This introductory paper is the research content of the paper ["Manufacturing of Aluminum Alloy Parts from Recycled Feedstock by PIG Die-Casting and Hot Stamping"] published by [MDPI].
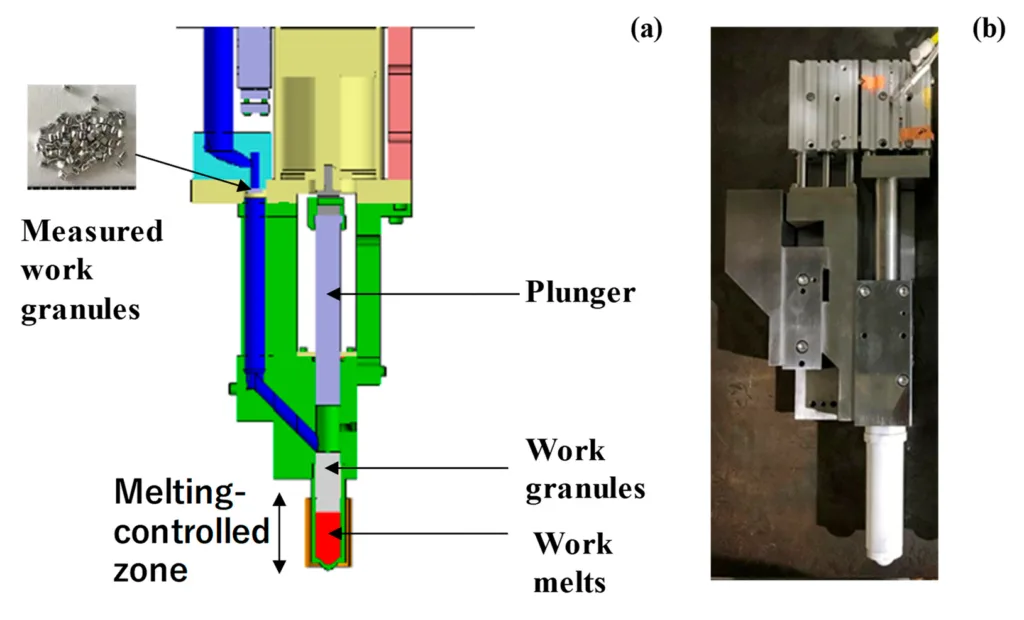
1. Overview:
- Title: Manufacturing of Aluminum Alloy Parts from Recycled Feedstock by PIG Die-Casting and Hot Stamping
- Author: Tatsuhiko Aizawa, Takeshi Kurihara and Hiroki Sakayori
- Publication Year: 2022
- Published Journal/Society: Lubricants
- Keywords: upward recycling; aluminum and aluminum alloys; pin injection gate; die casting; hot stamping; mechanical parts; heatsink; nitrogen supersaturation; TiAlN coating
2. Abstract
PIG (Pin-Injection-Gate) die-casting and hot stamping was developed for fabrication of small-sized and thin-walled aluminum alloy parts from the recycled feedstock. The pure aluminum and aluminum alloy granules were utilized as a feedstock model of recycled materials. The measured mass of granules with the estimated weight from 3D-CAD (Computer Aided Design) of products was poured into the PIG-nozzles before injection. After quickly melting by induction heating inside the PIG-nozzle units, the aluminum melts were injected into a die cavity through the PIG-nozzle. No furnaces and no crucibles were needed to store the melt aluminum stock in different from the conventional die-casting system. No clamping mechanism with huge loading machine was also needed to significantly reduce the energy consumption in casting. Much less wastes were yielded in these processes; the ratio of product to waste, or, the materials efficiency was nearly 100%. Nitrogen supersaturation and TiAlN coating were used to protect the PIG-nozzle and the stamping die surfaces from severe adhesion from aluminum melt. The pure aluminum gears and thin-walled mobile phone case were fabricated by this process. X-ray tomography proved that both products had no cavities, pores and shrinkages in their inside. Using the hot stamping unit, the micro-pillared pure aluminum heatsink was fabricated to investigate the holding temperature effect on the aspect ratio of micro-pillar height to width.
