This article introduces the paper ['High-pressure die-cast (HPDC) aluminium alloys for automotive applications'] presented at the ['Advanced materials in automotive engineering']
1. Overview:
- Title: High-pressure die-cast (HPDC) aluminium alloys for automotive applications
- Author: F. CASAROTTO, A. J. FRANKE and R. FRANKE
- Publication Year: 2012
- Publishing Journal/Academic Society: Advanced materials in automotive engineering / Woodhead Publishing Limited
- Keywords: aluminium alloys for automotive applications, innovative light metals, high-pressure die-cast (HPDC) aluminium alloys, low-iron primary alloys, ductile casting alloys.
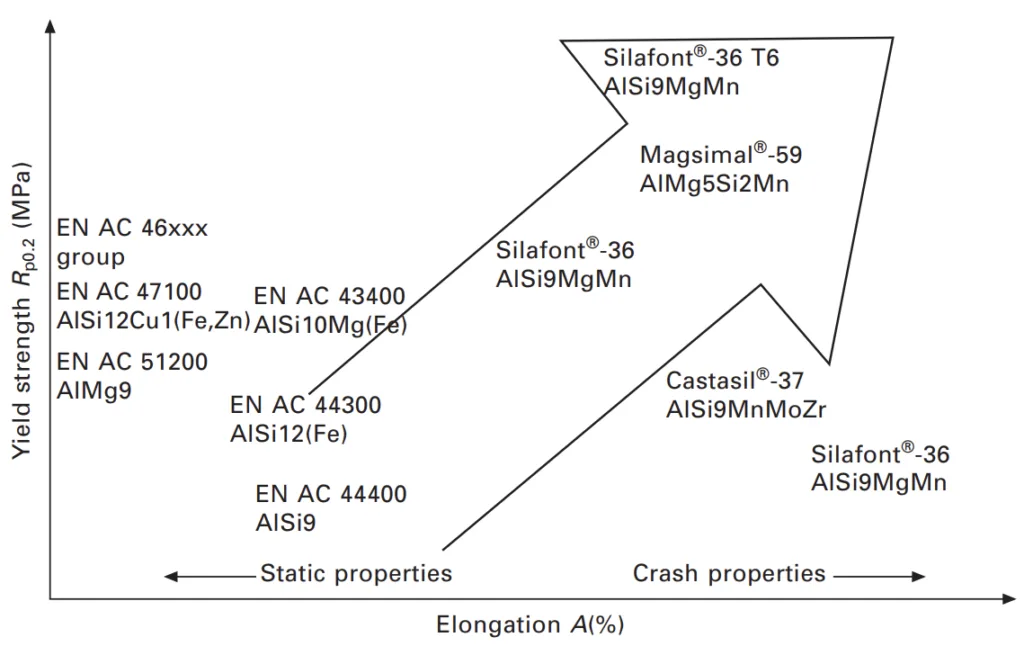
2. Research Background:
Background of the Research Topic:
The chapter addresses the historical progression of aluminium materials in automotive applications, with a central focus on High-Pressure Die-Cast (HPDC) aluminium alloys. It traces the evolution of HPDC from its early stages, primarily utilized for zinc casting, to its contemporary status as the default methodology for mass production of light metal components. The narrative emphasizes the driving forces behind the adoption of premium casting alloys, particularly in response to the automotive industry's escalating demands for sophisticated components.
Status of Existing Research:
Initially, HPDCing was perceived as a process suited for simple castings using low-cost secondary alloys, with limited consideration for metal handling or ductility. The evaluation of casting soundness relied on 'soft criteria' due to the non-critical nature of early applications. However, advancements in equipment and a deeper understanding of metallurgical processes, including high-vacuum HPDCing, squeeze casting, and semi-solid casting, have significantly enhanced the process capabilities. The focus has shifted from equipment-centric development to a material science approach, particularly with the introduction of new low-iron ductile HPDC alloys in the 1990s.
