This article introduces the paper "Simulation of variable thickness aluminum alloy plate casting".
1. Overview:
- Title: Simulation of variable thickness aluminum alloy plate casting
- Author: G. S. Reddy, and Md. Hafeez
- Publication Year: 2024
- Publishing Journal/Academic Society: Journal of Physics: Conference Series
- Keywords: Casting simulation, heat flow, fluid flow, cooling curves, solidification.
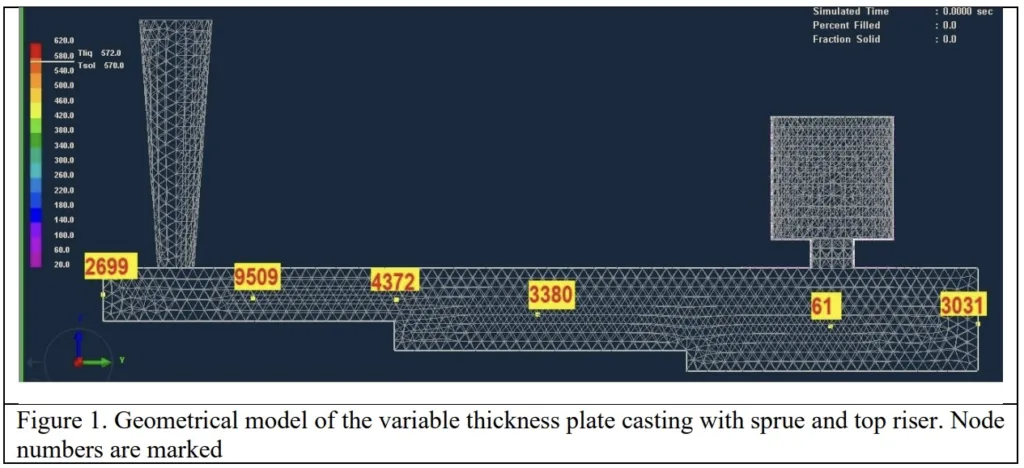
2. Research Background:
- Social/Academic Context of the Research Topic: Aluminum alloys are increasingly important due to their versatile properties, especially in the growing electric vehicle manufacturing sector. The automotive industry is shifting towards using more aluminum components.
- Limitations of Existing Research: There is a recognized gap between the predictions of casting simulations and real-world casting outcomes.
- Necessity of the Research: This research is necessary to improve the understanding of the solidification process in aluminum alloy castings, specifically to mitigate macro shrinkage. It aims to enhance the reliability and practical application of solidification models in casting processes.
3. Research Purpose and Research Questions:
- Research Purpose: The primary purpose of this research is to investigate the simulation of variable thickness aluminum alloy plate casting to better understand the solidification process and find ways to reduce macro shrinkage in castings.
- Key Research Questions: The study implicitly seeks to answer how simulation can be effectively used to understand and optimize the casting process of variable thickness aluminum alloy plates, particularly focusing on the solidification process and shrinkage mitigation.
- Research Hypotheses: The research operates under the hypothesis that simulation can be a valuable tool for understanding and optimizing the casting process to minimize or eliminate shrinkage porosity in variable thickness aluminum alloy plate castings.
4. Research Methodology
- Research Design: This research employs a simulation-based approach using finite element analysis to model the solidification process of a variable thickness aluminum alloy plate casting.
- Data Collection Method: The data is collected through simulation outcomes, focusing on temperature distribution, cooling curves, fluid flow, and solidification patterns within the casting model.
- Analysis Method: The analysis involves numerical examination of the simulation results to understand the solidification process, identify potential shrinkage areas, and evaluate the effectiveness of the casting design. The study focuses on heat transfer, fluid flow, and solidification dynamics.
- Research Subjects and Scope: The research focuses on the simulation of variable thickness plate casting using Al-13%Si alloy and sand molds. The geometrical model includes a blind top riser and open sprue. An alternative configuration with a side riser was also implemented for comparative analysis.
5. Main Research Results:
- Key Research Results: The simulation results indicate the absence of shrinkage porosity in the variable thickness aluminum alloy plate casting. The last solidification events are observed in the risers and sprue. The temperature distribution and cooling curves confirm directional solidification, aligning with desired temperature gradients.
