This technical summary is based on the academic paper "ASPECTS CONCERNING THE PROCESSING METHODS OF METALLIC ALLOYS IN THE SEMISOLID STATE" published by CIOATĂ Vasile George in ANNALS OF THE FACULTY OF ENGINEERING HUNEDOARA (2005, Tome III, Fascicole 3). It was analyzed and summarized for HPDC experts by CASTMAN experts with the help of LLM AI such as Gemini, ChatGPT, and Grok.
![Fig. 1. The microstructures: dendritic (left) and globular (right) of an aluminum alloy [2]](https://castman.co.kr/wp-content/uploads/image-2700.webp)
Keywords
- Primary Keyword: Semisolid Metal Processing
- Secondary Keywords: Rheo-casting, Thixo-forming, Thixotropy, Globular Microstructure, NRC-p process, Metallic Alloy Processing
Executive Summary
- The Challenge: While semisolid metal processing offers superior part quality and lower energy consumption than traditional methods, established routes like thixo-forming involve multiple, energy-intensive steps such as ingot casting and reheating.
- The Method: The paper reviews established semisolid processes and introduces a new, streamlined rheo-casting method, designated "NRC-p". This method integrates alloy feeding, mechanical agitation (vibration), and forming into a continuous operation.
- The Key Breakthrough: The NRC-p process eliminates the need to separately cast, cut, and reheat billets. By directly feeding the agitated, semisolid alloy into the forming die, it removes operations that "consume much energy and time."
- The Bottom Line: This research points toward a more efficient and economical pathway for semisolid processing, reducing operational complexity and cost without compromising the benefits of forming in a semisolid state.
The Challenge: Why This Research Matters for HPDC Professionals
For decades, the metallurgical industry has pursued two major aims: developing new materials with better performance and finding new processing methods to produce high-quality parts at lower costs. Semisolid metal processing, born from a discovery at MIT in the 1970s, has long been a promising solution.
Compared to conventional liquid-state casting or solid-state forging, semisolid techniques offer significant advantages. Because the material's heat content is lower than that of liquid metal, tool wear is reduced and processing speeds can be higher. The controllable, high viscosity of the semisolid slurry allows for the production of complex, thin-walled parts with fine micro-granulation, low segregation, and excellent surface quality. This approach can lower energy consumption by an estimated 35-40% compared to conventional processing. However, realizing these benefits often requires a multi-stage process that can be complex and costly. This paper directly addresses the need for a more efficient method.
The Approach: Unpacking the Methodology
The paper first outlines the two dominant routes for semisolid processing, which rely on the principle of thixotropy: the property of a material to become fluid when stirred or agitated and return to a gel-like state when at rest. To achieve this, the alloy's microstructure must be transformed from a rigid, dendritic (tree-like) structure to one where spherical (globular) solid particles are suspended in a liquid phase (Figure 1).
The study reviews two conventional approaches:
- Thixo-forming: This well-established route involves multiple stages, as shown in Figure 2. It begins with casting special ingots (a), cutting them into semi-finished slugs (b), reheating the slugs to the precise semisolid temperature (c), and finally forming them in a closed die (thixo-casting, d₂) or an open die (thixo-forging, d₁).
- New Rheo-casting (NRC): This process, detailed in Figure 4, involves pouring a molten alloy into a specially designed crucible (b), controlling the cooling to form a solid skeleton, reheating the resulting slug for temperature homogenization (c), and then transferring it to a casting machine for forming (e).
The paper then proposes a new method of the rheo-casting process (NRC-p), which is the core of its contribution. As shown in Figure 5, this method simplifies the entire workflow by integrating key steps.
The Breakthrough: Key Findings & Data
The central innovation presented is the NRC-p method, which aims to maximize efficiency by eliminating redundant steps.
- Finding 1: Process Simplification: The most significant advantage of the NRC-p method is the elimination of "pouring into the crucible and reheating for the homogenization of the temperature of the ingot." This removes two distinct operations that consume significant energy and time in traditional thixo-forming and NRC processes.
- Finding 2: Integrated Agitation: As illustrated in Figure 5, the NRC-p process introduces mechanical agitation via vibrations during the alimentation of the mould (b) and the forming stage (c). This continuous agitation is critical for creating the necessary flow behavior and ensuring the material fills the die cavity completely.