Necessity of the Research:
The impetus for this research stems from the automotive industry's continuous pursuit of improved car models, necessitating more complex castings with enhanced performance characteristics. Modern automotive applications demand HPDC components that are heat-treatable, weldable, ductile, and stronger, often with larger sizes and reduced wall thicknesses for lightweight design. These stringent requirements are underpinned by constructor's safety criteria, necessitating high quality standards and driving the need for advanced alloy development and process optimization in HPDC.
3. Research Purpose and Research Questions:
Research Purpose:
This chapter aims to provide a concise historical account of the logical progression leading to the development of novel aluminium materials tailored for automotive applications. The primary emphasis is placed on High-Pressure Die-Cast (HPDC) aluminium alloys, elucidating the factors that have propelled the industry towards the utilization of premium casting alloys. The study further intends to delineate the chemical composition, mechanical properties, and unique attributes of Silafont®-36, Magsimal®-59, and Castasil®-37, accompanied by processing and casting guidelines. Practical experiences are reported to address common queries regarding primary low-iron ductile alloys, and application examples are presented to underscore the innovative facets of each component.
Key Research:
The key research areas explored in this chapter are centered around the advancement and application of HPDC aluminium alloys in the automotive sector. Specifically, the chapter investigates:
- The evolution of HPDC aluminium alloys to meet the increasing demands of automotive applications.
- The characteristics and applications of three key premium alloys: Silafont®-36, Magsimal®-59, and Castasil®-37.
- The processing and casting considerations for these advanced alloys.
- The impact of material science approaches on improving casting alloys and HPDC technology.
Research Hypotheses:
While not explicitly stated as formal hypotheses, the chapter implicitly explores the following propositions:
- The development of low-iron ductile HPDC alloys is crucial for meeting the evolving performance and safety requirements in automotive engineering.
- Alloys such as Silafont®-36, Magsimal®-59, and Castasil®-37 represent significant advancements in HPDC aluminium alloys, offering tailored properties for specific automotive applications.
- Optimized HPDC processes, coupled with advanced alloy selection, are essential for achieving high-quality, high-performance automotive components.
4. Research Methodology
Research Design:
This chapter employs a descriptive and historical research design, tracing the evolution of HPDC aluminium alloys for automotive applications. It is structured as a review, drawing upon existing knowledge, industrial experiences, and alloy development data to present a comprehensive overview of the subject matter.
Data Collection Method:
The data presented in this chapter is collected through a review of industry practices, alloy specifications, and practical application examples. It incorporates data from practical experiences and foundry trials related to the processing and casting of the described alloys.
Analysis Method:
The analysis is primarily qualitative, involving a descriptive analysis of alloy characteristics, processing guidelines, and application examples. The chapter interprets performance data and application scenarios to highlight the advantages and suitability of different HPDC aluminium alloys for specific automotive components.
Research Subjects and Scope:
The scope of this chapter is focused on high-pressure die-cast (HPDC) aluminium alloys specifically designed for automotive applications. The primary subjects of the research are the premium alloys Silafont®-36, Magsimal®-59, and Castasil®-37, along with general classifications of aluminium alloys used in automotive parts. The scope encompasses the chemical composition, mechanical properties, processing, casting, joining, and application areas of these alloys within the automotive industry.
5. Main Research Results:
Key Research Results:
- Silafont®-36 (AlSi9MgMn): This alloy, developed by Aluminium Rheinfelden GmbH, was the first ductile aluminium alloy for HPDC, introduced in 1994 and designated as 365.0 by the American Aluminium Association in 1996. It is based on 99.8% pure primary aluminium with an average silicon content of 10.5%. Iron content is limited to a maximum of 0.15% to avoid detrimental intermetallic phases. Magnesium content varies (0.1–0.5%) to tailor mechanical properties. Different tempers (F, T4, T5, T6, T7) offer a wide range of mechanical properties, as summarized in Figure 6.3. Typical properties in as-cast state include a yield strength of 120-150 MPa and elongation of 5-12%. Dynamic tensile tests show increased properties compared to static tests (Figure 6.4). Fatigue strength is around 90 MPa in the as-cast state. Welding and joining techniques like MIG, TIG, LBW, EBW, FSW, self-pierce riveting, and flanging are applicable. Applications include space-frame nodes (Audi A8), vibration dampers, and structural parts.
