This article introduces the paper "SPH: A NEW WAY OF MODELLING HIGH PRESSURE DIE CASTING," presented at the Third International Conference on CFD in the Minerals and Process Industries in 2003. This paper explores the application of Smoothed Particle Hydrodynamics (SPH) for simulating the complex fluid dynamics of High Pressure Die Casting (HPDC).
1. Overview:
- Title: SPH: A NEW WAY OF MODELLING HIGH PRESSURE DIE CASTING
- Author(s): Paul W. CLEARY, Joseph HA, Mahesh PRAKASH and Thang NGUYEN
- Publication Year: January 2003
- Publishing Journal/Academic Society: Third International Conference on CFD in the Minerals and Process Industries, CSIRO, Melbourne, Australia, 10-12 December 2003.
- Keywords: High Pressure Die Casting (HPDC), Smoothed Particle Hydrodynamics (SPH), Lagrangian method, free surface flow, fragmentation, splashing, automotive components, isothermal simulation, thermal/solidification simulation, porosity prediction, die filling.
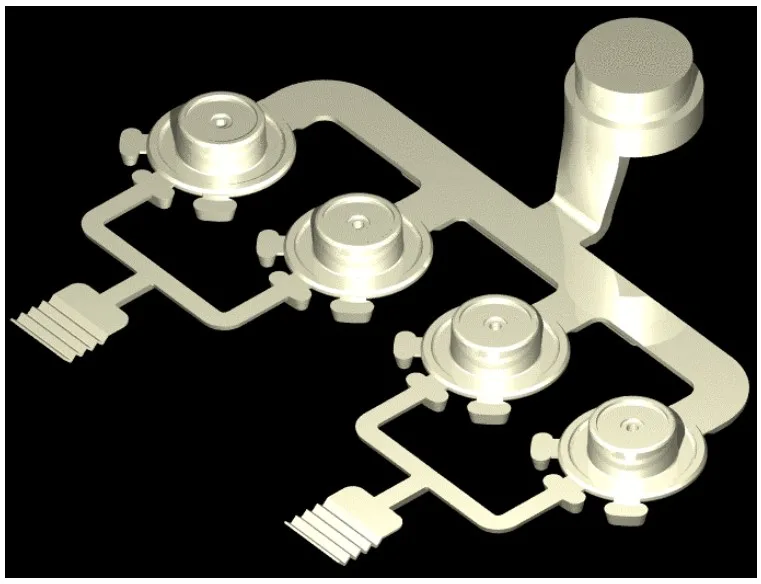
2. Research Background:
- Social/Academic Context of the Research Topic: High Pressure Die Casting (HPDC) is a crucial manufacturing process for producing high-volume, low-cost automotive components. The process involves complex three-dimensional fluid flows at high speeds within intricate die geometries. Understanding and optimizing this process is vital for improving product quality and manufacturing efficiency in the automotive industry.
- Limitations of Existing Research: Traditional methods for modeling fluid flow may struggle with the significant free surface deformation, fragmentation, and splashing inherent in HPDC. Fixed-grid methods can face challenges in accurately capturing the complex and rapidly changing fluid interfaces and handling momentum-dominated flows effectively.
- Necessity of the Research: Numerical simulation offers a powerful and cost-effective approach to study and optimize die designs and filling processes in HPDC. Accurate simulation tools are needed to predict filling patterns, identify potential porosity locations, and ultimately enhance product quality and process productivity. This research addresses the need for a robust simulation technique capable of handling the complexities of HPDC.
3. Research Purpose and Research Questions:
- Research Purpose: The primary purpose of this research is to investigate and demonstrate the effectiveness of Smoothed Particle Hydrodynamics (SPH) as a novel Lagrangian simulation technique for modeling High Pressure Die Casting (HPDC) processes. The study aims to showcase SPH's capability to accurately predict the intricate fluid flow behaviors, including free surface phenomena, within complex die geometries relevant to automotive component manufacturing.
- Key Research Questions:
- Can SPH accurately model the complex three-dimensional fluid flow characteristics of HPDC, including significant free surface fragmentation and splashing?
- Is SPH capable of providing detailed predictions of die filling patterns for complex automotive components, offering insights into the order of fill and potential sites for porosity formation?
- Can SPH simulations be validated against experimental observations and other numerical methods to confirm its accuracy and reliability in the context of HPDC?
- Can SPH be extended to incorporate thermal effects and solidification phenomena relevant to HPDC, enabling the prediction of temperature distributions and solidification patterns during the casting process?
