This introduction paper is based on the paper "Wear properties of a new Al80Mg10Si5Cu5 multicomponent alloy" published by "Elsevier B.V.".
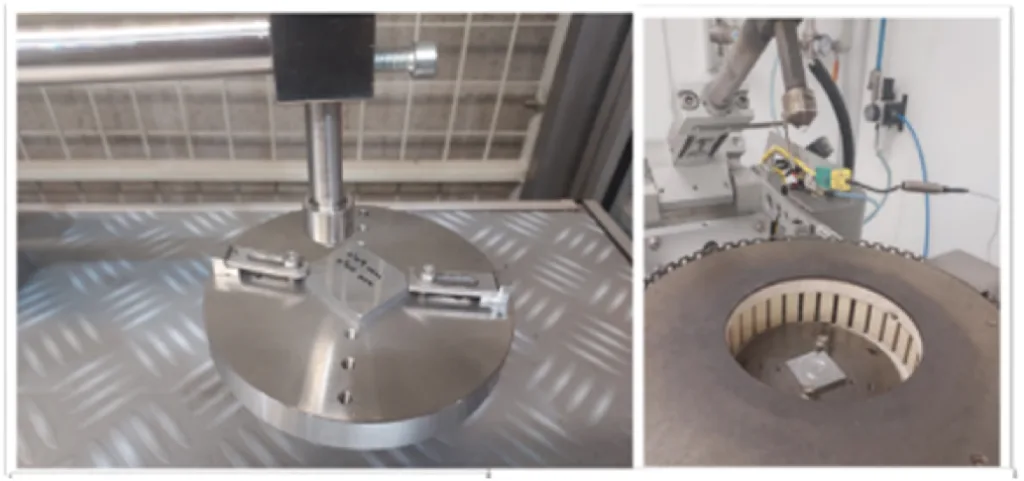
1. Overview:
- Title: Wear properties of a new Al80Mg10Si5Cu5 multicomponent alloy
- Author: Ester Villanueva, Iban Vicario, Joseba Albizuri, Gurutze Arruebarrena, Teresa Guraya
- Year of publication: 2024
- Journal/academic society of publication: Wear
- Keywords: Ball on disc, Friction, Wear, Aluminium multicomponent alloy, Abrasion
2. Abstract:
The present study investigates the tribological properties of a newly developed multicomponent aluminium weight-light multicomponent alloy for wear based on the Al80Mg10Si5Cu5 system for lightweight automotive applications, especially back drum discs. The samples were manufactured by High-Pressure Die Casting (HPDC) employing cast alloy returns and secondary aluminium ingots and were tested at room temperature (RT) and 200 °C. It has been observed that the A180Mg10Si5Cu5 alloy offers a higher hardness and wear resistance at RT and especially at 200 °C compared with the AlSi9Cu3 reference alloy (x10 times reduction in wear rate). The impact of maintaining the external surface layer (skin) of HPDC cast parts has been studied for the ball-on disc test, showing improved tribological properties and the possibility of avoiding the machining of contact surfaces. The as-cast A180Mg10Si5Cu alloy with the surface layer showed a wear rate coefficient of 5 × 10⁻⁴ mm³/N.m² at RT, a 50 % lower than that of the sample without skin. Solution heat-treated samples (72 h at 440 °C, water quenching at 75 °C, and natural aging) with the surface layer showed a wear rate coefficient of 11 × 10⁻⁴ mm³/N.m², approximately 20 % lower than the sample without a surface layer. The wear rate of AlSi9Cu3 alloy decreased by more than 50 % in the samples without skin at RT. At 200 °C, wear rate coefficients were lower in the samples with the surface layer.
3. Introduction:
Aluminium multiphase and non-equiatomic High Entropy Alloys (HEA) alloys based on the multi-component concept have been demonstrated to own excellent physical and mechanical properties, in contrast to single-phase alloys [1]. The effect of rapid solidification processes to obtain enhanced single-phase microstructures in these alloys has been collected in recent works [2]. On the other hand, the demand for lightweight vehicles in the industry causes rapid growth in the manufacture of aluminium casting parts, especially for electric vehicles with the GIGAPRESS technology by High-Pressure Die Casting (HPDC) [3]. The electric vehicle market is continuously increasing, and lightning is critical to increase car autonomy. Aluminium drum brakes can be used for lighting electric cars, because the forces of rear brakes are lower than front brakes, and by using Kinetic Energy Recovery Systems (KERS), reducing brake forces. Also, front disk brakes act before rear drum brakes, with reduced pressure in the rear brakes [4]. Aluminium drums are lighter than iron drums, with improved heat dissipation and reduced fade, avoiding the possible corrosion of grey cast iron discs and disc failures [5].
AlSiCu are the most common aluminium alloys used in HPDC, but they present certain limitations in their mechanical properties [6] with AlSiMgCu alloys providing higher corrosion and higher strength, being generally improved by heat treatments, which makes them suitable for different automotive parts requiring good wear resistance and friction [7,8]. Insufficient wear resistance is a problem for aluminium alloys [9], though the tribological properties of Al alloys can be enhanced by balancing the type and quantity of alloying elements, or by introducing ex-situ reinforcing phases and by heat treatments [10–12]. To replace cast iron brakes and reduce vehicle weight, aluminium-based metal matrix composite (AMC) brake rotors have been developed. AMCs have higher heat conductivity, lower density, and higher specific strengths than aluminium alloys. AMCs present a ductile aluminium matrix reinforced with hard ceramic particles such as Al2O3, SiC, and SiO2 to obtain customized properties [13].
However, the main disadvantages of AMCs are their production cost (especially machinability cost), the difficulty in the control of particle size and distribution, because wear characteristics greatly depend on reinforcement volume and size of the reinforced particles [14], the complex casting processes, and mainly the low or difficult recyclability of returns and scraps.
The most common method of enhancing the wear properties of cast aluminium alloys that are not AMCs is silicon alloying. Increasing the Si fraction, more Si hard crystals are produced, increasing the hardness of the alloy and its wear resistance. For tribological applications, the hypereutectic Al-Si alloys (with Si > 13 wt%) are typically employed, with a primary phase of silicon combined with aluminium in the eutectic phase. The silicon phases' type, morphology, size, and distribution are crucial to enhance the friction and wear resistance, by supporting an important portion of the load in the aluminium matrix regions deformed plastically [15–17]. In these alloys, Si in combination with Mg tends to precipitate as Mg2Si. An increase in the amount of Mg promotes an improvement in wear performance [18]. Complex intermetallic phases are key in preventing junction growth and adhesion in wear mechanisms. Alloys with high intermetallic phases have lower wear rates [19]. An increase in copper in the alloy increases the mechanical properties, reduces the corrosion resistance, and could increase porosity [20,21]. In AlSi7Mg alloy, a minimum of 1 wt% Cu was needed to obtain the Al₂Cu intermetallic phase that promotes finer grains and increased hardness and wear resistance, lowering the friction coefficient [22]. The mechanism for improving the hardness of an aluminium cast alloy is also influenced by the reactions of Mg with Al and of Cu with Si, promoting different precipitates responsible of the strengthening of the alloy. The definition of the different phases' formation and their behaviour is a complicated task because several phases can precipitate near or at the same time, such as β (Mg2Si), θ (Al₂Cu), S (Al₂CuMg) or Q (Al5Cu2Mg8Si6) [23]. During heat treatment, solution temperature, cooling rate, and time play an important role, resulting in several complex interactions. An aging process at an optimal temperature avoids the precipitation of large and non-coherent particles that could decrease strength and ductility. The combination of small amounts of other elements, as Fe, Mn, and Cr improves the hardness and strength of Al-Si alloys, increasing the wear resistance [24].
