This introduction paper is based on the paper "The Effect of Microstructural Features, Defects and Surface Quality on the Fatigue Performance in Al-Si-Mg Cast Alloys" published by "Jönköping University, School of Engineering, Dissertation Series No. 084".
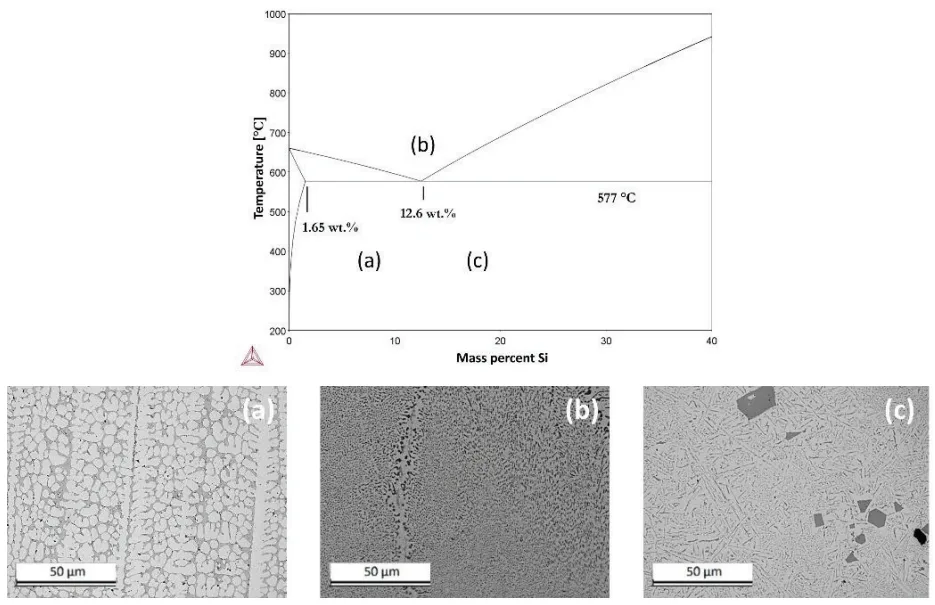
1. Overview:
- Title: The Effect of Microstructural Features, Defects and Surface Quality on the Fatigue Performance in Al-Si-Mg Cast Alloys
- Author: Toni Bogdanoff
- Year of publication: 2023
- Journal/academic society of publication: Jönköping University, School of Engineering, Dissertation Series No. 084
- Keywords: Al-Si-Mg cast alloys, fatigue performance, microstructural features, defects, surface quality, melt quality, copper addition, oxide bifilms, HIP, heat treatment, cast aluminium.
2. Abstract:
Global warming is driving industry to manufacture lighter components to reduce carbon dioxide (CO2) emissions. Promising candidates for achieving this are aluminium-silicon (Al-Si) cast alloys, which offer a high weight-to-strength ratio, excellent corrosion resistance, and good castability. However, understanding variations in the mechanical properties of these alloys is crucial to producing high-performance parts for critical applications. Defects and oxides are the primary reasons cast components in fatigue applications are rejected, as they negatively impact mechanical properties.
A comprehensive understanding of the correlation between fatigue performance and parameters such as the α-aluminium matrix, Al-Si eutectic, surface roughness, porosities, hydrogen content, oxides, and intermetallic phases in Al-Si castings has not been reached.
The research presented in this thesis used state-of-the-art experimental techniques to investigate the mechanical properties and crack-initiation and propagation behaviour of Al-Si-Mg cast alloy under cyclic loading. In-situ cyclic testing was conducted using scanning electron microscopy (SEM) combined with electron back-scattered diffraction (EBSD), digital image correlation (DIC), and focused ion beam (FIB) milling. These techniques enabled a comprehensive study of parameters affecting fatigue performance, including hydrogen content, surface roughness, oxides, and intermetallic phases. More specifically, we investigated the effect of melt quality, copper (Cu) content, oxide bifilms, surface quality, and porosity.
The increased Cu concentration in heat-treated Al-Si alloys increased the amount of intermetallic phases, which affected the cracking behaviour. Furthermore, oxide bifilms were detected at crack-initiation sites, even in regions far away from the highly strained areas. Si- and Iron (Fe)-rich intermetallics were observed to have precipitated on these bifilms. Due to their very small size, these oxides are generally not detected by non-destructive inspections, but affect mechanical properties because they appear to open at relatively low tensile stresses. Finally, Al-Si alloy casting skins showed an interesting effect in terms of improving fatigue performance, highlighting the negative effect of surface polishing for such alloys.
3. Introduction:
Reducing greenhouse gas emissions, particularly CO2, is a major global focus, driving industries like automotive to adopt lightweight materials [1]. Aluminium-silicon (Al-Si) cast alloys are prime candidates due to their high strength-to-weight ratio, cost efficiency, corrosion resistance, and castability [2, 3]. The use of recycled aluminium is increasing, offering significant energy savings compared to primary production [4-6]. While pure aluminium has limited strength, alloying, particularly with Si, Cu, and Mg, enhances mechanical properties through solid-solution and precipitation strengthening [7-12]. However, the high-cycle fatigue (HCF) performance of cast aluminium components remains a challenge, as fatigue accounts for approximately 90% of failures [13]. Defects such as oxide films (bifilms) and pores significantly reduce fatigue life [14-17], often limiting components to only 1% of their potential fatigue life [17]. While some defects like porosity can be detected [19], others like bifilms often remain hidden until failure [20, 21]. Surface conditions, including roughness, also critically influence fatigue initiation [16]. Standard laboratory fatigue tests on machined samples may not fully represent the behaviour of actual components with casting skins [22]. Therefore, a better understanding of how microstructural features, defects, and surface quality impact the mechanical performance, especially fatigue, of cast Al-Si alloys is crucial for optimizing components for demanding applications.
4. Summary of the study:
Background of the research topic:
The need for lightweight components to reduce CO2 emissions drives the use of Al-Si cast alloys in various industries, especially automotive [1, 2]. These alloys offer advantageous properties like high strength-to-weight ratio and good castability [3]. However, their application, particularly in fatigue-critical parts, is often limited by inherent microstructural features and defects.
Status of previous research:
Fatigue failure is a major concern for cast Al components [13]. Defects like porosities and oxide bifilms, along with surface roughness, are known to significantly degrade fatigue performance [14-17, 22]. While much research exists, a comprehensive understanding of the complex interplay between the α-aluminium matrix, Al-Si eutectic, various defects (porosity, oxides), intermetallic phases, hydrogen content, and surface roughness on fatigue life is still lacking [24]. Conflicting results and gaps exist in the literature, particularly regarding the role of surface roughness and defects originating from the melt state [24].
Purpose of the study:
The primary aim of this research was to investigate and understand the influence of various microstructural features, defects (including oxides/bifilms, porosity), melt quality parameters (hydrogen content), alloying additions (specifically Copper), and surface quality (roughness, casting skin) on the mechanical properties, particularly the fatigue performance (crack initiation and propagation), of Al-Si-Mg based cast alloys [25, 28]. The goal was to provide knowledge to optimize these alloys for high-performance applications and potentially reduce energy consumption in production.
