This article introduces the paper 'Study of Porosity Defect in Aluminum Die Castings and its Evaluation and Control for Automotive Applications' published by 'International Research Journal of Engineering and Technology (IRJET)'.
1. Overview:
- Title: Study of Porosity Defect in Aluminum Die Castings and its Evaluation and Control for Automotive Applications
- Author: Sumit Shukla
- Publication Year: July 2020
- Publishing Journal/Academic Society: International Research Journal of Engineering and Technology (IRJET)
- Keywords: Aluminum, Computed tomography, Non-Destructive Testing, Porosity & Radiographic Testing
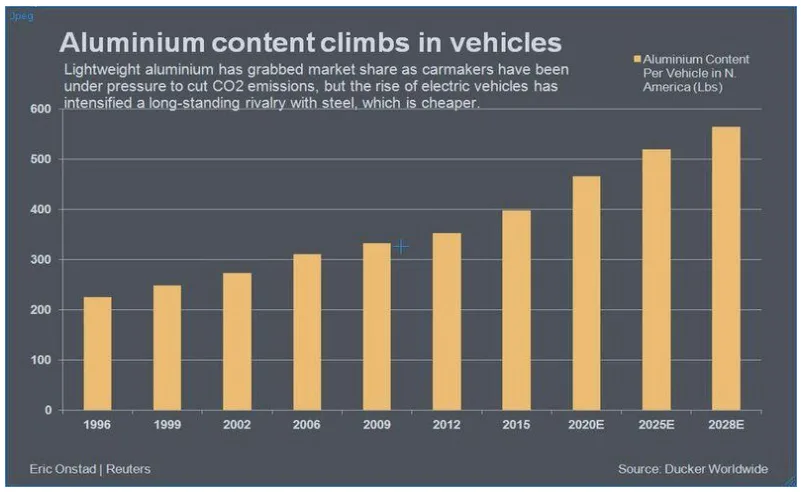
2. Abstracts
The growing requirement of competitive products in Automotive Market is in race and winner is always with high quality product built with defect free components. Certain Defects are unavoidable but yes can be limited by implementing certain controls in design and process. Die cast components are highly in use into Automotive applications such as Heatsinks or casings and so is the existence of Porosity in them analyzed and verified as OK up to certain levels. So, yes Porosity is a big concern in die casting as a defect but also the good news is that porosity doesn't always mean a casting is defective and that changes need to be made. A full inspection may show that it meets your stability and structural integrity requirements. This paper explains the detailed study of Porosity defect especially in Aluminum Die Castings used in Automotive Industry and focus on various Analysis and Verification methods used to identify the presence of Porosity based on common Standards.
3. Research Background:
Background of the Research Topic:
In the competitive automotive market, the demand for high-quality, defect-free components is paramount. Die casting is extensively utilized in automotive applications, particularly for components like Heatsinks and casings. Porosity, a common defect in die cast components, necessitates careful analysis and verification to ensure acceptable quality levels. While porosity is a recognized concern in die casting, it is crucial to understand that its presence does not automatically render a casting defective. Comprehensive inspection is essential to ascertain whether components meet stability and structural integrity requirements. Aluminum is increasingly favored in the automotive sector due to its advantageous properties, including lightweight nature, electrical and thermal conductivity, mechanical strength, and corrosion resistance. This has led to a significant incorporation of aluminum in automotive parts such as doors, trunks, hoods, engines, and notably as heatsinks in automotive electronics for effective heat dissipation. Aluminum is recognized as "the fastest growing automotive material" and is experiencing unprecedented growth in automotive material applications.
Status of Existing Research:
Existing research acknowledges that certain defects in die casting are unavoidable but can be limited through design and process controls. Porosity in die castings is a well-documented phenomenon that requires thorough analysis and verification. Industry surveys, such as those by Ducker Worldwide and WardsAuto and DuPont Automotive, highlight the increasing adoption of aluminum in automotive manufacturing to meet stringent fuel economy and emissions standards by 2025, further emphasizing the importance of managing defects like porosity in aluminum die castings.
