Optimizing Your Castings: How Sand Composition Dictates Zinc Alloy Performance
This technical brief is based on the academic paper "Properties of Zinc alloy cast product with different composition of Silica Sand and Bentonite in Green Sand Mould" by Zatil Alyani Mohd Amin, Faizul Che Pa, and P.M Ir. Mohd Ichwan Nasution. It is summarized and analyzed for casting professionals by the experts at CASTMAN.
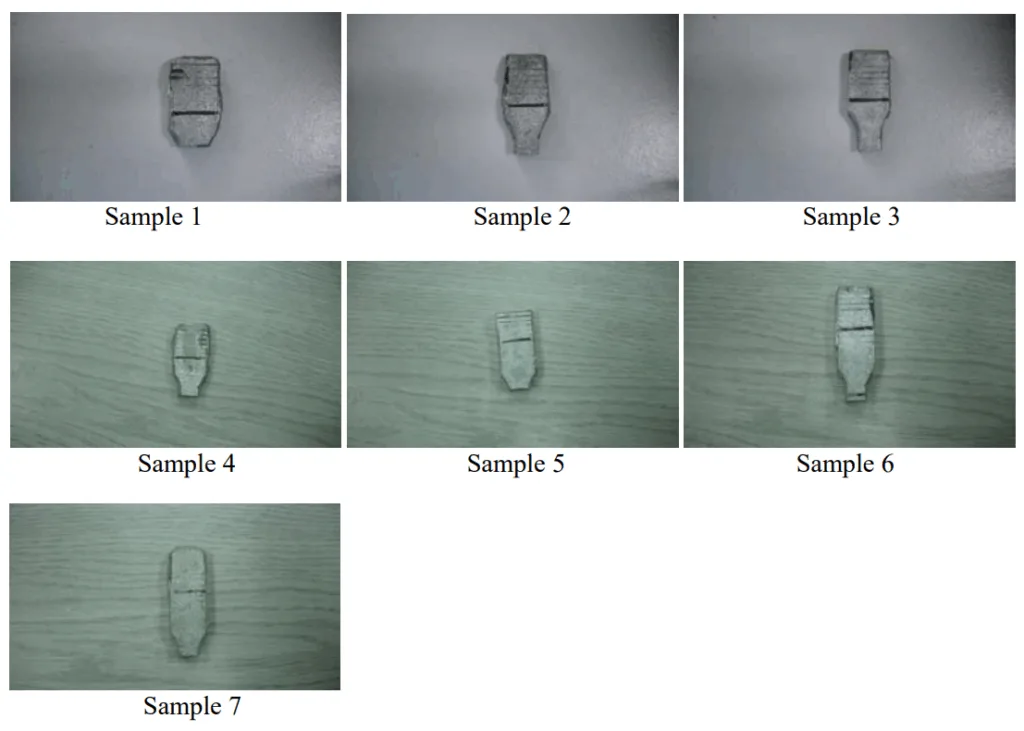
While our core expertise at CASTMAN lies in High-Pressure Die Casting (HPDC), we believe in staying at the forefront of all metal casting technologies. The principles of process control and material science are universal. This study on green sand casting provides valuable, data-driven insights into how fundamental mould components directly influence the final properties of a cast product—a lesson relevant to any engineer striving for quality and consistency.
Keywords
- Primary Keyword: Zinc Alloy Casting in Green Sand Moulds
- Secondary Keywords: Green Sand Mould Composition, Silica Sand Bentonite Ratio, Zinc Alloy Mechanical Properties, Casting Surface Finish, Casting Hardness, Zn-3Al-2Mg Alloy
Executive Summary
- The Challenge: In green sand casting, the precise composition of the mould is critical, yet the direct impact of varying the silica sand-to-bentonite ratio on the final properties of zinc alloy products is not always clear.
- The Method: Researchers prepared seven green sand moulds with different bentonite compositions (ranging from 5% to 17%). A tertiary Zinc-Aluminium-Magnesium (Zn-3Al-2Mg) alloy was cast in each mould.
- The Key Breakthrough: The study revealed a direct and non-linear relationship between bentonite percentage and the cast product's properties. Different compositions optimized for different outcomes: 11% bentonite produced the best surface finish, 13% yielded the highest hardness, and 15% resulted in the greatest tensile strength.
- The Bottom Line: There is no single "perfect" sand composition; rather, it's a trade-off. Process engineers must balance the ratio of silica sand and bentonite to achieve the specific combination of surface, hardness, and strength required for the application.
