This introduction paper is based on the paper "The Design of an Experiment to Choose an Aluminum Die Casting Alloy for Energy Absorbing Automotive Components" published by "SAE International (Reprinted from: Developments in Aluminum Use for Vehicle Design (SP-1164))".
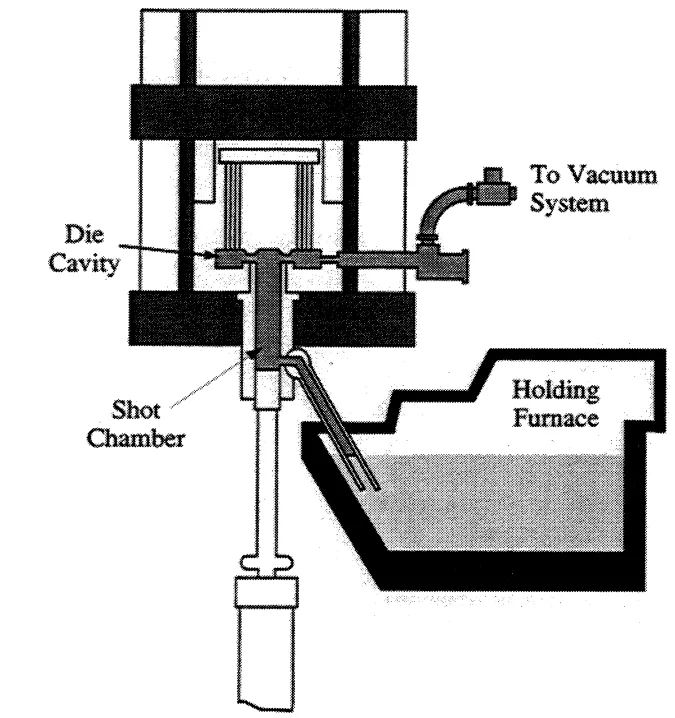
1. Overview:
- Title: The Design of an Experiment to Choose an Aluminum Die Casting Alloy for Energy Absorbing Automotive Components
- Author: Ron Stutsman, Barri Chamberlain, Mike Evans
- Year of publication: 1996
- Journal/academic society of publication: SAE Technical Paper Series (Paper 960159), Reprinted from: Developments in Aluminum Use for Vehicle Design (SP-1164), International Congress & Exposition, Detroit, Michigan, February 26-29, 1996.
- Keywords: Not specified in the paper.
2. Abstract:
Targeting a steering wheel as a component requiring energy absorbing characteristics, a development team was set up, consisting of a component supplier, pressure die caster and an aluminum supplier, with the objective of developing a suitable aluminum alloy. The component's desired mechanical properties were outlined and an aluminum alloy system was selected for study. After considering the alloying elements most likely to have an influence on mechanical and casting properties, an experiment was designed to test eight alloy variants and their effect on the as-cast properties of die cast test bars. The bars were tested at three separate laboratories and the results were used to determine the effects of alloying elements and their interactions.
The data confirmed the suitability of a castable aluminum-magnesium alloy, capable of exceeding 205 MPa (30 ksi) Ultimate tensile strength, 105 MPa (15 ksi) 0.2% yield strength and 15% elongation in the as-cast condition. This paper covers the design of experiment, alloy production, casting conditions and interpretation of results leading to the choice of a preferred alloy.
3. Introduction:
There is an increasing need for economical lightweight, energy absorbing components in automobiles to reduce body and chassis weight for better energy efficiency without sacrificing vehicle size or content. Light alloy, pressure die cast thin walled components can achieve these weight savings. The economics and mechanical properties are dictated by alloy choice and casting process. While magnesium offers the best weight savings, its supply and price stability make aluminum a strong contender.
Commonly used aluminum die casting alloys often have poor as-cast ductility. For instance, only Aluminum Association (AA) alloys 364.0, 443.0, 515.0, and 518.0 show greater than 7.5% elongation. This study focused on developing an aluminum die casting alloy for a steering wheel (Figure 1), currently made from a magnesium alloy by Delphi Interior & Lighting Systems. The target mechanical properties for as-cast test bars were set at a minimum of 205 MPa Ultimate Tensile Strength, 105 MPa 0.2% Yield Strength, and 15% Elongation. Based on prior experimental work by Gibbs Die Casting Corporation with an AA 515.2 type alloy, the new alloy design was based on a nominal magnesium content of 3.0%.