4. Research Methodology:
- Research Design: The research employs a computational simulation-based approach using Smoothed Particle Hydrodynamics (SPH). The study involves simulating the HPDC process for several automotive components with varying geometric complexities. Validation is performed through qualitative comparisons with experimental data, including water analogue experiments, short shot experiments, and comparisons with simulations from other software (Magmasoft).
- Data Collection Method: Data is collected through SPH simulations of die filling for various automotive components. These simulations generate detailed information on fluid flow patterns, velocity fields, temperature distributions (for thermal simulations), and viscosity variations. The filling patterns are visualized and analyzed at different time steps to understand the progression of the fluid front and identify potential issues like void formation.
- Analysis Method: The analysis is primarily qualitative, focusing on visual assessment of the simulated filling patterns and their agreement with experimental observations and manufacturer-reported porosity locations. The simulated fluid front progression, fragmentation, splashing, and void formation are examined in detail. Comparisons are made between SPH simulation results and:
- Water Analogue Experiments: For a front servo piston, SPH predictions were compared to water analogue experiments to validate the fill pattern.
- Magmasoft Simulations: For the front servo piston, a comparison was also made with simulations from Magmasoft, a commercial casting simulation software.
- Manufacturer Porosity Maps: Predicted last-to-fill locations from SPH simulations are compared with porosity maps provided by component manufacturers to assess the correlation between simulation predictions and real-world casting defects.
- Short Shot Experiments: For a simple coaster geometry, SPH simulations incorporating heat transfer and solidification were compared with experimental short shot castings to validate the thermal and solidification models.
- Research Subjects and Scope: The research focuses on simulating the HPDC process for a range of automotive components, representing varying levels of geometric complexity and industrial relevance. The components studied include:
- Front Servo Piston: A relatively simple, axially symmetric component used for initial validation.
- Steering Column Components: Components with more complex cylindrical structures and intricate runner systems.
- Engine Rocker Cover: A large, thin-walled component with complex stepped contours and a tangential runner system.
- Cross Member: A topologically complex component with strengthening ribs, cut-outs, and multiple gates.
- Coaster: A simple square shape used for coupled heat transfer and solidification studies and short shot validation.
The simulations encompass both isothermal fluid flow and coupled heat transfer/solidification scenarios to evaluate SPH's capabilities in modeling different aspects of the HPDC process.
5. Main Research Results:
- Key Research Results:
- Detailed Free Surface Prediction: SPH simulations demonstrated "unprecedented detail in the fluid free surfaces, particularly in the extent of fragmentation and void formation." This highlights SPH's strength in capturing the complex free surface dynamics inherent in HPDC.
- Validation of Isothermal Predictions: Validation against water analogue experiments and Magmasoft solutions for the front servo piston showed good agreement, confirming the accuracy of SPH for isothermal flow modeling in HPDC.
- Validation of Thermal/Solidification Predictions: Comparison with short shot experiments for the coaster validated the coupled thermal/solidification models within SPH, demonstrating its ability to predict solidification patterns and cold shut phenomena.
- Predictive Accuracy for Automotive Components: SPH simulations for various automotive components (front servo piston, rocker cover, steering column, cross member) provided filling patterns that correlated well with porosity/voidage observations reported by manufacturers. The simulations effectively identified last-to-fill locations, which are often prone to porosity.
- Computational Feasibility: The research demonstrated that "both isothermal and thermal simulations can be performed in reasonable computation times for large scale automotive castings," indicating the practical applicability of SPH for industrial HPDC simulation.
- Statistical/Qualitative Analysis Results: The analysis was primarily qualitative, focusing on visual comparisons. The paper states that observations from SPH simulations were "consistent with the porosity map supplied by the manufacturer" for the front servo piston and "these observations are consistent with observations made by the manufacturer" for the rack and pinion steering column and rocker cover. For the coaster short shot, "The predicted front profile is in very good agreement with the experiment." These qualitative assessments indicate a strong correlation between SPH predictions and real-world observations.
- Data Interpretation: The results strongly suggest that SPH is a highly effective and accurate method for modeling HPDC processes. Its Lagrangian nature and ability to handle complex free surfaces, fragmentation, and splashing make it particularly well-suited for simulating the challenging fluid dynamics of HPDC. The validation studies further reinforce the reliability of SPH for both isothermal and thermal/solidification simulations in this context. The detailed filling pattern predictions offer valuable insights for die design optimization and porosity reduction.
- Figure Name List:
- Figure 1: Geometry of front servo piston.
- Figure 2: Filling of front servo piston at selected times.
