Qian Zhang, Huijuan Liu, Member, IEEE, Zhenyang Zhang and Tengfei Song
Abstract
According to the demands of the small commercial electric vehicle (EV) traction driving system, an 18kW inverter-driven induction motor (IM) with a die-casting copper squirrel cage rotor for traction drive was designed and evaluated.
The 2D finite element model of the designed IM was built by considering the nonlinearity of core materials, and the geometric parameters of the motor were optimized. The operational performance of torque versus speed characteristics and the efficiency over the speed range under the rated (continuous) and overload condition were investigated.
Finally, the designed inverter-driven IM was developed and the performance of the IM operating in three typical modes were tested respectively.
The experimental results of the designed motor operating in various driven mode were compared with that of 2D FEM.
All the results proved that the designed inverter-driven IM could meet the target specification of the small commercial EV.
Korea Abstract
소형 상용 전기자동차(EV) 트랙션 구동 시스템의 요구 사항에 따라 트랙션 드라이브용 다이캐스팅 구리 농형 로터가 있는 18kW 인버터 구동 유도 전동기(IM)를 설계하고 평가했습니다. 설계한 IM의 2차원 유한요소모델은 코어재료의 비선형성을 고려하여 구축하였으며, 모터의 기하학적 파라미터를 최적화하였다. 정격(연속) 및 과부하 조건에서 속도 범위에 따른 토크 대 속도 특성의 작동 성능과 효율을 조사했습니다. 마지막으로 설계된 인버터 구동 IM을 개발하고 3가지 일반적인 모드에서 동작하는 IM의 성능을 각각 시험하였다. 다양한 구동 모드에서 작동하는 설계된 모터의 실험 결과를 2D FEM의 실험 결과와 비교했습니다. 모든 결과는 설계된 인버터 구동 IM이 소형 상용 EV의 목표 사양을 충족할 수 있음을 입증했습니다.
Keywords
Casting copper rotor, electric vehicle(EV), FEM, IM.
INTRODUCTION
DUE to growing air pollution in urban areas, global warming caused by greenhouse gases as well as limited resources of fossil energy, and environmental protection was paid more attention, development of electric vehicles (EVs) have become a hot topic in automobile industry and some fields of transportation applications, e.g. forklifts, golf carts trolley bus and so on, around the world [1-3]. Although EVs suffer from issues such as a limited driving range due to the lower energy storage density of batteries compared with gasoline, and taking more time for batteries charging compared with gasoline filling. With rapid development of lithium ion batteries and the infrastructure popularization of charging station, EV would become be the best and ultimate solution. Technology development for EV motors which form the core energy conversion components has gone a long way and progressed tremendously within the last two decades [4-7]. However, a typical EV motor still suffers from several key issues such as torque density in terms of weight and volume; region of torque-speed capability; energy efficiency; reliability; and costs in manufacturing and maintenance. Currently, EVs are often equipped with induction motors (IMs) or interior permanent magnet synchronous motors (IPMs) [8-9].
IPM motor is considered to have a higher torque density, higher power density and higher efficiency with respect to IMs. However, in order to achieve much larger overload torque over the speed range [10], a safer back electromotive force (EMF) of high speed uncontrolled generator operation [11] and little sensitivity to PM temperature, the rotor of the IPM must be designed with multiple flux barriers for having a high saliency, which might look complicated industrial wise. In addition, the permanent magnet has the risk of demagnetization, and the costs of permanent magnet material and manufacturing of IPMs are higher than that of IMs.
IPMs are adopted for their simple structure, high reliability, ruggedness, and universal availability, and the field-oriented vector control strategy is considered as an industrial standard. Moreover, IMs are naturally de-excited under the condition of inverter fault, and this is an important reason that extremely welcome among EV manufacturers, for safety.