- Finding 3: Enhanced Forming Dynamics: The paper posits that applying vibrations during forming positively influences "the flow geometry, the friction between material and work tools and the physical – mechanical characteristics of the pieces." The final forming is achieved by applying mechanical pressure with a punch or top die to ensure complete die filling and plastic deformation.
Practical Implications for HPDC Products
This research, while conceptual, offers a clear vision for a more streamlined and cost-effective future for semisolid manufacturing.
- For Process Engineers: The NRC-p concept suggests a pathway to a leaner manufacturing line. By eliminating the need for dedicated ingot reheating furnaces and the associated handling robotics, factories could reduce their footprint, lower capital expenditure, and drastically shorten the overall production cycle time.
- For Quality Control: The paper's emphasis on mechanical vibration as the means to control microstructure and flow reinforces the importance of process control. The consistency of the final part's mechanical properties is directly tied to the ability to precisely manage the agitation and forming parameters, as suggested by the research from a "collective from Faculty of Engineering Hunedoara" [6, 7].
- For Die Design & R&D: The principle of forming under vibration opens new avenues for producing highly complex components that are difficult to make with other methods. This suggests that future die designs could incorporate integrated vibration systems to enhance the flow of semisolid slurry into thin walls and intricate features, pushing the boundaries of what is possible in net-shape manufacturing.
Paper Details
ASPECTS CONCERNING THE PROCESSING METHODS OF METALLIC ALLOYS IN THE SEMISOLID STATE
1. Overview:
- Title: ASPECTS CONCERNING THE PROCESSING METHODS OF METALLIC ALLOYS IN THE SEMISOLID STATE
- Author: CIOATĂ Vasile George
- Year of publication: 2005
- Journal/academic society of publication: ANNALS OF THE FACULTY OF ENGINEERING HUNEDOARA
- Keywords: semisolid state, thixotropy, thixo-forming, rheo-casting
2. Abstract:
The paper shows some particularities of the die forging in semisolid state of the metallic materials, points out the advantages of using this process for producing the pieces and present a new method of semisolid processing in the semisolid state. Through this method, that is a variant of the Rheo-casting process, is eliminated the operations of pouring into the crucible and reheating for the homogenization of the temperature of the ingot, operations that consumes much energy and time.
3. Introduction:
The development and the realization of new materials, with better property and performances and with lower costs, and finding of new methods of processing, mixed or unconventional, that permit the obtained of the parts with highly mechanics characteristics, at low prices, constitute two the major aims of the metallurgical industry and of the materials processing. Relative new classes of the forming technologies, which realize these qualities, are the techniques of processing materials in the semisolid state. Based on the student discovery from Massachusetts Institute of Technology (MIT), in the 70 years, these techniques of processing were used-up first in SUA. Today, efforts for the development and implementation of these done on entire world because these offers many advantages as comparing to the conventional processing methods (casting in liquid state and forging, die-forging, stamping in solid state), advantages that come out of the behavior and characteristics of the materials in semisolid state. So, due to the heat content, lower than that of the liquid metal, high processing speeds can be applied, the wear of the deformation tools being lower. The presence of the solid during the filling of the die and the controllable viscosity, that is higher than that of the liquid metals, makes possible to reach parts with low blister cavities, with low macro and micro-segregation and with a fine micro-granulation structure. The gas capitation is also low, and the parts have an excellent surface quality. The materials in semi-liquid state have lower flow resistance than the material in solid state, which is why parts having complicated configuration and thin walls can be produced. The energetic consumption is lowered by approximate 35…40% as comparing to the conventional processing.
4. Summary of the study:
Background of the research topic:
The paper explores processing methods for metallic alloys in the semisolid state, a technology known for creating high-quality parts with significant advantages over traditional casting and forging.
Status of previous research:
The paper acknowledges two primary development routes: the thixo-forming route and the rheo-casting route. Thixo-forming is described as a multi-stage process involving ingot casting, cutting, reheating, and forming (Figure 2). Rheo-casting is presented as an alternative, with the paper specifically mentioning the New Rheo-casting (NRC) process developed in 1996 as an example (Figure 4).
