This article introduces the paper "Optimization in Novel Partial-Solid High Pressure Aluminum Die Casting by Taguchi Method," providing a comprehensive overview of its key aspects for experts and those interested in die casting technology.
1. Overview:
- Title: Optimization in Novel Partial-Solid High Pressure Aluminum Die Casting by Taguchi Method
- Author: Yekta Berk Suslu, Mehmet Sirac Acar, Mithat Senol, Muammer Mutlu, and Ozgul Keles
- Publication Year: 2018
- Publishing Journal/Academic Society: The Minerals, Metals & Materials Society (TMS) - Light Metals 2018 Conference Proceedings
- Keywords: High pressure die casting, Partial-solid processing, Aluminum, Taguchi method, Optimization
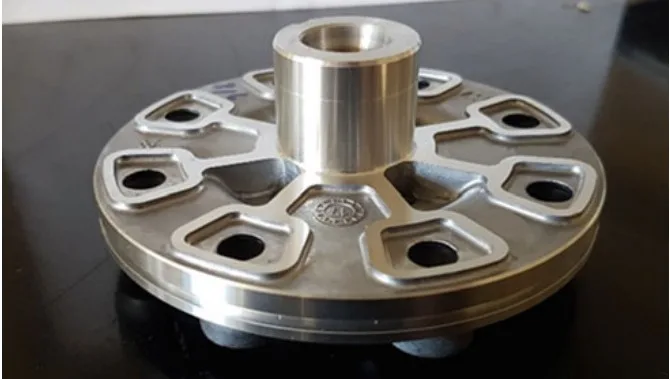
2. Research Background:
- Social/Academic Context of the Research Topic:
- High pressure die casting (HPDC) is a crucial manufacturing process for producing components in essential industries like automotive, aviation, and white goods.
- HPDC's advantage lies in its low cycle time due to rapid solidification, enabling mass production.
- However, porosity and shrinkage are significant defects in HPDC that reduce the efficiency and quality of the produced parts.
- Limitations of Existing Research:
- Traditional HPDC methods often face challenges in minimizing porosity and shrinkage defects.
- While techniques like vacuuming, chill vents, and injection velocity adjustments can be helpful, they may not fully eliminate these issues.
- Conventional casting methods, including HPDC, are susceptible to defects like porosity, shrinkage, and cold slug defects.
- Necessity of the Research:
- To overcome the limitations of traditional HPDC and enhance part quality, partial-solid casting is explored as a solution.
- Partial-solid casting, specifically using the Gas Induced Semi-Solid (GISS) technique, offers a way to modify the microstructure and improve mechanical properties.
- Optimizing the GISS-HPDC process is necessary to fully realize its potential in producing high-quality components with reduced defects.
- The Taguchi method, a design of experiments approach, is identified as a useful tool for optimizing the complex parameters involved in GISS-HPDC.
3. Research Purpose and Research Questions:
- Research Purpose:
- To optimize the parameters of the Gas Induced Semi-Solid (GISS) technique integrated with High Pressure Die Casting (HPDC) for producing "A" class quality partial-solid aluminum automotive parts.
- To determine the effects of key process parameters on porosity levels and microstructural characteristics in GISS-HPDC.
- Key Research Questions:
- How do melt temperature, gas blowing time, second phase velocity, and gate thickness affect the porosity ratio in partial-solid HPDC using the GISS technique?
- What are the optimal levels for melt temperature, gas blowing time, second phase velocity, and gate thickness to minimize porosity and achieve "A" class quality in aluminum automotive parts produced by GISS-HPDC?
- How does the GISS technique influence the microstructure of HPDC aluminum parts, specifically regarding the formation of globular structures and the distribution of intermetallic phases?
- Research Hypotheses: (Implicit in the research design)
- By applying the Taguchi method, optimal combinations of melt temperature, gas blowing time, second phase velocity, and gate thickness can be identified to minimize porosity in GISS-HPDC aluminum automotive parts.
- The GISS technique will promote the formation of a globular microstructure in HPDC aluminum parts, leading to improved mechanical properties and reduced porosity compared to conventional HPDC.
- Gate thickness, melt temperature, second phase velocity, and gas blowing time will have varying degrees of influence on the porosity level in GISS-HPDC, and their relative importance can be determined through Taguchi analysis.
4. Research Methodology:
- Research Design:
- Design of Experiments (DOE) approach using the Taguchi L9 orthogonal array.
- Four parameters, each at three levels, were investigated to optimize the GISS-HPDC process.
- The L9 orthogonal array allowed for the study of 4 parameters with only 9 experimental runs, significantly reducing the number of experiments compared to a full factorial design.
