This article introduces the paper "Study on Microstructures and Properties of the Al. Alloy Vacuum Die-Cast Parts of TL117 and C611" presented in the Journal of Physics: Conference Series.
1. Overview:
- Title: Study on Microstructures and Properties of the Al. Alloy Vacuum Die-Cast Parts of TL117 and C611
- Author: Lijun Han, Xuesong Wu, Junjie Zhu, Ming Bai, Xiaohong Zheng, and Ze Zhang
- Publication Year: 2023
- Publishing Journal/Academic Society: Journal of Physics: Conference Series, MSEE-2022
- Keywords: (Not explicitly listed in the paper, but implied keywords are) Vacuum die-casting, Aluminum alloy, Microstructure, Mechanical properties, TL117, C611, Heat treatment, Rare earth element, Strontium (Sr), Zirconium (Zr)
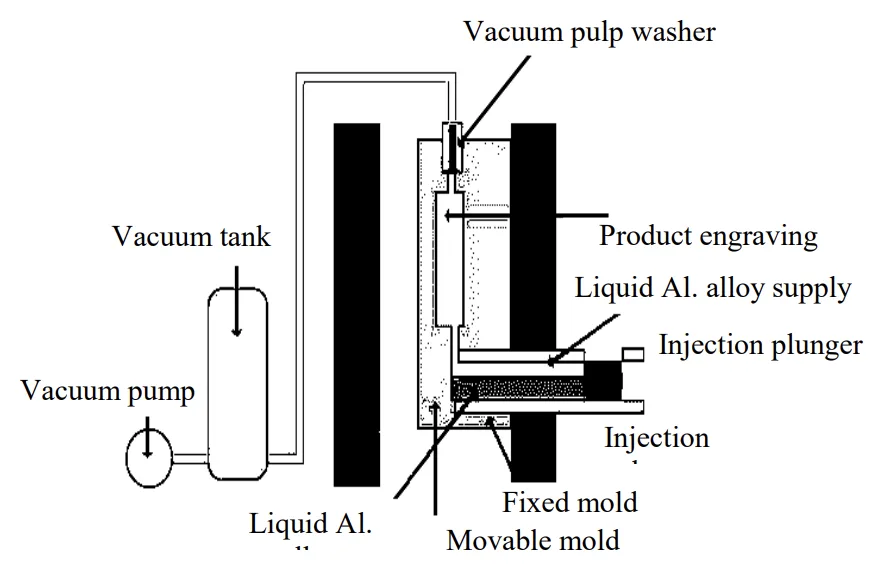
2. Research Background:
- Social/Academic Context of the Research Topic: The increasing demand for lightweight and environmentally friendly vehicles in the automotive industry drives the application of vacuum die-cast aluminum alloy parts. Vacuum die-casting offers advantages over common casting methods due to its ability to produce parts with higher strength, reduced weight, and lower CO2 emissions.
- Limitations of Existing Research: Traditional die-cast aluminum parts often require T6 heat treatment (HT) and part correction processes to achieve desired strength and dimensional accuracy. These post-processing steps increase manufacturing costs and process complexity.
- Necessity of the Research: There is a need to simplify the production of high-performance die-cast aluminum parts and reduce costs by eliminating T6 heat treatment and correction processes. This can be achieved by adjusting the alloy composition, particularly through the addition of rare earth elements like Strontium (Sr) and increased Zirconium (Zr).
3. Research Purpose and Research Questions:
- Research Purpose: To investigate the microstructures and properties of vacuum die-cast Aluminum alloy C611, using vacuum die-cast Aluminum alloy TL117 as a reference. The ultimate goal is to determine if C611, with compositional adjustments, can eliminate the need for T6 heat treatment and part correction in die-cast aluminum alloy production, thereby reducing costs.
- Key Research Questions:
- How do the microstructures of vacuum die-cast C611 and TL117 alloys differ?
- What are the differences in second phases, strength, elongation, and fracture morphologies between C611 and TL117?
