This introduction paper is based on the paper "UTILIZATION OF ECOLOGICAL FRIENDLY CORES FOR MAGNESIUM ALLOYS CASTINGS" published by "METAL 2013".

1. Overview:
- Title: UTILIZATION OF ECOLOGICAL FRIENDLY CORES FOR MAGNESIUM ALLOYS CASTINGS
- Author: Jaroslav BEŇOª, Petr LICHݪ, Eliška ADÁMKOVÁª, Michal CAGALAª, Petr JELÍNEKª, Marek BŘUSKAª, Karel GÁLª, Marcin MORYSᵇ
- Year of publication: 2013
- Journal/academic society of publication: METAL 2013 (15.- 17. 5. 2013, Brno, Czech Republic, EU)
- Keywords: inorganic salt cores, magnesium alloys, surface quality, solubility
2. Abstract:
The goal of this study is determination of utilization of cores based on inorganic materials without negative impacts on environment in gravity casting technology of Mg-alloys. The contribution includes analysis of preparation and treatment of these cores and their influence on quality, structure and properties of casting samples with regard to surface defects of castings. Experimental data obtained in this work can be also used in other casting technologies of Mg – alloys.
3. Introduction:
Currently, core mixtures based on organic resins (e.g., PUR COLD-BOX) are standard for pre-casting holes and cavities, offering rapid preparation, good shootability, high strength, and good collapsibility. However, their thermal destruction releases organic compounds, negatively impacting hygienic and environmental conditions. This has led to a "Renaissance" of inorganic binders, which do not have these negative impacts while offering comparable technological parameters.
One progressive technology involves using cores based on inorganic salts, particularly for non-ferrous alloys like Al-alloys. The use of salt cores dates back to the 1970s, with mass adoption in the 1990s for Diesel engine pistons via gravity and low-pressure casting. Manufacturing methods include high-pressure compaction of crystalline salts, casting or injecting salt melts, or using "classic" foundry techniques like shooting a salt matrix with a binder. Newer technologies like BEACH BOX and HYDROBOND utilize salt solutions or high-pressure compaction of NaCl.
Key advantages of salt cores include high primary strengths (comparable to PUR CB), dimensional accuracy, smooth casting surfaces, suitability for complex cavities difficult to clean mechanically, and good benchlife without moistening. They enable a closed ecological cycle where salt removed from the casting can be recrystallized and reused. Importantly, salts emit no VOCs during casting. Core properties can be optimized by adjusting preparation conditions (pressure, temperature) and composition (salt type, additives). While widely applicable for Al-alloys (gravity, low-pressure, research ongoing for high-pressure casting), this paper explores their use for Mg-alloys.
Magnesium alloys offer low density, high specific strength, and good castability but suffer from reduced strength at high temperatures, low creep resistance, and sometimes low corrosion resistance. Their high affinity for oxygen necessitates using inhibitors (like sulphur compounds, boric acid) during casting, especially in bentonite molding mixtures containing water. These inhibitors, while protective, can negatively affect the working environment and potentially deactivate the bentonite binder through complex chemical processes during casting, impacting mold properties like tensile strength and pH.
4. Summary of the study:
Background of the research topic:
The need for environmentally friendly casting processes drives interest in alternatives to organic binders for cores. Inorganic salt cores offer ecological benefits and are established for aluminum alloys. Magnesium alloy casting presents unique challenges due to high reactivity with oxygen, requiring inhibitors, which can interact negatively with traditional molding materials like bentonite.
Status of previous research:
Salt core technology has been developing since the 1970s, with established methods like high-pressure compaction and melt casting/injection used primarily for aluminum alloys. Research indicated high strength, good surface finish, and recyclability. The challenges of casting magnesium alloys, including oxidation and the effects of inhibitors on mold properties (especially bentonite binder deactivation by sulphur-based inhibitors), were known.
Purpose of the study:
This study aimed to investigate the feasibility of using inorganic salt cores for gravity casting of magnesium alloys (specifically AZ91) in bentonite-bound molding mixtures. The research focused on evaluating the technological properties of the salt cores (mechanical strength, dimensional accuracy, solubility, resulting casting surface quality) and assessing the influence of a sulphur-based inhibitor on the properties of the bentonite molding mixture.