- Data Collection Method:
- Experimental Casting: 9 casting trials were conducted based on the L9 orthogonal array, using an EN AC 48000 (AlSi12CuNiMg) aluminum alloy. 15 specimens were produced for each experiment using cold chamber HPDC machines with 7700 kN clamping force. Parts were machined after casting.
- Radiography Testing (Non-destructive): Bosello Industrial X-Ray scanner (115 kV, 1.5 mA) was used to assess porosity levels in the 5th, 10th, and 15th specimens from each experiment. Porosity was graded from 4 (best - A class) to 1 (worst - D class).
- Microstructural Characterization (Destructive): The 15th specimen from each experiment was used for microstructural examination.
- Optical Microscopy: Nikon Eclipse LV100ND optical microscope was used to observe the microstructure after metallographic preparation (grinding, polishing, etching with Keller's reagent for 10s).
- Scanning Electron Microscopy (SEM) and Energy Dispersive Spectroscopy (EDS): FESEM, JSM 7000 F was utilized for morphological analysis and to identify intermetallic phases.
- Analysis Method:
- Radiography Quality Score: Average quality score was calculated from the radiography grades of the 5th, 10th, and 15th specimens for each experiment.
- Signal-to-Noise (S/N) Ratio Analysis: S/N ratios were calculated based on the "Larger is better" quality characteristic, using the equation:
-10 log₁₀ (Σ(1/Yᵢ²)/n)
where Yᵢ are the quality scores for each specimen in an experiment, and n is the number of specimens (n=3 in this case, as 3 specimens were graded per experiment). Minitab 18 software was used for S/N ratio analysis.- Main Effects Plot for S/N Ratios: Generated to visualize the effect of each parameter level on the S/N ratio and identify optimal levels.
- Confirmation Experiment: A confirmation casting experiment was conducted using the optimal parameter combination identified by the Taguchi analysis to validate the results.
- Research Subjects and Scope:
- Material: Commercial EN AC 48000 (AlSi12CuNiMg) aluminum cast alloy. Chemical composition is provided in Table 2: Si (12%), Fe (0.21%), Mn (1.2%), Cu (0.9%), Ni (0.81%), Mg (0.74%), Al (Balance).
- Part Type: Automotive parts (specific geometry shown in Figure 1, described as "Produced part, cast and machined").
- Process: Partial-Solid High Pressure Die Casting (GISS-HPDC).
- Parameters Investigated:
- A: Melt Temperature (°C): Levels: 1 (650±5), 2 (670±5), 3 (690±5)
- B: Gas Blowing Time (s): Levels: 1 (0), 2 (5), 3 (10)
- C: 2nd Phase Velocity (m/s): Levels: 1 (4), 2 (4.5), 3 (5)
- D: Gate Thickness (mm): Levels: 1 (1.8), 2 (2.4), 3 (3.5)
- Quality Characteristic: Porosity level (minimized).
5. Main Research Results:
- Key Research Results:
- Optimal Parameter Combination: Based on S/N ratio analysis, the optimal parameter combination was determined to be A3B3C2D1, corresponding to:
- Melt Temperature: Level 3 (690 ± 5 °C)
- Gas Blowing Time: Level 3 (10 s)
- 2nd Phase Velocity: Level 2 (4.5 m/s)
- Gate Thickness: Level 1 (1.8 mm)
- Parameter Importance: Gate thickness was identified as the most effective parameter in reducing porosity, followed by melt temperature, second phase velocity, and gas blowing time (in decreasing order of influence based on the gap between minimum and maximum S/N values in Figure 4).
- Porosity Reduction and "A" Class Quality: The confirmation experiment using the optimal parameters (A3B3C2D1) resulted in "A" class quality parts, with radiography scores of 4, 4, and 4 for the 5th, 10th, and 15th specimens, respectively. This validated the Taguchi optimization and demonstrated successful production of high-quality parts.
- Microstructural Changes: GISS-applied specimens exhibited finer and more globular primary α-Al phase distribution compared to conventional HPDC. Non-dendritic microstructure was achieved.
- Intermetallic Phase Identification: SEM-EDS analysis identified intermetallic phases as α-Al matrix, Al-Cu-Ni mixtures, Al₃FeSi, Al₁₅Si₂(FeMn)₃, Al₂Cu, and Al₅(FeMn)Si₁.₅.
