This article introduces the paper "THERMOMECHANICAL MECHANISMS THAT CAUSE ADHESION OF ALUMINUM HIGH PRESSURE DIE CASTINGS TO THE DIE".
Overview:
- Title: THERMOMECHANICAL MECHANISMS THAT CAUSE ADHESION OF ALUMINUM HIGH PRESSURE DIE CASTINGS TO THE DIE
- Author: Alex Monroe
- Publication Year: 2021
- Publishing Journal/Academic Society: Michigan Technological University, Digital Commons @ Michigan Tech, Dissertations, Master's Theses and Master's Reports
- Keywords: HPDC, adhesion, sticking, soldering, thermomechanical, friction, intermetallic
Research Background:
- Social/Academic Context of the Research Topic: High Pressure Die Casting (HPDC) is a prevalent casting method for intricate non-ferrous components, particularly aluminum parts in automotive applications. A significant challenge in HPDC is adhesion, where cast material adheres to the die, leading to defects. While lubricants are employed to mitigate adhesion, they introduce drawbacks such as casting porosity, blisters, reduced die lifespan, and increased machine wear.
- Limitations of Existing Research: The prevailing theory attributes adhesion to kinetically controlled intermetallic phase formation between aluminum and steel die. However, coating die surfaces with non-reactive materials, based on this theory, proves only partially effective in industrial and laboratory settings. Furthermore, kinetics-based models fail to pinpoint areas of severe adhesion, indicating the need for additional explanatory mechanisms.
- Necessity of the Research: To enhance the prediction and reduction of adhesion defects in HPDC, it is crucial to explore and understand additional mechanisms beyond the kinetically controlled intermetallic formation theory. This research aims to investigate friction as a significant, yet often overlooked, mechanism contributing to sticking and soldering in HPDC.
Research Purpose and Research Questions:
- Research Purpose: This research aims to investigate the thermomechanical mechanisms, specifically focusing on friction, that contribute to adhesion in aluminum High Pressure Die Casting (HPDC). The study challenges the conventional understanding of adhesion being solely driven by kinetically controlled intermetallic phase formation and proposes a friction-based mechanism.
- Key Research Questions:
- To what extent does friction, arising from thermomechanical interference between the casting and die, contribute to sticking and soldering in HPDC?
- Can friction-based models more accurately predict adhesion phenomena in HPDC compared to models based solely on kinetics of intermetallic phase formation?
- Research Hypotheses:
- If soldering is primarily a result of kinetically driven phase formation, then laboratory diffusion couple experiments should effectively replicate and predict industrial soldering observations.
- If friction is a significant factor, increasing the draft angle of a die core should lead to a reduction in ejection force that is proportionally greater than the decrease in contact area, due to the reduced frictional force component in the ejection direction.
- If soldering is influenced by friction and material strength, increasing the ejection temperature should increase the likelihood of soldering because the alloy's strength decreases, making it less resistant to frictional shear stress.
Research Methodology
- Research Design: The research employed a mixed-methods approach, combining experimental investigations with computational modeling to analyze the mechanisms of adhesion in HPDC. This included:
- Experimental studies involving room temperature and hot ejection tests to measure ejection forces and observe soldering phenomena.
- One-dimensional (1D) and three-dimensional (3D) numerical modeling to simulate solidification, cooling, thermal stresses, and friction at the casting-die interface.
- Data Collection Method: Data was collected through:
- Measurement of ejection forces using a Tinius and Olsen tensile machine with an Omegadyne load cell for room temperature ejection tests.
- Recording temperatures using k-type thermocouples and measuring ejection force with a load cell for hot ejection tests. Displacement was measured with an LVDT.
- Simulation data generated from MAGMASOFT for 3D modeling of industrial castings and MATLAB for 1D thermomechanical modeling.
- Analysis Method: The collected data was analyzed using:
- Application of Coulomb and Tresca friction models to predict ejection forces and soldering likelihood.
- Statistical analysis, including paired Student's T-tests, to compare the effects of different alloys on ejection force.
- Fitting experimental data to friction models using Excel Solver to determine parameters like interfacial strength, contact pressure, and coefficient of friction.
- Comparison of model predictions with experimental observations and industrial case studies to validate the friction-based approach.
- Research Subjects and Scope: The research focused on:
- Cylindrical die (core) geometry within a tubular casting to simplify modeling and experimentation, assuming axial symmetry.
- Aluminum alloys: Primarily A380 and A356, with additional simulations for A362, A365, and A518 to assess alloy composition effects. Chemical compositions are detailed in Table 4.
- Die materials: H13 steel, H13 High K steel, and Inconel were considered in simulations (properties in Table 5).
- Variables investigated: Draft angle (0.5° to 25°), ejection temperature (room temperature to 555°C), alloy composition, die material, casting thickness, and core diameter.
Main Research Results:
- Key Research Results:
- Friction as Primary Mechanism: Room temperature ejection tests demonstrated that ejection force behaves as an interference fit, well-predicted by a friction model without needing an adhesion term. "The best fit occurs when the interfacial strength is set to zero, contact pressure is 5.9 MPa, and the coefficient of friction is 0.59. The best fit was plotted as the “Friction Model" line (Figure 20), and this approach was also plotted assuming adhesion from interfacial strength alone. This is the dashed “Adhesion Model” line, and it is a poor fit of the data."
- Draft Angle Effect: Increasing draft angle significantly reduced ejection force, consistent with friction model predictions. "A plot of all ejection force measurements showing a trend of decreasing ejection force with increasing draft angle but little effect of alloy" is shown in Figure 18.
- Hot Ejection and Soldering: Hot ejection tests confirmed that soldering occurs at elevated temperatures. "The hypothesis was partially confirmed by the hot ejection test, in that within a single casting cycle aluminum would adhere to the core (Figure 30)."
- 3D Simulation Validation: 3D simulations using the Tresca friction factor successfully predicted soldering locations in industrial die casting examples, aligning with observed soldering patterns in production tooling. "Locations of soldering and relative severity are well predicted using this friction-based prediction." (Figure 35).
