This article introduces the paper "Evaluation of Corrosion Behavior on Crept AlSi10MnMg (AA365) Alloy Produced by High-Pressure Die-Casting (HPDC)".
1. Overview:
- Title: Evaluation of Corrosion Behavior on Crept AlSi10MnMg (AA365) Alloy Produced by High-Pressure Die-Casting (HPDC)
- Authors: Seonghwan Park, Cheolmin Ahn, and Eunkyung Lee
- Publication Year: 2021
- Publishing Journal: Applied Sciences, MDPI
- Keywords: aluminum alloy; corrosion; microstructure; temperature; intermetallic compounds
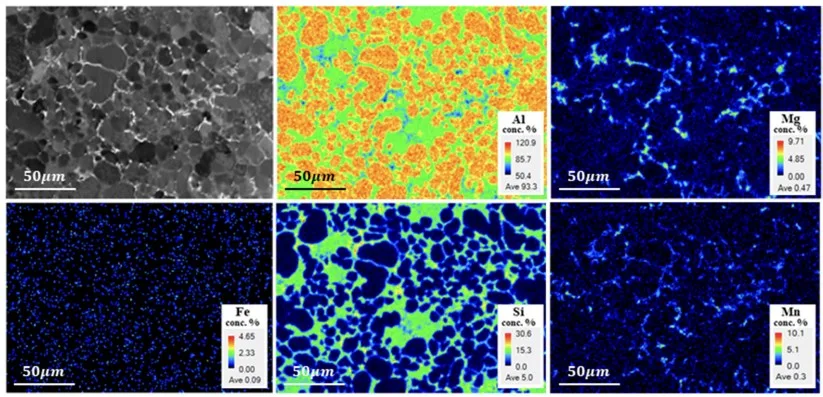
2. Research Background:
- Social/Academic Context of the Research Topic:
- The increasing demand for lightweight materials in industries like automotive, marine, and aerospace is driven by environmental regulations and the need for improved fuel efficiency.
- Aluminum alloys are gaining prominence due to their advantageous properties, including light weight, excellent corrosion resistance, and high strength-to-weight ratio [1].
- AlSi10MnMg (Silafont-36, AA365) alloy is a leading aluminum-silicon alloy known for its good castability, wear resistance, corrosion resistance, and high elongation [2].
- High-Pressure Die-Casting (HPDC) is the primary production method for AA365 alloy, enabling high productivity and the creation of complex components [3,4].
- HPDC AA365 alloy is extensively used in automotive powertrain systems, such as cylinder heads and engine blocks, which operate in high-temperature and corrosive environments [2].
- Limitations of Existing Research:
- While previous studies have explored various characteristics of AlSi10MnMg alloys, including microstructure, casting defects, heat treatment, mechanical properties, and corrosion resistance [11-14], there is a gap in understanding the corrosion behavior under creep conditions.
- Existing research has shown that the properties of AlSi10MnMg alloys vary with cooling rates after T4 and T6 heat treatments [9], and superior creep resistance has been observed under high temperature and stress [2]. However, the corrosion properties of AlSi10MnMg alloy affected by applied stress at high temperature remain under-investigated.
- Necessity of the Research:
- To address the limited understanding of corrosion behavior in crept AlSi10MnMg alloy, this research aims to investigate corrosion from a microstructural perspective.
- The study seeks to contribute to enhancing the reliability and long-term structural performance of AA365 alloy in automotive applications by examining the correlation between corrosion resistance and microstructural features like intermetallic compounds and micro-voids under creep conditions.
- Understanding this relationship is crucial for predicting and mitigating corrosion in components subjected to long-term temperature and stress.
3. Research Purpose and Research Questions:
- Research Purpose:
- The primary purpose is to investigate the corrosion behavior of crept AlSi10MnMg alloy (AA365) from a microstructural viewpoint.
- The research aims to establish the correlation between corrosion resistance and microstructures, specifically intermetallic compounds and micro-voids, in crept AA365 alloys under varying temperatures and stresses.
- Ultimately, the study seeks to contribute to improving the reliability and long-term structural performance of this alloy in automotive industry applications.