The squirrel cage rotor of induction motor is usually built with aluminum bars or copper bars. Die-casting of the squirrel cage is a manufacturing technology, which can make the cage bars directly connected to the end rings. The manufacturing technology of aluminum die-casting rotor cage can be dated back to 1916 [12]. The manufacturing technology of copper die-casting rotor cage increased the costs of IM for a manufacturer because of the high melting point of copper which made the die life significantly short in the past. Recent researches improved the copper die-casting manufacturing technology and some products for improving the motor efficiency are now on the market [13-16].
According to the demands of the small commercial EV traction driving system, an 18kW inverter-driven IM with cast copper rotor was designed, a 2D finite element model of the motor, which considered the nonlinearity of the core material, was investigated. The geometric parameters of the motor, such as the width of slot opening, air gap length and slot skewed, were optimized. The torque versus speed characteristics and the efficiency of the whole speed range were calculated by 2D FEM. Finally, prototype motor was developed and the performance testing was completed on the experimental platform. The performance when the designed IM operating in various driven mode simulated by FEM was then verified by experimental results to confirm the validity of the methods.
TRANSMISSION SYSTEM OF VEHICLE
The basic configuration of the transmission system for small commercial EV is shown in Fig.1. The wheels are driven by an IM through a transmission, and the IM of electric vehicle is driven by lithium batteries through DC-AC inverter. In addition to normal traction, the IM can work in the state of power generation, the mechanical energy of light-load and the kinetic energy of braking could be regenerate and reuse for the characteristic of four quadrant operation of the converter, which can improve the energy efficiency, extend the driving range of the EV.
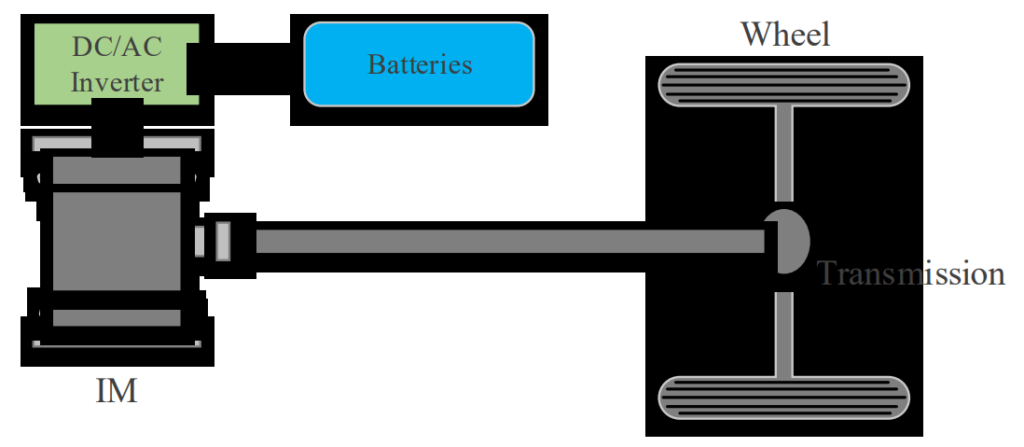
The torque characteristics of traction IM determine the vehicle running performance including vehicle acceleration, hill climbing ability and maximum speed. As shown in Fig.2, the actual torque characteristics curves of the small commercial EV traction motor contain rated and overload operation conditions. Both continuous curve (solid line) and overload (dashed line) curve have constant torque and constant power zones. It can be seen that EV requires a constant torque operating region to start and uphill march at low speed, while a constant power operating region at higher vehicle speed. The rated power P1 at maximum speed determines the maximum speed of the EV. The continuous torque T1 determines the maximum slope that the EV can climb continuously. Transient overload torque T0 is limited by the inverter current rating, and transient overload power is limited by the combination of voltage and current limits.