- Coatings Reduce Friction: AlCrN coatings reduced the coefficient of friction, suggesting that coatings mitigate sticking primarily by reducing friction. "Coatings reduced the coefficient of friction by 18% from 0.59 to 0.5. This suggests that the primary reason coatings reduce sticking is by reducing friction."
- Statistical/Qualitative Analysis Results:
- Alloy Insignificance at Room Temperature: Paired Student's T-test indicated no significant difference in ejection force between alloys 362 and 380 at room temperature. "A paired Student's T test was performed on the data from the two alloys, and the t-statistic was calculated as 0.94 for the paired test. This is less than the critical value of 1.71 assuming 95% level of significance. This implies that the 362 and 380 ejection force are not different…"
- Friction Model Fit: The friction model provided a better fit to the experimental data compared to an adhesion-only model. "The best fit is achieved with the “Friction Model” and is not improved by adding the adhesion term. The adhesion only model does not match the data." (Figure 20).
- Data Interpretation: The results strongly support the hypothesis that friction, arising from thermomechanical interference, is a dominant mechanism causing sticking and soldering in HPDC. The experimental and simulation findings indicate that adhesion in HPDC is better explained by friction models than by solely considering kinetics-based intermetallic formation. Contact pressure and ejection temperature are identified as critical factors influencing adhesion.
- Figure Name List:
- Figure 1: The moving half of a typical die casting die [2].
- Figure 2: (a) An example of sticking. Both images courtesy of Mercury Marine. (b) An example of soldering on a die insert.
- Figure 3: Temperature dependence of the proposed dimensionless ejection force, Fej * and ejection shear stress, Tr.
- Figure 4: (a) Conceptual plot of the Coulomb model where the ejection stress is low relative to the part strength at low temperatures, and the part sticks to the die. (b) Conceptual plot at high temperature where all ejection stresses are large relative to the part strength, and the part fails. Figure adapted from Widerøe and Welo [15].
- Figure 5: Stages of soldering as proposed by Chu et al. in 1993 [9].
- Figure 6: Soldering that occurs on a die that has a non-reactive coating identified by Wang et al. [8]. Lubricant spray was reduced, but the soldering (red circles) and sticking still occur (Image courtesy of Mercury Marine).
- Figure 7: Conceptual casting for developing a thermomechanical theory of soldering and sticking. Radii smaller than ri are the die steel core, and radii greater than ro are the die steel mold.
- Figure 8: Schematic of the common thermodynamics and kinetics-based theory of soldering and sticking.
- Figure 9: The predicted time to grow a 0.1 mm thick intermetallic layer [78]–[80], [83], [84]. A single activation energy of 190 kJ/mol provides good agreement with measured reaction rates both above and below the melting temperature of 660°C
- Figure 10: (a) Illustration of a typical aluminum iron diffusion couple [78]. (b) One dimensional intermetallic growth rate when the liquid is either initially pure or saturated with iron [85].
- Figure 11: (a) Static steel cylinder (12.7 mm diameter) dip tests in various aluminum alloys showed that pure aluminum dissolves steel more slowly than commercial casting alloys [89]. (b) Static steel cylinder (12.7 mm diameter) dip tests showed that the structural alloy Silafont 36 (A367) dissolves steel slower than the more common A390 diecasting alloy [88].
- Figure 12: Illustration of joints between steel and aluminum under the shear of the ejection force, Fe without (a,b) and with an intermetallic layer (c,d). When the bond strength is low a clean separation at the aluminum/steel interface is normally observed (a) Casting failure may occur due to the low strength of aluminum at elevated temperature. (b). Roll bonded, brazed, and friction stir welded joints typically fracture within the intermetallic layer when it is present (c), while HPDC conditions often contain an intermetallic layer with the fracture in die casting (d).
- Figure 13: A simplified schematic based on Figure 3 where only the sticking factor is considered.
- Figure 14: Conceptual model of the casting/die interface where Fej is the ejection force and Ac is the total contact area. tAl, tej, and tFe are the shear strength of the casting, interface, and die, respectively.
- Figure 15: Different factors that affect the local contact area in the die casting process.
- Figure 16: Schematic of room temperature ejection mold.
- Figure 17: Image of the fixture for measuring the ejection force. The top and bottom of the fixture could pivot by a few degrees to correct for misalignment.
- Figure 18: A plot of all ejection force measurements showing a trend of decreasing ejection force with increasing draft angle but little effect of alloy.
- Figure 19: Schematic of core denoting the contact area used to fit (eq. 6) to the experimental data (Figure 18).
- Figure 20: The best fit is achieved with the “Friction Model” and is not improved by adding the adhesion term. The adhesion only model does not match the data.
- Figure 21: Image of all 7 cores after over 10 casting cycles showing no buildup from the cast aluminum.
- Figure 22: Comparison of AlCrN coated cores showing no difference between the smooth (Diamond Polished) and rough (220 Grit Stoned) surface preparation.
- Figure 23: Friction model fit to the AlCrN coated cores versus the uncoated cores. The 95% confidence interval based on a minimum of 6 experiments for each data point is shown.
- Figure 24: HPDC soldering occurs when the Tresca friction factor is larger than a critical value, and it decreases with lower ejection temperatures, (subset of Figure 3).
- Figure 25: The L-H relationship as proposed in eqs. 9 through 12. UTS was calculated assuming the onset of necking where N(T)/1 – М(Т).
- Figure 26: Bulk stress state prior to ejection due to the thermal interference between the casting and core.
- Figure 27: Thermal strain compared to the yield strain as calculated using an 0.002 offset of elastic modulus in eq. 18.
- Figure 28: Predicted soldering likelihood of a cylindrical casting (eq. 21) based on the alloy described in eq. 9 versus the ejection temperature.
- Figure 29: General assembly view of the hot ejection test apparatus the casting, core, sand mold, and support plate.
- Figure 30: (a) Example of experimental rig prepared for casting. (b) Incipient soldering clearly shown on the case where ejection occurred at 550°C.
- Figure 31: Casting surface for hot ejection test showing surface shrinkage (casting) and aluminum buildup (core).
- Figure 32: Rectangular example showing that the contact pressure is proportional to the thickness of the casting relative to the bearing area, Ac, on the core.