- What are the mechanisms behind the high performance and small deformation observed in C611 parts without T6 heat treatment and correction?
- How does the addition of rare earth element Sr and increased Zr content in C611 affect its crystallization process and crystal morphology compared to TL117?
- Research Hypotheses: By adding rare earth element Sr and increasing Zr content in the Al. alloy, the crystallization process and crystal morphology can be controlled, leading to grain refinement and controlled phase transformation stress. This will enable C611 parts to achieve comparable or improved strength and deformation properties to TL117 parts (which require T6 treatment) without the need for T6 heat treatment and correction processes.
4. Research Methodology:
- Research Design: Comparative experimental study. Two aluminum alloys, TL117 and C611, were processed using vacuum die-casting. TL117 samples underwent T6 heat treatment and correction, while C611 samples were used as-cast, without T6 heat treatment or correction.
- Data Collection Method:
- Mechanical Property Testing: Tensile tests were conducted to measure yield strength, tensile strength, and elongation.
- Microstructural Analysis: Optical microscopy was used to examine the microstructures of both alloys in sections vertical and parallel to the surface.
- Phase Analysis: X-ray Diffraction (XRD) was employed to identify the phases present in both alloys.
- Differential Scanning Calorimetry (DSC): DSC analysis was performed to study the crystallization latent heat and phase transformation behavior of both alloys.
- Fracture Morphology Analysis: Scanning Electron Microscopy (SEM) was used to analyze the fracture surfaces of tensile tested samples.
- Analysis Method:
- Quantitative analysis of mechanical properties (yield strength, tensile strength, elongation).
- Qualitative and comparative analysis of microstructures, phases, fracture morphologies, and DSC curves between TL117 and C611.
- Research Subjects and Scope:
- Materials: Vacuum die-cast Aluminum alloys TL117 (AlSi10MnMg) and C611 (composition detailed in Table 2 of the paper).
- Manufacturing Process: Vacuum die-casting process with specific parameters (Injection speed: 3.0 m/s, Casting temperature: 700 °C, Pre-heating temperature: 200 °C, Pressure: 200 MPa, Vacuum degree: 20 mbar).
- Scope: Investigation of microstructure and mechanical properties relevant to automotive applications, focusing on the feasibility of eliminating T6 heat treatment and correction processes for die-cast aluminum parts.
5. Main Research Results:
- Key Research Results:
- Mechanical Properties: C611, without T6 treatment, exhibited slightly lower yield strength (average 123 MPa) compared to T6 treated TL117 (average 130 MPa), but higher tensile strength. Elongation to fracture was slightly lower for C611 but remained above 10% for both alloys.
- Microstructure: C611 showed finer and more spheroidized grains due to the addition of Sr modifier and higher Zr content. Both alloys exhibited fine and evenly distributed grains due to the vacuum die-casting process.
- Phase Analysis: Both alloys primarily consisted of α-Al matrix, Si, and Al4.01MnSi0.74 phases. TL117 also contained SiC. The content of monatomic Si was higher in TL117 due to aging treatment.
- DSC Analysis: C611 showed a unique DSC curve with two thermal equilibrium stages during solidification, suggesting a mechanism for reduced deformation.
- Statistical/Qualitative Analysis Results:
- Yield Strength: Average yield strength of TL117 was slightly higher than C611 (Figure 4).
- Tensile Strength: Average tensile strength of C611 was slightly higher than TL117 (Figure 5).
- Elongation: Average elongation of TL117 was slightly higher than C611 (Figure 6).
- Microstructure: Micrographs (Figure 8) visually confirmed finer and more spheroidized grains in C611 compared to TL117.
- XRD: XRD patterns (Figure 7) identified the phases present in both alloys.
- DSC: DSC curves (Figure 11) showed distinct solidification behavior for C611 with two equilibrium stages.
- Fracture Morphology: SEM images (Figure 10) showed dimple fracture morphology for both alloys, indicating plastic fracture.