Focus on tribology studies of casting aluminium alloys, systems such as AlSi and AlSiCuMg(X) [25–27] are the most studied. In high silicon aluminium alloys, in general, the wear mechanism variates from ductile delamination, abrasive, and brittle delamination to ploughed abrasive wear by increasing the load [28]. Abrasion and oxidation are the dominant wear phenomena in the mild wear regime, but not always. Delamination, adhesion, and severe plastic deformation are the dominant in the severe wear regime in AlSi9Cu3 HPDC alloys [23]. Delamination has been related with the removal of large wear particles through the plastic deformation of the surface layer which occurs by subsurface crack nucleation followed by crack propagation [29,30]. This mechanism is particularly evident at elevated temperatures, where subsurface separation forms transfer layers that adhere and increase the coefficient of friction [31]. Additionally, it has been reported that the wear rate at high temperatures is ten times greater than at room temperature [32]. Under these conditions, a scuffing mechanism can occur, involving severe plastic deformation, material and layer transfer and accumulation. During high temperatures the adhesion between the layers can decrease, facilitating the delamination.
In some works, the wear mechanism changes with temperature from delamination to partial abrasive wear at RT to plastic deformation and oxidative wear (with plastic relaxation mechanisms becoming dominant) over 150 °C [33–36]. In the AlSi9Cu3 alloy, the hardness decreases, and also the mechanical and wear properties, because of the precipitation of different phases [23,24]. The wear rate is much higher at temperatures higher than 150 °C than at RT, but it does not have a linear proportionality with temperature, with a significant increase at about 200 °C. The increase of temperature of the wear test, in AMCs and aluminium alloys promotes higher compactness and higher average resistance of the surface layer, accelerating the oxidation of particles. If a surface layer is formed before the surface layer breakdown, the wear rate is reduced [6]. But if the surface layer is not compacted, the superficial particles are removed, the surface is damaged and delamination occurs, increasing the wear rate [23].
The mild to severe wear transition mechanism has been described by a combination of test variables such as the applied load, counter partner ball material, the sliding speed, and the contact surface temperature. Normally severe wear is related to a massive plastic deformation due to the thermal softening of the alloy and depending on the conditions, the aluminium alloys can work in a non-severe wear condition, controlling the delamination wear [9]. The conditions for obtaining a mild wear mechanism in AlSiCu(Fe) cast alloys have been studied [9,11,12,16, 37–39].
It is also noted that there is increased interest in using coatings for wear applications [40,41].
The ball on disc (BOD) test is one of the most employed tests for determining the wear properties of a material. The mechanism of wear rate analyzing the ball-on-disc test data can be divided into three main stages or phases [42–45]. The first phase corresponds to the removal of the surface layer with the maximum adhesion force between the base material and the ball because of the superficial asperities deformation and by increasing the number of residual particles. The second phase is normally related to the formation of a protective tribochemical surface layer or by a reduction in the ploughing and asperities deformation processes. There is sometimes a subphase when the rise in pin surface temperature can result in the formation of an oxide layer on the sliding surface, preventing the exposure of soft matrix material to the counter-ball surface, and reducing the wear rate of the pin surface [46, 47]. The third phase is characterized by an interfacial steady state of tribological conditions.
The applied load effect over the wear rate changes depending on the alloy, with some alloys showing weak wear rate at low loads, with a high increase in wear rate values at medium loads, and a gradual increase at high loads. Low applied pressure normally promotes the debris formed due to wear got trapped in the valley of the counter surface. Due to entrapment of debris in the valley, point contact by asperities from the disc is shifted to the contact surface. The shifting to contact surface and work hardening of samples led to steady-state wear [48,49].
An increase in applied pressure showed a temperature rise, leading to the removal of the oxide layer [48]. The fractured/fragmented oxide layer and the wear debris of counter surfaces can cause the formation of a mechanically mixed layer (MML) or transfer film (TF). Under the influence of applied pressure, the deformation of transfer film (TF) results in strain hardening of wear debris, increasing the hardness of the TF [48]. The constant formation and removal of the TF prevented the metal-to-metal contact, with the wear rate remaining constant in the steady-state-wear zone.
The transition from mild to severe wear values can vary from about 4 to 8 N up to 30 N [50] depending on the applied load. In general, the specific wear rate values increase with an increase in the applied load.
For commercial brake rotors, the Coefficient Of Friction (COF) has values between 0.45 and 0.69. For some authors, there is not a linear increase in COF value increasing the load [51] and for others, there is a linear increase for Al-Al2O3 MMC and Al-SiC MMC alloys for example with stable friction coefficients between 0.30 and 0.60 for brake rotor applications [52].
The reported wear rate for drum brakes to define a mild or severe wear state varies. Severe wear rates have been reported, with k = 15 × 10⁻³ mm³/N.m for the Al7.1Si alloy [53], 6 × 10⁻³ mm³/N.m for LM17 alloy, and 7.5–10 × 10⁻³ mm³/N.m for aluminium composites with pressure and velocity (0.2–1.0 N/mm ² and 1.6 m/s respectively) representatives of braking conditions for brake rotors [54]. A LM27 alloy reinforced with rutile and sillimanite minerals Hybrid AMCs (HAMCs) for brake rotor applications showed wear rates at 500 m around 16.5 × 10⁻³ mm³/N.m for a commercial rotor material and 18 × 10⁻³ mm³/N.m for the HAMC, with final steady wear values around 6 and 7 × 10⁻³ mm³/N.m respectively. Values between 0.37x10⁻⁴ to 2.37x10⁻⁴ mm³/N.m are generally within the severe wear regime [55]. However, in the case of aluminium cast alloys, with a 15 N test force, they are around 5 × 10⁻³ mm³/N.m [56]. To determine the charge of the test, 15 N has been selected to compare the results with the bibliographic information for aluminium brakes because of the high bibliographic data variation depending on the tested alloy [56].
The selection of ball material is crucial because it can modify final results. With aluminium alloys, alumina is often employed as the ball material to avoid the formation of the MML containing Al-Fe-O during the tests when steel balls are employed, due to the affinity of aluminium with steel [55–57], minimizing the chemically driven aspects of adhesive wear due to the minimal chemical-driven adhesion. So, the determination of the effect of the aluminium alloy on wear properties is easier with alumina counter ball [58].
The new developed A180Mg10Si5Cu5 alloy has been designed to maintain its properties up to around 200 °C and the selection of alloying elements was carefully determined to obtain Mg2Si and Al₂Cu intermetallic phases (that increase the wear resistance) but without the presence of primary Si (to obtain better mechanical properties and some ductility). The application of the newly developed alloy could be for aluminium drum brakes, especially for the rear brakes of small electric cars.