- Optimal Parameter Combination: Based on S/N ratio analysis, the optimal parameter combination was determined to be A3B3C2D1, corresponding to:
- Statistical/Qualitative Analysis Results:
- Table 4: Presents the radiography grades (Y₁, Y₂, Y₃) for the 5th, 10th, and 15th specimens for each of the 9 experiments, the average quality score (Ỹ), and the calculated S/N ratio. Experiment 9, with the highest average quality score (4.00) and S/N ratio (12.04), represents the best result among the L9 experiments.
- Figure 3: Shows radiographic images of "A" class (best) and "D" class (worse) quality parts, visually demonstrating the difference in porosity levels. Figure 3a shows almost no porosities ("A" class), while Figure 3b shows porosities as white circular dots ("D" class).
- Figure 4: Main effects plot for S/N ratios, illustrating the influence of each parameter and level on the S/N ratio. It visually confirms gate thickness as the most influential parameter.
- Figure 5: Radiographic test results for the confirmation experiment specimens (5th, 10th, and 15th), showing consistently high quality (radiography score 4 for all).
- Figure 6: Optical microscope images of 15th specimens from all 9 experiments, showing the microstructural variations across different parameter combinations. Globular microstructure is evident in GISS-applied specimens.
- Figure 7: Microstructure of the Taguchi confirmation experiment specimen, showing broken dendrites and globular α-Al particles.
- Figure 8: SEM analysis BSE images of the Taguchi confirmation test specimen, revealing different intermetallic phases (Chinese letter-like, needle-like) and regions for EDS analysis.
- Table 5: EDS analysis results (wt%) for different regions in Figure 8d, identifying the possible intermetallic phases based on elemental composition and literature comparison.
- Data Interpretation:
- The S/N ratio analysis effectively identified the optimal parameter settings for minimizing porosity in GISS-HPDC.
- The confirmation experiment validated the Taguchi method's effectiveness in optimizing the process.
- The GISS technique successfully promoted a globular microstructure, which is known to improve mechanical properties.
- Gate thickness emerged as the most critical parameter for porosity reduction in this specific GISS-HPDC application.
- Gas blowing time, while important, needs to be optimized as excessive blowing time can negatively impact melt characteristics and potentially induce defects. The chosen 10s blowing time was deemed ideal to stabilize production cycle time without adverse effects.
- Figure Name List:
- Fig. 1 Produced part, cast and machined
- Fig. 2 Gas blowing process
- Fig. 3 "A" class as best and "D" class as worse quality
- Fig. 4 Main effects plot for the results
- Fig. 5 Radiographic test results for the parts taken in 5th, 10th and 15th specimens for the confirmation experiment
- Fig. 6 Optical microscope images taken from 15th samples
- Fig. 7 Microstructure of Taguchi confirmation experiment specimen
- Fig. 8 SEM analysis BSE images of Taguchi confidence test specimen; a General view, b Chinese letter like intermetallics, c Needle like intermetallics, d Region consists different type of intermetallic phases

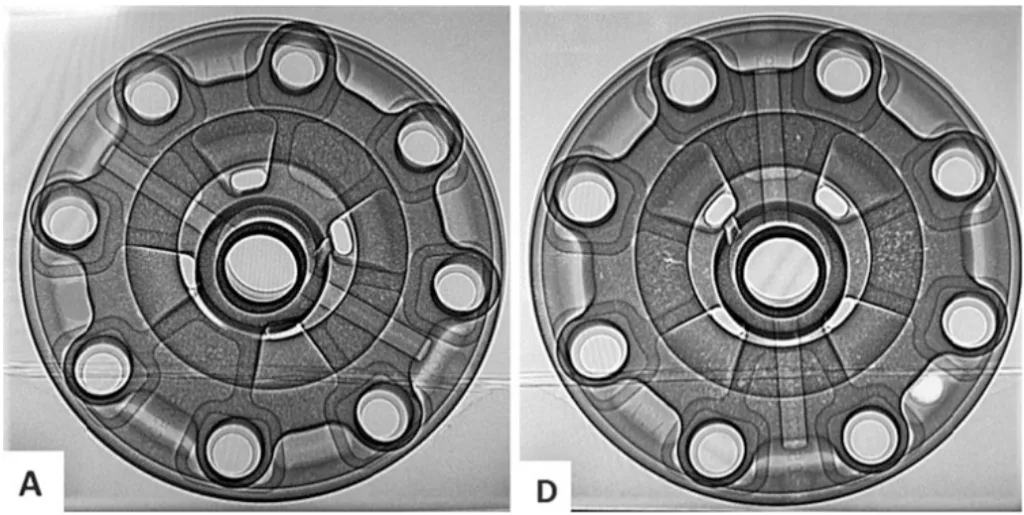
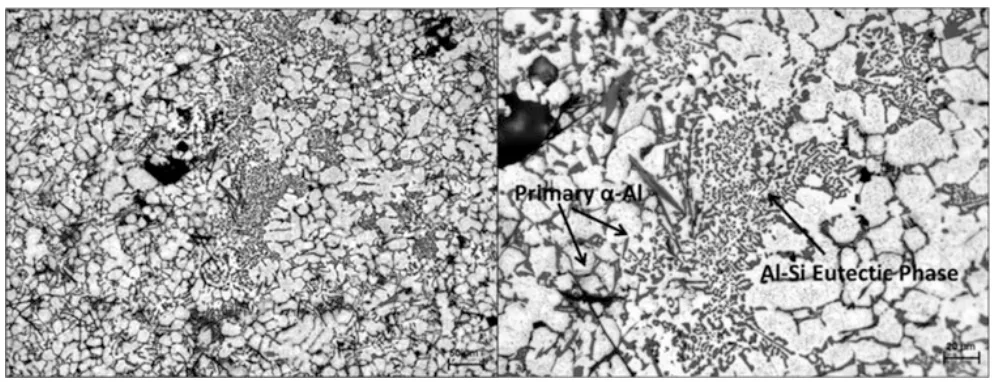
6. Conclusion and Discussion:
- Summary of Main Results:
- The Taguchi L9 orthogonal array method was successfully applied to optimize the GISS-HPDC process for producing aluminum automotive parts.
