This introduction paper is based on the paper "New Wear Resistant Hypereutectic AlSi4Cu4FeCrMn Alloys for High Pressure Die Casting" published by "International journal of metalcasting".

![Fig. 1: Relationship between sludge formation temperature and sludge factor for AlSi9Cu3(Fe) [10] and AlSi14Cu4FeMnCr](https://castman.co.kr/wp-content/uploads/image-2401.webp)
1. Overview:
- Title: New Wear Resistant Hypereutectic AlSi4Cu4FeCrMn Alloys for High Pressure Die Casting
- Author: O. Zak, B. Tonn, A. Baesgen and L. Kallien
- Year of publication: 2015 (December)
- Journal/academic society of publication: International journal of metalcasting
- Keywords: Keywords are not explicitly stated in the paper.
2. Abstract:
This paper introduces an innovative concept for developing new wear-resistant hypereutectic aluminum-silicon alloys suitable for high-pressure die casting (HPDC). Conventional hypereutectic AlSi17Cu4Mg alloys, while offering good wear resistance, present challenges in HPDC due to high casting temperatures and the abrasive nature of primary silicon. The proposed approach involves reducing the silicon content from 17 wt.-% to 14 wt.-% to lower casting temperatures, and incorporating iron to form hard α-Al15Fe3Si2 intermetallic phases, compensating for the reduced primary silicon volume fraction and enhancing tribological properties. Additions of chromium (Cr) and manganese (Mn) are used to promote the formation of compact α-phase intermetallics and avoid detrimental β-Al5FeSi platelets. The study investigates sludge formation, microstructure, mechanical properties, and HPDC processability of these new AlSi14Cu4FeCrMn alloys, demonstrating their potential for applications like monolithic engine blocks with improved castability and wear performance in HPDC.
3. Introduction:
Hypereutectic AlSi17Cu4Mg alloys are utilized for castings requiring significant wear resistance, low thermal expansion, and good mechanical properties at room and elevated temperatures, such as in climate compressor housings and monolithic engine blocks. Their wear resistance stems from primary silicon crystals (hardness up to 1148 HV). Monolithic engine blocks from these alloys offer weight advantages over those with cast iron liners. However, producing these blocks via high-pressure die casting (HPDC), a highly productive process, is limited. The high precipitation temperature of primary silicon (around 660 °C) leads to high casting temperatures, reducing die and shot chamber life, promoting hydrogen absorption, and oxide formation. The high latent heat of primary silicon also lowers melt viscosity, increasing the risk of melt spurting.
To address these limitations for HPDC applications and improve tribological properties, this paper introduces an innovative alloy concept:
- Reduce silicon content from 17 wt.-% to 14 wt.-% to enable lower casting temperatures.
- Add iron to compensate for the reduced volume fraction of hard primary silicon particles by forming the hard iron-containing α-Al15Fe3Si2-phase, thereby improving tribological properties.
- Add elements like Cr and Mn to prevent the formation of detrimental intermetallic β-Al5FeSi platelets.
4. Summary of the study:
Background of the research topic:
The research focuses on hypereutectic Al-Si alloys, specifically for applications demanding high wear resistance like engine components. While these alloys are beneficial, their use in high-pressure die casting (HPDC) is constrained by issues related to high silicon content, such as high casting temperatures and die wear.
Status of previous research:
Previous research indicates that a uniform distribution of fine primary silicon particles is key for optimal cylinder block surface characteristics, conventionally achieved by phosphorus addition. However, phosphorus increases silicon precipitation temperature and can promote detrimental β-platelets in the presence of iron. Iron, a common impurity, can form harmful β-Al5FeSi platelets or, with Mn and Cr, more compact and less detrimental α-Al15(Fe,Mn,Cr)3Si2 phases, which can also contribute to wear resistance (approx. 815 HV). However, these α-phases can form sludge if their precipitation temperature exceeds the melt temperature. The sludge factor (SF = Fe + 2 x wt. % Mn + 3 x wt. %Cr) is used to predict sludge formation tendency.