Recently, scrap-tolerant Al65Cu10Mg10Si10Zn5 and Al80Cu5Mg5Si5Zn5 HEA aluminium alloys have been studied, showing promising mechanical and wear properties [59] but there is still very little information on the wear properties of HEA aluminium alloys and less with materials produced by an industrial process based on secondary aluminium alloys or scraps. Secondary aluminium ingots, cast aluminium returns, and magnesium scraps melted in an electric crucible furnace and the HPDC processes were employed to obtain low CO2 manufacturing values [60].
So, in this study, the developed alloy will be studied at RT and 200 °C and compared with the most standard casting alloy (AlSi9Cu3 alloy) in the as-cast and thermally treated (TT) state.
In parallel, aluminium casting parts produced by HPDC show a skin region (or surface layer) in the external surface, which is nearly free of defects with improved mechanical properties [61]. However, the effect of maintaining the external surface layer on the wearing properties in the ball-on-disk (BOD) test has not been or very scarce studied [62].
4. Summary of the study:
Background of the research topic:
The automotive industry's push for lightweight vehicles, particularly electric vehicles (EVs), drives demand for aluminium alloys due to their low density. High-Pressure Die Casting (HPDC) is a key manufacturing process for these parts. While common AlSiCu alloys have limitations, multicomponent alloys offer potential for improved properties. Aluminium drum brakes are considered for EVs due to lower rear brake forces and weight savings compared to cast iron. However, the wear resistance of aluminium alloys remains a challenge.
Status of previous research:
Standard AlSiCu and AlSiMgCu alloys are widely used in HPDC, often requiring heat treatments to enhance properties. Wear resistance in Al alloys can be improved by controlling alloying elements (Si, Mg, Cu), introducing reinforcing phases (as in Aluminium Matrix Composites, AMCs), or via heat treatments. AMCs, while offering good properties, suffer from high cost, complex processing, and poor recyclability. For non-AMC alloys, Si content increases hardness (Mg2Si formation), Cu addition can form Al₂Cu enhancing hardness, and other elements (Fe, Mn, Cr) also contribute. Wear mechanisms in Al alloys typically involve abrasion, oxidation, and delamination, heavily influenced by temperature (wear often increases significantly above 150-200 °C) and load, transitioning from mild to severe regimes. Ball-on-disc (BOD) testing is a common method to evaluate tribological properties. HPDC parts feature a fine-grained surface 'skin' with enhanced properties, but its effect on wear is rarely studied.
Purpose of the study:
This study aimed to investigate the tribological properties (friction and wear) of a newly developed multicomponent alloy, Al80Mg10Si5Cu5, designed for wear resistance up to 200°C. The research compared this alloy, produced by HPDC using secondary materials, with the standard AlSi9Cu3 alloy. Key objectives included evaluating performance at room temperature (RT) and 200°C, and specifically assessing the impact of retaining the as-cast external surface layer (skin) versus testing machined surfaces. The potential application targeted is lightweight aluminium drum brakes for automotive use.
Core study:
The core of the study involved manufacturing test samples of the new Al80Mg10Si5Cu5 alloy and the reference AlSi9Cu3 alloy using industrial HPDC processes with secondary aluminium. Some Al80Mg10Si5Cu5 samples were subjected to a solution heat treatment (TT). Tribological performance was evaluated using ball-on-disc (BOD) wear tests under dry sliding conditions against an alumina counter ball at both RT and 200°C. Tests were conducted on samples with the original HPDC surface skin intact and on samples where the skin was removed (polished surface). Microstructure (Optical Microscopy, SEM/EDS), phase composition (XRD), and hardness (Vickers, RT & 200°C) were characterized. The study compared the friction coefficient and specific wear rate of the new alloy versus the standard alloy, analyzed the effect of the surface skin, the influence of heat treatment, and the impact of elevated temperature on wear behaviour and mechanisms.
5. Research Methodology
Research Design:
The study employed a comparative experimental design. A newly developed Al80Mg10Si5Cu5 alloy was compared against a standard reference alloy, AlSi9Cu3. Both alloys were produced using HPDC. The experimental variables included the alloy type, the presence or absence of the as-cast surface skin, the material condition (as-cast vs. heat-treated for the new alloy), and the testing temperature (Room Temperature vs. 200 °C).
Data Collection and Analysis Methods:
- Manufacturing: Samples produced by High-Pressure Die Casting (HPDC) using a 950t machine. Secondary Al alloys and returns were used as charge material. Some Al80Mg10Si5Cu5 samples underwent solution treatment (440 °C, 72 h) followed by water quenching (75 °C) and natural ageing (TT condition).
- Chemical Composition: Analyzed using Optical Emission Spectrometry (OES).
- Microstructural Analysis: Characterized using Optical Microscopy (MO) and Scanning Electron Microscopy (SEM) equipped with Energy Dispersive X-ray Spectrometry (EDS). Standard metallographic preparation procedures were followed.
- Phase Identification: Performed using X-ray Diffraction (XRD) with Cu-Kα radiation.
- Hardness Testing: Measured using Vickers diamond indentation (HV3) at RT and 200 °C according to UNE EN ISO 6507-1.
- Wear and Friction Testing: Conducted using a ball-on-disc tribometer in dry sliding, reciprocating mode (sphere-on-plate configuration) according to ASTM G99-05. Tests performed at RT and 200 °C using a 6 mm alumina ball counterface, a load of 15 N, a sliding speed of 0.1 m/s, and a total sliding distance of 500 m. Coefficient of Friction (COF) was recorded continuously.
- Wear Rate Measurement: Wear track volume loss determined using 3D laser scanning confocal microscopy. Specific wear rate (w) calculated using Equation (1): w = V / (s x F).
- Wear Surface/Subsurface Analysis: Examined using SEM/EDS and cross-sectional analysis via OM to determine wear mechanisms.
Research Topics and Scope:
The research focused on the tribological properties (friction and wear) of the novel Al80Mg10Si5Cu5 multicomponent alloy compared to the conventional AlSi9Cu3 alloy. The scope included:
- Evaluating the influence of the HPDC as-cast surface layer (skin) on wear and friction.
- Assessing the effect of a specific solution heat treatment (TT) on the Al80Mg10Si5Cu5 alloy's tribological performance.
- Investigating the impact of elevated temperature (200 °C) compared to room temperature (RT) on friction, wear rates, and wear mechanisms.
- Characterizing the microstructure, phases, and hardness of the alloys in different conditions.
- Testing was limited to dry sliding conditions using a specific set of BOD parameters (15N load, 0.1 m/s speed, alumina counterface).
6. Key Results:
Key Results:
- Hardness: The new Al80Mg10Si5Cu5 alloy exhibited higher hardness than the reference AlSi9Cu3 alloy in both as-cast and heat-treated (TT) conditions, at both RT and 200 °C. The surface layer (skin) consistently showed slightly higher hardness than the inner material due to finer microstructure. The TT condition resulted in lower hardness compared to the as-cast state for the Al80Mg10Si5Cu5 alloy.
