This article introduces the paper "Al Alloys and Casting Processes for Induction Motor Applications in Battery-Powered Electric Vehicles: A Review" presented at the MDPI Metals
1. Overview:
- Title: Al Alloys and Casting Processes for Induction Motor Applications in Battery-Powered Electric Vehicles: A Review
- Authors: Yuxian Li, Anita Hu, Yintian Fu, Sufeng Liu, Wutian Shen, Henry Hu, and Xueyuan Nie
- Publication Year: 2022
- Publishing Journal: Metals, MDPI
- Keywords: Al alloys; casting processes; electrical conductivity; electric motor; electric vehicle; mechanical properties; strengthening mechanisms
![Figure 1. Components of an electrical sheet, a rotor bar, and an end-ring in an induction motor [1].](https://castman.co.kr/wp-content/uploads/image-293-1024x731.webp)
2. Research Background:
The increasing environmental concerns and the rapid growth of the battery-powered electric vehicle (BEV) industry have significantly driven research into lightweight materials. Aluminum (Al) alloys are gaining considerable attention as potential substitutes for copper in induction motors. Copper, while possessing high electrical conductivity, is denser and heavier. Replacing copper with lighter, castable aluminum alloys can reduce the weight and size of electric induction motors, ultimately improving the energy efficiency and driving range of BEVs. Pure aluminum, however, suffers from poor castability and low strength, necessitating the development of suitable aluminum alloys and casting techniques.
3. Research Purpose and Research Questions:
This review paper aims to provide a comprehensive introduction to common cast aluminum alloys and their associated casting processes relevant to induction motors in BEVs. The primary goal is to motivate the further development of high-strength and high-conductivity aluminum alloys that can be practically implemented in BEV motors.
Key areas explored in this review include:
- Evaluation of various cast aluminum alloy systems containing elements like Cu, Si, Ni, Mg, Fe, and Ti.
- Comparison of these cast alloys with nanostructured wrought aluminum alloys.
- Description of conventional casting processes suitable for aluminum alloys, such as high pressure die casting, squeeze casting, and sand casting.
- Explanation of strengthening mechanisms in aluminum alloys, including solid solution strengthening, precipitation strengthening, dislocation accumulation strengthening, and grain boundary strengthening.
- Outline of the phenomenon of electrical conduction in aluminum alloys.
- Comprehensive listing and critical review of the mechanical and electrical properties of recently developed aluminum alloys for casting and deformation processes, considering their microstructural characteristics.
4. Research Methodology
This study is a review paper that synthesizes existing literature and research findings. The methodology involves:
- Literature Review: Examining and compiling information from a wide range of published articles and studies related to aluminum alloys, casting processes, electrical conductivity, and mechanical properties.
- Comparative Analysis: Evaluating and comparing different aluminum alloy systems, casting techniques, and strengthening mechanisms. The review contrasts conventional cast alloys with advanced nanostructured wrought alloys.
- Critical Review: Analyzing and interpreting the reported mechanical and electrical properties of aluminum alloys in relation to their microstructure. This involves a critical assessment of the data presented in various studies.
The scope of the review encompasses:
- Material Focus: Cast aluminum alloy systems containing Cu, Si, Ni, Mg, Fe, and Ti, as well as nanostructured wrought aluminum alloys.
- Process Focus: Conventional casting processes including high pressure die casting (HPDC), squeeze casting, and sand casting.
- Property Focus: Mechanical properties (strength, ductility, hardness) and electrical properties (conductivity, resistivity) of aluminum alloys.
5. Main Research Results:
This review paper consolidates a significant amount of information regarding aluminum alloys for BEV motor applications. Key findings and results presented include:
- Aluminum Alloy Systems: The paper evaluates various cast alloy systems, highlighting the role of alloying elements such as Copper (Cu) and Silicon (Si). For instance, Al-Cu alloys (2xx.x series) and Al-Cu-Si alloys (3xx.x series) are discussed in detail, with reference to their phase diagrams (Figure 2 and Figure 4). The A380 alloy is noted as a popular HPDC alloy due to its castability and low cost.