- Figure 33: Example die simulated in MAGMASOFT to test the validity of the Tresca friction factor to predict HPDC soldering.
- Figure 34: Second industrial HPDC example for comparison of the Tresca friction factor with HPDC soldering.
- Figure 35: Comparison of the contact pressure scaled by UTS in MAGMA (a) and (c) with the production die casting die at the end of a production run (b) and (d).
- Figure 36: Predicted soldering friction factor (right hand axis) vs simulation time. The temperatures at the same locations are plotted on the left-hand axis. Both locations exhibit increasing then decreasing soldering tendency related to the local temperature of the casting.
- Figure 37: Strength vs test temperature of typical wrought aluminum alloys in the as cast state [97]. UTS was assumed to occur at the onset of necking.
- Figure 38: The limits of ejection to avoid sticking and soldering. This is the axis-symmetric case of the general conceptual model proposed in the introduction (Figure 3).
- Figure 39: Density (a) and enthalpy (b) of the alloys in Table 4 as predicted by ThermoCalc equilibrium calculations [75]. Cumulative heat release (c) during solidification and cooling of the alloys. (d) Linearized thermal conductivity vs temperature for both alloys based on available literature measurements [100], [101].
- Figure 40: (a) Average casting temperature for a 12 mm tube casting with a 100 mm inner diameter. (b) Modeled contact pressure vs ejection time.
- Figure 41: A schematic that illustrates the limits on acceptable ejection times.
- Figure 42: Predicted average casting temperature (a) and ejection force (b) of the alloys from Table 4.
- Figure 43: Main effects plots for prediction of the range of possible ejection times for a core in a tubular casting of various, thickness, casting alloy, core diameter, initial die temperature.
- Figure 44: The main effect if die materials for the full factorial simulation. Different die materials are discerned by their thermal conductivity in Table 5.
- Figure 45: Enthalpy release of alloys in on a per volume basis during solidification and cooling.
- Figure 46: Soldering severity ranking from the NADCA Product Design Standards indicating A518 is castable but it has the worst die filling capacity and anti-solder capability [103].
- Figure 47: Cumulative heat release during solidification for A380 with 0.2 wt% iron and 0.2 wt% manganese compared to the same alloy with 1 wt% iron and 0.3 wt% manganese. There is a 3% reduction in heat released when iron and manganese are lowered.
Conclusion and Discussion:
- Summary of Main Results: This research concludes that friction, arising from thermomechanical interference at the casting-die interface, is a primary mechanism responsible for aluminum adhesion in HPDC, encompassing both sticking and soldering phenomena. Room temperature ejection tests demonstrated friction-like behavior without evidence of inherent adhesion forces. Hot ejection tests and 3D simulations further validated the role of friction, showing that soldering is linked to high Tresca friction factors. Minimizing contact pressure is identified as the most effective strategy to reduce adhesion.
- Academic Significance of the Research: This study provides a significant shift in understanding adhesion in HPDC by highlighting the importance of friction, a mechanism often overlooked in favor of kinetics-based intermetallic formation theories. The research introduces a novel thermomechanical framework for predicting and mitigating adhesion, offering a more comprehensive explanation of observed phenomena.
- Practical Implications: The research provides an optimum design methodology for HPDC processes focused on maximizing casting ejection temperature and minimizing contact pressure to reduce adhesion. The application of 3D simulation tools, incorporating the Tresca friction factor, is recommended for predicting soldering locations and optimizing die and process designs. Alloy selection and process parameter adjustments can be guided by the friction model to minimize adhesion and enhance casting quality.