- Statistical/Qualitative Analysis Results: Qualitative analysis of the simulation outcomes reveals:
- Absence of Shrinkage Porosity: "Simulation outcomes reveal the absence of shrinkage porosity".
- Last Solidification Location: "with the last solidification events occurring in risers and sprue".
- Directional Solidification: "The temperature distribution and cooling curves affirm directional solidification, aligning with desired temperature gradients."
- Data Interpretation: The results highlight the role of silicon in reducing shrinkage porosity in aluminum alloys. The study emphasizes the critical importance of quality input data, including temperature-dependent properties and initial boundary conditions, for accurate simulation results. Continuous monitoring of simulation process data, focusing on factors like turbulence, modulus ratios, and directional solidification, is crucial for refining predictive models.
- Figure Name List:
- Figure 1. Geometrical model of the variable thickness plate casting with sprue and top riser.
- Figure 2. Filling of liquid aluminum alloy into a mold cavity. Fluid flow velocity vectors show unidirectional flow without turbulence.
- Figure 3. Filling into riser cavity. The maximum fluid velocity observed is 0.621 m/s.
- Figure 4. Shrinkage porosity found in sprue and riser.
- Figure 5. Temperature distribution during post-solidification.
- Figure 6. Cooling curves demonstrate directional solidification from the sprue into the riser.
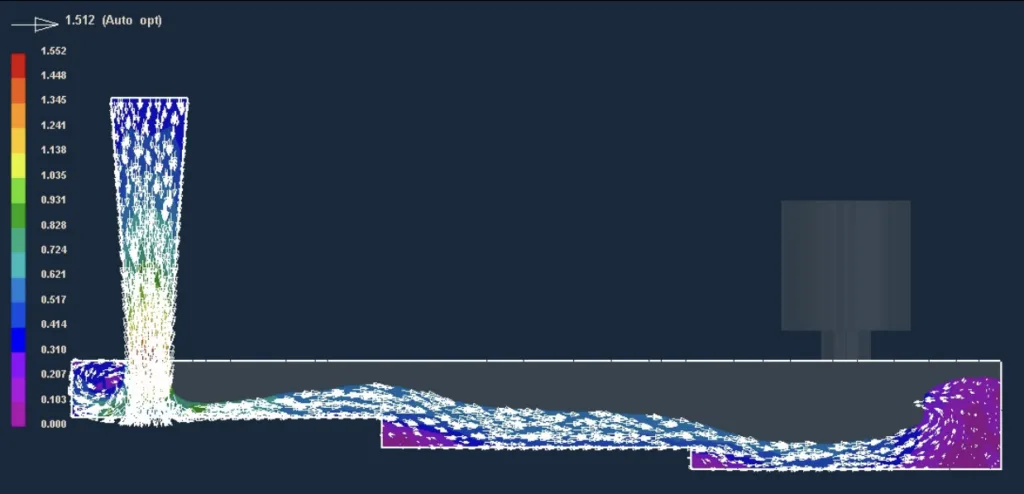
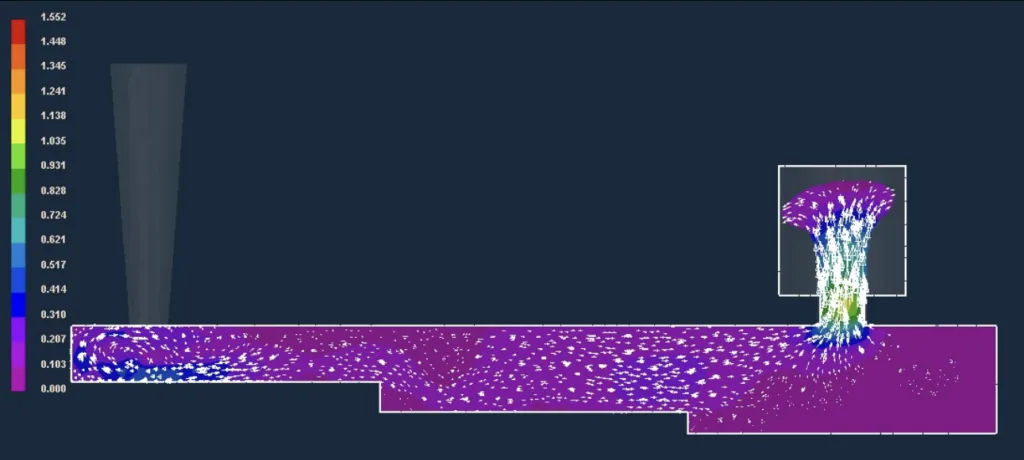
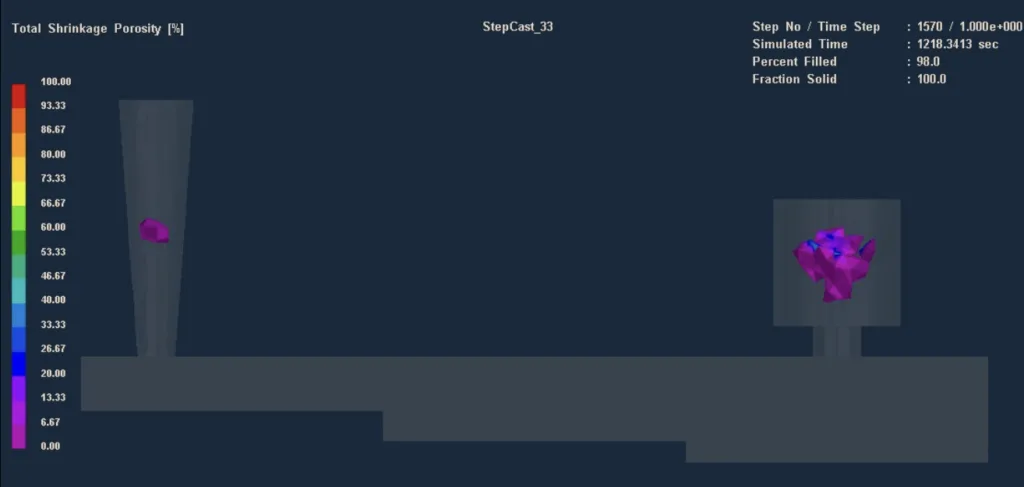
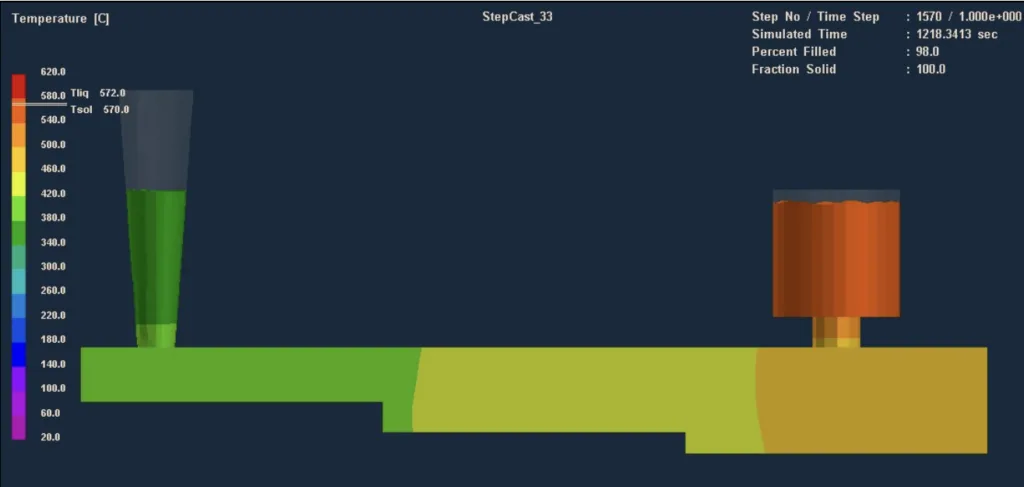
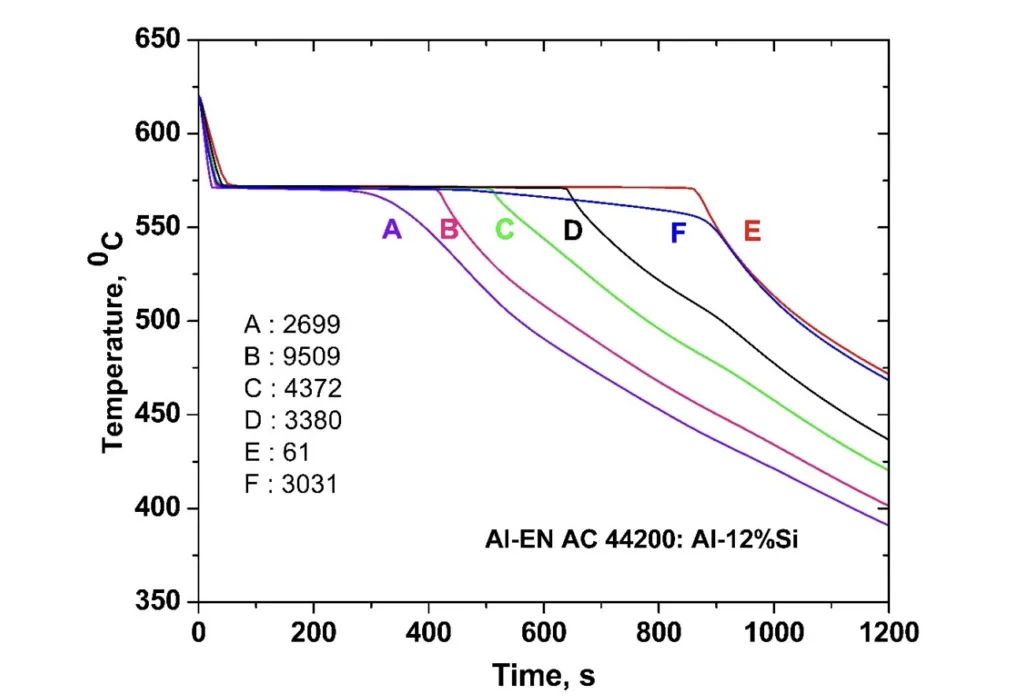
6. Conclusion and Discussion:
- Summary of Main Results: The simulation of variable thickness aluminum alloy plate casting successfully demonstrated the absence of shrinkage porosity, with the final solidification occurring in the riser and sprue. The simulation also confirmed directional solidification.
- Academic Significance of the Research: This research contributes to the advancement of understanding aluminum alloy solidification processes. It enhances the reliability and applicability of solidification models by bridging the gap between simulation and real-world casting outcomes.
- Practical Implications: The study provides valuable insights for optimizing casting processes through simulation, particularly for mitigating macro shrinkage in aluminum alloy castings. The findings are especially relevant to the automotive industry, which is increasingly adopting aluminum components.
