This introduction paper is based on the paper "Anodization of cast aluminium alloys produced by different casting methods" published by "ARCHIVES of FOUNDRY ENGINEERING".
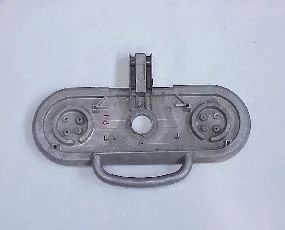
1. Overview:
- Title: Anodization of cast aluminium alloys produced by different casting methods
- Author: K. Labisz, L.A. Dobrzański, J. Konieczny
- Year of publication: 2008
- Journal/academic society of publication: ARCHIVES of FOUNDRY ENGINEERING (Published quarterly as the organ of the Foundry Commission of the Polish Academy of Sciences)
- Keywords: Aluminium cast alloys, Mechanical properties, Surface treatment, Alumina layer, Anodization
2. Abstract:
In this paper the usability of two casting methods, of sand and high pressure cast for the anodization of AlSi12 and AlSi9Cu3 aluminium cast alloys was investigated. With defined anodization parameters like electrolyte composition and temperature, current type and value a anodic alumina surface layer was produced. The quality, size and properties of the anodic layer was investigated after the anodization of the chosen aluminium cast alloys. The Alumina layer was observed used light microscope, also the mechanical properties were measured as well the abrasive wear test was made with using ABR-8251 equipment. The researches included analyze of the influence of chemical composition, geometry and roughness of anodic layer obtained on aluminum casts. Conducted investigations shows the areas of later researches, especially in the direction of the possible, next optimization anodization process of aluminum casting alloys, for example in the range of raising resistance on corrosion to achieve a suitable anodic surface layer on elements for increasing applications in the aggressive environment for example as materials on working building constructions, elements in electronics and construction parts in air and automotive industry.
3. Introduction:
The surface of aluminium parts naturally develops a thin Al2O3 layer. Anodization increases this layer's thickness to micrometers, enhancing resistance to environmental factors like salt water, acids, and mechanical influences. This process is common for corrosion protection, with standards like ISO 7599 and DIN 17611 defining properties. The use of aluminium alloys is growing across industries. Anodic layers serve protective and decorative functions on various products, including electronics, furniture, and automotive parts. Hard anodic layers are applied in aerospace and automotive industries. However, alloys with high copper content, like some investigated here, are more challenging to anodize due to corrosion susceptibility and potential issues like local burning or film cracking during the formation of thick porous oxides.
4. Summary of the study:
Background of the research topic:
Anodization is a crucial surface treatment for aluminium alloys, improving corrosion and wear resistance. The properties of the resulting anodic layer depend on the alloy composition, its manufacturing process (casting method), and the anodization parameters. Copper content in alloys can complicate the anodizing process.
Status of previous research:
Anodization is a well-established process with existing international standards and known applications. Previous studies have investigated the effects of alloy types, anodizing parameters (electrolyte, current, temperature), and the challenges associated with specific alloy compositions (e.g., high copper content) on the resulting anodic layer's properties and formation mechanisms [1-16].
Purpose of the study:
To investigate the usability of two different casting methods, sand casting and high pressure die casting, for the anodization of AlSi12 and AlSi9Cu3 aluminium cast alloys. The study aimed to examine the structure and thickness of the alumina layers formed and compare the influence of the casting method on the resulting anodic layer.
Core study:
Two aluminium alloys, EN AC-AlSi12(b) and EN AC-AlSi9Cu3(Fe), were produced using both high pressure casting and sand casting methods. These cast samples were then subjected to an anodization process under specifically defined parameters (H2SO4 electrolyte, controlled temperature and pulsating current). The resulting anodic alumina layers were characterized using light microscopy to assess structure and uniformity, and their thickness was measured. Abrasive wear resistance was evaluated using a standardized test (ISO 8251) by measuring mass loss, comparing anodized samples to unanodized ones.
5. Research Methodology
Research Design:
A comparative experimental study was conducted. Two common casting aluminium alloys (AlSi12, AlSi9Cu3) were prepared using two distinct casting methods (sand cast, high pressure cast). Samples from each group were anodized under identical, controlled conditions. The resulting surface layers were then analyzed and compared based on microstructure, thickness, and abrasive wear resistance. Unanodized samples served as a baseline for wear comparisons.
Data Collection and Analysis Methods:
- Material Preparation: Samples cut, mounted, ground, and polished using standard metallographic procedures.