- Limitations of the Research: Hot ejection tests encountered challenges in achieving uniform contact, deviating from the ideal axis-symmetric case assumed in models. The range of temperatures tested in hot ejection experiments exhibited limited variation in strain hardening coefficient, potentially affecting the sensitivity of soldering prediction in those specific tests.
![Figure 1: The moving half of a typical die casting die [2].](https://castman.co.kr/wp-content/uploads/image-145-1024x726.webp)
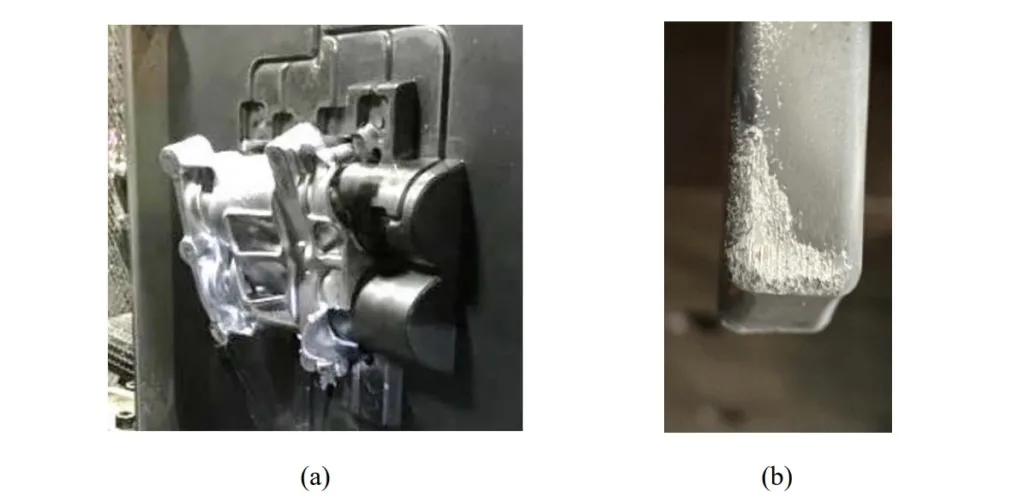
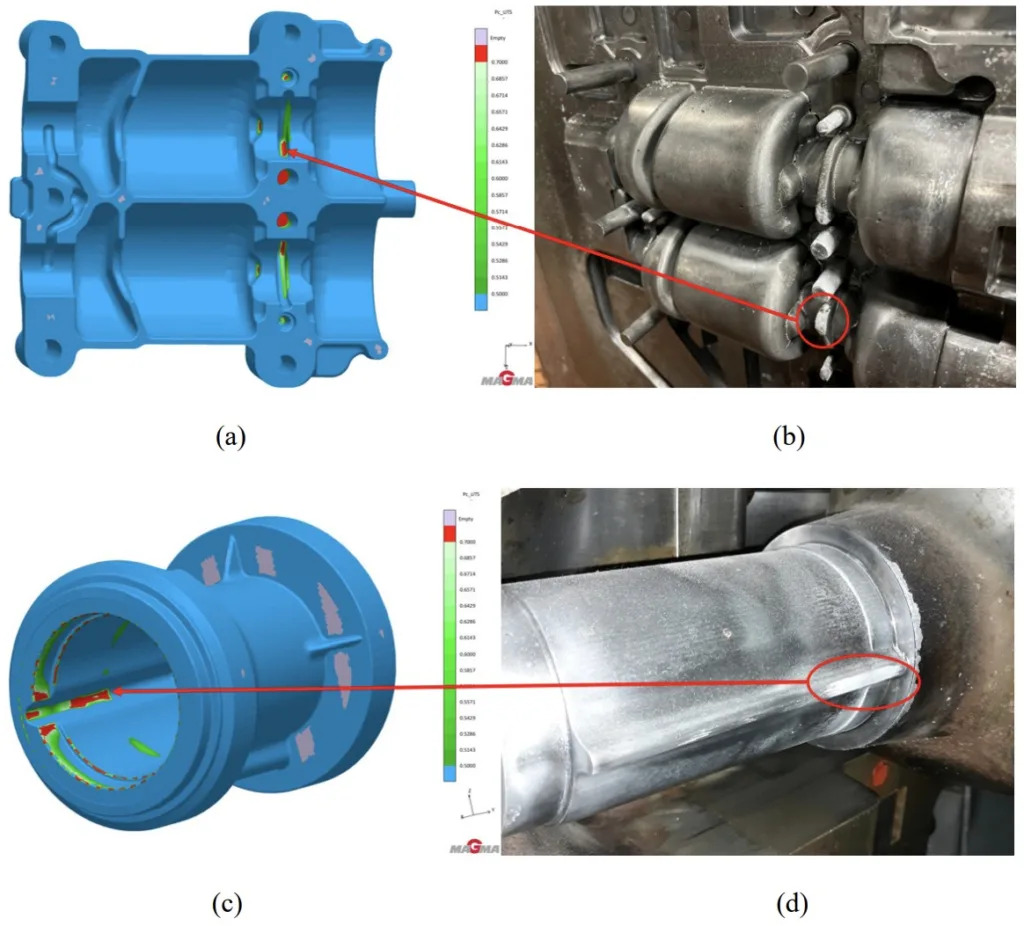
Future Follow-up Research:
- Directions for Follow-up Research: Future research should investigate the interaction between die lubricants and coatings, and the surface finish of die cores to further refine adhesion control strategies. Further study into the high temperature mechanical properties of Al-Si alloys, particularly with varying iron and manganese content, is warranted to enhance material-based solutions for adhesion reduction. Continued development and testing of die coatings aimed at reducing friction are also crucial.
- Areas Requiring Further Exploration: Exploring alloy optimization strategies that focus on enhancing high-temperature strength to resist frictional shear stresses is an area for further investigation. The potential of utilizing low thermal conductivity die materials to manage heat transfer and reduce sticking tendencies in difficult-to-cast alloys warrants further exploration.
References:
- [1] S. P. Udvardy, “2019 State of the Die Casting Industry,” Die Casting Engineer, no. January, p. 6, 2019.
- [2] 2018 Product Specification Standards for Die Castings, 2018th ed. North American Die Casting Association.
- [3] R. J. Donahue and G. K. Sigworth, “Die Casting Alloys that will Allow the Die Caster to Compete with Alloys A356, A357, 358 and 359 in PM Applications,” p. 17.
- [4] Aoyama, Shunzo, Akase, Makota, Sakamoto, Katsumi, and Umemura, Teruyoshi, “Die Lubricant Deposit and Its Effect on Ejection in Die Casting,” vol. T91-112.
- [5] R. A. Miller, “Fluidity from a Heat Transfer Perspective,” in NADCA Transactions, Ohio, Sep. 2016, vol. T16-081. Accessed: Apr. 10, 2018. [Online]. Available: https://www.diecasting.org/archive/transactions/T16-081.pdf
- [6] R. N. Lumley, I. J. Polmear, H. Groot, and J. Ferrier, “Thermal characteristics of heat-treated aluminum high-pressure die-castings,” Scr. Mater., vol. 58, no. 11, pp. 1006–1009, Jun. 2008, doi: 10.1016/j.scriptamat.2008.01.031.
- [7] D. Blondheim, Jr. and A. Monroe, “Macro Porosity Formation - A Study in High Pressure Die Casting,” Int. J. Met., 2021, doi: https://doi.org/10.1007/s40962-021-00602-x.
- [8] B. Wang, G. R. Bourne, A. L. Korenyi-Both, S. P. Midson, and M. J. Kaufman, “An investigation of the use of PVD die coatings to minimize or eliminate lubrication during high pressure die casting,” in North American Die Casting Congress, 2016, vol. T16-061.
- [9] Chu, Yeou-Li, Cheng, Patrick, and Shivpuri, Rajiv, “Soldering Phenomenon in Aluminum Die Casting: Possible Causes and Cures,” in North American Die Casting Congress, Cleveland, OH, Oct. 1993, pp. 361–372.
- [10] Tosa, Hiroki and Urakami, Akio, “Factors Influencing Die Casting Ejection," in North American Die Casting Congress, Chicago, IL, 1972, vol. T72-041.
- [11] B. Wang, G. R. Bourne, A. L. Korenyi-Both, A. K. Monroe, S. P. Midson, and M. J. Kaufman, “Method to evaluate the adhesion behavior of aluminum-based alloys on various materials and coatings for lube-free die casting,” J. Mater. Process. Technol., vol. 237, pp. 386–393, 2016, doi: 10.1016/j.jmatprotec.2016.06.031.