- Figure 3: Geometry of rocker cover.
- Figure 4: Filling of rocker cover at selected times.
- Figure 5: Geometry of steering column.
- Figure 6: Filling of steering column at selected times.
- Figure 7: Geometry of cross member.
- Figure 8: Filling of cross member at selected times.
- Figure 9: Geometry of coaster.
- Figure 10: Filling of coaster with fluid coloured by temperature.
- Figure 11: Filling of coaster with fluid coloured by viscosity.
- Figure 12: Short shot: experiment (left), simulation (right).
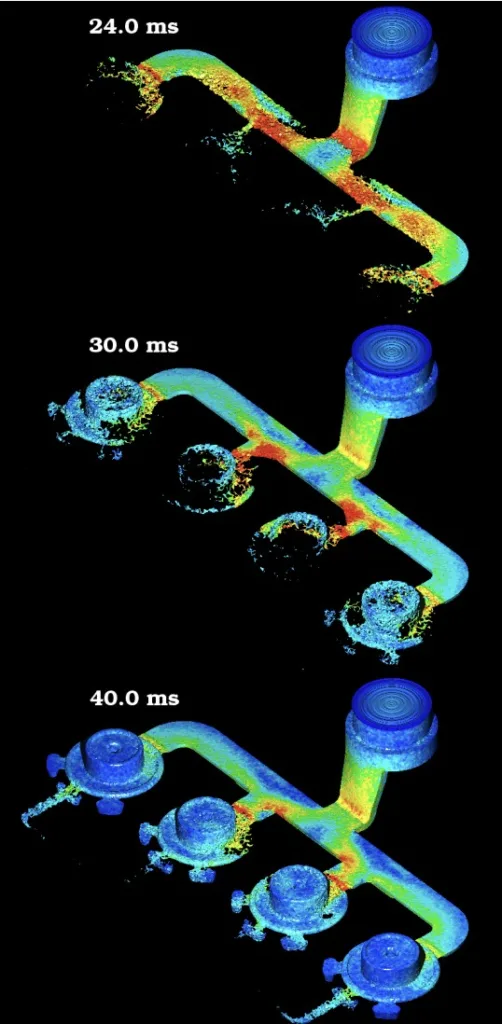
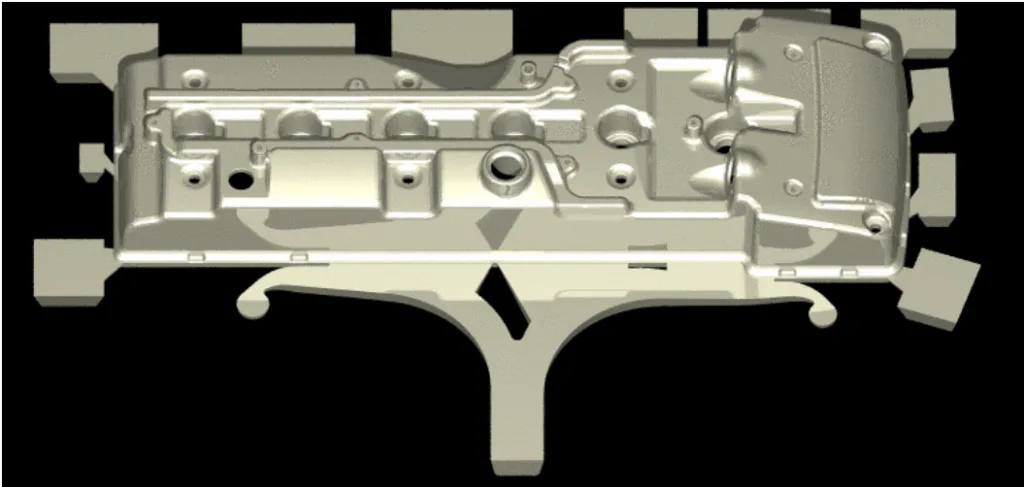
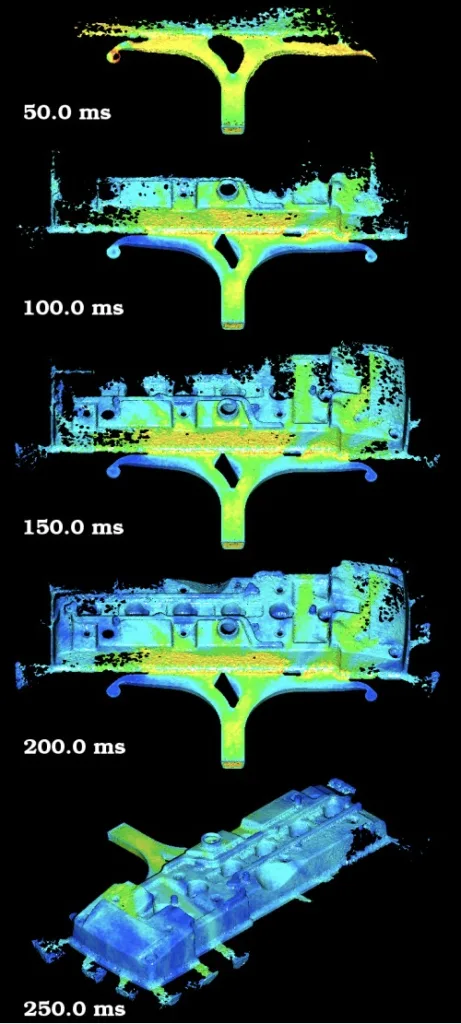

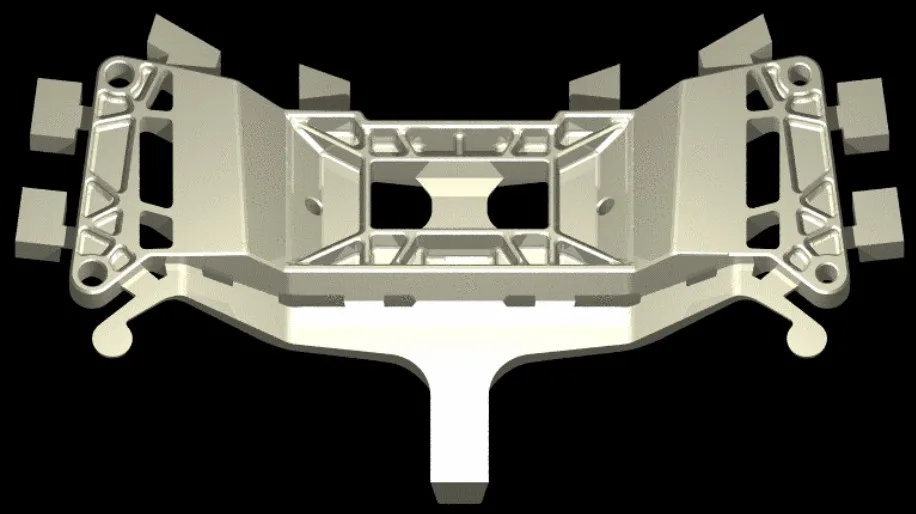

6. Conclusion and Discussion:
- Summary of Main Results: This research successfully demonstrated the application of Smoothed Particle Hydrodynamics (SPH) for simulating High Pressure Die Casting (HPDC) of automotive components. SPH simulations provided detailed and visually compelling predictions of die filling patterns, capturing complex free surface phenomena like fragmentation and splashing. Validation studies, including comparisons with water analogue experiments, Magmasoft simulations, manufacturer porosity maps, and short shot experiments, confirmed the accuracy and reliability of SPH for both isothermal and thermal/solidification modeling in HPDC. The simulations effectively identified potential porosity locations and provided insights into the influence of heat transfer and solidification on the filling process.