Purpose of the study:
The purpose is to present a "new method of processing in the semisolid state" called NRC-p. This method is proposed as a more efficient variant of the rheo-casting process, designed to eliminate time- and energy-consuming steps.
Core study:
The core of the study is the proposal of the NRC-p method (Figure 5). This method consists of four stages: a) alloy elaboration, b) alimentation of the mould with alloy combined with mechanical agitation through vibrations, c) forming the part under pressure while vibrations continue, and d) obtaining the finished part. The key innovation is the elimination of the separate ingot creation and reheating steps common to other methods.
5. Research Methodology
Research Design:
The paper presents a conceptual study. It reviews existing semisolid processing methods (Thixo-forming, NRC) and proposes a new, improved method (NRC-p). The methodology is presented through schematic diagrams and descriptive text.
Data Collection and Analysis Methods:
The paper does not involve empirical data collection. It analyzes and compares different process workflows based on their constituent steps, energy consumption, and operational efficiency, drawing upon existing scientific literature and patents [1-7].
Research Topics and Scope:
The research topic is the process-level innovation in semisolid metal forming. The scope is limited to a high-level, schematic comparison of thixo-forming, the NRC process, and the newly proposed NRC-p method, focusing on the advantages of the latter.
6. Key Results:
Key Results:
- Semisolid processing is based on thixotropy, requiring a globular microstructure where solid particles are covered in a liquid phase (Figure 1).
- The proposed new rheo-casting method (NRC-p) is composed of alloy elaboration, feeding the mould with the alloy under mechanical vibration, and forming the part under pressure and vibration (Figure 5).
- The primary benefit of the NRC-p method is the elimination of the "operations of pouring into the crucible and reheating for the homogenization of the temperature of the ingot," which saves significant energy and time.
- The use of vibrations during forming is stated to positively influence flow geometry, reduce friction, and improve the physical-mechanical characteristics of the final parts.
Figure Name List:
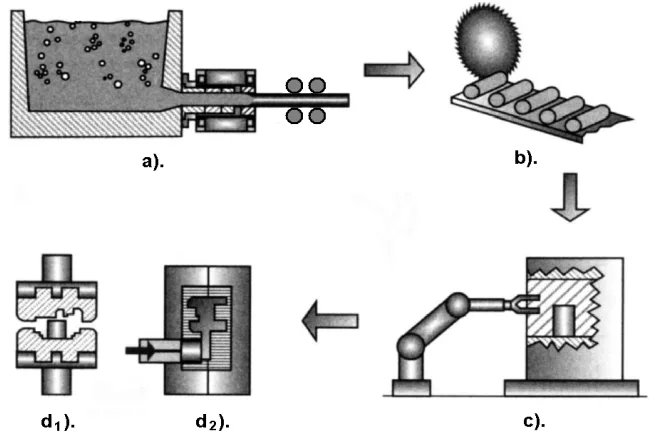
![Fig. 3. Material in the semisolid state, cuted whit the knife [2]](https://castman.co.kr/wp-content/uploads/image-2702.webp)
![Fig. 4. The scheme of the New Rheo-casing Process (NRC) [5]](https://castman.co.kr/wp-content/uploads/image-2703.webp)
- Fig. 1. The microstructures: dendritic (left) and globular (right) of an aluminum alloy [2]
- Fig. 2. The scheme of the thixo-forming process [3]
- Fig. 3. Material in the semisolid state, cuted whit the knife [2]
- Fig. 4. The scheme of the New Rheo-casing Process (NRC) [5]
- Fig. 5. The scheme of the new Rheo-casting method (NRC-p) a) alloy elaboration, b) alimentation of the mould with alloy and the mechanical agitation through vibrations; c) forming in presence of the vibrations; d) finite part
7. Conclusion:
The paper proposes a new method of processing in the semisolid state, termed NRC-p, which is a variant of the Rheo-casting process. This method streamlines production by eliminating the energy- and time-intensive operations of pouring into a crucible and reheating an ingot for temperature homogenization. The method leverages the benefits of plastic deformation in the presence of vibration to positively influence material flow, friction, and the final physical-mechanical properties of the parts. The forming is achieved by applying mechanical pressure via a punch or top die to fill the die cavity.
