This article introduces the paper "New Generation of Brake Callipers to Improve Competitiveness and Energy Savings in Very High Performance Cars" published by ResearchGate.
1. Overview:
- Title: New Generation of Brake Callipers to Improve Competitiveness and Energy Savings in Very High Performance Cars
- Author: Ivano Gattelli, Gianluigi Chiarmetta, Marcello Boschini, Renzo Moschini, Mario Rosso, Ildiko Peter
- Publication Year: September 2014
- Publishing Journal/Academic Society: Solid State Phenomena
- Keywords: semi-solid casting, rheocasting, brake callipers, ceramic cores, high performance cars
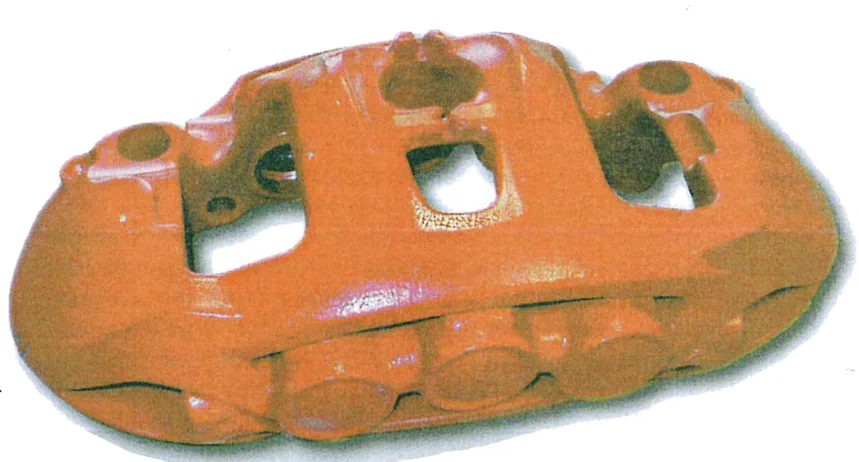
2. Abstracts or Introduction
Recent research in materials science and production processes has focused on energy consumption and weight reduction. Light alloys and semi-solid processes are promising for automotive and aeronautical applications. Effective microstructure control is critical for component mechanical behavior. Forging is optimal but expensive. Casting is more economical, but can have defects. Semi-solid processes reduce the gap between casting and forging, allowing better defect control. New semi-solid methods like squeeze casting, thixoforming, and rheocasting can produce components with properties comparable to forging. Despite half a century of development, more rheological data is needed. These processes reduce defects, improve surface quality, and dimensional accuracy. A key challenge is transferring technology from research to affordable mass production. This paper presents further optimization steps of a rheocasting process for high-performance industrial components, particularly brake callipers, to improve competitiveness and energy savings in high-performance cars, using special ceramic lost cores. This method enhances mechanical properties and aesthetic characteristics compared to gravity casting, while maintaining adequate strength, favoring use in high-performance cars and future applications.
3. Research Background:
Background of the Research Topic:
The research is situated in the context of increasing demand for energy consumption and weight reduction in materials science and production processes, particularly for industrial automotive and aeronautical applications. Light alloys and semi-solid processes are identified as promising solutions to meet these demands. The control of microstructure is emphasized as critical for determining the mechanical behavior of produced components.
Status of Existing Research:
Forging is recognized as the best method for producing high-performance components, but it is also the most expensive. Casting technologies are more economically competitive, but traditionally suffer from defects such as voids, cavities, inclusions, and oxides, and do not achieve the same performance levels as forging. Semi-solid processes are emerging as a way to bridge this gap, offering improved defect control. Existing research is exploring semi-solid methods like squeeze casting, thixoforming, and rheocasting to achieve comparable performance to forging through new manufacturing routes. However, there is a continued need for more detailed rheological data to further optimize these processes.
Necessity of the Research:
Despite significant advancements in semi-solid casting over the past half-century, there is still a demand for additional and more detailed rheological data to optimize these processes. Technological transfer from research labs to industry for affordable mass production remains a central challenge. There is a need to optimize production processes to enhance competitiveness and energy savings, particularly in high-performance automotive applications like brake callipers. The research aims to address these needs by further developing and optimizing a rheocasting process suitable for mass production of high-performance components.