- Casting Processes: Conventional casting processes suitable for aluminum alloys are described:
- High Pressure Die Casting (HPDC): A versatile process for mass-producing engineered metal parts with intricate shapes (Figure 6 and Figure 7).
- Squeeze Casting: A process combining permanent mold casting and die forging to produce fine-grained components with excellent surface finish and minimal porosity (Figure 8).
- Sand Casting: One of the oldest and most versatile casting processes, suitable for complex shapes and large parts (Figure 9).
- Strengthening Mechanisms: The review outlines key strengthening mechanisms in aluminum alloys:
- Solid Solution Strengthening: Adding solute atoms to the aluminum lattice.
- Precipitation Strengthening: Utilizing second-phase precipitates to impede dislocation movement.
- Dislocation Accumulation Strengthening: Increasing strength through dislocation density.
- Grain Boundary Strengthening: Reducing grain size to increase grain boundary area and impede dislocation motion.
Equation (1) is presented to estimate the total strength of alloys based on these mechanisms: S = So + Sgs +Sss + Sdis + Sp
- Electrical Conductivity: The phenomenon of electrical conduction in aluminum alloys is explained, noting that strengthening mechanisms generally degrade electrical conductivity. Equation (2) and (3) describe the electrical resistivity (ρ) and its components. ρ = ρτ + PD and PD = Pss + Pp + Pdis + Pv + Pgs. Table 2 lists the electrical conductivity and resistivity of pure metals.
- Nanostructured Aluminum Alloys: The paper discusses the potential of severe plastic deformation (SPD) processes like high-pressure torsion (HPT) and equal-channel angular pressing (ECAP) to produce nanostructured aluminum alloys with enhanced strength and conductivity (Figure 10). Table 3 summarizes the mechanical properties and electrical conductivity of nanostructured AA6201 and AA6060 alloys.
- Cast Aluminum Alloys for Motors: The review examines cast Al-Si-Cu-Mg alloys and a novel cast Al-Ni alloy ("Tesla alloy") for motor applications. Tables 5 and 6 detail the design of experiment and properties of Al-Si-Cu-Mg alloys. Figure 17 shows SEM micrographs of AlSi4Cu1Mg0.9 alloy microstructure. Figure 18 compares yield strength and electrical conductivity of various cast aluminum alloys. Figure 19 and Figure 20 present castability and shrinkage results for different aluminum alloys.
Figure Name List:
- Figure 1. Components of an electrical sheet, a rotor bar, and an end-ring in an induction motor [1].
- Figure 2. Phase diagram of Al-Cu system [7].
- Figure 3. Mechanical properties of Al-Cu alloys as a function of Cu content [8].
- Figure 4. Al-Si binary eutectic phase diagram with composition ranges of various alloy types [9].
- Figure 5. Effect of different Si contents on the mechanical properties. (a) Ultimate strength, (b) yield strength, (c) elongation, and (d) hardness in Al-Si alloys [12].
- Figure 6. Graphical illustration of hot-chamber die casting process [14].
- Figure 7. (a) Graphical illustration of a cold-chamber die casting machine. (b) Casting cycle for cold-chamber die casting [14].
- Figure 8. Schematic diagram for the direct squeeze casting process. (a) Preheat, (b) pouring, (c) solidification, and (d) ejection [22].
- Figure 9. Graphical illustration of sand casting [26].
- Figure 10. Room temperature electrical conductivity (in % of IACS) versus ultimate tensile strength for coarse grained (CG) pure Al and commercial Al-Mg-Si alloys, as well as their nanostructured counterparts obtained via severe plastic deformation (SPD) processes, including high pressure torsion (HPT) and equal-channel angular pressing (ECAP) [32].
- Figure 11. Schematic illustration of changes in GB energy, associated with the formation of a twin "T" inside the grain "A" [45].
- Figure 12. Variation of thermal conductivity with the composition of Cu for the Al based Al-Cu alloys [46].