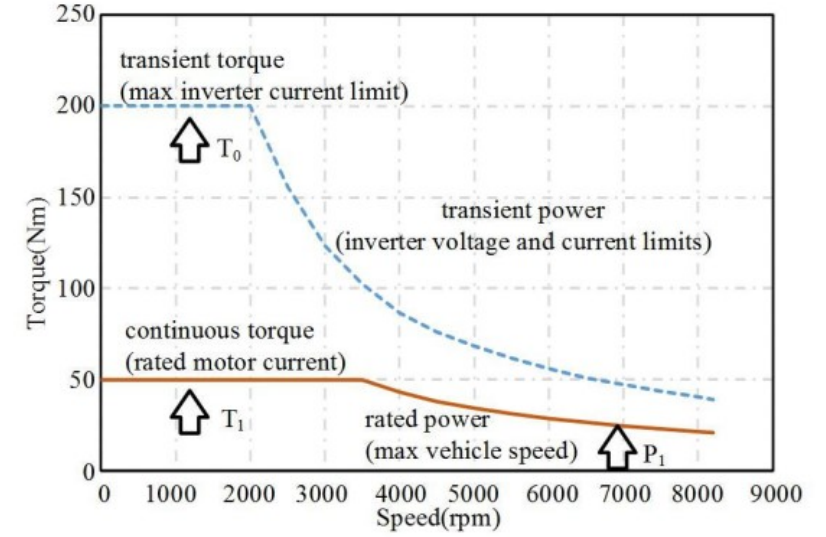
The IM rated torque can be achieved by keeping a constant voltage-frequency ratio in the constant torque region. In this region, with the increase of supply voltage, the IM output
power increases linearly. Because the supply voltage magnitude is limited by the allowable maximum voltage provided, the voltage-frequency ratio is no longer constant even if the supply frequency keeps increasing at the corner speed, and then, the IM enters into the constant power operation region in which the motor current is constant while the air-gap flux reduces inversely proportional to the supply frequency, and the torque decreases inversely proportional to the speed of IM.
