This introduction paper is based on the paper "Tensile and Compressive Creep Behavior of Magnesium Die Casting Alloys Containing Aluminum" published by "Magnesium Alloys and their Applications. Edited by K. U. Kainer. WILEY-VCH Verlag GmbH, Weinheim.".
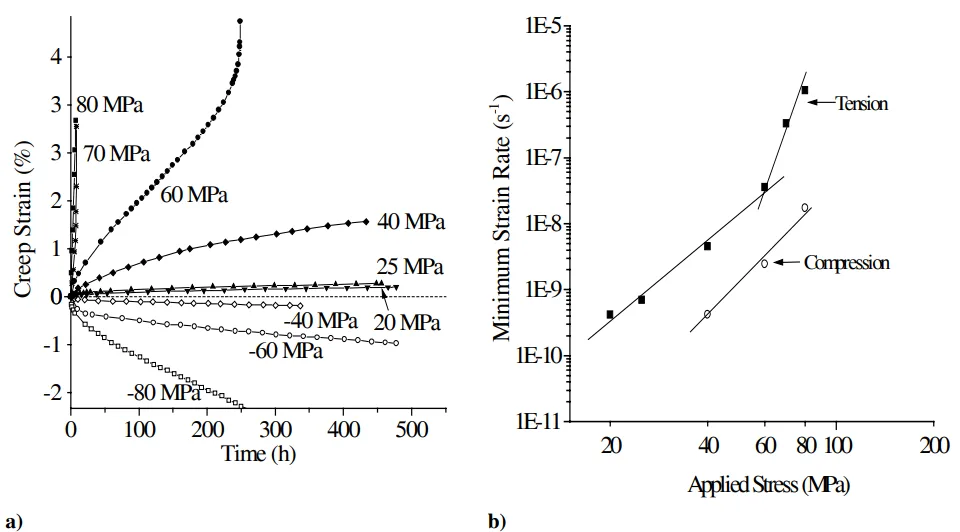
1. Overview:
- Title: Tensile and Compressive Creep Behavior of Magnesium Die Casting Alloys Containing Aluminum
- Author: S. R. Agnew, S. Viswanathan, E. A. Payzant, Q. Han, K. C. Liu, and E. A. Kenik
- Year of publication: 2000
- Journal/academic society of publication: Magnesium Alloys and their Applications. Edited by K. U. Kainer. WILEY-VCH Verlag GmbH, Weinheim.
- Keywords: Not specified in the paper.
2. Abstract:
This study investigates the creep mechanisms in commercial and experimental magnesium die casting alloys, focusing on their poor creep resistance which limits automotive applications. It reviews previous findings that die cast AM60B exhibits significantly slower creep rates in compression than in tension [1]. Building on evidence from Dargusch et al. [2] regarding the role of dynamic precipitation of the β-Mg17Al12 phase, this work forwards an explanation for the observed creep strength asymmetry in die cast magnesium alloys containing aluminum, attributing it to this dynamic precipitation. The overall aim is to expand the knowledge base for developing new alloys with improved creep resistance.
3. Introduction:
The automotive industry shows renewed interest in magnesium alloys due to their potential for vehicle mass reduction, leading to improved fuel efficiency. However, a primary limitation hindering their widespread application is their poor creep resistance. This study was undertaken to expand the understanding of creep mechanisms in current commercial and experimental die casting alloys, with the ultimate goal of developing new alloys possessing improved creep resistance. An earlier report [1] demonstrated that die cast AM60B alloy exhibited significantly slower creep rates in compression compared to tension. Furthermore, Dargusch et al. [2] previously presented evidence indicating that dynamic precipitation of the β-Mg17Al12 phase affected the creep behavior of magnesium alloys. This paper aims to provide an explanation for the observed creep strength asymmetry in die cast magnesium alloys containing aluminum, focusing on the role of dynamic precipitation.
4. Summary of the study:
Background of the research topic:
Magnesium alloys are attractive for automotive applications due to their low density, which can contribute to vehicle mass reduction and enhanced fuel efficiency. However, their inherent poor creep resistance at elevated temperatures poses a significant challenge, limiting their broader implementation in structural components.
Status of previous research:
Previous research indicated that die cast AM60B magnesium alloy exhibits a notable asymmetry in creep behavior, with significantly slower creep rates observed under compressive loading compared to tensile loading at the same stress levels [1]. Additionally, work by Dargusch et al. [2] suggested that the dynamic precipitation of the β-Mg17Al12 intermetallic phase during creep plays a crucial role in influencing the creep characteristics of magnesium alloys containing aluminum.
