This article introduces the paper "Development of Low-Pressure Die-Cast Al–Zn–Mg–Cu Alloy Propellers—Part I: Hot Tearing Simulations for Alloy Optimization" presented in Materials Journal.
1. Overview: High-Strength Aluminum Alloy Propellers, Addressing Hot Tearing Issues Through Alloy Optimization Research
- Title: Development of Low-Pressure Die-Cast Al–Zn–Mg–Cu Alloy Propellers—Part I: Hot Tearing Simulations for Alloy Optimization
- Authors: Min-Seok Kim and Jiwon Kim
- Publication Year: 2024
- Publishing Journal/Academic Society: Materials MDPI
- Keywords: Al–Zn–Mg–Cu alloy, low-pressure die casting, simulation, propeller, hot tearing
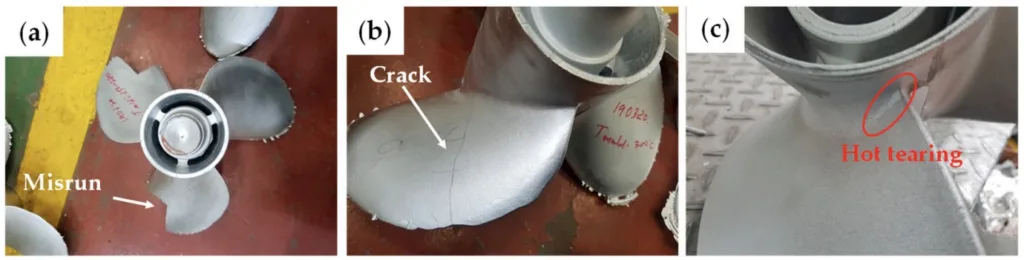
2. Research Background: Demand for High-Performance Leisure Boat Propellers, Hot Tearing Challenges in 7xxx Series Alloys
- Social/Academic Context of the Research Topic: The rapid growth of the leisure boat industry has increased the demand for high-performance propeller materials. Traditional Al-Si alloys, while offering good castability, have limitations in mechanical properties. In contrast, 7xxx series aluminum alloys (Al-Zn-Mg-Cu based) exhibit superior mechanical properties but are prone to hot tearing during casting.
- Limitations of Existing Research: Existing research has primarily focused on Al-Si alloys, with limited in-depth studies on the casting characteristics of 7xxx series alloys, particularly their hot tearing susceptibility. Direct application of commercially available high-strength alloys in casting processes has been challenging.
- Necessity of the Research: There is a need to develop high-strength aluminum alloys that can overcome the mechanical property limitations of Al-Si alloys and replace stainless steel propellers. Research is required to optimize the low-pressure die-casting (LPDC) process for 7xxx series alloys to enhance propeller performance and durability, addressing the issue of hot tearing.
3. Research Purpose and Research Questions: Evaluating Hot Tearing Susceptibility and Exploring Optimal Alloy Composition in 7xxx Series Alloys
- Research Purpose: This study aims to evaluate the hot tearing susceptibility (HTS) of 7xxx series aluminum alloys in low-pressure die-casting (LPDC) processes and to develop an optimal alloy composition that minimizes HTS.
- Key Research Questions:
- How do compositional changes in Al-Zn-Mg-Cu alloys affect hot tearing susceptibility (HTS) during low-pressure die casting?
- Can finite element simulations effectively predict hot tearing susceptibility in these alloys?
- What are the optimal Al-Zn-Mg-Cu alloy compositions with relatively low hot tearing susceptibility suitable for LPDC propeller production?
- Research Hypotheses:
- In Al-Zn-Mg-Cu alloys, increasing Zn and Cu content will generally increase hot tearing susceptibility (HTS).
- Sufficient Mg content addition can mitigate the increase in HTS caused by Zn and Cu.
- Optimal quaternary Al-Zn-Mg-Cu alloys with relatively low hot tearing susceptibility, suitable for LPDC propeller production, can be identified through simulation and experimental validation.
4. Research Methodology: Utilizing Constrained Rod Casting (CRC) and Finite Element Simulation
- Research Design: Experimental constrained rod casting (CRC) and finite element simulations were used in parallel to evaluate the hot tearing susceptibility (HTS) of various Al-Zn-Mg-Cu alloy compositions.