- Data Interpretation:
- The slightly lower yield strength of C611 is attributed to the absence of T6 solution treatment, which in TL117 enhances yield strength by dissolving strengthening elements into the α-Al matrix.
- The higher tensile strength of C611 is likely due to the finer grain size and grain boundary strengthening from precipitated phases, facilitated by Sr and Zr additions.
- The reduced deformation in C611 is attributed to the two-stage solidification process observed in DSC, which allows for stress relaxation during phase transformation.
- The addition of Sr and increased Zr in C611 effectively refines the microstructure and modifies grain morphology, contributing to its desirable properties without T6 treatment.
- Figure Name List:
- Figure 1. Structure of the vacuum die-cast equipment
- Figure 2. The vacuum die-cast Process
- Figure 3. The sample and product
- Figure 4. Yield strength of the samples
- Figure 5. Tensile strength of the samples
- Figure 6. Elongation to fracture of the samples
- Figure 7. The XRD spectrums of the TL117 and C611
- Figure 8. Microstructures of the C611 and TL117
- Figure 9. Tensile stress-strain curves of the samples
- Figure 10. SEM micrographs of the two kinds of samples
- Figure 11. DSC curves of the samples C611 and TL117
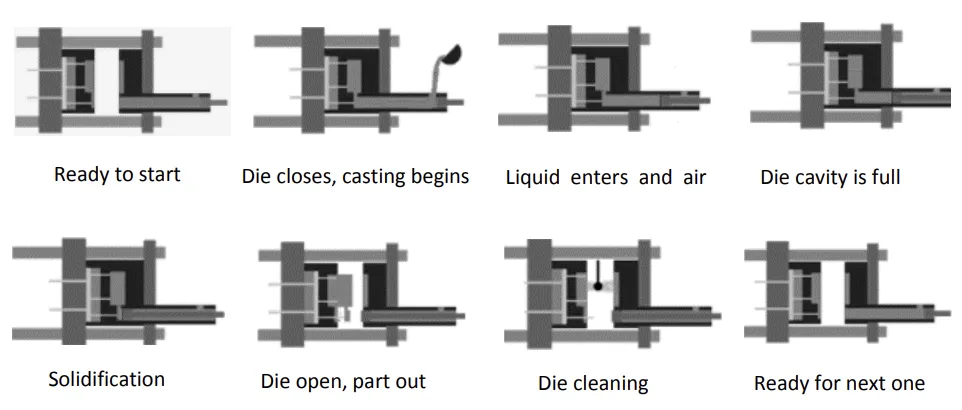
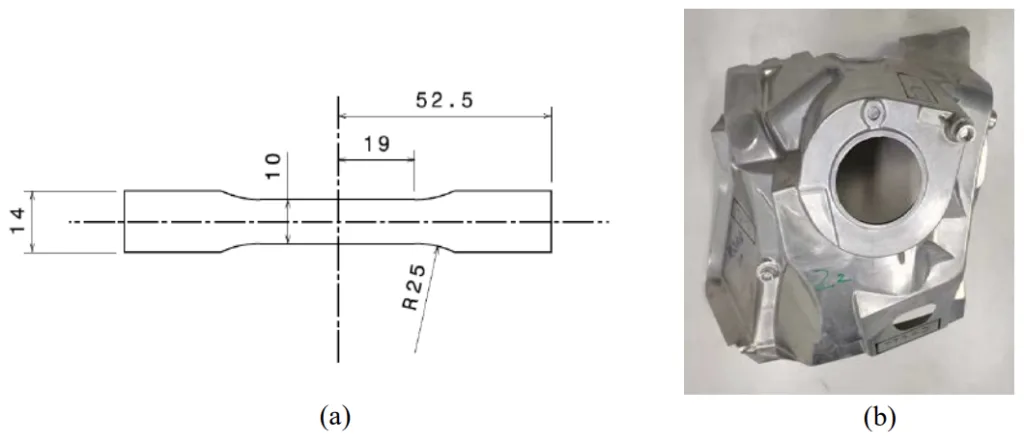
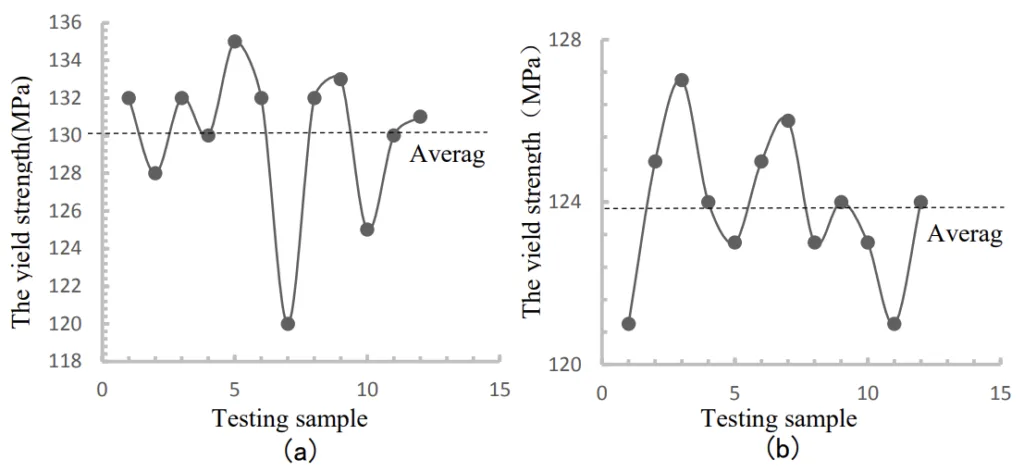
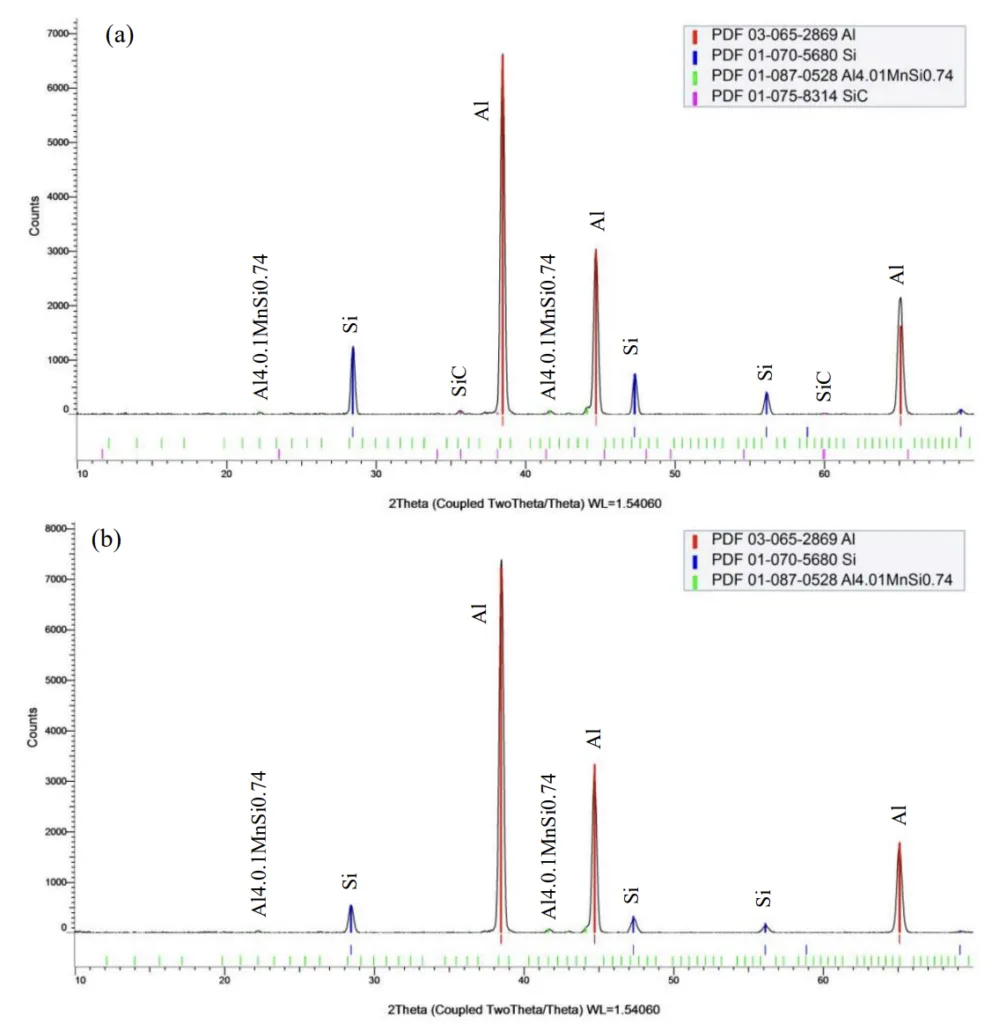
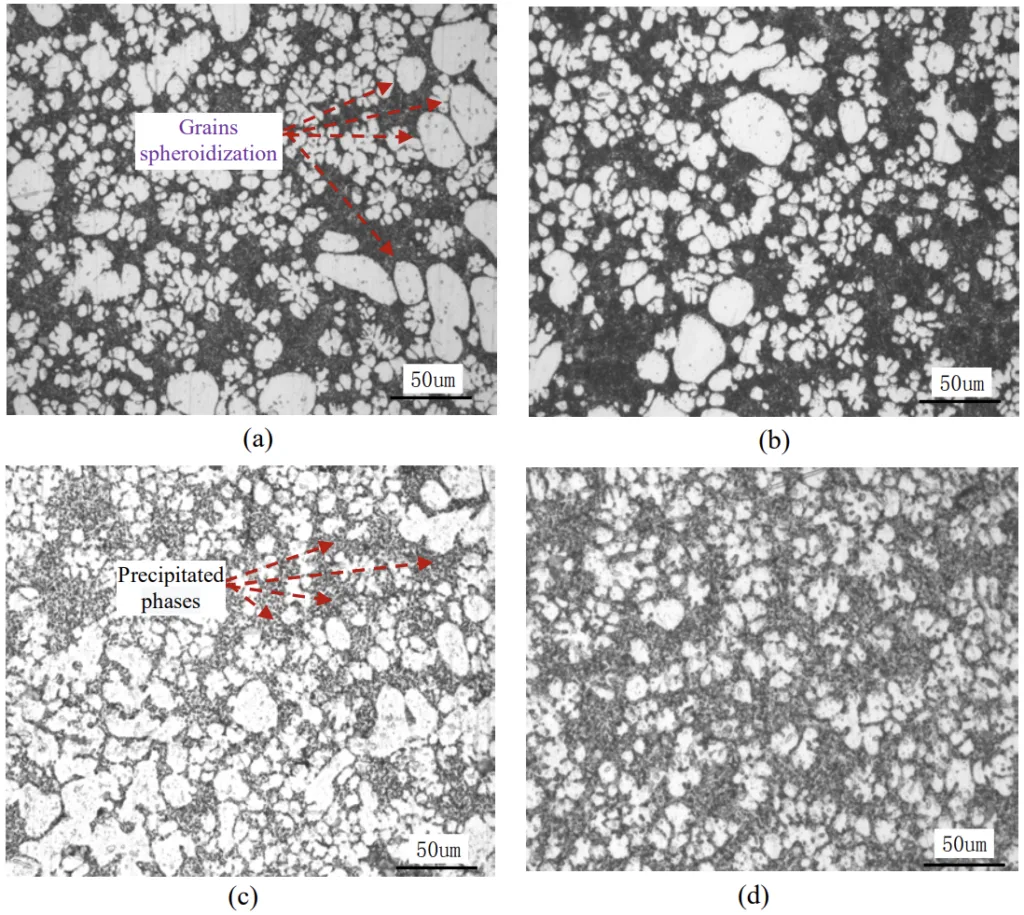
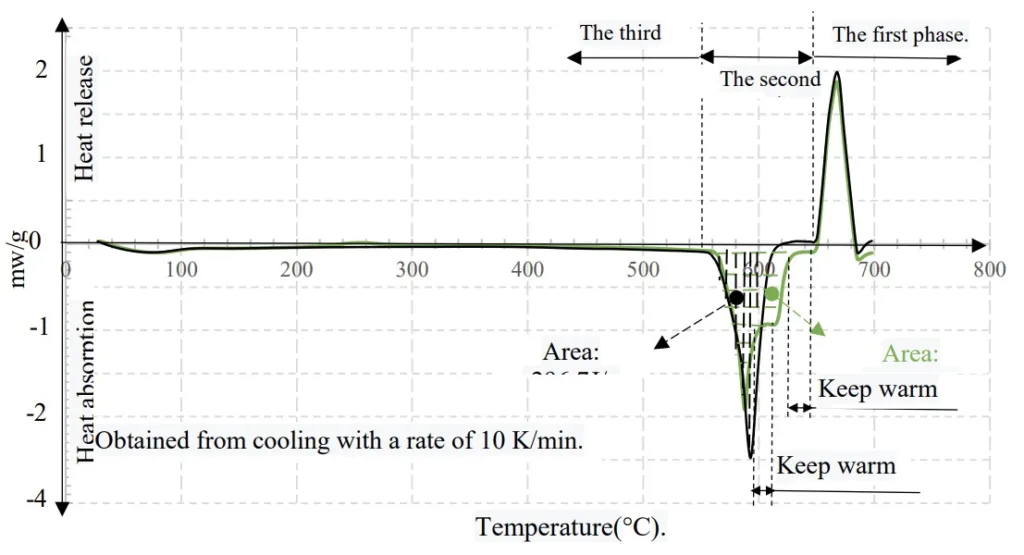
6. Conclusion and Discussion:
- Summary of Main Results: The study demonstrated that vacuum die-cast Al. alloy C611, with the addition of Sr and increased Zr, achieves high performance without T6 heat treatment and correction processes. C611 exhibits comparable mechanical properties to T6 treated TL117, with a slightly lower yield strength but higher tensile strength. The unique solidification behavior of C611, characterized by two thermal equilibrium stages, contributes to reduced deformation.
