This article introduces the paper ['COMPUTER AIDED COOLING DESIGN FOR DIE CASTING PROCESS'] presented at the ['The Ohio State University']
1. Overview:
- Title: COMPUTER AIDED COOLING DESIGN FOR DIE CASTING PROCESS
- Author: Ming-Tsong Lin, B.S.M.E
- Publication Year: 1993
- Publishing Journal/Academic Society: The Ohio State University
- Keywords: Die Casting, Cooling Design, Computer Aided Design, CAD, Boundary Element Method, BEM, Thermal Analysis, Mold Design
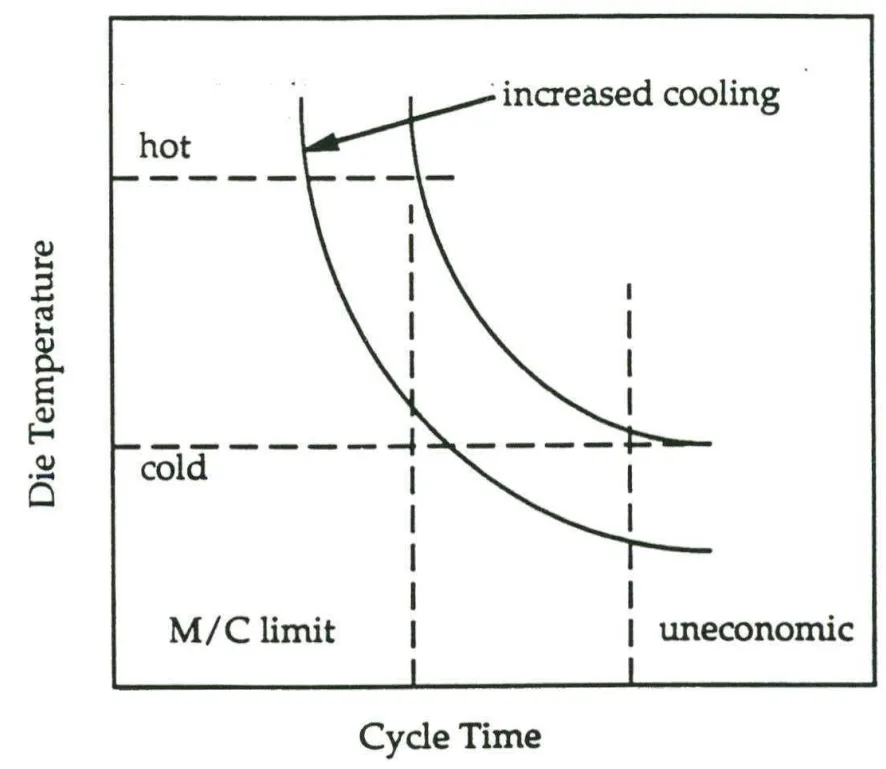
2. Research Background:
Background of the Research Topic:
Die casting is defined as a "net shape manufacturing process" (Street, 1977) where molten metal is injected into a metallic die under high pressure. However, the physical phenomena inherent in die casting are complex, making cooling system design a "highly skill-intensive activity" (Barton, 1981) reliant on substantial 'know-how'. Traditional die design, based primarily on past experience, is becoming "increasingly inadequate and inefficient" for larger, more complex castings and novel materials.
Status of Existing Research:
Academic and industrial research efforts are directed towards establishing a scientific foundation for die casting and integrating modern computer techniques, such as Computer Aided Design (CAD), into mold design and manufacturing. While simulation programs exist to analyze thermal characteristics influenced by heat inputs and cooling channel locations, "very few are directed at the die casting cooling system design issue". Existing software often suffers from "difficulty of use and insufficient design information".
Necessity of the Research:
The increasing demand for high casting quality and production rates necessitates sophisticated modeling programs to study die casting cooling processes. There is a need for a "practical and easy-to-use design tool for the cooling system of die casting dies". Such a program should "reduce the time and cost for design and manufacturing of the die by substituting the trial-and-error procedure in the design stage for that in the manufacturing stage of a real die."
3. Research Purpose and Research Questions:
Research Purpose:
The main objective is "to develop an interactive computer aided cooling design system for the die casting process" to assist in determining the "size and placement of cooling channels and process conditions to achieve a rapid, uniform and balanced cooling."
