This technical brief is based on the academic paper "Potential alternative for water and energy savings in the automotive industry: case study for an Austrian automotive supplier" by Peter Enderle, Otto Nowak, and Julia Kvas, published in the Journal of Cleaner Production (2012). It is summarized and analyzed for HPDC professionals by the experts at CASTMAN.
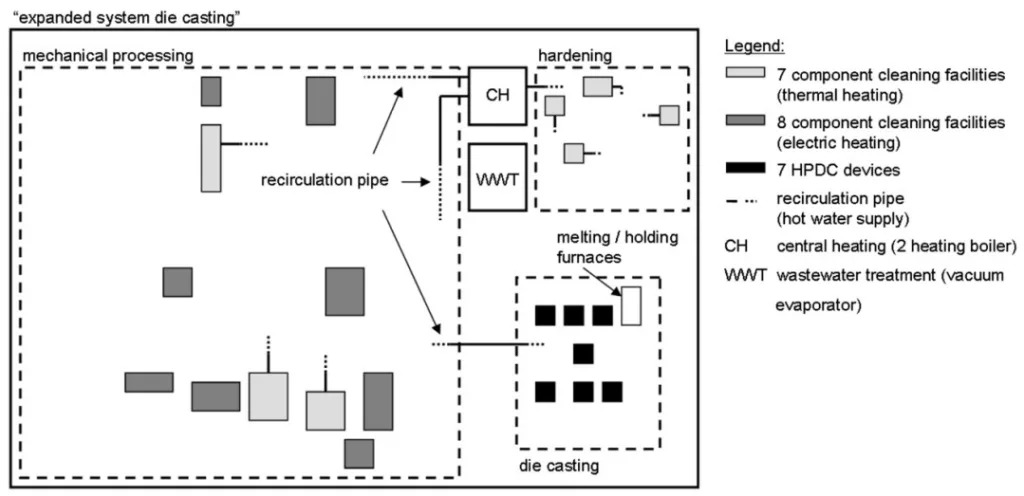
Keywords
- Primary Keyword: Water and energy savings in automotive die casting
- Secondary Keywords: HPDC system optimization, process water reuse, heat recovery, component cleaning, automotive supplier, ultrafiltration, release agent reuse
Executive Summary
- The Challenge: Automotive suppliers face constant pressure to improve the efficiency of water- and energy-intensive processes like high-pressure die casting (HPDC) and component cleaning.
- The Method: Researchers conducted a comprehensive system analysis at an Austrian automotive supplier, investigating the potential to combine heat recovery with process water reuse across multiple production lines.
- The Key Breakthrough: The study demonstrated that by treating heat and water management as an interconnected system, significant savings can be achieved. This includes recovering waste heat from furnaces to reduce gas consumption and treating wastewater for reuse within the process.
- The Bottom Line: An integrated, systematic approach to retrofitting existing HPDC operations can lead to major reductions in natural gas consumption, water usage, and operating costs, with short payback periods.
The Challenge: Why This Research Matters for HPDC Professionals
In the competitive automotive supply chain, resource efficiency is not just an environmental goal—it's a critical factor for economic performance.. Production areas like die casting and component cleaning are major consumers of energy and water.. For decades, engineers have worked to optimize individual machines, but often treat heat management and water circuits as separate issues. This study addresses a common industry challenge: how to unlock further efficiencies by looking at the entire production system holistically. It moves beyond isolated improvements to find savings in the interactions between processes, such as using waste heat from a furnace to support a cleaning line or reusing water from one stage to supply another..
The Approach: Unpacking the Methodology
To investigate this, the researchers expanded the system boundaries beyond just the "die casting" line to include mechanical processing and hardening, terming it the "expanded system die casting" (see Figure 1 in the paper).. This allowed them to analyze the complex exchange of material, energy, and water between different production steps..
The methodology involved a multi-step process:
- System Analysis: A plant-wide audit was conducted to acquire detailed data on all energy and water flows, identifying key consumption points like furnaces, HPDC machines, and cleaning facilities..
- Thermodynamic Calculation: The potential for a heat exchanger network was calculated to determine how waste heat from furnace exhaust could be captured and reused..
