data-driven case for using copper chill blocks with optimized vent gaps in vacuum-assist systems. The detailed design process (Figure 44) can be adapted by die designers to create their own high-efficiency vacuum venting systems, reducing reliance on expensive, high-maintenance valve systems and potentially lowering tooling costs.
Paper Details
Process and Tool Design for the High Integrity Die Casting of Aluminum and Magnesium Alloys
1. Overview:
- Title: Process and Tool Design for the High Integrity Die Casting of Aluminum and Magnesium Alloys
- Author: Varun Nandakumar
- Year of publication: 2014
- Journal/academic society of publication: The Graduate School of The Ohio State University
- Keywords: High Integrity Die Casting, HPDC, Aluminum Alloys, Magnesium Alloys, Vacuum Die Casting, Process Design, Tool Design, Porosity
2. Abstract:
The push for higher efficiency and lower emissions on present day automobiles have created a greater need for light alloys such as Aluminum and Magnesium to replace the customary steel parts in an automobile. A lot of these replaced parts are in structural load bearing components on a vehicle. This usually meant that processes such as the traditional High Pressure Die Casting would not be able to claim a stake in it due to its innate air and Hydrogen entrapment issues. But, with an overall higher maintenance of quality in the traditional process, it is possible to create higher integrity parts that are usable in structural applications. This thesis describes and tests some methods to improve the traditional High Pressure Die Casting process to enable it to produce higher integrity casts for Aluminum and Magnesium alloys. Methods to achieve a higher quality melt are researched and a rotary degasser is used for two experimental trials of similar Aluminum alloys. Similarly, methods to integrate vacuum into the existing setup are studied and the tooling part of the vacuum assist system with chill blocks is fully designed. The design of the chill blocks is carried out from the ground up using MAGMA and ANSYS simulation tools which were available at the Integrated Systems Engineering Lab. A designed experiment is completed to understand the effects of changing parameters on the design. Finally, the optimum design is completed on 3D CAD software and then manufactured in house.
3. Introduction:
High-Pressure Die Casting (HPDC) is a highly efficient process for mass-producing complex metal parts. However, its application in structural components has been limited by inherent porosity issues. This research addresses the growing demand from the automotive sector for lightweight, high-integrity structural parts made from aluminum and magnesium. The study aims to integrate and validate modern processes—specifically advanced melt treatment and vacuum die casting—into a conventional HPDC setup to overcome these limitations and enable the production of defect-free, structural-grade castings.
4. Summary of the study:
Background of the research topic:
The core problem is porosity in HPDC, which stems from dissolved hydrogen in the melt and air entrapped during injection. This prevents the use of HPDC for safety-critical, structural parts that require high ductility and heat treatability.
Status of previous research:
Previous research has identified various solutions, including high-integrity processes like Squeeze Casting and Vacuum Die Casting. For vacuum systems, both valve-based and valve-less (chill block) systems exist, each with pros and cons regarding efficiency, cost, and maintenance. This study builds on this knowledge by implementing and optimizing a cost-effective chill block system.
Purpose of the study:
The overall objective was to upgrade an existing HPDC cell at The Ohio State University to be capable of producing high-integrity, defect-free die castings. This involved two primary goals:
1. Develop a system to reduce hydrogen porosity in the melt.
2. Design a vacuum-capable die to evacuate air from the cavity.
Core study:
The study is divided into two main experimental and design phases:
1. Melt Quality Improvement: Two casting campaigns were conducted with aluminum alloys (A380 and a proprietary alloy) to determine the optimal operating conditions for a rotary degasser. Melt quality was evaluated using a Reduced Pressure Test and density measurements.
2. Vacuum Die Design: A complete vacuum-assist system featuring chill blocks was designed for an existing die. The process involved:
* Benchmarking commercial systems.
* Using MAGMA to simulate cavity filling and establish boundary conditions.
* Conducting a 2³ Designed Experiment in ANSYS to optimize the chill block's material, gap, and HTC.
