This article introduces the paper ['Magnesium and its alloys applications in automotive industry'] published by ['Springer-Verlag London Limited'].
1. Overview:
- Title: Magnesium and its alloys applications in automotive industry
- Author: Mustafa Kemal Kulekci
- Publication Year: 2008
- Publishing Journal/Academic Society: International Journal of Advanced Manufacturing Technology
- Keywords: Magnesium, Mg components, Mg applications, Automotive industry, Transportation, Fuel economy
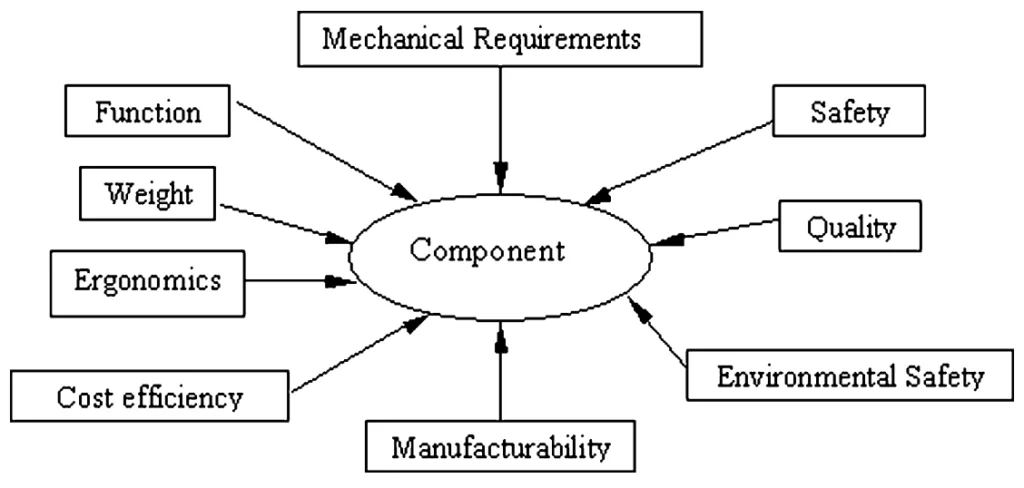
2. Abstracts or Introduction
The objective of this study is to review and evaluate the applications of magnesium in the automotive industry, highlighting its potential to significantly contribute to enhanced fuel economy and environmental conservation. The paper addresses current advantages, limitations, technological barriers, and future prospects of Magnesium (Mg) alloys within the automotive sector. It assesses the impact of magnesium usage in automotive applications on environmental conservation. Recent advancements in coating and alloying of Mg are discussed, focusing on improvements in creep and corrosion resistance properties of magnesium alloys for high-temperature and corrosive environments. The study concludes that reasonable pricing and enhanced properties of Mg and its alloys will drive substantial magnesium adoption. Compared to alternative materials, Mg alloys offer a weight reduction ranging from 22% to 70%. The increasing utilization of magnesium in automotive components is attributed to the growing understanding of Mg alloy forming processes.
3. Research Background:
Background of the Research Topic:
The automotive industry is driven by global trends towards manufacturing lighter, more environmentally friendly, safer, and cheaper vehicles [4]. Automakers are focused on reducing vehicle weight and limiting exhaust emissions due to legislative and consumer demands for safer, cleaner vehicles [7]. Carbon dioxide (CO2) emission is directly proportional to fuel consumption, making vehicle weight a critical design efficiency parameter [11]. Weight reduction is crucial not only for energy saving but also for reducing greenhouse gas emissions.
Status of Existing Research:
Auto manufacturing companies have invested significantly in research and development concerning Mg and its alloys. Volkswagen was the pioneer in applying magnesium in the automotive industry with its Beetle model [7]. Porsche's early work with magnesium engines dates back to 1928 [8]. Past material choices for certain auto parts included aluminium and some plastics. However, recent years have witnessed an increase in magnesium applications within the automotive sector [9]. Current research and development efforts are directed towards weight reduction, energy conservation, and minimizing environmental impact [10].
