This introduction paper is based on the paper "Selective laser melting aluminum alloys for automotive component" published by "Politecnico di Torino (Master of Science Thesis)".
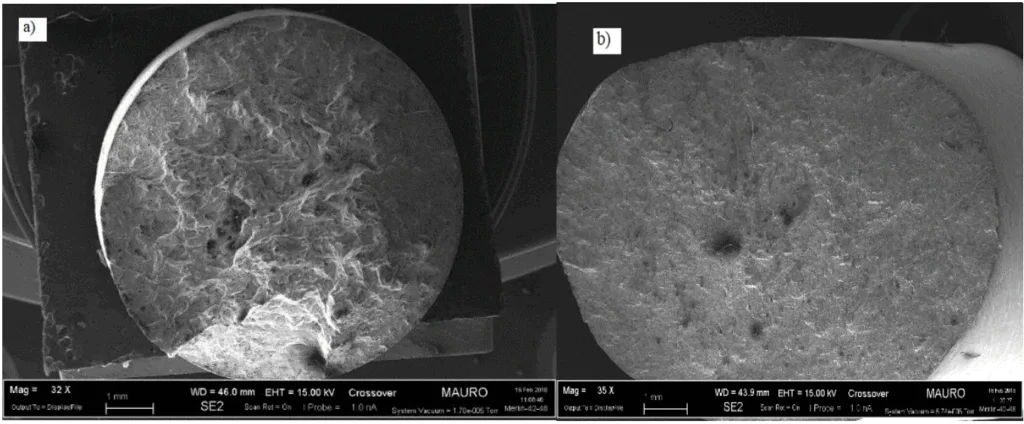
1. Overview:
- Title: Selective laser melting aluminum alloys for automotive component
- Author: Giulia Di Matteo
- Year of publication: 2018
- Journal/academic society of publication: Politecnico di Torino (Master of Science Thesis)
- Keywords: Selective Laser Melting (SLM), Additive Manufacturing, AlSi10Mg, aluminum alloys, automotive components, microstructure, mechanical properties, anisotropy, heat treatment, residual stress, powder characterization. (Keywords inferred from the text as none were explicitly listed).
2. Abstract:
A study on the properties of AlSi10Mg produced by Selective Laser Melting has been carried out both from a mechanical and a morphological point of view. Considering that one of the intrinsic characteristics of the components realized through SLM and in general by additive manufacturing technologies is the high anisotropy, the influence of the different building direction on the characteristics of the finished product has been investigated. Furthermore, the attention has also been focused on comparing the different mechanical proprieties of the materials subjected to heat treatment with respect to those as built and on the influence of the thickness of the powder layer. In this regard, a series of samples in AlSi10Mg alloy were made through SLM process. Samples were realized through four different jobs, one of which differs for the different thickness of the powder layer. The specimens were printed in two different building orientations and the mechanical behavior of the as-built and treated specimens was studied, through tensile test, HB micro-hardness test and Charpy test. The powder through which the specimens were obtained has also been subject of study since the properties of the finished products depend on powder characteristics such as shape, particle size and distribution, composition.
3. Introduction:
Additive Manufacturing (AM) technologies, particularly Selective Laser Melting (SLM), are increasingly integral in industrial sectors like automotive and aeronautics, offering advantages over conventional manufacturing. Key benefits include weight reduction (lower density components, integration of parts eliminating assembly), cost reduction (eliminating design/tooling phases, reduced manpower), and on-demand production (e.g., spare parts). SLM specifically enables high-density (up to 99.9%) metallic components with extremely fine microstructures and complex geometries, often leading to improved mechanical properties compared to conventional processes. However, AM faces limitations such as processing time (speed), potential defects (surface roughness, dimensional accuracy), inherent anisotropy due to layer-by-layer growth, size limitations imposed by machine dimensions, high costs of machines and raw materials, and the need for support structures. While AM, known initially as Rapid Prototyping (RP), has evolved significantly, its application for metal components, especially in the automotive industry, is a more recent development compared to polymers.