- Figure 13. Comparison of thermal conductivities of pure Al and Cu with those of Al-Cu alloys at different temperatures [46].
- Figure 14. Variations of electrical conductivity with the composition of Cu determined from the Smith-Palmer equation [46].
- Figure 15. Temperature dependence of electrical conductivity for liquid Al and Al-4 wt% Cu, Al-20 wt% Cu, and Al-30 wt% Cu liquid alloys [47].
- Figure 16. Optical micrographs of growth morphologies of directionally solidified (a1,a2) Al-6 wt% Cu; (b1,b2) Al-24 wt% Cu; (C1,C2) Al-33 wt% Cu alloys [48].
- Figure 17. SEM micrographs showing the microstructure of the s-5 alloy under the (a) as-cast and (b) T6 conditions [50].
- Figure 18. A yield strength versus the electrical conductivity plot for cast aluminum alloys [43].
- Figure 19. Castability of cast pure aluminum and Al alloys, (a) fluidity, (b) hot-tearing susceptibility [43].
- Figure 20. Shrinkage of cast pure aluminum and Al alloys [43].
![Figure 2. Phase diagram of Al-Cu system [7].](https://castman.co.kr/wp-content/uploads/image-294-png.webp)
![Figure 3. Mechanical properties of Al-Cu alloys as a function of Cu content [8].](https://castman.co.kr/wp-content/uploads/image-295-1024x670.webp)
![Figure 5. Effect of different Si contents on the mechanical properties. (a) Ultimate strength, (b) yield strength, (c) elongation, and (d) hardness in Al-Si alloys [12]](https://castman.co.kr/wp-content/uploads/Figure-5.-Effect-of-different-Si-contents-on-the-mechanical-properties.-a-Ultimate-strength-b-yield-strength-c-elongation-and-d-hardness-in-Al-Si-alloys-12-1024x879.webp)
![Figure 6. Graphical illustration of hot-chamber die casting process [14].](https://castman.co.kr/wp-content/uploads/image-297-png.webp)
![Figure 7. (a) Graphical illustration of a cold-chamber die casting machine. (b) Casting cycle for cold-chamber die casting [14].](https://castman.co.kr/wp-content/uploads/image-298-1024x424.webp)
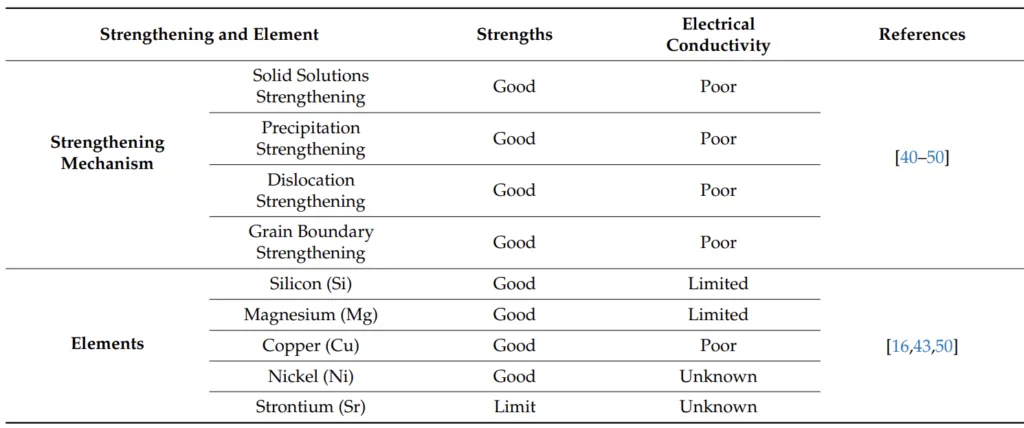
6. Conclusion and Discussion:
Summary of Main Results:
This review paper effectively summarizes the current state of research on aluminum alloys and casting processes for application in BEV induction motors. It highlights the potential of aluminum alloys as lightweight alternatives to copper, emphasizing the need to balance mechanical strength and electrical conductivity. The paper discusses various cast aluminum alloy systems, suitable casting processes (HPDC, squeeze casting, sand casting), and strengthening mechanisms. It also explores recent advancements in nanostructured aluminum alloys and cast alloys specifically designed for motor components.