- Academic Significance of the Research: The study contributes to the field of computational fluid dynamics and materials processing by showcasing SPH as a viable and powerful Lagrangian method for simulating complex industrial flows like HPDC. It highlights the advantages of SPH in handling free surface flows and momentum-dominated scenarios, offering an alternative and potentially superior approach compared to traditional grid-based methods for certain applications.
- Practical Implications: The findings have significant practical implications for the die casting industry. SPH simulations can be used as a valuable tool for:
- Optimizing Die Design: By visualizing filling patterns and identifying potential porosity locations, SPH simulations can guide the design of gating systems, runner systems, and die geometries to promote more uniform filling and reduce defects.
- Improving Process Control: Understanding the influence of process parameters on filling patterns through SPH simulations can help optimize process settings for improved product quality and process efficiency.
- Reducing Product Development Time and Costs: Numerical simulation with SPH can reduce the need for costly and time-consuming physical prototyping and experimentation in die design and process development.
- Limitations of the Research: While the paper demonstrates the effectiveness of SPH, it does not explicitly discuss limitations. Implicit limitations might include:
- Computational Cost: While stated as "reasonable," the computational cost for very large and complex simulations could still be a factor.
- Parameter Sensitivity: SPH models may have parameters that require careful tuning and validation for different materials and process conditions.