4. Summary of the study:
Background of the research topic:
Additive Manufacturing (AM), specifically Selective Laser Melting (SLM), is a growing field for producing high-quality, complex metallic components, particularly relevant for the automotive industry seeking lightweight and high-performance parts. AlSi10Mg is a common casting alloy used in automotive applications, making it a candidate for SLM processing.
Status of previous research:
SLM technology allows fabrication of near-full density AlSi10Mg parts with fine microstructures. However, challenges exist, including process-induced anisotropy (variations in properties based on build direction), potential defects like porosity, and the influence of process parameters (laser power, scan speed, layer thickness, scan strategy) and post-processing (heat treatment) on the final properties. Aluminum alloys specifically present difficulties due to high reflectivity, high thermal conductivity, tendency to oxidize, and powder flowability issues.
Purpose of the study:
This thesis aimed to investigate the mechanical and morphological properties of AlSi10Mg alloy produced by SLM. The study focused on understanding the effects of:
- Building orientation (anisotropy).
- Post-process heat treatment (stress relieving).
- Powder layer thickness.
Core study:
The research involved producing AlSi10Mg samples using an EOS M290 SLM system under different conditions (four distinct "jobs"). Two primary build orientations (Z-axis and XY-plane) were compared. Samples were characterized in both the as-built state and after a stress-relieving heat treatment (300°C for 2 hours). One job utilized a thicker powder layer (0.06 mm vs. 0.03 mm). The starting powder (two batches, A and B) was also characterized. Characterization methods included density and porosity measurements, optical microscopy (OM), scanning electron microscopy (SEM) for microstructure and fracture surface analysis, X-ray diffraction (XRD) for phase identification and residual stress analysis, tensile testing, micro-hardness testing (Brinell), and Charpy impact testing.
5. Research Methodology
Research Design:
The study employed an experimental design comparing AlSi10Mg samples fabricated via SLM under varying conditions. Key variables included:
- Starting powder batch (A and B).
- SLM process parameters (defined by Jobs A, B, C, D using an EOS M290).
- Building orientation (samples built along Z-axis vs. samples built in XY-plane).
- Powder layer thickness (Job C used 0.06 mm, others used 0.03 mm).
- Post-processing heat treatment (as-built vs. stress relief at 300°C for 2h).
Data Collection and Analysis Methods:
- Powder Characterization:
- Flowability: Measured time for 50g to flow through a 2.5mm orifice.
- Tapped Density: Measured using a tapping system (Figure 23) to calculate Compressibility Index (CI) and Hausner Ratio (HR) (Equations 5, 6).
- Particle Size Distribution: LASER PARTICLE SIZER ANALYSETTE 22 NANOTEC (Figure 25), wet dispersion.
- Morphology: Scanning Electron Microscopy (SEM).
- Phase Composition: X-ray Diffraction (XRD).
- Sample Characterization:
- Density and Porosity: Archimedes’ balance (Figure 26), calculated using Equations 6, 7, 8, 9, 10, 11, 13. Samples were mechanically polished first.
- Microstructure: Optical Microscopy (OM) (Leica DMI 5000 M) on polished and etched (Keller's reagent) cross-sections (parallel and perpendicular to build direction). Scanning Electron Microscopy (SEM) (Leo 435VP) for detailed morphology and fracture surface analysis (Figure 32).
- Phase Identification: X-ray Diffraction (XRD) (Panalytical X’PERT PRO PW3040/60, Cu Kα).
- Residual Stress: X-ray Diffraction (XRD) using the sin²ψ method with a GNR Stress X diffractometer (Figure 27), analyzing parallel and perpendicular faces relative to the growth direction (Equations 14-21, Figures 28-31).
- Mechanical Properties:
- Tensile Test: According to UNI EN ISO 6893, using MTS CITERION MODEL 43 and GALDABINI mod. SUN40 machines (Figure 34). Calculation of Rm, Rp, elongation (Equations 22, 23).