Academic Significance:
The review provides a valuable resource for researchers and engineers in materials science, automotive engineering, and electrical engineering. It consolidates dispersed information into a single, accessible document, offering a comprehensive overview of the challenges and opportunities in using aluminum alloys for BEV motors.
Practical Implications:
The findings of this review have significant practical implications for the automotive industry. By guiding the development of high-performance aluminum alloys and optimized casting processes, this research contributes to the realization of lighter, more energy-efficient BEVs with improved driving range. The exploration of cost-effective casting methods for complex motor components is particularly relevant for mass production.
Limitations of the Research:
As a review paper, this study is limited by the scope and availability of existing research. It does not present original experimental data. Furthermore, while the paper discusses various aluminum alloys, the castability of some advanced alloys, such as the Al-Ni "Tesla alloy," requires further investigation and verification.
7. Future Follow-up Research:
The review identifies several directions for future research:
- Development of As-Cast High-Performance Alloys: Future research should focus on developing as-cast aluminum alloys that achieve a desirable balance of high strength and electrical conductivity without requiring extensive thermal treatments. This would reduce manufacturing costs and energy consumption.
- Castability Optimization: Further exploration is needed to optimize the castability of advanced aluminum alloys, particularly those with novel compositions like Al-Ni alloys, to ensure they can be reliably used in complex motor component designs.
- Microstructure-Property Relationship: A deeper understanding of the microstructure-property relationships in cast aluminum alloys is crucial for tailoring alloy compositions and casting processes to achieve specific performance requirements for BEV motors.
8. References:
- Boukhnifer, M.; Raisemche, A. Fault tolerant control for induction motor in electrical vehicle. In Proceedings of the 2012 IEEE International Conference on Control Applications, Dubrovnik, Croatia, 3–5 October 2012; pp. 136–141.
- Popovich, A.; Sufiiarov, V.; Polozov, I.; Borisov, E.; Masaylo, D.; Orlov, A. Microstructure and mechanical properties of additive manufactured copper alloy. Mater. Lett. 2016, 179, 38–41. [CrossRef]
- Daesung, J.U.N.G. End Ring for Induction Motor. U.S. Patent No. 9,866,095, 9 January 2018.
- Davis, J. (Ed.) ASM Specialty Handbook: Aluminum and Aluminum Alloys; ASM International: Materials Park, OH, USA, 2002.
- Beaulieu, D. Characteristics of Structural Aluminum; Presses de l'aluminum: Chicoutimi, QC, Canada, 2005.
- Fang, L. Development of As-Cast High Strength Aluminum Alloys with Ni and Sr Addition. Ph.D. Dissertation, University of Windsor, Windsor, ON, Canada, 2018.
- Davis, J.R. ASM Handbook, Alloy. Phase Diagrams; Section 2; ASM International: Material Park, OH, USA, 2002; Volume 5, p. 44.
- Mondolfo, L.F. Metallography of Aluminum Alloys. 2007. Available online: https://www.amazon.com/Metallography-Aluminum-Alloys-Lucio-Mondolfo/dp/1406736724 (accessed on 5 January 2022).
- Backerud, L.; Chai, G.; Tamminen, J. Solidification characteristics of aluminum alloys. AFS Trans. 1990, 2, 24–37, 71–81.
- Abdel-Jaber, G.T.; Omran, A.M.; Khalil, K.A.; Fujii, M.; Seki, M.; Yoshida, A. An investigation into solidification and mechanical properties behavior of Al-Si casting alloys. Int. J. Mech. Mechatron. Eng. IJMME-IJENS 2010, 10, 34–41.