Necessity of the Research:
Environmental conservation is a primary driver for the focus on Mg and its alloys. The transportation industry's contribution to CO2 emissions necessitates weight reduction as a cost-effective strategy for decreasing fuel consumption and emissions [9, 16]. European and North American car producers aim for substantial fuel consumption and CO2 emission reductions [9, 16, 17]. Despite the increasing consumption of magnesium in recent decades, a significant portion is still used for alloying aluminium, with only about 34% directly utilized for magnesium parts [4, 19]. High cost remains a major barrier to wider magnesium adoption in the automotive industry, requiring competitive pricing for finished products.
4. Research Purpose and Research Questions:
Research Purpose:
The research aims to review the science, technology, and applications of magnesium and its alloys in the automotive industry, emphasizing their contribution to fuel economy and environmental conservation in light of recent advancements. It also intends to examine the current advantages, limitations, technological barriers, and future projections for the utilization of Mg alloys in this sector.
Key Research:
The key research areas explored in this study include:
- Evaluation of magnesium applications in the automotive industry.
- Analysis of advantages, limitations, and technological barriers to magnesium use.
- Assessment of future prospects for magnesium alloys in automotive applications.
- Investigation of the impact of magnesium usage on environmental conservation.
- Review of recent developments in coating and alloying of magnesium to improve material properties.
Research Hypotheses:
The paper does not explicitly state research hypotheses. However, implicitly, the study operates under the premise that:
- Increased use of magnesium alloys in automotive components leads to significant weight reduction and improved fuel economy.
- Overcoming limitations related to cost and material properties will enable massive adoption of magnesium in the automotive industry.
- Advancements in magnesium alloy processing and coating technologies are crucial for expanding magnesium applications.
5. Research Methodology
Research Design:
This study employs a review-based research design. It synthesizes existing literature and research findings to provide a comprehensive overview of magnesium applications in the automotive industry.
Data Collection Method:
The data collection method is based on a literature review of published articles, reports, and industry data related to magnesium alloys and their applications in automotive engineering.
Analysis Method:
The analysis method is qualitative, involving a descriptive synthesis and evaluation of the collected literature. The paper analyzes trends, challenges, and opportunities related to magnesium use in vehicles based on the reviewed sources.
Research Subjects and Scope:
The research focuses on magnesium and its alloys within the context of the automotive industry. The scope encompasses:
- Material properties of magnesium alloys relevant to automotive applications.
- Processing technologies for magnesium components.
- Applications of magnesium in various automotive parts.
- Factors influencing the adoption of magnesium, such as cost, performance, and environmental considerations.
6. Main Research Results:
Key Research Results:
- Magnesium alloys offer a 22% to 70% weight reduction compared to alternative materials in automotive components.
- Specific strength of magnesium is considerably higher than aluminium and iron, while specific stiffness is comparable (Figure 4).
- Cost of magnesium alloys has decreased relative to aluminium since 2004 (Figure 3).
- New magnesium alloys like AE42 and Mg-Al-Sr systems exhibit improved creep resistance (Figure 5, Figure 6).
- Teflon resin coating, obtained with aluminium vapour deposition, provides a low-cost, chromium-free corrosion-resistant coating for magnesium alloys (Figure 7).
- Die-casting is a primary fabrication method for magnesium automotive components.
- Automotive components made of Mg alloy and obtained weight reduction are shown in Figure 8.
- Examples of automotive components made of Mg alloys are shown in Figure 9.
- VW strategy of magnesium technology development is illustrated in Figure 11.
Analysis of presented data:
- Figure 1: Illustrates basic requirements for vehicle components, including Function, Weight, Ergonomics, Cost efficiency, Manufacturability, Safety, Quality, and Environmental Safety [1].
- Figure 2: Shows the relationship between vehicle mass and fuel consumption, demonstrating that reduced vehicle weight leads to improved fuel economy [5].
- Figure 3: Depicts changes in the prices of magnesium and aluminium, indicating a decrease in magnesium price relative to aluminium since 2004 [20].
- Figure 4: Compares basic structural properties of magnesium, aluminium, and iron, highlighting magnesium's superior specific strength [1].
- Figure 5: Compares creep deformation of die-cast Mg-alloys, showing improved creep resistance in AE42 and Mg-Al-Sr alloys compared to AZ91D [31].