- Micro-Hardness Test: Brinell hardness (HB) according to UNI EN 6506-1, using EMCOTEST M5U 300/030 machine (Figure 36) with a 2.5 mm tungsten carbide sphere, 10 N load for 10s (Equations 24, 25, 26). Measured on parallel and perpendicular faces.
- Charpy Impact Test: According to ASTM E 23, using notched samples (Figure 37).
Research Topics and Scope:
The research focused on SLM processing of AlSi10Mg alloy for potential automotive applications. The scope included:
- Characterization of the starting AlSi10Mg powder (EOS supplied, two batches).
- Fabrication of test specimens using an EOS M290 SLM machine with defined process parameters (Figure 18 / Figure 42).
- Investigation of the influence of building orientation (Z vs. XY, Figure 9, Figure 21) on material properties.
- Evaluation of the effect of a standard stress-relieving heat treatment.
- Assessment of the impact of increased powder layer thickness (Job C).
- Comprehensive characterization of the produced samples' density, porosity, microstructure, phase composition, residual stress, and mechanical properties (tensile, hardness, impact toughness).
6. Key Results:
Key Results:
- Powder: Two batches (A and B) were used. Both showed roughly spherical morphology typical of gas atomization, with some satellites/agglomerates (Figure 38). Average particle size was ~27 μm for both. Powder B exhibited better flowability (65sec/50g) and lower Compressibility Index/Hausner Ratio than Powder A (which did not flow), attributed to differences in particle size distribution (Powder B had coarser particles and narrower distribution, Figure 39, Table 6). XRD confirmed Al and Si as the main crystalline phases in virgin powders (Figure 40). Si peak intensity increased in powder collected after the SLM job, suggesting better crystallization due to heat exposure (Figure 41).
- Density & Porosity: All SLM samples showed lower density and higher porosity (1.6-2.1%) compared to EOS datasheet values (~1%) (Table 7). Porosity was particularly evident at melt pool edges, suggesting incomplete consolidation. Neither heat treatment nor increased powder layer thickness significantly affected the overall density or porosity (Figure 43). Pores were generally < 10 μm (Figure 44).
- Microstructure: Samples exhibited a very fine microstructure characteristic of rapid solidification in SLM. Optical micrographs revealed melt pool structures (Figure 43). Sections parallel to the build direction showed layered, half-cylindrical melt pools. Sections perpendicular showed elongated melt pools, likely due to thermal gradients and Marangoni effects (Figure 44). SEM analysis of fracture surfaces showed small (< 2 μm) α-Al grains surrounded by segregated Si at grain boundaries (Figure 55).
- Tensile Properties: Mechanical properties depended strongly on build direction, heat treatment, and powder layer thickness (Figures 45-49, Table 8, Table 9).
- Anisotropy: Z-axis samples showed higher ultimate tensile strength (Rm) but lower yield strength (Rp) and elongation compared to XY-plane samples.
- Heat Treatment: Stress relieving generally decreased Rm (by ~13-20%) and Rp (by ~12-18%) but significantly increased elongation (by ~20% for Job A, up to 70% for Job B Z-axis). The effect was more pronounced for Z-axis samples.
- Layer Thickness: Samples made with thicker layers (Job C) showed much less change in mechanical properties after heat treatment compared to those made with thinner layers.
- Fracture Mechanism: SEM showed inter-domain ductile fracture at low magnification, particularly for Z-samples (separation between melt pools, Figure 52a). At higher magnification, intergranular ductile fracture (micro-void coalescence, dimples) was observed (Figure 53, Figure 55). Heat treatment enhanced Si segregation (and likely Mg2Si formation) at grain boundaries (Figure 57), hindering grain growth but contributing to property changes. Fracture in Z-samples propagated perpendicular to layers (weak interfaces), while in XY-samples it propagated parallel to layers (Figure 51).