Necessity of the Research:
Porosity in die cast components can significantly impact structural integrity and functionality, potentially leading to weak points and affecting pressure tightness and ingress protection. For instance, porosity can cause leakage and compromise performance in parts designed to contain gases or fluids. Furthermore, porosity can indirectly affect surface finishing requirements and customer satisfaction. Therefore, characterizing porosity in castings is vital for estimating fatigue strength and ensuring long-term service life. This study addresses the necessity for a detailed examination of porosity defects specifically in Aluminum Die Castings used within the Automotive Industry. It focuses on various Analysis and Verification methods employed to identify porosity, referencing common industry Standards for evaluation and control.
4. Research Purpose and Research Questions:
Research Purpose:
This paper aims to provide a detailed study of Porosity defects, specifically in Aluminum Die Castings utilized in the Automotive Industry. The primary focus is to elucidate various Analysis and Verification methods employed to detect and evaluate the presence of Porosity, referencing common industry standards.
Key Research:
The key research areas investigated in this study are:
- Analysis of Porosity defects in Aluminum Die Castings.
- Examination of Verification methods for Porosity detection, including Non-Destructive Testing (NDT) techniques.
- Review of Common Standards utilized for Porosity evaluation in the automotive industry.
Research Hypotheses:
This paper does not explicitly state research hypotheses.
5. Research Methodology
Research Design:
This study employs a descriptive and analytical research design, functioning as a handbook-level review of porosity defects in aluminum die casting. It synthesizes existing knowledge and standards to provide a comprehensive overview of the subject matter, focusing on automotive applications.
Data Collection Method:
The data collection method is based on a comprehensive review of existing literature, industry standards, and technical resources pertinent to porosity in die casting. This includes analysis of published research, industrial standards such as ASTM E505 and VDG Specification P 201, and relevant industry surveys and reports.
Analysis Method:
The analysis method involves a descriptive examination of porosity characteristics, including types, causes, and effects on die cast components. It includes a comparative analysis of different Non-Destructive Testing (NDT) methods, specifically Radiographic Testing (RT) and Computed Tomography (CT), for porosity detection and evaluation. Furthermore, the study provides an analytical overview of industry standards for porosity assessment, detailing their application and significance.
Research Subjects and Scope:
The research is focused on porosity defects occurring in aluminum die castings, specifically within the context of automotive applications. The scope encompasses a detailed discussion of porosity types (Gas-Related Porosity and Shrinkage-Related Porosity), evaluation methodologies using NDT techniques, and the application of industry-recognized standards for porosity assessment and control.
6. Main Research Results:
Key Research Results:
The key research results presented in this paper are:
- A comprehensive explanation of porosity as a critical defect in die casting components, detailing its implications for structural integrity and functional performance.
- A clear classification and description of porosity types, distinguishing between Gas-related Porosity and Shrinkage-related Porosity, including their causes and characteristic appearances.
- A detailed exposition of Radiographic Testing (RT) and Computed Tomography (CT) as primary Non-Destructive Testing (NDT) methods for porosity analysis, highlighting their principles, applications, and comparative advantages in porosity detection and characterization.
- An overview of industry standards, specifically ASTM E505 and VDG Specification P 201, used in the automotive industry for porosity evaluation, detailing their standard definitions, reference radiographs, and acceptance criteria.
- A discussion on strategies for minimizing porosity in aluminum die castings, emphasizing the importance of design considerations and manufacturing process optimization, including design stage guidelines and manufacturing stage techniques like vacuum casting.
Analysis of presented data:
The paper effectively utilizes figures and tables to present data and illustrate key concepts:
- Figures 1-4: Illustrate the growing demand for aluminum in automotive applications and provide an overview of Aluminum Die Casting processes, including High Pressure and Low Pressure Die Casting, and Hot-Chamber and Cold-Chamber types.
- Figures 5-10: Depict various manifestations of porosity in die cast components, including surface and internal porosity, and specifically Gas Porosity and Shrinkage Porosity, showcasing their visual characteristics.
- Figures 11-13: Compare 2D and 3D Radiographic Inspection techniques for porosity detection, illustrating the appearance of porosity in radiographic images and the advantages of Computed Tomography (CT).
- Figures 14-15: Present an analysis of a diecast component using CT imaging, demonstrating the application of CT scan data for porosity measurement and evaluation.
- Figure 16: Provides an overview of test methods and measured variables for determining porosity, comparing Visual inspection, 2D Radiographic test (X-ray), and 3D Radiographic test (CT X-ray).