Key Research:
The methodology involves integrating "two computer aided cooling analysis/design programs" within a "well-organized computer graphics design environment":
(a) A "preliminary design program" to efficiently suggest initial design parameters based on "energy balance through a cycle as well as uniformity of temperature over the cavity surface."
(b) An "integrated computer aided cooling analysis program, interfaced with a CAD system," for three-dimensional heat transfer analysis, utilizing a "boundary element analysis program".
Research Hypotheses:
While not explicitly stated as hypotheses, the research is based on the premise that:
- A computer-aided cooling design system can improve the efficiency and effectiveness of die casting die cooling system design.
- Integrating analytical and numerical methods within a CAD environment provides a practical approach to cooling system design.
- The Boundary Element Method (BEM) is a suitable numerical technique for analyzing heat transfer in die casting dies.
4. Research Methodology
Research Design:
The research employs a system development approach, creating a two-stage computer-aided cooling design system. This system comprises:
- Preliminary Design System (WATER_DESIGN): Based on an analytical model for rapid estimation of cooling channel parameters.
- Optimum Design System (BEM_COOL): A three-dimensional Boundary Element Method program for detailed thermal analysis and design verification.
Data Collection Method:
The research focuses on software development and implementation. Validation and demonstration are performed through example cases and simulation results generated by the developed system.
Analysis Method:
- Preliminary Design: Analytical method based on the "model developed at Battelle Columbus Laboratories(Kaiser et.al, 1972)", specifically the ILZRO model.
- Optimum Design: Numerical method using the Boundary Element Method (BEM) for three-dimensional transient heat transfer analysis.
Research Subjects and Scope:
The research is focused on the design of cooling systems for die casting dies. The scope includes:
- Development of software tools for cooling channel design.
- Integration of these tools within a CAD environment (CAEDS).
- Application of the Boundary Element Method for thermal analysis in die casting.
- Demonstration of the system's capabilities using a representative die casting example.
5. Main Research Results:
Key Research Results:
The primary outcome is the development of a computer-aided cooling design system featuring two programs:
- WATER_DESIGN: A preliminary design program implemented with a menu-driven interface (Fig 4.1), utilizing the ILZRO model to estimate waterline parameters. It outputs waterline location, total heat input, and heat transfer coefficient (Fig 4.3).
- BEM_COOL: An optimum design system incorporating a three-dimensional BEM program integrated with CAEDS (Fig 4.4). It allows for detailed thermal analysis, displaying temperature contours (Fig 4.10, Fig 4.12) and temperature-time traces (Fig 4.9, Fig 4.11).
Data Interpretation:
- WATER_DESIGN provides rapid initial estimates for cooling channel locations based on simplified geometry and analytical calculations.
- BEM_COOL enables detailed 3D thermal analysis of die geometries, allowing designers to evaluate temperature distributions and refine cooling system designs. The example case demonstrates the system's ability to simulate die temperature variations during a casting cycle and visualize temperature contours. However, the current BEM implementation is noted to have limitations in accuracy for cases with high Biot numbers, typical in die casting.