Purpose of the study:
The primary objectives of this study were:
- To expand the existing knowledge of creep mechanisms in commercial and experimental magnesium die casting alloys that contain aluminum.
- To utilize this understanding to guide the development of new magnesium alloys with enhanced creep resistance.
- Specifically, to propose and substantiate an explanation for the observed tension/compression creep strength asymmetry in these alloys, linking it to the phenomenon of dynamic precipitation.
Core study:
The core of this research involved a comprehensive investigation into the tensile and compressive creep behavior of several magnesium alloys. This included die cast AM60B and a series of permanent mold (PM) cast alloys: AZ91D, AM60B, AS41, AE42, and a Mg-4 wt%Al-0.8 wt%Ca alloy. A key component of the study was the use of in-situ high-temperature X-ray diffraction (XRD) to monitor and analyze the dynamic precipitation of the β-Mg17Al12 phase during simulated creep conditions (annealing). This allowed for correlation between microstructural evolution and the macroscopic creep behavior, particularly the asymmetry between tensile and compressive creep.
5. Research Methodology
Research Design:
The study was designed as an experimental investigation into the creep behavior of magnesium alloys.
- Materials and Specimen Preparation:
- Two types of creep specimens were utilized. The first series consisted of specimens machined directly from an AM60B die cast automotive component with an average thickness of 5 mm. These die cast AM60B samples had porosity levels on the order of 2-4%.
- The second set comprised specimens permanent mold (PM) cast as tensile test bars of AZ91D, AM60B, AS41, AE42, and Mg-4 wt%Al-0.8 wt%Ca alloys. The PM cast AM60B and AZ91D samples were fully dense.
- Density of samples was measured by weighing in air and in water.
- Creep Testing:
- All creep tests were conducted at 150°C.
- Six die cast AM60B specimens were tested in tension at constant applied engineering stresses of 20, 25, 40, 60, 70, or 80 MPa.
- Three compressive creep tests on die cast AM60B were conducted at -40, -60, and -80 MPa.
- In-situ High Temperature X-ray Diffraction:
- Used to investigate dynamic precipitation.
- Thin samples (0.5 x 10 x 10 mm) were cut from AM60B (die cast) and AZ91D (PM cast), then polished, etched, and mounted on a Pt13%Rh heater strip using carbon paint in a Buehler HDK 2.3 high temperature furnace attachment, run under vacuum.
- θ-2θ scans were made over the range 2θ = 30-50° (Cu-Kα radiation) each hour for 30 hours and again at ~48 hours during annealing at 225°C.
Data Collection and Analysis Methods:
- Creep Data: Creep strain was measured as a function of time. Minimum creep rates were determined from the creep curves. The relationship between applied stress and minimum creep rate was analyzed using a power-law type constitutive equation to determine stress exponents.
- XRD Data:
- An estimate of the β phase volume fraction was made using the summed integrated intensity of all its peaks.
- The lattice constants of the primary magnesium phase were determined as a function of annealing time.
- Data were analyzed using Jade 5.0 [Materials Data, Inc.].
Research Topics and Scope:
- Tensile and compressive creep behavior of die cast AM60B and PM cast Mg-Al alloys (AZ91D, AM60B, AS41, AE42, Mg-4Al-0.8Ca) at 150°C.
- Investigation of the tension/compression creep strength asymmetry.
- The role of dynamic precipitation of the β-Mg17Al12 phase during creep.
- Microstructural evolution, specifically β phase precipitation and changes in magnesium lattice parameters, during in-situ annealing using XRD.
- Influence of aluminum content and ternary additions on creep behavior.
6. Key Results:
Key Results:
- Creep Asymmetry in AM60B: Die cast AM60B tested at 150°C showed significantly lower creep rates in compression than in tension by an order of magnitude for all pairs tested at the same stress level (Figure 1a, 1b).
- Stress Exponents: For AM60B, a stress exponent, n ≈ 4, was determined for the low tensile stress range and the entire range of compression stresses, suggesting dislocation climb accommodated by self-diffusion as the rate-controlling step. At high tensile stresses (>60 MPa), the apparent stress exponent increased to n ≈ 10, indicative of power-law breakdown.