- Limitations of the Research: The study underscores that the accuracy of simulation results is highly dependent on the quality of input data, including temperature-dependent material properties and initial boundary conditions. This highlights the need for careful data management and validation in casting simulations.
7. Future Follow-up Research:
- Directions for Follow-up Research: Future research should focus on continued exploration of alloy composition, various casting techniques, and advancements in simulation methodologies. This will further improve the performance and broaden the utility of aluminum alloys in diverse industries.
- Areas Requiring Further Exploration: Further exploration is needed in refining predictive models by continuously auditing simulation process data. Key areas include turbulence dynamics during mold filling, modulus of volume-to-surface area ratios, and directional solidification control.
8. References:
- G.M. Scamans, N. Birbilis, R.G. Buchheit, “Corrosion of Aluminium and its Alloys", Shreir's Corrosion, Volume 3, 2010, Pages 1974-2010; https://doi.org/10.1016/B978-044452787-5.00095-0
- J. Gilbert Kaufman, and Elwin L. Rooy, “Aluminum alloy castings: Properties, Processes, and applications", 2004 ASM International. pp 1-321.
- Baser, T. A., Umay, E., & Akinci, V. (2022). “New trends in aluminum casting alloys for automotive applications. The Eurasia Proceedings of Science Technology engineering and mathematics, 21, 79-87. https://doi.org/10.55549/epstem.1227541.