- Data Collection Methods:
- Alloy Chemical Composition Analysis: ICP-OES (Inductively Coupled Plasma Optical Emission Spectrometry) analysis.
- Hot Tearing Evaluation: Visual inspection of CRC castings, categorizing the degree of hot tearing into four levels (short hairline, full hairline, crack, half-broken rod).
- Simulation Data: Hot tearing indicator (HTI) and effective plastic strain data collected using ProCAST 2021 software.
- Analysis Methods:
- Calculation of Experimental HTS Index (HTSexp.): HTS index calculated based on crack severity, rod length, and crack location.
- Calculation of Simulation HTS Index (HTSsimul.): HTSsimul. values derived from HTI values using Gurson constitutive model-based ProCAST software.
- Analysis of HTSsimul. changes according to alloy composition variations.
- Research Subjects and Scope: Commercial 7xxx series aluminum alloys (AA7075, AA7068, AA7055) and Al-Zn-Mg-Cu quaternary alloys with various compositions were set as research subjects. The research scope included HTS evaluation through constrained rod casting (CRC) and LPDC simulation and experimental casting of propellers using optimized alloys.
5. Main Research Results: HTS Increases with Zn and Cu Content, Mitigated by 2wt.% Mg Addition
- Key Research Results:
- CRC experiments showed HTSexp. values of 328, 376, and 384 for AA7075, AA7068, and AA7055 alloys, respectively, indicating an increasing trend of HTS from AA7075 to AA7055.
- Simulation results showed a high linear relationship between predicted HTS(rod)simul. values and experimentally evaluated HTS(rod)exp. values, validating the simulation model.
- In Al-Zn-Mg-Cu quaternary alloys, HTSsimul. values tended to increase with increasing Zn and Cu content, but this increase was mitigated when the Mg content was 2 wt.% or higher.
- Two optimized quaternary alloys with relatively low HTSsimul. values (Al-6Zn-2Mg-0.5Cu and Al-6Zn-2Mg-1.5Cu) were selected.
- LPDC simulation and experimental casting of propellers showed no hot tearing in the Al-6Zn-2Mg-0.5Cu alloy, while hot tearing occurred at the hub-blade junction in the Al-6Zn-2Mg-1.5Cu alloy, consistent with simulation predictions.
- Statistical/Qualitative Analysis Results:
- Experimental HTSexp. values for commercial alloys increased in the order AA7075 < AA7068 < AA7055.
- A strong linear correlation (R² = 0.98) was confirmed between HTS(rod)simul. and HTS(rod)exp. values.
- HTSsimul. values for quaternary alloys showed an increasing trend with increasing Zn and Cu content, but the rate of increase slowed down with the addition of 2 wt.% Mg.
- Data Interpretation:
- The increase in HTS with higher Zn and Cu content is attributed to the wider solidification temperature range (STR).
- Mg addition of 2 wt.% effectively reduces HTS, likely due to the formation of a sufficient eutectic liquid phase, effectively compensating for solidification and thermal shrinkage.
- Simulation results accurately predicted the trend and location of hot tearing in both CRC and LPDC processes.
- Figure Name List:
- Figure 1. Examples of casting defects in the LPDC 7xxx series aluminum alloy propellers: (a) misrun; (b) crack; (c) hot tearing.
- Figure 2. Appearance of mold for constrained rod casting.
- Figure 3. Simulation models showing 3D mesh: (a) CRC; (b) LPDC.
- Figure 4. Thermo-physical properties of aluminum alloys used in the simulation: (a) conductivity; (b) density; (c) enthalpy; (d) viscosity; (e) thermal expansion; (f) Young's modulus; (g) yield stress; (h) Poisson's ratio; (i) plastic modulus.
- Figure 5. Results of constrained rod casting: (a) AA7075; (b) AA7068; (c) AA7055.
- Figure 6. Simulation results of the hot-tearing indicator for CRC 7xxx alloys.
- Figure 7. Comparison of simulation and experiment results for CRC 7xxx alloys: (a) HTS(rod)exp. vs. HTS(rod)simul.; (b) HTSexp. vs. HTSsimul..
