This introductory paper is the research content of the paper "The die-cast copper motor rotor – a new copper market opportunity" published by the Copper Development Association Inc.
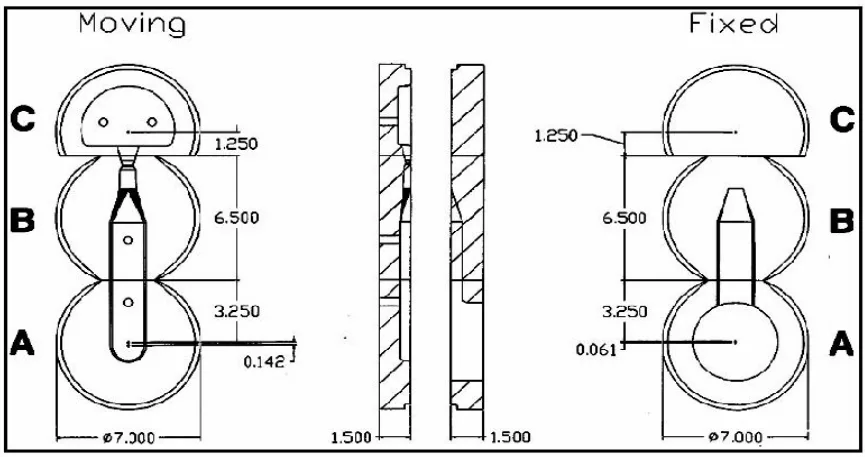
1. Overview:
- Title: The die-cast copper motor rotor – a new copper market opportunity
- Author: D. T. Peters, J. G. Cowie, E. F. Brush, Jr.
- Publication Year: Not specified in the provided text.
- Published Journal/Society: Not directly specified, but the authors are affiliated with the Copper Development Association Inc.
- Keywords: die-cast copper, motor rotor, squirrel cage, die life, thermal fatigue, nickel-base alloy, motor efficiency, energy loss reduction.
2. Abstract
Induction motor manufacturers have long known that substitution of copper for die-cast aluminum in the rotor squirrel cage would significantly reduce motor losses and improve electrical energy efficiency. Aluminum is readily die-cast, while copper is much more difficult to die-cast due to its high melting temperature, leading to premature die failure. This work addresses the die life problem. Candidate high-temperature die materials were surveyed. Computer simulation of cyclic thermal and stress gradients provided insight into the "heat checking" failure mechanism. A nickel-base alloy die system preheated to and operated at ~625°C has been developed. Copper motor rotors were die-cast, and motor test results showing a 15-20% reduction in motor losses and reduced operating temperatures are presented.
3. Research Background:
Background of the research topic:
- Induction motors commonly use die-cast aluminum in the rotor squirrel cage.
- Replacing aluminum with copper can significantly reduce motor losses and improve efficiency.
- Copper's high melting temperature makes die-casting difficult, causing premature die failure.
Status of previous research:
- A short report on copper motor rotor development was presented at Copper 99 (1).
- Tungsten alloy (Anviloy) was found suitable for die-casting copper.
- Certain nickel-base alloys showed promise.
- High die preheat and operating temperature were introduced to minimize thermal and strain gradients.
Need for research:
- Existing methods for producing copper rotors (for large or special purpose motors) are costly and slow, not suitable for mass production.
- Die-casting copper is preferable but challenging due to short die life caused by copper's high melting point.
- There's a need to solve the copper die-casting problem to offer motors with improved efficiency and reduced operating temperatures.
4. Research purpose and research question:
Research purpose:
- To address the die life problem in die-casting electrical grade copper.
- To develop a die system and process for mass-producing die-cast copper motor rotors.
Core research:
- Investigating high-temperature die materials.
- Understanding the "heat checking" failure mechanism through computer simulation.
- Developing a die insert heating and insulation system.
- Evaluating motor performance with die-cast copper rotors.
5. Research methodology
- Research Design: Experimental and computational.
- Data Collection:
- Survey of candidate high-temperature die materials.
- Computer simulation (3-D) of cyclic thermal and stress gradients in dies.
- Die material evaluation tests using H-13 steel, TZM, Anviloy, and nickel-base alloys (INCONEL 617, 625, 718, 754, 601).
- Pressure die-casting trials of copper test parts and motor rotors.
- Motor performance tests (dynamometer efficiency tests per IEEE Specification 112, test method B, and IEC 34-2 method).
- Analysis:
- Analysis of temperature profiles and stress distributions in die inserts.
- Evaluation of die material performance based on heat checking, cracking, and erosion.
- Comparison of motor efficiency and losses between copper and aluminum rotors.
- Metallurgical examination of cast copper rotors.
- Research Scope: Development and testing of die materials and casting processes for copper motor rotors, and evaluation of motor performance.
6. Key research results:
Key research results and presented data analysis:
- Computer simulation provided insight into thermal fatigue failure and how to minimize it by using high die preheat and operating temperatures.
- A nickel-base alloy (INCONEL alloys 617 and 625) die system, preheated and operated at ~625°C, significantly extended die life compared to conventionally operated die steels.
- A die insert heating and insulation system (Figure 3) was developed to maintain high operating temperatures.
- Die-cast copper rotors showed a 15-20% reduction in motor losses and reduced operating temperatures.
- Rotor resistance losses were reduced by 40% (Table I).
- Stray load losses were reduced by 23% (Table I).
- Windage and friction losses were reduced by 37% (Table I).
- Overall motor efficiency increased by at least 1.2 percentage points (Table II).
- Motor temperature rise was reduced by 4.5°C (Table II).
- Metallurgical examination showed minimal interaction between copper conductor bars and iron laminations.