- Magsimal®-59 (AlMg5Si2Mn): Developed in 1995 by Aluminium Rheinfelden GmbH, this non-heat-treatable AlMg alloy is designed for HPDC applications requiring high strength and ductility in the as-cast state. Its nominal composition is given in Table 6.3. It exhibits 'strain-induced ageing' during tensile testing (Figure 6.14). Mechanical properties in the as-cast state vary with wall thickness (Table 6.4), with yield strength ranging from >220 MPa to 120-145 MPa. Fatigue strength in the as-cast state is around 100 MPa (Figure 6.15). Welding (MIG, TIG) and joining (structural gluing, self-piercing riveting) are feasible. Applications include inner door panels, door frames, shock towers, and gearbox crossbeams.
- Castasil®-37 (AlSi9MnMoZr): Introduced in 2003 by Aluminium Rheinfelden GmbH, this non-heat-treatable AlSi alloy combines good castability with high elongation and moderate yield strength in the as-cast state. Its chemistry is tailored to avoid age-hardening, with magnesium content limited to 0.06% (Table 6.6). Mechanical properties in temper F and O heat-treated states are shown in Figure 6.24. Static tensile tests yield around 120 MPa Rp0.2%, 265 MPa Rm, and 15.9% elongation, with dynamic tests showing increased values (Figure 6.26). Fatigue strength is around 86 MPa. Welding (WIG, MIG, LBW, EBW, FSW) and joining (self-pierce riveting, flanging) are applicable. Applications include wide-surfaced structural parts, Lamborghini Gallardo Spyder nodes, Jaguar XK door panels, and Audi A8 rear connector sill frame.
Data Interpretation:
The research highlights the development and characteristics of three premium HPDC aluminium alloys tailored for automotive applications. Silafont®-36 is positioned as a versatile alloy with heat-treatability for enhanced strength and ductility, suitable for structural and safety-critical components. Magsimal®-59 excels in applications requiring high as-cast strength and corrosion resistance, eliminating the need for heat treatment. Castasil®-37 is designed for complex structural parts demanding high ductility and good castability without heat treatment, particularly in warmer engine compartment environments where age-hardening is undesirable. The alloys represent a progression in HPDC technology, enabling lighter, stronger, and more complex automotive components.
Figure Name List:
- Figure 6.1 Ranking aluminium alloys, focussing on the mechanical properties.
- Table 6.1 General classification of the most common aluminium automotive parts
- Figure 6.2 Eight target levels for HPDC with corresponding suitable alloys and main control process levers.
- Table 6.2 The percentage chemical composition of Silafont®-36
- Figure 6.3 Yield strength and elongation of Silafont®-36, according to different magnesium contents and heat-treatments.
- Figure 6.4 Dynamic versus static tensile tests for Silafont®-36 in the T7 state.
- Figure 6.5 High-pressure die-casting nodes of the A-pillar in the first ASF of Audi A8.
- Figure 6.6 Bed plate with integrated filter for a SUV.
- Figure 6.7 Rear lid frames of the BMW Series 5 GT.
- Figure 6.8 Integral engine mounting of a middle-class passenger car.
- Figure 6.9 Side door panel of the BMW Z8.
- Figure 6.10 Engine mounting of a BMW upper-class car.
- Figure 6.11 Side door cast nodes for the Audi A4.
- Figure 6.12 (a) Housing for vibration dampers. (b) the assembled damper: Silafont-36 with 0.16% Mg; (c) cross section of the flanged 'crown' of the vibration damper.
- Figure 6.13 The microstructure of Magsimal®-59 – (a) compared to a common AlMg5Si2Mn alloy - (b).
- Table 6.3 The percentage chemical composition of Magsimal®-59
- Figure 6.14 Stress-strain curve of Magsimal®-59, in the as-cast state for a 3 mm-wall thick sample.