- Fang, L.; Zhang, X.; Hu, H.; Nie, X.; Tjong, J. Microstructure and tensile properties of squeeze cast aluminium alloy A380 containing Ni and Sr addition. Adv. Mater. Process. Technol. 2017, 3, 90–100. [CrossRef]
- Elzanaty, H. Effect of different Si content on the mechanical properties in Al-based alloy. Int. J. Res. Eng. Technol. 2014, 2, 49–54.
- Kalhapure, M.G.; Dighe, P.M. Impact of silicon content on mechanical properties of aluminum alloys. Int. J. Sci. Res. 2015, 4, 38–40.
- Vinarcik, E.J. High. Integrity Die Casting Process; John Wiley & Sons Inc.: Hoboken, NJ, USA, 2003.
- Doehler, H. Die Casting; McGraw Hill Book Company: New York, NY, USA, 1951.
- Hollinggrak, J. Casting Metals. UK Patent 4371, 8 September 1819.
- Chernov, D.K. Reports of the Imperial Russian Metallurgical Society. UK Patent 4371, 17 December 1878.
- Plyatskii, V.M.; Hammond, R.E.; Wald, A. Extrusion Casting; Primary Sources: New York, NY, USA, 1965.
- Seredenko, V.P.; Malei, T.P. Pressing of components from liquid steel. Dokl. Akad. Nauk SSSR 1961, 5, 253–255.
- Gulyaev, B.B. Crystallization of Steel under mechanical pressure. Liteinoe Proizv. 1960, 12, 33.
- Meyer, W. Squeeze Forming a Process for Producing High-Quality Castings; Metall: Clausthal-Zellerfeld, Germany, 1976.
- Hu, H. Squeeze casting of magnesium alloys and their composites. J. Mater. Sci. 1998, 33, 1579–1589. [CrossRef]
- Ghomashchi, M.R.; Vikhrov, A. Squeeze casting: An overview. J. Mater. Processing Technol. 2000, 101, 1–9. [CrossRef]
- Biringuccio, V.; Smith, C.S., Translators; The Pirotechnia of Vannoccio Biringuccio: The Classic Sixteenth-Century Treatise on Metals and Metallurgy; Dover Publications: Mineola, NY, USA, 17 April 2013.
- Weiss, D. Advances in the Sand Casting of Aluminium Alloys. In Fundamentals of Aluminium Metallurgy; Woodhead Publishing: Sawston, UK, 2018; pp. 159–171.
- Saleem, M.Q. Helium Assisted Sand Casting of Aluminum Alloys. Ph.D. Dissertation, Worcester Polytechnic Institute, Worcester, MA, USA, 2011.
- Kamikawa, N.; Huang, X.; Tsuji, N.; Hansen, N. Strengthening mechanisms in nanostructured high-purity aluminium deformed to high strain and annealed. Acta Mater. 2009, 57, 4198–4208. [CrossRef]
- Asgharzadeh, H.; Simchi, A.; Kim, H.S. Microstructural features, texture and strengthening mechanisms of nanostructured AA6063 alloy processed by powder metallurgy. Mater. Sci. Eng. A 2011, 528, 3981–3989. [CrossRef]
- Soboyejo, W. Mechanical Properties of Engineered Materials; CRC Press: Boca Raton, FL, USA, 2002; Volume 152.
- Kelly, A.; Nicholson, R.B. (Eds.) Strengthening Methods in Crystals; Elsevier: London, UK, 1971.
- Ashby, M.F. The deformation of plastically non-homogeneous materials. Philos. Mag. 1970, 21, 399–424. [CrossRef]
- Murashkin, M.Y.; Sabirov, I.; Sauvage, X.; Valiev, R.Z. Nanostructured Al and Cu alloys with superior strength and electrical conductivity. J. Mater. Sci. 2016, 51, 33–49. [CrossRef]
- Hall, E.O. The deformation and aging of mild steel. Proc. Phys. Soc. B 1951, 64, 747-753. [CrossRef]
- Rossiter, P.L. The Electrical Resistivity of Metals and Alloys; Cambridge University Press: Cambridge, UK, 1987.
- Kasap, S.; Capper, P. (Eds.) Springer Handbook of Electronic and Photonic Materials; Springer: Wurzburg, Germany, 2006.
