This article introduces the paper ["INFLUENCE OF INJECTION PARAMETERS ON THE POROSITY AND TENSILE PROPERTIES OF HIGH-PRESSURE DIE CAST AI-SI ALLOYS: A REVIEW"] published by ["International Journal of Metalcasting"].
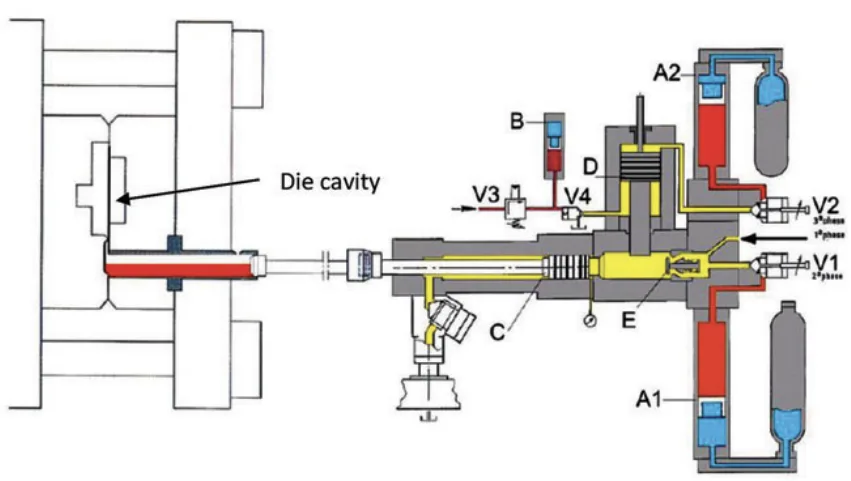
1. Overview:
- Title: INFLUENCE OF INJECTION PARAMETERS ON THE POROSITY AND TENSILE PROPERTIES OF HIGH-PRESSURE DIE CAST AI-SI ALLOYS: A REVIEW
- Author: Anilchandra R. Adamane, Lars Arnberg, Elena Fiorese, Giulio Timelli, Franco Bonollo
- Publication Year: 2015
- Publishing Journal/Academic Society: International Journal of Metalcasting/Volume 9, Issue 1, 2015
- Keywords: foundry aluminum alloys, high-pressure die casting, injection parameters, porosity, tensile properties, HPDC
2. Abstracts or Introduction
Aluminum-Silicon alloys are extensively utilized as Al foundry alloys and are prevalent in high-pressure die casting (HPDC) for automotive components. Achieving sound and reliable castings in HPDC necessitates the control of several process parameters. Among these, injection parameters, specifically gate velocity and intensification pressure (IP), are critical throughout the HPDC process. This paper critically reviews the impact of injection parameters on porosity and tensile properties in die castings. The review summarizes literature findings and suggests optimal values for gate velocity and IP.
3. Research Background:
Background of the Research Topic:
High-pressure die casting (HPDC) is highlighted as a cost-effective method for producing large quantities of castings with high dimensional accuracy. A primary challenge in HPDC is the entrapment of gas and oxides due to turbulent metal flow during die cavity filling, leading to porosity and reduced casting quality. The injection process in cold chamber HPDC involves injecting molten metal into the die cavity using a hydraulic piston-cylinder system. Fine control over plunger movements is achieved through valves and gas accumulators.
Status of Existing Research:
Existing literature on HPDC of Al-Si alloys largely focuses on casting parameters affecting microstructure and tensile behavior, particularly injection phase variables. Gate velocity and intensification pressure are identified as key injection parameters. While vent and overflow design is crucial for casting quality, limited research directly links vent design to porosity distribution or tensile properties. Many parameters are interrelated and can be optimized using numerical simulation software.
Necessity of the Research:
Understanding and optimizing injection parameters is crucial for enhancing the quality of HPDC Al-Si alloy castings. A comprehensive review of the influence of injection parameters on porosity and tensile properties is needed to guide process optimization and improve casting reliability.