4. Research Purpose and Research Questions:
Research Purpose:
The principal goal of this research is to improve the competitiveness and energy savings in high performance cars by developing a new generation of brake callipers using an optimized rheocasting process. This involves achieving enhanced mechanical properties and superior esthetical characteristics compared to gravity casting, while maintaining adequate strength for brake callipers.
Key Research:
The key research focuses on the production of brake callipers using a rheocasting process and the implementation of special ceramic lost cores in the manufacturing process. The research investigates the mechanical properties, microstructure, and feasibility of mass production for these rheocast brake callipers.
5. Research Methodology
Research Design:
The research employs an experimental design focused on the development and optimization of a rheocasting process for brake calliper production. It involves using an innovative rheocasting process developed by ATS Company with a TCS vertical hydraulic press Rotorone 400 tons. The process uses A357 alloy and ceramic lost cores.
Data Collection Method:
Data was collected through:
- Radiographic analysis: To verify the integrity of samples and detect defects.
- Microstructural characterization: Using optical microscopy (OM, Zeiss Observer Dim model) to analyze the microstructure of the produced callipers.
- Mechanical characterization: Including tensile tests (Galdabini Sun 5 model) to assess mechanical properties and non-destructive testing (NDT, Bosello SRE MAX 225 KVtype) to study soundness.
Analysis Method:
The analysis methods included:
- Comparison of microstructure: Comparing the microstructure of brake callipers produced by gravity casting and rheocasting.
- Evaluation of mechanical properties: Analyzing tensile test data to assess the strength and elongation of rheocast samples and comparing them to standard requirements (UNI EN 1706/2010).
- Radiographic image analysis: Interpreting radiographic images to identify and evaluate defects in the castings.
Research Subjects and Scope:
The research subjects are brake callipers produced using A357 aluminum alloy via rheocasting process with ceramic lost cores. The scope of the research is focused on optimizing the rheocasting process for mass production of these brake callipers and evaluating their mechanical and esthetical properties.
6. Main Research Results:
Key Research Results:
- Rheocasting process using ceramic cores was successfully implemented for brake calliper production.
- Rheocast brake callipers exhibited a globular and fine microstructure, in contrast to the dendritic microstructure of gravity cast callipers (Figure 2).
- Enhanced mechanical properties, in terms of stiffness, bending, and compression strength, were achieved using ceramic cores.
- Superior esthetical characteristics were obtained compared to gravity casting.
- Weight reduction of about 5% was achieved compared to traditional methods.
- Tensile test results for rheocast A357 T6 alloy exceeded the standard requirements (UNI EN 1706/2010) for sand cast and chill cast alloys (Table 2).
- Radiographic analysis revealed a reduction in defects in rheocast components (Figure 3).
- Validation bench tests and severe braking cycle tests demonstrated high fracture toughness and reliability of the rheocast components, even in the presence of minor defects.
Analysis of presented data:
- Table 1 shows the chemical composition (wt.%) of the A357 alloy used for brake calliper production, specifying the weight percentages of Si, Fe, Cu, Mn, Mg, Zn, Ti, and Al.
- Table 2 presents the average tensile properties of rheocast A357 T6 samples, including UTS (340±14 MPa), Yield Strength (302±4 MPa), and Elongation (4.135±2.7%). These values are compared to the standard requirements (UNI EN 1706/2010) for sand cast and chill cast A357 T6 heat treated alloy, showing that the measured values exceed the standard thresholds.
- Figure 1 is a photograph of the produced Brembo brake calliper using the rheocasting process.
- Figure 2 compares the microstructure of brake callipers produced by gravity casting (a) and rheocasting (b), showing a dendritic structure in (a) and a globular and fine microstructure in (b).
- Figure 3 is a radiographic image of the brake calliper, revealing the absence of significant defects in the investigated sample.
- Figure 4 shows microstructures of scraps from "worst case" castings, indicating the presence of some defects (bifilms).