- Laboratory and Pilot Tests: To validate water reuse strategies, researchers used an ultrafiltration (UF) pilot plant to treat excess release agent wastewater. They also conducted laboratory tests using freeze concentration to assess further purification possibilities..
The Breakthrough: Key Findings & Data
The study produced clear, quantifiable results demonstrating the power of an integrated systems approach.
- Finding 1: Significant Heat Recovery is Possible: The research identified major opportunities for waste heat recovery. By installing a heat exchanger to capture exhaust heat (cooling it from 140°C to 110°C) from the melting and holding furnaces, the facility could recover 184 MWh/year. A similar integration in the central heating system could recover another 181 MWh/year. Combined, these measures were calculated to save approximately 40,000 m³ of natural gas annually..
- Finding 2: Excess Release Agent Can Be Reused: The pilot tests proved that ultrafiltration is effective for treating excess release agent wastewater. The process achieved an average Chemical Oxygen Demand (COD) reduction of 77%. This treated water was viable for reuse as a solvent in preparing new release agent mixtures, with a concept designed to treat and reuse 18% of the accruing excess agent..
- Finding 3: Component Cleaning Efficiency Can Be Dramatically Increased: By adapting the bath maintenance system of a high-throughput component cleaning facility—including implementing an automatic chemical dosage system and changing to a modular cleaning formulation—the lifetime of the cleaning baths was extended from 5 weeks to 25 weeks. This single optimization reduced the facility's yearly operating costs by 43%..
Practical Implications for Your HPDC Products
Based strictly on the paper's results and conclusions, these findings have direct applications for real-world manufacturing environments.
- For Process Engineers: The findings in the "Energy-related considerations" section suggest that installing a heat exchanger to capture waste heat from furnace exhaust stacks and use it to pre-heat the return flow of the main hot water circuit is a viable, cost-saving project. This research suggests that by considering this, you might be able to achieve a significant reduction in natural gas consumption..
- For Quality Control: The paper highlights that the quality of water used for release agent dilution is critical to avoiding product defects like discoloration and increased porosity.. The correlation shown in the study between treatment (ultrafiltration) and water purity provides a new potential indicator for monitoring process inputs to ensure consistent casting quality.
- For Die and System Maintenance: This study on process water reuse implies that contaminants like leaked hydraulic fluids (glycols) are a primary obstacle to effective water recycling.. This underscores the importance of robust preventative maintenance programs to minimize leaks, not only for machine health but also to improve the feasibility and reduce the cost of water treatment initiatives.
Paper Details
Potential alternative for water and energy savings in the automotive industry: case study for an Austrian automotive supplier
1. Overview:
- Title: Potential alternative for water and energy savings in the automotive industry: case study for an Austrian automotive supplier..
- Author: Peter Enderle, Otto Nowak, Julia Kvas..
- Year of publication: 2012 (Available online 20 November 2011)..
- Journal/academic society of publication: Journal of Cleaner Production..
- Keywords: Aluminium die casting, Component cleaning, System optimization, Process water reuse, Heat recovery..
2. Abstract:
This paper shows the alternative possible optimization measures to increase the water and energy efficiency in the automotive industry. A potential study on the technological system optimization of an automotive supplier was performed by combining the fields of process water reuse and heat recovery. Possible optimization measures to retrofit existing processes with the focus on high pressure die casting and component cleaning were worked out. Furthermore, limiting factors for a successful and extensive implementation in the case of retrofitting existing processes and systems were evaluated..
3. Introduction:
The automotive industry is a critical industrial sector where suppliers play an integral role, producing nearly 80% of a modern automobile's components.. While not the most water- and energy-intensive industry overall, specific production areas like die casting, mechanical processing, and paint finishing have a high potential for resource efficiency improvements.. This study focuses on High-Pressure Die Casting (HPDC) and component cleaning, which are common, high-impact processes within the automotive supply chain..
4. Summary of the study:
Background of the research topic:
The research is set against the backdrop of increasing economic and environmental pressure on the automotive industry to improve resource efficiency. The focus is on HPDC, a key process for producing complex, lightweight aluminum components, and the associated cleaning steps, which are often water, chemical, and energy-intensive..
Status of previous research:
Previous studies have focused on specific issues like eco-innovations or vehicle recycling.. However, this paper identifies a need for a more integrated, systematic approach that combines heat recovery and process water reuse, looking at the production facility as an interconnected system rather than a collection of standalone processes..