- Key Research Questions:
- How do different creep temperatures (373 K, 473 K, and 573 K) influence the microstructure of HPDC AA365 alloy, particularly the formation and distribution of intermetallic compounds and micro-voids?
- What is the relationship between the microstructure of crept AA365 alloy and its corrosion resistance in a corrosive environment?
- Does the density and type of intermetallic compounds, or the presence of micro-voids, have a more significant impact on the corrosion behavior of crept AA365 alloy?
- Research Hypotheses:
- The microstructure of crept AA365 alloy, specifically the density and characteristics of intermetallic compounds and micro-voids, will be significantly altered by the creep temperature.
- Variations in microstructure, induced by different creep temperatures, will directly influence the corrosion resistance of the AA365 alloy.
- Intermetallic compounds, rather than micro-voids, are hypothesized to be the primary factor influencing the corrosion behavior of crept AA365 alloy due to the potential for micro-galvanic corrosion.
4. Research Methodology:
- Research Design:
- The study employed an experimental research design to evaluate the corrosion behavior of crept HPDC AA365 alloy.
- Creep tests were conducted at different temperatures to induce microstructural changes, followed by electrochemical corrosion tests and detailed microstructural analysis.
- Data Collection Method:
- Creep Tests: Cylindrical creep specimens of HPDC AA365 alloy were subjected to creep tests at three different temperatures: 373 K (190 MPa), 473 K (120 MPa), and 573 K (80 MPa). These conditions were selected based on preliminary experiments to ensure the formation and re-dissolution of intermetallic compounds.
- Electrochemical Corrosion Tests: Cyclic potentiodynamic polarization (CPDP) and open circuit potential (OCP) measurements were performed using a computer-controlled GAMRY potentiostat and a three-electrode electrochemical cell system in a 3.5 wt% sodium chloride (NaCl) solution at room temperature.
- Microstructural Analysis:
- Scanning Electron Microscopy (SEM) and Energy-Dispersive X-ray Spectroscopy (EDS): FE-SEM (MIRA3, Tescan) with EDS was used to investigate the microstructure of crept and corroded samples and to identify the elemental composition of intermetallic phases.
- Electron Probe X-ray Microanalyzer (EPMA): EPMA (JXA-8230, JEOL) was utilized to analyze the chemical elements of intermetallic phases distributed in the Al matrix.
- Analysis Method:
- Electrochemical Data Analysis: Gamry Echem Analyst software was used to analyze CPDP curves. Tafel extrapolation method was employed to determine corrosion potential (Ecorr) and corrosion current density (Icorr).
- Microstructural Analysis: SEM and EPMA images were analyzed to characterize the morphology, distribution, and composition of intermetallic compounds and micro-voids. EDS analysis was used to identify the types of intermetallic phases.
- Correlation Analysis: The study correlated the microstructural features (density and type of intermetallic compounds, presence of micro-voids) with the electrochemical corrosion parameters (Ecorr and Icorr) to understand the relationship between microstructure and corrosion behavior.
- Research Subjects and Scope:
- The research focused on HPDC AA365 (Silafont 36) aluminum alloy supplied by Rio Tinto (USA).
- Three crept samples were investigated: AA365 alloy crept at 373 K, 473 K, and 573 K under specific applied stresses.
- Corrosion tests were conducted in a 3.5 wt% NaCl solution to simulate a corrosive environment.
- Microstructural analysis was performed on both crept and corroded samples to assess the changes induced by creep and corrosion processes.
5. Main Research Results:
- Key Research Results:
- Microstructure: Crept AA365 alloy at 473 K exhibited a significantly higher density of intermetallic phases compared to alloys crept at 373 K and 573 K (Figure 1b). The alloy crept at 573 K showed the lowest density of intermetallic precipitates (Figure 1c). EDS and EPMA analysis identified the brittle intermetallic compounds as π-Al12FeMg1.5Si5 and α-Al16(Mn,Fe)Si3 (Figure 1d, Figure 2).
- Corrosion Potential (Ecorr): The corrosion potentials were -687.0 mVSCE, -684.0 mVSCE, and -673.0 mVSCE for crept AA365 alloys at 373 K, 473 K, and 573 K, respectively (Table 2). The corrosion potential was highest (least negative) for the 573 K sample.
