This introductory paper is the research content of the paper ["'PROMISING CASTING ALUMINUM ALLOYS WITHOUT REQUIREMENT FOR HEAT TREATMENT'"] published by ['METAL 2019 Conference Proceedings'].
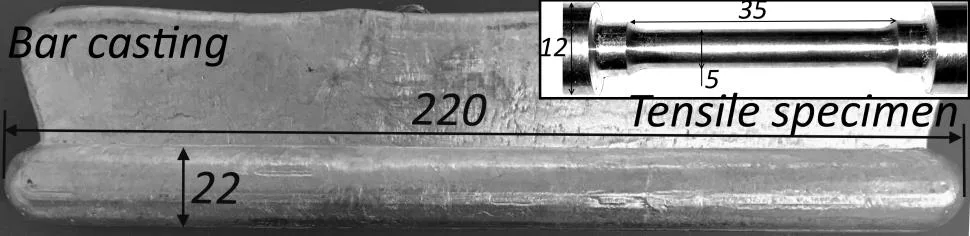
1. Overview:
- Title: PROMISING CASTING ALUMINUM ALLOYS WITHOUT REQUIREMENT FOR HEAT TREATMENT
- Authors: Pavel SHURKIN, Torgom AKOPYAN, Askar MUSIN
- Publication Year: 2019
- Published Journal/Society: METAL 2019 Conference Proceedings (May 22nd - 24th 2019, Brno, Czech Republic, EU)
- Keywords: casting, Al-Zn-Mg system, nickel, calcium, cerium
2. Abstract
Three kinds of aluminum alloys based on Al-Zn-Mg system and doped with Ca, Ni and Ce were studied. Determination of hot tearing tendency, phase composition and structure formation investigation were conducted. Alloying with the elements of Ca, Ni, Ce group is effective to increase casting properties that is better than those of a commercial A206 alloy. The structure after slow cooling during sand mold casting contains mainly needle like Al3Fe. But after permanent mold casting the iron containing phases are only ternary phases Al10CaFe2, Al9FeNi and Al10CeFe2. Most of Zn and Mg content are in aluminum solid solution as a result of casting that cause of appropriate mechanical properties under as-cast state. Moreover the high content of iron can allow us to include new alloys into the recycled type which means the opportunity to be produced using low grade aluminum or can scrap.
3. Research Background:
Background of the research topic:
Most casting aluminum alloys are Al-Si (4xx) alloys, known for their good castability due to eutectic constituents and recyclability [1, 2]. However, non-heat-treatable Al-Si alloys typically have limited ultimate tensile strength (UTS) or low ductility in the as-cast state [2, 4, 5]. Al-Mg (5xx) alloys can achieve high ductility, but often have low yield strength (YS) [2, 6-8]. Al-Zn-Mg (7xxx) alloys, typically used in wrought applications, offer high strength after aging but have poor castability due to the lack of eutectic liquid [1].
Status of previous research:
Previous research has explored adding eutectic-forming elements and iron to Al-Zn-Mg alloys [10, 11]. Al-Zn-Mg-Ni-Fe alloys have shown promise, achieving high UTS in the T6 state [11]. Calcium additions to Al-Zn-Mg alloys can improve corrosion resistance and reduce density [12], with some studies focusing on Al-Zn-Mg-Ca-Fe alloys [10]. Cerium forms eutectic phases in aluminum alloys [14], but its use in Al-Zn-Mg alloys is limited, with some studies showing coarse Al8Cu4Ce formation in Al-Zn-Mg-Cu alloys [15].
Need for research:
There is a need for casting aluminum alloys that exhibit high strength and ductility in the as-cast state, without requiring heat treatment, and that can potentially utilize recycled materials.
4. Research purpose and research question:
Research purpose:
To substantiate a principal opportunity to obtain new promising high strength aluminum alloys based on the Al-Zn-Mg-Ni(Ca, Ce)-Fe system for use under as-cast state.
Core research:
Determination of casting properties, microstructure and mechanical properties investigation.
5. Research methodology
The research involved creating three experimental aluminum alloys based on an Al-5.5% Zn-1.5% Mg matrix, alloyed with 0.5% Fe and separately doped with 1% Ni, 1% Ca, and 1% Ce. The alloys were produced by smelting pure materials and master alloys. Melt purification was performed using C2Cl6 powder injection. Chemical composition was analyzed using an ARL3460 emission spectrometer (Table 1). Hot tearing tests were conducted using pencil-type castings. Microstructure analysis was performed using SEM (TESCAN VEGA 3) and electron microprobe analysis (Oxford AZtec). Specimens were etched electrolytically. Slow cooling (sand mold) and permanent mold castings (Figure 1) were produced. Tensile tests were performed on as-cast samples using a Z250 Zwick/Roell machine.