- Anodization: Performed using H2SO4 electrolyte, specific temperature range (-4 to 2°C), and a defined pulsating current regime (Table 2).
- Microstructure Investigation: Light microscopy (Olympus BX60M) at 500-1000x magnification to observe the anodic layer structure and underlying alloy microstructure.
- Layer Thickness Measurement: Assessed from micrographs (Results presented in Fig. 6).
- Abrasive Wear Test: Conducted using an ABR-8251 tester according to ISO 8251 standard. Mass loss [mg] was measured after 400 steps under a 4.9N load (Table 3). Tests were replicated 5 times under controlled conditions (Table 4).
- Initial Surface Geometry: Mentioned analysis using MicroProf laser gauge but not detailed in results discussion.
Research Topics and Scope:
The research focused primarily on the influence of the casting method (sand vs. high pressure) on the anodizability and resulting properties (layer structure, thickness, uniformity, wear resistance) of AlSi12 and AlSi9Cu3 cast alloys. The scope was limited to the specific alloys, casting methods, and anodizing parameters detailed (Table 1 & 2).
6. Key Results:
Key Results:
- Anodic alumina layers were successfully produced on both AlSi12 and AlSi9Cu3 alloys cast by both high pressure and sand casting methods.
- Metallographic examination revealed no discontinuities in the anodic layers for any sample group (Fig. 7-12).
- The thickness of the anodic layer was significantly greater (approx. 5 times) on sand cast materials compared to high pressure cast materials for both alloys (Fig. 6).
- Layer uniformity varied: For pressure cast parts, AlSi12 yielded a more uniform (though thinner) layer than AlSi9Cu3. For sand cast parts, AlSi9Cu3 yielded a better uniformity (though thinner overall compared to sand cast AlSi12). The refined eutectic structure in AlSi12 was noted to give better uniformity.
- Anodization treatment decreased abrasive wear (mass loss) compared to unanodized samples (Table 5).
- The greatest improvement in wear resistance (approx. 50% reduction in mass loss) was observed for the anodized EN AC-AlSi9Cu3(Fe) alloy produced by sand casting. Other anodized samples showed mass loss reductions between 30% and 47%.
- Sand cast alloys generally exhibited lower mass loss (higher abrasive resistance) after anodization compared to pressure cast alloys.
- The combination of AlSi9Cu3 alloy with sand casting and AlSi12 alloy with pressure casting demonstrated the greatest abrasion resistance among the tested groups.
Figure Name List:
- Fig. 1. Scheme of the anodization process including the anodized part, electrolyte, power supply and the alumina surface layer.
- Fig. 2. Stages in the development of the alumina surface layer, a) barrier layer development, b) growth of small inhomogenities, c) continuously grow of pores, d) stabilization of the interpore distances (JPK Instruments AG, 2003).
- Fig. 3. Non anodized element made from the AC-AlSi12 aluminium alloy, produced by the Pressure Cast method
- Fig. 4. Anodized element made from the AC-AlSi9Cu3 aluminium alloy, produced by the Pressure Cast method
- Fig. 5. Overanodized element made from the AC-AlSi9Cu3 aluminium alloy, produced by the Pressure Cast method
- Fig. 6. Results of the anodic layer thickness measurement
- Fig. 7. Anodic alumina layer generated on the AlSi9Cu3 alloy, high pressure cast
- Fig. 8. Anodic alumina layer generated on the AlSi12 alloy, sand cast
- Fig. 9. Microstructure of the AlSi9Cu3 alloy, high pressure cast
- Fig. 10. Microstructure of the AlSi12 alloy, sand cast
- Fig. 11. Microstructure of the AlSi12 alloy, high pressure cast
- Fig. 12. Microstructure of the AlSi9Cu3 alloy, sand cast
7. Conclusion:
The study demonstrated that both sand casting and high pressure die casting methods are viable for producing AlSi12 and AlSi9Cu3 alloy parts suitable for anodization. The combination yielding the highest abrasion resistance was found to be AlSi9Cu3 alloy produced by sand mould casting, followed closely by AlSi12 alloy produced by pressure die casting. Conversely, AlSi12 sand cast and AlSi9Cu3 pressure cast parts showed lower abrasive resistance. Anodization significantly reduces weight loss due to abrasive wear compared to non-anodized alloys. The casting method influences the abrasive resistance of the anodized layer, with sand cast alloys generally showing greater resistance in this study.