- Figure 6.15 Wöhler's curve for Magsimal®-59.
- Figure 6.16 Fatigue properties of different alloys in corrosive context.
- Table 6.4 Mechanical properties of Magsimal®-59 in the as-cast state, as a function of the wall-thickness
- Table 6.5 Tensile tests performed on welded and non-welded samples in Magsimal®-59.
- Figure 6.17 Inner door panels of a SUV.
- Figure 6.18 Door frame.
- Figure 6.19 Shock tower.
- Figure 6.20 Integral crossbeam for BMW Allroad, Series 5, 6 and 7.
- Figure 6.21 Gearbox crossbeams of the Mercedes S-Class.
- Figure 6.22 Steering wheel of the VW Beetle.
- Figure 6.23 Suspension strut bracket for SUVs.
- Figure 6.24 The mechanical properties of Castasil®-37 in temper F and for different O heat-treated states.
- Table 6.6 The percentage chemical composition of Castasil®-37
- Figure 6.25 Microstructure of Castasil®-37 - (a) compared to Silafont®-36's one - (b) As-cast state, 3 mm wall-thick sample.
- Figure 6.26 Dynamic versus static tensile tests for Castasil®-37 in the as-cast state.
- Figure 6.27 Compression test results for Castasil®-37 and a common 226.
- Figure 6.28 HPDC nodes of the Lamborghini Gallardo Spyder.
- Figure 6.29 Hinge and latch door panels of the Jaguar XK.
- Figure 6.30 Rear connector sill frame member of the new A8.
- Figure 6.31 Frontal cross brace of the Audi R8.
- Figure 6.32 RHT folding levers of the VW EOS.
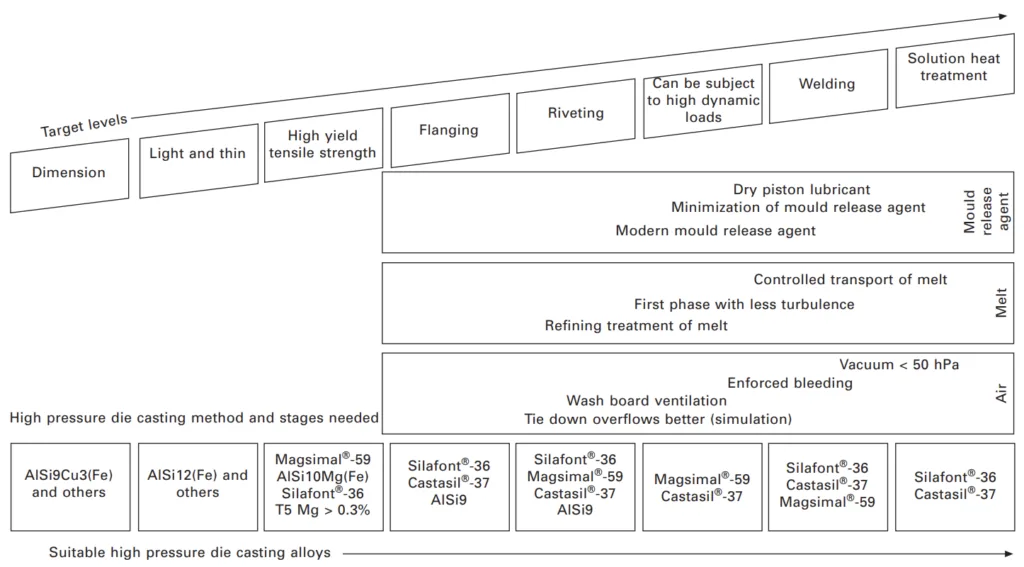
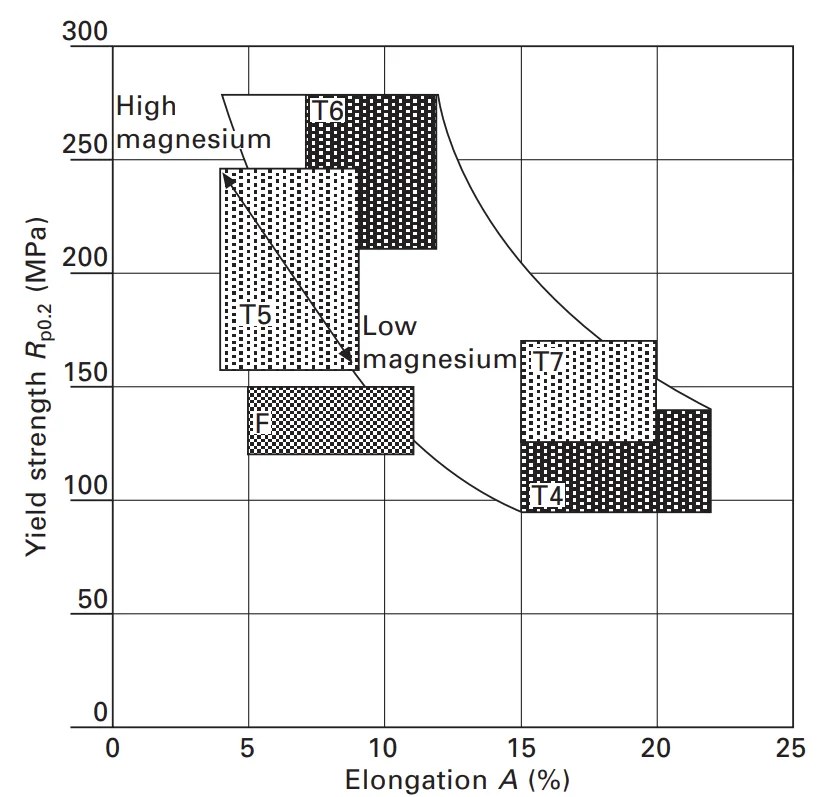
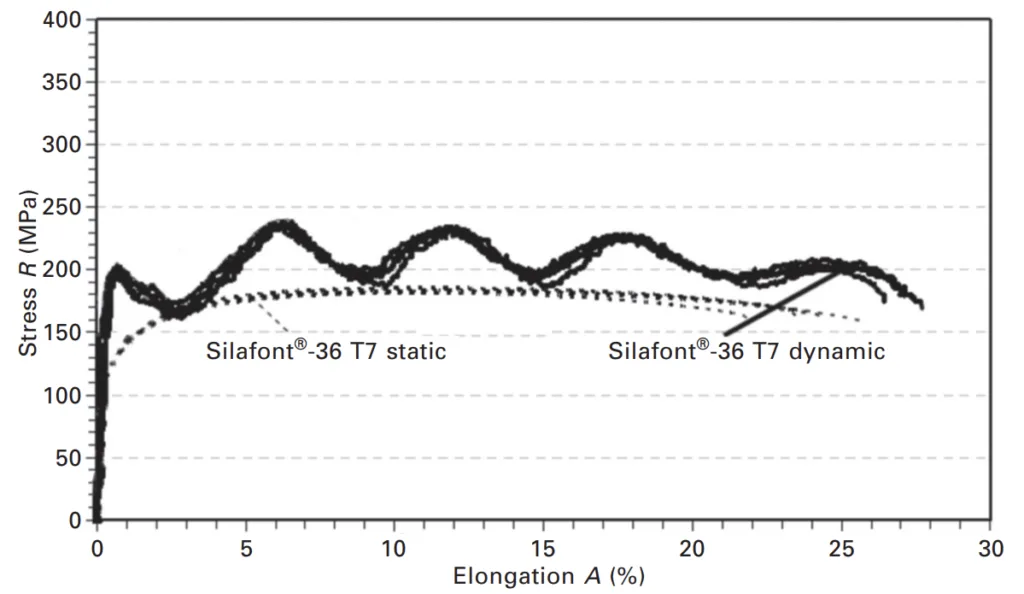
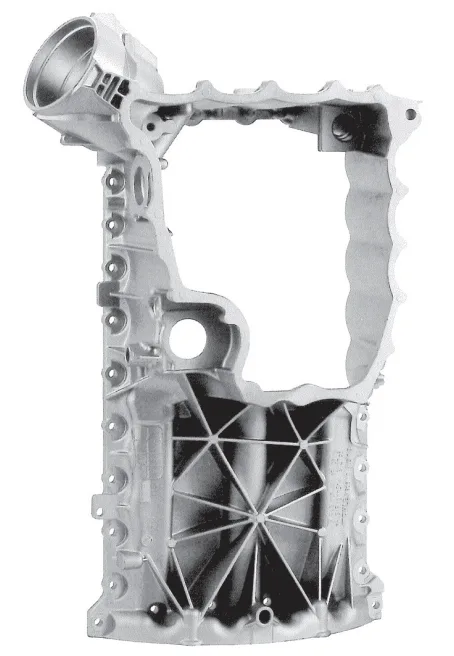