Core study:
The research focused on several key aspects influencing the fatigue performance of Al-Si-Mg and Al-Si-Mg-Cu cast alloys:
- Melt Quality: Assessing the impact of melt handling and treatments (like rotary degassing) in foundry production on the final mechanical properties, using techniques like RPT and tensile testing to reveal both visible (pores) and hidden (bifilms) damage (Supplements I, II).
- Role of Copper: Investigating how varying Cu content (0 to 3 wt.%) affects fatigue crack initiation and propagation mechanisms in both as-cast and heat-treated conditions, correlating this with changes in microstructure (intermetallic phases like Q-phase, θ-phase) and matrix properties (Supplements IV, V).
- Hidden Damage (Oxide Bifilms): Characterizing the nature and effect of inherent oxide bifilms, often termed 'hidden damage', on local strain concentration and fracture behaviour using DIC, SEM, FIB-tomography, and STEM-EDS. Investigating the role of HIP in mitigating these defects (Supplements III, VI, VII).
- Surface Quality and Defect Size: Evaluating the combined effects of surface condition (as-cast skin vs. machined/polished) and internal defect characteristics (pore size distribution influenced by hydrogen content) on the fatigue life of Al-Si-Cu-Mg castings (Supplement VIII).
5. Research Methodology
Research Design:
The research employed an experimental approach based on a positivistic perspective and deductive reasoning [132, 133]. Experiments were conducted on both laboratory scales under controlled conditions and in full-scale industrial foundry settings (HPDC and sand casting). Standardized testing procedures (ISO, ASTM) were followed where applicable, with modifications noted [25]. The design aimed to isolate and study the effects of independent variables (e.g., Cu content, surface condition, hydrogen level, processing steps) on dependent variables (mechanical properties, fatigue life, crack behaviour) [26, 27].
Data Collection and Analysis Methods:
A range of techniques were utilized:
- Material Preparation: Casting via HPDC, sand casting (coated/uncoated moulds), and directional solidification (Bridgman furnace) [29-33]. Post-casting treatments included Hot Isostatic Pressing (HIP) and various T6-like heat treatment cycles (solution treatment, quenching, ageing) [38, 50].
- Melt Quality Assessment: Reduced Pressure Test (RPT), HYCAL hydrogen analysis, Optical Emission Spectroscopy (OES) for chemical composition, Spiral fluidity test, Density measurements (Archimedes principle) [35, 45-49].
- Microstructural Characterisation: Optical Microscopy (OM), Scanning Electron Microscopy (SEM) with Energy Dispersive Spectrometry (EDS), Wavelength Dispersive Spectroscopy (WDS), Electron Backscatter Diffraction (EBSD) for grain size/orientation, Focused Ion Beam (FIB) milling for cross-sectioning, 3D tomography, and Scanning Transmission Electron Microscopy (STEM) sample preparation [39-41]. Quantitative analysis included SDAS, grain size, particle size/distribution (e.g., 3NN distance), phase fractions, and defect characterization.
- Mechanical Testing: Tensile testing (ST, σY, eF) according to ISO 6892-1, Axial fatigue testing (R=-1, 50 Hz) using staircase method (ISO 12107) and for S-N curve generation [43].
- Crack Initiation/Propagation Studies: In-situ cyclic fatigue testing within an SEM using miniature compact-tension samples, Digital Image Correlation (DIC) using MatchID software (2D for micro-scale, 3D Stereo DIC for macro-scale) to map strain fields (Von Mises strain) [41, 43-44, 53-56].
- Defect Analysis: Computed Tomography (CT) scanning, fracture surface analysis (fractography) using SEM [62, 71].
- Statistical Analysis: Weibull distribution analysis for elongation (eF), quality index (QT), and fatigue life (Nf), Lognormal distribution analysis for pore size (deq), Basquin law parameters estimation, Anderson-Darling goodness-of-fit tests, linear regression [59, 64, 91, 97, 102, 104, 106].
Research Topics and Scope:
The research addressed four main questions (RQ1-RQ4) focusing on:
- RQ1: Influence of the production process (ingot to final component, including melt handling and degassing) on mechanical properties of cast Al-Si components, particularly using recycled alloys. Studied EN-AC 46000 in HPDC.
- RQ2: Effect of Cu addition (0-3 wt.%) on fatigue crack initiation and propagation in as-cast and heat-treated Al-Si-Mg alloys. Studied modified Al7SiMg cast via Bridgman furnace.
- RQ3: Identification, characterization, and impact of hidden damage (oxide bifilms) originating from the molten state on mechanical properties. Studied EN-AB 42000 (sand-cast), EN-AC 46000 (HPDC), C355 (Bridgman). Investigated HIP effects.
- RQ4: Combined effects of surface roughness (casting skin vs. machined/polished) and internal defects (porosity linked to hydrogen) on fatigue performance of Al-Si castings. Studied Al7Si3CuMg sand-cast alloy.
6. Key Results:
Key Results:
- Melt Quality & Degassing: Assessing melt quality requires more than RPT; tensile testing, especially elongation (eF) analysed with Weibull statistics, reveals 'hidden' entrainment damage from melt handling (transfer steps) [Supplement I]. Rotary degassing in the studied industrial case (EN-AC 46000) reduced visible porosity in RPT samples but did not improve, and potentially worsened, the actual mechanical properties (eF, QT) of the final casting due to breaking down existing coarse bifilms into finer ones without effective removal [Supplement I, II]. Degassing eliminated the Weibull mixture distribution observed in non-degassed samples but shifted the single distribution towards lower quality [Supplement II].
- Effect of Copper: Increasing Cu content (0 to 3.2 wt.%) in Al7SiMg alloys increased yield strength (σY) and tensile strength (ST) in both as-cast and heat-treated conditions, but significantly reduced ductility (eF), especially in the as-cast state due to brittle Cu-rich intermetallic phases (Q-Al5Mg8Cu2Si6, θ-Al2Cu) [Supplement IV, V]. Heat treatment improved strength further and mitigated the drop in ductility compared to as-cast. Crack initiation shifted from slip bands/Si particles (low Cu) to eutectic regions/Cu-rich phases (high Cu) in as-cast. In heat-treated alloys, crack initiation occurred in primary dendrites (low Cu), shifting to interdendritic regions and grain boundaries (high Cu). Crack propagation paths became more tortuous and shifted from trans-dendritic towards interdendritic/intergranular with increasing Cu content and matrix strengthening. Higher Cu content led to more secondary cracking during fatigue, particularly in heat-treated conditions [Supplement V, VII].