- Figure 8. HTSsimul. values for various Zn, Mg, and Cu contents in Al-Zn-Mg-Cu Alloys: (a) Al-7Zn-xMg-yCu; (b) Al-xZn-2.0Mg-yCu.
- Figure 9. Simulation and experimental results of LPDC Al-Zn-Mg-Cu alloys: (a) Al-6Zn-2Mg-0.5Cu; (b) Al-6Zn-2Mg-1.5Cu (in wt.%).
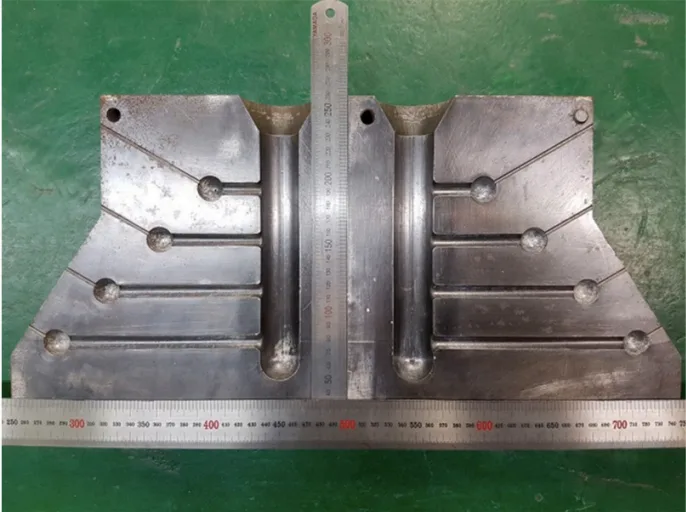
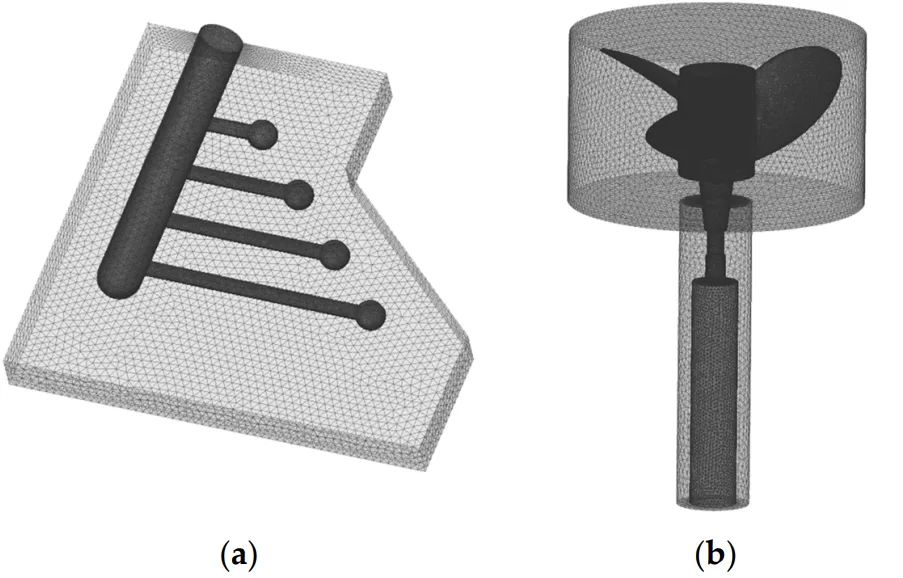
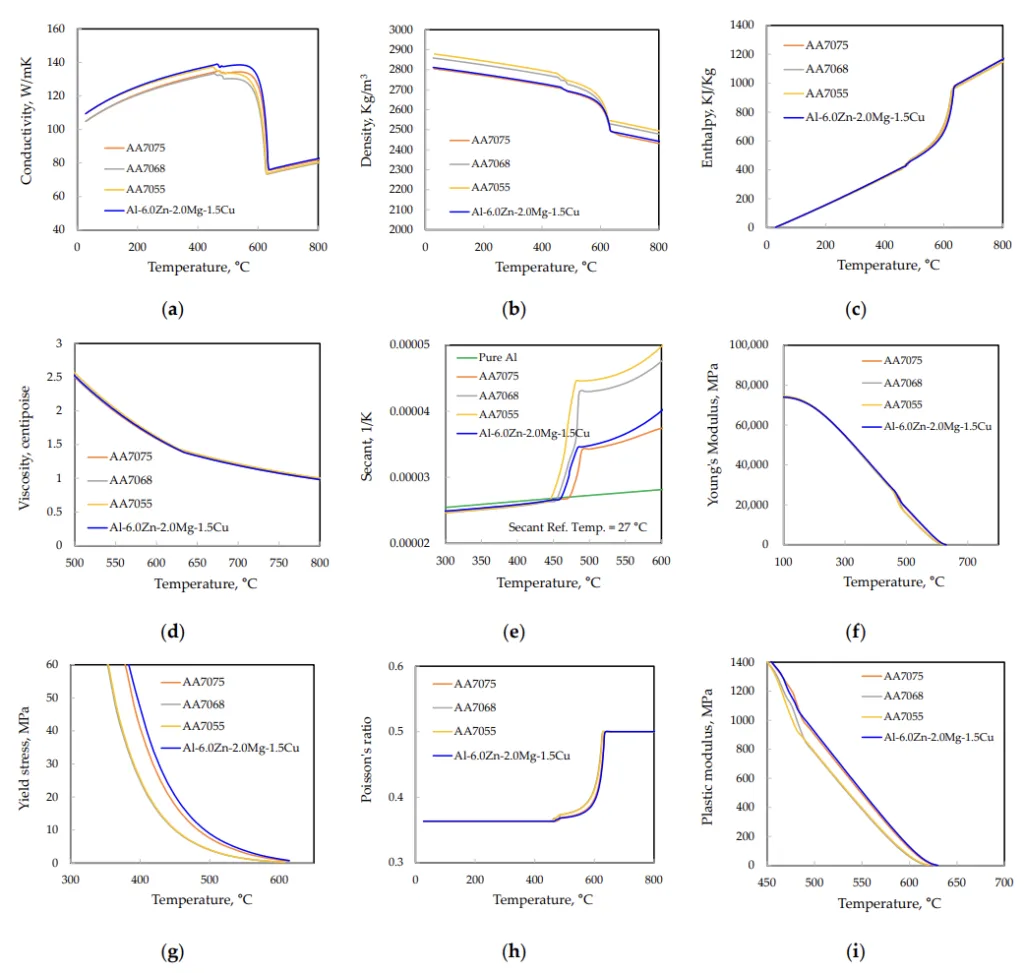
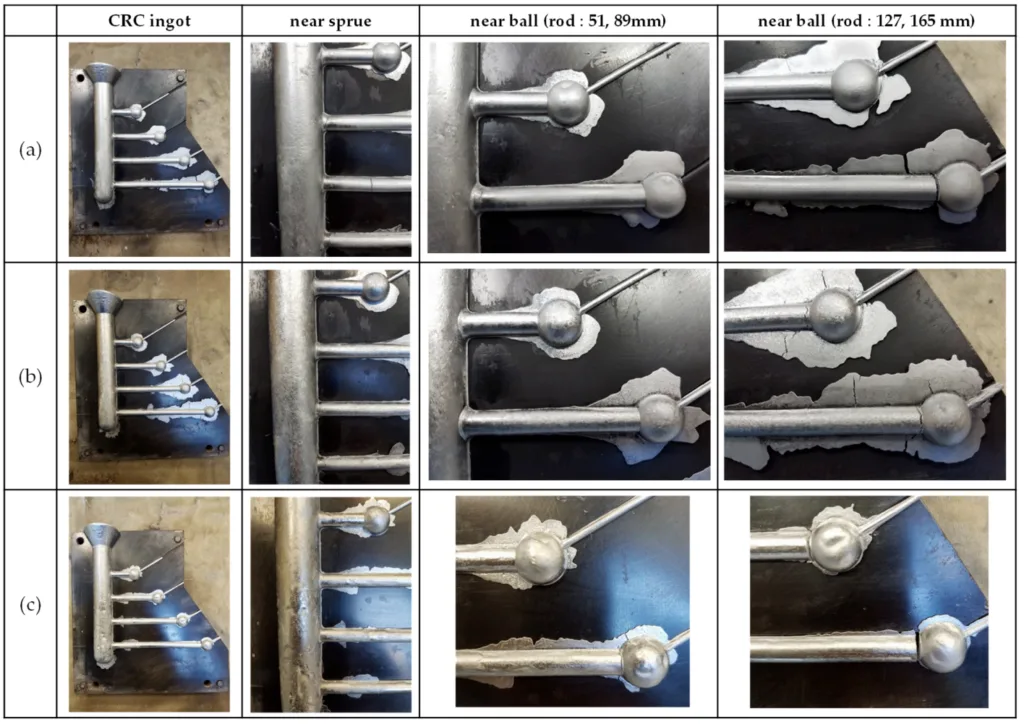
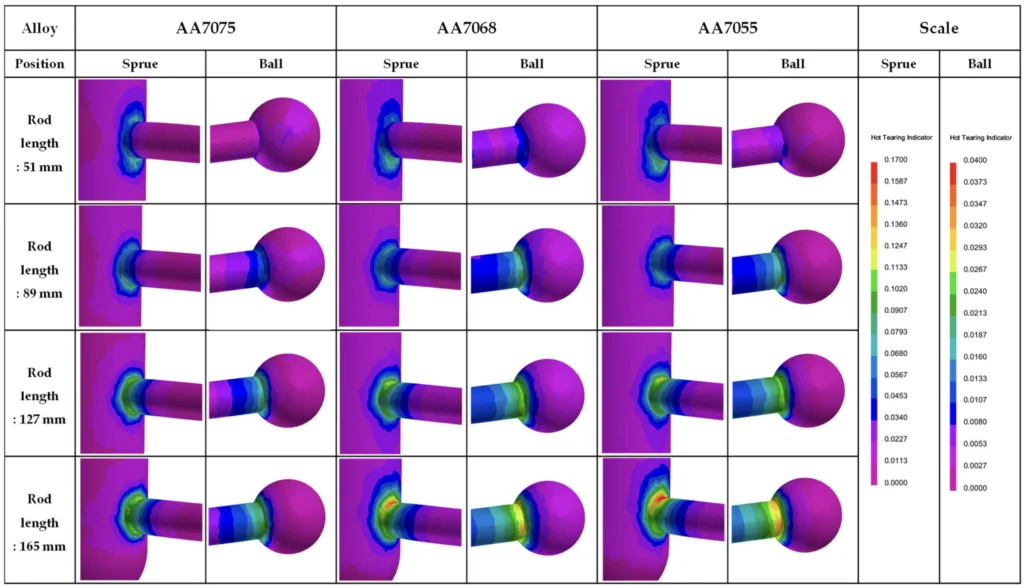
6. Conclusion and Discussion: Feasibility of 7xxx Series Alloy Propeller Manufacturing Confirmed, Further Process Optimization Needed
- Summary of Main Results: This study successfully evaluated the hot tearing susceptibility (HTS) of commercial and optimized Al-Zn-Mg-Cu alloys using CRC experiments and finite element simulations. It was found that increasing Zn and Cu generally increases HTS, while sufficient Mg (2 wt.%) mitigates it. Two optimized alloys (Al-6Zn-2Mg-0.5Cu and Al-6Zn-2Mg-1.5Cu) with low HTS were selected, and their feasibility for LPDC propeller manufacturing was validated.
- Academic Significance of the Research: This research enhances the understanding of hot tearing mechanisms in 7xxx series aluminum alloys and demonstrates the effectiveness of simulation-based alloy optimization methods. It elucidated the complex interplay between alloy composition, solidification temperature range, and eutectic phase fraction in determining HTS.
- Practical Implications: This study provides practical guidelines for designing Al-Zn-Mg-Cu alloys with improved castability for LPDC, specifically for propeller manufacturing. The identified alloy compositions, particularly Al-6Zn-2Mg-0.5Cu, offer a viable alternative to traditional alloys for high-performance propellers, reducing hot tearing defects and potentially lowering production costs.