- Academic Significance of the Research: This research contributes to the understanding of how compositional modifications, specifically the addition of Sr and increased Zr, can alter the microstructure and properties of vacuum die-cast aluminum alloys. It highlights the potential to control crystallization and phase transformation processes through alloy design, leading to simplified manufacturing.
- Practical Implications: The findings suggest that Al. alloy C611 can be used to produce vacuum die-cast parts with high performance and dimensional stability without the need for costly and complex T6 heat treatment and correction processes. This has significant practical implications for cost reduction and process simplification in the automotive and potentially other industries utilizing die-cast aluminum components.
- Limitations of the Research: The study focused on a comparative analysis of only two alloys, TL117 and C611. Further research could explore a wider range of alloy compositions and processing parameters to optimize the properties of vacuum die-cast aluminum alloys without T6 treatment. The elongation of C611 was slightly reduced compared to TL117, which could be further investigated and potentially improved.
7. Future Follow-up Research:
- Directions for Follow-up Research:
- Further optimization of the composition of C611-type alloys, exploring different concentrations of Sr and Zr, and potentially other rare earth elements.
- Investigation of the effect of varying vacuum die-casting parameters on the microstructure and properties of C611.
- Detailed analysis of the two-stage solidification process in C611 and its impact on stress relaxation and deformation.
- Evaluation of other mechanical properties, such as fatigue and impact resistance, of C611.
- Application studies of C611 in specific automotive components to validate its performance in real-world conditions.
- Areas Requiring Further Exploration: The slight reduction in elongation of C611 compared to TL117 warrants further investigation to understand the underlying mechanisms and explore potential alloy modifications or process adjustments to enhance ductility while maintaining high strength and dimensional stability.