- Hidden Damage (Oxide Bifilms): Oxide bifilms, formed during melt handling and casting, act as significant 'hidden' defects. DIC revealed localized strain concentrations associated with these bifilms, even far from geometric stress raisers [Supplement VI]. FIB/STEM-EDS analysis confirmed these cracks contained aluminium oxide layers, indicating they were pre-existing bifilms that opened under load [Supplement VI, VII]. These bifilms act as nucleation sites for intermetallic phases (e.g., Al5FeSi) and Si particles [Supplement VII]. HIP effectively closed gas porosity but did not fully heal or eliminate these oxide bifilms, which could still open during subsequent fatigue loading [Supplement III, VII]. Damage observed in castings should be differentiated between entrainment damage (bifilms from liquid state) and mechanical damage (from service loading) [Supplement VII].
- Surface Quality & Porosity: Contrary to common assumptions, the presence of the as-cast surface skin significantly improved fatigue life compared to machined and polished (PS) surfaces for sand-cast Al-Si-Cu-Mg alloy [Supplement VIII]. Polishing removed the skin, exposing subsurface defects (pores/bifilms) directly to the surface, thereby reducing or eliminating the crack initiation phase and drastically lowering fatigue life. Fatigue failure initiated from subsurface defects (pores/imperfections near the skin) in as-cast samples, but directly from surface-exposed defects in polished samples. Increased hydrogen content led to larger pores and higher porosity fraction, resulting in wider fatigue life distributions (lower Weibull modulus M), especially for polished samples, but had less impact on the mean fatigue life for rough as-cast surfaces. The interaction between surface quality and pore size distribution is complex. Existing fatigue life prediction models (e.g., Juvinall) require modification to account for the beneficial effect of casting skin [Supplement VIII].
Figure Name List:
- Figure 1. Al-Si phase diagrams: a) hypoeutectic, b) eutectic, and c) hypereutectic microstructures.
- Figure 3. Entrainment of surface oxides [79].
- Figure 4. Hydrogen solubility in pure aluminium and aluminium alloys [42].
- Figure 5. a) Impurity-induced twinning [97]; b) restricted TPRE growth [98].
- Figure 6. The stress-strain curve of an as-cast Al7SiMg alloy, with emphasis placed on the essential parameters used in the research presented in this thesis.
- Figure 7. Overview of the research methodology.
- Figure 8. a) Cylindrical rods (length 150 mm and diameter 9 mm). b) schematic illustration of the Bridgman furnace; c) stair casting geometry (dimensions in mm).
- Figure 9. The geometry of the casting in the sand mould.
- Figure 10. The production process used in the HPDC plant.
- Figure 11. a) Schematic diagram of the tensile testing sample; b) a sample exposed to the HIP process and heat treatment.
- Figure 12. a) Dimensions of the compact-tension sample in mm; b) miniature stage for in-situ cyclic testing; c) FOV of the compact-tension sample.
- Figure 13. Tensile- and fatigue-testing sample geometry.
- Figure 14. The cross-sections of the RPT samples at different stages of production.
- Figure 15. The Weibull distributions of elongation in the different stages of production.
- Figure 16. Cross-sections of RPT samples taken at different stages of the production process, with and without degassing.
- Figure 17. The Weibull distributions of the structural quality of the two production routes.
- Figure 18. (a) Alloy Cu 0 in as-cast condition, b) Alloy Cu 0 in heat-condition.
- Figure 19. Three-nearest-neighbour (3NN) distances between particles: a) Si particles; b) Q-phases. The error bars represent the standard deviation.
- Figure 20. Beginning of crack initiation in as-cast condition: a) Alloy Cu 0; b) Alloy Cu 1.5.
- Figure 21. Crack propagation in all heat-treated alloys, imaged using a combination of EBSD and DIC: a–b) Alloy Cu 0; c–d) Alloy Cu 0.5; e–f) Alloy Cu 1.5; g–h) Alloy Cu 3.0. The yellow dashed lines represent grain boundaries, superimposed from EBSD, and the red arrows point to the initiation sites. The colour bar represents the von Mises equivalent strain, and is valid for all frames.
- Figure 22. Crack propagation in all as-cast alloys, imaged using a combination of EBSD and DIC: a) Alloy Cu 0; b) Alloy Cu 0.5; c) Alloy Cu 1.5; d) Alloy Cu 3.0. The yellow dashed lines represent grain boundaries, superimposed from EBSD. The final fracture, shown as a black dashed line in the picture, was manually added. The colour bar represents the von Mises equivalent strain.
- Figure 23. Development of slip bands during the cycling testing of alloys with different Cu contents: a) Alloy Cu 0, at the crack edge; b) Alloy Cu 0, 150 µm from the crack edge; c) Alloy Cu 1.5, at the crack edge, d) Alloy Cu 1.5, 150 µm from the crack edge.
- Figure 24. Development of secondary cracks (indicated by arrows) in heat-treated Alloy Cu 3.0 after a) 825 cycles; b) 925 cycles. c–d) magnified micrographs of the secondary cracks visible in b).
- Figure 25. FIB milling was used to investigate the material around the crack in heat-treated alloys. a) Alloy Cu 0, test stopped at 1253 cycles; b) and c) show related sections. d) Alloy Cu 3.0, test stopped at 640 cycles; e) and f) show related sections. The black arrows point to Fe-rich phases, the white arrows point to superficial cracks, and the red arrows point to the crack coming from underneath.
- Figure 26. Three-dimensional reconstruction of the FIB sections of cracks in heat-treated alloys. a) FIB section of Alloy Cu 0, test stopped at 1253 cycles, and b) three-dimensional reconstruction. c) FIB section of Alloy 3.0 Cu, test stopped at 640 cycles, and d) three-dimensional reconstruction. The red arrows show the cracks, and the blue arrows indicate the intermetallic phases.
- Figure 27. Microstructures of Al7SiMg alloy: (a) as-cast condition, 16 mm thickness, (b) as-cast condition, 32 mm thickness. The red squares highlight a magnified area. The red ovals highlight the inhomogeneous microstructure in the 32 mm-thick sample.
- Figure 28. Microstructures of the Al7SiMg alloy: (a) heat-treated condition, 16 mm thickness; (b) heat-treated condition, 32 mm thickness. The red squares highlight a magnified area.
- Figure 29. CT scan of the material in as-cast condition, showing the porosities (blue); having been HIPped (red); and having been heat-treated (green). a) 16 mm, b) 32 mm.
- Figure 30. Crack propagation in the HIPped and heat-treated conditions. a–c) the 16 mm sample, showing initiation and propagation; d–f) the 32 mm sample, showing cracks and evaluation of crack propagation.
- Figure 31. Full-field distributions of von Mises equivalent strain in a sample A under a load of (a) 11.9 kN and (b) 15.4 kN.
- Figure 32. (a) Sample A after fracture. The red circle indicates the location of the strain concentration seen in Figure 31b. (b), which is an SEM image of the oxide film found in the strain-concentration area. (c) Increased magnification of the oxide draped over the microstructure.
- Figure 33. Stress-strain curve throughout tensile testing of sample A for both the strain concentration and a symmetry reference point.
- Figure 34. (a) DIC strain field of sample B under a load of 15.9 kN just before fracture. (b) Close-up image of the upper strain concentration with an optical microscope after failure. (c) Visible crack on the sample surface after paint removal in the SEM.