3. Research Background:
Background of the research topic:
Green manufacturing is a growing need in sustainable, carbon-neutral societies [1]. Solid-state recycling offers a method to reprocess used aluminum alloys without remelting [2].
Status of previous research:
Previous research includes solid-state recycling methods like warm and hot extrusion of aluminum alloy debris [3]. Conventional die-casting [4] is effective for near-net shaping but is energy-intensive. Existing PIG die-casting systems address some limitations of conventional die-casting [5-7], particularly for small-sized and thin-walled parts.
Need for research:
Conventional die-casting requires large furnaces and significant clamping forces, leading to high energy consumption and material waste. There's a need for a more efficient process, especially for recycling aluminum.
4. Research purpose and research question:
Research purpose:
To develop an advanced PIG die-casting system integrated with hot stamping for the efficient production of aluminum alloy parts from recycled feedstock.
Core research:
To demonstrate the capability of the integrated PIG die-casting and hot-stamping system to produce small-sized, thin-walled, and micro-textured aluminum parts with minimal waste and high material efficiency.
5. Research methodology
The research employed a combined PIG die-casting and hot stamping system.
-Research Design: Experimental, combining PIG die-casting and hot-stamping.
-Data Collection:
- Weight measurement of feedstock.
- Temperature monitoring during induction heating.
- High-speed video recording of free injection.
- Short-shot experiments for flow analysis.
- X-ray tomography for defect analysis.
- Laser microscopy and profilometry for surface texture measurement.
- SEM-EDX for elemental composition analysis.
- Micro-Vickers hardness testing.
-Analysis: - Visual analysis of flow patterns.
- Quantitative analysis of injection speed.
- Dimensional analysis of cast and stamped parts.
- Defect analysis via X-ray tomography.
- Tribological characterization of nitrided surfaces.
-Materials: - Pure aluminum (99.7% purity) granules.
- AA5052 aluminum alloy particles.
- AISI420J2 for PIG-nozzles and casting dies.
- AISI316 for warm/hot stamping dies.
-Surface Treatments: - Low-temperature plasma nitriding.
- TiAlN coating.
- Plasma printing for micro-texturing.
-Scope: Fabrication of pure aluminum gears, AA5052 mobile phone cases, and micro-pillared pure aluminum heatsinks.
6. Key research results:
Key research results and presented data analysis:
- Efficient Material Use: The PIG die-casting process achieved nearly 100% material efficiency.
- Free Injection: Free injection experiments showed an average injection velocity of 0.8 m/s (Figure 10).
- Aluminum Flow: Short-shot experiments demonstrated a flow pattern similar to plastic mold injection (Figure 11).
- Defect-Free Products: X-ray tomography confirmed the absence of cavities, pores, and shrinkages in the cast parts (Figure 12, Figure 13).
- Micro-Texturing: Hot stamping successfully created micro-pillars on a pure aluminum heatsink (Figure 14, Figure 15). The holding temperature significantly affected the aspect ratio of the micro-pillars.
- Tribological properties: The nitrogen supersatruation process was mainly utilized for protection of the PIG-nozzle and die surfaces from the adhesion of aluminum remelts. TiAlN coating onto the nitrided PIG-nozzle wrought well to protect the PIG-nozzle inner surface from severe adhesion of aluminum melts.