* Finalizing the design in 3D CAD and manufacturing the components.
5. Research Methodology
Research Design:
The research employed a combination of experimental investigation and computational simulation. An observational study was conducted to determine best practices for rotary degassing. For the chill block design, a 2³ full factorial designed experiment with center points was used to systematically evaluate the influence of key design parameters on performance (freezing time).
Data Collection and Analysis Methods:
- Melt Quality: Data was collected using a Palmer® Reduced Pressure Tester and an Archimedes density apparatus. Results were compared against standard charts and plotted over time.
- Chill Block Design: Data was generated via transient thermal simulations in ANSYS. The results (fill time and distance) were analyzed using Analysis of Variance (ANOVA) to determine the statistical significance of each factor and their interactions.
Research Topics and Scope:
The scope was focused on upgrading a specific 250T cold chamber HPDC cell for high-integrity casting of aluminum and magnesium alloys. The research covered melt degassing techniques and the complete design and validation workflow for a valve-less vacuum venting system (chill blocks).
6. Key Results:
Key Results:
- Optimal degassing time with a rotary degasser was found to be 10-15 minutes, which was sufficient to produce a melt quality that allowed for subsequent heat treatment without blistering.
- The ANOVA of the chill block design simulation revealed that Material (Copper > H13) and Gap (smaller is better) were highly significant factors affecting freezing time.
- The Heat Transfer Coefficient (HTC), within the tested range of 60-120 kW/m²K, was found to be statistically insignificant for this specific geometry.
- The final optimized design chosen was a copper chill block with a 0.030-inch gap, which balanced high performance with manufacturability.
- A complete design for the vacuum system, including vent passages and sealant grooves, was created and validated.
Figure Name List:
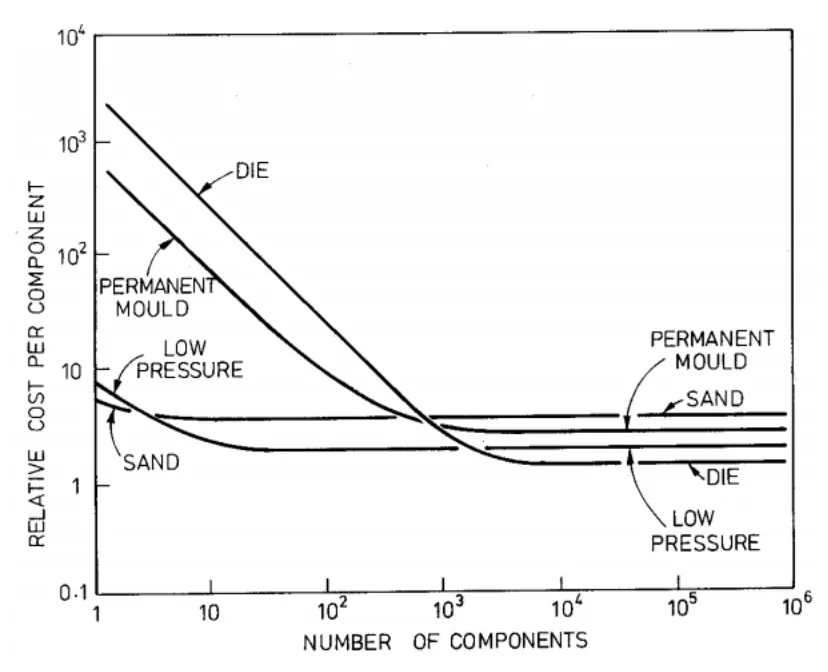
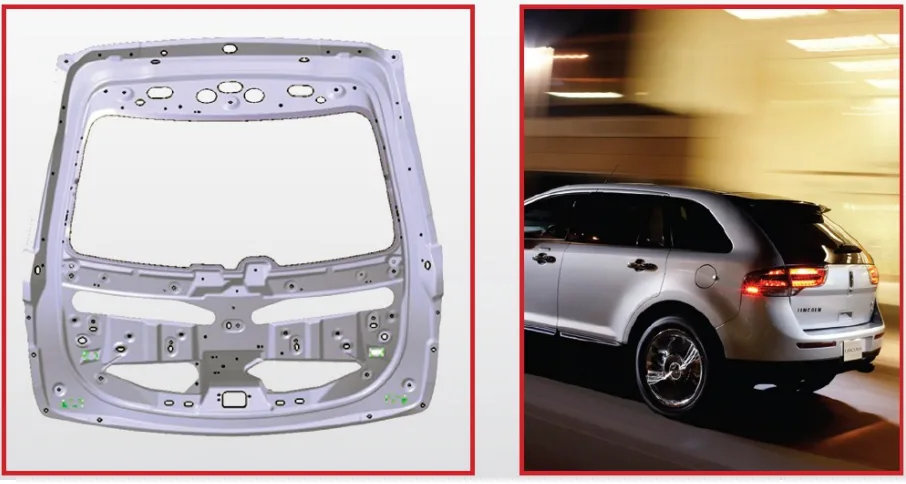
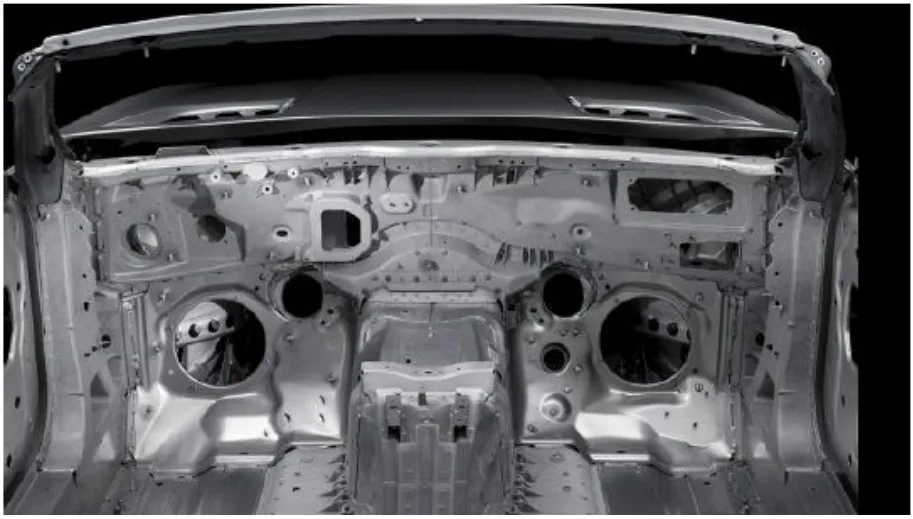
- Figure 1. Relationship of various casting processes to pressure and velocity (Anderson, 2004)
- Figure 2. Steps in a HPDC process (NADCAdesign)