- Figure 35. (a) Location of the lamella in front of the crack. (b) Extraction of the lamella. (c) STEM-EDS map of oxygen distribution in the lamella, which revealed the oxide film inside the crack.
- Figure 36. a) The FOV (300 × 300 μm) had no visible cracks after 100 cycles. b) cracks outside the FOV after 100 cycles.
- Figure 37. a) After 200 cycles, the cracks showed no continued propagation. (b) A crack was initiated at the notch after 550 cycles.
- Figure 38. a) Two cracked phases perpendicular to the loading direction. (b) BSE image of the trenching of the lamella. (c) BSE image of the 1.2 μm lamella before lifting.
- Figure 39. a) BSE, b) STEM, c) HADF, d) DF images of the lamella. The arrow points to the observed line around the open crack.
- Figure 40. a) SEM image of a crack. b) STEM-EDS image of the same crack, showing the intermetallic phases around it.
- Figure 41. a) STEM-EDS measurement of oxygen in the crack. b) EDS line scan results from points 1 to 51.
- Figure 42. Three-dimensional scans of a 900 × 900 µm area of as-cast components a) without coating (rough surface) and b) with coating (fine surface).
- Figure 43. The investigated surface conditions: a) PS, b) FS, and c) RS.
- Figure 44. Microstructure of the cast material, showing the aluminium dendrites, Si particles, and Cu- and Fe-rich phases.
- Figure 45. a) The microstructure of the sand-cast material with low hydrogen content; b) an enlarged view of the area highlighted by a red square in (a), showing oxides in the vicinity of the porosity; c) a sample with high hydrogen content, where two distinct pore sizes are evident.
- Figure 46. The probability density functions of the pore size distributions for the LH and HH conditions.
- Figure 47. Wöhler curves for a) LH and b) HH samples.
- Figure 48. Fatigue-life distributions for (a) LH and (b) HH samples with different surface conditions.
- Figure 49. a) The crack initiation point in the fracture surface of an LH sample with a casting skin. The red arrow is pointing to the casting skin. b) The crack initiation point in the fracture surface in the PS sample, at a defect located at the surface.
- Figure 50. The probability density functions of Weibull distributions for (a) samples with casting skins and (b) MS and PS samples.
7. Conclusion:
This research investigated microstructural features, defects, and surface quality effects on Al-Si-Mg cast alloy fatigue performance. Key conclusions are:
- Melt Quality: Complete melt quality assessment requires both RPT and tensile testing to reveal hidden damage. Rotary degassing may not improve properties if the melt is initially damaged and can eliminate Weibull mixture distributions without improving mechanical performance.
- Role of Copper: Increasing Cu content enhances strength (σY, ST) but reduces ductility (eF), especially as-cast. It increases intermetallic phases, altering crack initiation/propagation paths and increasing secondary cracking, particularly after heat treatment.
- Hidden Damage: Oxide bifilms are critical defects originating from the melt, acting as nucleation sites and opening under tensile stress. DIC and STEM-EDS confirmed their presence and impact. HIP closes pores but may not fully heal bifilms. Distinguishing entrainment damage from mechanical damage is crucial.
- Surface Quality & Defect Size: Casting skin significantly improves fatigue life compared to polished surfaces by acting as a barrier to subsurface defects and delaying/preventing crack initiation from surface-exposed defects. Polishing drastically reduces fatigue life. Increased porosity (from higher H) primarily affects fatigue life variability, interacting complexly with surface condition. Designing components with minimal machining benefits fatigue performance.
8. References:
- [1] N. Hooftman, M. Messagie, J. Van Mierlo, T. Coosemans, A review of the European passenger car regulations–Real driving emissions vs local air quality, Renewable and Sustainable Energy Reviews 86 (2018) 1-21.
- [2] A.C. Serrenho, J.B. Norman, J.M. Allwood, The impact of reducing car weight on global emissions: the future fleet in Great Britain, Philosophical Transactions of the Royal Society A: Mathematical, Physical and Engineering Sciences 375(2095) (2017) 20160364.
- [3] A.I. Taub, A.A. Luo, Advanced lightweight materials and manufacturing processes for automotive applications, Mrs Bulletin 40(12) (2015) 1045-1054.
- [4] E. Balomenos, D. Panias, I.J.M.P. Paspaliaris, E.M. Review, Energy and exergy analysis of the primary aluminum production processes: a review on current and future sustainability, 32(2) (2011) 69-89.
- [5] I. Polmear, D. StJohn, J.-F. Nie, M. Qian, Light alloys: metallurgy of the light metals, Butterworth-Heinemann2017.
- [6] C. Jirang, H.J.J.T.o.N.M.S.o.C. Roven, Recycling of automotive aluminum, 20(11) (2010) 2057-2063.
- [7] S. Seifeddine, E. Sjölander, T. Bogdanoff, On the role of copper and cooling rates on the microstructure, defect formations and mechanical properties of Al-Si-Mg alloys, (2013).
- [8] C. Caceres, C. Davidson, J. Griffiths, Q. Wang, The effect of Mg on the microstructure and mechanical behavior of Al-Si-Mg casting alloys, Metallurgical and materials transactions A 30(10) (1999) 2611-2618.
- [9] S. Shabestari, H. Moemeni, Effect of copper and solidification conditions on the microstructure and mechanical properties of Al–Si–Mg alloys, Journal of Materials Processing Technology 153 (2004) 193-198.
- [10] M.T. Di Giovanni, E.A. Mørtsell, T. Saito, S. Akhtar, M. Di Sabatino, Y. Li, E. Cerri, Influence of Cu addition on the heat treatment response of A356 foundry alloy, Materials Today Communications 19 (2019) 342-348.
- [11] Y. Zheng, W. Xiao, S. Ge, W. Zhao, S. Hanada, C. Ma, Effects of Cu content and Cu/Mg ratio on the microstructure and mechanical properties of Al–Si–Cu–Mg alloys, Journal of Alloys and Compounds 649 (2015) 291-296.
- [12] S. Morin, E. Elgallad, H. Doty, S. Valtierra, F.J.A.i.M.S. Samuel, Engineering, Effect of Mg content and heat treatment on the mechanical properties of low pressure Die-Cast 380 alloy, 2016 (2016).
- [13] U. Krupp, Fatigue crack propagation in metals and alloys: microstructural aspects and modelling concepts, John Wiley & Sons2007.
- [14] I. Serrano-Munoz, J.-Y. Buffiere, R. Mokso, C. Verdu, Y. Nadot, Location, location & size: defects close to surfaces dominate fatigue crack initiation, Scientific reports 7(1) (2017) 45239.
- [15] I. Serrano-Munoz, J.-Y. Buffiere, C. Verdu, Y. Gaillard, P. Mu, Y. Nadot, Influence of surface and internal casting defects on the fatigue behaviour of A357-T6 cast aluminium alloy, International Journal of Fatigue 82 (2016) 361-370.