- Friction (COF): At RT, both alloys (as-cast) showed similar steady-state COF values around 0.37-0.39. At 200 °C, significant differences emerged: Al80Mg10Si5Cu5 maintained relatively lower COF (around 0.41-0.42 for as-cast, ~0.50-0.53 for TT), while AlSi9Cu3 showed much higher COF (~0.64 with skin, ~0.80 without skin). The presence of the surface skin generally led to slightly lower COF values, particularly during the initial stages. The TT-Al80Mg10Si5Cu5 showed higher COF than the as-cast version at 200°C. All tests displayed a typical 3-stage friction curve (except at 200°C where the initial settling stage was suppressed).
- Wear Rate: The Al80Mg10Si5Cu5 alloy demonstrated significantly better wear resistance than AlSi9Cu3. At RT, the as-cast Al80Mg10Si5Cu5 with skin had the lowest wear rate (4.9 x 10⁻⁴ mm³/N.m). Removing the skin increased wear by ~50% for as-cast Al80Mg10Si5Cu5 and ~57% for AlSi9Cu3. At 200 °C, the wear resistance advantage of Al80Mg10Si5Cu5 was even more pronounced, showing a wear rate ~10 times lower than AlSi9Cu3 (e.g., 4.4 x 10⁻³ vs 44.8 x 10⁻³ mm³/N.m for samples without skin). The surface skin consistently reduced wear rates at both temperatures. Notably, the heat treatment (TT) increased the wear rate of the Al80Mg10Si5Cu5 alloy compared to its as-cast condition at both RT and 200 °C.
- Wear Mechanisms: For as-cast Al80Mg10Si5Cu5, abrasion was the dominant wear mechanism at both RT and 200 °C, indicating mild wear. For TT-Al80Mg10Si5Cu5, abrasion combined with some ductile delamination was observed, classified as mild wear with more cracks at RT and mild-to-severe wear at 200 °C. The AlSi9Cu3 alloy showed abrasion with ductile delamination (mild-severe signs) at RT, and predominantly severe ductile delamination at 200 °C. SEM/EDS analysis confirmed the role of microstructure (finer skin), phases (Mg2Si, Al₂Cu, Al₂CuMg), oxidation, and debris formation in the observed wear behaviour.
- Counter-ball Analysis: Material transfer (adhesion) onto the alumina counter-ball was observed in all tests, being more significant at 200 °C, particularly for the AlSi9Cu3 alloy.
Figure Name List:
- Fig. 1. Detail of tribometer employment and their components.
- Fig. 2. Detail of wearing surface topography.
- Fig. 3. XRD analysis of as-cast A180Mg10Si5Cu5 alloy.
- Fig. 4. XRD analysis of heat-treated A180Mg10Si5Cu5 alloy.
- Fig. 5. Analyzed phases in as-cast A180Mg10Si5Cu5 alloy.
- Fig. 6. Surface cast layer backscattered SEM images (x400 augmentation) of as-cast A180Mg10Si5Cu5 alloy.
- Fig. 7. Prepared sample backscattered SEM images (x400 augmentation) of as-cast A180Mg10Si5Cu5 alloy.
- Fig. 8. Surface cast layer sample SEM images (x400 augmentation) of the heat-treated A180Mg10Si5Cu5 alloy.
- Fig. 9. Inner region sample SEM images (x400 augmentation) of the heat-treated A180Mg10Si5Cu5 alloy.
- Fig. 10. Outside region optical microscopy images (x200 augmentation) of as-cast AlSi9Cu3 alloy.
- Fig. 11. Inner region optical microscopy images (x200 augmentation) of as-cast AlSi9Cu3 alloy.
- Fig. 12. Evolution of the coefficient of friction for the studied alloys at RT (0.1 m/s) with the surface layer.
- Fig. 13. Evolution of the coefficient of friction for the studied alloys at RT (0.1 m/s) without the surface layer.
- Fig. 14. Evolution of coefficient of friction for the experimental alloys at 200 °C (0,1 m/s) with the surface layer.
- Fig. 15. Evolution of coefficient of friction for the experimental alloys at 200 °C (0,1 m/s) without the surface layer.
- Fig. 16. Wear profiles at RT and 200 °C.
- Fig. 17. Material track area after BOD tests. (a) As-cast A180Mg10Si5Cu5 RT, (b) TT-A180Mg10Si5Cu5 RT, (c) As-cast AlSi9Cu3 RT, (d) As-cast A180Mg10Si5Cu5 200 °C, (e) TT-A180Mg10Si5Cu5 200 °C, (f) As-cast AlSi9Cu3 200 °C.
- Fig. 18. Material track thickness determination at RT: (a) As-cast A180Mg10Si5Cu5 RT, (b) TT-A180Mg10Si5Cu5 RT, (c) As-cast AlSi9Cu3 RT, and at 200 °C: (d) As-cast A180Mg10Si5Cu5, (e) TT-A180Mg10Si5Cu5, (f) As-cast AlSi9Cu3.
- Fig. 19. SEM images of worn surface tested at RT for as-cast A180Mg10Si5Cu5. (a), (b) and (c) = With surface layer at the magnification of×40, ×400 and x800. (d), (e) and (f) = Without surface layer at the magnification of×40, × 400 and x800.
- Fig. 20. SEM images of worn surface tested at RT for heat-treated A180Mg10Si5Cu5. (a), (b) and (c) = With surface layer at the magnification of×40, ×400 and x800. (d), (e) and (f) = Without surface layer at the magnification of×40, ×400 and x800.
- Fig. 21. SEM images of worn surface tested at RT for as-cast AlSi9Cu3. (a), (b) and (c) = With surface layer at the magnification of×40, ×400 and x800. (d), (e) and (f) = Without surface layer at the magnification of×40, × 400 and x800.
- Fig. 22. SEM images of worn surface for as-cast A180Mg10Si5Cu5. (a), (b) and (c) = With surface layer at the magnification of×40, ×400 and x800. (d), (e) and (f) = Without surface layer at the magnification of×40, ×400 and ×800 at 200 °C.
- Fig. 23. SEM images of worn surface for TT-A180Mg10Si5Cu5. (a), (b) and (c) = With surface layer at the magnification of×40, ×400 and x800. (d), (e) and (f) = Without surface layer at the magnification of×40, ×400 and ×800 at 200 °C.
- Fig. 24. SEM images of worn surface for as-cast AlSi9Cu3. (a), (b) and (c) = With skin at the magnification of×40, ×400 and x800. (d), (e) and (f) = Without skin at the magnification of×40, × 400, ×800 at 200 °C.
- Fig. 25. OM cross-section micrographs of the wear tracks tested at RT for as-cast A180Mg10Si5Cu5 at x100 (a), x200 (b), and ×500 (c) and as-cast AlSi9Cu3 at x100 (d), x200 (e) and ×500 (f).
- Fig. 26. OM cross-section micrographs of the wear tracks tested at 200 °C for as-cast A180Mg10Si5Cu5 at x100 (a), x200 (b), x500 (c), as-cast AlSi9Cu3 at ×100 (d), x200 (e) and ×500 (f).