- Figures 17-21: Detail the ASTM E 505 standard, including reference radiographs for different porosity grades, acceptance limit examples, and representative radioscopy pictures for porosity assessment based on the standard.
- Figures 22-23: Illustrate the representation of Pore Diameter and Pore Length as defined in VDG Specification P 201 and provide an example of a Porosity Key in engineering drawings based on this standard.
- Figure 24: Shows CT scan evaluation results for component samples, demonstrating the application of porosity standards in practical evaluation.
- Figure 25: Presents examples of microstructures with varying pore contents, visually correlating porosity levels with microstructure images.
- Figures 26-28: Provide Die cast checklist examples for part design and manufacturing stages, and an example checklist part 1,2&3 for die specifications, emphasizing design for manufacturability and quality control.
- Figure 27: Compares die castings produced with and without vacuum casting, illustrating the reduction in porosity achieved through vacuum casting techniques.
Figure Name List:
- Fig 1: Growing demand of Aluminum into the Automotive World
- Fig 2: Aluminum Die Casting components generally used for Automotive Applications
- Fig 3: Types of Pressure Die Casting Process
- Fig 4: Types of High Pressure Die Casting Process
- Fig 5: Porosity in the Die cast components
- Fig.6: Problems associated with Porosity
- Fig.7: Gas Porosity
- Figure 8: Gas porosity is round with smooth walls
- Fig.9: Shrinkage Porosity
- Fig.10: Shrinkage Porosity closed view
- Figure 11: The porosity (highlighted in green) is shown in a lighter appearance, while the rest of the casting has a darker appearance.