4. Summary of the study:
Background of the research topic:
The automotive industry requires lightweight, energy-absorbing components to improve fuel efficiency. Aluminum die castings are a viable option, but existing alloys often lack the necessary ductility for such applications. Aluminum-magnesium (Al-Mg) alloys offer a range of properties; low Mg content alloys have good formability, while higher Mg content increases strength and improves castability in foundry alloys, though very high Mg alloys (e.g., AA 518.2 with 8% Mg) can be difficult to cast and have issues like hot cracking and die soldering. The study aimed to find an Al-Mg alloy with a balanced set of properties.
Status of previous research:
The paper references the Aluminum Association (AA) for compositional ranges of Al-Mg alloys (Table 1). It notes that commonly used aluminum die casting alloys have poor as-cast ductility. Gibbs Die Casting Corporation had prior experience with an AA 515.2 type aluminum alloy. The influence of various alloying elements like silicon (Si), iron (Fe), manganese (Mn), and others on Al-Mg alloys is generally known; for example, Mondolfo³ reported on the effects of Si, and the role of Fe in die soldering reduction and Mn in modifying the embrittling effect of iron. The "sludge factor" (related to Fe, Mn, Cr content) is a known concern for castability (Figure 2). An internal report by Alcan International Limited⁴ on die soldering was also considered.
Purpose of the study:
The primary purpose was to design and identify an aluminum die casting alloy capable of meeting specific mechanical properties for energy-absorbing automotive components, specifically a steering wheel. The target properties were:
- Ultimate Tensile Strength (UTS): ≥ 205 MPa
- 0.2% Yield Strength (YS): ≥ 105 MPa
- Elongation: ≥ 15%
in the as-cast condition. The study aimed to understand the effects of key alloying elements (Fe, Si, Mn, Ti) on these properties in an Al-3%Mg base alloy.
Core study:
The core of the study involved a Design of Experiment (DOE) approach to evaluate eight different variants of an aluminum alloy with a constant 3.0% magnesium content. The experiment varied the levels of four major alloying elements: Iron (Fe), Silicon (Si), Manganese (Mn), and Titanium (Ti, added as Ti-B grain refiner). A 24-1 fractional factorial design (Table 2) was employed. Test bars were die cast using these eight alloy compositions and subsequently tested for their mechanical properties (UTS, YS, Elongation) at three different laboratories. The results were then analyzed to determine the influence of each alloying element and their interactions on the final properties.
5. Research Methodology
Research Design:
A 24-1 fractional factorial design of resolution R = IV was employed. This design allowed for the study of the main effects of four alloying elements (Fe, Si, Mn, Ti-B) and some two-factor interactions, without confounding main effects with two-factor interactions. Magnesium was held constant at 3.0%.
The levels for the elements were:
- Silicon (Si): High 0.45%, Low 0.2%
- Iron (Fe): High 0.6%, Low 0.25%
- Manganese (Mn): High 0.6%, Low 0.25%
- Titanium (Ti, as titanium-boride hardener): Nominal High 0.045%, Low (trace) <0.01%
Sodium and calcium were controlled at <0.0010% and copper at <0.10%. Eight alloy variants were produced.
Data Collection and Analysis Methods:
Ingots for the eight alloy variants were produced by Alcan Recycling, Guelph Alloys Plant (Figure 3). These ingots were remelted at Gibbs Die Casting Corp. in a 450 kg gas-fired crucible furnace, transferred to a 225 kg ladle, degassed, and cleaned. Test bars conforming to ASTM Standard Tension Test specimen for Die Castings (Figure 5) were cast in pairs using the Gibbs Vertical Vacuum High Pressure Die Casting Process (Figure 4). This process involves vacuum evacuation of die cavities, controlled metal injection, and high pressure application during solidification.