4. Research Purpose and Research Questions:
Research Purpose:
The primary research purpose is to critically review and summarize the effects of injection parameters, specifically gate velocity and intensification pressure, on the porosity and tensile properties of high-pressure die cast Al-Si alloys, based on existing literature.
Key Research:
- To analyze the influence of gate velocity on porosity and tensile strength of HPDC Al-Si alloys.
- To investigate the impact of intensification pressure on porosity and tensile strength of HPDC Al-Si alloys.
- To review the effect of runner and gate designs on melt flow and casting quality in HPDC.
- To identify optimal ranges for gate velocity and intensification pressure based on the literature.
Research Hypotheses:
Based on the paper's content, it is implicitly hypothesized that:
- Higher gate velocity, up to an optimal point, reduces porosity and improves tensile properties in HPDC Al-Si alloys.
- Increased intensification pressure reduces porosity and enhances tensile properties in HPDC Al-Si alloys.
- Runner and gate designs significantly affect melt flow patterns, influencing porosity distribution and casting quality.
5. Research Methodology
Research Design:
This research employs a literature review design. It systematically examines and synthesizes findings from existing research papers, technical articles, and industry publications related to the influence of injection parameters on the properties of high-pressure die cast Al-Si alloys.
Data Collection Method:
The data collection method involves gathering information from published literature focusing on experimental studies, numerical simulations, and industrial practices related to HPDC and injection parameters. The sources include academic journals, conference proceedings, technical reports, and handbooks in the field of die casting and metallurgy.
Analysis Method:
The analysis method is qualitative and involves critical review and synthesis of the collected literature. The authors analyze and compare findings from different studies to identify trends, contradictions, and consensus regarding the effects of gate velocity, intensification pressure, and runner/gate designs on porosity and tensile properties. The review aims to summarize the current state of knowledge and suggest optimal parameter ranges based on the analyzed literature.
Research Subjects and Scope:
The research focuses on high-pressure die casting (HPDC) of Aluminum-Silicon (Al-Si) alloys. The scope is limited to the influence of injection parameters, specifically gate velocity and intensification pressure, and runner/gate designs on porosity and tensile properties of these alloys. The review encompasses literature discussing experimental results, simulation studies, and practical applications within this specific domain.
6. Main Research Results:
Key Research Results:
- Gate Velocity Effects:
- Increasing gate velocity generally reduces cavity filling time.
- Optimal gate velocity exists for minimizing porosity. Both excessively low and high velocities can increase porosity.
- Higher gate velocities tend to improve tensile strength and ductility, and reduce the scatter in strength values.
- The percentage of smaller pores (< 20µm) increases with gate velocity, while larger pores (> 100 µm) can be eliminated at higher velocities.
- Intensification Pressure (IP) Effects:
- Higher IP significantly reduces porosity content and improves casting density.
- Combining appropriate gate thickness and IP is crucial for minimizing porosity.
- High IP may lead to shear bands in the microstructure near the gate.
- Higher IP is more effective than melt velocity in controlling porosity.
- Runner and Gate Design:
- Runner-gate system design is critical for controlling melt flow and casting quality.
- Different runner-gate types (Linear, Fan, T-shaped, Split) influence die cavity filling patterns and porosity distribution.
- Fan-type gates can lead to higher velocity along die cavity walls and gas entrapment in certain regions.
- Tangential gate delivery systems can be more efficient for uniform filling and reduced turbulence.
Analysis of presented data:
- Porosity vs. Gate Velocity (Figure 5): Figure 5 shows the change in porosity content with different gate velocities. Data from Gunasegaram et al. [17] and Ghomashchi [19] indicate that porosity initially decreases with increasing gate velocity, but may plateau or slightly increase at very high velocities. This suggests an optimal gate velocity range for minimizing porosity.
- Tensile Properties vs. Gate Velocity (Figure 6 & 7): Figure 6 and 7 illustrate the improvement in tensile strength and ductility with increasing gate velocity. Figure 6 shows tensile test curves at different gate velocities, indicating higher strength and elongation at higher velocities. Figure 7 summarizes data from multiple studies, consistently showing improved tensile properties with increased gate velocity.