- [12] S.-B. Kim, Y.-H. Yim, and D.-H. Roh, “Prediction of Die Soldering in Die Casting by a Numerical Algorithm based on the Combination of Thermal and Fluid Factors Verified with Experimental Results,” in Die Casting Congress and Tabletop, Cleveland, OH, 2019, p. 9.
- [13] K. Domkin, J. H. Hattel, and J. Thorborg, “Modeling of high temperature- and diffusion-controlled die soldering in aluminum high pressure die casting,” J. Mater. Process. Technol., vol. 209, no. 8, pp. 4051–4061, 2009, doi: 10.1016/j.jmatprotec.2008.09.031.
- [14] D. Tabor, “Friction - the present state of our understanding,” J. Lubr. Technol., vol. 103, no. 2, pp. 169–179, Apr. 1981.
- [15] F. Widerøe and T. Welo, “Conditions for Sticking Friction between Aluminium Alloy AA6060 and Tool Steel in Hot Forming,” Key Eng. Mater., vol. 491, pp. 121-128, Sep. 2011, doi: 10.4028/www.scientific.net/KEM.491.121.
- [16] H. Wang and C. A. Loong, “Experimental Studies on Ejection FORCES of a die cast Aluminum Part,” in North American Die Casting Congress, Cleveland, OH, 1999, vol. T99-052.
- [17] M. J. Roy, D. M. Maijer, and L. Dancoine, “Constitutive behavior of as-cast A356," Mater. Sci. Eng. A, vol. 548, pp. 195–205, Jun. 2012, doi: 10.1016/j.msea.2012.03.106.
- [18] Shankar, Samantha and Apelian, Diran, “Die Soldering: Mechanism of the interface reaction between molten aluminum alloy and tool steel,” vol. 33B, no. June 2002, pp. 465–476, doi: 10.1007/s11663-002-0057-7.
- [19] ASM Handbook: Welding, Brazing, and Soldering, vol. 6. ASM International (R), Materials Park, Ohio, USA, 1993.
- [20] A. Long, D. Thornhill, C. Armstrong, and D. Watson, “Predicting die life from die temperature for high pressure dies casting aluminium alloy,” Appl. Therm. Eng., vol. 44, pp. 100–107, Nov. 2012, doi: 10.1016/j.applthermaleng.2012.03.045.
- [21] A. Long, D. Thornhill, C. Armstrong, and D. Watson, “Determination of the heat transfer coefficient at the metal–die interface for high pressure die cast AlSi9Cu3Fe," Appl. Therm. Eng., vol. 31, no. 17–18, pp. 3996–4006, Dec. 2011, doi: 10.1016/j.applthermaleng.2011.07.052.
- [22] Z. W. Chen, “Formation and progression of die soldering during high pressure die casting,” Mater. Sci. Eng. A, vol. 397, no. 1–2, pp. 356–369, 2005, doi: 10.1016/j.msea.2005.02.057.
- [23] Y. Zhu, D. Schwam, J. F. Wallace, and S. Birceanu, “Evaluation of soldering, washout and thermal fatigue resistance of advanced metal materials for aluminum die-casting dies,” Mater. Sci. Eng. A, vol. 379, no. 1–2, pp. 420–431, 2004, doi: 10.1016/j.msea.2004.03.020.
- [24] Chu, Yeou-Li, Balasubramaniam, Srikanth, Rajan, Rajendra, and Shivpuri, Rajiv, "A Study of the Cast Alloy-Die Surface Interactions in Aluminum Die Casting,” in North American Die Casting Congress, Minneapolis, MN, 1997, vol. T97-075. [Online]. Available: https://diecasting.org/wcm/Technology/Technical_Archive/wcm/Technology/Technical_Archive.aspx?hkey=62f825ba-424c-41c3-b10f-3b860771ffa4
- [25] S. Gulizia, M. Z. Jahedi, and E. D. Doyle, “Performance evaluation of PVD coatings for high pressure die casting,” Surf. Coat. Technol., vol. 140, no. 3, pp. 200-205, Jun. 2001, doi: 10.1016/S0257-8972(01)01037-4.
- [26] Hairy, P. and Richard, M., “Reduction of Sticking in Pressure Die Casting by Surface Treatment,” in North American Die Casting Congress, 1997, vol. T97-102.
- [27] K. Bobzin, T. Brögelmann, U. Hartmann, and N. C. Kruppe, "Analysis of CrN/AlN/Al2O3 and two industrially used coatings deposited on die casting cores after application in an aluminum die casting machine,” Surf. Coat. Technol., vol. 308, pp. 374-382, Dec. 2016, doi: 10.1016/j.surfcoat.2016.09.040.
- [28] Q. Han and S. Viswanathan, “Analysis of the Mechanism of Die Soldering in Aluminum Die Casting,” Metall. Mater. Trans. A, vol. 34A, no. January, pp. 139–146, 2003.
- [29] Shankar, Sumanth and Apelian, Diran, “Mechanism and Preventive Measures for Die Soldering during Al Casting in a Ferrous Mold,” JOM, vol. 54, no. August 2002, pp. 47–54, doi: 10.1007/BF02711867.
- [30] C. Mitterer, F. Holler, F. Üstel, and D. Heim, "Application of hard coatings in aluminium die casting – soldering, erosion and thermal fatigue behaviour,” Surf. Coat. Technol., vol. 125, no. 1–3, pp. 233–239, Mar. 2000, doi: 10.1016/S0257-8972(99)00557-5.
- [31] Norstrom, Lars-Ake, Klarenfjord, Bengt, and Svensson, Maths, “General Aspects on 'Washout' Mechanisms in Aluminum Die Casting Dies," 1993, vol. T93-075–1.
- [32] M. Yu, R. Shivpuri, and R. A. Rapp, “Effects of Molten Aluminum on H13 Dies and Coatings,” J. Mater. Eng. Perform., vol. 4, no. 2, pp. 175–181, Apr. 1995.
- [33] R. J. Barnhurst, D. Argo, and W. Walkington, “NADCA Sponsored Research: The Causes of Soldering in Zinc Die Casting,” in Die Casting Congress, 1997, vol. T97-033.
- [34] M. Stern, “PROGRESS_OF_DIE-CASTING_INDUSTRY,” in Transactions of the American Foundrymen's Association, 1930, vol. 37, pp. 723–733.