- Hardness: Hardness was anisotropic. Faces perpendicular to the growth direction (Z-axis) consistently showed higher HB values than parallel faces (Table 11). This is attributed to the different thermal history: perpendicular faces represent the last solidified layer with rapid cooling, while parallel faces experience prolonged exposure to elevated temperatures during the build, allowing some stress relaxation/softening. Heat treatment did not significantly influence hardness values, suggesting hardness in as-built parts is mainly due to fine microstructure and residual stresses, while Mg2Si precipitation during heat treatment compensates for stress relief. SLM hardness was comparable to or better than standard cast AlSi10Mg, but lower than precipitation-hardened (T6) or high-pressure die-cast and aged material (Table 12).
- Charpy Impact: Clear anisotropy was observed. XY-plane samples absorbed significantly more energy (higher toughness) than Z-axis samples, both as-built and heat-treated (Table 13). This is due to the crack path relative to the layer orientation (Figure 59). Heat treatment substantially increased the absorbed energy (fracture toughness) for both orientations, with a more dramatic increase (approx. 5x) for Z-axis samples.
- Residual Stress: XRD analysis revealed a complex state of compressive and shear stresses on both parallel and perpendicular faces (Figures 60, 61, 63, 64). Higher compressive stresses were measured on the face perpendicular to the growth direction, consistent with hardness results and thermal history. The presence of Si in supersaturated solid solution likely distorted the lattice, affecting the absolute accuracy of stress measurements (d-spacing variation). Heat treatment seemed to have little effect on the compressive/axial stress component but led to a significant reduction in shear stress (Figure 62, 63, 64).
Figure Name List:
- Figure 1 : Comparison between AM costs and conventional methods ones[4]
- Figure 2 : Common metal additive manufacturing process[7]
- Figure 3 : EBM schematic representation
- Figure 4: schematic representation of LPBF process [8]
- Figure 5: schematic representation of SLM process
- Figure 6: scheme of LMD process
- Figure 7: Schematic representation of the SLM process
- Figure 8 The schematic of hatch angle in raster filling patterns
- Figure 9: different building orientation a) z plane b) c) xy plane
- Figure10: solid-liquid system wettability
- Figure11: schematic representation of water atomization process
- Figure 12 : schematic representation of plasma atomization process
- Figure 13 : schematic representation of centrifugal atomization
- Figure 14: schematic representation of gas atomization process
- Figure15: state diagram Al-Si
- Figure 16 : EOS M290 [27] system and its technical data
- Figure 17: Different scanning strategies.
- Figure18 : Eos M290 process parameters
- Figure 20: cubic and parallelepiped samples
- Figure 21: main samples geometries a), d) samples with building orientation along z-axes , b), c) samples with building orientation in x-y plane
- Figure 22: charpy test samples
- Figure 23 : tapping system
- Figure 24 : determination flow character through Hausner ratio e compress index
- FGUR E 25: ANALYSETTE 22 Nanotec
- Figure 26 : Archimede’s balance
- Figure 27 : CRF Metals Lab diffractometer
- Figure 28: Positions of XR source and detector for resisual stress measurements.
- Figure 29 Effect of stress on plane spacing in crystals with different orientation.
- Figure 30 Calculation of residual stress from the slope of the plot
- Figure 31 : inter-planar distance as a function of sin2 ψ a) Regular behavior b) ψ splitting c) Oscillatory -indicating the presence of an inhomogeneous stress/strain state within the material [30]
- Figure32: scheme of SEM
- Figure 33: tensile test sample a) before testing b) after testing
- Figure 34: MTS CITERION MODEL 43 machine
- Figure 35 : principle measurement of the Brinell hardness.
- Figure 36 : Brinnel EMCOTEST M5U 300/030 machine [ 30]
- Figure 37: ASTM E23 Charpy samples
- Figure 38 : SEM image of the two AlSi10Mg powders: A) first batch and B) second batch
- Figure 39 : particle size distribution; A virgin powder and B virgin powder
- Figure 40 : A and B virgin powder spectra
- Figure 41 : XRD spectrum of powder A: a) comparison among virgin powder, powder collected after DMLS job and as residual coming from nozzle; b) zoom on Si peak.