- Figure 6: Shows creep resistance of new alloys in comparison to AZ91 and AE42 alloy at 135°C under stress of 85 MPa [17].
- Figure 7: Presents a schematic view of the cross-section for Teflon resin coating [34].
- Figure 8: Illustrates some automotive components made of Mg alloy and the obtained weight reduction.
- Figure 9: Provides examples of automotive components made of Mg alloys.
- Figure 10: Shows North American automotive magnesium usage [15].
- Figure 11: Illustrates VW strategy of magnesium technology development [7].
Figure Name List:
![Fig. 2 The relation between vehicle mass and fuel consumption [5]](https://castman.co.kr/wp-content/uploads/image-775-png.webp)
![Fig. 3 Changes in the prices of magnesium and aluminium [20]](https://castman.co.kr/wp-content/uploads/image-776-1024x384.webp)
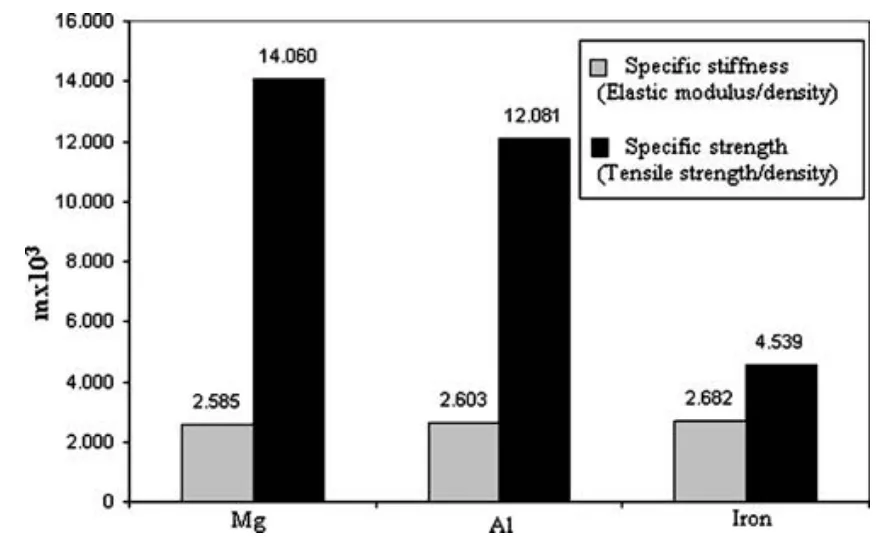
![Fig. 5 Comparison at creep deformation of die-cast Mg-alloys
(35 MPa, 150°C, 200 h) [31]](https://castman.co.kr/wp-content/uploads/image-778-png.webp)
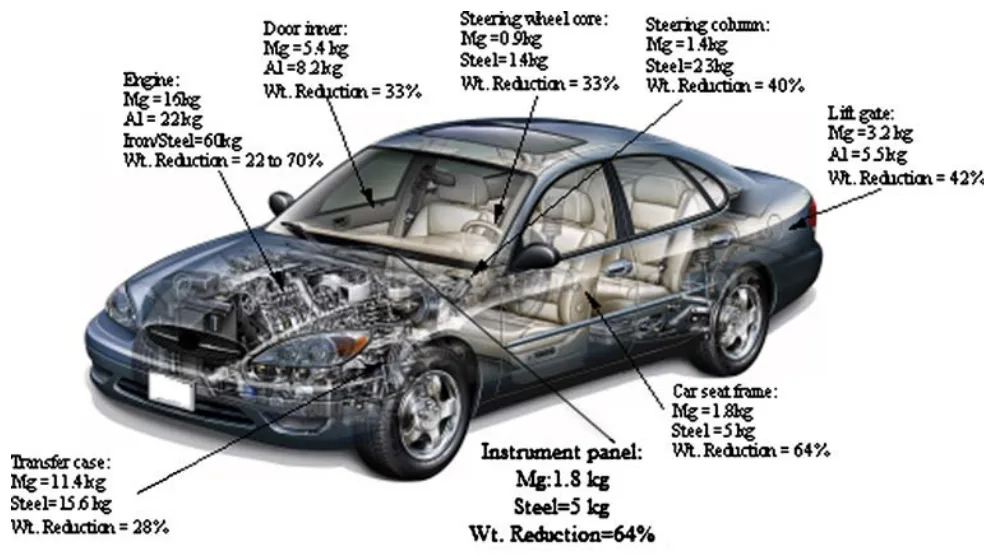
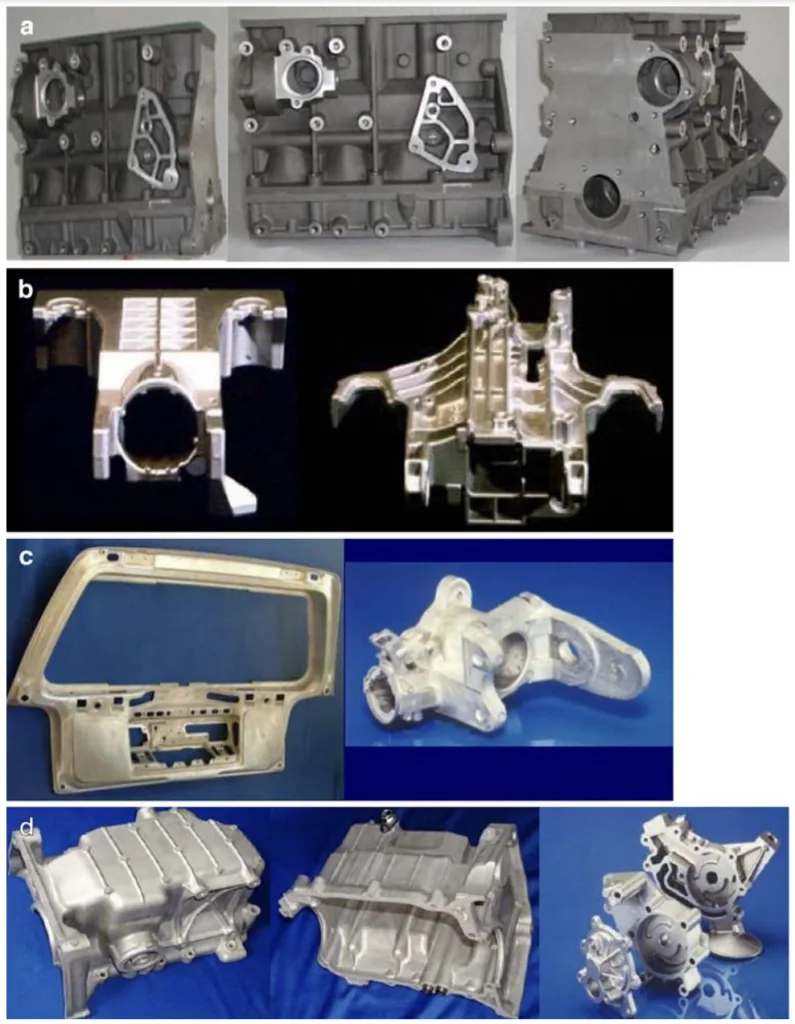
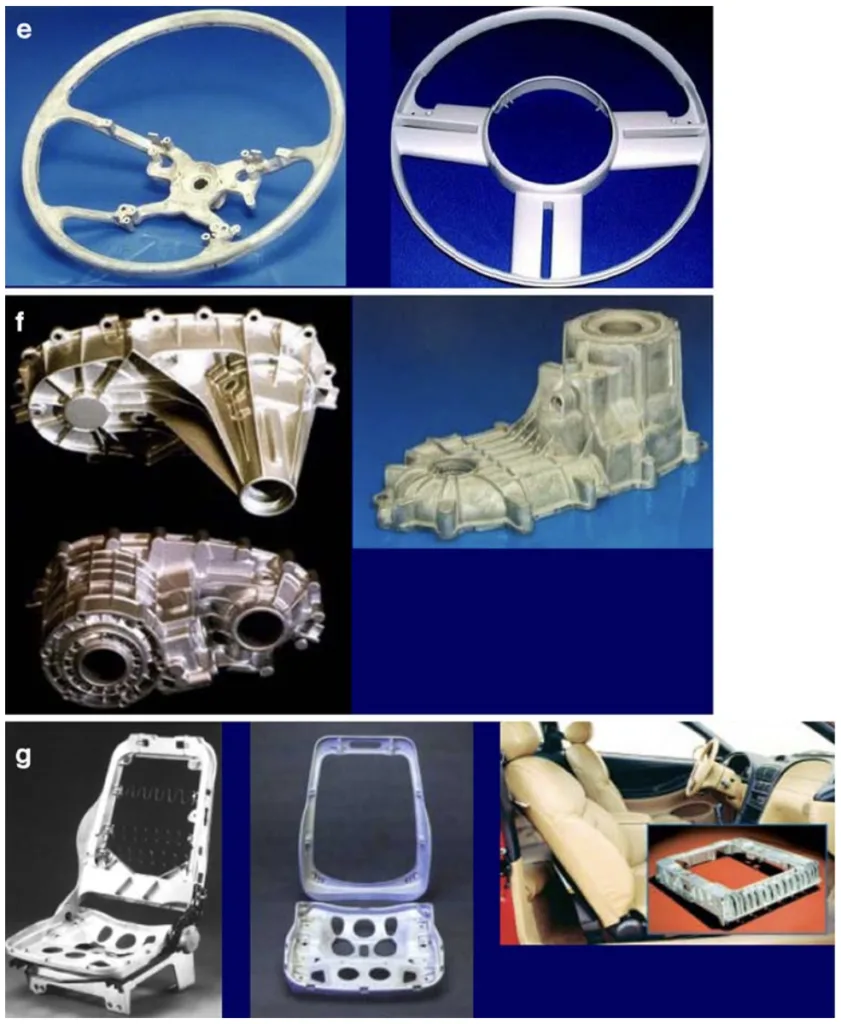
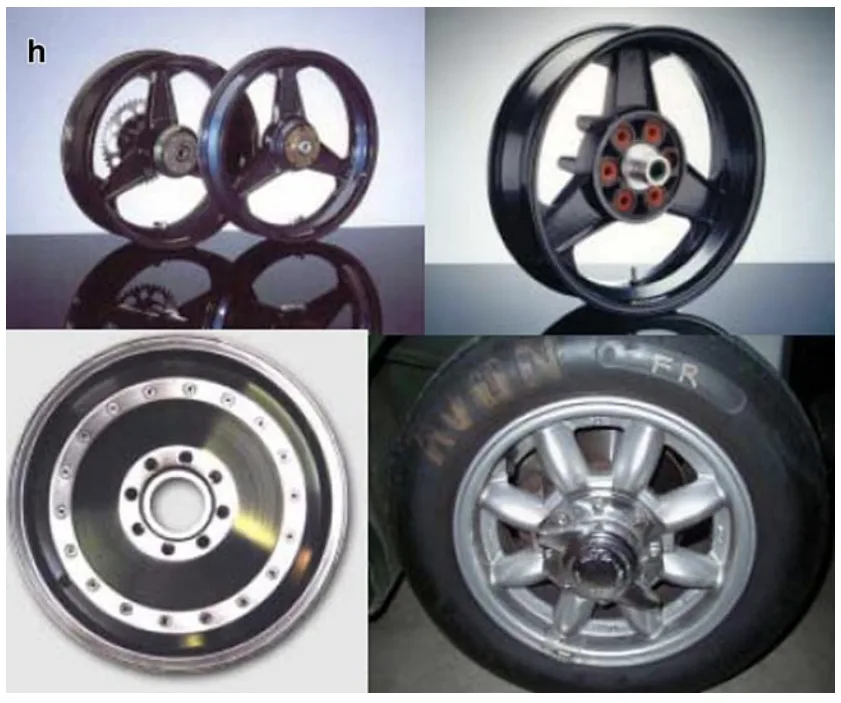
![Fig. 10 North American automotive magnesium usage [15]](https://castman.co.kr/wp-content/uploads/image-783-png.webp)
![Fig. 11 VW strategy of magnesium technology development [7]](https://castman.co.kr/wp-content/uploads/image-784-png.webp)
- Fig. 1 Basic requirements for vehicle components [1]