- Figure 12: Characterization of Porosity Types through Radiographic Inspection
- Figure 13: Characterization of Porosity through simple 2D Radiographic Inspection
- Figure 14: Analysis through CT Image of a diecast component
- Figure 15: Shows the result of the metallographic examination of the part with the largest content of porosities detected by the tomographic scan.
- Figure 16: Overview of test methods/measured variables for determining porosity
- Figure 17: ASTM E 505: Reference Radiographs for Inspection of Aluminum Die Castings
- Figure 18: Acceptance Limit example
- Figure 19: Category and Grade Requirement
- Figure 20: Representative radioscopy pictures captures
- Figure 21: Results as depicted from representative radioscopy pictures
- Figure 22: Representation of Pore Diameter / Pore Length
- Figure 23: Representation of Porosity Key in drawings
- Figure 24: Component 1 and 2 – Section views at different areas
- Figure 25
- Figure 26: Die cast checklist example
- Figure 27: Without vacuum casting (left) With vacuum casting (right)
- Figure 28: Example checklist Part 1,2&3
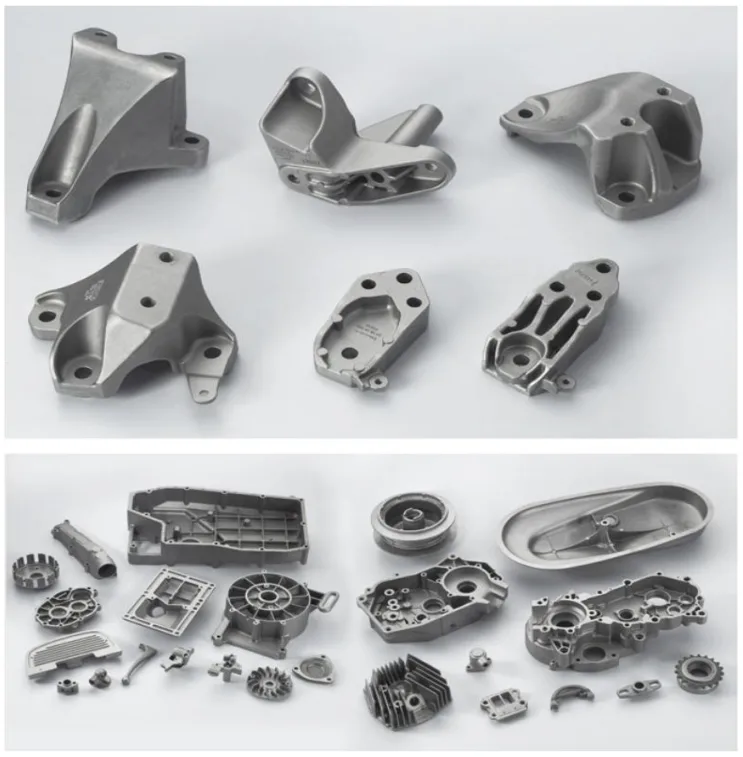
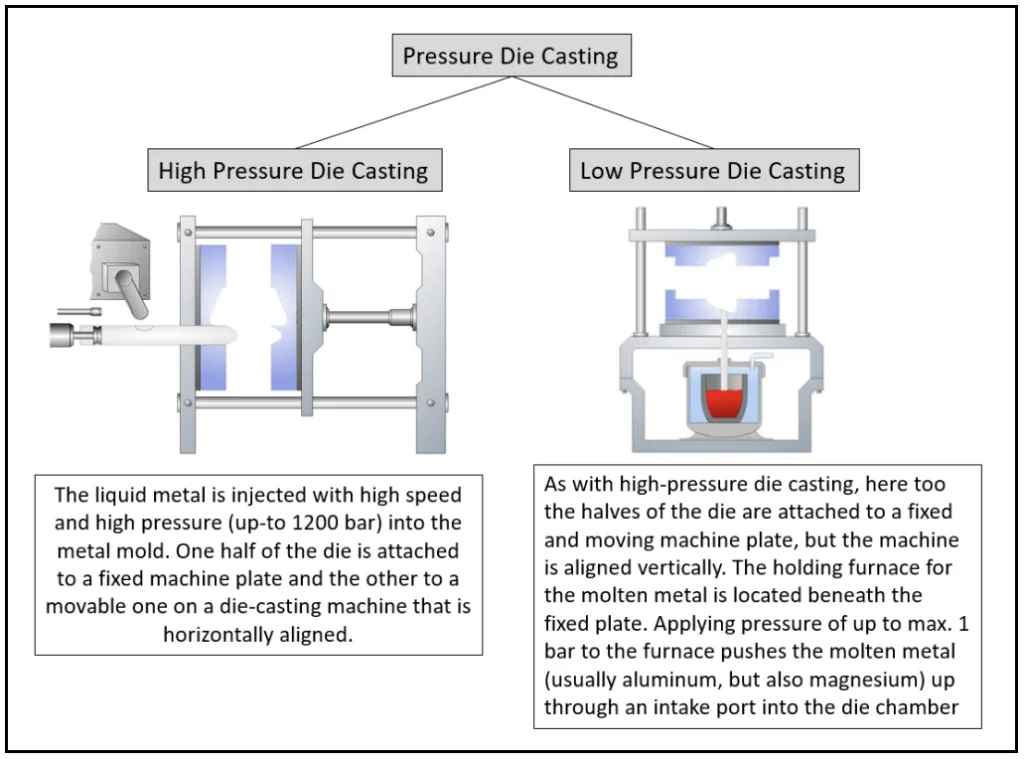
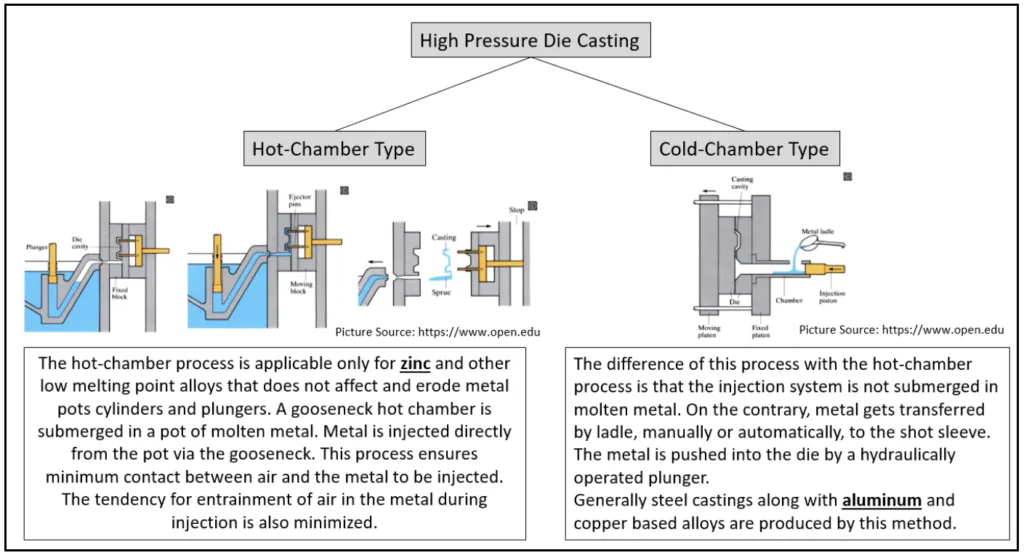
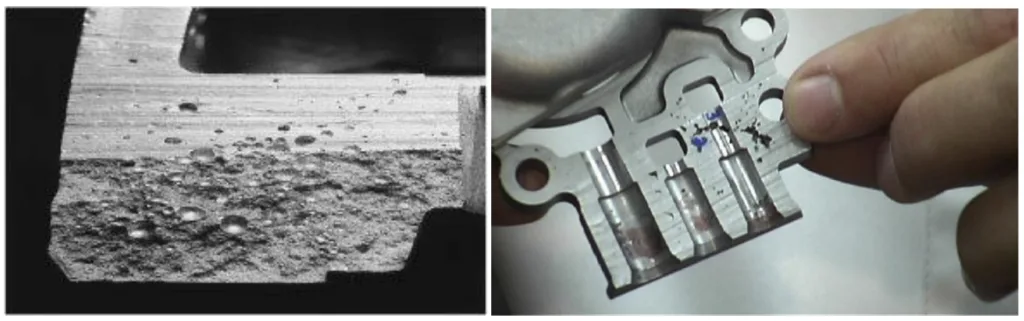
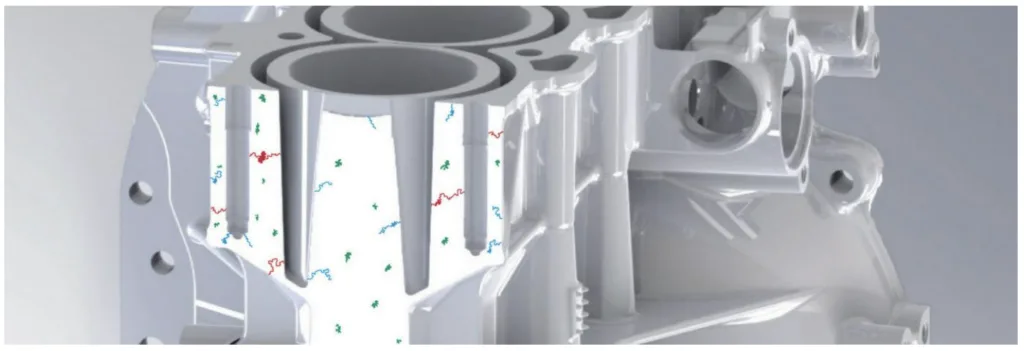
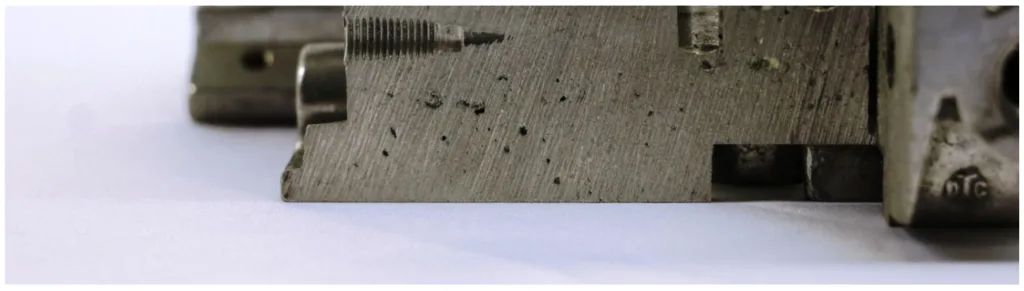
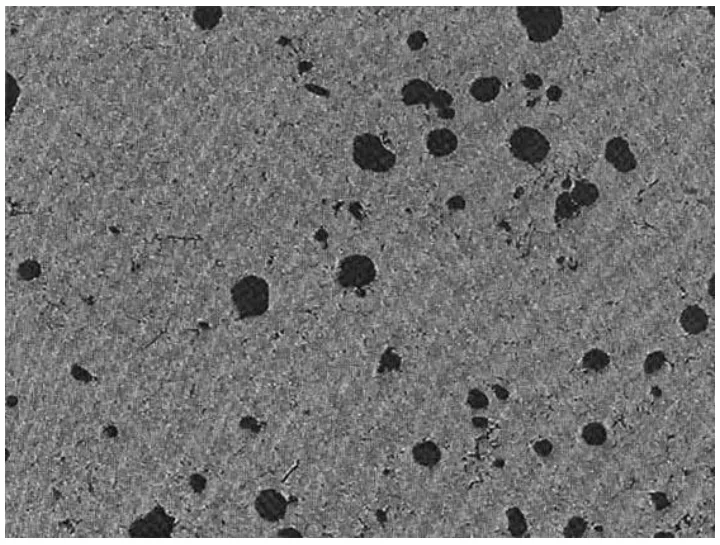
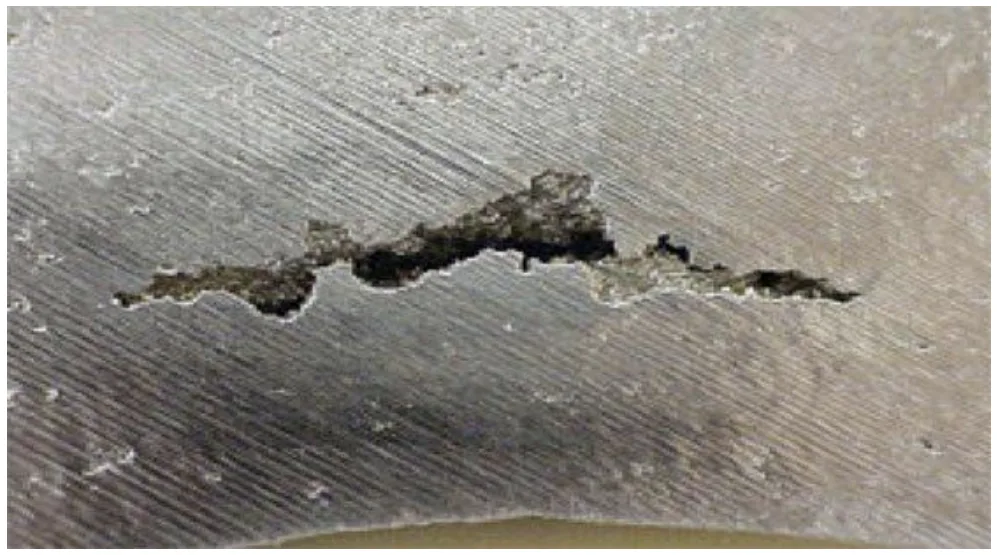
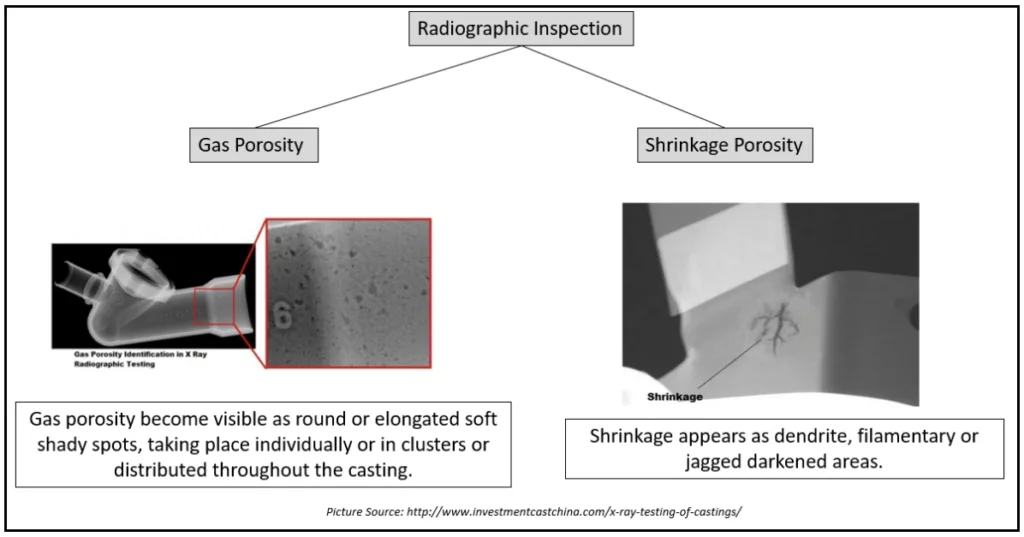
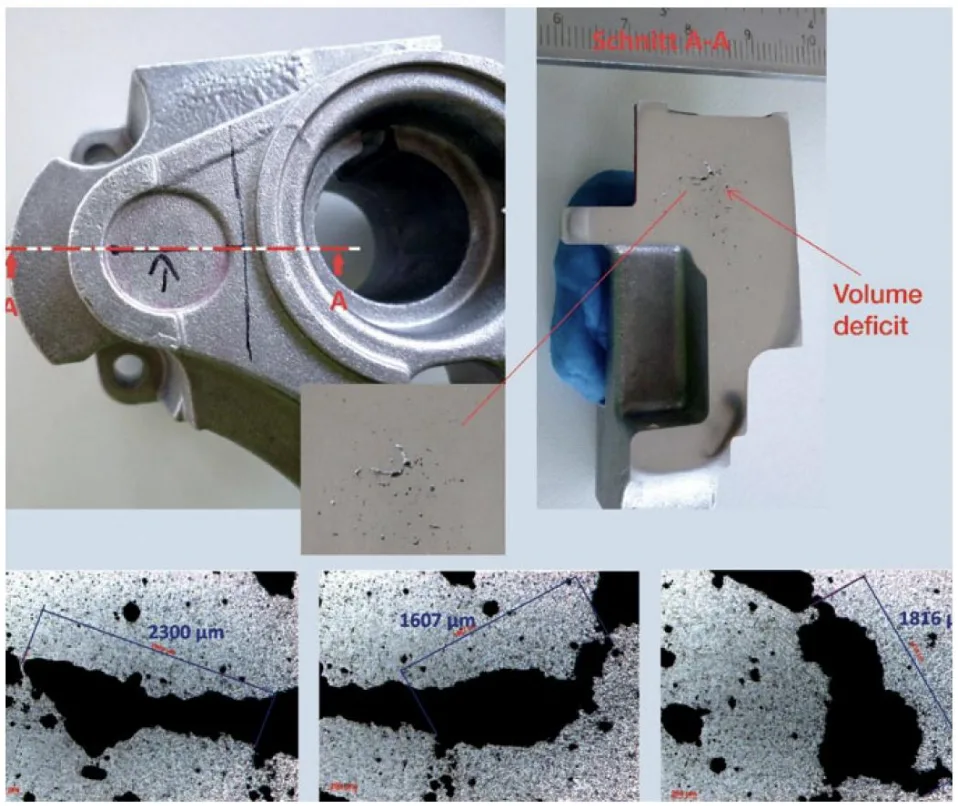
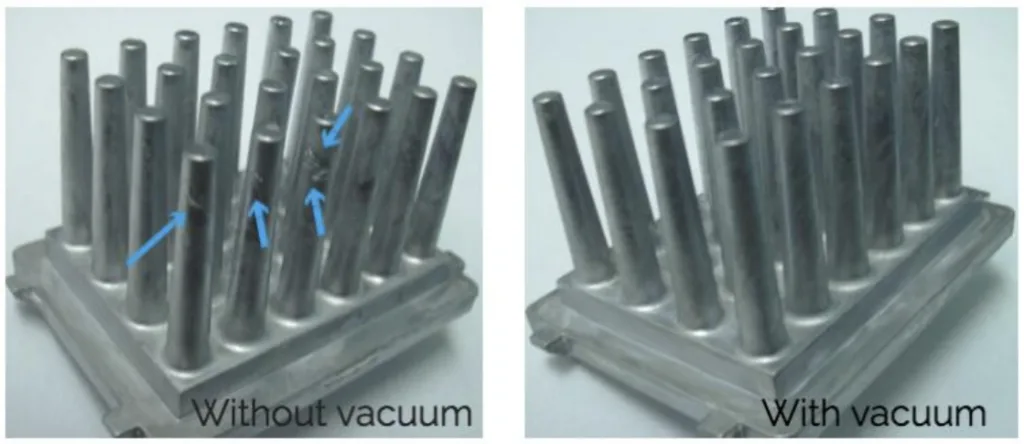
7. Conclusion:
Summary of Key Findings:
This study underscores that Porosity is a critical factor influencing the Function and Safety of die cast products, particularly in the automotive industry. The research highlights the essential role of Non-Destructive Testing (NDT) methods, specifically Radiographic Testing (RT) and Computed Tomography (CT), in evaluating porosity levels and characteristics. Furthermore, the paper emphasizes the significance of industry standards, such as ASTM E505 and VDG Specification P 201, which provide crucial guidelines for porosity assessment and quality control in automotive die castings. A key finding is that by adopting a structured technical approach encompassing both the Design and Manufacturing stages, it is possible to significantly mitigate casting defects, including porosity, early in the production process. This proactive approach minimizes deviations and complexities that may arise in later stages of manufacturing.