- [16] H. Jiang, P. Bowen, J.J.J.o.m.s. Knott, Fatigue performance of a cast aluminium alloy Al-7Si-Mg with surface defects, 34(4) (1999) 719-725.
- [17] C. Nyahumwa, Ν.R. Green, J. Campbell, The concept of the fatigue potential of cast alloys, Journal of the Mechanical Behavior of Materials 9(4) (1998) 227-236.
- [19] O. Lashkari, L. Yao, S. Cockcroft, D. Maijer, X-ray microtomographic characterization of porosity in aluminum alloy A356, Metallurgical and Materials Transactions A 40 (2009) 991-999.
- [20] Z. Ma, A. Samuel, F. Samuel, H. Doty, S. Valtierra, A study of tensile properties in Al–Si–Cu and Al–Si–Mg alloys: Effect of β-iron intermetallics and porosity, Materials Science and Engineering: A 490(1-2) (2008) 36-51.
- [21] J. Campbell, M. Tiryakioğlu, Fatigue Failure in Engineered Components and How It Can Be Eliminated: Case Studies on the Influence of Bifilms, Metals 12(8) (2022) 1320.
- [22] M.R. Bayoumi, A. Abdellatif, Effect of surface finish on fatigue strength, Engineering Fracture Mechanics 51(5) (1995) 861-870.
- [24] A.E. Jarfors, A comparison between semisolid casting methods for aluminium alloys, Metals 10(10) (2020) 1368.
- [25] J. Olofsson, I.L. Svensson, Incorporating predicted local mechanical behaviour of cast components into finite element simulations, Materials & Design 34 (2012) 494-500.
- [26] M. Tiryakioglu, D. Askeland, C. Ramsay, Relationship between metal fluidity and optimum pouring time: a literature review, TRANSACTIONS AMERICAN FOUNDRYMENS SOCIETY (1993) 685-685.
- [27] J. Olofsson, I.L. Svensson, P. Lava, D. Debruyne, Characterisation and investigation of local variations in mechanical behaviour in cast aluminium using gradient solidification, Digital Image Correlation and finite element simulation, Materials & Design 56 (2014) 755-762.
- [28] D. Dwivedi, R. Sharma, A. Kumar, Influence of silicon content and heat treatment parameters on mechanical properties of cast Al–Si–Mg alloys, International Journal of Cast Metals Research 19(5) (2006) 275-282.
- [29] S. Roy, L.F. Allard, A. Rodriguez, W.D. Porter, A. Shyam, Comparative evaluation of cast aluminum alloys for automotive cylinder heads: Part II—mechanical and thermal properties, Metallurgical and Materials Transactions A 48(5) (2017) 2543-2562.
- [30] N. Tenekedjiev, J. Gruzleski, Hypereutectic aluminium-silicon casting alloys—a review, Cast Metals 3(2) (1990) 96-105.
- [31] O. Atasoy, F. Yilmaz, R. Elliott, Growth structures in aluminium-silicon alloys I. The coupled zone, Journal of crystal growth 66(1) (1984) 137-146.
- [32] A. Dahle, K. Nogita, S. McDonald, J. Zindel, L. Hogan, Eutectic nucleation and growth in hypoeutectic Al-Si alloys at different strontium levels, Metallurgical and Materials Transactions A 32(4) (2001) 949-960.
- [33] A. Samuel, F. Samuel, Effect of alloying elements and dendrite arm spacing on the microstructure and hardness of an Al-Si-Cu-Mg-Fe-Mn (380) aluminium die-casting alloy, Journal of Materials Science 30(7) (1995) 1698-1708.
- [35] E. Sjölander, S. Seifeddine, The heat treatment of Al–Si–Cu–Mg casting alloys, Journal of Materials Processing Technology 210(10) (2010) 1249-1259.
- [38] S.J.M.S. Shabestari, E. A, The effect of iron and manganese on the formation of intermetallic compounds in aluminum–silicon alloys, 383(2) (2004) 289-298.
- [39] C.M. Dinnis, J.A. Taylor, A.K.J.S.m. Dahle, As-cast morphology of iron-intermetallics in Al–Si foundry alloys, 53(8) (2005) 955-958.
- [40] A. Dahle, K. Nogita, S. McDonald, C. Dinnis, L. Lu, Eutectic modification and microstructure development in Al–Si Alloys, Materials Science and Engineering: A 413 (2005) 243-248.
- [41] A. Greer, Overview: Application of heterogeneous nucleation in grain-refining of metals, The Journal of Chemical Physics 145(21) (2016) 211704.
- [42] J. Campbell, Castings, Butterworth-Heinemann2003.
- [43] J. Campbell, Entrainment defects, Materials science and technology 22(2) (2006) 127-145.
- [45] M. Divandari, J. Campbell, Mechanisms of bubble trail formation in castings, Trans. AFS 109 (2001) 433-442.
- [46] G. Gyarmati, G. Fegyverneki, M. Tokár, T. Mende, The effects of rotary degassing treatments on the melt quality of an Al–Si casting alloy, International Journal of Metalcasting 15(1) (2021) 141-151.
- [48] M.B. Đurđević, Z. Odanović, J. Pavlović-Krstić, Melt quality control at aluminum casting plants, Metalurgija 16(1) (2010) 63-76.
- [49] M. Riestra, A. Bjurenstedt, T. Bogdanoff, E. Ghassemali, S. Seifeddine, Complexities in the Assessment of Melt Quality, International Journal of Metalcasting 12(3) (2018) 441-448.
- [50] M. Uludağ, R. Çetin, D. Dispinar, M.J.M. Tiryakioğlu, Characterization of the effect of melt treatments on melt quality in Al-7wt% Si-Mg alloys, 7(5) (2017) 157.
- [52] G. Eisaabadi, M. Tiryakioğlu, P. Davami, S.-K. Kim, Y.O. Yoon, G.-Y. Yeom, N.-S. Kim, The effect of remelting on the melt and casting quality in Al–7% Si–Mg castings, Materials Science and Engineering: A 605 (2014) 203-209.
- [59] G. Timelli, F. Bonollo, Fluidity of aluminium die castings alloy, International Journal of Cast Metals Research 20(6) (2007) 304-311.
- [60] M. Di Sabatino, L. Arnberg, A review on the fluidity of Al based alloys, Metallurgical Science and Tecnology 22(1) (2004).
- [61] A. Dahle, P. Tøndel, C. Paradies, L. Arnberg, Effect of grain refinement on the fluidity of two commercial Al-Si foundry alloys, Metallurgical and Materials Transactions A 27(8) (1996) 2305-2313.
- [62] A. Rotella, Y. Nadot, M. Piellard, R. Augustin, M. Fleuriot, Fatigue limit of a cast Al-Si-Mg alloy (A357-T6) with natural casting shrinkages using ASTM standard X-Ray inspection, International Journal of Fatigue (2018).
- [64] K. Fisher, W. Kurz, Fundamentals of solidification, Trans Tech Publications (1986).