- Fig. 2 The relation between vehicle mass and fuel consumption [5]
- Fig. 3 Changes in the prices of magnesium and aluminium [20]
- Fig. 4 Comparison of basic structural properties of magnesium with Al and iron
- Fig. 5 Comparison at creep deformation of die-cast Mg-alloys (35 MPa, 150°C, 200 h) [31]
- Fig. 6 Creep resistance of new alloys in comparison to AZ91 and AE42 alloy at 135°C under stress of 85 MPa: (1) AZ91; (2) AE42; (3) MRI 155; (4) MRI 153; (5) MRI 154; (6) MRI 151; (7) MRI 152 [17]
- Fig. 7 Schematic view of the cross-section for Teflon resin coating [34]
- Fig. 8 Some automotive components made of Mg alloy and obtained weight reduction
- Fig. 9 Examples of automotive components made of Mg alloys (a: Engine block, b: Steering column module, c: Door frame / Key lock housing, d: Oil pan, e: Steering wheel, f: Transfer case/Transmission housing, g: Seat frame, h: Wheel)
- Fig. 10 North American automotive magnesium usage [15]
- Fig. 11 VW strategy of magnesium technology development [7]
7. Conclusion:
Summary of Key Findings:
The study concludes that magnesium alloys offer significant potential for weight reduction in automotive applications, contributing to improved fuel economy and reduced CO2 emissions. Key findings include the superior specific strength of magnesium, decreasing cost trends, and advancements in alloy development and coating technologies that address limitations such as creep