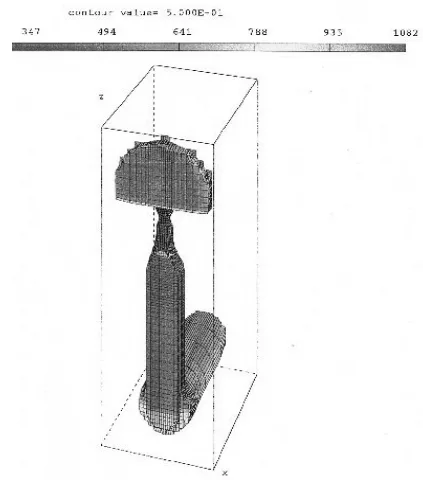
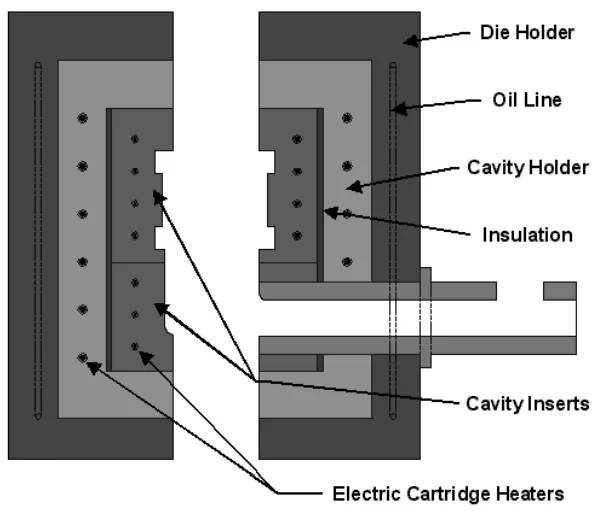
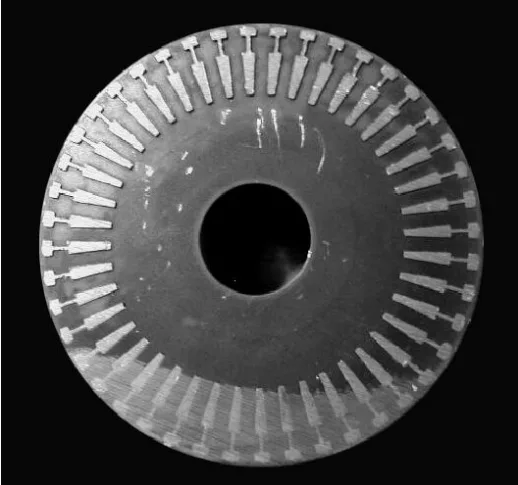
List of figure names:
- Figure 1 - Die Material Test Die Made up of Six Machined Inserts.
- Figure 2 - Output of Thermal Modeling Showing H-13 Die Surface “Painted” onto the Test Casting at Instant of Fill with 1200°C Copper.
- Figure 3 - Schematic Illustration of Placement of Electric Resistance Heaters and Insulation in the Die Material Test Set-up Developed in the Course of this Study.
- Figure 4 – Photograph of the Cross Section of a Die-cast Copper Rotor
7. Conclusion:
Summary of key findings:
- INCONEL alloys 617 and 625, operated at 600-650°C, are promising die materials for long die life in copper rotor production.
- Elevated die operating temperature is crucial for extending die life by minimizing thermal fatigue.
- Die-cast copper rotors significantly improve motor efficiency and reduce losses.
- The die-casting process for copper rotors is practical and reproducible.
- The research successfully addressed the challenge of die-casting copper for motor rotors, demonstrating a viable method for mass production.
- The findings have significant implications for improving motor efficiency, reducing energy consumption, and extending motor life.
- The development of a practical die heating and insulation system is a key contribution.
- The work supports the potential for a substantial new market for copper.
8. References:
- [1] D.T. Peters and J.G. Cowie, “The Copper Motor Rotor and Plastic Injection Molds – New Developments Relying on Copper's Conductivity”, Copper 99- Cobre 99, G.A. Eltringham, N.L. Piret and M. Sahoo, Eds., The Minerals, Metals & Materials Society, 1999, 313-325.
- [2] U.S. Department of Energy, DOE/CS-0147, “Classification and Evaluation of Electric Motors and Pumps”, February 1980.
- [3] E.A. Herman, J.F. Wallace, A.A. Machonis, Copper Alloy Pressure Die Casting, International Copper Research Association, New York, 1975, p.52.
- [4] D.T. Peters, J.G. Cowie, E.F. Brush, Jr. and S.P. Midson, “Use of High Temperature Die Materials and Hot Dies for High Pressure Die casting Pure Copper and Copper Alloys",
- S. Lie, and C. Di Pietro, “Copper Die-cast Rotor Efficiency Improvement and Economic Consideration”, IEEE Trans. Energy Conservation, Vol. 10, No. 3, 1995, 419-424.
- M. Poloujadoff, J.C. Mippo, and M. Nurdin, “Some Economical Comparisons
Between Aluminum and Copper Squirrel Cages”, IEEE Trans. Energy
Conservation, Vol. 10, No. 3, 1995, 415-418. - Private communication with manufacturer.
9. Copyright:
- This material is a paper by "[D.T. Peters, J.G. Cowie, E.F. Brush, Jr.]": Based on "[The die-cast copper motor rotor – a new copper market opportunity]".
- Source of paper: [DOI URL - Note: The DOI URL is not provided in the original document]
This material was created to introduce the above paper, and unauthorized use for commercial purposes is prohibited. Copyright © 2025 CASTMAN. All rights reserved.