The Challenge: Why This Research Matters for Casting Professionals
Molding sands, typically a mixture of silica sand, clay binders like bentonite, and water, are the foundation of the green sand casting process. As the paper's introduction notes, this method is valued for its low cost, high production rates, and the recyclability of the sand. However, achieving consistent, high-quality results for zinc alloys—which are increasingly in demand for automotive and decorative parts—presents a significant challenge.
The properties of the final cast part are not determined by the metal alloy alone. They are profoundly influenced by the mould itself. How does changing the amount of bentonite binder affect surface finish? What is the impact on hardness or tensile strength? Answering these questions is crucial for any foundry looking to minimize defects, optimize mechanical performance, and deliver superior products. This research tackles this fundamental process control problem head-on.
The Approach: Unpacking the Methodology
To isolate the effect of mould composition, the researchers conducted a controlled experiment.
- Mould Preparation: Seven distinct green sand moulds were created. The water content was kept constant at 0.24 kg for all samples, while the ratio of silica sand to bentonite was systematically varied. The bentonite content ranged from 5% (Ratio 95:5) up to 17% (Ratio 83:17), as detailed in Table 1 of the paper.
- Casting Process: A tertiary zinc alloy (Zn-3Al-2Mg) was melted and poured into each of the seven unique moulds to create dog-bone-shaped test samples.
- Analysis: The resulting cast samples were then subjected to a series of tests to evaluate their physical and mechanical properties, including visual inspection of the surface, hardness testing, and tensile strength testing.
The Breakthrough: Key Findings & Data
The study demonstrated that small changes in the bentonite-to-sand ratio have a significant and measurable impact on the final product.
Finding 1: Surface Finish is a Balancing Act: The visual appearance of the cast samples varied significantly. The lowest (5%) and highest (17%) percentages of bentonite produced a "dull surface." According to the paper, "The shiniest surface is from the 11% of bentonite" (see Figure 1 for images of all samples). This suggests an optimal window for achieving the best surface quality.
Finding 2: Hardness Peaks at 13% Bentonite: The hardness test results, shown in Figure 2, revealed a clear trend. The highest hardness value (131.74) was achieved with the mould containing 13% bentonite (Sample 5). Interestingly, increasing the bentonite further to 15% (Sample 6) resulted in the lowest hardness value (106.06).
Finding 3: Tensile Strength Peaks at 15% Bentonite: The tensile strength results showed a different peak. As seen in Figure 3, the highest tensile strength (112.113 MPa) was recorded for the sample cast in the 15% bentonite mould (Sample 6). Conversely, the sample with the best surface finish (11% bentonite, Sample 4) exhibited the lowest tensile strength (77.892 MPa).
Finding 4: Consistent Microstructure: Despite the significant differences in mechanical properties and surface finish, the researchers noted that the microstructures of the different samples showed "not much difference from each other."
Practical Implications for Your Casting Operations
The findings from this paper offer clear, actionable insights for any facility using green sand casting processes.
- For Process Engineers: This research proves that optimizing your sand mixture is a critical trade-off. The data suggests that you cannot simultaneously maximize hardness, tensile strength, and surface finish with a single composition. The conclusion that "the best ratios for the bentonite and silicate sand are the 13 % and 15 % of bentonite" highlights that the ideal mix depends entirely on the most critical property for the final application.
- For Quality Control: The strong correlation between bentonite percentage and specific outcomes (Figure 2 and Figure 3) provides a powerful tool for process control. If a batch of products shows lower-than-expected hardness, this study suggests that the bentonite ratio in the sand mixture is a primary variable to investigate.
- For Material Selection: The paper reinforces that the properties of a cast part are a function of both the alloy and the mould system. When specifying a Zn-3Al-2Mg alloy, it is equally important to specify the mould parameters required to achieve the desired mechanical properties.