- Optimal process parameters (A3B3C2D1: Melt Temperature 690 ± 5 °C, Gas Blowing Time 10 s, 2nd Phase Velocity 4.5 m/s, Gate Thickness 1.8 mm) were identified to minimize porosity and achieve "A" class quality.
- Gate thickness was found to be the most influential parameter on porosity.
- GISS technique resulted in non-dendritic, globular microstructure.
- Intermetallic phases (α-Al, Al-Cu-Ni, Al₃FeSi, Al₁₅Si₂(FeMn)₃, Al₂Cu, Al₅(FeMn)Si₁.₅) were identified.
- Confirmation experiment validated the optimization results.
- Academic Significance of the Research:
- This study demonstrates the effective application of the Taguchi method for optimizing a novel manufacturing process like GISS-HPDC.
- It provides valuable insights into the influence of key process parameters on porosity and microstructure in partial-solid die casting of aluminum alloys.
- The research contributes to the understanding of the GISS technique and its potential for enhancing HPDC part quality.
- Practical Implications:
- The optimized GISS-HPDC process can be directly implemented in industrial settings to produce high-quality aluminum automotive parts with reduced porosity and improved performance.
- The identified optimal parameter settings serve as a valuable guideline for manufacturers using GISS-HPDC with EN AC 48000 alloy and similar part geometries.
- The study highlights the importance of gate thickness in controlling porosity in GISS-HPDC, providing practical guidance for die design.
- Limitations of the Research:
- The optimization was performed for a specific aluminum alloy (EN AC 48000) and a particular automotive part geometry. The optimal parameters may need to be re-evaluated for different alloys or part designs.
- The study focused on porosity as the primary quality characteristic. Other aspects of part quality, such as mechanical properties and surface finish, could be further investigated.
- The range of parameters and levels investigated were limited to those defined in Table 3. Exploring a wider range or finer levels might reveal further optimization potential.
7. Future Follow-up Research:
- Directions for Follow-up Research:
- Investigate the effect of optimized GISS-HPDC parameters on mechanical properties (tensile strength, yield strength, elongation, hardness, fatigue resistance) of the produced parts.
- Explore the applicability of the optimized GISS-HPDC process to other aluminum alloys and different part geometries.
- Further optimize the GISS process parameters by considering additional factors such as mold temperature, injection pressure profile, and cooling rate.
- Investigate the influence of different inert gases (e.g., argon, nitrogen) and gas injection methods on the GISS process and part quality.
- Conduct detailed analysis of the formation mechanisms of intermetallic phases in GISS-HPDC and their impact on mechanical properties.
- Explore the use of advanced simulation tools to further optimize the GISS-HPDC process and predict part quality.
- Areas Requiring Further Exploration:
- Long-term performance and reliability of parts produced by optimized GISS-HPDC in real-world automotive applications.
- Cost-effectiveness and scalability of the GISS-HPDC process for mass production.
- Environmental impact assessment of the GISS-HPDC process compared to conventional HPDC.
8. References:
- http://www.aluminum.org/product-markets (August, 2017)
- Bonollo F, Gramegna N, Timelli G (2015) High-pressure die-casting: Contradictions and challenges. JOM, 67(5), 901–908.