- Corrosion Current Density (Icorr): The corrosion current density was highest for the crept AA365 alloy at 473 K, with a value of 13.3 × 10-6 Acm-2, compared to 8.02 × 10-6 Acm-2 at 373 K and 0.51 × 10-6 Acm-2 at 573 K (Table 2).
- Corrosion Morphology: Localized corrosion was observed on the Al matrix in the vicinity of intermetallic compounds, indicating micro-galvanic corrosion (Figure 5). The alloy crept at 473 K showed the most severe corrosion.
- Statistical/Qualitative Analysis Results:
- Corrosion Potentials (Ecorr):
- 373 K: -687.0 mVSCE
- 473 K: -684.0 mVSCE
- 573 K: -673.0 mVSCE
- Corrosion Current Densities (Icorr):
- 373 K: 8.02 × 10-6 Acm-2
- 473 K: 13.3 × 10-6 Acm-2
- 573 K: 0.51 × 10-6 Acm-2
- Corrosion Potentials (Ecorr):
- Data Interpretation:
- The higher density of intermetallic compounds in the AA365 alloy crept at 473 K is attributed to the precipitation of non-equilibrium solute atoms from the supersaturated α-Al matrix during creep.
- The lower density of intermetallic compounds at 573 K is due to the re-dissolution of these phases back into the Al matrix at higher temperatures.
- The corrosion potential results indicate that the corrosion process is slowest for the 573 K sample and fastest for the 473 K sample.
- The significantly higher corrosion current density for the 473 K sample suggests that a large amount of intermetallic compounds promotes corrosion.
- The localized corrosion around intermetallic compounds confirms that micro-galvanic corrosion between the intermetallic phases (cathodic) and the Al matrix (anodic) is the primary corrosion mechanism.
- The study infers that the amount of intermetallic compounds is a more critical factor in corrosion than micro-voids in crept AA365 alloy.
- Figure Name List:
- Figure 1. SEM and EDS analysis of microstructure of crept HPDC AA365 alloys: (a) crept AA365 alloy at 373 K; (b) crept AA365 alloy at 473 K; (c) crept AA365 alloy at 573 K; (d) A higher magnification micrograph and EDS analysis of crept AA365 alloy at 473 K.
- Figure 2. EPMA micrograph and chemical element distribution maps of crept AA365 alloy at 373 K: Al, Mg, Fe, Si, Mn.
- Figure 3. Variation of the open circuit potential (OCP) of crept AA365 alloys in 3.5 wt.% NaCl during a hour of immersion: (a) crept AA365 alloy at 373 K; (b) crept AA365 alloy at 473 K; (c) crept AA365 alloy at 573 K.
- Figure 4. Cyclic potentiodynamic polarization (CPDP) curves of crept HPDC AA365 alloys in 3.5 wt.% NaCl.
- Figure 5. SEM and EDS analysis of corroded surface morphology of crept HPDC AA365 alloys of the attack after electrochemical testing in 3.5 wt.% NaCl: (a) crept HPDC AA365 alloy at 373 K; (b) crept HPDC AA365 alloy at 473 K; (c) crept HPDC AA365 alloy at 573 K; (d) BSE image of crept HPDC AA365 alloy at 473K along with the EDS elemental maps of Al, Si, Fe, Mg, and O.
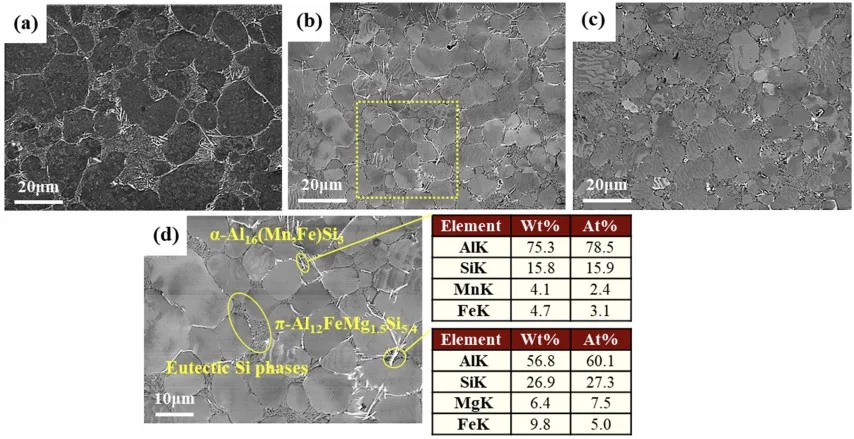
6. Conclusion and Discussion:
- Summary of Main Results:
- Creep temperature significantly influences the microstructure and corrosion behavior of HPDC AA365 alloy.