- Limitations of the Research: This study focused on alloy composition optimization. Further process optimization is needed, especially for higher-Cu-content alloys like Al-6Zn-2Mg-1.5Cu, to completely eliminate hot tearing in LPDC. This research is Part I, focusing on hot tearing simulations; further experimental validation and process optimization will be explored in Part II.
7. Future Follow-up Research: Need for LPDC Process Variable Optimization and Heat Treatment Studies
- Directions for Follow-up Research: Future research should focus on optimizing the LPDC process for Al-Zn-Mg-Cu alloys, especially those with higher Mg and Cu content, to more effectively suppress hot tearing.
- Areas Requiring Further Exploration: Part II research will analyze the effects of LPDC process variables on hot tearing using simulation models and discuss process optimization strategies in detail. Further research is also needed to optimize heat treatment processes to maximize the mechanical properties of these cast alloys.
8. References:
- Kluczyk, M.; Grządziela, A.; Batur, T. Design and operational diagnostics of marine propellers made of polymer materials. Pol. Marit. Res. 2022, 29, 49–59.
- Cass, A.; Nielson, J.R. Smart energy systems approach to zero emissions long-range sailing vessels. Smart Energy 2022, 7, 100086.
- Oloruntobi, O.; Mokhtar, K.; Gohari, A.; Asif, S. Sustainable transition towards greener and cleaner seaborne shipping industry: Challenges and opportunities. Clean. Eng. Technol. 2023, 13, 100628.
- Baley, C.; Davies, P.; Troalen, W.; Chamley, A.; Dinham-Price, I.; Marchandise, A.; Keryvin, V. Sustainable polymer composite marine structure: Developments and challenges. Prog. Mater. Sci. 2024, 145, 101307.
- Dashtimanesh, A.; Ghaemi, M.H.; Wang, Y. Digitalization of high speed craft design and operation challenges and opportunities. Procedia Comput. Sci. 2022, 200, 566–576.
- Begovic, E.; Bertorello, C.; De Luca, F. KISS (Keep It Sustainable and Smart): A research and development program for a zero-emission small crafts. J. Mar. Sci. Eng. 2022, 10, 16.
- Choudhary, G.; Singh, G. Comparative analysis of corrosion behaviour of stainless steel grades 304 and 316L for different applications. I-Manag. J. Mater. Sci. 2020, 7, 8–22.
- Mendagaliev, R.; Klimova-Korsmik, O.; Promakhov, V.; Schulz, N.; Zhukov, A.; Klimenko, V.; Olisov, A. Heat treatment of corrosion resistant steel for water propellers fabricated by direct laser deposition. Materials 2020, 13, 2738.
- Konieczny, J.; Labisz, K. Materials used in the combat aviation construction. Transp. Probl. 2021, 16, 5–18.
- Bhuiyan, M.S.; Sian, I.H.; Kharshiduzzaman, M. Unveiling the microstructure of LES manufactured parts for sustainable productive business. J. Alloys Compd. 2023, 4, 100038.
- Zhou, B.; Liu, B.; Zhang, S. The advancement of 7xxx series aluminum alloys for aircraft structures: A review. Metals 2021, 11, 718.
- Wang, Z.; Jiang, H.; Li, H.; Li, S. Effect of solution-treating temperature on the intergranular corrosion of a peak-aged Al-Zn-Mg-Cu alloy. J. Mater. Res. Technol. 2020, 9, 6497–6511.
- Cheng, Q.; Ye, L.; Huang, Q.; Dong, Y.; Liu, S. Effect of two-stage overaging on microstructure and corrosion properties of an Al-Zn-Mg-Cu alloy. J. Mater. Res. Technol. 2022, 20, 3185–3194.
- Wang, A.; Silva, K.; Jones, M.; Robinson, P.; Larribe, G.; Gao, W. Anticorrosive coating systems for marine propellers. Prog. Org. Coat. 2023, 183, 107768.
- Xue, W.; Wang, C.; Tian, H.; Lai, Y. Corrosion behaviors and galvanic studies of microarc oxidation films on Al-Zn-Mg-Cu alloy. Surf. Coat. Technol. 2007, 201, 8695–8701.
- Jolly, M.; Katgerman, L. Modelling of defects in aluminium cast products. Prog. Mater. Sci. 2022, 123, 100824.