6. Key research results:
Key research results and presented data analysis:
Hot tearing tests (Figure 2) showed that the experimental alloys (A1, A2, A3) had better casting properties than a commercial A206 alloy. Microstructure analysis after slow cooling (Figure 3) revealed predominantly needle-like Al3Fe phases. Permanent mold castings exhibited finer microstructures (Figure 4). The A1 (Ni-containing) alloy showed Al9FeNi phase and a supersaturated aluminum solid solution. The A2 (Ca-containing) alloy showed (Al, Zn)4Ca and likely Al10CaFe2. The A3 (Ce-containing) alloy showed Al10CeFe2. Tensile tests (Figure 5) showed that A1 and A2 alloys achieved UTS > 330 MPa and YS > 220 MPa with elongation > 5%. The A3 alloy had lower YS but higher elongation.

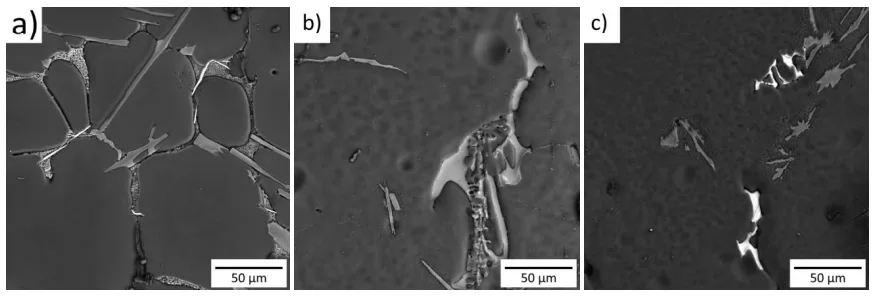
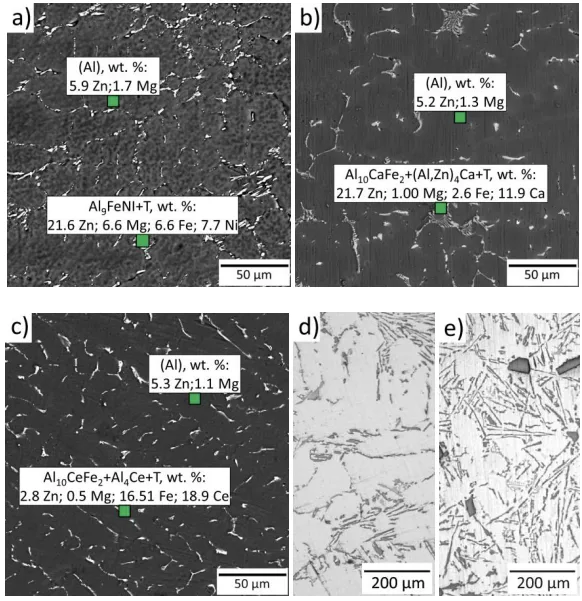
(a) A1 alloy; (b) A2 alloy; (c) A3 alloy; (d) Al7Si0.3Mg alloy; (e) Al12Si2Cu alloy;
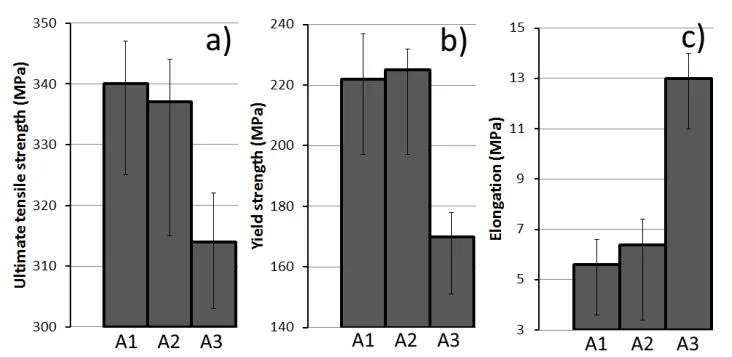
List of figure names:
- Figure 1 Bar permanent casting
- Figure 2 Pencil-type hot tearing test castings: (a) A1 alloy; (b) A2 alloy; (c) A3 alloy; (d) A206 commercial alloy
- Figure 3 As-cast microstructures of experimental alloys after slow cooling: (a) A1 alloy; (b) A2 alloy; (c) A3 alloy
- Figure 4 As-cast microstructures of experimental alloys after permanent mold casting: (a) A1 alloy; (b) A2 alloy; (c) A3 alloy; (d) Al7Si0.3Mg alloy; (e) Al12Si2Cu alloy;
- Figure 5 Tensile properties of experimental alloys under as-cast state: (a) UTS; (b) YS; (c) El
7. Conclusion:
Summary of key findings:
New casting aluminum alloys based on the Al-Zn-Mg system with additions of Ni, Ca, Ce, and Fe were investigated in the as-cast state. The addition of these elements improved hot tearing resistance. Fine, dispersed structures containing ternary phases (Al9FeNi, Al10CaFe2, Al10CeFe2) were obtained after permanent mold casting. The combination of eutectic intermetallics and supersaturated solid solution resulted in high mechanical properties, exceeding those of commercial non-heat-treatable casting aluminum alloys. The high iron content allows for the use of secondary stock or low-grade aluminum.