Purpose of the study:
The study aimed to develop a new wear-resistant hypereutectic AlSi-alloy specifically tailored for high-pressure die casting. The objectives were to overcome the limitations of existing alloys by:
- Allowing lower casting temperatures.
- Improving tribological properties.
- Ensuring good castability in HPDC.
- Maintaining adequate mechanical properties.
This was pursued by modifying the alloy composition, specifically by reducing Si content and strategically adding Fe, Cr, and Mn.
Core study:
The core of the study involved:
- Investigation of sludge formation: Determining the sludge formation temperatures for new AlSi14Cu4FeMnCr alloys with varying sludge factors (1.6, 2.0, 2.9) and comparing them to commercial AlSi9Cu3(Fe) alloys.
- Microstructural analysis: Characterizing the primary silicon and iron-containing intermetallic phases (α-AlFeSi, β-AlFeSi) in gravity die-cast and HPDC samples using optical microscopy, SEM, and EDX.
- Mechanical property evaluation: Conducting tensile tests on gravity die-cast and HPDC samples to determine properties like tensile strength (Rm), yield strength (Rp0.2), and elongation (A5%).
- HPDC experiments: Evaluating the castability and performance of the new alloys in HPDC, including:
- Effect of casting temperature on microstructure.
- Hot tear formation tendency.
- Soldering effects (ejector force).
- Abrasive effects on the die.
- Influence of zinc (Zn) additions.
- Tribological property assessment: Performing wear resistance tests (disc-cylinder method) to compare the new alloy with a conventional hypereutectic AlSi17Cu4Mg alloy.
5. Research Methodology
Research Design:
The research employed an experimental design. Alloys with targeted compositions (AlSi14Cu4 with varying Fe, Mn, Cr, and later Zn) were prepared and subjected to a series of investigations:
- Sludge formation studies in an electrical resistance furnace.
- Gravity die casting for initial microstructure and mechanical property assessment.
- High-pressure die casting (HPDC) trials using a specialized test geometry to evaluate processability and performance under industrial-like conditions.
Data Collection and Analysis Methods:
- Chemical Analysis: Samples from the melt surface were taken for chemical analysis to determine sludge formation temperatures.
- Microstructure Analysis:
- Optical microscopy for general microstructure.
- Scanning Electron Microscopy (SEM) for detailed phase morphology and fracture surface analysis.
- Energy Dispersive X-ray Spectroscopy (EDX) for determining the chemical composition of intermetallic phases.
- Quantitative analysis of phase volume fractions and particle sizes.
- Mechanical Testing: Tensile tests were performed to measure Rm, Rp0.2, and A5%.
- Hot Tear Formation Assessment: Visual inspection of HPDC samples and penetrant testing. MAGMA simulation was also used for prediction.
- Soldering Effect Measurement: Evaluation of the force needed to eject castings from the die.
- Abrasive Effect Assessment: A steel test pin integrated into the runner of the HPDC die was examined for wear after multiple castings.
- Tribological Testing: Wear resistance was evaluated using a disc-cylinder method, measuring friction coefficients and test duration until failure.
Research Topics and Scope:
The research focused on the development and characterization of new hypereutectic AlSi14Cu4FeCrMn alloys for HPDC. The scope included:
- Investigating the effect of Fe, Mn, and Cr content (via sludge factor) on sludge formation temperature.
- Characterizing the morphology, size, and composition of primary silicon and iron-containing intermetallic phases (α-Al15Fe3Si2 and β-Al5FeSi).
- Evaluating the mechanical properties (tensile strength, yield strength, elongation) of the new alloys in as-cast conditions (gravity and HPDC).
- Assessing HPDC processability: optimal casting temperature, hot tear susceptibility, die soldering tendency, and abrasive effects on die materials.
- Studying the influence of Zn additions (1 wt.-% and 3 wt.-%) on the properties of the new alloy.
- Comparing the tribological performance (friction and wear) of the new alloy with conventional hypereutectic AlSi17Cu4Mg alloys.