Figure Name List:
- Fig 1.1 Design process using CAD
- Fig 2.1 Heat flow paths available in die casting
- Fig 2.2 Temperature versus time for select die casting cycle
- Fig 2.3 Die surface temperature, heat flux, and total heat absorbed as functions of time for single die casting cycle
- Fig 2.4 Relationship between die temperature, cycle time and die cooling
- Fig 2.5 The casting sectioned and numbered for calculation
- Fig 2.6 Aluminum casting fill and heat flow diagram
- Fig 2.7 The die surface temperature variation
- Fig 3.1 Waterline placement configuration for strip casting
- Fig 3.2 The wireframe modeling is ambiguous
- Fig 3.3 The data structure of B-rep scheme
- Fig 4.1 The menu of the WATER_DESIGN program
- Fig 4.2 The decomposition of the die sections and runner system
- Fig 4.3 An output of the WATER_DESIGN program
- Fig 4.4 The system structure of the three-dimensional cooling analysis system
- Fig 4.5 An approximation of a typical casting cycle into three regions
- Fig 4.6 The geometry and mesh of one quadrant of the die
- Fig 4.7 The menu system of the BEM_COOL program
- Fig 4.8 Simulation process control data file for cooling analysis using BEM
- Fig 4.9 The die temperature versus time trace for a casting cycle(Case. 1)
- Fig 4.10 The temperature contour of the die at the time of casting ejection(Case. 1)
- Fig 4.11 The die temperature versus time trace for a casting cycle(Case. 2)
- Fig 4.12 The temperature contour of the die at the time of casting ejection(Case. 2)
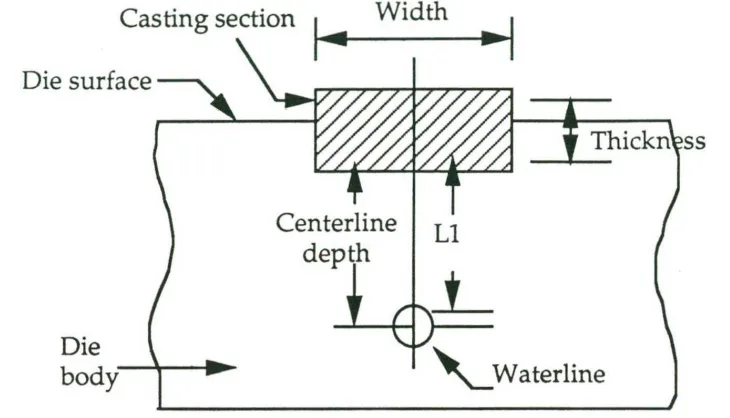
6. Conclusion:
Summary of Main Results:
This research successfully developed a computer-aided cooling design system for die casting, integrating two distinct tools: WATER_DESIGN for preliminary analysis and BEM_COOL for optimum design. Implemented within the CAEDS environment, this system aims to enhance the design process for cooling lines and process conditions, ultimately minimizing cooling time, maximizing part quality, and improving overall design quality and productivity.
Academic Significance of the Research:
The research demonstrates the effective integration of analytical (ILZRO model) and numerical (BEM) methods within a commercial CAD system for die casting cooling design. It highlights the application of the Boundary Element Method for transient heat transfer analysis in this domain, emphasizing its advantage in reducing dimensionality and simplifying data preparation compared to domain-based methods like FEM.
Practical Implications:
The developed system offers die casting designers a valuable tool to move beyond traditional trial-and-error approaches. WATER_DESIGN provides a means for "quick" preliminary design, while BEM_COOL enables detailed three-dimensional cooling analysis. This combination facilitates a more efficient and informed cooling system design process, potentially leading to reduced cycle times, improved casting quality, and increased productivity in die casting operations.
Limitations of the Research
The accuracy of the BEM_COOL program is limited by the assumption of small Biot numbers (Bi < 0.1), which may not be fully representative of typical die casting conditions where Biot numbers are often greater than 0.1. Further, the current BEM model requires refinement to better capture local heat transfer phenomena between the mold and cavity.
7. Future Follow-up Research:
- Directions for Follow-up Research
Future research should focus on: - Enhancing the BEM_COOL program to accurately model heat transfer in die casting scenarios with "large Biot number".
- Incorporating "modeling the local heat transfer variation between the mold and cavity".
- Developing a more interactive graphical user interface for "graphically defining the attribute information" in BEM_COOL.
- Expanding WATER_DESIGN to include "graphically displaying the relationship between the die surface temperature and individual design parameters."
- Areas Requiring Further Exploration
Further exploration should consider: - Integrating "a decision support aid for the evaluation and modification with a numerical analysis capability in a CAD environment."
- Developing "heuristic reasoning capability in the system" to further assist in cooling channel design optimization.
8. References:
- Allen, G.,"An Introduction to Solid Modeling," Computer & Graphics, Vol.8, No.4., 1984 , pp.439-447.
- Barton, H.K., Product Design for Die Casting, SDCE River Grove, IL.
- Blazek, S. "Cooling of Die Casting Dies," Machinery and Production Engineering, April, 1970.
- C. A. Brebbia, The Boundary Element Methods for Engineers, Pentech Press, London, 1978.
- CAEDS, vers. 6.0 Computer Software. Structural Dynamics Reserach Corporation, 1992.
- Cocks, D.L., C.Eng., FIM, and A.J. Wall, Bsc, PhD, "Thermal Aspects of Zinc Die Casting," 1982.
- Davey, K, and S. Hinduja, "Modeling of the Transient Thermal Bahavior of the Pressure Die Casting Process with BEM," Appl. Math. Modeling, Vol. 14,1990.