- C. Berlanga-Labari, M. V. Biezma-Moraleda, and Pedro J. Rivero, “Corrosion of Cast Aluminum Alloys: A Review", MDPI journal, Metals 2020, 10, 1384; doi:10.3390/met10101384
- Mariem Ben Saada, Mohamed El Mansouri, “Assessment of the effect of 3D printed sand mold thickness on solidification process of AlSi13 casting alloy", International Journal of Advanced Manufacturing Technology, 2021, 114 (5-6), pp.1753-1766. 10.1007/s00170-021-06999-3. HAL-03220855
- Meet Upadhyay, Tharmalingam Sivarupan, Mohamed El Mansori, “3D printing for rapid sand casting- A review", Journal of Manufacturing Processes, 2017, 29, pp.211-220. 10.1016/j.jmapro.2017.07.017. hal-02417595.
- D. Martinez, C. Bate, and G. Manogharan, “Towards functionally graded sand molds for metal casting: Engineering thermo-mechanical properties using 3D sand printing", 2020 The Minerals, Metals & Materials Society, https://doi.org/10.1007/s11837-019-03975-x, Materials properties, ESI Group, 04-June-2013
- Cusato, N.; Nabavizadeh, S.A.; Eshraghi, M. A Review of large-scale simulations of microstructural evolution during alloy solidification. Metals 2023, 13, 1169. https://doi.org/10.3390/met13071169, Academic editors: Changing Fang and Chang Yong Jo.
- Philip King and Guha Manogharan, “Novel experimental method for metal flow analysis using open molds for sand casting”, International Journal of Metal casting/Volume 17, Issue 4, 2023. Pp 2892-2903.
- Bate, C.; King, P.; Sim, J.; Manogharan, G, “A novel approach to visualize liquid aluminum flow to advance casting science, Materials, 2023, 16, 756. https://doi.org/10.3390/ma16020756.
- Griffiths, W. D., & Atkinson, H. V. (1999). The influence of alloy composition on shrinkage porosity formation during the solidification of aluminum alloys. Metallurgical and Materials Transactions A, 30(2), 361-372.
- El-Bealy, M. M., Abd-Elhady, E. A., & Abdel-Rahman, A. M. (2019). Simulation of shrinkage defects in aluminum alloy castings using numerical modeling. Journal of Manufacturing Processes, 41, 72-80.
- GS Reddy, WJ Mascarenhas, JN Reddy, Metallurgical Transactions B 24, 677 -684.
- Cheng Guª, Colin D. Ridgewaya, Emre Cinkilica, Yan Luª, Alan A. Luo a,*
- Olawale Olarewaju Ajibola, et al, "Effects of molding sand permeability and pouring temperatures on properties of cast 6061 aluminum alloy", International Journal of Metals, Volume 2015, Article ID 632021, pp 21-13, http://dx.doi.org/10.1155/2015/632021
- Neuser, M.; Grydin, O.; Andreiev, A.; Schaper, M. Effect of Solidification Rates at Sand Casting on the Mechanical Joinability of a Cast Aluminium Alloy. Metals 2021, 11, 1304. https://doi.org/10.3390/met11081304
- Dash, S.S.; Chen, D. A, “Review on processing-microstructure-property relationships of Al-Si alloys"; Recent advances in deformation behavior, Metals 2023, 13, 609. https://doi.org/10.3390/met13030609.
- For a Livable Climate: Net-Zero Commitments Must Be Backed by Credible Action. Available online: https://www.un.org/en/climatechange/net-zero-coalition (accessed on 20 January 2023).
- Svendsen, A. Aluminum Continues Unprecedented Growth in Automotive Applications. Available online: https://www.lightmetalage.com/news/industry-news/automotive/aluminum-continues-unprecedented-growth-in-automotiveapplications/(accessed on 20 January 2023
- Javidani, M.; Larouche, D. Application of CastAl-Si Alloys in Internal Combustion Engine Components. Int. Mater. Rev. 2014, 59, 132–158. [CrossRef].