6. Key Results:
Key Results:
- Sludge Formation: The new AlSi14Cu4FeMnCr alloys exhibited lower sludge formation temperatures compared to commercial AlSi9Cu3(Fe) alloys for a given sludge factor. An alloy with Sf=2.9 (AlSi14Cu4Fe1.8Cr0.3Mn0.1) showed a sludge formation temperature of 650 °C, allowing for lower casting temperatures. This composition also promoted the highest volume fraction of hard α-AlFeSi phase.
- Microstructure (Gravity Casting): The AlSi14Cu4Fe1.8Cr0.3Mn0.1 alloy showed primary silicon particles (average size 20 µm, 5% volume) and α-AlFeSi phases (average size 16 µm, 4% volume) in a polyhedral shape, with minimal detrimental β-AlFeSi. Silicon particle size was smaller than in conventional hypereutectic alloys, even without phosphorus. EDX analysis confirmed higher Mn and Cr content in the compact α-Al15Fe3Si2 phase compared to the platelet β-Al5FeSi phase.
- Mechanical Properties (Gravity Casting): The new AlSi14Cu4FeMnCr alloy (Rm 197 MPa, Rp0.2 176 MPa, A5 0.3%) showed comparable mechanical properties to conventional AlSi17Cu4Mg (Rm 180-235 MPa, Rp0.2 170-225 MPa, A5 <1.0%), with advantages of lower melting/casting temperatures and reduced material costs.
- HPDC - Casting Temperature: A lower pouring temperature of 680 °C for HPDC resulted in a more uniform distribution of primary silicon particles for the AlSi14Cu4Fe1.8Cr0.3Mn0.1 alloy.
- HPDC - Hot Tear Formation: The new alloys exhibited excellent castability in HPDC, with no hot tears observed in critical sections of the test castings, verified by penetrant testing.
- HPDC - Soldering Effects: Ejector forces decreased with increasing iron and zinc contents in the new alloys. The ejector force for the new alloys was significantly lower (about 30 times) than that for AlSi93Cu3 (Note: paper states AlSi93Cu3).
- HPDC - Abrasive Effects: After 150 castings with the new hypereutectic iron-containing alloys, a tool steel (X38CrMoV5) test pin in the runner showed no significant wear on its sharp corners, suggesting die durability similar to processing standard AlSi9Cu3.
- HPDC - Microstructure: EDX analysis of HPDC samples confirmed that block-shaped α-AlFeSi phases had increased Cr and Mn content, while plate-shaped β-AlFeSi phases showed no Cr or Mn. The size of block-shaped α-AlFeSi phases in AlSi14Cu4Fe1.8Cr0.3Mn0.1 and AlSi14Cu4Fe1.8Cr0.3Mn0.1Zn1 was similar to primary silicon, beneficial for wear resistance. The eutectic structure was generally not refined or only partially refined.
- HPDC - Mechanical Properties: For HPDC samples, increasing iron content led to decreased elongation (0.75% to 0.45%). Tensile strength remained around 250 MPa. Zinc additions increased yield strength by approx. 25 MPa. The AlSi14Cu4Fe1.8Cr0.3Mn0.1Zn1 alloy (Rm 249 MPa, Rp0.2 196 MPa, A5 0.5%) showed higher tensile and yield strength than standard AlSi9Cu3 (Rm 240 MPa, Rp0.2 170 MPa, A5 0.7%).
- Tribological Properties: In wear tests (disc-cylinder, 20N load, 100Hz, 0.5mm amplitude), the new AlSi14Cu4Fe1.8Cr0.3Mn0.1 HPDC alloy exhibited significantly better wear resistance, failing after 135 minutes, compared to AlSi17Cu4Mg (both HPDC and LPDC samples), which failed in less than 10 minutes. The new alloy also showed the lowest friction coefficient (µ ≈ 0.127 vs. ≈0.196 for AlSi17Cu4Mg HPDC and ≈0.237 for AlSi17Cu4Mg LPDC).