Spectrographic disc samples were taken from remelted stock for chemical analysis (Table 3). Five test bars from each alloy batch were pulled in the as-cast condition at an initial strain rate of 0.06 mm/mm per minute at each of the three participating laboratories (Delphi, Alcan, Gibbs). Ultimate Tensile Strength, 0.2% Yield Strength, and Percentage Elongation were recorded (Table 4). Results from test bars that broke outside the gauge length were discarded.
Multiple Regression Modelling was used to analyze the data and determine the major effects of the alloying additions on the mechanical properties.
Research Topics and Scope:
The research focused on an aluminum die casting alloy with a nominal 3.0% magnesium content, intended for energy-absorbing automotive components. The scope was limited to the effects of four alloying elements: iron (Fe), silicon (Si), manganese (Mn), and titanium (Ti, as Ti-B). The study investigated how variations in these elements, within commercially relevant ranges, influenced the as-cast mechanical properties (UTS, YS, Elongation) of die-cast test bars. The study also considered the castability aspect by controlling elements like Zn, Ni, Cr, Cu, Sn, Ca, and Na at low levels and by considering the sludge factor.
6. Key Results:
Key Results:
The experiment successfully mapped a window of possible properties for die-cast test bars from an Al-3%Mg alloy.
- Elongation: Silicon (Si) and Iron (Fe) were found to be the main elements affecting elongation negatively (Figure 6). Increasing Si from 0.16% to 0.44% was predicted to lower ductility from 21% E. to 15% E. (Figure 7). Increasing Fe from 0.20% to 0.60% consistently lowered elongation by about 2% across the silicon range studied (Figure 8, Figure 9).
- 0.2% Yield Strength: Silicon (Si) and Manganese (Mn) were found to increase the 0.2% Yield Strength (Figure 10). Increasing Mn from 0.24% to 0.59% raised yield strength by approximately 12 MPa (Figure 12). Increasing Si from 0.16% to 0.44% raised yield strength by approximately 20 MPa (Figure 11). The influence of manganese was consistent over the range of silicon studied (Figure 13).
- Grain Refiner (Ti-B): The grain refiner (Titanium-Boron) was not found to improve the yield strength nor have any marked effect on the ductility of the test bars.
- Optimal Properties: To obtain optimum properties, low iron and manganese at a tolerable level were suggested. The silicon level could be tailored to meet component requirements for yield and elongation.
- Sludge Factor: Care must be taken with the manganese level due to sludging. An alloy with 0.2% Fe and 0.6% Mn would have a sludge factor of 1.4%, allowing a safety margin for chromium and temperature effects.
- Preferred Alloy: Alloy number 2 (nominal Si at 0.2%, Fe at 0.2%, Mn at 0.6%, and Ti as titanium-boron grain refiner) was identified as worth investigating further. The average as-cast properties for this alloy (from testing at three laboratories) were:
- Ultimate Tensile Strength: 229 MPa
- 0.2% Yield Strength: 121 MPa
- Elongation: 22%
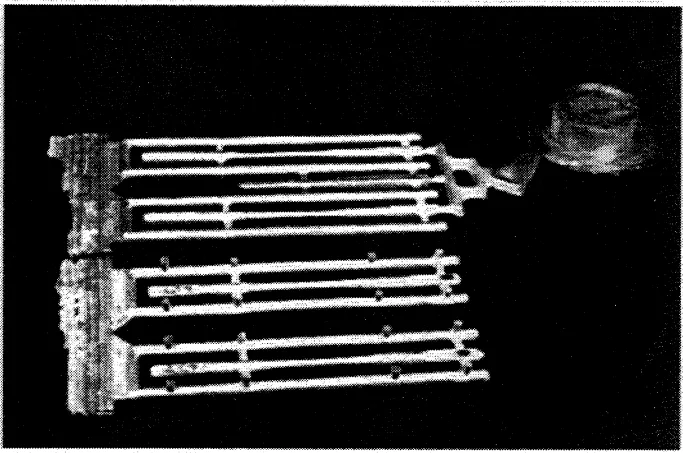
Figure Name List:
- Figure 1. Delphi Interior and Lighting Systems' magnesium alloy steering wheel component.