- Density vs. Intensification Pressure (Figure 10 & 11): Figure 10 demonstrates that density increases with increasing intensification pressure. Different curves represent varying injection plunger velocities, showing that higher IP consistently leads to higher density. Figure 11 visually compares castings produced under "Worst" and "Best" density conditions, highlighting reduced visible porosity with higher density (achieved with higher IP).
- Gate Freezing Time (Figure 12): Figure 12 shows the effect of intensification pressure and gate velocity on gate freezing time. Increasing IP increases gate freezing time, while increasing gate velocity initially decreases it and then plateaus. This indicates that IP is more effective in extending gate freezing time compared to gate velocity.
Figure Name List:
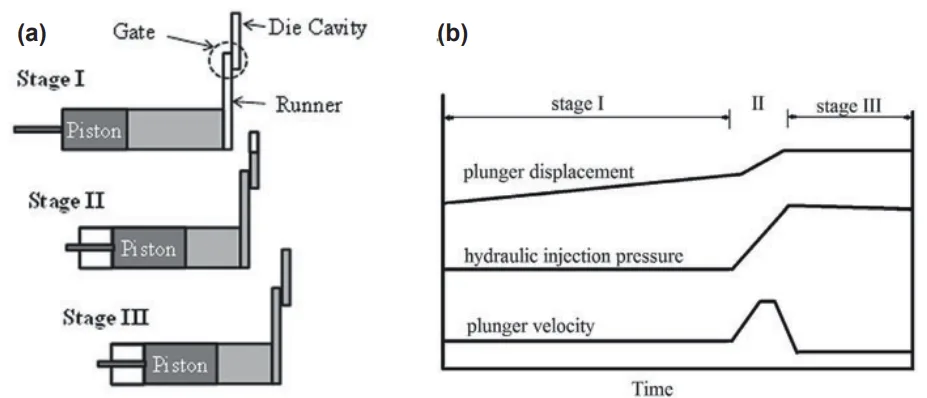
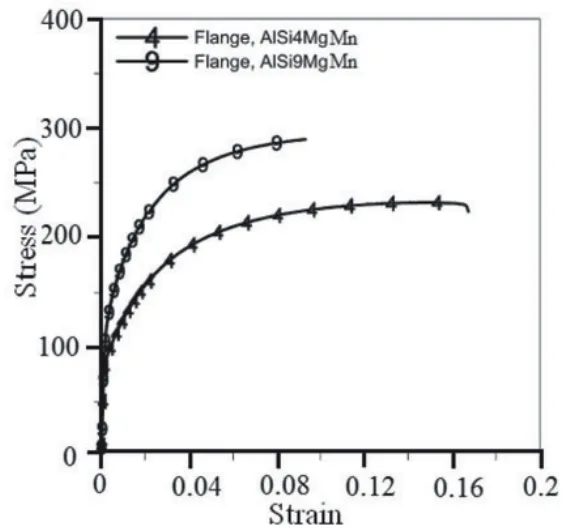

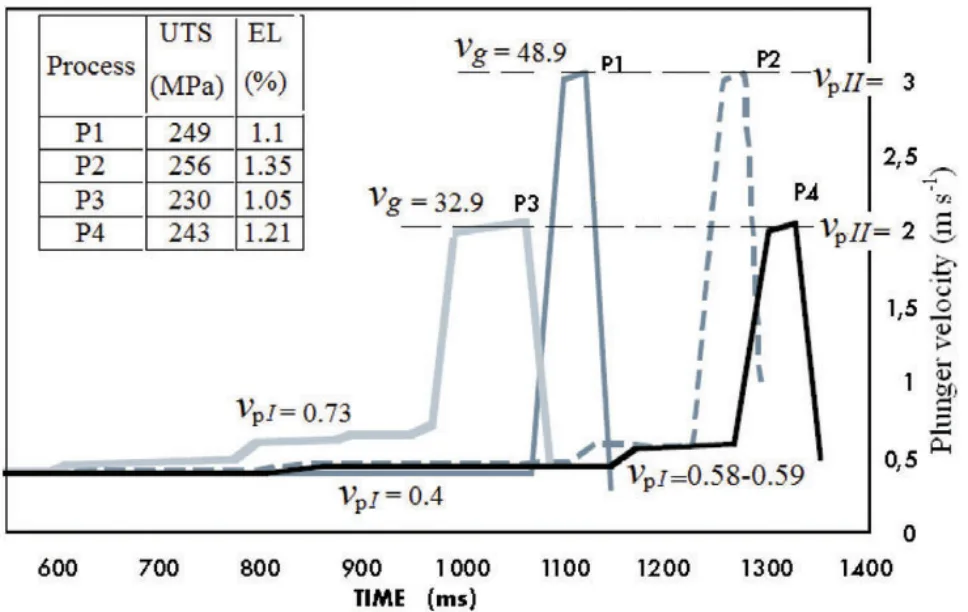
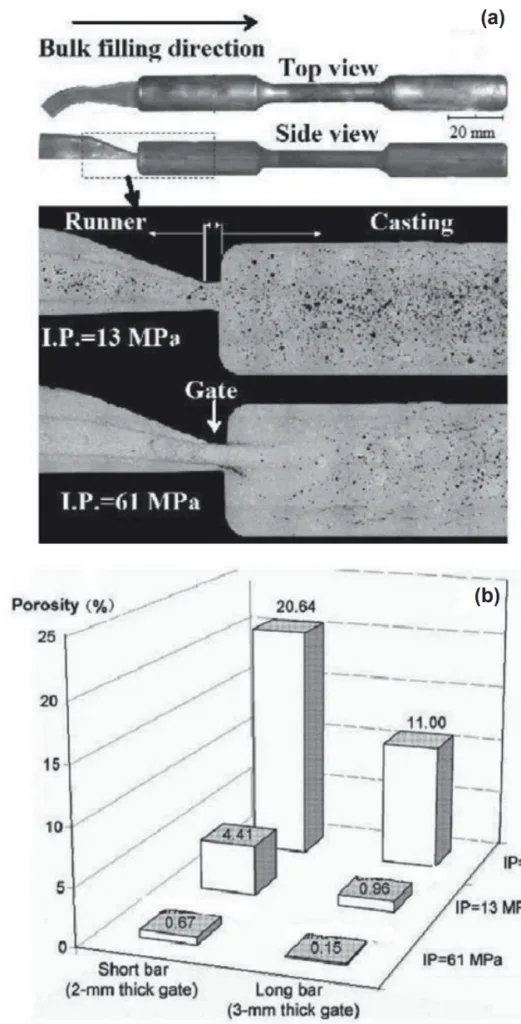

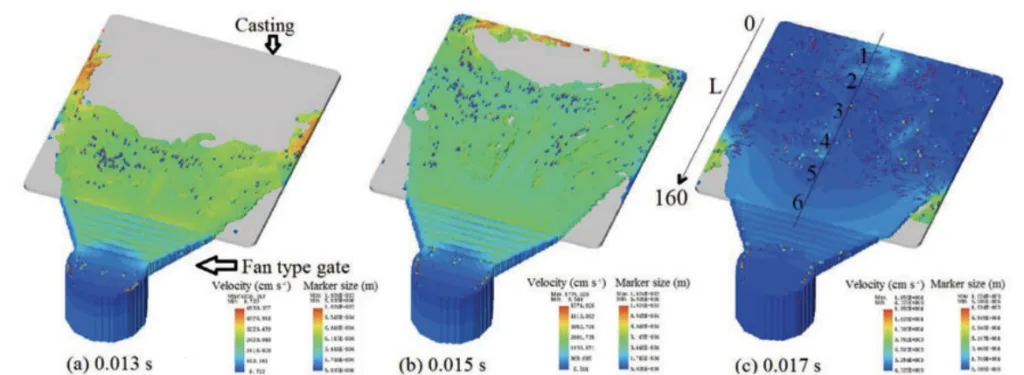
Figure 4. Tensile stress-strain curves of three different
AlSi9Cu3(Fe) castings with density values indicated
within the parentheses (g cm-3).4 Lower density castings
show reduced strength properties owing to higher
casting defects.