EVs are usually equipped with totally enclosed type motor in order to obtain better protection performance and prevent the external muddy water from damaging the EV motors. Due to the wide IM speed range and limitation of installation space, the cooling of motor designed in this paper is no longer dependent on the cooling fan on shaft, but on the aluminum alloy shell with the radiating rib of the motor which improves the cooling effect by the air flow in the motion of the EV. The equally distributed ventilation holes of rotor promote the cooling effect, and reduce the quality of IM.
...
...
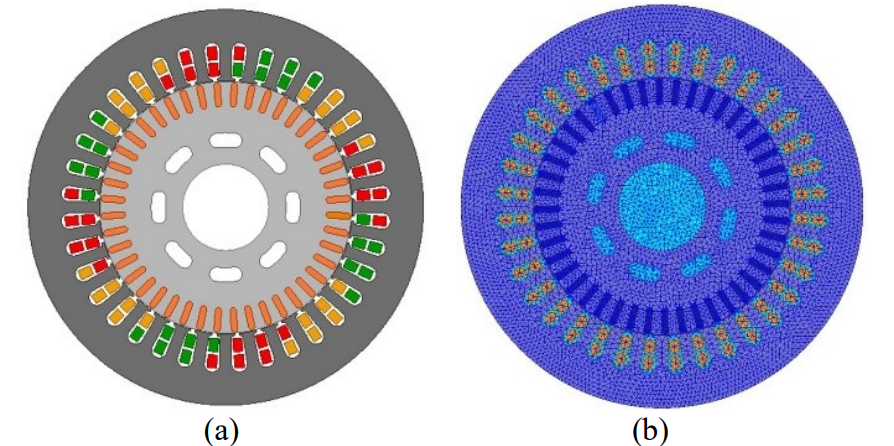
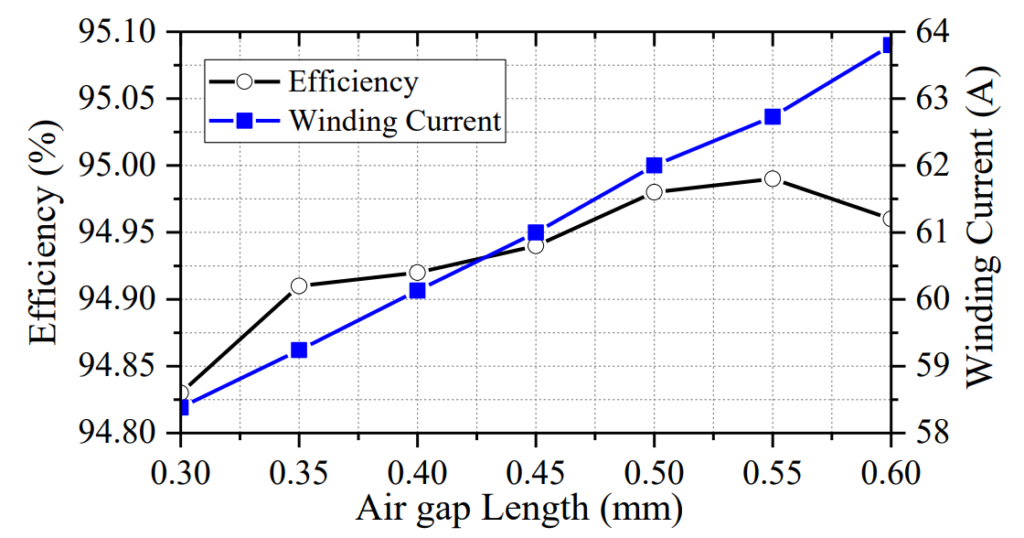
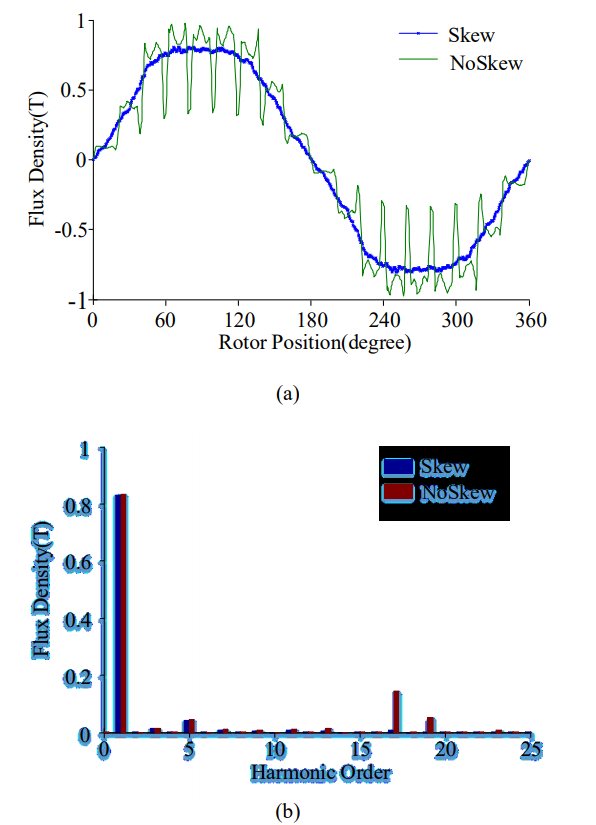