Paper Details
Properties of Zinc alloy cast product with different composition of Silica Sand and Bentonite in Green Sand Mould
1. Overview:
- Title: Properties of Zinc alloy cast product with different composition of Silica Sand and Bentonite in Green Sand Mould
- Author: Zatil Alyani Mohd Amin, Faizul Che Pa, P.M Ir. Mohd Ichwan Nasution
- Year of publication: 2014 (based on upload date)
- Journal/academic society of publication: ResearchGate (Pre-print/Conference Paper)
- Keywords: green sand mould, zinc alloy, silica sand
2. Abstract:
This project is to produce tertiary alloy of Zinc-Aluminium-Magnesium (Zn-3AI-2Mg) with different composition of bentonite and silica sand in the green sand mould. Zn alloy casting industry using green sand molding is increasingly becoming to very competitive circumstance, due to the various casting methods such as die cast, sand mould and so on with the recent coming of the lightening demand in automotive and decorative industry. However, Zn alloy casting using green sand still now plays an important role in the foundry society, because it allows us to manufacture at low cost and also sand can be recycled. Furthermore, it is appropriate method for multi kind and small quantity production. The mentioned method of mold is differing in composition of bentonite with 5%-17%. Differ in the composition of bentonite and silica sand give differ in result. The properties are obtains from the surface, the hardness test, the tensile test and the microstructure. Lowest and highest percentage of bentonite gives a dull surface properties compare to the in between. The shiniest surface is from the 15% of bentonite. Meanwhile, for the hardness test and the tensile strength, the results show the same with the surface properties. The morphologies give not much difference from each other.
3. Introduction:
Molding sands in metal casting are primarily made by mixing virgin silica sand with binders like bentonite clays (sodium and calcium bentonite). These are known as green sands. Green sand molding is a popular method where molten metal is poured into a mould containing moisture. The sand grains are coated with a clay-water mixture, which binds the sand into a rigid mass under force. A key advantage of these clay-bonded sands is their reusability; they can be cooled and remixed with additions of water, new clay, and other materials to replace what was lost or destroyed during casting. The raw materials are inexpensive and are only broken down in the parts of the mould in direct contact with molten metal.
4. Summary of the study:
Background of the research topic:
The study focuses on green sand moulding, a widely used, low-cost, and recyclable casting method. The alloy of interest is a Zinc-Aluminium-Magnesium (Zn-3Al-2Mg) alloy, which is part of a class of zinc casting alloys developed primarily in North America for applications requiring strength and wear resistance.
Status of previous research:
The paper acknowledges the established components of green sand moulds: silica sand (82-90%), bentonite clay (5-8%), and water (1.5-4%). It builds on the understanding that water is a critical component for activating the clay binder, which creates the bonds responsible for the mould's strength.
Purpose of the study:
The project's purpose was to produce and analyze a tertiary Zn-3Al-2Mg alloy cast using green sand moulds with varying compositions of bentonite and silica sand (from 5% to 17% bentonite) and to determine how these different compositions affect the final product's properties, specifically surface finish, hardness, and tensile strength.
Core study:
The core of the study involved the systematic variation of the bentonite-to-silica sand ratio in seven different green sand moulds. A Zn-3Al-2Mg alloy was cast in each mould, and the resulting samples were tested to correlate the mould composition with the physical and mechanical properties of the cast product.
5. Research Methodology
Research Design:
The research was designed as a comparative experiment. Seven samples were prepared, each using a green sand mould with a different ratio of silica sand to bentonite, as shown in Table 1. The ratios of bentonite were 5%, 7%, 9%, 11%, 13%, 15%, and 17%. The amount of water was held constant for all moulds.
Data Collection and Analysis Methods:
A tertiary zinc alloy (3wt% aluminium, 2wt% magnesium) was melted and poured into the moulds. After casting and shakeout, the samples were analyzed for:
1. Physical Properties: Visual inspection of the surface finish.
2. Hardness: A hardness test was performed on each sample.
3. Tensile Strength: A tensile test was conducted to determine the strength of the material.
4. Microstructure: The microstructure of the samples was examined.
Research Topics and Scope:
The research was scoped to the Zn-3Al-2Mg alloy and the green sand casting process. The primary variable investigated was the percentage of bentonite binder in the sand mould and its effect on the cast product's final properties.
6. Key Results:
Key Results:
- The surface finish was best at 11% bentonite, with lower and higher percentages resulting in a duller surface.
- The highest hardness (131.74) was achieved with 13% bentonite.
- The highest tensile strength (112.113 MPa) was achieved with 15% bentonite.
- The lowest tensile strength (77.892 MPa) corresponded to the sample with the best surface finish (11% bentonite).
- The conclusion states that "Bentonite and silicate sand truely have an influence towards the hardness and the surface results."