- [35] W. Bonsack, “Trends in Aluminum Casting Alloys,” in Transactions of the American Foundrymen's Association, 1950, vol. 76, pp. 69–75.
- [36] D. L. Colwell and E. Trela, “New Aluminum Die Casting Alloys,” in Transactions of the American Foundrymen's Association, 1954, vol. 93, pp. 359–364.
- [37] D. L. Colwell and O. Tichy, “Machinability of Aluminum Die Castings,” in Transactions of the American Foundrymen's Association, 1956, vol. 92, pp. 236–241.
- [38] S. U. Siena, “Die Casting Aluminum Alloys by the Cold Chamber Process,” 1944.
- [39] W. Bonsack, “Iron-The Problematic Factor in Quality Of Aluminum Alloy Die Castings," in Transactions of the American Foundrymen's Association, 1961, vol. 114, pp. 712-720.
- [40] Holz, Earl K., “Trouble Shooting Aluminum Die Casting Quality Problems,” in 7th SDCE International Die Casting Congress, Chicago, IL, 1972, vol. T72-043.
- [41] Kajoch, Wladyslaw and Fajkiel, Alexander, “Testing the Soldering Tendencies of Aluminum Die Casting Alloy,” in North American Die Casting Congress, Detroit, MI, Oct. 1991, vol. T91-034, pp. 67–74.
- [42] W. Jonsson, “THE EFFECT OF IRON AND MAGNESIUM ON TEH PROPERTIES OF ALUMINUM DIE CASTING ALLOYS,” Nov. 1964, p. 8.
- [43] Chu, Yeou-Li, Cheng, Patrick, and Shivpuri, Rajiv, “Investigation of the soldering problem in aluminum die casting - Phenomena, mechanism and protection,” National Science Foundation Engineering Research Center for Net Shape Manufacturing, NADCA Technical Archive, ERC/NSM-C-93-36, Sep. 1993.
- [44] Y. Tsuchiya, H. Kawaura, K. Hashimoto, H. Inagaki, and T. Arai, “Core Pin Failure in Aluminum Die Casting and the Effect of Surface Treatment,” in The Many Faces of Die Casting, Minneapolis, MN, 1997, vol. T97-103.
- [45] Z. W. Chen, D. T. Fraser, and M. Z. Jahedi, “Structures of intermetallic phases formed during immersion of H13 tool steel in an Al–11Si–3Cu die casting alloy melt," Mater. Sci. Eng. A, vol. 260, no. 1–2, pp. 188–196, Feb. 1999, doi: 10.1016/S0921-5093(98)00963-0.
- [46] R. J. Barnhurst, D. Argo, and W. Walkington, “NADCA Sponsored Research: The Causes of Soldering in Zinc Die Casting,” in Die Casting Congress, 1997, vol. T97-033.
- [47] J. Song, X. Wang, T. DenOuden, and Q. Han, “Evolution of Intermetallic Phases in Soldering of the Die Casting of Aluminum Alloys,” Metall. Mater. Trans. A, vol. 47, no. 6, pp. 2609–2615, 2016, doi: 10.1007/s11661-016-3454-2.
- [48] A. Duarte, F. J. Oliveira, and F. M. Costa, “Characterisation of interface formed at 650°C between AISI H13 steel and Al–12Si–1Cu aluminium melt," Int. J. Cast Met. Res., vol. 23, no. 4, pp. 231–239, Aug. 2010, doi: 10.1179/136404610X12665088537455.
- [49] S. Sumanth and A. Diran, “The Role of Aluminum Alloy Chemistry and Die Material on Die Soldering,” in North American Die Casting Congress, Cleveland, OH, 1999, vol. T99-083. [Online]. Available: https://diecasting.org/wcm/Technology/Technical_Archive/wcm/Technology/Technical_Archive.aspx?hkey=62f825ba-424c-41c3-b10f-3b860771ffa4
- [50] M. Vilaseca, S. Molas, and D. Casellas, “High temperature tribological behaviour of tool steels during sliding against aluminium,” Wear, 2011, doi: 10.1016/j.wear.2011.07.007.
- [51] P. Terek et al., “Effects of die core treatments and surface finishes on the sticking and galling tendency of Al-Si alloy casting during ejection,” Wear, vol. 356–357, pp. 122-134, Jun. 2016, doi: https://doi.org/10.1016/j.wear.2016.03.016.
- [52] H. Cagin, “Techniques for Removing Stuck Castings," in NADCA Transactions, Jun. 1981, vol. T81-025, p. 4.
- [53] P. Terek et al., “The Influence of CrAlN Coating Chemical Composition on Soldering Resistance in Contact with Al-Si-Cu Alloy,” Mater. Proc., vol. 2, no. 1, p. 28, May 2020, doi: 10.3390/CIWC2020-06837.
- [54] P. Terek, L. Kovačević, A. Miletić, D. Kukuruzović, S. Baloš, and B. Škorić, "Improved ejection test for evaluation of soldering tendency of cast alloy to die core materials,” J. Mater. Process. Technol., vol. 266, pp. 114–124, Apr. 2019, doi: 10.1016/j.jmatprotec.2018.10.038.
- [55] Chen, Z. W. and Jahedi, M. Z., “Die erosion and its effect on soldering formation in high pressure die casting of aluminum alloys,” Mater. Des., vol. 20, pp. 303-309, 1999.
- [56] J. Jerina and M. Kalin, “Initiation and evolution of the aluminium-alloy transfer on hot-work tool steel at temperatures from 20 °C to 500 °C,” Wear, vol. 319, no. 1–2, pp. 234-244, Nov. 2014, doi: 10.1016/j.wear.2014.07.021.
- [57] R. Kimura, M. Yoshida, G. Sasaki, J. Pan, and H. Fukunaga, “Characterization of heat insulating and lubricating ability of powder lubricants for clean and high quality die casting,” J. Mater. Process. Technol., vol. 130–131, pp. 289–293, Dec. 2002, doi: 10.1016/S0924-0136(02)00808-7.