- Creep at 473 K resulted in the highest density of intermetallic compounds, leading to the highest corrosion current density (13.3 × 10-6 Acm-2) and thus the fastest corrosion rate.
- Creep at 573 K, due to the re-dissolution of intermetallic compounds, resulted in the lowest corrosion current density (0.51 × 10-6 Acm-2) and the slowest corrosion rate.
- Micro-galvanic corrosion, driven by the potential difference between intermetallic compounds and the Al matrix, is identified as the primary corrosion mechanism.
- The study concludes that the density of intermetallic compounds is a more dominant factor in controlling the corrosion behavior of crept AA365 alloy than micro-voids.
- Academic Significance of the Research:
- This research provides valuable insights into the complex interplay between creep-induced microstructural evolution and corrosion behavior in HPDC AA365 alloy.
- It enhances the fundamental understanding of corrosion mechanisms in aluminum alloys containing intermetallic compounds, particularly in the context of creep conditions.
- The findings contribute to the broader field of materials science and engineering by highlighting the importance of microstructural control in achieving desired corrosion resistance in structural alloys.
- Practical Implications:
- The study's results are crucial for the reliable application of HPDC AA365 alloy in automotive components operating at elevated temperatures and in corrosive environments.
- Understanding the detrimental effect of intermetallic compounds on corrosion resistance under creep conditions can guide the development of strategies to mitigate corrosion.
- Potential strategies include optimizing alloy composition, controlling solidification and cooling rates during HPDC, or employing post-casting heat treatments to manage the formation and distribution of intermetallic phases and thereby improve corrosion performance.
- Limitations of the Research:
- The study focused on a specific set of creep conditions and a single alloy composition.
- Further research is needed to generalize these findings to a broader range of creep conditions, stress levels, and variations in AA365 alloy composition or other similar aluminum alloys.
- The long-term corrosion behavior under creep conditions requires further investigation to fully assess the durability of the material in real-world applications.
7. Future Follow-up Research:
- Directions for Follow-up Research:
- Long-term corrosion studies under various creep conditions are recommended to comprehensively evaluate the material's durability.
- Investigating the influence of different types and distributions of intermetallic compounds on corrosion behavior would provide a more detailed understanding.
- Exploring methods to modify the microstructure, such as tailored heat treatments or minor alloy modifications, to control intermetallic phase formation and improve corrosion resistance is a promising avenue.
- Areas Requiring Further Exploration:
- The precise role of different types of intermetallic compounds (β-Al5SiFe, α-Al15(Mn,Fe)3Si2, Mg2Si, π-Al8Mg3FeSi6) in the micro-galvanic corrosion process needs further clarification.
- While the study suggests intermetallic compounds are more significant, the potential synergistic effect of micro-voids and intermetallic compounds on corrosion initiation and propagation warrants further exploration.
- Investigating the corrosion behavior in more complex and realistic corrosive environments, beyond 3.5 wt% NaCl solution, would enhance the practical relevance of the research.
8. References:
- Dias, M.; Oliveira, R.; Kakitani, R.; Cheung, N.; Henein, H.; Spinelli, J.E.; Garcia, A. Effects of solidification thermal parameters and Bi doping on silicon size, morphology and mechanical properties of Al-15wt.% Si-3.2wt.% Bi and Al-18wt.% Si-3.2wt.% Bi alloys. J. Mater. Res. Technol. 2020, 9, 3460–3470.
- Ahn, C.; Jo, I.; Ji, C.; Cho, S.; Mishra, B.; Lee, E. Creep behavior of high-pressure die-cast AlSi10MnMg aluminum alloy. Mater. Charact. 2020, 167, 110495.
- Jaglinski, T.; Lakes, R. Creep Behavior of Al-Si Die-Cast Alloys. J. Eng. Mater. Technol. 2004, 126, 378–383.