- [65] Y. Cho, H.-C. Lee, K. Oh, A. Dahle, Effect of strontium and phosphorus on eutectic Al-Si nucleation and formation of β-Al 5 FeSi in hypoeutectic Al-Si foundry alloys, Metallurgical and Materials Transactions A 39(10) (2008) 2435-2448.
- [66] E.A. Mørtsell, F. Qian, C.D. Marioara, Y. Li, Precipitation in an A356 foundry alloy with Cu additions-A transmission electron microscopy study, Journal of Alloys and Compounds 785 (2019) 1106-1114.
- [67] T. Saito, E.A. Mørtsell, S. Wenner, C.D. Marioara, S.J. Andersen, J. Friis, K. Matsuda, R. Holmestad, Atomic structures of precipitates in Al–Mg–Si alloys with small additions of other elements, Adv. Eng. Mater. 20(7) (2018) 1800125.
- [68] S. Roy, L.F. Allard, A. Rodriguez, T.R. Watkins, A. Shyam, Comparative Evaluation of Cast Aluminum Alloys for Automotive Cylinder Heads: Part I—Microstructure Evolution, Metallurgical and Materials Transactions A (2017) 1-14.
- [69] R. Taghiabadi, A. Fayegh, A. Pakbin, M. Nazari, M. Ghoncheh, Quality index and hot tearing susceptibility of Al–7Si–0.35 Mg–xCu alloys, Transactions of Nonferrous Metals Society of China 28(7) (2018) 1275-1286.
- [70] M. Avalle, G. Belingardi, M.P. Cavatorta, R. Doglione, Casting defects and fatigue strength of a die cast aluminium alloy: a comparison between standard specimens and production components, International journal of Fatigue 24(1) (2002) 1-9.
- [71] F. Guerra, A. Bedolla-Jacuinde, H. Valdes-Vera, J. Quintero-Ortiz, A. Zarate-Rangel, J. Pacheco-Cedeño, Measurement of Air Entrainment and its Effect on the Microstructure and Mechanical Properties of a A356 Aluminum Alloy, International Journal of Metalcasting (2022) 1-19.
- [73] M. Tiryakioğlu, P. Yousefian, P.D.J.M. Eason, M.T. A, Quantification of entrainment damage in A356 aluminum alloy castings, 49(11) (2018) 5815-5822.
- [74] D. Dispinar, J. Campbell, Porosity, hydrogen and bifilm content in Al alloy castings, Materials Science and Engineering: A 528(10) (2011) 3860-3865.
- [76] X. Cao, J.J.M. Campbell, M.T. A, The nucleation of Fe-rich phases on oxide films in Al-11.5 Si-0.4 Mg cast alloys, 34(7) (2003) 1409-1420.
- [79] J. Campbell, Perspective chapter: A personal overview of casting processes, Casting Processes and Modelling of Metallic Materials (2020) 1-17.
- [80] M. Tiryakioğlu, The Effect of Hydrogen on Pore Formation in Aluminum Alloy Castings: Myth Versus Reality, Metals 10(3) (2020) 368.
- [82] V.-D. Le, N. Saintier, F. Morel, D. Bellett, P. Osmond, Investigation of the effect of porosity on the high cycle fatigue behaviour of cast Al-Si alloy by X-ray micro-tomography, International Journal of Fatigue 106 (2018) 24-37.
- [86] C. Caceres, M. Djurdjevic, T. Stockwell, J. Sokolowski, The effect of Cu content on the level of microporosity in Al-Si-Cu-Mg casting alloys, Scripta Materialia 40(5) (1999) 631-637.
- [97] S.-Z. Lu, A. Hellawell, Growth mechanisms of silicon in Al-Si alloys, Journal of Crystal growth 73(2) (1985) 316-328.
- [98] D. Jenkinson, L. Hogan, The modification of aluminium-silicon alloys with strontium, Journal of Crystal Growth 28(2) (1975) 171-187.
- [99] M. Timpel, N. Wanderka, R. Schlesiger, T. Yamamoto, N. Lazarev, D. Isheim, G. Schmitz, S. Matsumura, J. Banhart, The role of strontium in modifying aluminium–silicon alloys, Acta Materialia 60(9) (2012) 3920-3928.
- [100] A. Knuutinen, K. Nogita, S. McDonald, A. Dahle, Modification of Al–Si alloys with Ba, Ca, Y and Yb, Journal of Light Metals 1(4) (2001) 229-240.
- [101] S.J. Mashl, H. Bodycote, Hot Isostatic Pressing of Castings, Casting, 2008.
- [102] A. Eklund, M. Ahlfors, Heat treatment of PM parts by Hot Isostatic Pressing, Metal Powder Report 73(3) (2018) 163-169.
- [103] H. Atkinson, S. Davies, Fundamental aspects of hot isostatic pressing: an overview, Metallurgical and Materials Transactions A 31(12) (2000) 2981-3000.
- [104] M.H. Lee, J.J. Kim, K.H. Kim, N.J. Kim, S. Lee, E.W. Lee, Effects of HIPping on high-cycle fatigue properties of investment cast A356 aluminum alloys, Materials Science and Engineering: A 340(1-2) (2003) 123-129.
- [105] C. Lei, W. Frazier, E. Lee, The effect of hot isostatic pressing on cast aluminum, Jom 49(11) (1997) 38-39.
- [106] G. Ran, J. Zhou, Q. Wang, The effect of hot isostatic pressing on the microstructure and tensile properties of an unmodified A356-T6 cast aluminum alloy, Journal of alloys and compounds 421(1-2) (2006) 80-86.
- [107] L. Ceschini, A. Morri, G. Sambogna, The effect of hot isostatic pressing on the fatigue behaviour of sand-cast A356-T6 and A204-T6 aluminum alloys, Journal of materials processing technology 204(1-3) (2008) 231-238.
- [109] T. Rich, J. Orbison, R. Duncan, P. Olivero, R. Peterec, The effect of hot isostatic pressing on crack initiation, fatigue, and mechanical properties of two cast aluminum alloys, Journal of materials engineering and performance 8(3) (1999) 315-324.
- [113] A. Mohamed, F. Samuel, Influence of Mg and solution heat treatment on the occurrence of incipient melting in Al–Si–Cu–Mg cast alloys, Materials Science and Engineering: A 543 (2012) 22-34.
- [116] N.E. Dowling, Mechanical behavior of materials: engineering methods for deformation, fracture, and fatigue, Pearson2012.
- [117] E. Ghassemali, M. Riestra, T. Bogdanoff, B.S. Kumar, S. Seifeddine, Hall-Petch equation in a hypoeutectic Al-Si cast alloy: grain size vs. secondary dendrite arm spacing, Procedia Engineering 207 (2017) 19-24.
- [118] T. Bogdanoff, S. Seifeddine, A.K. Dahle, The effect of SI content on microstructure and mechanical properties of Al-Si alloy, La Metallurgia Italiana 108(6) (2016).
- [119] C. Caceres, I.L. Svensson, J. Taylor, Strength-ductility behaviour of Al-Si-Cu-Mg casting alloys in T6 temper, International Journal of Cast Metals Research 15(5) (2003) 531-543.