8. References:
- [1] HATCH, J.E. Aluminum: Properties and Physical Metallurgy. Ohio: American Society for Metals,1984. p. 424.
- [2] GLAZOFF, M., KHVAN, A., ZOLOTOREVSKY, V., BELOV, N., DINSDALE, A. Casting Aluminum Alloys: 2nd Edition: Their Physical and Mechanical Metallurgy. Elsevier, 2018. p. 608
- [3] ZÁVODSKÁA, D., TILLOVÁA, E., ŠVECOVÁA, I., KUCHARIKOVÁ, L., CHALUPOVÁ, M. Secondary cast Al-alloys with higher content of iron. Materials Today: Proceedings, vol. 5, 2018, pp. 26680-26686.
- [4] DONG, X., YANG, H., ZHU, X., JI, S. High strength and ductility aluminium alloy processed by high pressure die casting. JALCOM. 2019. vol. 773, pp. 86-96.
- [5] YANG, H., JI S., FAN, Z. Effect of heat treatment and Fe content on the microstructure and mechanical properties of die-cast Al-Si-Cu alloys. Materials & Design. 2015. vol. 85, pp. 823-832.
- [6] JI, S., WATSON, D., FAN, Z., WHITE, M. Development of a super ductile diecast Al–Mg–Si alloy. Mat. Sci. & Eng. A. 2012. vol. 556, pp. 824-833.
- [7] ZHANG, P., LI, Z., LIU, B., DING, W., PENG, L. Improved tensile properties of a new aluminum alloy for high pressure die casting. Mat. Sci. & Eng. A. 2016. vol. 651, pp. 376-390.
- [8] HU, Z., WAN, L., WU, S., WU, H., LIU, X. Microstructure and mechanical properties of high strength die-casting Al–Mg–Si–Mn alloy. Materials & Design. 2013. vol. 46, pp. 451-456.
- [9] BENEDETTI, A.V., CABOT, P.L., GARRIDO, J.A., MOREIRA, A.H. Influence of iron addition on the microstructure and the electrochemical corrosion of Al–Zn–Mg alloys. J. App. Electrochem.. 2001. vol. 31, issue 3, pp. 293-300.
- [10] SHURKIN, P.K., DOLBACHEV, A.P., NAUMOVA, E.A., DOROSHENKO, V.V. Effect of iron on the structure, hardening and physical properties of the alloys of the Al-Zn-Mg-Ca system. Tsvetnye Metally. 2018. no. 5, pp. 69-77.
- [11] MANN, V.Kh., ALABIN, A.N., KROKHIN, A.Yu., FROLOV, A.V., BELOV, N.A. New Generation of High Strength Aluminum Casting Alloys. Light Metal Age. 2015. vol. 73, №5, pp. 44-47.
- [12] VOLKOVA, O.V., DUB, A.V., RAKOCH, A.G., GLADKOVA, A.A., SAMOSHINA, M.E. Comparison of pittong corrosion tendency for castings made of Al6Ca, Al1Fe, Al6Ca1Fe experimental alloys and AK12M2 industrial alloy, Izvestiya Vuzov Tsvetnaya Metallurgiya (Proceedings of Higher Schools Nonferrous Metallurgy). 2017. vol. 5, pp. 75-81.
- [13] GOTO, S., KIM, B-II., PARK, H.-H., BELOV, N.A., ZOLOTOREVKIJ, V.S., ASO, S., Komatsu Y. Application of Multiphase Eutectics to Development of High Strength Cast Aluminum Alloys. Journal of Society of Materials Engineering for Resources of Japan. 2002. vol.15, no. 2, pp.66-73.
- [14] LAI, J.-P., JIANG, R.-P., LIU, H.-S., DUN, X.-L., LI, Y.-F., LI, X.-Q. Influence of cerium on microstructures and mechanical properties of Al-Zn-Mg-Cu alloys. Journal of Central South University. 2012. vol. 19, issue 4, pp. 869–874.
9. Copyright:
- This material is a paper by "[SHURKIN, P., AKOPYAN, T., & MUSIN, A.]": Based on "[PROMISING CASTING ALUMINUM ALLOYS WITHOUT REQUIREMENT FOR HEAT TREATMENT]".
- Source of paper: [DOI: 10.37904/metal.2019.742]
This material was created to introduce the above paper, and unauthorized use for commercial purposes is prohibited. Copyright © 2025 CASTMAN. All rights reserved.