- Figure 1. Schematic illustration of hydraulic injection system.¹
- Figure 2 (a) Schematic representation of the plunger movement during HPDC and (b) the corresponding change in velocity and pressure at different stages.
- Figure 3. Engineering stress-strain curves of high pressure die-cast AlSi4MgMn and AlSi9MgMn alloys.³
- Figure 4. Tensile stress-strain curves of three different AlSi9Cu3(Fe) castings with density values indicated within the parentheses (g cm³).⁴ Lower density castings show reduced strength properties owing to higher casting defects.
- Figure 5. Change of porosity content with different gate velocity in HPDC.
- Figure 6. Tensile test curves of specimens cast with three different gate velocities: porosity content (%) are also indicated in the brackets.¹⁷
- Figure 7. Effect of gate velocity on the tensile properties of die cast Al-Si alloys.
- Figure 8. Plot depicting the effect of varying plunger velocity on the tensile properties of Al-9Si alloy equivalent to US A380 aluminum alloy.²²,²³
- Figure. 9 Effect of different IP on the (a) microstructure of the die castings³⁰ and (b) percentage porosity.³¹
- Figure 10. Density as a function of different IP levels: the curves refer to different injection plunger velocities.
- Figure 11. Photographs showing the double cylinder cover casting under Worst and (b) Best density values.³³
- Figure 12. Effect of (a) intensification pressure and (b) gate velocity, on the gate freezing time.¹⁶
- Figure 13. Different types of runner-gate systems used by Itamura et al.³⁶ The gate angle in the Fan-type and the gate width in the T-shaped systems were varied.
- Figure 14. The simulation results of melt flow velocity and gas entrapment (represented by marker size) at different time of injection. Markers with different colors indicate entrapped gas with different size. Sampling location for tensile and porosity measurements is indicated in (c).³⁷
- Figure 15. Tensile properties and porosity measurements made at different locations along the length of the casting (L) as shown in Fig. 13c .³⁷
- Figure 16. (a,b,c) Schematic of the three gate types along with the corresponding (d,e,f) temperature distribution during die filling.³⁸
- Figure 17. Runner-gate systems investigated by Dargush et al.³⁹
- Figure 18. Projected area of the die in the parting surface.
7. Conclusion:
Summary of Key Findings:
This review concludes that both higher gate velocity and intensification pressure are crucial injection parameters for reducing porosity and improving tensile properties in HPDC Al-Si alloys. Optimal gate velocities exist to minimize porosity, and higher IP consistently enhances casting density and reduces porosity. Runner and gate designs significantly influence melt flow and casting quality, with tangential gate systems showing advantages in uniform filling. Maintaining plunger velocity in Stage I approximately 10 times lower than in Stage II is recommended to minimize turbulence.
Academic Significance of the Study:
This study provides a comprehensive review of the existing literature on the influence of injection parameters in HPDC, consolidating findings from various research efforts. It highlights the complex interplay between injection parameters, porosity, tensile properties, and runner/gate designs, offering valuable insights for researchers and academics in the field of die casting.
Practical Implications:
The findings offer practical guidelines for die casting engineers and practitioners to optimize injection parameters for improved casting quality. Specifically, the review emphasizes the importance of:
- Controlling gate velocity within an optimal range to minimize porosity and enhance tensile properties.
- Utilizing high intensification pressure to reduce porosity and improve casting soundness.
- Carefully designing runner and gate systems to ensure uniform die cavity filling and minimize turbulence.
- Considering thin gates (1-3mm) and high gate velocities to avoid early solidification while managing potential challenges.