- Atkinson H (2010) Semisolid processing of metallic materials. Materials Science and Technology, 26(12): 1401-1413.
- Czerwinski F (2006) The basics of modern semi-solid metal processing. JOM, 58(6): 17.
- Nafisi S, Gomashchi R (2016) Semi-solid processing of aluminum alloys, Springer, Switzerland, 9.
- Rice CS, Mendez PF (2001) Slurry-Based Semi-Solid DIE CASTING. Advanced materials & processes, 159(10): 49-52.
- Wannasin J et al. (2008) Development of the Gas Induced Semi-Solid metal process for aluminum die casting applications. In Solid State Phenomena, 141: 97-102.
- Flemings MC, Yurko JA, Martinez RA (2004) Solidification processes and microstructures. Proceedings of the TMS Annual Meeting, 3-14.
- Wannasin J, Janudom S, Rattanochaikul T, Canyook R, Burapa R, Chucheep T, Thanabumrungkul S (2010) Research and development of gas induced semi-solid process for industrial applications. Transactions of Nonferrous Metals Society of China 20: 1010-1015.
- Curle UA (2010) Semi-solid near-net shape rheocasting of heat treatable wrought aluminum alloys. Transactions of Nonferrous Metals Society of China (20)9: 1719-1724.
- Mahathaninwong N, Plookphol T, Wannasin J, Wisutmethangoon S (2012) T6 heat treatment of rheocasting 7075 Al alloy. Materials Science and Engineering: A, 532: 91-99.
- Verran GO, Mendes RPK, Dalla Valentina LVO (2008) DOE applied to optimization of aluminum alloy die castings. Journal of materials processing technology, 200.1: 120-125.
- Syrcos GP (2003) Die casting process optimization using Taguchi methods. Journal of materials processing technology, 135.1: 68-74.
- Thanabumrungkul S, et al. (2010) Industrial development of gas induced semi-solid process. Transactions of Nonferrous Metals Society of China 20: 1016-1021.
- Jumpol W, Wannasin J, Janudom S, Canyook R, Plookphol T, Wisutmethangoon S (2015) Effects of Solid Fractions in a Slurry Die Casting Process on Defects of 7075 Aluminum Alloy. In Applied Mechanics and Materials, 752: 7–10.
- Wannasin J, Martinez RA, Flemings MC (2006) Grain refinement of an aluminum alloy by introducing gas bubbles during solidification. Scripta Materialia, 55.2: 115-118.
- Canyook R, et al. (2012) Characterization of the microstructure evolution of semi-solid metal slurry during the early stages. Acta Materialia, 60.8: 3501-3510.
- Shabestari SG, Honarmand M, Saghafian H. (2015) Microstructural evolution of A380 aluminum alloy produced by gas-induced semi-solid technique (GISS). Advances in Materials and Processing Technologies, 1(1-2), 155-163.
- Janudom S, Rattanochaikul T, Burapa R, et al. (2010) Feasibility of semi-solid die casting of ADC12 aluminum alloy. Transactions of Nonferrous Metals Society of China 20(9);1756–1762.
- Krendelsberger N, Weitzer F, Schuster JC. (2007) On the Reaction Scheme and Liquidus Surface in the Ternary System Al-Fe-Si. Metallic Materials Transactions, 38A: 1681-1691.
- Bosselet F et al. (2004) Affinement expérimental de l'isotherme Al-Fe-Si à 1000 K. Journal de Physique IV (Proceedings), 122: 41-46.
- Dinnis CM, Taylor JA, Dahle AK (2005) As-cast morphology of iron-intermetallics in Al-Si foundry alloys. Scripta Materialia, 53 (8): 955-958.
- Irizalp SG, Saklakoglu N, (2014) Effect of Fe-rich intermetallics on the microstructure and mechanical properties of thixoformed A380 aluminum alloy. Engineering Science and Technology, an International Journal, 17(2): 58-62.
- Mohamed AMA, Samuel AM, Samuel FH, Doty HW (2009) Influence of additives on the microstructure and tensile properties of near-eutectic Al-10.8% Si cast alloy. Materials & Design, 30 (10): 3943-3957.
9. Copyright:
- This material is Yekta Berk Suslu, Mehmet Sirac Acar, Mithat Senol, Muammer Mutlu, and Ozgul Keles's paper: Based on Optimization in Novel Partial-Solid High Pressure Aluminum Die Casting by Taguchi Method.
- Paper Source: https://doi.org/10.1007/978-3-319-72284-9_40
This material was summarized based on the above paper, and unauthorized use for commercial purposes is prohibited.
Copyright © 2025 CASTMAN. All rights reserved.