This article introduces the paper ['A Review on Corrosion behaviour of Mn added Magnesium and its alloys'] published by ['International Advanced Research Journal in Science, Engineering and Technology'].
1. Overview:
- Title: A Review on Corrosion behaviour of Mn added Magnesium and its alloys
- Author: Mrs.Minal Sanjay Dani, Dr. Vandana J Rao, Dr. Indravadan B Dave
- Publication Year: 2015
- Publishing Journal/Academic Society: International Advanced Research Journal in Science, Engineering and Technology, Vol. 2, Issue 12, December 2015
- Keywords: Magnesium alloy; Manganese, Aluminium, Alloying Elements, Intermetallic phase; corrosion
![Fig. 1.Some automotive components made of Mg alloy and obtained weight reduction[14]](https://castman.co.kr/wp-content/uploads/image-1099-png.webp)
2. Abstracts or Introduction
This research review elucidates the corrosion behavior of Manganese (Mn) added Magnesium (Mg) and its alloys. Magnesium, the lightest of all engineering metals, presents itself as an attractive substitute for steels and aluminum. However, the persistent corrosion susceptibility of Mg and its alloys remains a significant technological impediment to their broader application. Various forms of corrosion affecting Mg alloys, including Galvanic corrosion, pitting corrosion, intergranular corrosion (IGC), filiform corrosion, crevice corrosion, stress corrosion cracking (SCC), and corrosion fatigue (CF), have been previously documented. Notably, in Magnesium-Aluminium (Mg-Al) alloys, the formation of the intermetallic Al8(Mn,Fe)5 phase has been observed to enhance corrosion resistance by sequestering elemental iron particles. Electrochemical methods and Weight loss methods (Immersion tests) were employed to assess corrosion rates, revealing that Mn additions augment the Fe impurity tolerance level. This suggests that Mn effectively mitigates the detrimental impact of Fe impurities on Mg alloy corrosion. Furthermore, factors influencing the corrosion behavior of Mg alloys, such as alloying elements, microstructure, secondary phases, grain size, welding effects, and heat treatment, are also considered.
3. Research Background:
Background of the Research Topic:
Magnesium (Mg) is recognized as the lightest engineering metal, rendering it a compelling alternative to Steels and Aluminium, particularly in sectors like automobiles, electronics, and aerospace, as cited by [7]. Despite these advantages, the corrosion of Mg and its alloys is a well-established major technological challenge that restricts their more extensive utilization. A significant demand exists for the development of magnesium alloys exhibiting improved corrosion resistance. A prerequisite for this development is a comprehensive and fundamental understanding of the roles played by key alloying elements and impurities in the corrosion process.
Status of Existing Research:
Prior research has extensively discussed various corrosion mechanisms in Mg alloys, including Galvanic corrosion, pitting corrosion, intergranular corrosion (IGC), filiform corrosion, crevice corrosion, stress corrosion cracking (SCC), and corrosion fatigue (CF), as referenced by [13]. In Mg-Al alloys, the formation of the intermetallic Al8(Mn,Fe)5 phase has been shown to enhance corrosion resistance by removing elemental iron particles from the Mg matrix and its alloys, as noted in [10]. Corrosion rate assessments have been conducted using electrochemical and Weight loss methods (Immersion tests). These investigations have indicated that samples with Mn additions demonstrate an increased tolerance to Fe impurities, suggesting Mn's ability to moderate the adverse effects of Fe on Mg alloy corrosion.
Necessity of the Research:
An "overwhelming demand" exists for the creation of magnesium alloys with enhanced corrosion resistance. Achieving this necessitates a "detailed and fundamental understanding of the role of key alloying elements and impurities." The primary objective of ongoing research is to modify Magnesium metal or Mg alloys to achieve superior corrosion resistance, positioning them as viable alternatives to Aluminium alloys.
4. Research Purpose and Research Questions:
Research Purpose:
The primary purpose of this review is "to provide an understanding of useful research directions for producing Mg and its alloys with lower corrosion rates [8]."
Key Research:
This paper focuses on the "corrosion behaviour of Manganese added Magnesium and its alloys." It investigates the "influencing factor of corrosion behaviour of Mg alloys like effect of allying element, Microstructure and secondary phases, grain size, effect of welding and heat treatment" as critical parameters affecting corrosion performance.
