This introduction paper is based on the paper "Quality Evaluations of Induction Motor Rotors during Die Casting Process" published by "Journal of the Korea Academia-Industrial cooperation Society".
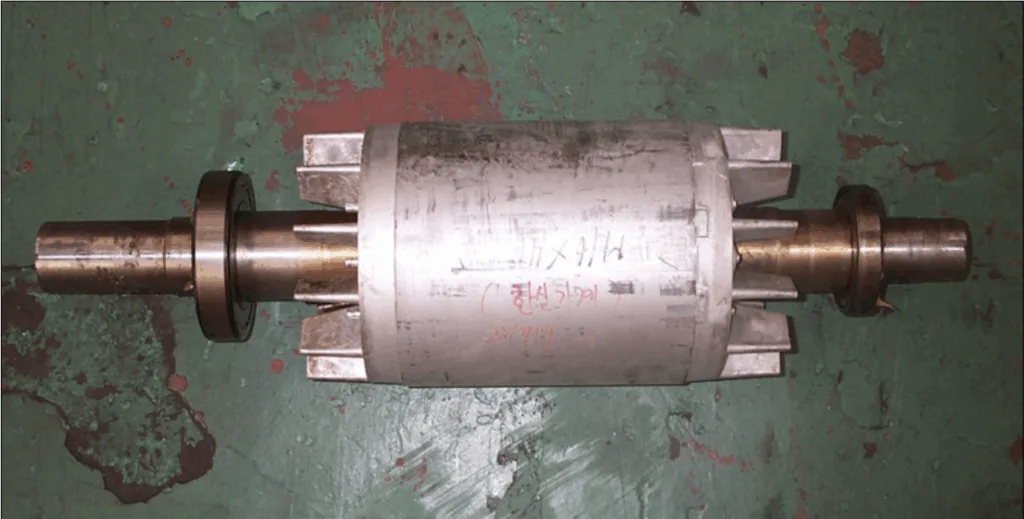
1. Overview:
- Title: Quality Evaluations of Induction Motor Rotors during Die Casting Process
- Author: Sang-Chul Park
- Year of publication: 2018
- Journal/academic society of publication: Journal of the Korea Academia-Industrial cooperation Society (Vol. 19, No. 10 pp. 115-120)
- Keywords: Induction Motor, Rotor, Die Casting, Rotor Core, Aluminum Cast, Filling Analysis
2. Abstract:
This study examined the cast quality of small-sized induction motor rotors during the die casting process. Numerical analyses with 3-dimensional half models were performed to investigate the filling patterns of aluminum molten metals into a mold after high-speed injections. The following were obtained from numerical analyses and experimental results. First, molten metals started to fill the lower end ring, then moved horizontally to fill the core slot and upper end ring, and finally stopped to fill the rotor core slot. Second, circulation of molten metals occurred at the lower end ring, resulting considerable porosity at the section of lower end ring from the experimental results. Third, further work for obtaining sound quality of rotor core cast is required to develop a new shape of the rotor core cast or improve the die casting conditions.
3. Introduction:
Induction motors are widely used in industry to generate mechanical power. The rotor is the component that rotates around the central axis. Rotors for induction motors are diverse in type depending on capacity and purpose, and are often manufactured by die casting molten aluminum into the slots of the rotor core in a short time [1]. Small induction motor rotors, in particular, are often produced using a side gate type die casting process. Recently, quality problems with the cast part have been reported, leading to reduced electrical efficiency and unbalancing issues during high-speed rotation, causing noise and requiring additional balancing work, which hinders productivity improvement. This study aims to evaluate the quality of the rotor end ring part under current die casting conditions using both analytical (simulation) and experimental methods.
4. Summary of the study:
Background of the research topic:
Small-sized induction motor rotors are commonly manufactured using the die casting process. However, quality issues in the cast aluminum parts have become a concern, potentially affecting motor performance (efficiency, noise, vibration due to unbalancing).
Status of previous research:
The paper acknowledges the general context of die casting [1] and the occurrence of defects in high-pressure die casting [2-4]. It highlights a reported problem in the specific application of die casting small induction motor rotors, suggesting a need for focused investigation into the quality under current production conditions.
Purpose of the study:
To evaluate the cast quality of small-sized induction motor rotors produced by die casting. Specifically, the study investigates the filling pattern of molten aluminum during the process and assesses the quality of the rotor end ring parts using numerical simulation and experimental validation.
Core study:
The core of the study involves performing numerical simulations using the AnyCasting software to analyze the filling process of molten aluminum into the rotor mold. A 3-dimensional half model was used, considering the geometry of the runner system, ingates, and the rotor core cast (excluding the steel core and shaft). The simulation analyzed the filling sequence and flow patterns at different fill percentages (10%, 20%, 40%, 60%) and within specific cross-sections of the cast. The simulation results, particularly regarding defect prediction in the lower end ring, were compared with experimental observations from sectioning an actual die-cast rotor.
5. Research Methodology
Research Design:
The study employed a combination of numerical simulation and experimental verification. Numerical analysis was used to predict the fluid flow behavior during mold filling, and experimental results from actual cast parts were used to validate the simulation findings.
Data Collection and Analysis Methods:
- Numerical Simulation:
- Software: AnyCasting (FVM-based) [5].
- Model: 3D half model of the rotor core cast including runner system and 3 side ingates (Fig. 4, Fig. 5). Shaft and rotor core were excluded.
- Boundary Conditions: Virtual die.
- Mesh: Approx. 16,000,000 cells.