- Figure 3, Advantages of High Pressure Die Casting (Twarog, 2011)
- Figure 4. Cold Chamber Process (Groover, 2007)
- Figure 5. The Hot Chamber Process (Groover, 2007)
- Figure 6, Graph howing the relative cost of a component manufactured by different casting processes (Kalpakjian, 2009)
- Figure 7, Magnesium Lincoln MKT lift gate (Die Casting Engineer, 2010)
- Figure 8, Upper Fire wall (European Aluminium Association)
- Figure 9, Audi Space frame, Showing Structural Die Castings in Red (Hartlieb, 2013)
- Figure 10, Fe rich needle like phase that causes low elongation and flow capabilities (Hartlieb, 2013)
- Figure 11, Major sources of defects in a HPDC product (Twarog, 2011)
- Figure 12, Solubility of Hydrogen drops drastically as the aluminum solidifies, not so much a problem with Magnesium (Campbell, 2011)
- Figure 13, Protection of the surface of the melt by the addition of liquid Argon
- Figure 14, Surface protection by delivery of argon gas parallel to the surface of the melt
- Figure 15, Efficiencies of three different techniques to degassing
- Figure 16, Coupling flux injection with rotor degassing (Neff, 2002)
- Figure 17, For a given size of a bubble, (a) larger oxides are easily floated out while (b) smaller ones follow the streamlines of the rising bubble and so do not collect the bubble (Campbell, 2011)
- Figure 18 Vss- Critial Slow Shot Velocities (Anderson, 2004)
- Figure 19, Illustration showing Atomized flow that is typical in a conventional HPDC (Vinarcik, 2002 )
- Figure 20, Left - Close to eutectic with a small mushy zone, Right - bigger mushy zone (NADCAdesign)
- Figure 21 Conventional Vacuum Die Casting Process (PFIEFER Vacuum, 2006)
- Figure 22, Difference time in vacuum application for Vacural vs. others (Jorstad, 2008 )
- Figure 23, Vacuural Process schematic (Jorstad, 2008 )
- Figure 24, Residual gas content a seen on X-ray (Jorstad, 2008 )
- Figure 25, Valve and Valve less technology for creating vacuum inside the die cavity
- Figure 26, Erroneous Cavity vacuum reading in case of chill blocks (Bagnoud & Bigger, 2008)
- Figure 27, Comparison between Chill Blocks and Valves, (Adapted from (Bagnoud & Bigger, 2008))
- Figure 28, 250 T Cold Chamber die casting Machine at OSU
- Figure 29, PYROTEK® STAR 300® Rotary Degasser
- Figure 30, Specially designed mounts on the furnace to receive the Rotary degasser
- Figure 31, Palmers® Reduced Pressure Tester