Research Hypotheses:
The research implicitly tests the hypothesis that "Mn addition was able to moderate the effect of the Fe impurity on the corrosion of the Mg alloy." Furthermore, it is based on the established understanding that "In Magnesium- Aluminium (Mg-Al) alloys, the formation of intermetallic Al8(Mn,Fe)5 phase improves the corrosion resistance by removing elemental iron particles from the Mg and its alloy[10]."
5. Research Methodology
Research Design:
This study is structured as a review paper, synthesizing existing literature to provide a comprehensive overview of the corrosion behavior of Mn-added magnesium alloys.
Data Collection Method:
The research methodology employed is a comprehensive literature review. The authors compiled and analyzed findings from various studies focusing on the corrosion of magnesium alloys, with a specific emphasis on the effects of manganese additions.
Analysis Method:
The analysis method is qualitative, involving the synthesis and interpretation of findings from the reviewed literature. The authors analyze and summarize the current state of knowledge regarding the corrosion mechanisms of magnesium alloys and the role of manganese in mitigating corrosion.
Research Subjects and Scope:
The scope of this review is centered on the "corrosion behaviour of Mg metal and Mg alloys" with a particular focus on the impact of "Mn addition in Mg Alloys[2]." The review encompasses various aspects of corrosion, including different types of corrosion, influencing factors, and measurement techniques relevant to magnesium alloys.
6. Main Research Results:
Key Research Results:
The key findings of this review are that "samples with Mn additions exhibited an increased Fe impurity tolerance level. This indicates that the Mn addition was able to moderate the effect of the Fe impurity on the corrosion of the Mg alloy." Furthermore, the review highlights that "influencing factor of corrosion behaviour of Mg alloys like effect of allying element, Microstructure and secondary phases, grain size, effect of welding and heat treatment were discussed." The paper also details various types of corrosion observed in Mg alloys, including Galvanic corrosion, pitting corrosion, intergranular corrosion, filiform corrosion, crevice corrosion, stress corrosion cracking (SCC), and corrosion fatigue (CF).
Analysis of presented data:
The paper presents several tables and figures to support its review:
- TABLE I: COMPARISONS OF PHYSICAL PROPERTIES OF METALS: This table compares the physical properties of Magnesium, Aluminum, and Iron, highlighting Magnesium's low density.
- TABLE II TYPICAL MECHANICAL PROPERTIES OF MG ALLOYS AT ROOM TEMPERATURE: This table presents typical mechanical properties for various Mg alloys (AZ91, AM60, AM50, AM20, AE42).
- TABLE: III METAL ION ELECTRODE POTENTIAL: This table lists the metal ion electrode potential for various metals, including Mg, illustrating Mg's highly active nature.
- TABLE:IV CORROSION POTENTIAL VALUES FOR MAGNESIUM AND FOR COMMON MAGNESIUM SECOND PHASES: This table provides corrosion potential values for Magnesium and common second phases in Mg alloys.
- TABLE: V CORROSION POTENTIAL OF PURE PHASES AFTER 3 H IMMERSION IN ASTM D1384 WATER: This table compares the corrosion potential of Mg, AlMn, and β (Mg17Al12) phases.
- Fig. 1: Illustrates "Some automotive components made of Mg alloy and obtained weight reduction[14]," showcasing practical applications and weight savings.
- Fig:2: Depicts "Magnesium forged alloy wheels," an example of high-performance Mg alloy applications.
- Fig:3: Shows "Machining Rolling slab: Elektron 43," highlighting the use of high-strength Mg alloys in aircraft seating.
- Fig:4: Presents "Handrails for city bus made byAZ31B," demonstrating the use of extruded Mg tubing for lightweight structures.
- Fig:5: Illustrates "Magnesium Engine Front Covers Lighten the Load," comparing Mg and Aluminum engine covers.
- Fig 6: Shows "Effect of alloying elements on corrosion rate of Mg alloy," graphically representing the impact of various alloying elements on corrosion rate.
- Fig:7: Depicts "Effect of addition of Mn in Mg-Al alloy," illustrating the influence of Mn addition on corrosion behavior in Mg-Al alloys.
- Fig:8,9: Illustrates "Galvanic Corrosion," explaining the mechanism of galvanic corrosion in Mg alloys.