- Process Parameters: Core length 230mm, mold material SKD 61, mold preheat 200°C, rotor core initial temp 25°C, cast injection temp 680°C, plunger speed max 4,500 mm/sec, cast-mold heat transfer coefficient 0.02cal/cm²·sec·°C, ambient temp 25°C.
- Analysis: Evaluation of filling patterns over time (Fig. 6) and flow characteristics within specific cross-sections (Section-1, Section-2, Section-3, Fig. 7, Fig. 8, Fig. 9, Fig. 10).
- Experimental Validation:
- Method: Sectioning the lower end ring of an actual die-cast rotor produced under the studied conditions.
- Analysis: Visual inspection of the sectioned surface to identify casting defects like porosity (Fig. 11).
Research Topics and Scope:
The research focused on the die casting process of a specific small-sized, 2-pole induction motor rotor. The scope included:
- Simulating the mold filling stage with molten aluminum using existing production parameters (side gate, high plunger speed).
- Analyzing the filling sequence and flow patterns, particularly in the upper and lower end rings and the rotor core slots.
- Predicting the formation of defects (porosity) based on flow simulation results (e.g., vortex formation).
- Verifying the predicted defects through experimental sectioning of the lower end ring.
6. Key Results:
Key Results:
- The filling sequence determined by simulation starts with the lower end ring, followed by horizontal movement of the melt filling the core slot and upper end ring, with the final filling occurring in the rotor core slot region.
- Simulation results indicated the formation of vortices in the molten metal flow within the lower end ring, particularly around the blade features. This suggested a high probability of air entrapment and subsequent porosity formation in this area. Analysis of different sections (Section-1, Section-2, Section-3) showed variations but consistently predicted issues in the lower end ring.
- Experimental validation through sectioning the lower end ring of an actual rotor (Fig. 11) confirmed the simulation predictions, revealing considerable porosity (numerous small and large pores) distributed across the section.
- The study concludes that further work, such as modifying the cast shape or adjusting die casting conditions, is necessary to achieve sound quality rotors.
Figure Name List:
- Fig. 1. Configuration of Induction Motor Rotor
- Fig. 2. Shape of Rotor Core
- Fig. 3. Schematic Diagram of Die Casting Equipment
- Fig. 4. Shape of Rotor Core Cast
- Fig. 5. Analysis Model of Rotor Core Cast
- Fig. 6. Filling Patterns of Cast Model (a) 10% (b) 20% (c) 40% (d) 60%
- Fig. 7. Evaluation Location of Cast Model (a) Section-1 (b) Section-2 (c) Section-3
- Fig. 8. Filling Patterns at Section-1 (a) 15% (b) 45% (c) 60% (d) 90%
- Fig. 9. Filling Patterns at Section-2 (a) 15% (b) 30% (c) 45% (c) 60%
- Fig. 10. Filling Patterns at Section-3 (a) 15% (b) 30% (c) 45% (d) 60%
- Fig. 11. Sectional View of Lower End Ring
7. Conclusion:
This study evaluated the quality of aluminum cast in small induction motor rotors during die casting using numerical analysis and experiments, leading to the following conclusions:
1) Filling analysis showed that molten metal first fills the lower end ring, then moves horizontally to fill the upper end ring and core slot, finally completing filling in the core slot area.
2) Analysis of the melt filling pattern indicated that vortex flow occurs in the lower end ring, predicting defect formation. Experimental results confirmed the presence of numerous defects in the cross-section of the lower end ring.
3) To manufacture rotors of good quality, further research is needed, such as modifying the cast shape or optimizing process conditions. This will be reported in future work.
8. References:
- [1] J. Campbell, "Complete Casting Handbook", Elsevier, 2011.
- [2] M. O. Durowoju, "Numerical Characterization of the Pores and the Determination of the Point Of Crack Initiation in Some Cast Aluminum Alloys", International Journal of Modern Engineering Research, Vol.3, No.2, pp.1229-1237, March, 2013.
- [3] R. Podprocká, J. Malik, D. Bolibruchová, "Defects in High Pressure Die Casting Process", Manufacturing Technology, Vol.15, No.4, pp.674-678, 2015.
- [4] B. G. Jeong, H. K. Kwon, "A Case Study on Developing Automotive Part(Housing) by Filling and Solidification Analysis", Journal of Society of Korea Industrial and System Engineering, Vol.38, No.1, pp.44-51, 2015. DOI: https://dx.doi.org/10.11627/jkise.2014.38.1.44
- [5] AnyCasting Co., Ltd., version 1.1
- [6] Y. L. Hsu, C. C. Yu, “Computer Simulation of Casting Process of Aluminium Wheels - A Case Study", Proceedings of the Institution of Mechanical Engineers, Part B: Journal of Engineering Manufacture, Vol.220, No.2, pp.203-211, 2006. DOI: https://dx.doi.org/10.1243/09544054JEM381
- [7] Y. Otsuka, "Experimental Verification and Accuracy Improvement of Gas Entrapment and Shrinkage Porosity Simulation in High Pressure Die Casting Process", Materials Transactions, Vol.55, No.1, pp.154-160, 2014. DOI: https://dx.doi.org/10.2320/matertrans.F-M2013835
9. Copyright:
- This material is a paper by "Sang-Chul Park". Based on "Quality Evaluations of Induction Motor Rotors during Die Casting Process".
- Source of the paper: https://doi.org/10.5762/KAIS.2018.19.10.115
This material is summarized based on the above paper, and unauthorized use for commercial purposes is prohibited.
Copyright © 2025 CASTMAN. All rights reserved.