Limitations of the Study and Areas for Future Research:
This study is limited to a review of existing literature. It does not include original experimental work or numerical simulations. Future research areas include:
- Further investigation into optimal gate velocity ranges for specific Al-Si alloys and casting geometries.
- Detailed studies on the interaction between gate velocity, intensification pressure, and runner/gate designs.
- Research on advanced runner and gate designs to further minimize porosity and improve casting quality.
- Exploration of real-time control strategies for injection parameters based on cavity pressure feedback and melt flow monitoring.
8. References:
- Benini, A., "High-Pressure Die-Casting Technology – Casting Process and Machines Through the Analysis of Some Case Histories,” Brochure of Italpresse (BS - Italy) (2009).
- Vinarick, E.J., “Die Casting Processes,” John Wiley & Sons Inc., NJ, USA (2003).
- Dørum, C., Laukli, H.I., Hopperstad, O.S., Langseth, M., "Structural Behaviour of Al-Si Die-castings: Experiments and Numerical Simulations," European Journal of Mechanics - A/Solids, vol. 28, issue 1, pp. 1-13 (2009).
- Avalle, M., Belingardi, G., Cavatorta, M. P., Doglione, R., "Static and Fatigue Strength of a Die Cast Aluminium Alloy under Different Feeding Conditions," Proceedings of the Institution of Mechanical Engineers, Part L: Journal of Materials Design and Applications, pp. 25-30 (2002).
- Avalle, M., Belingardi, G., Cavatorta, M.P., Doglione, R., "Casting Defects and Fatigue Strength of a Die Cast Aluminium Alloy: A Comparison Between Standard Specimens and Production Components,” Int. J. Fatigue, vol. 24, pp. 1–9 (2002).
- Srivastava, M.C., “High Pressure Die Casting of Aluminium and Magnesium Alloys," Ph.D.Thesis, NTNU-Norway, 2009:207 (2009).
- Kotadia, H.R., Babu, N.H., Zhang, H., Arumuganathar, S., Fan, Z., "Solidification Behavior of Intensively Sheared Hypoeutectic Al-Si Alloy Liquid," Metall. Mater. Trans. A, vol. 42, pp. 1117-1126 (2011).
- Joshi, V., Srivastava, A., Shivpuri, R., Rolinski, E., “Investigating Ion Nitriding for the Reduction of Dissolution and Soldering in Die-casting Shot Sleeves," Surf. Coat. Technol., vol. 163–164, pp. 668–673 (2003).
- Helenius, R., Lohne, O., Arnberg, L., Laukli, H.I., "The Heat Transfer During Filling of a High-Pressure Die-casting Shot Sleeve," Mater. Sci. Eng., A, vol. 413–414, pp. 52-55 (2005).
- Verran, G.O., Mendes, R.P.K., Rossi, M.A., “Influence of Injection Parameters on Defects Formation in Die Casting Al12Si1, 3Cu Alloy: Experimental Results and Numeric Simulation,” J. Mater. Process. Technol., vol. 179, pp. 190-195 (2006).
- Ward, M., “Gating Manual,” NADCA, USA (2006).
- Jian, X., Wu, G., “An Experimental Investigation on the Flow Behavior of Liquid Aluminium Inside Pressure Die-casting Dies Using High-Speed Photography," SPIE Proceedings, vol. 1358, 19th International Congress on High-Speed Photography and Photonics, pp. 1237-1244 (1990).
- Hartmann, G.C., Chadwick, G., Lindeberg, B., "Process Analysis, Computer Modelling and Production Development of High Pressure Die Casting," EUR 15230EN (1995).
- Karban, R., "The Effects of Intensification Pressure, Gate Velocity, and Intermediate Shot Velocity on the Internal Quality of Aluminum Die Castings,” PhD thesis, Purdue University, West Lafayette, IN, USA (2000).