7. Conclusion:
This paper has comprehensively investigated the friction and wear properties of a new A180Mg10Si5Cu5 cast alloy and compared them with the AlSi9Cu3 cast alloy at RT and at 200 °C in as-cast and thermal treated state, including the effect of the external skin of die-cast parts on wear. The conclusions are as follows:
(1) →The novel A180Mg10Si5Cu5 alloy developed for HPDC is characterized by enhanced wear properties compared to the standard AlSi9Cu3 alloy at RT (+50 % reduction in wear rate). This improvement is attributed to the hardness of the surface and subsurface, but also to the type and morphology of the microstructure in the new alloy, with abrasion as the main wear mechanism. AlSi9Cu3 alloy showed abrasion accompanied by some ductile delamination with a higher specific wear rate. At RT, A180Mg10Si5Cu5 alloy showed a mild wear rate and AlSi9Cu3 mild wear but with some signs of severe wear.
(2) →At 200 °C, the wear rate and COF values are higher. A180Mg10Si5Cu5 alloy in the as-cast condition with the surface layer presented again the lowest wear rate with abrasion wear, showing mild wear. TT-A180Mg10Si5Cu5 alloy exhibited abrasion along with a predominant secondary ductile delamination wear mechanism in comparison to as cast A180Mg10Si5Cu5 alloy, showing mild wear but with some signs of severe wear. As-cast AlSi9Cu3 alloy exhibited the highest wear rates (x10 times reduction in wear rate) and predominantly showed the ductile delamination mechanism, showing severe wear.
(3) →Samples with the surface layer presented lower COF values and specific wear rates, because of higher hardness, better microstructure, and reduced quality defects. Avoiding the machining of HPDC cast parts could improve in-service performance under wearing conditions.
(4) → The newly developed alloy shows promise as a cost-effective and low CO2 alternative for aluminium drum brakes. It offers advantages due to its performance properties obtained from secondary aluminium alloys, which are also lighter than iron which potentially enhance fuel efficiency. Additionally, the HPDC process used for its production results in reduced cycle times among other advantages.
8. References:
- [1] P. Sharma, V.K. Dwivedi, S.P. Dwivedi, Development of high entropy alloys: a review, Mater. Today: Proc. 43 (1) (2021) 502–509, https://doi.org/10.1016/j.matpr.2020.12.023.
- [2] S. Salifu, P.A. Olubambi, Effects of fabrication techniques on the mechanical properties of high entropy alloys: a review, Int. J. Lightweight Mater Manufact (2023) 13–53, https://doi.org/10.1016/j.ijlmm.2023.08.001.
- [3] D. Lehmhus, Advances in metal casting technology: a review of state of the art, challenges and trends – Part I: changing markets, changing products, Metals 12 (2022) 1959, https://doi.org/10.3390/met12111959.
- [4] Applications - Chassis & Suspension, Brake System; the Aluminium Automotive Manual, European-Aluminium Association, 2011. Available online: https://european-aluminium.eu/wp-content/uploads/2022/11/aam-applications-chassis-suspension-5-brake-system.pdf.
- [5] S.A. Awe, A. Thomas, The prospects of lightweight SICAlight discs in the emerging disc brake requirements, Eurobrake (2020) 1–8.
- [6] M.N. Ervina, H.J. Kong, C.K. Kok, Review: effect of alloying element on Al-Si alloys, Adv. Mater. Res. 845 (2013) 355–359. https://doi.org/10.4028/www.scientific.net/AMR.845.355.
- [7] S. Sharma, T. Nanda, O.P. Pandey, Investigation of T4 and T6 heat treatment on the wear properties of sillimanite reinforced LM30 aluminium alloy composites, Wear (2019) 426–427, https://doi.org/10.1177/13506501211036543, 27–36.
- [8] Y. Chen, Q. Hu, S. Pan, H. Zhang, H. Liu, B. Zhu, X. Liu, W. Liu, Influences of Cu content on the microstructure and strengthening mechanisms of Al-Mg-Si-xCu alloys, Metals 9 (5) (2019) 524, https://doi.org/10.3390/met9050524.
- [9] J. Zhang, A.T. Alpas, Transition between mild and severe wear in aluminium alloys, Acta Mater. 45 (1997) 513–528, https://doi.org/10.1016/S1359-6454(96)00191-7.
- [10] A. Pauschitz, M. Roy, F. Franek, Mechanisms of sliding wear of metals and alloys at elevated temperatures, Tribol. Int. 41 (7) (2008) 584–602, https://doi.org/10.1016/j.triboint.2007.10.003.
- [11] D. Culliton, A.J. Betts, D. Kennedy, Impact of intermetallic precipitates on the tribological and/or corrosion performance of cast aluminium alloys: a short review, Int. J. Cast Metals Res. 26 (2013) 65–71, https://doi.org/10.1179/1743133612Y.0000000038.
- [12] K.Y. Lee, S.L. Lee, C.T. Wu, W.C. Chen, J.C. Lin, Effects of T6 heat treatment on thermal stability and wear behaviour of Al-12.5Si-4.5Cu-1.0Mg alloy, Mater. Sci. Technol. 28 (2012) 639–643, https://doi.org/10.1179/1743284711Y.0000000057.
- [13] P.K. Dinesh, S. Darius, Aluminium-Silicon based Metal Matrix Composites for brake rotor applications: a review, Eng. Res. Express 5 (2023) 022002, https://doi.org/10.1088/2631-8695/accdb6.
- [14] S. Kumar, R. Pandey, R. Panwar, O.P. Pandey, Effect of particle size on wear of particulate reinforced aluminum alloy composites at elevated temperatures, J. Mater. Eng. Perform. 22 (11) (2013) 1–12, https://doi.org/10.1007/s11665-013-0642-8.
- [15] M.R. Schütte, J. Ehrich, D. Linsler, S. Hanke, Effects of microstructure modification by friction surfacing on wear behaviour of Al alloys with different Si contents, Materials 15 (2022) 1641, https://doi.org/10.3390/ma15051641.
- [16] B.E. Slattery, A. Edrisy, T. Perry, Investigation of wear induced surface and subsurface deformation in a linerless Al-Si engine, Wear 269 (3–4) (2010) 298–309, https://doi.org/10.1016/j.wear.2010.04.012.
- [17] P.K. Yadav, G. Dixit, S. Dixit, V.P. Singh, S.K. Patel, R. Purohit, B. Kuriachen, Effect of eutectic silicon and silicon carbide particles on high stress scratching wear of aluminium composite for various testing parameters, Wear 482–483 (2021) 3–13, https://doi.org/10.1016/j.wear.2021.
- [18] S. Aksoy, F. Kabakc, M. Acarer, H. Düzcükoğlu, E. Ünüvar, F. Fındık, Effect of Mg addition on microstructure and mechanical properties of AlSi12 alloy produced by high-pressure casting method, Ind. Lubric. Tribol. 75 (1) (2023) 27–35, https://doi.org/10.1108/ILT-10-2021-0410.