- [122] S. Suresh, Fatigue of materials, Cambridge university press1998.
- [124] M. Leitner, C. Garb, H. Remes, M. Stoschka, Microporosity and statistical size effect on the fatigue strength of cast aluminium alloys EN AC 45500 and 46200, Materials Science and Engineering: A 707 (2017) 567-575.
- [126] J.T. Staley Jr, M. Tiryakioğlu, J. Campbell, The effect of hot isostatic pressing (HIP) on the fatigue life of A206-T71 aluminum castings, Materials Science and Engineering: A 465(1-2) (2007) 136-145.
- [127] D.A. Lados, D. Apelian, Fatigue crack growth characteristics in cast Al–Si–Mg alloys: Part I. Effect of processing conditions and microstructure, Materials Science and Engineering: A 385(1-2) (2004) 200-211.
- [128] D.A. Lados, D. Apelian, J.F. Major, Fatigue crack growth mechanisms at the microstructure scale in Al-Si-Mg cast alloys: Mechanisms in regions II and III, Metallurgical and Materials Transactions A 37(8) (2006) 2405-2418.
- [131] Q. Wang, D. Apelian, D. Lados, Fatigue behavior of A356/357 aluminum cast alloys. Part II–Effect of microstructural constituents, Journal of light metals 1(1) (2001) 85-97.
- [132] K. Williamson, Research methods for students, academics and professionals: Information management and systems, Elsevier2002.
- [133] P. Johannesson, E. Perjons, An introduction to design science, Springer2014.
- [134] K.A. Kasvayee, E. Ghassemali, K. Salomonsson, S. Sujakhu, S. Castagne, A.E. Jarfors, Microstructural strain mapping during in-situ cyclic testing of ductile iron, Materials Characterization 140 (2018) 333-339.
- [135] K.A. Kasvayee, K. Salomonsson, E. Ghassemali, A.E. Jarfors, Microstructural strain distribution in ductile iron; comparison between finite element simulation and digital image correlation measurements, Materials Science and Engineering: A 655 (2016) 27-35.
- [136] E. Erzi, M. Tiryakioğlu, A simple procedure to determine incoming quality of aluminum alloy ingots and its application to A356 alloy ingots, International Journal of Metalcasting 14(4) (2020) 999-1004.
- [137] D. Dispinar, J. Campbell, A comparison of methods used to assess aluminium melt quality, 136th TMS Annual Meeting, Shape Casting: 2nd International Symposium, Orlando, Florida, USA,(February 2007), 2007, pp. 11-18.
- [138] D. Dispinar, S. Akhtar, A. Nordmark, M. Di Sabatino, L. Arnberg, Degassing, hydrogen and porosity phenomena in A356, Materials Science and Engineering: A 527(16-17) (2010) 3719-3725.
- [139] W. Weibull, A statistical theory of strength of materials, IVB-Handl. (1939).
- [140] W. Weibull, A statistical distribution function of wide applicability, Journal of applied mechanics (1951).
- [141] M. Tiryakioğlu, D. Hudak, On estimating Weibull modulus by the linear regression method, Journal of materials science 42(24) (2007) 10173-10179.
- [142] M. Tiryakioğlu, D. Hudak, Guidelines for two-parameter Weibull analysis for flaw-containing materials, Metallurgical and Materials Transactions B 42(6) (2011) 1130-1135.
- [143] M. Tiryakioğlu, D. Hudak, G. Ökten, On evaluating Weibull fits to mechanical testing data, Materials Science and Engineering: A 527(1-2) (2009) 397-399.
- [144] D. Dispinar, J. Campbell, Metal quality studies in secondary remelting of aluminium, Foundry Trade Journal 178(3612) (2004) 78-81.
- [145] R. Kimura, Molten Metal Quality of Aluminium Alloy Die Castings, J.JFS 87 (2015) 412-416.
- [146] M. Tiryakioğlu, J. Campbell, N.D. Alexopoulos, On the ductility of cast Al-7 pct Si-Mg alloys, Metallurgical and Materials Transactions A 40(4) (2009) 1000-1007.
- [147] M. Tiryakioğlu, J. Campbell, N.D. Alexopoulos, On the ductility potential of cast Al–Cu–Mg (206) alloys, Materials Science and Engineering: A 506(1-2) (2009) 23-26.
- [148] M. Tiryakioğlu, J. Campbell, N.D. Alexopoulos, Quality indices for aluminum alloy castings: A critical review, Metallurgical and Materials Transactions B 40(6) (2009) 802-811.
- [149] M. Tiryakioğlu, J. Campbell, Quality index for aluminum alloy castings, International Journal of Metalcasting 8(3) (2014) 39-42.
- [150] M. Tiryakioğlu, J. Campbell, Weibull analysis of mechanical data for castings: A guide to the interpretation of probability plots, Metallurgical and Materials Transactions A 41 (2010) 3121-3129.
- [151] T. Lu, J. Wu, Y. Pan, S. Tao, Y. Chen, Optimizing the tensile properties of Al–11Si–0.3 Mg alloys: Role of Cu addition, Journal of Alloys and Compounds 631 (2015) 276-282.
- [152] E. Sjölander, S. Seifeddine, Optimisation of solution treatment of cast Al–Si–Cu alloys, Materials & design 31 (2010) S44-S49.
- [153] J.H. Sokolowski, X. Sun, G. Byczynski, D. Northwood, D. Penrod, R. Thomas, A. Esseltine, The removal of copper-phase segregation and the subsequent improvement in mechanical properties of cast 319 aluminium alloys by a two-stage solution heat treatment, Journal of Materials Processing Technology 53(1-2) (1995) 385-392.
- [154] G. Wang, Q. Sun, L. Feng, L. Hui, C. Jing, Influence of Cu content on ageing behavior of AlSiMgCu cast alloys, Materials & design 28(3) (2007) 1001-1005.
- [155] S. Toschi, Optimization of A354 Al-Si-Cu-Mg Alloy Heat Treatment: Effect on Microstructure, Hardness, and Tensile Properties of Peak Aged and Overaged Alloy, Metals 8(11) (2018) 961.
- [156] J.J. Friel, Practical guide to image analysis, ASM international2000.
- [157] J.-M. Song, C.-F. Huang, H.-Y. Chuang, Microstructural characteristics and vibration fracture properties of Sn-Ag-Cu-TM (TM= Co, Ni, and Zn) alloys, Journal of electronic materials 35(12) (2006) 2154-2163.
- [158] D.A. Lados, D. Apelian, P.E. Jones, J.F. Major, Microstructural mechanisms controlling fatigue crack growth in Al–Si–Mg cast alloys, Materials Science and Engineering: A 468 (2007) 237-245.
- [159] N. Rathod, J. Manghani, Effect of modifier and grain refiner on cast Al-7Si aluminum alloy: A review, International Journal of emerging trends in engineering and development 5(2) (2012) 574-582.