- Torres, R.; Esparza, J.; Velasco, E.; Garcia-Luna, S.; Colas, R. Characterisation of an Aluminum Engine Block. Int. J. Microstructure. Mater. Prop. 2006, 1, 129. [CrossRef]
- Czerwinski, F. Thermal Stability of Aluminum Alloys. Materials 2020, 13, 3441. [CrossRef]
- Fan, Y.; Makhlouf, M.M. The Al-Al3Ni Eutectic Reaction: Crystallography and Mechanism of Formation. Metall. Mater. Trans. A 2015, 46, 3808–3812. [CrossRef]
- Czerwinski, F.; Kasprzak, W.; Sediako, D.; Emadi, D.; Shaha, S.; Friedman, J.; Chen, D.L. High-Temperature Aluminum Alloys for Automotive Powertrains; Cast Aluminum AlloysWere Developed with High-Temperature Tensile and Fatigue Strengths to Withstand Elevated-Temperature Applications in Modern Engines. Adv. Mater. Process. 2016, 174, 16–21.
- Geoffrey Sigworth, and Timothy A. Kuhn, “Grain Refinement of Aluminum Casting Alloys", International Journal of Metal casting, September 2007, 115(2):1-12; DOI:10.1007/BF03355416.
- Jun Wang, Shuxian He, and Baode Sun, "Grain refinement of Al-Si alloy (A356) by melt thermal treatment", Journal of Materials Processing Technology, October 2003, 141(1):29-34, DOI:10.1016/S0924-0136(02)01007-5
- Zamani, Mohammadreza, “Al-Si Cast alloys - Microstructure and mechanical properties at ambient and elevated temperatures”, Ph.D. thesis, 2017, Jönköping University, School of Engineering.
- Fracchia, E.; Gobber, F.S.; Rosso, M. "Effect of alloying elements on the Sr modification of Al-Si cast alloys”. Metals 2021, 11, 342. https:// doi.org/10.3390/met11020342.
- Sathyapal Hegde and K. Narayan Prabhu, “Modification of eutectic silicon in Al-Si alloys", J Mater Sci (2008) 43:3009–3027, DOI 10.1007/s10853-008-2505-5, pp 1-19.
- X Cao and J Campbell, "Hard spot defects in aluminum-silicon cast alloys", Shape Casting: The John Campbell Symposium Edited by Murat Tiryakioglu and Paul N. Crepeau TMS (The Minerals, Metals, & Materials Society), 2005 https://www.researchgate.net/publication/287911378
- Anil Saigal, Edwin R. Fuller Jr, “Analysis of stresses in aluminum-silicon alloys", Computational Materials Science, Volume 21, Issue 1, May 2001, Pages 149-158.
- R.B. Gundlach et al, “Thermal fatigue resistance of hypoeutectic aluminum-silicon casting alloys", AFS Trans. (1994)
- Bao Quoc Doan, Dinh Tuyen Nguyen, Minh Nhat Nguyen, Tri Hieu L, Thi Minh Hao Dong, Le Hung Duong, “A Review on Properties and Casting Technologies of Aluminum Alloy in The Machinery Manufacturing", Journal of Mechanical Engineering Research and Developments ISSN: 1024-1752 CODEN: JERDFO Vol. 44, No. 8, pp. 204-217 the Published Year 2021.
- G.S. Reddy and G.R.K. Murthy, "Liquid forging of an aluminum alloy”, Trans of the IIM, 31 (5), 484-487, 1978.
- G.S. Reddy, Ph.D. thesis, “Solidification of metals and alloys under pressure", 1987, Institute of Technology, BHU, Varanasi, India.
- GS Reddy, K Saurabh, DM Krishna, ‘Numerical Simulation Of Directionally Solidified CM247LC High Pressure Turbine Blade', Materials Today: Proceedings 4 (8), 7820-7830.
- GS Reddy, K. Saurabh, R Yedu Krishnan, Numerical Simulation of CM247SX Single Crystal High-Pressure Turbine Vane, Materials Today Proceedings Science Direct, 7837 – 7847.
9. Copyright:
- This material is G. S. Reddy, and Md. Hafeez's paper: Based on Simulation of variable thickness aluminum alloy plate casting.
- Paper Source: doi:10.1088/1742-6596/2837/1/012092
This material was summarized based on the above paper, and unauthorized use for commercial purposes is prohibited.
Copyright © 2025 CASTMAN. All rights reserved.