Figure Name List:
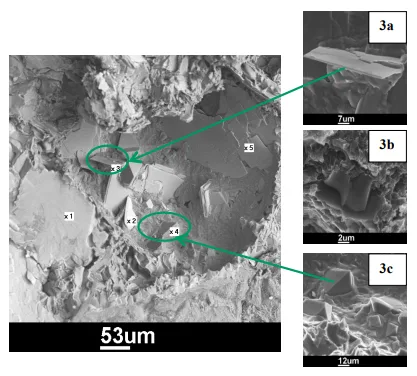
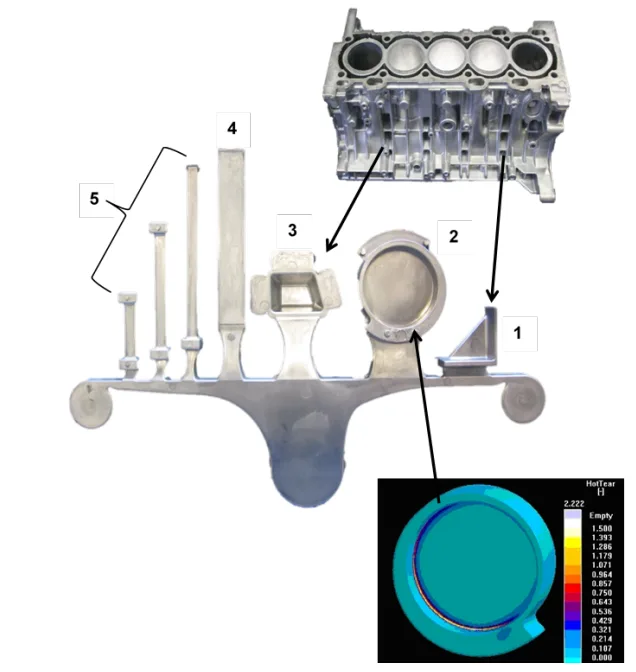
- Fig. 1: Relationship between sludge formation temperature and sludge factor for AlSi9Cu3(Fe) [10] and AlSi14Cu4FeMnCr
- Fig. 2: Microstructure of gravity die cast AlSi14Cu4Fe1,8Cr0,3Mn0,1 alloy
- Fig. 3: SEM micrographs of fracture surface of gravity die casting specimens of AlSi14Cu4Fe1,8Cr0,3Mn0,1
- Fig. 4: High pressure die casting test geometry shows critical sections which appear in real life engine blocks. The disc shaped casting indicates
- Fig. 5: Steel made test geometry for estimating abrasive effects during fill phase of hpdc mold
- Fig. 6: a) AlSi14Cu4Fe1,8Cr0,3Mn0,1; cast at 720° b) AlSi14Cu4Fe1,8Cr0,3Mn0,1; cast at 680 °C
- Fig. 7: Penetrant crack testing on an test casting out of the alloy AlSi14Cu4Fe1,8Cr0,3Mn0,1
- Fig. 8: Ejector force of the different test alloys
- Fig. 9: Test geometry for displaying the abrasive effects of the various alloys made of X38CrMoV51: a) unused b) used during all hpdc tests in the runner of the mold
- Fig. 10: Cr- and Mn-contents of different phases
- Fig. 11: Block shaped primary silicon and α-AlFeSi phases in AlSi14Cu4Fe1,8Cr0,3Mn0,1
- Fig.12: Block shaped primary silicon and α-AlFeSi phases in AlSi14Cu4Fe1,8Cr0,3Mn0,1Zn3
- Fig. 13: Eutectic structure of AlSi14Cu4Fe1,8Cr0,3Mn0,1Zn1
- Fig. 14: Mechanical properties of the analyzed alloys
- Fig. 15: Testing scheme for determining friction coefficients
- Fig. 16: Friction coefficients of different hypereutectic AlSi alloys
7. Conclusion:
The study demonstrates that the newly developed AlSi14Cu4Fe1.8FeCr0.3Mn0.1 alloy successfully combines excellent castability with extraordinary tribological properties for high-pressure die casting applications. This improved performance is attributed to the precipitated iron phases (α-AlFeSi) exhibiting a size similar to that of the primary silicon particles, contributing effectively to wear resistance. Furthermore, the mechanical properties of this new alloy are comparable to those of conventional high-pressure die casting alloys currently used for series production of components like engine blocks. These findings suggest that the new alloy system is a promising candidate for producing wear-resistant parts via HPDC with benefits in processing and performance.