- [160] M. Riestra, E. Ghassemali, T. Bogdanoff, S. Seifeddine, Interactive effects of grain refinement, eutectic modification and solidification rate on tensile properties of Al-10Si alloy, Materials Science and Engineering: A 703 (2017) 270-279.
- [161] L. Ceschini, A. Morri, S. Toschi, S. Seifeddine, Room and high temperature fatigue behaviour of the A354 and C355 (Al–Si–Cu–Mg) alloys: Role of microstructure and heat treatment, Materials Science and Engineering: A 653 (2016) 129-138.
- [162] T. Bogdanoff, L. Lattanzi, M. Merlin, E. Ghassemali, S. Seifeddine, The Influence of Copper Addition on Crack Initiation and Propagation in an Al-Si-Mg Alloy During Cyclic Testing, Materialia (2020) 100787.
- [163] T. Bogdanoff, L. Lattanzi, M. Merlin, E. Ghassemali, A.E. Jarfors, S.J.M.S. Seifeddine, E. A, The complex interaction between microstructural features and crack evolution during cyclic testing in heat-treated Al–Si–Mg–Cu cast alloys, 825 (2021) 141930.
- [164] G. Gyarmati, G. Fegyverneki, Z. Kéri, D. Molnár, M. Tokár, L. Varga, T. Mende, Controlled precipitation of intermetallic (Al, Si) 3Ti compound particles on double oxide films in liquid aluminum alloys, Materials Characterization 181 (2021) 111467.
- [165] X. Cao, J. Campbell, The solidification characteristics of Fe-rich intermetallics in Al-11.5 Si-0.4 Mg cast alloys, Metallurgical and Materials Transactions A 35(5) (2004) 1425-1436.
- [170] M. Schaffer, B. Schaffer, Q. Ramasse, Sample preparation for atomic-resolution STEM at low voltages by FIB, Ultramicroscopy 114 (2012) 62-71.
- [171] Y. Umeno, A. Kushima, T. Kitamura, P. Gumbsch, J. Li, Ab initio study of the surface properties and ideal strength of (100) silicon thin films, physical Review B 72(16) (2005) 165431.
- [172] S.-M. Dubois, G.-M. Rignanese, T. Pardoen, J.-C. Charlier, Ideal strength of silicon: An ab initio study, Physical Review B 74(23) (2006) 235203.
- [173] M. Mueller, G. Žagar, A. Mortensen, In-situ strength of individual silicon particles within an aluminium casting alloy, Acta Materialia (2017).
- [174] M. Mueller, M. Fornabaio, G. Žagar, A. Mortensen, Microscopic strength of silicon particles in an aluminium–silicon alloy, Acta Materialia 105 (2016) 165-175.
- [175] A. Noreyan, Y. Qi, V. Stoilov, Critical shear stresses at aluminum–silicon interfaces, Acta materialia 56(14) (2008) 3461-3469.
- [176] M. Tiryakioğlu, On the heterogeneous nucleation pressure for hydrogen pores in liquid aluminium, International Journal of Cast Metals Research 33(4-5) (2020) 153-156.
- [177] P. Yousefian, M. Tiryakioğlu, Pore formation during solidification of aluminum: reconciliation of experimental observations, modeling assumptions, and classical nucleation theory, Metallurgical and Materials Transactions A 49 (2018) 563-575.
- [178] S. Pomberger, M. Leitner, M.J.M.T.P. Stoschka, Evaluation of surface roughness parameters and their impact on fatigue strength of Al-Si cast material, Materials Today Preceedings 12 (2019) 225-234.
- [179] M. Tiryakioğlu, J. Campbell, C.J.M. Nyahumwa, M.T. B, Fracture surface facets and fatigue life potential of castings, 42(6) (2011) 1098-1103.
- [180] H. Dvorak, E. Schwegtier Jr, Statistical distribution of flaw sizes, International Journal of Fracture Mechanics 8(1) (1972) 110-111.
- [181] M. Tiryakioğlu, Pore size distributions in AM50 Mg alloy die castings, Materials Science and Engineering: A 465(1-2) (2007) 287-289.
- [182] M. Tiryakioğlu, On fatigue life variability in cast Al–10% Si–Mg alloys, Materials Science and Engineering: A 527(6) (2010) 1560-1564.
- [183] T.W. Anderson, D.A. Darling, A test of goodness of fit, Journal of the American statistical association 49(268) (1954) 765-769.
- [184] O. Basquin, The exponential law of endurance tests, Proc Am Soc Test Mater, 1910, pp. 625-630.
- [185] S. Sarkani, T. Mazzuchi, D. Lewandowski, D. Kihl, Runout analysis in fatigue investigation, Engineering Fracture Mechanics 74(18) (2007) 2971-2980.
- [186] R. Hidalgo Coca, J.A. Esnaola Ramos, I. Llavori Osa, M. Larrañaga Serna, N. Herrero Dorca, I. Hurtado Hurtado, A. Kortabarria Lezeta, Influence of Surface Finish and Porosity on the Fatigue behaviour of A356 Aluminium Casting Alloy, 12th International Fatigue Congress (FATIGUE 2018), France, 2018.
- [187] J. Linder, M. Axelsson, H. Nilsson, The influence of porosity on the fatigue life for sand and permanent mould cast aluminium, International Journal of Fatigue 28(12) (2006) 1752-1758.
- [188] B. Zhao, J. Song, L. Xie, Z. Hu, J. Chen, Surface roughness effect on fatigue strength of aluminum alloy using revised stress field intensity approach, Scientific reports 11(1) (2021) 19279.
- [189] B. Skallerud, T. Iveland, G. Härkegård, Fatigue life assessment of aluminum alloys with casting defects, Engineering Fracture Mechanics 44(6) (1993) 857-874.
- [191] L. Wang, N. Limodin, A. El Bartali, J.-F. Witz, R. Seghir, J.-Y. Buffiere, E. Charkaluk, Influence of pores on crack initiation in monotonic tensile and cyclic loadings in lost foam casting A319 alloy by using 3D in-situ analysis, Materials Science and Engineering: A 673 (2016) 362-372.
- [192] R.C. Juvinall, Engineering considerations of stress strain and strength, 1967, 580 P. MCGRAW-HILL BOOK CO., NEW YORK (1967).
- [193] H. Özdeş, M. Tiryakioğlu, On estimating high-cycle fatigue life of cast Al-Si-Mg-(Cu) alloys from tensile test results, Materials Science and Engineering: A 688 (2017) 9-15.
- [194] H. Özdeş, M. Tiryakioğlu, The effect of structural quality on fatigue life in 319 aluminum alloy castings, Journal of Materials Engineering and Performance 26 (2017) 736-743.
9. Copyright:
- This material is a paper by "Toni Bogdanoff". Based on "The Effect of Microstructural Features, Defects and Surface Quality on the Fatigue Performance in Al-Si-Mg Cast Alloys".
- Source of the paper: http://urn.kb.se/resolve?urn=urn:nbn:se:hj:diva-61111
This material is summarized based on the above paper, and unauthorized use for commercial purposes is prohibited.
Copyright © 2025 CASTMAN. All rights reserved.