Purpose of the study:
The study's purpose was to identify and evaluate possible optimization measures to increase water and energy efficiency at an automotive supplier's production site. The goal was to develop practical concepts for retrofitting existing systems by combining heat recovery and water reuse, while identifying the limiting factors for implementation..
Core study:
The core of the study was a detailed system analysis of an Austrian automotive supplier producing driveline and chassis control systems. The analysis focused on the "expanded system die casting," which includes the die casting line, mechanical processing, and hardening lines. Researchers evaluated energy and water flows, calculated heat recovery potential, and conducted pilot tests on ultrafiltration for treating excess release agent wastewater for reuse..
5. Research Methodology
Research Design:
The research was designed as a case study involving a comprehensive potential study at a single, large-scale automotive supplier. The approach was stepwise, beginning with a plant-wide audit and moving to detailed analysis and pilot testing. The system boundaries were intentionally expanded to include interconnected production lines to identify cross-process optimization opportunities..
Data Collection and Analysis Methods:
Data was collected from technical documents, internal company data (operating times, resource inputs), and direct measurements. The analysis involved calculating the overall energy and water balance, performing thermodynamic calculations for a heat exchanger network, and using laboratory/pilot tests (ultrafiltration, freeze concentration) to verify the separation efficiency of water treatment technologies. Parameters like COD, TOC, and TIC were analyzed to measure water quality..
Research Topics and Scope:
The scope covered the production lines for die casting, mechanical processing, and hardening. The primary research topics were:
- Heat recovery from melting/holding furnaces and the central heating system..
- Process water reuse, specifically the treatment and reuse of excess water-soluble release agent from HPDC machines..
- Optimization of component cleaning processes..
6. Key Results:
Key Results:
The study successfully identified concrete measures for energy and water savings. The main results include a calculated natural gas reduction of approx. 40,000 m³/y through waste heat recovery, a validated concept for reusing 18% of excess release agent via ultrafiltration, and a 43% reduction in annual operating costs for a cleaning system by improving its maintenance and chemical formulation..
Figure Name List:
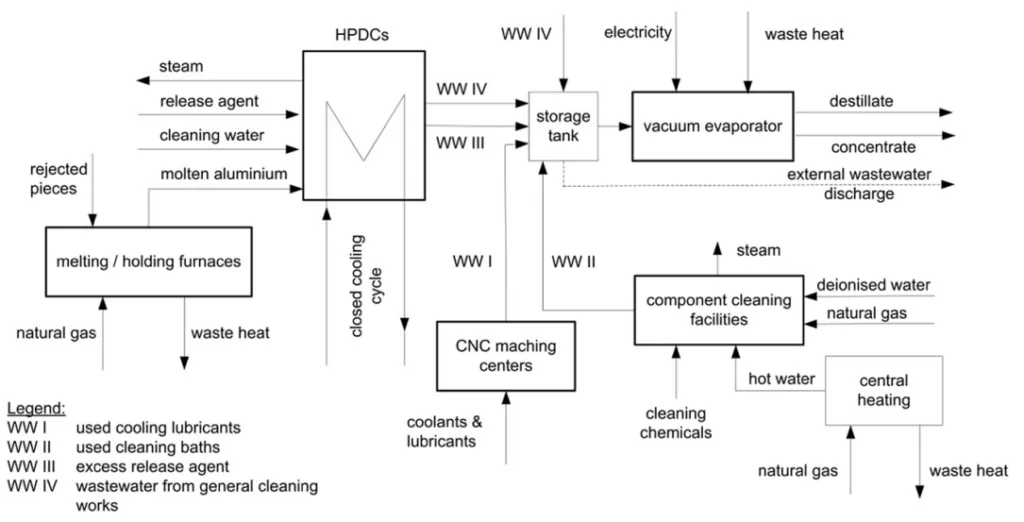
- Fig. 1. Production site and system boundaries including the relevant processes considered within the project..
- Fig. 2. Considered in- and output flows within the investigated company.
7. Conclusion:
The paper concludes that industrial water and energy systems are highly interconnected. A systematic approach that considers the entire system is essential for developing effective optimization concepts. The study demonstrated that combining heat recovery and process water reuse is feasible and economically beneficial, though retrofitting existing systems is often limited by various sub-processes. The most successful optimization measures are those that intelligently combine technology and system-level thinking, focusing on solutions with short payback periods..