- Figure 33, Density measurement after degassing, yellow points indicate that degassing was done
- Figure 34, Four Heat treated samples and one as cast on the extreme right, no blistering observed
- Figure 35, Ejector and cover die with inserts
- Figure 36, Available design space on the cover die half was 4X2X.5 in
- Figure 37, Outer envelope of chill block and initial concept design
- Figure 38, ISO view and section view of entire chill block assembly showing internal trapezoidal passages and required area for venting into vacuum tank
- Figure 39, Initial geometry for chill profile with a cut away (.52X.40in) for consistent vent area
- Figure 40, MAGMA simulation Parameters
- Figure 41, Temperature and Flow lengths at an arbitrary 84% fill, Stars showing location of control points
- Figure 42, Boundary Conditions (BC1 and BC2) & Thermal loads for the 2D Model
- Figure 43, Main effect plots for the factors
- Figure 44, Chill Block design process
- Figure 45, CAD model section view showing the vent passage in the ejector die and hole on the cover die
- Figure 46, Ejector die vent cutout area
- Figure 47, Design criteria for Sealant; to determine optimal sealing.
- Figure 48, Sealant Path on the cover die
7. Conclusion:
This work successfully integrated scattered knowledge to create an overall framework for producing high-integrity aluminum and magnesium castings. Best practices for melt quality were established, and a vacuum-assist die with chill blocks was designed from the ground up using simulation and a designed experiment. The ANOVA results validated the chill block design, showing that copper material and a smaller gap provide the best freezing times. The chill block has since been manufactured, and the die is being machined, proving the practical applicability of the research.
8. References:
- [The full list of 29 references from the paper is extensive. A selection of key references cited in this summary includes:]
- Anderson, W. (2004). Die Cast Engineering: A Hydraulic, Thermal, and Mechanical Process. CRC Press.
- Bagnoud, C., & Bigger, R. (2008). Die Evacuatuation : Valve or Chill Vent? And a Novel System for Process Monitoring and Product Quality Assurance. NADCA Cast Expo. Atlanta: NADCA.
- Campbell, J. (2011). Complete casting handbook: metal casting processes, metallurgy, techniques and design. Elsevier.