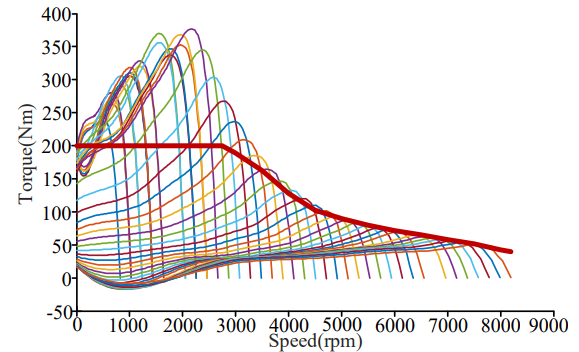
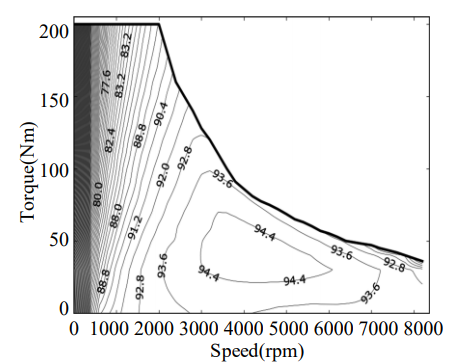
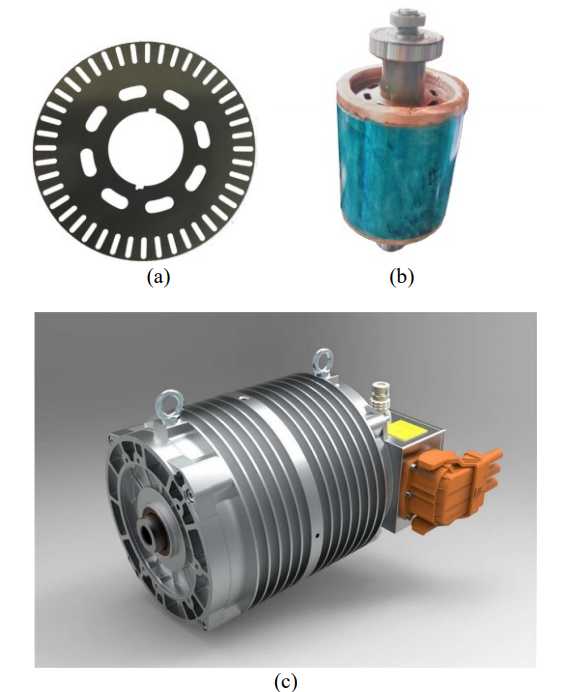
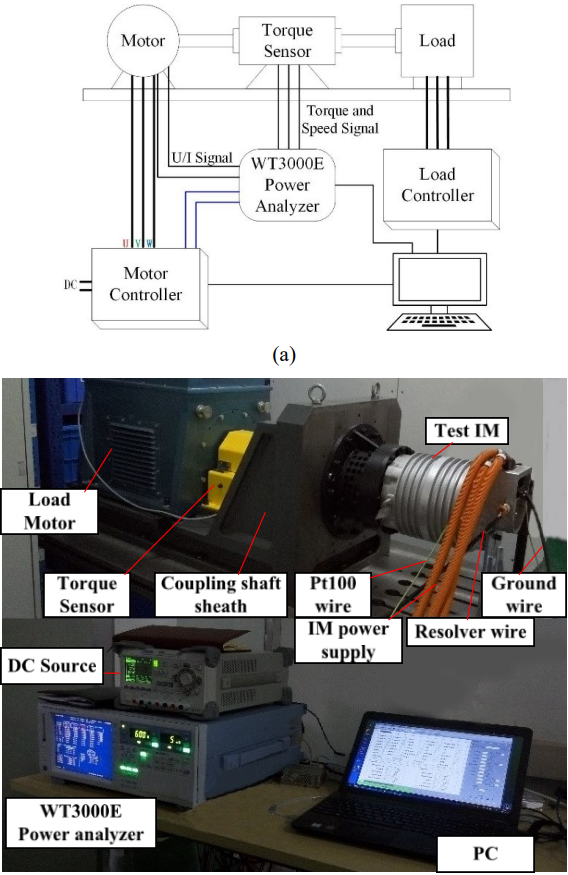
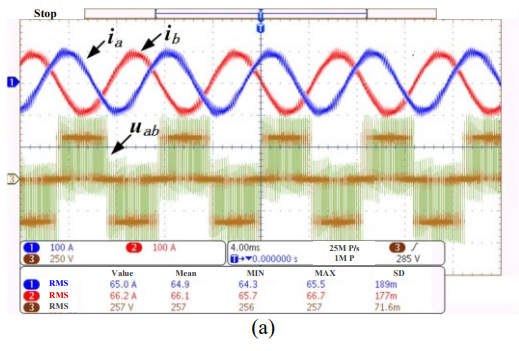
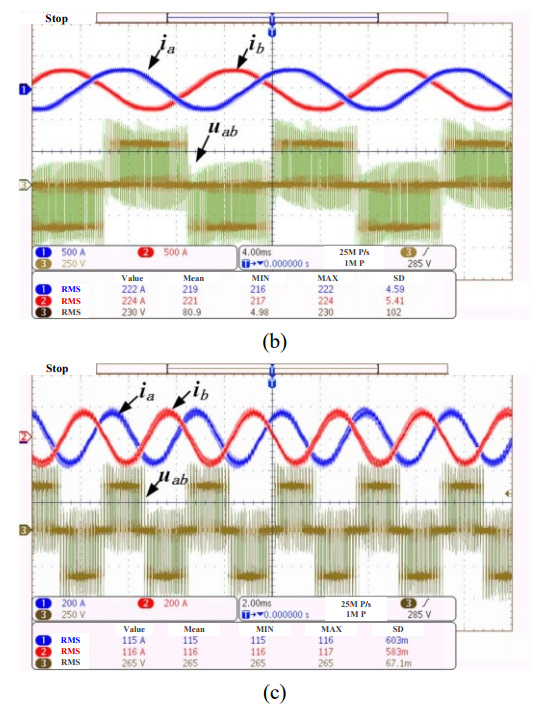
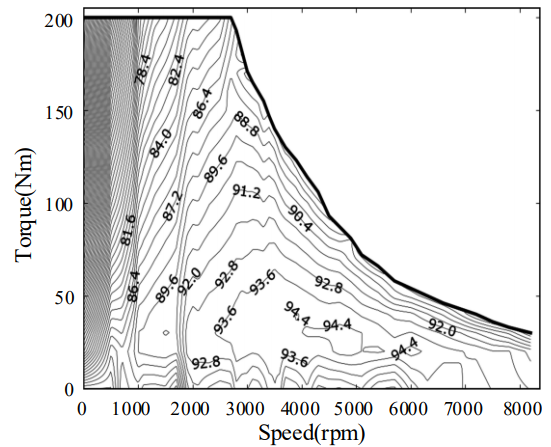
REFERENCES
[1] M. Zeraoulia, M. Benbouzid, and D. Diallo, “Electric motor drive selection issues for HEV propulsion systems: A comparative study,” IEEE Transactions on Vehicular Technology, vol. 55, no. 6, pp. 1756-1764, Nov. 2006.
[2] Z. Q. Zhu, and Q. Q. Chan, “Electrical machine topologies and technologies for electric, hybrid, and fuel cell vehicles,” in Proc. IEEE
VPPC, Harbin, China, pp. 1-6, Sep. 2008.
[3] I. Boldea, L. N. Tutelea, L. Parsa, and D. Dorrell, “Automotive electric propulsion systems with reduced or no permanent magnets: an overview,” IEEE Transactions on Industrial Electronics, vol. 61, no. 10, pp. 5696-5711, Oct. 2014.
[4] A. Emadi, Y. J. Lee, and K. Rajashekara, “Power electronics and motor drives in electric, hybrid electric, and plug-in hybrid electric vehicles,” IEEE Transactions Industrial Electronics, vol. 55, no. 6, pp. 2237-2245, Jun. 2008.
[5] F. L. Mapelli, D. Tarsitano, and M. Mauri, “Plug-in hybrid electric vehicle: modeling, prototype, realization, and inverter losses reduction analysis,” IEEE Transactions Industrial Electronics, vol. 57, no. 2, pp. 598-607, Feb. 2010.