- [58] N. Nishi, “Challenge to Ultra Thin-Wall Zinc Die Casting under 0.5 mm Thickness," Cast. Eng., no. September 2007, p. 5, 2007.
- [59] MAGMAsoft. Kackerstrasse 11, 52072 Aachen, Germany: MAGMA Gmbh, 2019.
- [60] T. Cedorge and J. Colton, “Draft angle and surface roughness effects on sterolighography molds," Polym. Eng. Sci. Newtown, vol. 40, no. 7, p. 1581, Jul. 2000.
- [61] A. E. Palmer and J. S. Colton, “Failure mechanisms in stereolithography injection molding tooling,” Polym. Eng. Sci., vol. 40, no. 6, pp. 1395–1404, Jun. 2000, doi: 10.1002/pen.11269.
- [62] G. T. Pham and J. S. Colton, “Ejection force modeling for stereolithography injection molding tools,” Polym. Eng. Sci., vol. 42, no. 4, pp. 681–693, Apr. 2002, doi: 10.1002/pen.10981.
- [63] B. Omar and K. Barney, “Prediction of Local Part-Mold and Ejection Force in Injection Molding,” Trans. ASME, vol. 127, no. August 2005, pp. 598–604, Aug. 2005, doi: 10.1115/1.1951785.
- [64] S. Tetsuo, K. Nobuhiro, S. Kenji, K. Yoshikazu, and T. Ayumu, “An experimental study on ejection forces of injection molding,” J. Int. Soc. Precis. Eng. Nanotechnol., vol. 24, pp. 270–273, 2000, doi: 0141-6359/00/.
- [65] M. Sorgato, D. Masato, and G. Lucchetta, “Effects of machined cavity texture on ejection force in micro injection molding,” Precis. Eng., vol. 50, pp. 440–448, 2017, doi: 10.1016/j.precisioneng.2017.06.019.
- [66] Monroe, Alexander, Gaddam, Deepika, and Glim, Beau, “Preliminary Study on Ejection Force Prediction,” NADCA Congr. Tabletop, vol. T16-083, 2016.
- [67] A. L. ALTIERI and P. H. STEEN, “Adhesion Upon Solidification and Detachment in the Melt Spinning of Metals,” Metall. Mater. Trans. B, vol. VOLUME 45B, pp. 2262-2268, Dec. 2014, doi: 10.1007/s11663-014-0128-6.
- [68] M. D. Hanna, “Tribological evaluation of aluminum and magnesium sheet forming at high temperatures,” Wear, vol. 267, no. 5–8, pp. 1046–1050, Jun. 2009, doi: 10.1016/j.wear.2009.01.007.
- [69] H. Kitano, K. Dohda, M. Kalin, and K. F. Ehmann, “Galling growth analysis in metal forming,” Manuf. Lett., vol. 16, pp. 32–35, Apr. 2018, doi: 10.1016/j.mfglet.2018.03.003.
- [70] E. Huttunen-Saarivirta, L. Kilpi, T. J. Hakala, J. Metsäjoki, and H. Ronkainen, "Insights into the behaviour of tool steel-aluminium alloy tribopair at different temperatures,” Tribol. Int., vol. 119, pp. 567–584, Mar. 2018, doi: 10.1016/j.triboint.2017.11.041.
- [71] L. Wang and H. Yang, “Friction in aluminium extrusion—part 2: A review of friction models for aluminium extrusion,” Tribol. Int., vol. 56, pp. 99–106, Dec. 2012, doi: 10.1016/j.triboint.2012.06.006.
- [72] X. Ma, M. de Rooij, and D. Schipper, “A load dependent friction model for fully plastic contact conditions,” Wear, vol. 269, no. 11–12, pp. 790–796, Oct. 2010, doi: 10.1016/j.wear.2010.08.005.
- [73] X. Ma, M. B. de Rooij, and D. J. Schipper, “Friction conditions in the bearing area of an aluminium extrusion process,” Wear, vol. 278–279, pp. 1–8, Mar. 2012, doi: 10.1016/j.wear.2011.11.001.
- [74] L. Wang, J. Zhou, J. Duszczyk, and L. Katgerman, “Friction in aluminium extrusion-Part 1: A review of friction testing techniques for aluminium
- [75] J. Shigley, C. Mischke, and R. Budynas, Mechanical Engineering Design, 7th Edition. McGraw-Hill, 2004.
- [76] MATLAB. Natick, Massachusetts: Mathworks, 2020.
- [77] J. O. Andersson, T. Helander, P. F. Shi, and B. Sundman, Thermo-Calc and DICTRA, Computational tools for material science. 2002.
- [78] H. Springer, A. Kostka, J. F. dos Santos, and D. Raabe, “Influence of intermetallic phases and Kirkendall-porosity on the mechanical properties of joints between steel and aluminium alloys,” Mater. Sci. Eng. A, vol. 528, no. 13–14, pp. 4630–4642, May 2011, doi: 10.1016/j.msea.2011.02.057.
- [79] H. Springer, A. Kostka, E. J. Payton, D. Raabe, A. Kaysser-Pyzalla, and G. Eggeler, “On the formation and growth of intermetallic phases during interdiffusion between low-carbon steel and aluminum alloys,” Acta Mater., vol. 59, no. 4, pp. 1586–1600, Feb. 2011, doi: 10.1016/j.actamat.2010.11.023.
- [80] V. Jindal, V. C. Srivastava, A. Das, and R. N. Ghosh, “Reactive diffusion in the roll bonded iron-aluminum system,” Mater. Lett., vol. 60, no. 13–14, pp. 1758–1761, Jun. 2006, doi: 10.1016/j.matlet.2005.12.013.
- [81] Z. W. Chen, “Formation and progression of die soldering during high pressure die casting,” Mater. Sci. Eng. A, vol. 397, no. 1–2, pp. 356–369, 2005, doi: 10.1016/j.msea.2005.02.057.
- [82] C. Z. W., J. M.Z., and L. J.A., “Metallurgical Phenomena in Die/Casting Interfacial Regions During High Pressure Die Casting of Aluminum Alloys,” in North American Die Casting Congress, Cleveland, OH, 1999, vol. T99-084.