- Hamasaiid, A., Dour, G., Dargusch, M., Loulou, T., Davidson, C., & Savage, G. (2008). Heat-Transfer Coefficient and In-Cavity Pressure at the Casting-Die Interface during High-Pressure Die Casting of the Magnesium Alloy AZ91D. Metallurgical and Materials Transactions A, 853-864.
- Jorstad, J. (2008 ). Keynote Presentation: High Vacuum Die Casting. NADCA Cast Expo. Atlanta: NADCA.
- Twarog, D. (2011, January). State of The Die Casting Industry. Die Casting Engineer, p. 16.
- Wang, L., Gershenzon, M., Nguyen, V., & Savage, G. (2007). Air Evacuation and Metal Solidification with Varied Profiles of Chill Surfaces. 111th Metalcasting Congress. Houston: NADCA.
Expert Q&A: Your Top Questions Answered
Q1: What was the single most critical factor identified in this study for improving the vacuum system's performance?
A1: The study's designed experiment concluded that the chill block material was the most influential factor, with copper significantly outperforming H13 steel in freezing the metal front. This is detailed in the "Analysis of Variance" section and supported by the data in Table 6 and the main effect plots in Figure 43.
Q2: How does the chill block approach compare to traditional vacuum valve systems?
A2: The paper's "Valve based and valve-less systems" section notes that while sensor-actuated valves can evacuate a cavity faster, they are more complex and historically prone to maintenance issues. The valve-less chill block approach, as implemented in this study, is a simpler, more robust, and lower-cost alternative, though it may be less efficient in terms of evacuation speed (Figure 27).
Q3: Is this finding applicable to all types of alloys, or a specific one?
A3: The research on melt quality was conducted using A380 aluminum and a similar proprietary alloy. The vacuum die design simulations, as described in the "Designed Experiments" section, were conducted using the properties of magnesium alloy AZ91, as it had similar properties to the target experimental alloy AT72. Applicability to other alloys would require further investigation.
Q4: What specific simulation technique did the researchers use to arrive at the chill block design?
A4: The researchers utilized a two-stage simulation process. First, MAGMA flow simulation was used to determine the metal's temperature (909K) and velocity (16.65m/s) at the cavity exit. Second, these values were used as inputs for a transient thermal analysis in ANSYS to run the designed experiment and determine the freezing time, as explained in the "Magma Simulation" and "ANSYS® Simulations & Results" sections.
Q5: According to the paper, what is the main limitation or area for future research?
A5: The author states in the "Future Work" section that the next steps are to create the remainder of the vacuum system (the trap and control system), run trials to compare casting with and without vacuum, and potentially use MAGMA to validate the approximations made during the ANSYS simulations.
Q6: What is the direct, practical takeaway from this paper for a die casting facility?
A6: The core takeaway is that by combining systematic melt degassing with a well-designed, cost-effective vacuum system using copper chill blocks, a facility can significantly reduce porosity and upgrade its capability to produce high-integrity, structural-grade castings. This is the central conclusion of the paper, "Process and Tool Design for the High Integrity Die Casting of Aluminum and Magnesium Alloys".
Conclusion & Next Steps
This research provides a valuable roadmap for enhancing part integrity in HPDC. By tackling porosity at both the melt preparation and cavity filling stages, the findings offer a clear, data-driven path toward improving quality, reducing defects, and expanding a die caster's market into structural components.
At CASTMAN, we are dedicated to applying the latest industry research to solve our customers' most challenging die casting problems. If the issues discussed in this paper resonate with your operational goals, contact our engineering team to discuss how we can help you implement these advanced principles in your components.
Copyright
- This material is a summary of a thesis by Varun Nandakumar. Based on "Process and Tool Design for the High Integrity Die Casting of Aluminum and Magnesium Alloys".
- Source of the paper: The Ohio State University, 2014.
This material is for informational purposes only. Unauthorized commercial use is prohibited.
Copyright © 2025 CASTMAN. All rights reserved.