8. References:
- [1] Z H Yuan, et al, Microstructure evolution of modified die-cast AlSi10MnMg alloy during solution treatment and its effect on mechanical properties, Trans. Nonferrous Met. Soc. China. 29 (2019) 919–930.
- [2] C L Yang, Effects of cooling rate on solution heat treatment of as-cast A356 alloy [J], Transactions of Nonferrous Metals Society of China. 25 (2015) 3189–3196.
- [3] B Dang, Effect of as-solidified microstructure on subsequent solution-treatment process for A356 Al alloy [J], Transactions of Nonferrous Metals Society of China. 26 (2016) 634–642.
- [4] H X Cao, et al, The influence of different vacuum degree on the porosity and mechanical properties of aluminum die-casting [J], Vacuum. 146 (2017) 278–281.
- [5] L X Bo, et al, Trans. Nonferrous Met. Soc. China 29(2019) 919–930 929mechanical properties in vacuum-assist high-pressure die-casting of AZ91D alloy [J], Journal of Materials Processing Technology. 231 (2016)1–7.
- [6] L Wang, et al, Microstructure and mechanical properties of high vacuum die-casting AlSi10MnMgFe alloy [J], Special casting and nonferrous alloys. 34(2014) 499-503
- [7] M Vlach, et al, Heat treatment and age hardening of Al–Si–Mg–Mn commercial alloy with addition of Sc and Zr [J], Materials Characterization. 129 (2017) 1–8.
- [8] G J Gao, et al, Influence of different solution methods on microstructure, precipitation behavior and mechanical properties of Al–Mg–Si alloy [J], Transactions of Nonferrous Metals Society of China. 28 (2018) 839–847.
- [9] L P Ding, et al, The natural aging and precipitation hardening behavior of AlMgSiCu alloys with different Mg/Si ratios and Cu additions [J], Materials Science and Engineering A. 627(2015) 119–126.
- [10] D K Dwivedi, et al, Influence of silicon content and heat treatment parameters on mechanical properties of cast AlSiMg alloys[J], International Journal of Cast Metals Research. 19(2006) 275–282.
- [11] D A Lados, et al, Solution treatment effects on microstructure and mechanical properties of Al (1 to 13 pct) SiMg cast alloys [J], Metallurgical and Materials Transactions B, 42(2011) 171–180.
- [12] Juan Zhou, et al, Effect of Zr on microstructure and properties of cast high strength aluminum alloy, Foundry. 58 (2009): 266-269
- [13] J Q GAN, et al, Effect of Sr modification on microstructure and thermal conductivity of hypoeutectic Al–Si alloys, Transactions of Nonferrous Metals Society of China. 30(2020)2879-2890
- [14] A Mazahery, et al, Modification mechanism and microstructural characteristics of eutectic Si in casting Al–Si alloys, A review on experimental and numerical studies [J]. 66 (2014) 726–738.
- [15] Q Cai, et al, Microstructure evolution and mechanical properties of new die-cast Al–Si–Mg–Mn alloys, Materials and Design. 187(2020) 1-11
- [16] Y Zhang, et al, Cluster-assisted nucleation of silicon phase in hypoeutectic Al–Si alloy with further inoculation [J], Acta Materialia. 70 (2014) 162–173.
- [17] A M SAMUEL, et al. Effect of grain refining and Sr-modification interactions on the impact toughness of Al–Si–Mg cast alloys [J], Materials and Design. 56 (2013) 264-273.
9. Copyright:
- This material is Lijun Han et al.'s paper: Based on Study on Microstructures and Properties of the Al. Alloy Vacuum Die-Cast Parts of TL117 and C611.
- Paper Source: https://doi.org/10.1088/1742-6596/2468/1/012111
This material was summarized based on the above paper, and unauthorized use for commercial purposes is prohibited.
Copyright © 2025 CASTMAN. All rights reserved.