- Fog:10: Shows "Pitting morphology of extruded AM60 in 3.5%NaCl aqueous solution," demonstrating pitting corrosion in Mg alloys.
- Fog:11: Presents "Intergranular corrosion morphology of AZ80-T5 in 3.5%NaCI aqueous solution after 1 h," illustrating intergranular corrosion.
- Fig 12: Shows "Corrosion morphology of weld zone of AZ31 with laser beam welding," demonstrating corrosion behavior in welded Mg alloy joints.
- Fig 13: Illustrates "Corrosion morphologies of AM60 as extruded in 3.5%NaCl aqueous solution at pH=3(a), pH=7(b) and pH=12(c), respectively," showing the effect of pH on corrosion morphology.
Figure Name List:
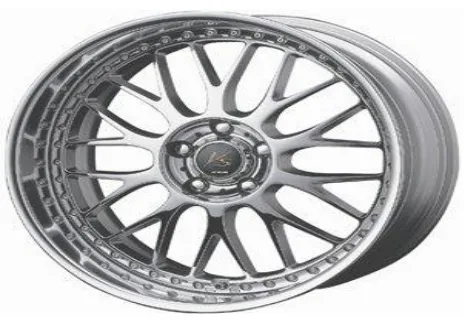
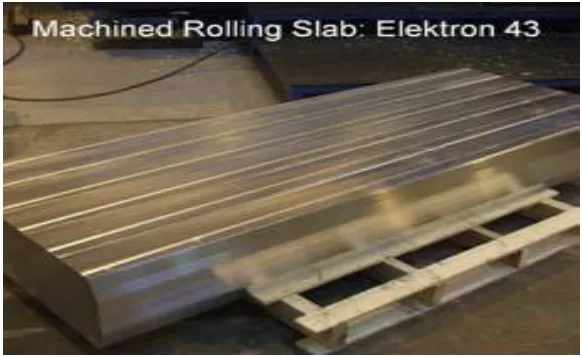
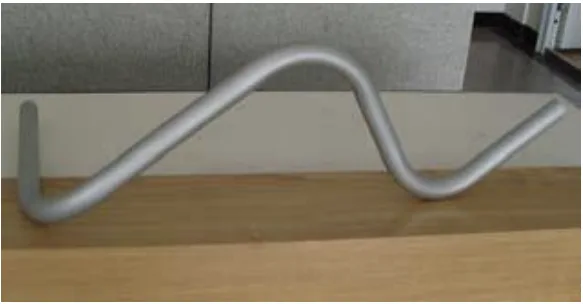

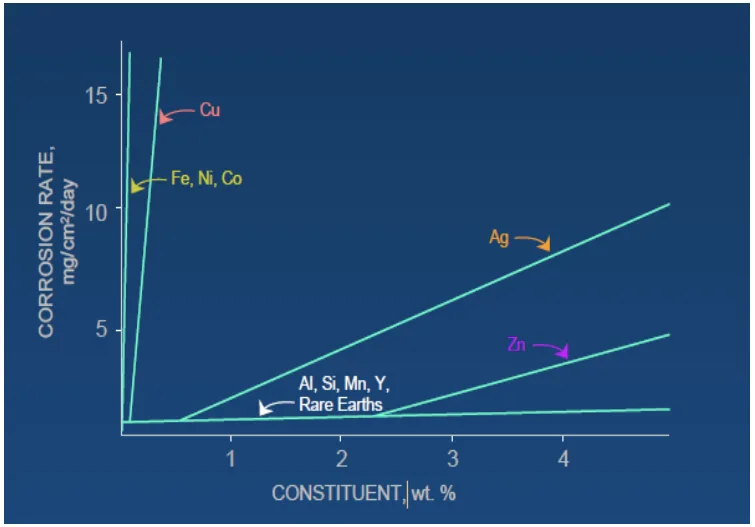
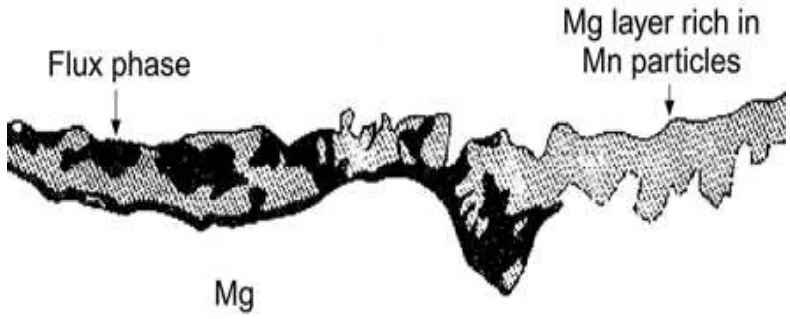
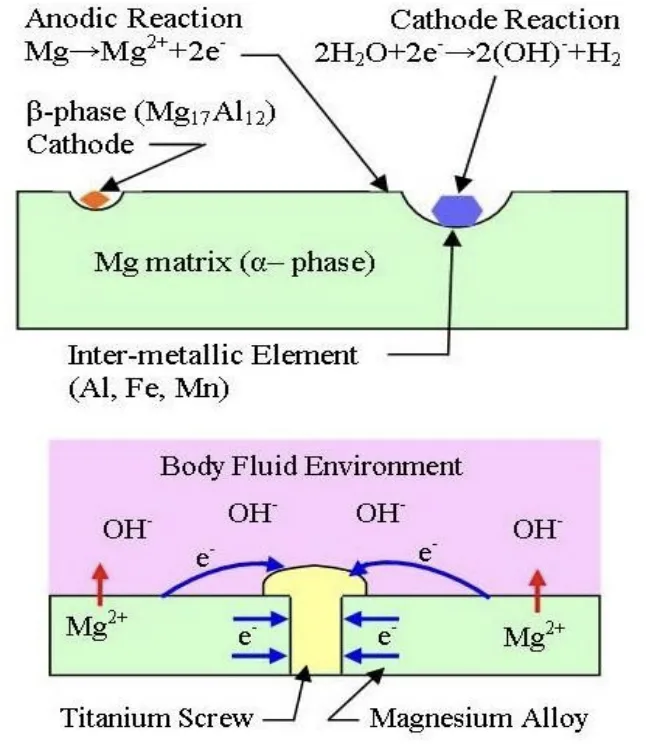
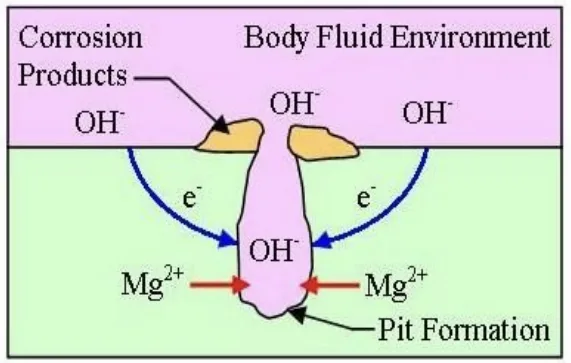
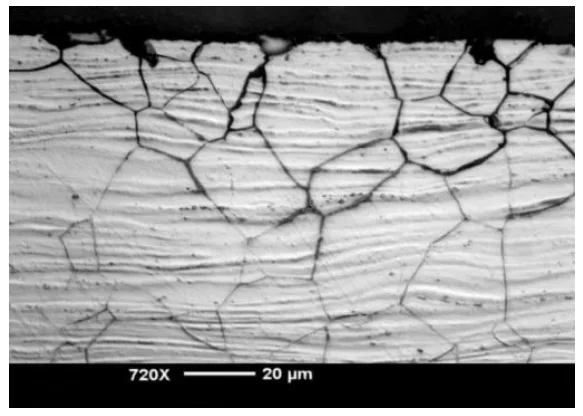
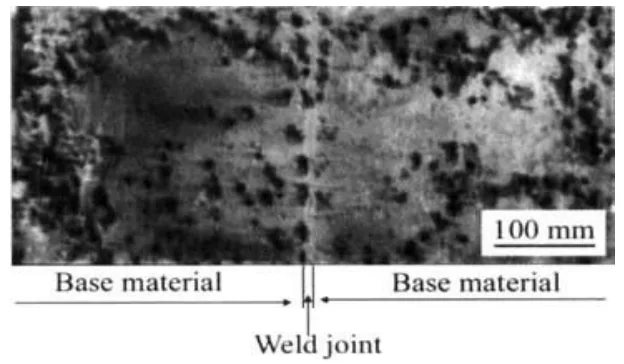
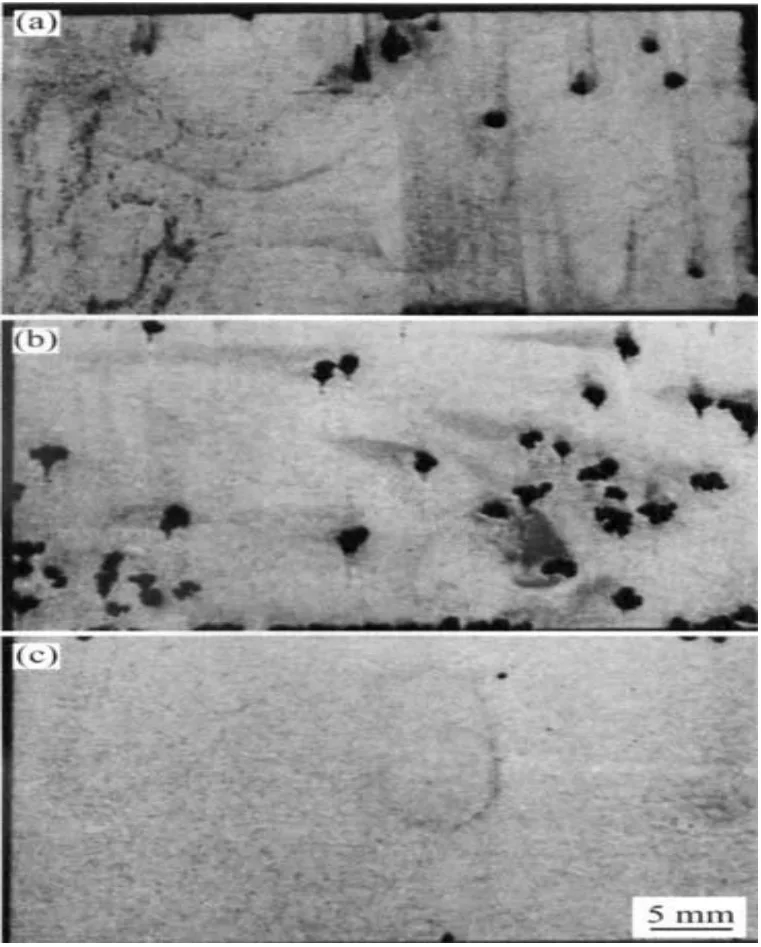
7. Conclusion:
Summary of Key Findings:
This review concludes that Manganese (Mn) addition in Magnesium (Mg) alloys enhances corrosion resistance, primarily by increasing the tolerance to iron (Fe) impurities. Mn facilitates the formation of the Al8(Mn,Fe)5 intermetallic phase, which effectively removes detrimental iron particles and reduces soluble iron content in Mg-Al alloys. The study emphasizes that the corrosion behavior of Mg alloys is complex and influenced by various factors, including alloying elements, microstructure, secondary phases, grain size, and processing techniques like welding and heat treatment. The review also provides an overview of different corrosion types prevalent in Mg alloys, such as galvanic, pitting, intergranular, and stress corrosion cracking.
Academic Significance of the Study:
This study provides a valuable academic contribution by consolidating and reviewing the current understanding of corrosion in Mn-added Mg alloys. It underscores the critical role of Mn in mitigating iron impurity effects and highlights the multifaceted nature of Mg alloy corrosion. The review identifies knowledge gaps and emphasizes the ongoing need for research to fully elucidate the corrosion mechanisms in these alloys.
Practical Implications:
The practical implications of this review are significant for the die casting industry and materials engineers working with magnesium alloys. The findings guide research and development efforts towards producing Mg alloys with improved corrosion resistance by strategically utilizing Mn additions and controlling processing parameters. This knowledge is crucial for expanding the application of lightweight Mg alloys in various industries, particularly in automotive, aerospace, and electronics, where corrosion resistance is paramount.
Limitations of the Study and Areas for Future Research:
The paper acknowledges that "The corrosion mechanisms of magnesium alloys are still not well understood." Therefore, it explicitly states that "it is definitely necessary to continue this investigation." The review identifies a "challenge for corrosion scientists to create a Mg alloy with better corrosion resistance." Future research should focus on gaining a deeper understanding of the fundamental corrosion mechanisms, developing novel Mg alloys with enhanced corrosion resistance, and creating more effective and sustainable corrosion protection systems and recycling technologies for Mg alloys.