8. References:
- [1] Korn, Derek: "How to hone an atypical aluminum alloy", Modern Machine Shop, 9/17/2008.
- [2] Development of Aluminum Powder Metallurgy Composites for Cylinder Liners, International Congress & Exposition Detroit, Michigan February 28-March 3,1994
- [3] Aluminum and aluminum alloys and casting problems; http://www.keytometals.com/Article83.htm
- [4] Marisa Di Sabatino: "Fluidity of aluminium foundry alloys", Dissertation, Norwegian University of Science and Technology (NTNU), 2005.
- [5] Aluminium-Motorblöcke: Konzepte, Visionen, Serien. Metall (2007), Heft 3, S. 92-97.
- [6] Zak, H., Zak, O., Tonn, B.: Entwicklung einer eisenhaltiger Aliminium-Silizium-Legierung zur Herstellung monolithischer Motorblock im Druckgießverfahren", Gießerei Praxis, Ausgabe 5, 2011.
- [7] Taylor, John A.: "The effect if iron in Al-Si casting alloys", The University of Queensland
- [8] Belov, N.A., Alsenov, A. A., Eskin, D. G.: "Iron in aluminum alloys", 2002.
- [9] Makhlouf M. Makhlouf Diran Apelian: "Casting characteristic of aluminum die casting alloys", 2002.
- [10] Jorstad, J. L, "Understanding Sludge", Proc. Of the 14th SDCE International Die Casting Congress and Exposition, Toronto, Ont, Canada, May 11-14, 1987, Paper No. G-T87-011.
- [11] Gobrecht, J. "Gravity-Segregation of Iron, Manganese and Chromium in an Aluminum-Silicon Casting, Part I", Giesserei, Vol. 61, No. 10, 1975, pp 263-265.
- [12] Taghaddos, E., Hejazi M. M., Taghiabadi R., Shabestari S. G.: Effect of iron-intermetallics on the fluidity of 413 aluminum alloy, Journal of Alloy and Compounds, 468, 2009, p. 539-545.
- [13] Zak, H.; Tonn, B.: „Melt Treatment, Grain refinement Modification I: Effect of Alloying Elements on Iron-Containing Intermetallics in Al-Si-Mg-Cu 319 and 380 Alloys"; Aluminium Alloys, Edited by Jürgen Hirsch, Birgit Skrotzki and Günter Gottstein, Weley-VCH GmbH KGaA, 2002; S. 283
- [14] Baesgen, A.: „Beitrag zur prozesssicheren und kosteneffektiven Herstellung von verschleißbeanspruchen Druckgussteilen aus übereutektischen Aluminium-Silizium-Legierungen; Dissertation 2012; ISBN 978-3-8440-2006-9
- [15] Abschlussbericht zum DFG-Projekt TO 271/6-1-2, Förderzeitraum 01.10.2005-20.09.2008.
- [16] Chai, G.; Bäckerud, L.: „Einige Einflussgrößen auf die Veredelung von Aluminiumgußlegierungen bei Zusatz von strontiumhaltigen Vorlegierungen“, Gießerei-Praxis 11/12; 1993
9. Copyright:
- This material is a paper by "O. Zak, B. Tonn, A. Baesgen and L. Kallien". Based on "New Wear Resistant Hypereutectic AlSi4Cu4FeCrMn Alloys for High Pressure Die Casting".
- Source of the paper: https://doi.org/10.1007/BF03356040
This material is summarized based on the above paper, and unauthorized use for commercial purposes is prohibited.
Copyright © 2025 CASTMAN. All rights reserved.