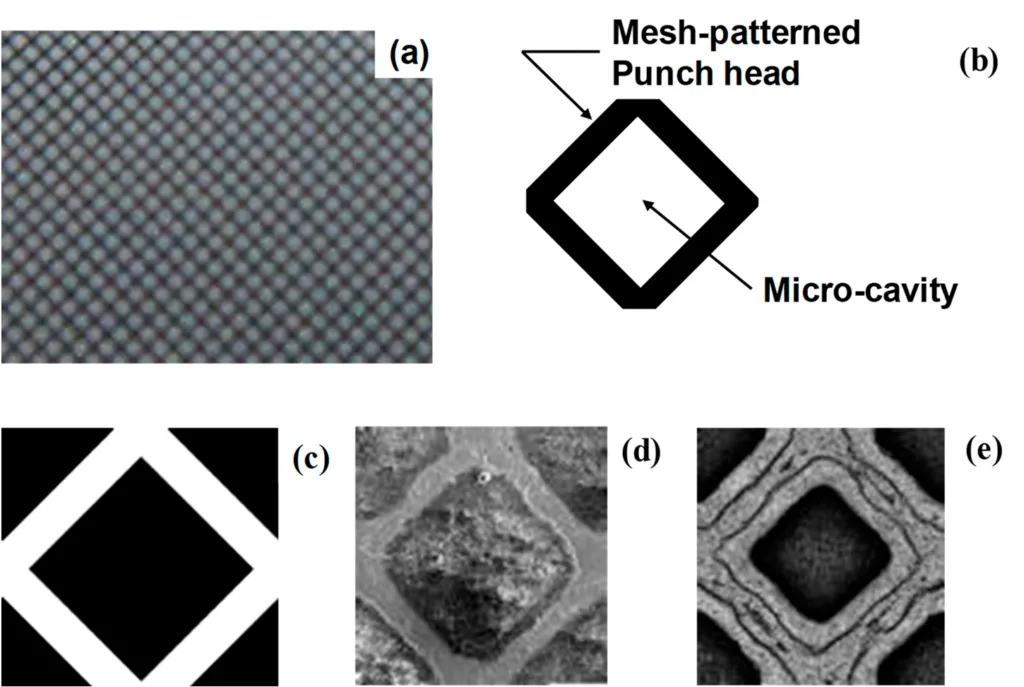
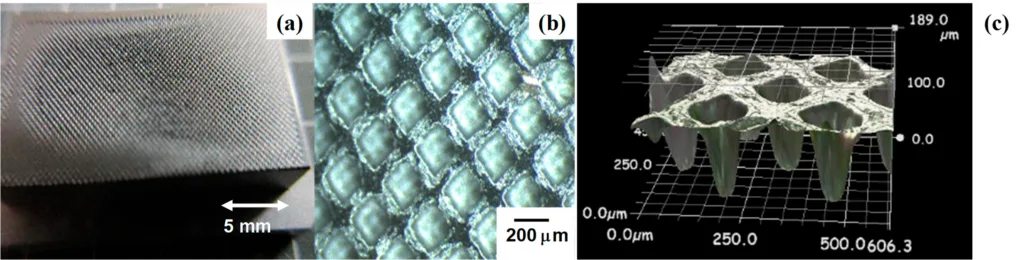

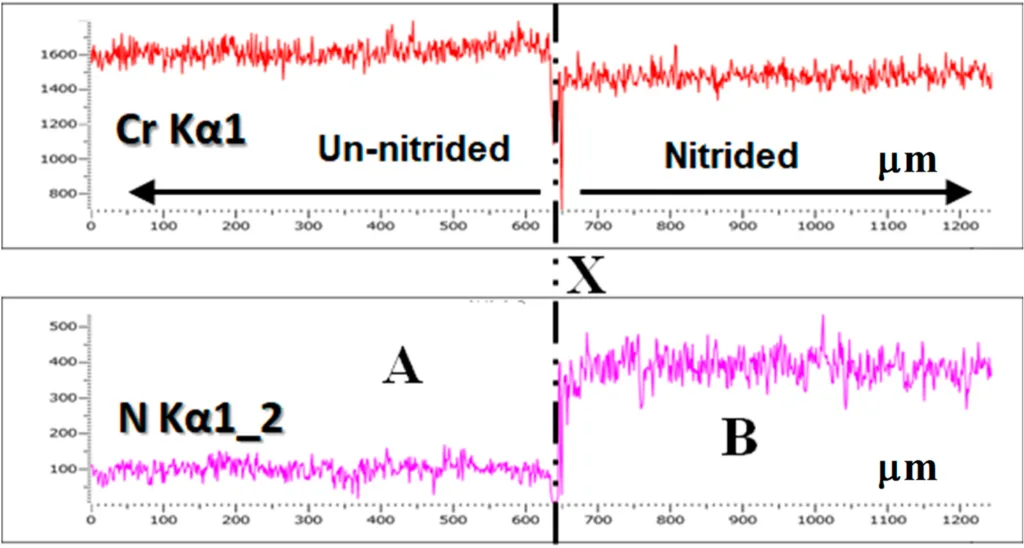
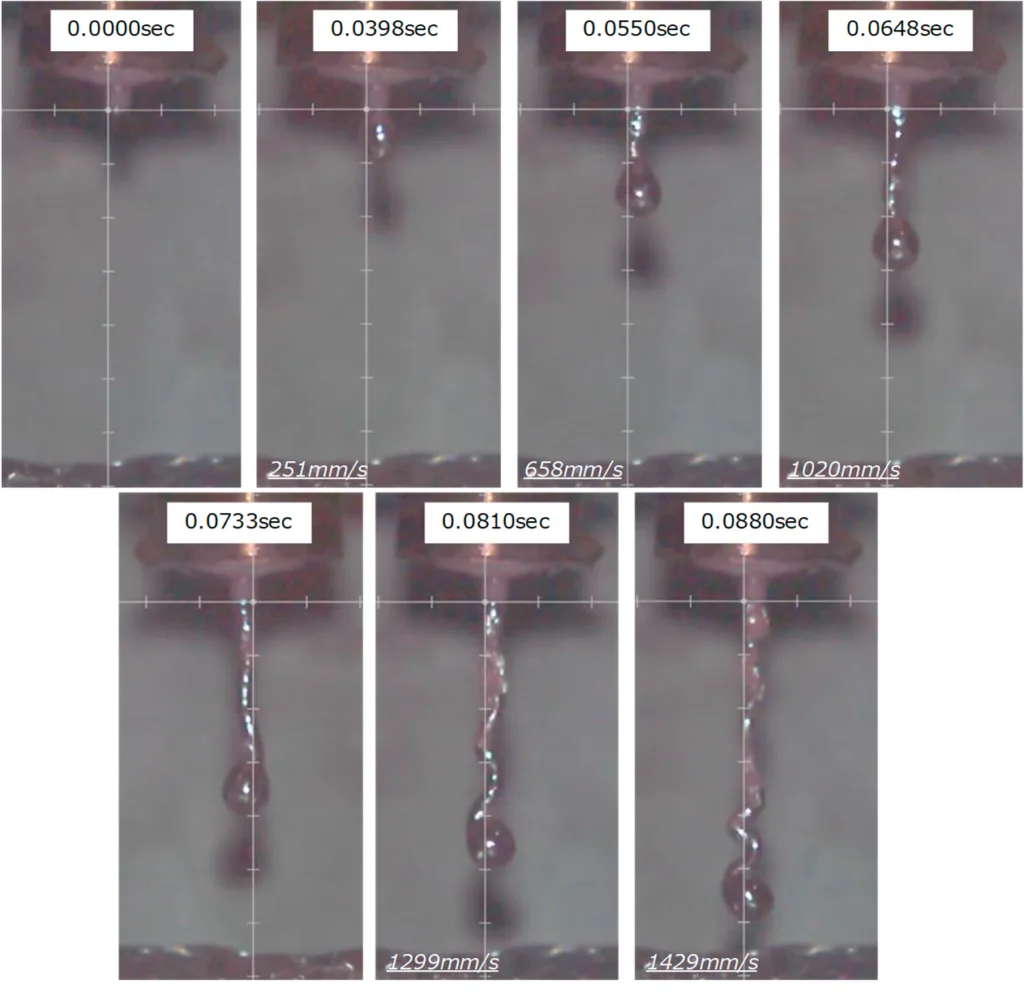

List of figure names:
- Figure 1. Two procedures to yield the aluminum products.
- Figure 2. Manufacturing system including the PIG die-casting and hot stamping unit.
- Figure 3. PIG-nozzle unit including the weight-measuring section, the plunger, the pressurizing tools, and the heating section.
- Figure 4. A low temperature plasma nitriding system.
- Figure 5. A plasma printing procedure with aid of the low temperature plasma nitriding.
- Figure 6. The mesh-textured AISI316 punch by the plasma printing.
- Figure 7. Nitrogen solute content and hardness depth profiles in the nitrided AISI20J2 materials for PIG-nozzles and dies.
- Figure 8. Comparison of the corrosion and erosion toughness between the un-nitrided and nitrided AISI420J2 surfaces.