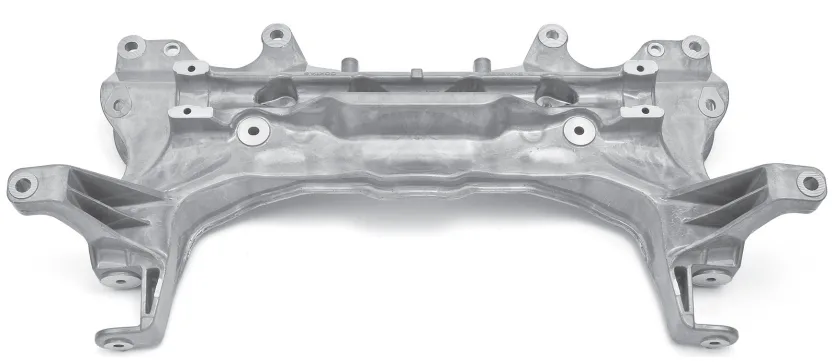
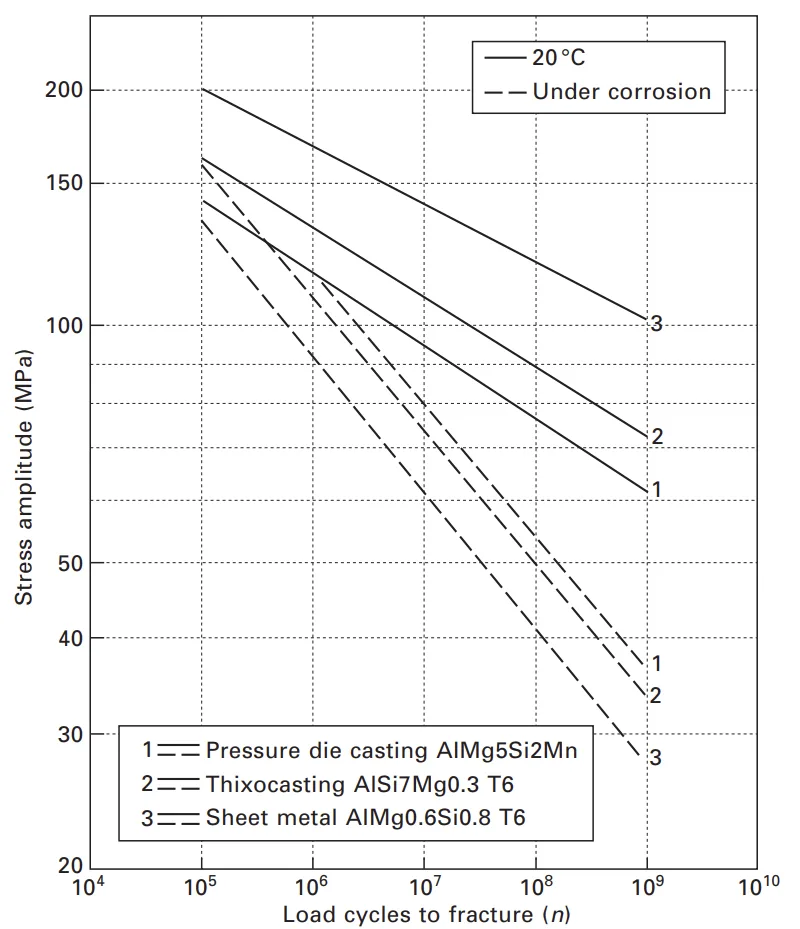
6. Conclusion:
Summary of Main Results:
This chapter has provided a historical overview of the development of high-performance HPDC aluminium alloys for automotive applications. It detailed the characteristics, processing, and applications of three key alloys: Silafont®-36, Magsimal®-59, and Castasil®-37. These alloys represent significant advancements in meeting the automotive industry's demands for lightweight, high-strength, and ductile components. Silafont®-36 offers versatility through heat treatment, Magsimal®-59 provides high as-cast strength and corrosion resistance, and Castasil®-37 is tailored for complex, heat-treatment-free structural parts.