- PM Cast Alloy Behavior: PM cast specimens of various alloy compositions (AZ91D, AM60B, AS41, AE42, Mg-4% Al- 0.8% Ca) exhibited a similar transition in creep behavior (power law breakdown) above ~50 MPa (Figure 2). The creep resistance trend was AZ91D < AM60B < AS41 < AE42 ~ Mg-4% Al- 0.8% Ca. A lower aluminum content generally resulted in better creep performance, and ternary additions were also important.
- Asymmetry in Fully Dense Alloys: The tension/compression asymmetry was also observed in fully dense PM cast AM60B and AZ91D samples (Figure 3a), indicating that porosity is not the sole cause of this phenomenon. In contrast, aluminum alloy A380 exhibited essentially symmetric creep behavior (Figure 3b).
- Dynamic Precipitation of β-Mg17Al12: In-situ high-temperature XRD studies at 225°C confirmed dynamic precipitation of the β-Mg17Al12 phase in supersaturated regions (Figure 4).
- The volume fraction of the β phase was observed to grow during annealing (Figure 5, Figure 6a).
- Concurrently, the primary magnesium phase's lattice constants dilated as aluminum exited the matrix to form the new precipitate, evidenced by the Bragg peaks shifting to lower 2θ values (Figure 5, Figure 6b).
- Explanation for Creep Asymmetry: The asymmetric creep behavior is explained by two factors related to dynamic precipitation:
- Lattice Dilation: The precipitation reaction results in lattice dilation. This dilation is enhanced under tension (due to positive hydrostatic stress) and suppressed under compression. If there is synergy between precipitation and dislocation climb (e.g., due to increased vacancy concentration or mobility), creep will proceed faster in tension.
- Precipitation-Induced Strain: The precipitation reaction itself is measurable (e.g., 20 hrs at 225°C results in a net tensile strain of ~0.1%). This strain would add to the creep strain measured in tension and decrease it in compression.
- Influence of Aluminum Supersaturation: The connection between aluminum supersaturation and creep strength asymmetry is supported by Figure 3a, which shows more asymmetry for AZ91D (higher Al content) than for AM60B.
- Effect of Ternary Additions: As mentioned with reference to Sohn et al. [6], ternary additions (e.g., Ca or RE) can reduce asymmetry in alloys like AZ91 and AM50, even when aluminum levels are similar to those in alloys showing asymmetry.
- Deleterious Effect of Excess Aluminum: Excess aluminum is detrimental to creep resistance not due to the β phase itself (which can harden if finely dispersed by aging), but because of the dynamic precipitation event occurring during creep.
- Strategies for Improved Creep Resistance:
- Reducing the aluminum content of an alloy (with care, as high Al content aids die casting performance).
- Adding ternary elements that preferentially bind aluminum, reducing the driving force for β precipitation.
- Aging alloys prior to service to reduce aluminum supersaturation.
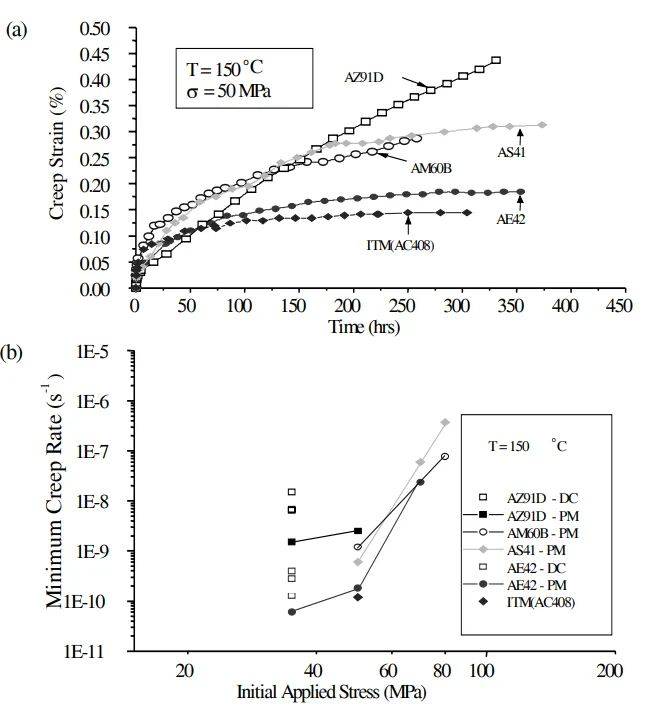
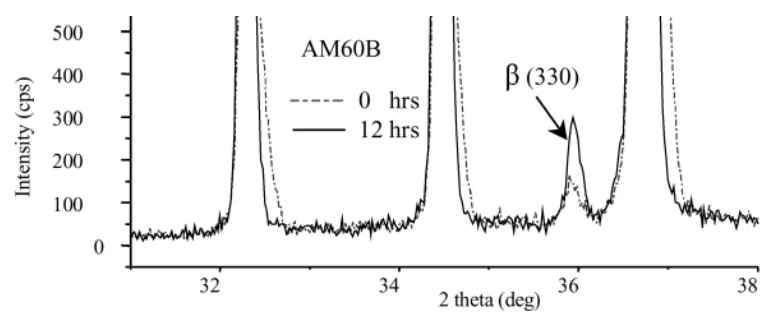
Figure Name List:
- Figure 1: (a) Creep curves of AM60B die cast samples subjected to tension or compression over a range of applied stresses at 150°C. (b) A log-log plot of the applied stress versus minimum creep rate shows that the low and high stress regions can be fitted to a power law with stress exponents of n ≈ 4 and 10, respectively.