Core study:
The core of the study involved preparing salt cores based on chemically pure KCl (N) and KCl with two different additives (A, B) using a high-pressure compacting method at two different forces (100 kN and 200 kN). These cores were then used in the gravity casting of AZ91 magnesium alloy into bentonite molds containing a sulphur-based inhibitor. Castings were made at two temperatures (700°C and 800°C). The study measured the bending strength and solubility of the salt cores, the surface roughness (Ra) of the resulting castings, and the mechanical properties (compression strength, splitting strength, wet tensile strength) and pH of the bentonite molding mixture before and after casting to assess thermal degradation and inhibitor effects.
5. Research Methodology
Research Design:
The study employed an experimental design comparing different salt core formulations (pure KCl vs. KCl with additives A or B) prepared under different compaction pressures (100 kN vs. 200 kN). These cores were tested in a practical application: gravity casting of AZ91 magnesium alloy into a standard bentonite molding mixture containing a sulphur-based inhibitor. The effects were evaluated by measuring core properties, casting quality, and changes in mold properties after thermal exposure at two different casting temperatures.
Data Collection and Analysis Methods:
- Salt Core Preparation: High-pressure compaction (100 kN, 200 kN) of pure KCl and KCl with 15% concentration of additives (A, B).
- Salt Core Properties:
- Bending strength measured using a multifunctional testing machine (LFV 100, Walter + Bai ag).
- Solubility tested by dissolving cores under a stream of water (22–27 °C, 2.5 l/min) and measuring time until core loss ("decoring" time).
- Casting: Gravity casting of AZ91 alloy into bentonite molds (91% silica sand, 4.5% bentonite, 5% sulphur inhibitor, water for 46±2% compactibility) at 700°C and 800°C (mold/metal ratio 9.3:1).
- Casting Quality:
- Mean arithmetic surface roughness (Ra) measured using Mitutoyo SurfTest SJ-301.
- Surface details evaluated using stereomicroscope (Olympus SZX12).
- Bentonite Molding Mixture Properties: Measured on raw mixture (STANDARD) and samples after casting (BMM700, BMM800).
- Compression and splitting strength (WADAP LRU-1).
- Wet tensile strength (+GF+ SPNF type).
- Cone Jolt Toughness (calculated ratio).
- Moisture content (drying at 105°C).
- pH (1:10 water suspension).
- Analysis: Comparison of properties based on core type (N, A, B), compaction force (1, 2), and mold condition (STANDARD, BMM700, BMM800).
Research Topics and Scope:
The research focused specifically on the application of high-pressure compacted KCl-based salt cores in the gravity casting of AZ91 magnesium alloy. The scope included:
- Evaluating the mechanical properties (bending strength) and solubility of the salt cores.
- Assessing the surface quality of Mg-alloy castings produced using these cores.
- Investigating the impact of a sulphur-based inhibitor on the properties (mechanical strength, pH, wet tensile strength) of the bentonite molding mixture, particularly after thermal exposure during casting.
- The study did not explore other Mg alloys, casting methods (e.g., pressure casting), or other types of inorganic cores or inhibitors.
6. Key Results:
Key Results:
- Salt Core Strength: Salt cores exhibited high primary bending strengths, approximately 2-3 times higher than commonly used PUR COLD-BOX cores. Strength increased with higher compacting pressure (200 kN vs 100 kN) and the addition of additives (A, B). Maximum strengths were achieved with additives A and B at 200 kN compaction force (KA2: 11.164 MPa, KB2: 11.410 MPa). (Table 1)
- Core Solubility/Removability: The salt cores were easily removable from the castings. The "decoring" time ranged from 1:00 min (K1B1) to 1:58 min (K2A1). No direct correlation was found between solubility time and salt composition, casting temperature, or compaction force.