8. References:
- [1] http://www.intlmag.org
- [2] Magnesium Alloys and Technologies. by Karl U. Kaine www.okokchina.com
- [3] ASM handbook, Volume 13, Corrosion, ASM International,4th Ed. 1992
- [4] Mg and Mg alloys in Uling's Corrosion Handbook, 2000.pg.793-830
- [5] http://www.hindustanmagnesium.com for aerospace industry
- [6] www.asminternational.org Corrosion Resistance of Magnesium Alloys
- [7] Revised by Barbara A. Shaw, Pennsylvania State University, ASM Handbook, Volume 13A Corrosion: Fundamentals, Testing, and Protection (#06494G)
- [8] M.R. Bothwell, in The Corrosion of Light Metals, John Wiley & Sons, 1967, p 269
- [9] ZENG Rong-chang', HANG Jin HUANG Wei-', W. DIETZEL',K. U. KAINER2, C. BLAWERT2, KE Wei3,, Trans. Nonferrous Met. SOC. China 16(2006)s763-s771, www.sciencedirect.co19 Available online at
- [10] C. Suman, Paper 900794, Society of Automotive Engineers, 1990
- [11] S. Jayalakshmi, Q.B. Nguyen, M. Gupta, Materials Chemistry and Physics, Volume 134, Issues 2-3, 15 June 2012, Pages 721-727
- [12] Dr.Sung, Advance Engineering Materials, 2005,7,no.7(Recent progress in corrosion and it's protection for Mg alloys)
- [13] T. Tański*, K. Labisz, L.A. Dobrzański,'effect of Al addition and heat treatment" AMME, vol 44 issuew 1, 2011
- [14] A.V. Sameljuk *, O.D. Neikov, A.V. Krajnikov, Yu.V. Milman,, G.E. Thompson, Corrosion Science 46 (2004) 147-158, www.elsevier.com/locate/corsci
- [15] Gonzalo Galicia a, Nadine Pébère b, Bernard Tribollet a, Vincent Vivier a,* LISE - UPR 15 du CNRS, Université Pierre et Marie Curie, 4 place Jussieu, 75252 Paris Cedex 05, France b Université de Toulouse, CIRIMAT, UPS/INPT/CNRS, ENSIACET, 118 route de Narbonne, 31077 Toulouse Cedex 04, France
- [16] Andrej Atrens a, Guang-Ling Song a,1, Fuyong Cao a, Zhiming Shi a, Patrick K. Bowen, a The University of Queensland, Materials Engineering, Brisbane, Qld 4072 Australia ,Michigan Technological University, Received 20 August 2013, ScienceDirect, Journal of Magnesium and Alloys 1 (2013) 177e200,www.elsevier.com/journals/journal-of-magnesium-and-alloys/2213-9567
- [17] Dictionary of Metals, Edited by Harold M. Cobb, ASM international.
- [18] D.S. Gandel, N. Birbilis, M.A. Easton, M.A. Gibson, 'Influence of Manganese, Zirconium and Iron on the Corrosion of Magnesium' Corrosion & prevention, 2010, Paper 118, p. 1.
- [19] Kelvii Wei Guo*, "A Review of Magnesium/Magnesium Alloys Corrosion and its Protection" Recent Patents on Corrosion Science, 2010, 2, 13-21
- [20] STEPHENS R I, SCHRADER C D, LEASE K B. Corrosion fatigue Of AZ91E-T6 cast magnesium alloy in a 3.5 percent NaCl aqueous environment.[J]Journal of engineering technology
- [21] ELIEZER D, UZAN P, AGHION E. Effect of second phases on the corrosion behavior of magnesium alloys [J]. Material Science 2003,419-422: 857-866
- [22] SONG G Recent progress in corrosion and protection of magnesium alloys [J]. Advance Engineering Materials, 2005,7(7): 563-586.
9. Copyright:
- This material is "Mrs.Minal Sanjay Dani, Dr. Vandana J Rao, Dr. Indravadan B Dave"'s paper: Based on "A Review on Corrosion behaviour of Mn added Magnesium and its alloys".
- Paper Source: DOI 10.17148/IARJSET.2015.21212
This material was summarized based on the above paper, and unauthorized use for commercial purposes is prohibited.
Copyright © 2025 CASTMAN. All rights reserved.