- Matthiessen, A.; Vogt, C. On the influence of temperature on the electric conducting-power of alloys. Philos. Trans. R. Soc. Lond. 1864, 154, 167-200.
- Lu, L.; Shen, Y.; Chen, X.; Qian, L.; Lu, K. Ultrahigh strength and high electrical conductivity in copper. Science 2004, 304, 422–426. [CrossRef]
- Dugdale, J.S. The Electrical Properties of Metals and Alloys; Arnold: London, UK, 1977.
- Valiev, R.Z.; Sabirov, I.; Zhilyaev, A.P.; Langdon, T.G. Bulk nanostructured metals for innovative applications. JOM 2012, 64, 1134–1142. [CrossRef]
- Valiev, R.Z.; Murashkin, M.Y.U.; Sabirov, I. A nanostructural design to produce high strength Al alloys with enhanced electrical conductivity. Scr. Mater. 2014, 76, 13–16. [CrossRef]
- Bobruk, E.V.; Murashkin, M.Y.; Kazykhanov, V.U.; Valiev, R.Z. Aging behavior and properties of ultra-fine grained aluminium alloys of Al-Mg-Si system. Rev. Adv. Mater. Sci. 2012, 31, 14–34.
- Miller, M.K. Atom. Probe Tomography: Analysis at the Atomic Level; Springer Science & Business Media: Boston, MA, USA, 2012.
- Sivanesh, P.; Charlie, K.; Robert, S.J.; Ethan, F.; Paul, E. Aluminum Alloys for Die Casting. U.S. Patent No. WO 2020/028730 A1, 6 February 2020.
- Cubero-Sesin, J.M.; Arita, M.; Horita, Z. High strength and electrical conductivity of Al-Fe alloys produced by synergistic combination of high-pressure torsion and aging. Adv. Eng. Mater. 2015, 17, 1792–1803. [CrossRef]
- Chen, X.H.; Lu, L.; Lu, K. Electrical resistivity of ultra-fine grained copper with nanoscale growth twins. J. Appl. Phys. 2007, 102, 083708. [CrossRef]
- Aksöz, S.; Ocak, Y.; Maraşlı, N.; Çadirli, E.; Kaya, H.A.S.A.N.; Böyük, U. Dependency of the thermal and electrical conductivity on the temperature and composition of Cu in the Al based Al-Cu alloys. Exp. Therm. Fluid Sci. 2010, 34, 1507–1516. [CrossRef]
- Plevachuk, Y.; Sklyarchuk, V.; Yakymovych, A.; Eckert, S.; Willers, B.; Eigenfeld, K. Density, viscosity, and electrical conductivity of hypoeutectic Al-Cu liquid alloys. Metall. Mater. Trans. A 2008, 39, 3040–3045. [CrossRef]
- Kaya, H.A.S.A.N. Dependence of electrical resistivity on temperature and composition of Al-Cu alloys. Mater. Res. Innov. 2012, 16, 224–229. [CrossRef]
- Ishikawa, H.; Takashima, Y.; Okada, Y. Squirrel-Cage motor Rotor and Squirrel-Cage Motor. U.S. Patent No. 9,935,533, 4 March 2018.
- Xia, S.; Sanjiu, Y.; Xiao, B.; Sirui, L. Effects of Si, Cu and Mg addition on electrical conductivity and mechanical properties of cast aluminum alloys. Spec. Cast. Nonferrous Alloys 2010, 12, 12–20.
9. Copyright:
- This material is Yuxian Li, Anita Hu, Yintian Fu, Sufeng Liu, Wutian Shen, Henry Hu and Xueyuan Nie's paper: Based on Al Alloys and Casting Processes for Induction Motor Applications in Battery-Powered Electric Vehicles: A Review.
- Paper Source: https://doi.org/10.3390/met12020216
This material was summarized based on the above paper, and unauthorized use for commercial purposes is prohibited.
Copyright © 2025 CASTMAN. All rights reserved.