- Casting Surface Quality: The surface quality of the test castings was generally high, with mean arithmetic roughness (Ra) ranging from 5.91 µm to 25.63 µm. Additives improved surface smoothness. The best surface finish (lowest Ra = 5.91 µm) was obtained with additive A and the maximum compaction force (200 kN), likely due to reduced core porosity and metal penetration. (Table 4)
- Molding Mixture Properties:
- The sulphur-based inhibitor significantly impacted the bentonite molding mixture properties, especially after thermal exposure.
- While standard mechanical strengths (compression, splitting) did not change significantly after casting (Table 3), the wet tensile strength and pH decreased considerably with increasing thermal exposure (casting temperature). (Fig. 1)
- The pH and wet tensile strength decreased from STANDARD (pH ~10, WTS 4.4 kPa) to BMM800 (pH ~9.6, WTS 3.3 kPa), indicating binder deactivation due to the acid nature of the inhibitor and thermal effects. (Fig. 1)
- Process Consideration: The combination of salt cores and magnesium alloys necessitates efficient degassing/venting of the mold cavity during casting due to intensive gas evolution, which can otherwise lead to surface defects.
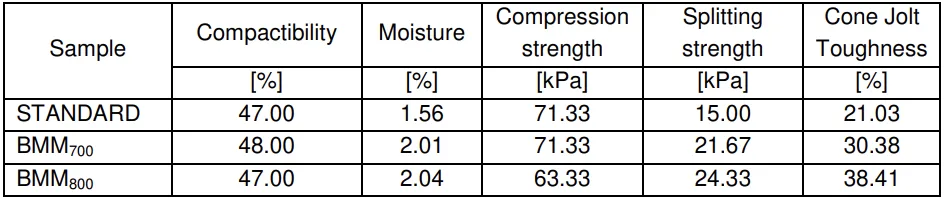
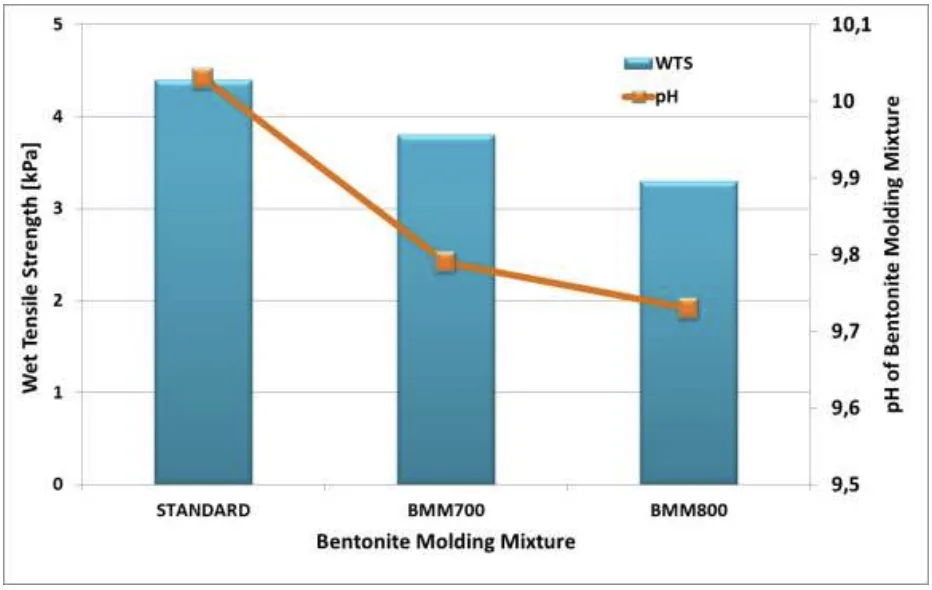

Figure Name List:
- Table 1 Bending strength of tested salt cores
- Table 3 Main technological parameters of bentonite molding mixtures
- Fig. 1 Wet tensile strength and pH of bentonite molding mixture samples
- Table 4 Surface quality of testing castings
7. Conclusion:
This study confirmed the potential of using inorganic salt cores for casting magnesium alloys, offering high primary strength (2-3 times higher than PUR COLD-BOX mixtures), easy removability (decoring times up to 2 minutes), and sufficient casting surface quality.