- Figure 2: (a) Creep curves comparing the alloys tested at 150°C. (b) Minimum strain rate as a function of the applied stress. Die cast AZ91D and AE42 tested at 35 MPa shown for comparison.
- Figure 3: (a) A tension compression asymmetry is observed even for fully dense AM60B and AZ91D PM cast samples. (b) Aluminum alloy A380 exhibits essentially symmetric behavior.
- Figure 4: Schematic of magnesium supersaturated with aluminum precipitating the β phase
- Figure 5: Small segment of the scanned 2θ range (30-50°) during 225°C annealing shows the growth of a β phase peak and the shift of the magnesium peaks to lower 20 values.
- Figure 6: (a) shows the increase in the volume fraction of the β phase, as determined by the integrated intensities and (b) shows the dilation of the primary magnesium's lattice (AZ91D).
7. Conclusion:
The study concludes that the observed asymmetry in tensile and compressive creep behavior of magnesium-aluminum alloys is not solely due to porosity but is fundamentally linked to the dynamic precipitation of the β-Mg17Al12 phase. This precipitation process results in lattice dilation and induces a measurable strain, both of which are influenced by the hydrostatic stress state: tensile stresses enhance these effects, leading to accelerated creep, while compressive stresses suppress them, resulting in slower creep. The degree of aluminum supersaturation in the alloy is a critical factor; higher supersaturation leads to more pronounced asymmetry and contributes to the generally deleterious effect of high aluminum content on creep resistance. To improve creep performance, strategies such as reducing aluminum content, adding ternary elements to bind aluminum, or pre-aging alloys to reduce supersaturation before service are recommended.
8. References:
- [1] S. R. Agnew, K. C. Liu, E. A. Kenik and S. Viswanathan, Magnesium Technology 2000, Eds. H. I. Kaplan, J. Hryn, and B. Clow, TMS, Warrendale, PA, 2000, p. 285.
- [2] M. S. Dargusch, G. L. Dunlop, K. Pettersen, Magnesium Alloys and their Applications, Eds. B. L. Mordike and K. U. Kainer, Werkstoff-Informationsgesellschaft, Frankfurt, Germany, 1998, p. 277-282.
- [3] J. E. Dorn, Creep and Recovery, ASM, Metals Park, Ohio, 1957, 255-283.
- [4] F. C. Chen, J. W. Jones, T. A. McGinn, J. E. Kearns, A. J. Nielsen, and J. E. Allison, SAE Technical Paper, #970325, 1997, 13-21.
- [5] J.-P. Poirier, Creep of Crystals, Cambridge, New York, 1985, p. 145.
- [6] K. Y. Sohn, J. W. Jones, and J. E. Allison, Magnesium Technology 2000, Eds. H. I. Kaplan, J. Hryn, and B. Clow, TMS, Warrendale, PA, 2000, 271-278.
9. Copyright:
- This material is a paper by "S. R. Agnew, S. Viswanathan, E. A. Payzant, Q. Han, K. C. Liu, and E. A. Kenik". Based on "Tensile and Compressive Creep Behavior of Magnesium Die Casting Alloys Containing Aluminum".
- Source of the paper: DOI not provided in the paper.
This material is summarized based on the above paper, and unauthorized use for commercial purposes is prohibited.
Copyright © 2025 CASTMAN. All rights reserved.