8. References:
- Enderle, P., Nowak, O., Kvas, J., 2012. Potential alternative for water and energy savings in the automotive industry: case study for an Austrian automotive supplier. Journal of Cleaner Production 34, 146-152.
- Brunn, K., 2001. Modular Aqueous Cleaning Systems-Different Fields of Application. SurTec Technical Letter 3. Surtec GmbH, Zwingenberg, Germany (in German)..
- EIPPCB (European IPPC Bureau), 2005. Reference Document on Best Available Techniques in the Smitheries and Foundries Industry. European Commission..
- Keudel, L., 2011. Treatment of wastewater from the automotive industry. In: Proceedings DWA Conference Behandlung von Industrie- und Gewerbeabwasser. Kassel, Germany, 2011, pp. 322-345 (in German)..
- Mueller, W., 1998. Corrosion at Die Casting Facilities When Using Aqueous Products. Technical Letter. Geiger + Co. Schmierstoff-Chemie GmbH, Heilbronn, Germany (in German)..
Expert Q&A: Your Top Questions Answered
Q1: What was the single most critical factor identified in this study for improving efficiency?
A1: The study concluded that the most critical factor is adopting a systematic approach that intelligently combines technology and system optimization. The paper states this is the "basic requirement in order to develop practical optimization concepts" because areas like heat recovery and water reuse are closely connected and influence one another. [1, Conclusion].
Q2: How does this research compare to traditional methods for addressing water and energy use?
A2: The paper's approach differs from traditional "end-of-pipe" methods, where waste streams are simply treated before discharge. This research focuses on an integrated strategy of process water reuse and heat recovery, aiming to loop resources back into the production system, as detailed in the methodology and results sections..
Q3: Is this finding applicable to all types of alloys, or a specific one?
A3: The research was conducted at a supplier producing lightweight components from aluminum alloys, but the specific alloy is not mentioned. [1, Introduction]. The principles of heat recovery and water/chemical management for release agents and cleaning systems are generally applicable to many HPDC operations, though specific parameters would need to be adjusted.
Q4: What specific measurement or simulation technique did the researchers use to arrive at this conclusion?
A4: The researchers utilized several techniques, including a pilot-scale ultrafiltration (UF) test facility to test the reuse of excess release agent, laboratory tests for freeze concentration, and thermodynamic calculations to design and evaluate a potential heat exchanger network for waste heat recovery. [1, Research Methodology].
Q5: According to the paper, what is the main limitation or area for future research?
A5: The authors state in the Conclusion
that a key limitation is that the "maximum efficiency is influenced through a variety of sub-processes, which limit the economical implementation potential as a whole." For example, contamination of release agent wastewater with glycol from hydraulic leaks was a limiting factor for reuse, and the reuse of waste heat from the hardening process was rejected due to technical and economic reasons..
Q6: What is the direct, practical takeaway from this paper for a die casting facility?
A6: The core takeaway is that by optimizing interconnected systems—specifically by capturing waste heat from furnaces and treating process water for reuse—it is possible to achieve significant, quantifiable reductions in energy consumption, water use, and operational costs, a conclusion strongly supported by the overall results of the paper, "Potential alternative for water and energy savings in the automotive industry: case study for an Austrian automotive supplier"..
Conclusion & Next Steps
This research provides a valuable roadmap for enhancing resource efficiency in HPDC. The findings offer a clear, data-driven path toward improving quality, reducing waste, and optimizing production costs by treating energy and water as an integrated system.
At CASTMAN, we are dedicated to applying the latest industry research to solve our customers' most challenging die casting problems. If the issues discussed in this paper resonate with your operational goals, contact our engineering team to discuss how we can help you implement these advanced principles in your components.
Copyright
- This material is a paper by "Peter Enderle, Otto Nowak, Julia Kvas". Based on "Potential alternative for water and energy savings in the automotive industry: case study for an Austrian automotive supplier".
- Source of the paper: https://doi.org/10.1016/j.jclepro.2011.11.013
This material is for informational purposes only. Unauthorized commercial use is prohibited.
Copyright © 2025 CASTMAN. All rights reserved.