Figure Name List:
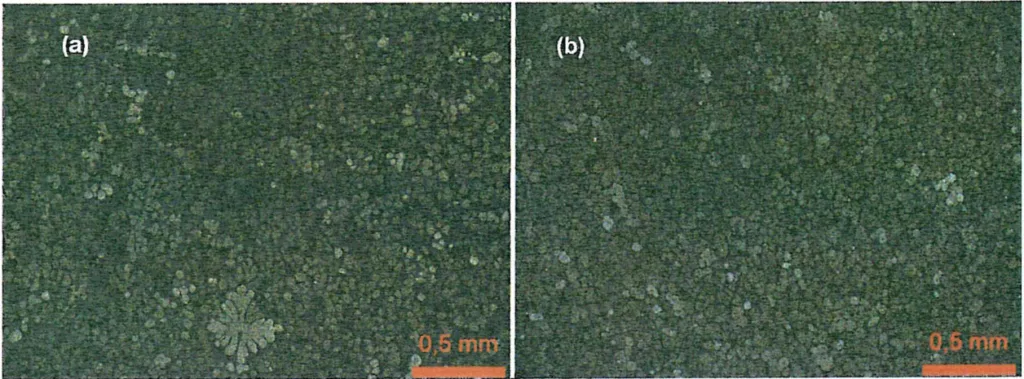
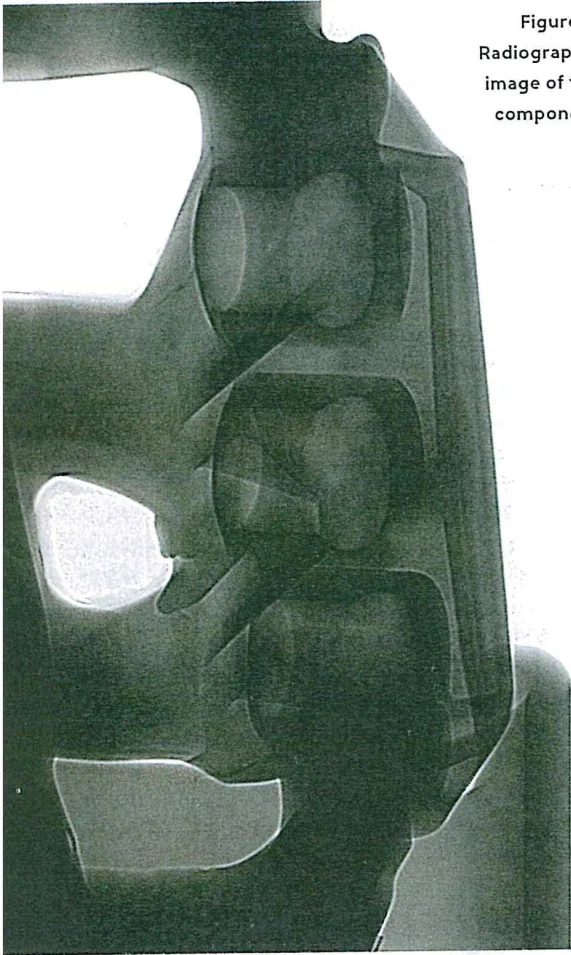
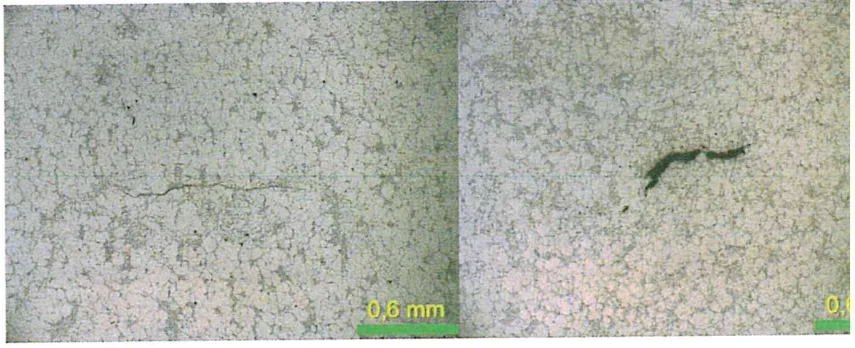
- Figure 1: Photograph of the produced Brembo brake calliper
- Figure 2: Microstructure of the brake calliper produced by gravity casting process (a) and by rheocasting process (b)
- Figure 3: Radiographic image of the component
- Figure 4: Microctructures of scraps showing the presence of some defects (bifilms)
7. Conclusion:
Summary of Key Findings:
The study successfully demonstrated the production of new generation brake callipers using an optimized rheocasting process with ceramic lost cores. The rheocast callipers exhibited improved microstructure, enhanced mechanical properties, superior esthetics, and weight reduction compared to gravity cast components. The use of ceramic cores enabled complex shapes and improved structural integrity. Testing confirmed high fracture toughness and reliability, even with minor defects.