- Figure 42: jobs process parameters
- Figure 43: Job A as built and heat treated samples micrographs (magnification 50 x): on the left is presented the section parallel to the building direction, on the right the perpendicular one.
- Figure 44 :Typical microstructure morphology of Laser Melted parts: on the left the section parallel to the building direction (Z axis); on the right the section perpendicular to the building direction( Z axis)
- Figure 45 : Job A, Z samples as built and heat treated ,Stress-strain curves.
- Figure 46: Job A, XY samples as built and heat treated ,Stress-strain curves.
- Figure 47: Job B, Z samples as built and heat treated ,Stress-strain curves.
- Figure 48: Job B, XY samples as built and heat treated ,Stress-strain curves.
- Figure 49: Job C, XY samples as built and heat treated ,Stress-strain curves
- Figure 50: a) Z samples fracture surface b) XY samples fracture surface
- Figure 51 : Schematic representation of interactions between building orientation and the stress direction : a) Z samples b) XY samples
- Figure 52 : a) as built Z samples fracture surface (100x) b) as built XY samples fracture surface higher magnitude (100X)
- Figure 53 : as built Z sample fracture surface magnitude 1,50K,x
- Figure 54 : Al-Si phase diagram
- Figure 55 :Fracture surface os Z samples at high magnification: aluminum grains smaller than 2 µm with silicon segregation at the grain boundaries.
- Figure 56 :heat treated Z samples inter-domain fracture surfaces different magnitude
- Figure 57: Enhanced segregation at grain boundaries of silicon that hinders the aluminium grain growth during the heat treatment.
- Figure 58 :heat treated XY samples fracture surfaces, different magnifications
- Figure 59 : cross section of Charpy samples ,different layers orientation with respect to V notch for samples built along Z axis and on XY plane
- Figure 60: residual stress analysis on the perpendicular face of the as built sample
- Figure 61: residual stress analysis on the parallel face of the as built sample
- Figure 62: Temperature gradient influences on the formation of residual stress
- Figure 63: residual stress analysis on the perpendicular face of the heat treated sample
- Figure 64: residual stress analysis on the parallel face of the heat treated sample
7. Conclusion:
Specimens of AlSi10Mg alloy were produced via Laser Beam Melting (SLM) technology and characterized. Key conclusions are:
- All samples exhibited lower density and higher porosity than producer (EOS) datasheet values, likely due to incomplete consolidation at melt pool edges. Final density and porosity were not significantly affected by heat treatment or powder layer thickness.
- Tensile tests confirmed mechanical properties depend on growth direction, heat treatment, and powder layer thickness. Z-axis samples showed higher tensile strength but lower yield strength and elongation than XY-plane samples. Stress relieving heat treatment primarily increased elongation and decreased strength, especially for Z-axis samples. Thicker powder layers reduced the impact of heat treatment.
- Electron microscopy revealed a microstructure of very small aluminum grains surrounded by silicon segregated at grain boundaries. Fracture occurred via inter-domain and intergranular ductile mechanisms. Heat treatment enhanced silicon segregation, preventing significant grain growth.
- Material anisotropy affected hardness and fracture work. Hardness was higher on faces perpendicular to the growth direction due to different thermal histories. Stress relieving did not significantly change hardness. Fracture work (Charpy) was higher for XY-plane samples and increased significantly after heat treatment, particularly for Z-axis samples.
- Residual stress analysis showed a complex state of compression and shear stress, higher on the face perpendicular to the growth direction. The presence of silicon in solid solution affected stress evaluation accuracy. A significant reduction in shear stress was observed after stress relieving treatment.
8. References:
- [1] M. Javidani, J. Arreguin-Zavala, J. Danovitch, Y. Tian, and M. Brochu, “Additive Manufacturing of AlSi10Mg Alloy Using Direct Energy Deposition: Microstructure and Hardness Characterization,” J. Therm. Spray Technol., vol. 26, no. 4, pp. 587–597, 2017.