- [19] K. Kanayo, T. Moyosore, P. Apata, Corrosion and wear behaviour of Al-Mg-Si alloy matrix hybrid composites reinforced with rice husk ash and silicon carbide, J. Mater. Res. Technol. 3 (1) (2014) 9–16, https://doi.org/10.1016/j.jmrt.2013.10.008.
- [20] B. Chandra Mouli, D. Naresh, K.S.J. Prakash, A. Bala Krishna, Effect of copper content on wear properties of aluminium alloy, J. Chem. Pharmaceut. Sci. 10 (2) (2017) 1059–1071.
- [21] M.S. Prabhudeva, V. Auradi, K. Venkateswarlu, N.H. Siddalingswamy, S.A. Kori, Influence of Cu addition on dry sliding wear behaviour of A356 alloy, Procedia Eng. 97 (2014) 1361–1367, https://doi.org/10.1016/j.proeng.2014.12.417.
- [22] N. Kashimat, S. Sharma, R. Nayak, K.B. Manjunathaiah, M. Shettar, G. M. Chennegowda, Experimental investigation of mechanical property and wear behaviour of T6 treated A356 alloy with minor addition of copper and zinc, J. Compos. Sci. 7 (2023) 149, https://doi.org/10.3390/jcs7040149.
- [23] G. Timelli, A. Fabrizi, S. Vezzù, A. De Mori, Design of wear-resistant diecast AlSi9Cu3(Fe) alloys for high-temperature components, Metals 10 (55) (2020) 1–16, https://doi.org/10.3390/met10010055.
- [24] G. Timelli, Evolution of sludge particles in secondary die-cast aluminum alloys as function of Fe, Mn and Cr contents, Mater. Chem. Phys. 153 (2015) 168–179, https://doi.org/10.1016/j.matchemphys.2014.12.050.
- [25] M.L. Rahaman, L. Zhang, An investigation into the friction and wear mechanisms of aluminium high silicon alloy under contact sliding, Wear 376–377 (2017) 940–946, https://doi.org/10.1016/j.wear.2016.10.026.
- [26] J. Zhu, Z. Luo, S. Wu, H. Yan, The effect of Sr on the microstructure and wear properties of AlSi5Cu1Mg alloy, Adv. Mech. Eng. 10 (12) (2018) 1–10, https://doi.org/10.1177/1687814018819536.
- [27] Q. Zhang, S. Wei, J. Gu, M. Qi, High-temperature dry sliding wear behavior of Al-12Si-CuNiMg alloy and its Al2O3 fiber-reinforced composite, Met. Mater. Int. 9 (2021) 1–11, https://doi.org/10.1007/s12540-020-00654-4.
- [28] C. Fiell, P. Fiell, Friction, lubrication and wear technology, ASM Handb. 18 (2017) 1599–1617.
- [29] N.P. Suh, The delamination theory of wear, Wear 25 (1) (1973) 111–124, https://doi.org/10.1016/0043-1648(73)90125-7.
- [30] N.P. Suh, E.P. Abrahamson, A.P.L. Turner, Further investigation of the delamination theory of wear, J. Lubric. Technol. 96 (1974) 631–637, https://doi.org/10.1115/1.3452511.
- [31] C.R. Raghavgendra, Analysis of tribological behavior, pin temperature, and surface roughness of a brake pad material with nano coating, Tribology 197 (2024) 109727, https://doi.org/10.1016/j.triboint.2024.109727.
- [32] C.R. Raghavendra, S. Basavarajappa, I. Sogalal, Sliding wear behaviour of Ni-α-Al2O3 nano composite coating at elevated temperatures, Colloid Interface Sci. Commun. 27 (2018) 18–25, https://doi.org/10.1016/j.colcom.2018.09.003.
- [33] L. Wang, Y. He, J. Zhou, J. Duszczyk, Effect of temperature on the frictional behaviour of an aluminium alloy sliding against steel during ball-on-disc tests, Tribol. Int. 43 (2010) 299–306, https://doi.org/10.1016/j.triboint.2009.06.009.
- [34] G. Rajaram, S. Kumaran, T. Srinivasa Rao, High temperature tensile and wear behaviour of aluminum silicon alloy, Mater. Sci. Eng. 528 (2010) 247–253, https://doi.org/10.1016/j.msea.2010.09.020
- [35] M. Vilaseca, S. Molas, D. Casellas, High-temperature tribological behaviour of tool steels during sliding against aluminium, Wear 272 (1) (2011) 105–109, https://doi.org/10.1016/j.wear.2011.07.007.
- [36] L. Ceschini, A. Morri, S. Toschi, S. Johansson, S. Seifeddine, Microstructural and mechanical properties characterization of heat treated and overaged cast A354 alloy with various SDAS at room and elevated temperature, Mater. Sci. Eng. 648 (2015) 340–349, https://doi.org/10.1016/j.msea.2015.09.072.
- [37] V. Abouei, H. Saghafian, S.G. Shabestari, M. Zarghami, Efect of Fe-rich intermetallics on the wear behavior of eutectic Al-Si piston alloy (LM13), Mater. Des. 31 (2010) 3518–3524, https://doi.org/10.1016/j.matdes.2010.02.015.
- [38] R. Taghiabadi, H.M. Ghasemi, S.G. Shabestari, Effect of iron-rich intermetallics on the sliding wear behaviour of Al-Si alloys, Mater. Sci. Eng. 490 (2008) 162–170, https://doi.org/10.1016/j.msea.2008.01.001.
- [39] M. Dhiman, D.K. Dwivedi, R.S. Sehgal, I.K. Bhat, Effect of iron (wt.%) on adhesive wear response of Al-12Si-1Cu-0.1Mg alloy in dry sliding conditions, Trans. Indian Inst. Met. 61 (2008) 451–456.
- [40] C.R. Raghavgendra, K.P. Jhansilakshmi, Study on pin temperature and wear behaviour of plasma sprayed Ni-Cr coatings with nano Al2O3 particle, Int. J. Surf. Eng. Coating. 102 (2024) 215–228, https://doi.org/10.1080/00202967.2024.2326388.
- [41] C.R. Raghavgendra, Relationship between flash temperature and wear characteristics in Ni-nano Al2O3 coating, J. Adhes. Sci. Technol. 36 (2021) 1–16, https://doi.org/10.1080/01694243.2021.2010880.
- [42] E.C. Talibouya, M. Rosa, P. Sérgio, R. Martins, M.P. Martins da Cruz, V. Ferreira, Investigation of the effects of skewness Rsk and kurtosis Rku on tribological behavior in a pin-on-disc test of surfaces machined by conventional milling and turning processes, Mater. Res. 24 (2) (2021) 1–14, https://doi.org/10.1590/1980-5373-MR-2020-0435.
- [43] M. Krbata, M. Eckert, J. Majerik, I. Barenyi, Wear behaviour of high strength tool steel 90MnCrV8 in contact with Si3N4, Metals 10 (756) (2020), https://doi.org/10.3390/met1006075.