Academic Significance of the Study:
This study contributes to the academic field by providing further insights into the application of rheocasting and ceramic core technologies for manufacturing high-performance automotive components. It demonstrates the effectiveness of semi-solid processing in reducing the performance gap between casting and forging. The research also provides valuable data on the mechanical properties and microstructure of rheocast A357 alloy, adding to the body of knowledge in semi-solid metallurgy.
Practical Implications:
The practical implications of this study are significant for the automotive industry, particularly for high-performance vehicle manufacturing. The developed rheocasting process offers a viable route for mass production of lightweight, high-performance brake callipers with improved energy efficiency and competitiveness. The use of ceramic cores allows for more complex and optimized designs, enhancing brake system performance and esthetics.
Limitations of the Study and Areas for Future Research:
The paper does not explicitly state limitations or future research areas. However, implicitly, future research could focus on:
- Further optimization of the rheocasting process parameters for different alloys and component geometries.
- Exploring the long-term durability and performance of rheocast brake callipers in real-world driving conditions.
- Investigating the cost-effectiveness of mass production using ceramic cores and rheocasting compared to traditional methods.
- Extending the application of this process to other high-performance automotive components and industries.
8. References:
- [1] Campbell F.C., Manufacturing technology for aerospace structural materials. Elsevier; 2006.
- [2] Warren A.S., Developments and challenges for aluminium - A Boeing perspective. Mater Forum 2004, 28 pp. 24-31.
- [3] Blanco M.I., The economics of wind energy. Renewable and Sustainable Energy Reviews 2009, 13, pp. 1372-1382.
- [4] Atkinson H.V., Liu D., (2008) "Microstructural coarsening of semi-solid aluminium alloys" Materials Science and Engineering A, Volume 496, 1-2, 25, pp. 439-446.
- [5] Barnes H., (1997) "Thixotropy - a review", Journal of Non-Newtonian Fluid Mechanics, 70, pp.1-33.
- [6] Cetin, A., Kalkanli, A., (2009) " Investigation of microporosity formation mechanisms in A356 aluminium alloy castings", International Journal of Microstructure and Materials Properties, Vol. 4, No.3, pp.377-385.
- [7] Curle U. A., Govender G., (2010), "Semi-solid rheocasting of grain refined aluminum alloy 7075", Transaction of nonferrous metals. Society of China 20, pp 832-836.
- [8] Rosso M., Peter I., Villa, R., (2008), "Effects of T5 and T6 heat treatments applied to rheocast A356 parts for automotive applications", Journal of Solid State Phenomena Vol. 141-143, pp. 237-242.
- [9] Rosso M., Peter I., "New frontiers for thixoforming", International Journal of Microstructure and Materials Properties, Vol. 8, Issue 1-2, 2013, pp. 113-124
- [10] Zhen Z., Ma Qian, Ji S., Fan Z., "The effects of rheo-diecasting on the integrity and mechanical properties of Mg-6Al-1Zn", Scripta Materialia 54 (2006), 207-211, ISSN 1359-6462.
- [11] Kaufmann H., Wabusses H., Uggowitzer J., "Aspects of the NRC semi-solid casting technology", Journal of Metallurgical and processing Technology, vol. 76, no1-2, pp. 70-75.
- [12] Rosso, M., Peter, I., Chiarmetta, G., Gattelli, 1., (2010), "Development of industrial components by advanced squeeze casting", Proceedings of the 11th International Conference on Semi-Solid Processing of Alloys and Composites, Beijing, 16th - 18th September.
- [13] Rosso M., Peter I., Chiarmetta G., Gatelli I., "Extremely light weight rheocast components for auto motive", Diffusion and Defect Data Pt.B: Solid State Phenomena 192-193, 2012, pp. 545-550.
- [14] Moschini R., Molina R., "Production of hollow components in high pressure die casting through the use of ceramic cores". HTDC, Vicenza Feb 2012.
- [15] Campbell J., Castings 2nd edn., pp. 443-452; 2003, Oxford, Butterworth-Heinemann.
- [16] Campbell J., Casting practice, 2004, Oxford, Butterworth Heinemann.
9. Copyright:
- This material is "Ivano Gattelli"'s paper: Based on "New Generation of Brake Callipers to Improve Competitiveness and Energy Savings in Very High Performance Cars".
- Paper Source: DOI: 10.4028/www.scientific.net/SSP.217-218.471
This material was summarized based on the above paper, and unauthorized use for commercial purposes is prohibited.
Copyright © 2025 CASTMAN. All rights reserved.