Figure Name List:
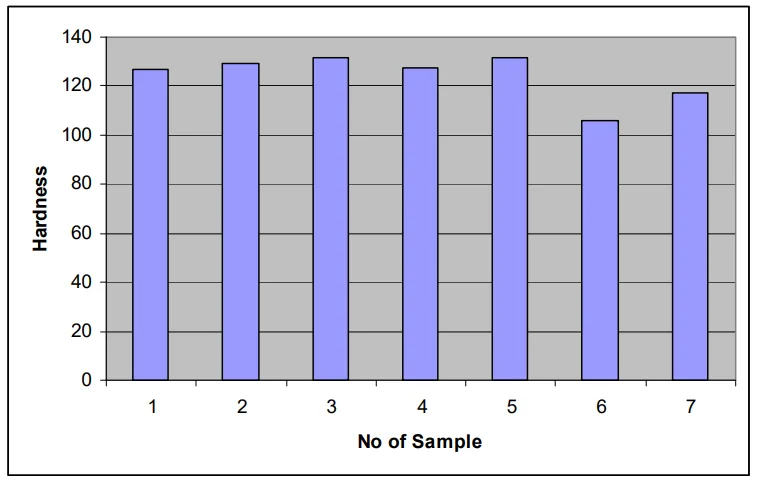
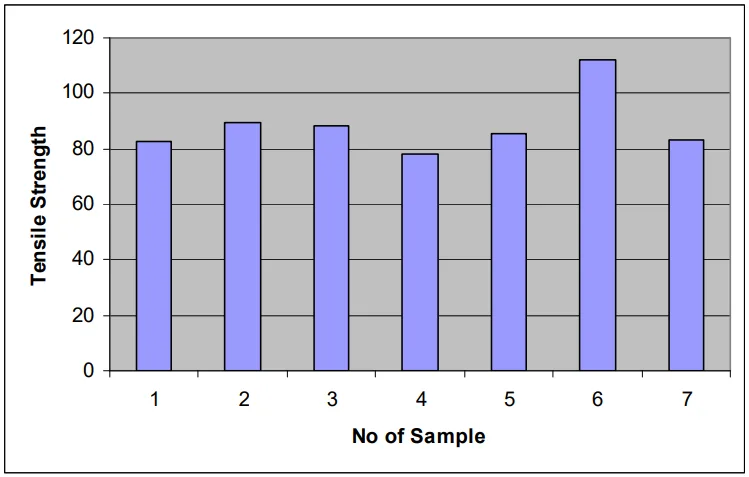
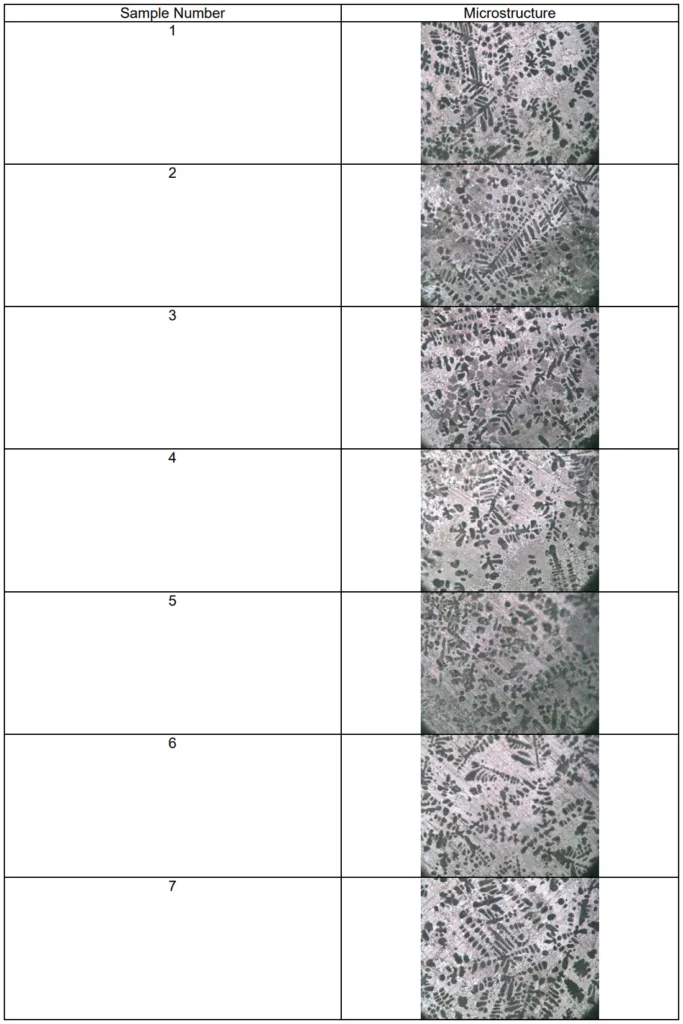
- Figure 1: Surface properties for all the ratios
- Figure 2: Hardness for the Zn-3AI-2Mg for 7 different moulds
- Figure 3: Tensile strength for the Zn-3AI-2Mg for 7 different moulds
7. Conclusion:
I. The best ratios for the bentonite and silicate sand are the 13 % and 15 % of bentonite.
II. Bentonite and silicate sand truely have an influence towards the hardness and the surface results.
III. All the mixture have nearly the same results for the hardness excepts for the two last ratios.
8. References:
- Yujue Wang, 2006, Study on the application of advanced oxidation processing in green sand foundries
- Luther, N.B., Metal casting and molding processes 1007-1998.7,29-35
- Smiernow, G. A,; Doheny, E.L,; Kay, J.G. 1980. Bonding mechanisms in sand aggregates. Am Foundry Soc. Transaction, 88, 659-682
- Odom, I.E. 1998 Functional properties of Na and Ca bentonites in green sand system. Am Foundry Soc. Transaction. 96, 229-236
- Odom, I.E. 1992. Chemical and physical factors that influence MB analysis of bentonites and system sand. Am. Foundry. Soc. Transaction. 100, 313-321
- Amen, C.W. 2000, Metalcasting, Mc Graw-hill, New York,
- Kawatra, S.K.; Ripke, S.J. 2001. Developing and understanding the bentonite fiber bonding mechanism. Miner. Eng, 14, 647-659
- M.A.savas, S.altintas. 1993. The microstructural control of cast and mechanical properties of zinc-aluminium alloys. Journal of material science 28. 1775-1780
- Kauffmann, P.; Voigt, R.C. 1997. Empirical study of impact of casting process changes on VOC and benzene emission levels and factors, am. Foundry soc. Trans. 105, 297-303
- Crandell, G.R.; Knight, S.M,; Schito, J.F,; Rarick, T.W. 2002. An examination of the effects of process variables on air emission from metal casting. Am. Foundry soc. Trans. 110, 1311-1320
Conclusion & Next Steps
This research provides a valuable roadmap for enhancing zinc alloy products made via green sand casting. The findings offer a clear, data-driven path toward optimizing for specific mechanical properties by carefully controlling the sand composition. It underscores the principle that true process control requires understanding the trade-offs between different quality metrics.
At CASTMAN, we are dedicated to applying the latest industry research to solve our customers' most challenging die casting problems. If the issues of balancing hardness, strength, and surface finish resonate with your operational goals, contact our engineering team to discuss how we can help you implement advanced principles in your components.