- Li, Y.; Li, H.; Katgerman, L.; Du, Q.; Zhang, J. Recent advances in hot tearing during casting of aluminium alloys. Prog. Mater. Sci. 2021, 117, 100741.
- Pulisheru, K.S.; Birru, A.K. Effect of pouring temperature on hot tearing susceptibility of Al-Cu cast alloy: Casting simulation. Mater. Today Proc. 2021, 47, 7086–7090.
- Ali, R.; Zafar, M.; Manzoor, T.; Kim, W.Y.; Rashid, M.U.; Abbas, S.G.; Zai, B.A.; Ali, M. Elimination of solidification shrinkage defects in the casting of aluminum alloy. J. Mech. Sci. Tehnol. 2022, 36, 2345–2353.
- Rahangmetan, K.A.; Sariman, F.; Parenden, D. The effect of riser use in the quality of casting Al 7075 for ship propeller. Int. J. Mech. Eng. Technol. 2019, 10, 10–17.
- Dong, G.; Li, S.; Ma, S.; Zhang, D.; Bi, J.; Wang, J.; Starostenkov, M.D.; Xu, Z. Process optimization of A356 aluminum alloy wheel hub fabricated by low-pressure die casting with simulation and experimental coupling methods. J. Mater. Res. Tehnol. 2023, 24, 3118–3132.
- Song, J.; Pan, F.; Jiang, B.; Atrens, A.; Zhang, M.X.; Lu, Y. A review on hot tearing of magnesium alloys. J. Magnes. Alloy 2016, 4, 151–172.
- Wang, Z.; Song, J.; Huang, Y.; Srinivasan, A.; Liu, Z.; Kainer, K.U.; Hort, N. An Investigation on Hot Tearing of Mg-4.5Zn-(0.5Zr) Alloys with Y Additions. Metall. Mater. Trans. A 2015, 46, 2108–2118.
- Wang, J.; Fu, P.; Peng, L.; Wang, Y.; Ding, W. A simplified hot-tearing criterion for shape castings based on temperature-field simulation. Metall. Mater. Trans. A 2019, 50, 5271–5280.
- Li, L.; Zhang, R.; Yuan, Q.; Huang, S.; Jiang, H. An integrated approach to study the hot tearing behavior by coupling the microscale phase field model and macroscale casting simulations. J. Mater. Proc. Technol. 2022, 310, 117782.
- Xu, Y.; Zhang, Z.; Gao, Z.; Bai, Y.; Zhao, P.; Mao, W. Effect of main elements (Zn, Mg and Cu) on the microstructure, castability and mechanical properties of 7xxx series aluminum alloys with Zr and Sc. Mater. Charact. 2021, 182, 111559.
- Guo, J.; Samonds, M.T. Alloy thermal physical property prediction coupled computational thermodynamics with back diffusion consideration. J. Phase Equlib. Diff. 2007, 28, 58–63.
- Li, Y.; Zhang, Z.R.; Zhao, Z.Y.; Li, H.X.; Katgerman, L.; Zhang, J.S.; Zhuang, L.Z. Effect of main elements (Zn, Mg, and Cu) on hot tearing susceptibility during direct-chill casting of 7xxx aluminum alloys. Metall. Mater. Trans. A 2019, 50, 3603–3616.
- Kim, J.H.; Jo, J.S.; Sim, W.J.; Im, H.J. The influence of alloy composition on the hot tear susceptibility of the Al-Zn-Mg-Cu alloy system. Korean J. Met. Mater. 2012, 50, 669–675.
- Clyne, T.W.; Wolf, M.; Kurz, W. The effect of melt composition on solidification cracking of steel, with particular reference to continuous casting. Metall. Trans. B 1982, 13, 259–266.
9. Copyright:
This material is based on Min-Seok Kim and Jiwon Kim's paper: "Development of Low-Pressure Die-Cast Al–Zn–Mg–Cu Alloy Propellers—Part I: Hot Tearing Simulations for Alloy Optimization."
Paper Source: [DOI URL] https://doi.org/10.3390/ma17133133
This material was summarized based on the above paper, and unauthorized use for commercial purposes is prohibited.
Copyright © 2025 CASTMAN. All rights reserved.