- [83] A. Bouayad, C. Gerometta, A. Belkebir, and A. Ambari, “Kinetic interactions between solid iron and molten aluminium,” Mater. Sci. Eng. A, vol. 363, no. 1–2, pp. 53-61, Dec. 2003, doi: 10.1016/S0921-5093(03)00469-6.
- [84] F. Yin, M. Zhao, Y. Liu, W. Han, and Z. Li, “Effect of Si on growth kinetics of intermetallic compounds during reaction between solid iron and molten aluminum," Trans. Nonferrous Met. Soc. China, vol. 23, no. 2, pp. 556–561, Feb. 2013, doi: 10.1016/S1003-6326(13)62499-1.
- [85] G. Eggeler, W. Auer, and H. Kaesche, “REACTIONS BETWEEN LOW ALLOYED STEEL AND INITIALLY PURE AS WELL AS IRON-SATURATED ALUMINUM MELTS BETWEEN 670 AND 800-DEGREES-C," Z. Met., vol. 77, no. 4, pp. 239–244, 1986.
- [86] Makhlouf M. Makhlouf and Diran Apelian, “Casting Characteristics of Aluminum Die Casting Alloys,” DOE/ID/13716, 792701, Feb. 2002. doi: 10.2172/792701.
- [87] A. Zovi and F. Casarotto, “SILAFONT-36, THE LOW IRON DUCTILE DIE CASTING ALLOY DEVELOPMENT AND APPLICATIONS,” Metall. Ital., 2007, [Online]. Available: https://www.fracturae.com/index.php/aim/article/view/517/488
- [88] Chu, Yeou-Li, Balasubramaniam, Srikanth, Rajan, Rajendra, and Shivpuri, Rajiv, "A Study of the Cast Alloy-Die Surface Interactions in Aluminum Die Casting," vol. T97-075, 1997.
- [89] Yu, Mulong, Chu, Yeou-Li, and Shivpuri, Rajiv, “A Study of Corrosion of Die Materials and Die Coatings in Aluminum Die Casting,” in North American Die Casting Congress, Cleveland, OH, Oct. 1993, vol. T93-072, pp. 191–198.
- [90] M. Movahedi, A. H. Kokabi, and S. M. Seyed Reihani, “Investigation on the bond strength of Al-1100/St-12 roll bonded sheets, optimization and characterization,” Mater. Des., vol. 32, no. 6, pp. 3143–3149, Jun. 2011, doi: 10.1016/j.matdes.2011.02.057.
- [91] M. Roulin and J. W. Luster, “Strength and Structure of Furnace-Brazed Joints between Aluminum and Stainless Steel,” Weld. Res. Suppl., vol. 78, no. 5, pp. 151-155, May 1999.
- [92] J. Vrenken, C. Goos, T. Veldt, and W. Braunschweig, “Fluxless Laser Brazing of Aluminium to Steel,” Join. Automot. Eng., 2009, [Online]. Available: Fluxless Laser Brazing of Aluminium to Steel
- [93] Tosa, Hiroki and Urakami, Akio, “Factors Influencing Die Casting Ejection,” in North American Die Casting Congress, Chicago, IL, Oct. 1972, vol. T72-041.
- [94] "Buhler Evolution Die Casting Machine Brochure.” Buhler. Accessed: May 01, 2021. [Online]. Available: https://www.buhlergroup.com/content/buhlergroup/global/en/products/evolution_die-castingmachineevolution.html
- [95] J. Lu, Y. Song, L. Hua, P. Zhou, and G. Xie, “Effect of temperature on friction and galling behavior of 7075 aluminum alloy sheet based on ball-on-plate sliding test,” Tribol. Int., vol. 140, p. 105872, Dec. 2019, doi: 10.1016/j.triboint.2019.105872.
- [96] C. M. Estey, S. L. Cockcroft, D. M. Maijer, and C. Hermesmann, “Constitutive behaviour of A356 during the quenching operation,” Mater. Sci. Eng. A, vol. 383, no. 2, pp. 245-251, Oct. 2004, doi: 10.1016/j.msea.2004.06.004.
- [97] A. Alankar and M. A. Wells, “Constitutive behavior of as-cast aluminum alloys AA3104, AA5182 and AA6111 at below solidus temperatures,” Mater. Sci. Eng. A, vol. 527, no. 29–30, pp. 7812–7820, Nov. 2010, doi: 10.1016/j.msea.2010.08.056.
- [98] C. H. Cáceres, “A Rationale for the Quality Index of Al-Si-Mg Casting Alloys,” p. 17, 1998.
- [99] F. A. Nichols, “Plastic instabilities and uniaxial tensile ductilities,” Acta Metall., vol. 28, no. 6, pp. 663–673, Jun. 1980, doi: 10.1016/0001-6160(80)90144-3.
- [100] R. Overfelt, S. Bakhtiyarov, and R. Taylor, “Thermophysical properties of A201, A319, and A356 aluminium casting alloys,” High Temp.-High Press., vol. 34, no. 4, pp. 401–409, 2002, doi: 10.1068/htjr052.
- [101] R. Brandt and G. Neuer, “Electrical Resistivity and Thermal Conductivity of Pure Aluminum and Aluminum Alloys up to and above the Melting Temperature," Int. J. Thermophys., vol. 28, no. 5, pp. 1429–1446, Nov. 2007, doi: 10.1007/s10765-006-0144-0.
- [102] J. A. Dantzig and M. Rappaz, Solidification, 1 st. EPFL Press, 2009.
- [103] P. Brancaleon, “Specifications and Standards Development for Enhanced Casting Performance through Examination of Mechanical Properties versus Casting Section Thickness,” in NADCA Transactions, Virtual Event, 2020, p. 7.
Copyright:
- This material is Alex Monroe's paper: Based on THERMOMECHANICAL MECHANISMS THAT CAUSE ADHESION OF ALUMINUM HIGH PRESSURE DIE CASTINGS TO THE DIE.
- Paper Source: https://doi.org/10.37099/mtu.dc.etdr/1277
This material was summarized based on the above paper, and unauthorized use for commercial purposes is prohibited.
Copyright © 2025 CASTMAN. All rights reserved.