- Figure 9. Distribution of chromium and nitrogen contents on the dipped AISI420J2 surfaces from "A" to "B" across "X".
- Figure 10. Dynamic behavior in the free injection of the aluminum melt from the PIG-nozzle outlet gate.
- Figure 11. A short-shot experiment by using the double PIG-nozzle units for PIG die-casting.
- Figure 12. PIG die-cast, small-sized gear block by using a single PIG-nozzle unit.
- Figure 13. PIG die-cast, thin-walled AA5052 mobile phone case by using the double PIG-nozzle units.
- Figure 14. Warm stamping of pure aluminum solidified preform for microtexturing its surface.
- Figure 15. Effect of the holding temperature during the hot stamping on the microtexture formation.
7. Conclusion:
Summary of key findings:
The integrated PIG die-casting and hot stamping system successfully fabricated small-sized, thin-walled, and micro-textured aluminum parts from recycled feedstock with high material efficiency and minimal defects. Nitrogen supersaturation and TiAlN coating effectively protected the tooling from adhesion wear. The holding temperature in hot stamping significantly influenced the micro-pillar aspect ratio.
- Academic significance: The research demonstrates a novel approach to aluminum recycling and manufacturing, combining PIG die-casting and hot stamping. It provides insights into the flow behavior of aluminum melts in the PIG system and the effect of surface treatments on tool life.
- Practical implications: The developed system offers a more sustainable and efficient alternative to conventional die-casting, reducing energy consumption and material waste. It is suitable for producing small, complex aluminum parts with high precision.
8. References:
- [1] Edwards, N. With green aluminum flowing, manufactures struggle to make product ESG top priority. Forbes 22 July 2020.
- [2] Aizawa, T.; Luangvaranunt, T.; Kondoh, K. Solid state recycling from green wastes to aluminum alloys with high material efficiency. J. JIM 2001, 65, 581–588.
- [3] Jeong, M.-S.; Lee, S.-Y.; Lee, I.-K.; Lee, S.-K.; Kim, D.; Cho, Y.-J.; Ko, D.-C. Green alternative aluminum extrusion process through process convergence. Int. J. Prec. Eng. Manuf. 2014, 15, 1173–1177.
- [4] Hartlieb, M.; Anderson, K. Die casting. 2A. In Aluminum Science and Technology; ASM International: Almere, The Netherlands, 2018.
- [5] Aizawa, T.; Yamaguchi, T.; Sakayori, H. JP-Patent 2019 with P19HS-001, 31 December 2019.
- [6] Aizawa, T.; Yamaguchi, T.; Sakayori, H. Die Casting System and Manufacturing Procedure of Die Cast Products. JP-Patent 2021 with P21SL-001, 31 December 2021.
- [7] Aizawa, T.; Yamaguchi, T.; Sakayori, H. Metal Forming System and Production Procedure. JP-Patent 2021 with P21SL-002, 31 December 2021.
- [8] Aizawa, T.; Kurihara, T.; Yamaguchi, T.; Sakayori, H. Near-net shaping of aluminum alloy parts by pin-injection-gate die-casting. In Proceedings of the 13th AWMFT, Shanghai, China, 6 December 2021; pp. 253–262.
- [9] Funazuka, T.; Dohda, K.; Takatsuji, N.; Hu, C.; Ngernbamrung, S. Effect of die coating on surface crack depth of hot extruded 7075 aluminum alloy. Friction 2022, 143, 21–32.
- [10] Aizawa, T. Low Temperature Plasma Nitriding of Austenitic Stainless Steels. Chapter 3 in Stainless Steels and Alloys; IntechOpen: London, UK, 2019; pp. 31–50.
- [11] Aizawa, T.; Dohda, K.; Shiratori, T. Nano-structured tribo-coating for cold and hot stamping. In Proceedings of the 52nd ICFG Plenay Meeting, San Sebastian, Spain, 16 September 2019; pp. 116–123.
- [12] Shiratori, T.; Aizawa, T.; Saito, Y.; Dohda, K. Fabrication of micro-punch array by plasma printing for micro-embossing into copper substrates. Materials 2019, 12, 2640.