8. References:
- [1] M.H. Robert, D. Delbin: Production of cellular A2011 alloy from semi-solid state, Journal of Achievements in Materials and Manufacturing Engineering, 17, (2006), pp. 137-140.
- [2] M. Wierzbińska, J. Sieniawski: Effect of morphology of eutectic silicon crystals on mechanical properties and cleavage fracture toughness of AlSi5Cu1 alloy, Journal of Achievements in Materials and Manufacturing Engineering, 14, (2006), pp. 31-36
- [3] Ι. Tsangaraki-Kaplanoglou, S. Theohari, Th. Dimogerontakis, Y. Wang, H. Kuo, S. Kia: Effect of alloy types on the anodizing process of aluminum, Surface & Coatings Technology, 200, (2006), pp. 2634 - 2641
- [4] K. P. Han, J. L. Fang: Decorative-protective coatings on aluminium, Surface and Coathings Technology, 88 (1996) pp. 178-182
- [5] H. Konno, K. Utaka, R. Furuichi: Two step of anodizing process of aluminium as a means of improving the chemical and physical properties of oxide films, Corrosion Science, 38, (1996), pp. 2247-2256
- [6] M. Maejima, K. Saruwatari, M. Takaya: Friction behaviour of anodic oxide film on aluminum impregnated with molybdenum sulfide compounds, Surface and Coatings Technology, 132 (2000), pp. 105-110
- [7] I. Vrublevsky, V. Parkoun, V. Sokol, J. Schreckenbach: Study of chemical dissolution of the barrier oxide layer of porous alumina films formed in oxalic acid using a re-anodizing technique, Applied Surface Science 236 (2004) pp. 270-277
- [8] J. Konieczny, L.A. Dobrzański, K. Labisz, J. Duszczyk: The influence of cast method and anodizing parameters on structure and layer thickness of aluminum alloys, Journal of Materials Processing Technology, 157-158 (2004), pp. 718-723
- [9] L.E. Fratila-Apachitei, J. Duszczyk, L. Katgerman: AlSi(Cu) anodic oxide layers formed in H2SO4 at low temperature using different current waveforms, Surface and Coatings Technology, 165, (2003), pp. 232-240
- [10] S.J. Garcia-Vergara, P. Skeldon, G.E. Thompson, H. Habazaki: Pore development during anodizing of Al-3.5 at.%W alloy in phosphoric acid, Surface & Coatings Technology, 201, (2007), pp. 9506-9511
- [11] M. Shahid, A.Q. Khan: Mechanism of film growth during anodizing of Al-alloy-8090/SiC metal matrix composite in sulphuric acid electrolyte, Journal of Materials Science, 32, (1997), pp. 3775-3781
- [12] T. Haga, H. Sakaguchi, H. Inui, H. Watari, S. Kumai, Aluminum alloy semisolid strip casting using an unequal diameter twin roll caster, Journal of Achievements in Materials and Manufacturing Engineering, 14, (2006), pp. 157-162
- [13] D. Djozan, M. Amir-Zehni, Anodizing of inner surface of long and small-bore aluminum tube, Surface and Coatings Technology, 173, 2003, pp. 185-191
- [14] L.E. Fratila-Apachitei, J. Duszczyk, L. Katgerman, Voltage transients and morphology of AlSi(Cu) anodic oxide layers formed in H2SO4 at low temperature, Surface and Coatings Technology, 157 (2002) pp. 80-92
- [15] J. Zhang, X. Zhao, Y. Zuo, J. Xiong, The bonding strength and corrosion resistance of aluminum alloy by anodizing treatment in a phosphoric acid modified boric acid/sulfuric acid bath, Surface & Coatings Technology, 202, 2008, pp. 3149-3156
- [16] T. Dimogerontakis, L. Kompotiatis, I. Kaplanoglou, oxygen evolution during the formation of barrier type anodic film on 2024-T3 aluminium alloy, Corrosion Science, 39, (1998), 1939-1951
9. Copyright:
- This material is a paper by "K. Labisz, L.A. Dobrzański, J. Konieczny". Based on "Anodization of cast aluminium alloys produced by different casting methods".
- Source of the paper: [Please insert DOI URL if available, otherwise state 'DOI Not Available']
This material is summarized based on the above paper, and unauthorized use for commercial purposes is prohibited.
Copyright © 2025 CASTMAN. All rights reserved.