- Sadeghi, M.; Mahmoudi, J. Experimental and Theoretical Studies on the Effect of Die Temperature on the Quality of the Products in High-Pressure Die-Casting Process. Adv. Mater. Sci. Eng. 2012, 2012, 1–9.
- Avalle, M. Casting defects and fatigue strength of a die cast aluminium alloy: A comparison between standard specimens and production components. Int. J. Fatigue 2002, 24, 1-9.
- Zhang, B.; Cockcroft, S.L.; Maijer, D.M.; Zhu, J.D.; Phillion, A. Casting defects in low-pressure die-cast aluminum alloy wheels. JOM 2005, 57, 36-43.
- Qi, M.; Kang, Y.; Qiu, Q.; Tang, W.; Li, J.; Li, B. Microstructures, mechanical properties, and corrosion behavior of novel high-thermal-conductivity hypoeutectic Al-Si alloys prepared by rheological high pressure die-casting and high pressure die-casting. J. Alloy. Compd. 2018, 749, 487-502.
- Lee, E.; Mishra, B. Effect of Solidification Cooling Rate on Mechanical Properties and Microstructure of Al-Si-Mn-Mg Alloy. Mater. Trans. 2017, 58, 1624-1627.
- Lee, E.; Mishra, B. Effect of Cooling Rate on the Mechanical Properties of AA365 Aluminum Alloy Heat-Treated Under T4, T5, and T6 Conditions. Int. J. Met. 2017, 12, 449-456.
- Narayanan, L.A.; Samuel, F.H.; Gruzleski, J.E. Crystallization behavior of iron-containing intermetallic compounds in 319 aluminum alloy. Met. Mater. Trans. A 1994, 25, 1761-1773.
- Niklas, A.; Bakedano, A.; Orden, S.; da Silva, M.; Nogués, E.; Fernández-Calvo, A.I. Effect of Microstructure and Casting Defects on the Mechanical Properties of Secondary AlSi10MnMg(Fe) Test Parts Manufactured by Vacuum Assisted High Pressure Die Casting Technology; Elsevier Ltd.: Amsterdam, The Netherlands, 2015; Volume 2.
- Niklas, A.; Orden, S.; Bakedano, A.; Da Silva, M.; Nogués, E.; Fernández-Calvo, A. Effect of solution heat treatment on gas porosity and mechanical properties in a die cast step test part manufactured with a new AlSi10MnMg(Fe) secondary alloy. Mater. Sci. Eng. A 2016, 667, 376-382.
- Ahn, C.; Lee, E. [ICACE2019] Effect of cooling rate on the corrosion resistance and mechanical property of AlSi10MnMg alloy. J. Korean Soc. Mar. Eng. 2019, 43, 618-624.
- Shi, J.; Pries, H.; Stammen, E.; Dilger, K. Chemical pretreatment and adhesive bonding properties of high-pressure die cast aluminum alloy: AlSi10MnMg. Int. J. Adhes. Adhes. 2015, 61, 112-121.
- Jo, I.; Ahn, C.; Lee, E. High-temperature tensile deformation behavior and failure mechanisms of Al-10Si-Mn-Mg high-pressure die-cast alloy. J. Korean Soc. Mar. Eng. 2019, 43, 788-792.
- Ji, S.; Watson, D.; Fan, Z.; White, M. Development of a super ductile diecast Al-Mg-Si alloy. Mater. Sci. Eng. A 2012, 556, 824-833.
- Aballe, A.; Bethencourt, M.; Botana, F.J.; Marcos, M.; Osuna, R. Using EIS to study the electrochemical response of alloy AA5083 in solutions of NaCI. Werkstoffe und Korrosion 2001, 52, 185–192.
9. Copyright:
- This material is Seonghwan Park, Cheolmin Ahn and Eunkyung Lee's paper: Based on "Evaluation of Corrosion Behavior on Crept AlSi10MnMg (AA365) Alloy Produced by High-Pressure Die-Casting (HPDC)".
- Paper Source: https://doi.org/10.3390/app11136227
This material was summarized based on the above paper, and unauthorized use for commercial purposes is prohibited.
Copyright © 2025 CASTMAN. All rights reserved.