[6] A. Y. Saber, G. K. Venayagamoorthy, “Plug-in vehicles and renewable energy sources for cost and emission reductions,” IEEE Transactions Industrial Electronics, vol. 58, no. 4, pp. 1229-1238, Apr, 2011.
[7] D. J. Thrimawithana, U. K. Madawala, “A novel matrix converter based bi-directional IPT power interface for V2G applications,” in Proc. IEEE IEC, Manama, Bahrain, pp. 495-500, Dec. 2010.
[8] Z. Q. Zhu, D. Howe, “Electrical machines and drives for electric, hybrid, and fuel cell vehicles,” Proceedings of the IEEE, vol. 95, no. 4, pp. 746-765, Apr. 2007.
[9] K. T. Chau, C.C. Chan, C. H. Liu, “Overview of Permanent-Magnet Brushless Drives for Electric and Hybrid Electric Vehicles,” IEEE Transactions Industrial Electronics, vol. 55, no. 6, pp. 2246-2257, Jun. 2008.[10] G. Pellegrino, A. Vagati, P. Guglielmi, and B. Boazzo, “Performance comparison between surface-mounted and interior PM motor drives for electric vehicle application,” IEEE Transactions Industrial Electronics, vol. 59, no. 2, pp. 803-811, Feb. 2012.
[11] T. M. Jahns, V. Caliskan, “Uncontrolled generator operation of interior PM synchronous machines following high-speed inverter shutdown,” IEEE Transactions on Industry Applications, vol. 35, no. 6, pp. 1347-1357, Nov/Dec. 1999.
[12] P. L. Alger, R. E. Arnold, “History of Induction Motors in America,”
Proceedings of the IEEE, vol. 64, no. 9, pp. 1380-1383, Sep. 1976.
[13] E. B. Agamloh, A. Cavagnino, “High efficiency design of induction machines for industrial applications,” in Proc. IEEE WEMDCD, Paris, France, pp. 33-46, Mar. 2013.
[14] K. J. Park, K. Kim, S. Lee, D. Koo, K. Ko; and J. Lee, “Optimal design of rotor slot of three phase induction motor with die-cast copper rotor cage,” in Proc. ICEMS, Wuhan, China, pp. 61-63, Oct. 2008.
[15] J. L. Kirtley, J. G. Cowie, E. F. Brush, D. T. Peters, and R. Kimmich, “Improving Induction Motor Efficiency with Die-cast Copper Rotor Cages,” in Proc. IEEE PESG, Tampa, America, pp. 1-6, Jun. 2007.
[16] Ashwin D, Ashok S, M. Dixit, and V. Chavan, “Design optimization of 15 kW, 2-pole induction motor to achieve IE4 efficiency level with copper die-casting,” in Proc. ICTAP Energy, Kollam, India, pp. 98-102, Jun. 2015.
[17] S. K. Chen, “Design of the Electrical Machines,” 2nd ed., Beijing: China Machine Press, 2000, pp.231-237.
[18] Z. G. Huang, F. L. Fu, “Handbook of small and medium sized rotating machines design,” 2nd ed., Beijing: China Electric Power Press, 2014, pp.45-46.
[19] G. Z. Huang, F. L. Fu, “Y2 series three-phase asynchronous motors technical manual,” Beijing: China Machine Press, 2004.
[20] D. Lin; P. Zhou, W. N. Fu, Z. Badics, Z. J. Cendes, “A Dynamic Core Loss Model for Soft Ferromagnetic and Power Ferrite Materials in Transient Finite Element Analysis,” IEEE Transactions on Magnetics, vol. 40, no. 2, pp. 1318-1321, Mar, 2004.
[21] H. Guan, Z. M. Zhao, S. Meng, and X. D. Wu, “Optimal design for inverter-driven induction motors,” Proceedings of the CSEE, vol. 24, no.7, pp.194-199, Jul. 2004.
[22] Zhao, N., and N. Schofield, “An improved induction machine design procedure for electric vehicle traction,” in Proc. PEMD, pp.1-6, Apr. 2016.