Academic Significance of the Study:
This study offers significant academic value by providing a comprehensive and structured overview of porosity defects in aluminum die casting, a critical area in materials engineering and manufacturing. It consolidates information on porosity types, evaluation methodologies, and relevant industry standards, serving as a valuable resource for researchers, academics, and students in the field of die casting and non-destructive testing. The paper contributes to the body of knowledge by elucidating the complexities of porosity in automotive aluminum die castings and emphasizing the importance of robust quality control measures.
Practical Implications:
The practical implications of this study are substantial for the automotive die casting industry. The paper provides engineers and designers with actionable insights into understanding, evaluating, and minimizing porosity in aluminum die cast components. It guides practitioners in selecting appropriate NDT methods for porosity detection and characterization, enabling more effective quality assurance processes. The detailed explanation of industry standards like ASTM E505 and VDG Specification P 201 equips manufacturers with the necessary tools for implementing standardized porosity assessment and acceptance criteria. Moreover, the emphasis on design and manufacturing process optimization offers practical strategies for reducing porosity, enhancing component quality, and improving overall production efficiency.
Limitations of the Study and Areas for Future Research:
As a review paper, this study is limited by its reliance on existing literature and standards, rather than presenting original experimental data. Future research could benefit from quantitative studies focused on specific automotive components, investigating the formation and control of porosity under varying die casting process parameters. Further exploration into advanced NDT techniques beyond RT and CT, such as ultrasonic testing or eddy current testing, and their effectiveness in porosity evaluation would be valuable. Additionally, research focused on optimizing die casting processes and design parameters, including gating systems, venting strategies, and cooling channel designs, to minimize porosity in aluminum die castings, represents a promising area for future investigation.
8. References:
- [1] [2]: www.spotlightmetal.com
- [3]: https://www.godfreywing.com/blog
- [4]: Zhao, X., He, Z., Zhang, S., Liang, D.: A sparse representation based robust inspection system for hidden defects classification in casting components. Neurocomputing 153, 1-10 (2015)
- [5]: VW 50093: Issue 2012-07
- Fig [2]: www.investmentcastchina.com
- Fig [5]: https://www.hillandgriffith.com/die-casting-news/die-casting-porosity-2 and
http://www.mapeng.net/Files/Remoteupfile/2015-1/24/01-gas-porosity-in-castings.jpg - Fig [6] [7] [9]: https://www.godfreywing.com/blog/how-to-fix-die-casting-porosity
- Fig [8] [10]: https://www.hillandgriffith.com/die-casting-news/diecasting-gas-porosity-problem-solving
- Fig [11]: https://www.godfreywing.com
- Fig [13] [14]: https://www.yxlon.com/en/applications/foundries
- Fig [15]: http://www.papco.cz/ke_stazeni/soubor2_62.pdf
- Fig [16]: P202 Version: September 2010 BDG-Layout August 2015
- Fig [18] [19]: http://www.voith.com/corp-en/VN_3068_en.pdf
- Fig [22] [25]: BDG, Hansaallee 203, 40549 Düsseldorf, for download: www.bdguss.de
- Fig [27]: https://www.dynacast.com/en/knowledge-center/multiple-design-solutions/die-cast-design/part-improvement/porosity
- Fig [28]: NADCA Product Specification Standards for Die Castings / 2015
9. Copyright:
- This material is "Sumit Shukla"'s paper: Based on "Study of Porosity Defect in Aluminum Die Castings and its Evaluation and Control for Automotive Applications".
- Paper Source: www.irjet.net
This material was summarized based on the above paper, and unauthorized use for commercial purposes is prohibited.
Copyright © 2025 CASTMAN. All rights reserved.