8. References:
- [1.] FLOREA, J., s.a., Dinamica fluidelor polifazice si aplicatiile ei tehnice, Ed. Tehnica, Bucuresti, 1987, p. 62-64
- [2.] SPENCER, S. B., Rheological behavior of Sn-15 Pct Pb in the cristallization range, Metallurgical Transactions 3, 1972, p. 1925-1932
- [3.] GULLO, G. C., Thixotrope Formgebung von Leichtmetallen - Neue Legierungen und Konzepte, Diss. ETH-Zürich, 2001
- [4.] KENNY, M. P., s.a., Metals Handbook, volum 15, American Society for Metals, 1988, p. 327-338
- [5.] FLEMINGS, M. C., s.a., Behavior of metal alloys in the semi-solid state, Metallurgical Transaction A, 22A, 1991, p. 957-981
- [6.] ILCA, I., CIOATA, V. G., Cerere de brevet cu nr. A/00529/2004 pentru inventia cu titlul "Procedeu si instalatie de obtinere a pieselor prin matritare din materiale metalice semilichide", 2004
- [7.] CIOATA, V. G., Studii si cercetari privind matritarea metalelor si aliajelor in stare semilichida, Teza de doctorat, Universitatea Politehnica Timisoara, 2004
Expert Q&A: Your Top Questions Answered
Q1: What is the main difference between traditional thixo-forming and the proposed NRC-p method?
A1: The main difference is process simplification. Thixo-forming, as shown in Figure 2, requires pre-casting an ingot, cutting it, and reheating it before forming. The NRC-p method, detailed in Figure 5, eliminates these intermediate steps by feeding the agitated, semisolid alloy directly into the forming die, saving considerable energy and time.
Q2: How does semisolid processing improve part quality compared to conventional casting?
A2: According to the paper's introduction, the semisolid process allows for the creation of parts with "low blister cavities, with low macro and micro-segregation and with a fine micro-granulation structure." The high, controllable viscosity also helps achieve "excellent surface quality."
Q3: What is the key mechanism that allows semisolid material to flow like a liquid?
A3: The mechanism is thixotropy. When the material is agitated or stirred, the robust skeleton of solid particles is disrupted, allowing the now "isolated globular particles [to] float in the viscous melt," resulting in a much lower viscosity. When the agitation stops, the network of particles reforms, and the material behaves like a solid again.
Q4: The paper mentions energy consumption is lowered by 35-40%. Where do these savings come from?
A4: The introduction attributes these savings to the fact that the material's heat content is lower than that of fully liquid metal. Furthermore, the proposed NRC-p method adds to these savings by completely eliminating the reheating step required in other semisolid processes, which "consumes much energy and time."
Q5: Why is the "globular" microstructure shown in Figure 1 so important?
A5: The paper states that to achieve thixotropic behavior, the solid phase must be made of "spherical (globular) particles covered in liquid phase." This special microstructure, achieved through stirring during solidification, is fundamental to enabling the semisolid process and all its associated benefits.
Q6: What is the primary advantage of the proposed NRC-p method?
A6: The primary advantage, as stated explicitly in the paper, is that it "eliminated the operations of pouring into the crucible and reheating for the homogenization of the temperature of the ingot, operations that consumes much energy and time."
Conclusion & Next Steps
This research provides a valuable roadmap for enhancing efficiency in semisolid metal processing. The findings offer a clear, data-driven path toward improving quality, reducing defects, and optimizing production by simplifying the manufacturing workflow. The proposed NRC-p method presents a compelling vision for a leaner, more cost-effective approach to producing high-performance components.
At CASTMAN, we are dedicated to applying the latest industry research to solve our customers' most challenging die casting problems. If the issues discussed in this paper resonate with your operational goals, contact our engineering team to discuss how we can help you implement these advanced principles in your components.
Copyright
- This material is a paper by "CIOATĂ Vasile George". Based on "ASPECTS CONCERNING THE PROCESSING METHODS OF METALLIC ALLOYS IN THE SEMISOLID STATE".
- Source of the paper: The original paper was published in "ANNALS OF THE FACULTY OF ENGINEERING HUNEDOARA" (2005, Tome III, Fascicole 3).
This material is for informational purposes only. Unauthorized commercial use is prohibited. Copyright © 2025 CASTMAN. All rights reserved.