However, the research also highlighted a significant negative interaction when using these cores in conjunction with bentonite molding mixtures containing a sulphur-based inhibitor, which is common practice for Mg alloys. The presence of the acid inhibitor, especially after thermal exposure during casting, leads to a decrease in the tensile strength in the water condensation zone and a reduction in the mixture's pH. This degradation of mold properties can lead to casting defects (e.g., rat tails) and complicates the optimal control of the molding mixture.
Therefore, while salt cores are feasible for Mg alloys, careful consideration must be given to the chemical interactions within the mold system (core, mold binder, inhibitor). Ensuring sufficient exhausting of gases from the mold cavity during pouring and cooling is critical to achieving high casting quality due to the chemical nature of the materials involved.
8. References:
- [1] JELÍNEK, P. Anorganická pojiva si razí cestu do sléváren. Slévárenství, 2012, roč. 60, č. 3-4, s. 66-70
- [2] KANEKO, Y., MORITA, A. New developments in water soluble salt cores for die casting. In Transaction of the 6th SDCE International die casting congress, 1970, 16 – 19 November, Cleveland, Ohio, No. 91. NOVÁK, J. Dějiny technického pokroku. 1. vyd. Praha: Akademia, 1998. 330 s.
- [3] LOPER, C. R.; aj.: The Use of Salt In Foundry Cores. AFS Transactions, 1985, 85 – 82,545 – 560.
- [4] ANDERKO, K.; WITTSTOCK, P.: Process of casting metals by use of water-soluble salt cores. United States Patent Office, December 5, 1967
- [5] STINGL, P.; SCHILLER, G.: Gichte und rückstandsfreie Entkernung - Salzkerne für den Aluminiumguss. Giesserei-Erfahrungsaustausch, 2009, č. 6, s. 4 – 8)
- [6] HÄNSEL, H. Ein anorganisches bindersystem der innovativen Art. Giesserei, 2002, 89 2 s.74-76
- [7] FALLER, M. – MÖSSNER, A. Die Zukunft wartert schon heute. Giesserei, 2009, 96 9 72-74
- [8] DOBOSZ, S. et.al. Development tendencies of moulding and core sands. China Foundry, roč. 8, č. 4, s. 438-446.
- [9] JELÍNEK, P., et. al.: Development of Technology of salt cores manufacture. Slévárenství, 2013, 61, 1 – 2, s.28-31
- [10] BOUCNÍK, P., et. al.: Použití hořčíkových slitin ve slévárenství. In Proceeding of 5. Medzinárodna vedecká konferencia CO-MAT-TECH, Trnava, 14.10. 15.10.1997
- [11] ČÍŽEK, L. et.al. Vliv obsahu hliníku na vlastnosti hořčíkových slitin při odlévání do bentonitových a furanových směsí. In Metal 2005: 14. mez. metal. konference: 24. - 26. 5. 2005. Hradec nad Moravicí, Česká Republika Ostrava: TANGER: Květen, 2005, s. 82-89. ISBN 80-85988-48-8.
- [12] MORDIKE, B.L., EBERT, T. Magnesium Properties – applications - potential. Materials Science and Engineering, 2001, A302, 37-45
- [13] JUŘIČKA, I. Studium interakce forma-kov při výrobě odlitků z Mg – slitin. Disertační práce, VŠB – TU Ostrava, 1992
- [14] LAFAY, V.S. Succesfully bonded bentonite sands: What have we learned in the last 25 years. AFS Transactions, 2011, paper 11-001, s. 349-360
9. Copyright:
- This material is a paper by "Jaroslav BEŇO, Petr LICHÝ, Eliška ADÁMKOVÁ, Michal CAGALA, Petr JELÍNEK, Marek BŘUSKA, Karel GÁL, Marcin MORYS". Based on "UTILIZATION OF ECOLOGICAL FRIENDLY CORES FOR MAGNESIUM ALLOYS CASTINGS".
- Source of the paper: [DOI URL Not Available in Provided Document]
This material is summarized based on the above paper, and unauthorized use for commercial purposes is prohibited.
Copyright © 2025 CASTMAN. All rights reserved.