- [2] I. Campbell, D. Bourell, and I. Gibson, “Additive manufacturing: rapid prototyping comes of age,” Rapid Prototyp. J., vol. 18, no. 4, pp. 255–258, 2012.
- [3] S. H. Huang, P. Liu, A. Mokasdar, and L. Hou, “Additive manufacturing and its societal impact: A literature review,” International Journal of Advanced Manufacturing Technology, vol. 67, no. 5–8. pp. 1191–1203, 2013.
- [4] W. E. Frazier, “Metal additive manufacturing: A review,” Journal of Materials Engineering and Performance, vol. 23, no. 6. pp. 1917–1928, 2014.
- [5] N. Guo and M. C. Leu, “Additive manufacturing: Technology, applications and research needs,” Frontiers of Mechanical Engineering, vol. 8, no. 3. pp. 215–243, 2013.
- [6] S. Trouton, “A Deloitte series on additive manufacturing,” Deloitte Univ. Press, 2016.
- [7] V. Bhavar, P. Kattire, V. Patil, S. Khot, K. Gujar, and R. Singh, “A Review on Powder Bed Fusion Technology of Metal Additive Manufacturing,” Mater. Sci. Technol. 2014, pp. 251–262, 2014.
- [8] J.-P. Kruth, “Materials and Processing Issues in Powder Fusion Additive Manufacturing,” 2013.
- [9] R. M. Mahamood, E. T. Akinlabi, M. Shukla, and S. Pityana, “Material Efficiency of Laser Metal Deposited Ti6A14V: Effect of Laser Power,” Eng. Lett., vol. 21, no. 1, pp. 18–22, 2013.
- [10] B. Liu, R. Wildman, C. Tuck, I. Ashcroft, and R. Hague, “Investigation the effect of particle size distribution on processing parameters optimisation in selective laser melting process,” Int. solid Free. Fabr. Symp. an Addit. Manuf. Conf., no. mm, pp. 227–238, 2011.
- [11] A. Aversa et al., “Effect of Process and Post-Process Conditions on the Mechanical Properties of an A357 Alloy Produced via Laser Powder Bed Fusion,” Metals (Basel)., vol. 7, no. 3, p. 68, 2017.
- [12] K. H. Leitz et al., “Fundamental analysis of the influence of powder characteristics in Selective Laser Melting of molybdenum based on a multi-physical simulation model,” Int. J. Refract. Met. Hard Mater., vol. 72, no. December 2017, pp. 1–8, 2018.
- [13] D. Manfredi, F. Calignano, M. Krishnan, R. Canali, E. P. Ambrosio, and E. Atzeni, “From powders to dense metal parts: Characterization of a commercial alsimg alloy processed through direct metal laser sintering,” Materials (Basel)., vol. 6, no. 3, pp. 856–869, 2013.
- [14] N. Kang, P. Coddet, L. Dembinski, H. Liao, and C. Coddet, “Microstructure and strength analysis of eutectic Al-Si alloy in-situ manufactured using selective laser melting from elemental powder mixture,” J. Alloys Compd., vol. 691, pp. 316–322, 2017.
- [15] A. Aversa, “Development and Characterisation of Aluminium Alloys and Aluminium Matrix Composites Produced via Laser Powder Bed Fusion By,” 2017.
- [16] I. Yadroitsev, L. Thivillon, P. Bertrand, and I. Smurov, “Strategy of manufacturing components with designed internal structure by selective laser melting of metallic powder,” Appl. Surf. Sci., vol. 254, no. 4, pp. 980–983, 2007.
- [17] K. G. Prashanth et al., “Microstructure and mechanical properties of Al-12Si produced by selective laser melting: Effect of heat treatment,” Mater. Sci. Eng. A, vol. 590, pp. 153–160, 2014.