Academic Significance of the Research:
The chapter contributes to the academic understanding of material science and engineering in the context of automotive die casting. It highlights the importance of alloy design and process optimization in achieving specific performance targets. The detailed analysis of alloy properties and application examples serves as a valuable resource for researchers and engineers in the field of advanced materials and manufacturing.
Practical Implications:
The practical implications of this chapter are substantial for the automotive industry and die casting foundries. It offers a handbook-level guide for selecting and implementing advanced HPDC aluminium alloys in automotive component design and manufacturing. The processing and casting guidelines, along with the showcased applications, provide actionable insights for improving component performance, reducing weight, and enhancing design flexibility.
Limitations of the Research
The chapter primarily focuses on the alloys developed by Aluminium Rheinfelden GmbH, which may limit the breadth of alloys covered. As a review chapter, it synthesizes existing knowledge and industrial experiences, rather than presenting novel experimental research. The rapidly evolving nature of materials science and automotive technology may necessitate further research to keep pace with new advancements beyond the scope of this chapter's publication date in 2012.
7. Future Follow-up Research:
- Directions for Follow-up Research
- Areas Requiring Further Exploration
This chapter does not explicitly detail directions for future follow-up research. However, based on the content, potential areas for further exploration could include:
- Investigating the long-term performance and durability of components made from Silafont®-36, Magsimal®-59, and Castasil®-37 in diverse automotive operating conditions.
- Exploring further optimization of HPDC processes for these alloys, including advanced die design, cooling strategies, and automation techniques.
- Researching new alloy compositions and modifications to further enhance mechanical properties, corrosion resistance, and castability for future automotive demands.
- Investigating the application of these alloys in emerging automotive technologies, such as electric vehicles and autonomous driving systems, where lightweighting and high performance are critical.
- Comparative studies with other advanced materials and manufacturing processes to assess the competitive advantages and limitations of HPDC aluminium alloys.
8. References:
- [1] Aluminium Rheinfelden GmbH, Publication Code 807, Neue Entwicklungen auf dem Gebiet der warmfesten Aluminium-Gusswerkstoffe, AlCu5Mn(Ni, Ce), AlMg2Si(Sc,Zr), Sonderdruck aus Giesserei 91, pages 32–38, 08/2004.
- [2] M. Garat, G. Laslaz, Improved Aluminium Alloys for Common Rail Diesel Cylinder Heads, AFS Transactions 2007, Paper 07-002(02), 2007.
- [3] Aluminium Rheinfelden GmbH, Primary aluminium alloys for pressure die casting, 1 Edition, June 2007.
- [4] Aluminium Rheinfelden GmbH, Publication Code 637, Optimizing the Manganese and Magnesium Content for Structural Part Application, Silafont-36, AlSi9MgMn, 22nd International Die Casting Congress and Exposition by NADCA, Indianapolis, 2003.
- [5] G. Luvará, Studio di Saldabilitá (LBW-FSW-EBW) di Leghe da Pressocolata a Base di Alluminio, Universitá degli Studi di Genova, Facoltá di Scienze M.F.N., Α.Α. 2008-2009, Genova, 2009.