- [44] M. Stembalskin, P. Pres, W. Skoczynski, Determination of the friction coefficient as a function of sliding speed and normal pressure for steel C45 and steel 40HM, Arch. Civ. Mech. Eng. 13 (2013) 444–448, https://doi.org/10.1016/j.acme.2013.04.010.
- [45] J. Salguero, J.M. Vazquez-Martinez, I. Del Sol, M. Batista, Application of pin-on-disc techniques for the study of tribological interferences in the dry machining of A92024-T3 (Al-Cu), Alloys. Mater. 11 (7) (2018) 1236, https://doi.org/10.3390/ma11071236, 3–9.
- [46] R.N. Rao, S. Das, D.P. Mondal, G. Dixit, S.L.T. Devi, Dry sliding wear maps for AA7010 (Al-Zn-Mg-Cu) aluminium matrix composite, Tribol. Int. 60 (2013) 77–82, https://doi.org/10.1016/j.triboint.2012.10.007.
- [47] B.M. Satish, B.P. Shivakumar, M.B. Hanamantraygouda, Wear behaviour of hot forged SiC reinforced aluminium 6061Composite materials, Aust. J. Mech. Eng. 20 (2020) 425–432, https://doi.org/10.1080/14484846.2020.1714353.
- [48] J. Singh, A. Chauhan, Overview of wear performance of aluminium matrix composites reinforced with ceramic materials under the influence of controllable variables, Ceram. Int. 42 (1) (2016) 56–81, https://doi.org/10.1016/j.ceramint.2015.08.150.
- [49] M. Walczak, D. Pieniak, M. Zwierzchowski, The tribological characteristics of SiC particle reinforced aluminium composites, Arch. Civ. Mech. Eng. 15 (2015) 116–123, https://doi.org/10.1016/j.acme.2014.05.003.
- [50] Q. Chen, Y. Yu, G. Ma, X. Sun, L. Lu, Dry sliding wear behavior and mild-severe wear transition of the AA2195-T6 alloy under different loads, Crystals 13 (2023) 698, https://doi.org/10.3390/cryst13040698.
- [51] R. Gupta, S. Sharma, T. Nanda, O.P. Pandey, Wear studies of hybrid AMCs reinforced with naturally occurring sillimanite and rutile ceramic particles for brake-rotor applications, Ceram. Int. 46 (10) (2020) 16849–16859, https://doi.org/10.1016/j.ceramint.2020.03.262.
- [52] P.J. Blau, B.C. Jolly, J. Qu, W.H. Peter, C.A. Blue, Tribological investigation of titanium-based materials for brakes, Wear 263 (2007) 1202–1211, https://doi.org/10.1016/j.wear.2006.12.015.
- [53] A. Daoud, M.T. Abou El-khair, Wear and friction behavior of sand cast brake rotor made of A359-20 vol% SiC particle composites sliding against automobile friction material, Tribol. Int. 43 (2010) 544–553, https://doi.org/10.1016/j.triboint.2009.09.003.
- [54] S. Sharma, T. Nanda, O.P. Pandey, Effect of dual particle size (DPS) on dry sliding wear behaviour of LM30/sillimanite composites, Tribol. Int. 123 (2018) 142–154, https://doi.org/10.1016/j.triboint.2017.12.031.
- [55] M.J. Ghazali, W.M. Rainforth, H. Jones, The wear of wrought aluminium alloys under dry sliding conditions, Tribol. Int. 40 (2007) 160–169, https://doi.org/10.1016/j.triboint.2005.09.009.
- [56] M. Elmadagli, T. perry, A.T. Alpas, A parametric study of the relationship between microstructure and wear resistance of Al-Si alloy, Wear 262 (2007) 79–92, https://doi.org/10.1016/j.wear.2006.03.043.
- [57] A.K. Prasada, K. Das, B.S. Murty, M. Chakraborty, Microstructure and the wear mechanism of grain-refined aluminum during dry sliding against steel disc, Wear 264 (7–8) (2008) 638–647, https://doi.org/10.1016/j.wear.2007.05.010.
- [58] M.J. Ghazali, W.M. Rainfoth, M.Z. Omar, A comparative study of mechanically mixed layers (MMLs) characteristics of commercial aluminium alloys sliding against alumina and steel sliders, J. Mater. Process. Technol. 201 (2008) 662–668, https://doi.org/10.1016/j.jmatprotec.2007.11.158.
- [59] J.M. Sanchez, H. Galarraga, E. Del Molino, J. Albizuri, T. Guraya, S.W. Hudson, Microstructure and mechanical properties of two novel scrap tolerant Al65Cu10Mg10Si10Zn5 and Al80Cu5Mg5Si5Zn5 high entropy aluminum alloys, Intermetallics 162 (2023) 1–13, https://doi.org/10.1016/j.intermet.2023.10.
- [60] F. Bonollo, N. Gramegna, G. Timelli, High-pressure die-casting: contradictions and challenges, J. Occup. Med. 67 (2015) 901–908, https://doi.org/10.1007/s11837-015-1333-8.
- [61] S. Otarawanna, C.M. Gourlay, H.I. Laukli, A.K. Dahle, Formation of the surface layer in hypoeutectic Al-alloy high-pressure die castings, Mater. Chem. Phys. 130 (2011) 251–258, https://doi.org/10.1016/j.matchemphys.2011.06.035.
- [62] S. Mezlini, Ph Kapsa, C. Henon, J. Guillemenet, Abrasion of aluminium alloy: effect of subsurface hardness and scratch interaction simulation, Wear 257 (2004) 892–900, https://doi.org/10.1016/j.wear.2004.05.004.
- [63] T.M. Devenport, J.M. Griffin, B.F. Rolfe, M.P. Pereira, Friction and wear in stages of galling for sheet metal forming applications, Lubricants 11 (2023) 288, https://doi.org/10.3390/lubricants11070288.
- [64] ASTM International, ASTM G99-05 - Standard Test Method for Wear Testing with a Pin-On-Disk Apparatus, ASTM International, West Conshohocken, 2010, pp. 1–5.
- [65] G. Maculotti, E. Goti, G. Genta, L. Mazza, M. Galetto, Uncertainty-based comparison of conventional and surface topography-based methods for wear volume evaluation in pin-on-disc tribological test, Tribol. Int. 165 (2022) 1–18, https://doi.org/10.1016/j.triboint.2021.107260.
- [66] A. Torres Pérez, A. Hernández Battez, G. García-Atance, J.L. Viesca, R. González, M. Hadfield, Use of optical profilometry in the ASTM D4172 standard, Wear 271 (11–12) (2011) 2963–2967, https://doi.org/10.1016/j.wear.2011.06.016.
- [67] P. Pawlus, A. Dzierwa, Wear analysis of discs and balls on a micro-scale, Teh. Vjesn. 25 (2) (2018) 299–305, https://doi.org/10.17559/TV-20160530222544.
- [68] J. Gobrecht, Settling-out of Fe, Mn and Cr in Al-Si casting alloys, Giessereiforschung 62 (1975) 263–266.
- [69] J.L. Jorstad, Understanding sludge, Die Cast. Eng. 30 (1986) 30–36.