- Figure 2. Sludge formation as a factor of bath temperature.
- Table 1. Compositional range of current AA registered Al-Mg alloys (Note: The paper labels this as Table 1, but it is a table, not a figure. Included here as it's a visual data representation mentioned in the text.)
- Table 2. Fractional Factorial Design 24-1 for Experimental Model (Note: Table, not figure.)
- Figure 3. Simplified process flow sheet for remelt ingot—Alcan Recycling, Guelph Alloy Works.
- Figure 4. Schematic of Gibbs Vertical Vacuum High Pressure Die Casting Process. Vacuum started to evacuate die and lift metal to the shot chamber.
- Figure 5. Pressure die cast test bars, conforming to ASTM E8-92a.
- Table 3. Chemical composition of remelted alloys. (Note: Table, not figure.)
- Figure 6. Main elements affecting elongation.
- Table 4. Mechanical properties (Note: Table, not figure.)
- Figure 7. Effect of silicon on elongation, other elements adjusted.
- Figure 8. Effect of iron on elongation, other elements adjusted.
- Figure 9. Effect of silicon on elongation, with iron at 0.2% and 0.59%.
- Figure 10. Main element effects on 0.2% yield strength.
- Figure 11. Adjusted values of yield strength with increasing silicon content.
- Figure 12. Adjusted values of yield strength with increasing manganese content.
- Figure 13. Yield strength with silicon at high and low manganese.
7. Conclusion:
The Design of Experiment allowed for the evaluation of eight alloy variants of an Al-3%Mg base, providing insight into the effects of Si, Mn, Fe, and Ti-B on the mechanical properties of die-cast test bars. Silicon and manganese were found to be effective in increasing the yield strength. However, silicon and iron were observed to degrade elongation values. The titanium-boron grain refiner did not show a significant impact on yield strength or ductility in this study.
To achieve optimum properties, the study suggests that an alloy would require low iron content and manganese at a tolerable level, considering the risk of sludging. The silicon level can be adjusted to tailor the yield strength and elongation to meet specific component requirements.
Based on the experiment, alloy number 2, with nominal compositions of 0.2% Si, 0.2% Fe, 0.6% Mn, and Ti as a titanium-boron grain refiner, was identified as promising for further investigation. This alloy composition (with 0.2% Fe and 0.6% Mn) would have a sludge factor of 1.4%, providing a safety margin. The average as-cast properties obtained for alloy number 2 from testing at the three laboratories were an Ultimate Tensile Strength of 229 MPa, a 0.2% Yield Strength of 121 MPa, and an elongation of 22%.
8. References:
- [1] Registration Record of Aluminum Association Alloy Designations and Chemical Compositional Limits for Aluminum Alloys in the Form of Castings and Ingots, the Aluminum Association, Inc, Revised January 1989.
- [2] Aluminum and Aluminum Alloys, E.L. Rooy, ASM Metals Handbook, Ninth Edition, Volume 15, Casting, 1988.
- [3] Aluminum Alloys: Structure and Properties, L. F. Mondolfo, Butterworth (Publishers) Inc.
- [4] Study of Die Soldering in the Die Casting Process, B. Chamberlain, Alcan International Limited, internal report, K-IR-457-67-22-1, 1967.
- [5] Statistics for Experimenters, G.E.P. Box, W.G. Hunter and J.S. Hunter, John Wiley & Sons, published 1978.
- [6] ASTM E8-92a, Fig 18, Standard Test Methods of Tension Testing of Metallic Materials, Annual Book of ASTM Standards, Vol 03-01, American Society of Testing And Materials, Philadelphia, PA.
9. Copyright:
- This material is a paper by "Ron Stutsman, Barri Chamberlain, Mike Evans". Based on "The Design of an Experiment to Choose an Aluminum Die Casting Alloy for Energy Absorbing Automotive Components".
- Source of the paper: DOI URL: Not provided in the document. (SAE Paper 960159)
This material is summarized based on the above paper, and unauthorized use for commercial purposes is prohibited.
Copyright © 2025 CASTMAN. All rights reserved.