- Doyle, G.R., W.D. Kaiser and T.P. Groeneveld, "Computer Aided Die Design for Zinc Die Casting Dies," Transactions, 11th SDCE International Die Casting Exposition and Congress, Society of Die Casting Engineers, Cleveland, Ohio (1981), paper No. G-T81-054.
- Groeneveld, T.P., R. Robinson, and W.D. Kaiser, "Design Data for Size, Number, and Locations of Waterlines in Zinc Die Casting Dies," Transactions, 8th SDCE International Die Casting Exposition and Congress, Society of Die Casting Engineers, Detroit, Michigan, (1975), paper No. G-T75-085.
- Herman E.A., Die Casting Dies: Designing, SDCE, 1979.
- Hong, C.P., T. Umeda and Y. Kimura, "Numerical model for casting solidification : Part I. The coupling of the boundary element method for solidification problems," Metall. Trans. B, 15B, 91,1984.
- Hong, C.P., T. Umeda and Y. Kimura, "Numerical model for casting solidification : Part II. Application of the boundary element method for solidification problems," Metall. Trans. B, 15B, 101, 1984.
- Kaiser, W.D., S.D. Sander, and P.D. Frost. "The IIZRO-Battelle Multichannel Temperature Controller," Transactions, 7th SDCE International Die Casting Exposition and Congress, Society of Die Casting Engineers, Detroit, Michigan, (1972), paper No. 5172.
- Kwon,T.H., "Mold Cooling System Design Using Boundary Element Method," Transactions of the ASME, Vol. 110, November, 1988.
- Kwon, T.H., S.F., Shen, and K.K. Wang, "Computer Aided Cooling System Design for Injection Molding," SPE Technical Papers, Vol.32, 1986,p.110.
- Lin, Rongjau, Ph. D. dissertation, Experimental and Numerical Analysis of RTM and SRIM Processes in Non-isothermal Conditions, 1991.
- Lu, Shao-Chiung, Master Thesis, Integration of FEA and CAD for Sheet Stamping Design, 1992.
- Mortenson, M.E., Geometrical Modeling, John Wiley & Sons Inc., 1985.
- Osborne, M.A., C.E. Mobley, R.A. Miller and L.H. Kallien, "Modeling of the Cold Chamber Die Casting Process using MAGMAsoft, "1993.
- Papai, Jonathan and Carroll, Mobley, "Die Thermal Fields and Heat Flux During Die Casting of 380 Aluminum Alloy in H-13 Steel Dies," 16th Die Casting Congress & Exposition, September, 1991, Detroit, Michigan, Paper No. Detroit T-91-0C1.
- Requicha, A.A.G. and H.B. Voelcker, "Solid Modeling: A Historical Summary and Contemporary Assessment," IEEE Computer Graphics & Applications, Vol.2, No.2, Mar, 1982, pp.9-24.
- Shephard, M.S., "Finite Element Modeling within an Integrated Geometric Modeling Environment: Part II- Attribute specification, domain differences and indirect element types," Engineering with Computer, 1,1985b, pp.73-85.
- Siauw, H.T., and T.T. Nguyen, "A Computer Aided Thermal Analysis Package for Pressure Die Casting Dies,"15th Die Casting Congress & Exposition, October, 1989, St. Louis, MO, Paper No. G-T89-044.
- Sully, L.J.D., "Die Casting", Metal's Handbook, 9th Edition, v15, 1988, pp.287-295.
- Szakacs, Geza, "Thermal Analysis of Die Casting Dies for Cooling Channel Location," SDCE Transactions, Paper No. G-T87-007, 1987.
- Thukkaram, D. "Heat Transfer in Die Casting Dies," SDCE Transactions, Paper No. 61, 1970.
- Truelove, R. L., "Die Casting Temperature Control: A new science," Die Casting Engineer, January, 1982.
9. Copyright:
- This material is "Ming-Tsong Lin"'s paper: Based on "COMPUTER AIDED COOLING DESIGN FOR DIE CASTING PROCESS".
- Paper Source: [https://etd.ohiolink.edu/] (Example URL, replace with actual DOI or repository link if available)
This material was summarized based on the above paper, and unauthorized use for commercial purposes is prohibited.
Copyright © 2025 CASTMAN. All rights reserved.