Expert Q&A: Your Top Questions Answered
Q1: What was the single best bentonite composition identified in the study?
A1: The paper concludes that there isn't one single "best" ratio, but a trade-off. It states, "The best ratios for the bentonite and silicate sand are the 13 % and 15 % of bentonite" (Conclusion I). The 13% ratio yielded the highest hardness (Figure 2), while the 15% ratio produced the highest tensile strength (Figure 3).
Q2: How does water content affect the green sand mould?
A2: As explained on page 6, water level is critical. Too much water "caused a decreased in the green strength and this can lead to gas elated defects, poor surface finish and difficulty in the make out of sand." Conversely, with too little water, "clay is not fully activated... and this leads to brittle, friable molds that may crack prior to pouring or during pouring."
Q3: What specific zinc alloy was used in this research?
A3: The study used a "tertiary alloy of Zinc-Aluminium-Magnesium (Zn-3AI-2Mg)," as stated in the Abstract
. The specific composition was 3wt% aluminium and 2wt% magnesium.
Q4: Did the mould composition affect the microstructure of the alloy?
A4: No, according to the Abstract
, the "morphologies give not much difference from each other." This suggests the changes in mechanical properties were due to factors other than large-scale microstructural changes.
Q5: What was the main conclusion regarding the influence of the sand mixture?
A5: The paper's second conclusion point is definitive: "Bentonite and silicate sand truely have an influence towards the hardness and the surface results." This confirms that the sand composition is a primary driver of final product quality.
Q6: What is the direct, practical takeaway from this paper for a casting facility?
A6: The core takeaway, based on the paper "Properties of Zinc alloy cast product...", is that a foundry must consciously choose its sand composition based on the most critical property for the part's application. Optimizing for surface finish (11% bentonite) will result in lower tensile strength, while optimizing for tensile strength (15% bentonite) will result in lower hardness.
Copyright
- This material is an analysis of the paper "Properties of Zinc alloy cast product with different composition of Silica Sand and Bentonite in Green Sand Mould" by Zatil Alyani Mohd Amin, et al.
- Source of the paper: https://www.researchgate.net/publication/228508414
- This material is for informational purposes only. Unauthorized commercial use is prohibited.
- Copyright © 2025 CASTMAN. All rights reserved.