- Davis, A.J., Robinson, P.M., “Production of Aluminum Die Castings Using a Fan Gate, Part 2. The Effect of Flow Conditions at the Gate on Casting Quality," Trans. Society of Diecasting Engineers, Paper No. G-T75-122, Detroit, MI, USA (1975).
- Niu, X.P., Tong, K.K., Hu, B.H., Pinwill, I., “Cavity Pressure Sensor Study of the Gate Freezing Behaviour in Aluminium High Pressure Die Casting," Int. J. Cast Met. Res., vol. 11, pp. 105-112 (1998).
- Gunasegaram, D.R., Finnin, B.R., Polivka, F.B., “Melt Flow Velocity in High Pressure Die Casting: Its Effect on Microstructure and Mechanical Properties in an Al-Si Alloy," Mater. Sci. Technol., vol. 23, pp. 847-856 (2007).
- Caceres, C.H., Selling, B.I., "Casting Defects and the Tensile Properties of an Al-Si-Mg Alloy," Mater. Sci. Eng. A, vol. 220, pp. 109-116 (1996).
- Ghomashchi, M.R., “High-Pressure Die Casting: Effect of Fluid Flow on the Microstructure of LM24 Die-Casting Alloy," J. Mater. Process. Technol., vol. 52, pp. 193-206 (1995).
- Ghomashchi, R., Proceedings of the 9th International Conference on Aluminium Alloys (ed. J. F. Nie et al.), Melbourne, Institute of Materials Engineering Australasia Ltd. pp.1290–1296 (2004).
- Lumley, R., Deeva, N., Gershenzon, M., “An Evaluation of Quality Parameters for High Pressure Die Castings," Int. J. of Metalcasting, vol. 5, issue 3, pp. 37-56 (2011).
- Timelli, G., Bonollo, F., “Quality Mapping of Aluminium Alloy Diecastings," Metallurgical Science and Technology, vol. 26, no.1, pp. 2-8 (2008).
- Timelli, G., "Constitutive and Stochastic Models to Predict the Effect of Casting Defects on the Mechanical Properties of High Pressure Die Cast AlSi9Cu3(Fe) Alloys," Metallurgical Science and Technology, vol. 28, no. 2, pp. 9-17 (2010).
- Gunasegaram, D.R., Givord, M., O'Donnel, R.G., Finnin, B.R., "Improvements Engineered in UTS and Elongation of Aluminum Alloy High Pressure Die Castings Through the Alteration of Runner Geometry and Plunger Velocity," Mater. Sci. Eng., A, vol. 559, pp 276-286 (2013).
- Pitsaris, C., Savage, G., Abbott, T., Proc. 22nd NADCA International Die Casting Cong., Indianapolis, IN, USA, pp.195-203 (2003).
- Klein, F., Proc. 51st Annual World Magnesium Conf., Berlin, Germany, Inter. Magnesium Association (USA), pp. 35-43 (1994).
- Herman, E.A., "Gating Die Casting Dies,” NADCA, Rosemont, IL, pp. 1-3 and 73-93 (1996).
- Dargusch, M.S., Wang, G., Schauer, N., Dinnis, C.M., Savage, G., "Manufacture of High Pressure Die-Cast Radio Frequency Filter Bodies,” Int. J. Cast Met. Res., vol. 18, issue 1, pp. 47-54 (2005).
- Dargusch, M.S., Dour, G., Schauer, N., Dinnis, C.M., Savage, G., "The Influence of Pressure During Solidification of High Pressure Die Cast Aluminium Telecommunications Components,” J. Mater. Process. Technol., vol. 180, pp. 37-43 (2006).
- Schaffer, P.L., Laukli, H.I., “Recent Developments in Aluminum High Pressure Die Castings,” Die Casting Engineer, pp. 20-22 (May 2012).
- Otarawanna, S., Laukli, H.I., Gourlay, C.M., Dahle, A.K., "Feeding Mechanisms in High-Pressure Die Castings," Metall. Mater. Trans. A, vol. 41, pp. 1836-1846 (2010).