- [13] Shiratori, T.; Aizawa, T.; Saito, Y.; Wasa, K. Plasma printing of an AISI316 micro-meshing punch array for micro-embossing onto copper plates. Metals 2019, 9, 396.
- [14] Borgioli, F.; Galvanetto, E.; Bacco, T. Low temperature nitriding of AISI300 and 200 series austenitic stainless steels. Vacu**um *2016*, *12*, 51–60.
- [15] Domain, C.; Becquart, C.S.; Foct, J. Ab initio study of foreign interstitial atom (C, N) interactions with intrinsic point defects in a-Fe. Phys. Rev. B 2004, 69, 144122.
- [16] ECO, Aluminum Die Casting. Available online: https://www.ecodiecasting.com/aluminum-die-casting/ (accessed on 3 June 2022).
- [17] Xie, Z.; Jiao, J.; Yang, K. Theoretical and experimental study on the fluid-structure—Acoustic coupling dynamics of a new water lubricated bearing. Tribol. Int. 2023, 177, 107982.
- [18] Cleary, P.W.; Ha, J.; Prkash, M.; Nguyen, T. Short shots and industrial case studies: Understanding fluid flow and solidification in high pressure die casting. Appl. Math. Model. 2010, 34, 2018–2033.
- [19] Seow, L.W.; Lm, Y.C. Optimizing flow in plastic injection molding. J. Mater. Process. Technol. 1997, 72, 333–341.
- [20] JST, Aluminum Alloy Gear. Available online: http://www.precise-gear.com/aluminum-alloy-gear.html (accessed on 3 June 2022).
- [21] Gangopadhyay, S.; Acharya, R.; Chattopadhyay, A.K.; Sargade, V.G. Effect of cutting speed and surface chemistry of cutting tools on the formation of bul or bue and surface quality of the generated surface in dry turning of AA6005 aluminum alloy. Mach. Sci. Technol. 2010, 14, 208–223.
- [22] Maeno, T.; Mori, K.-I.; Yachi, R. Hot stamping of high-strength aluminum alloy aircraft parts using quick heating. CIRP Ann. 2017, 66, 269–272.
- [23] Kumaraguruparan, G.; Sornakumar, T. Development of testing of aluminum micro channel heat sink. J. Therm. Sci. 2010, 19, 245–252.
- [24] Gong, M.F.; Li, Z.; Dong, J. Mechanics analysis of reinforcing rib structure in aluminum heating-plate automatic casting system. Adv. Mater. Res. 2012, 538-541, 1755–1761.
- [25] Ohashi, T.; Tabetabei, H.M.; Nishimura, T. Rib-structure on A5083 aluminum alloy sheet generated friction stir forming. Preced. Eng. 2017, 207, 1153–1158.
- [26] Ma, Z.; Ji, H.; Huang, X.; Xiao, W.; Tang, X. Research on high temperature stamping forming performance and process parameters optimization of 7075 aluminum alloy. Materials 2021, 14, 5435.
- [27] Chemical Resistance Reference Chart. Available online: https://www.calpaclab.com/content/chemical-charts/Aluminum.pdf (accessed on 6 November 2022).
- [28] Kumar, S.; Maity, S.R.; Patnaik, L. Friction and tribological behavior of bare nitrided, TiAlN and AlCrN coated MDC-K hot work tool steel. Ceram. Int. 2020, 46, 17280–17294.
- [29] Tollmann, W.; Grisales, D.; Stangier, D.; Butzke, T. Tribomechanical behavior of TiAlN and CrAlN coatings deposited onto AISI H11 with different pre-treatments. Coatings 2019, 9, 519.
- [30] Dohda, K.; Aizawa, T.; Funazuka, T. Process tribology of PVD nitride coated dies in hot metal forming. Friction 2022; in press.
9. Copyright:
- This material is a paper by "Tatsuhiko Aizawa, Takeshi Kurihara and Hiroki Sakayori": Based on "Manufacturing of Aluminum Alloy Parts from Recycled Feedstock by PIG Die-Casting and Hot Stamping".
- Source of paper: https://doi.org/10.3390/lubricants11010013
This material was created to introduce the above paper, and unauthorized use for commercial purposes is prohibited. Copyright © 2025 CASTMAN. All rights reserved.