- [18] K. Kempen, L. Thijs, J. Van Humbeeck, and J.-P. Kruth, “Mechanical Properties of AlSi10Mg Produced by Selective Laser Melting,” Phys. Procedia, vol. 39, pp. 439–446, 2012.
- [19] L. Wang, J. Jue, M. Xia, L. Guo, B. Yan, and D. Gu, “Effect of the Thermodynamic Behavior of Selective Laser Melting on the Formation of In situ Oxide Dispersion-Strengthened Aluminum-Based Composites,” Metals (Basel)., vol. 6, no. 11, p. 286, 2016.
- [20] J. Kruth, P. Mercelis, J. Van Vaerenbergh, and T. Craeghs, “Feedback control of Selective Laser Melting,” Proc. 3rd Int. Conf. Adv. Res. Virtual Rapid Prototyp., pp. 1–7, 2007.
- [21] M. Entezarian, F. Allaire, P. Tsantrizos, and R. A. L. Drew, “Plasma atomization: A new process for the production of fine, spherical powders,” JOM, vol. 48, no. 6, pp. 53–55, 1996.
- [22] EOS GmbH - Electro Optical Systems, “Material information Compatibility DMLS Materials – EOSINT M 280,” p. 82152.
- [23] S. Hegde and K. N. Prabhu, “Modification of eutectic silicon in Al-Si alloys,” J. Mater. Sci., vol. 43, no. 9, pp. 3009–3027, 2008.
- [24] W. Li et al., “Effect of heat treatment on AlSi10Mg alloy fabricated by selective laser melting: Microstructure evolution, mechanical properties and fracture mechanism,” Mater. Sci. Eng. A, vol. 663, pp. 116–125, 2016.
- [25] N. T. Aboulkhair, N. M. Everitt, I. Ashcroft, and C. Tuck, “Reducing porosity in AlSi10Mg parts processed by selective laser melting,” Addit. Manuf., vol. 1, pp. 77–86, 2014.
- [26] B. Duman and M. C. Kayacan, “Doğrudan Metal Lazer Sinterleme / Ergitme Yöntemi ile İmal Edilecek Parçanın Mekanik Özelliklerinin Tahmini Predicting The Mechanical Properties Of The Part Produced By Direct Metal Laser Sintering / Melting Method,” 2017.
- [27] EOS GmbH, “EOS M290 Datasheet Status 09/2017,” 2017.
- [28] A. Popovich and V. Sufiiarov, “Metal Powder Additive Manufacturing,” New Trends 3D Print., 2016.
- [29] Fritsch, “Operating Instructions Analysette 22.”
- [30] M. Fitzpatrick, A. Fry, P. Holdway, F. Kandil, J. Shackleton, and L. Suominen, “Determination of Residual Stresses by X-ray Diffraction - Issue 2,” Meas. Good Pract. Guid., no. 52, p. 74, 2005.
- [31] JEOL, “Scanning Electron Microscope A To Z,” Serv. Adv. Technol., p. 32, 2006.
- [32] 1.Rosenthal, I., Stern, A. & Frage, N. Strain rate sensitivity and fracture mechanism of AlSi10Mg parts produced by Selective Laser Melting. Mater. Sci. Eng. A 682, 509–517 (2017).
- [33] 1.Mertens, A., Dedry, O., Reuter, D., Rigo, O. & Lecomte-Beckers, J. THERMAL TREATMENTS OF AlSi10Mg PROCESSED BY LASER BEAM MELTING. 1007–1016
- [34] 1.Aboulkhair, N. T., Everitt, N. M., Ashcroft, I. & Tuck, C. Reducing porosity in AlSi10Mg parts processed by selective laser melting. Addit. Manuf. 1, 77–86 (2014).
9. Copyright:
- This material is a paper by "Giulia Di Matteo". Based on "Selective laser melting aluminum alloys for automotive component".
- Source of the paper: Not Available (Master Thesis, Politecnico di Torino)
This material is summarized based on the above paper, and unauthorized use for commercial purposes is prohibited.
Copyright © 2025 CASTMAN. All rights reserved.