- Otarawanna, S., Gourlay, C.M., Laukli, H.I., Dahle, A.K., "Microstructure Formation in AlSi4MgMn and AlMg5Si2Mn High-Pressure Die Castings," Metall. Mater. Trans. A, vol. 40, pp. 1645-1659 (2009).
- Verran, G.O., Mendes, R.P.K., Rossi, M.A., "Influence of Injection Parameters on Defects Formation in Die Casting Al12Si1,3Cu Alloy: Experimental Results and Numeric Simulation," J. Mater. Process. Technol., vol. 179, pp. 190-195 (2006).
- Verran, G.O., Mendes, R.P.K., Valentina, L.V.O.D., "DOE Applied to Optimization of Aluminum Alloy Die Castings,” J. Mater. Process. Technol., vol. 200, pp. 120-125 (2008).
- Herman, E., “Searching for the Perfect Gate Velocity," Die Casting Engineer, pp. 58-61 (March 2004).
- Itamura, M., Murakami, K., Harada, T., Tanaka, M., Yamamoto, N., "Effect of Runner Design on Metal Flow Into Cavity," Int. J. Cast Met. Res., vol. 15, pp. 167-172 (2002).
- Zhao, H.D., Wang, F., Li, Y.Y., Xia, W., “Experimental and Numerical Analysis of Gas Entrapment Defects in Plate ADC12 Die Castings,” J. Mater. Process. Technol., vol. 209, pp. 4537-4542 (2009).
- Kim, Y.C., Kang, C.S., Cho, J.I., Jeong, C.Y., Choi, S.W., Hong, S.K., “Die Casting Mold Design of the Thin-walled Aluminum Case by Computational Solidification Simulation," J. Mater. Sci. Technol., vol. 24 (3), pp. 383-388 (2008).
- Dargusch, M.S., Wang, G., Schauer, N., Dinnis, C.M., Savage, G., "Manufacture of High Pressure Die-cast Radio Frequency Filter Bodies,” Int. J. Cast Met. Res., vol. 18, pp. 47–53 (2005).
- Ward, M., “Gating Manual,” NADCA, USA, (2006).
- Herman, E., “Searching for the Perfect Gate Velocity," Die Casting Engineer, pp. 58-61 (March 2004).
- Kim, C.H., Kwon, T.H., "A Runner-Gate Design System for Die Casting," Mater. Manuf. Processes, vol. 16 (6), pp. 789-801 (2001).
- Lin, C.B., Ma, C.L., Chung, Y.W., “Microstructure of A380-SiC(p) Composites for Die Casting," J. Mater. Process. Technol., vol. 48, pp. 236–246 (1998).
- Chen, Z.W., “Skin Solidification During High Pressure Die Casting of Al–11Si-2Cu-1Fe Alloy," Mater. Sci. Eng., A, vol. 348, pp. 145-153 (2003).
- Ji, S., Wang, Y., Watson, D., Fan, Z., “Microstructural Evolution and Solidification Behavior of Al-Mg-Si Alloy in High-Pressure Die Casting,” Metall. Mater. Trans. A, vol. 44, pp. 3185-3197 (2013).
- Niu, X.P., Tong, K.K., Hu, B.H., Pinwill, I., "Cavity Pressure Sensor Study of the Gate Freezing Behaviour in Aluminium High Pressure Die Casting," Int. J. Cast Met. Res., vol. 11, pp. 105–112 (1998).
9. Copyright:
- This material is "[Anilchandra R. Adamane, Lars Arnberg, Elena Fiorese, Giulio Timelli, Franco Bonollo]"'s paper: Based on "[INFLUENCE OF INJECTION PARAMETERS ON THE POROSITY AND TENSILE PROPERTIES OF HIGH-PRESSURE DIE CAST AI-SI ALLOYS: A REVIEW]".
- Paper Source: https://doi.org/10.1007/s40962-015-0008-x
This material was created to introduce the above paper, and unauthorized use for commercial purposes is prohibited.
Copyright © 2025 CASTMAN. All rights reserved.