- [6] Aluminium Rheinfelden GmbH, Neuentwickelte Druckgusslegierung mit ausgezeichneten mechanischen Eigenschaften im Gußzustand, Magsimal-59, AlMg5Si2Mn, Sonderdruck aus Giesserei Ausgabe 3/98.
- [7] Aluminium Rheinfelden GmbH, Publication Code 632, Erfahrung aus der Serienproduktion von druckgegossenen Lenkradskeletten in der Legierung Magsimal-59, AlMg5Si2Mn, TMS Annual Meeting and Exhibition, San Diego, March 1999.
- [8] Aluminium Rheinfelden GmbH, Aluminium Druckguss Legierungen, 1 Edition, May 2003.
- [9] O. Ozdemir, J. E. Gruzleski, R. A. L. Drew, Effect of Low-levels of Strontium on the Oxidation Behaviour of Selected Molten Aluminium-magnesium Alloys, Springer Science+Business Media, LLC, 2009.
- [10] Aluminium Rheinfelden GmbH, Primary Aluminium Casting Alloys, February 2006.
- [11] Aluminium Rheinfelden GmbH, Publication Code 806, Non Aging Ductile Pressure Die Casting Alloys for Car Construction, Castasil®-37, AlSiMn, 08/2004.
- [12] Aluminium Rheinfelden GmbH, Publication Code 638, Economic Production of Ductile and Weldable Aluminium Castings, Castasil®-37, AlSi9Mn, Reprint from Casting Plant and Technology International, pages 22–27, February 2006.
- [13] K. Greven, D. Dragulin, Ductile High Pressure Die Casting – Heat Treated or Temper F?, Proceedings of the 2nd International Light Metals Technology Conference 2005, 2005.
- [14] Rheinfelden Alloys GmbH & Co. KG, Hüttenaluminium-Gusslegierungen, Ausgabe 7, 01/2010.
- [15] Aluminium Rheinfelden GmbH, Publication Code 635, Möglichkeiten des Aluminiumdruckgiessens. Anwendung dieser Technologie im Grenzenbereich, Magsimal®-59, AlMg5Si2Mn, Sonderdruck aus Giesserei 90, Nr. 7, 2003.
- [16] Aluminium Rheinfelden GmbH, Publication Code 630, Producing Low-iron Ductile Aluminium Die Castings, 18th International Die Casting Congress and Exposition by NADCA, Indianapolis, 1995.
- [17] H. Koch, U. Sternau, H. Sternau, A. J. Franke, Magsimal-59, an AlMgMnSi-Type Squeeze-Casting Alloy Designed for Temper F, TMS Annual Meeting, Anaheim, LA, February 1996.
- [18] Aluminium Rheinfelden GmbH, Publication Code 633, Experience of Three Years Producing Low Iron Ductile Pressure Die Castings, 19th International Die Casting Congress and Exposition by NADCA, Minneapolis, 1997.
- [19] Aluminium Rheinfelden GmbH, Publication Code 636, Potentials of Aluminium Pressure Die Casting. Application of this technology close to the limits, Magsimal-59, AlMg5Si2Mn, Casting Plant and Technology International, No. 2/2003.
- [20] Aluminium Rheinfelden GmbH, Publication Code 545, Magsimal-59, AlMg5Si2Mn, Anwendungsmerkblatt, February 2004.
- [21] Aluminium Rheinfelden GmbH, Publication Code 623, Qualitätsorientierte Schmelzprüfung in der Aluminiumgiesserei, Sonderdruck aus Giesserei Heft 23/1987, pages 695-700, 1987.
9. Copyright:
- This material is "F. CASAROTTO, A. J. FRANKE and R. FRANKE"'s paper: Based on "High-pressure die-cast (HPDC) aluminium alloys for automotive applications".
- Paper Source: Woodhead Publishing Limited, 2012
This material was summarized based on the above paper, and unauthorized use for commercial purposes is prohibited.
Copyright © 2025 CASTMAN. All rights reserved.