- [70] L. Sun, Y.Y. Guo, L. Chen, G.Q. Zhao, Effects of solution and ageing treatments on the microstructure and mechanical properties of cold rolled 2024 Al alloy sheet, J. Mater. Res. Technol. 12 (2021) 1126–1142, https://doi.org/10.1016/j.jmrt.2021.03.051.
- [71] Y.J. Kwon, I. Shigematsu, N. Saito, Mechanical property improvements in aluminum alloy through grain refinement using friction stir process, Mater. Trans. 45 (2004) 2304–2311.
- [72] B.J. Jung, H.K. Lee, H.C. Park, Effect of grain size on the indentation hardness for polycrystalline materials by the modified strain gradient theory, Int. J. Solid Struct. 50 (2013) 2719–2724.
- [73] Y. Liu, S. Ma, M.C. Gao, C. Zhang, T. Zhang, H. Yang, Z. Wang, J. Qiao, Tribological properties of AlCrCuFeNi2 high-entropy alloy in different conditions, Metall. Mater. Trans. A Phys. Metall. Mater. Sci. 47 (2016) 3312–3321, https://doi.org/10.1007/s11661-016-3396-8.
- [74] W. Hong, W. Cai, S. Wang, M. Tomovic, Mechanical wear debris feature, detection, and diagnosis: a review, Chin. J. Aeronaut. 31 (5) (2018) 867–882, https://doi.org/10.1016/j.cja.2017.11.016.
- [75] H.L. Costa, M.M. Oliveira Junior, J.D.B. de Mello, Effect of debris size on the reciprocating sliding wear of aluminium, Wear 376–377 (2017) 1399–1410, https://doi.org/10.1016/j.wear.2016.10.025.
- [76] M.M. De Oliveira, H.L. Costa, W.M. Silva, J.D.B. De Mello, Effect of iron oxide debris on the reciprocating sliding wear of tool steels, Wear 426–427 (2019) 1065–1075, https://doi.org/10.1016/j.wear.2018.12.047.
- [77] H.J. Kim, W. Windl, D. Rigney, Structure and chemical analysis of aluminum wear debris, Acta Mater. 55 (19) (2007) 6489–6498, https://doi.org/10.1016/j.actamat.2007.08.013.
- [78] Μ.Ο.Α. Mokhtar, The effect of hardness on the frictional behaviour of metals, Wear 78 (1982) 297–304, https://doi.org/10.1016/0043-1648(82)90240-X.
- [79] S. Martin, S. Kandermir, M. Antonov, Investigation of the high temperature dry sliding wear behavior of graphene nanoplatelets reinforced aluminum matrix composites, J. Compos. Mater. 0 (2020) 1–14, https://doi.org/10.1177/0021998320979037.
- [80] H. Zhu, C. Jar, J. Song, J. Zhao, J. Li, Z. Xie, High temperature dry sliding friction and wear behavior of aluminum matrix composites (Al3Zr+Al2O3)/Al, Tribology 48 (2012) 78–86, https://doi.org/10.1016/j.triboint.2011.11.011.
- [81] C. Bellini, V. Cpccp, D. Lacoviello, F. Lacoviello, Temperature influence on brake pad friction coefficient modelisation, Materials 17 (2024) 189, https://doi.org/10.3390/ma17010189.
- [82] N. Valizade, Z. Farhat, A review on abrasive wear of aluminum composites: mechanisms and influencing factors, J. Compos. Sci. 8 (2024) 149, https://doi.org/10.3390/jcs8040149.
- [83] Classification of wear processes, Tribol. 10 (1987) 80–131, https://doi.org/10.1016/S0167-8922(08)70722-3.
- [84] Y. Ozmen, Micromechanical approach to wear mechanisms, J. Eng. Sci. 2 (1995) 145–152.
- [85] A. Fischer, W. Dudzinski, B. Gleising, P. Stemmer, Analyzing mild- and ultra-mild sliding wear of metallic materials by transmission electron microscopy, Adv. Anal. Methods Tribol. 2 (2018) 29–59.
- [86] V.F. Sousa, F.J.G. Silva, Recent advances on coated milling tool technology—a comprehensive review, Coatings 10 (2020) 235, https://doi.org/10.3390/coatings10030235.
- [87] K.H. Zum, Microstructure and wear of materials, Tribol. 10 (1987) 1–560.
- [88] Z.B. Yusoff, S.B. Jamaludin, Tribology and development of wear theory: review and Discussion, in: Conf: Int. J. Curr. Res. Rev 3, 2011. India.
- [89] M.A. Wimmer, M.P. Laurent, Tribology of the Artificial Hip, vol. 3, Fastest Musculoskeletal Insight Engine, 2016.
- [90] N. Radhika, S. Ramanathan, S.V. Prasat, B. Anandavel, Dry sliding wear behaviour of aluminium/alumina/graphite hybrid metal matrix composites, Ind. Lubric. Tribol. 64 (2012) 259–366, doi.org/110.1108/00368791211262499.
- [91] M.H. Abdelaziz, H.W. Doty, S. Valtierra, F.H. Samuel, Static versus dynamic thermal exposure of transition elements-containing Al-Si-Cu-Mg cast alloy, Mater. Sci. Eng., A 739 (2019) 499–512, https://doi.org/10.1016/j.msea.2018.09.096.
- [92] L. Ceschini, A. Morri, S. Toschi, S. Johansson, S. Seifeddine, Effect of microstructure and overaging on the tensile behavior at room and elevated temperature of C355-T6 cast aluminum alloy, Mater. Des. 83 (2015) 626–634, https://doi.org/10.1016/j.matdes.2015.06.031.
- [93] C. Cai, H.F. Geng, S.F. Wang, B.X. Gong, Z. Zhang, Microstructure evolution of AlSi10Mg (Cu) alloy related to isothermal exposure, Materials 11 (5) (2018) 809, https://doi.org/10.3390/ma11050809, 1–13.
- [94] Bo Lin, Haoyu Li, Rui Xu, Yuliang Zhao, Huaqiang Xiao, Zhengqiang Tang, Shaobo Li, Thermal exposure osure of Al-Si-Cu-Mn-Fe alloys and its contribution to high temperature mechanical properties, J. Mater. Res. Technol. 9 (29) (2020) 1856–1865, https://doi.org/10.1016/j.jmrt.2019.12.018.
- [95] S.H. Rhee, K.C. Ludema, Mechanisms of formation of polymeric transfer films, Wear 46 (1978) 231–240.
- [96] G. Plasensia, A.T. Utigard, High temperature oxidation mechanism of dilute copper aluminium alloys, Corrosion Sci. 47 (2005) 1149–1163, https://doi.org/10.1016/j.corsci.2004.06.031.
9. Copyright:
- This material is a paper by "Ester Villanueva, Iban Vicario, Joseba Albizuri, Gurutze Arruebarrena, Teresa Guraya". Based on "Wear properties of a new Al80Mg10Si5Cu5 multicomponent alloy".
- Source of the paper: https://doi.org/10.1016/j.wear.2024.205585
This material is summarized based on the above paper, and unauthorized use for commercial purposes is prohibited.
Copyright © 2025 CASTMAN. All rights reserved.