- Model Complexity: Further development and validation may be needed to incorporate more complex physical models, such as turbulence, detailed solidification kinetics, and multi-phase flow effects, for even greater accuracy in specific HPDC scenarios.
7. Future Follow-up Research:
- Directions for Follow-up Research: Future research could focus on:
- Expanding Material Models: Incorporating more sophisticated material models to account for alloy-specific properties, non-Newtonian fluid behavior, and more detailed solidification physics.
- Die Thermal Management: Developing more comprehensive models for die thermal behavior, including heat transfer within the die, cooling channel effects, and die distortion.
- Process Optimization Studies: Using SPH simulations to systematically investigate the impact of various process parameters (injection speed, pressure, melt temperature, die temperature) on filling patterns and casting quality, leading to optimized process windows.
- Turbulence Modeling: Integrating turbulence models within the SPH framework to improve the accuracy of simulations for highly turbulent flows in HPDC.
- Multi-Phase Flow: Extending SPH to model multi-phase flow phenomena, such as air entrapment and gas porosity formation, in more detail.
- Areas Requiring Further Exploration:
- Computational Efficiency: Further optimization of SPH algorithms and implementation to enhance computational efficiency and enable simulations of even larger and more complex HPDC systems.
- Experimental Validation: Conducting more extensive and quantitative experimental validation studies, including detailed measurements of filling patterns, temperature distributions, and porosity levels, to further refine and validate SPH models.
- Integration with Industry Workflows: Developing user-friendly SPH-based simulation tools and workflows that can be readily integrated into industrial die design and process optimization processes.
8. References:
- CLEARY, P.W. (1998). Modelling confined multi-material heat and mass flows using SPH. Applied Mathematical Modelling, 22, 981–993.
- CLEARY, P.W., HA, J., & AHUJA, V. (2000). High pressure die casting simulation using smoothed particle hydrodynamics. Int. J. Cast Metals Res, 12, 335-355.
- CLEARY, P.W., HA, J., MOONEY, J., & AHUJA, V. (1998). Effect of heat transfer and solidification on high pressure die casting, Proc. 13th Australasian Fluid Mechanics Conference, Melbourne, Australia, 679-682.
- CLEARY, P.W. & MONAGHAN, J.J. (1999). Conduction modelling using smoothed particle hydrodynamics. J. Comp. Phys., 148, 227-264.
- HA, J. AND CLEARY, P.W. (2000). Comparison of SPH simulations of high pressure die casting with the experiments and VOF simulations of Schmid and Klein. Int. J. Cast Metals Res, 12, 409-418.
- HA, J., CLEARY, P. W., ALGUINE, V. AND NGUYEN, T. (1999). Simulation of die filling in gravity die casting using SPH and MAGMAsoft, Proc. 2nd Int. Conf. on CFD in Minerals & Process Industries, Melbourne, Australia, 423-428.
- HA, J., CLEARY, P. W., PRAKASH, M., ALGUINE, V., NGUYEN, T. AND SCOTT, C. (2003). SPH, MAGMAsoft and water analogue modellings of die filling of a servo piston, Proc. 3rd Int. Conf. on CFD in Minerals & Process Industries, Melbourne, Australia.
- HULTMAN, J. AND KALLANDER, D. (1997). An SPH code for galaxy formation problems: presentation of the code, Astron. Astrophys., 324, 534-548.
- MONAGHAN, J.J. (1992). Smoothed particle hydrodynamics. Ann. Rev. Astron. Astrophys., 30, 543-574.
- MONAGHAN, J.J. (1994). Simulating free surface flows with SPH. J. Comp. Phys., 110, 399-406.
- SWEGLE, J.W. AND ATTAWAY, S.W. (1995). On the feasibility of using smoothed particle hydrodynamic for underwater explosion calculations, Comput. Mechanics, 17, 151.
- TAKEDA, H., MIYAMA, S.M. AND SEKIYA, M. (1994). Numerical simulation of viscous flow by smoothed particle hydrodynamics, Prog. Theoretical Physics, 92, 939-960.
9. Copyright:
*This material is Paul W. Cleary, Joseph Ha, Mahesh Prakash and Thang Nguyen's paper: Based on SPH: A NEW WAY OF MODELLING HIGH PRESSURE DIE CASTING.
*Paper Source: https://www.researchgate.net/publication/237473743
This material was summarized based on the above paper, and unauthorized use for commercial purposes is prohibited.
Copyright © 2025 CASTMAN. All rights reserved.