and corrosion resistance. Die-casting remains the dominant manufacturing process, but further research into forming processes is needed to expand magnesium usage. While magnesium faces challenges like reactivity and galvanic corrosion, these can be mitigated through design and protective measures.
Academic Significance of the Study:
This review paper provides a comprehensive overview of the state-of-the-art in magnesium alloy applications within the automotive industry. It consolidates findings from various studies, offering valuable insights into the material's potential, limitations, and future directions. The paper serves as a handbook-level resource for experts and researchers in materials science, automotive engineering, and manufacturing technology.
Practical Implications:
The practical implications of this study are significant for the automotive industry. The findings support the increased adoption of magnesium alloys to meet growing demands for fuel efficiency and environmental regulations. The paper highlights specific areas for technological development, such as cost-effective alloying, improved corrosion protection coatings (like Teflon resin coating), and advanced forming techniques, which can enable wider and more effective use of magnesium in vehicle manufacturing.
Limitations of the Study and Areas for Future Research:
This study is limited to a review of existing literature and does not include original experimental research. Areas for future research include:
- Further development of magnesium alloys with enhanced creep resistance, particularly for high-temperature powertrain applications.
- Optimization of magnesium alloy forming processes, especially for sheet and extrusion applications, to overcome limitations imposed by the hexagonal crystal structure.
- Research into cost-effective and environmentally friendly surface treatments and coatings to improve corrosion resistance and address galvanic corrosion concerns.
- Life cycle assessments to fully quantify the environmental benefits of magnesium alloy substitution in vehicles, considering production, usage, and recycling phases.
8. References:
- [1] Davies G (2003) Magnesium. Materials for automotive bodies, Elsevier, G. London, pp 91, 158, 159
- [2] Kuo JL, Sugiyama S, Hsiang SH, Yanagimoto J (2006) Investigating the characteristics of AZ61 Magnesium alloy on the hot and semi-solid compression test. Int J Adv Manuf Technol 29(7-8):670-677
- [3] Jain CC, Koo CH (2007) Creep and corrosion properties of the extruded magnesium alloy containing rare earth. Mater Trans 2:265-272
- [4] Blawert C, Hort N, Kainer KV (2004) Automotive applications of magnesium and its alloys. Trans Indian Inst Met 57(4):397-408
- [5] Eliezer D, Aghion E, Froes FH (1998) Magnesium science and technology. Adv Mat Performance 5:201-212
- [6] Aghion E, Bronfin B (2000) Magnesium alloys development towards the 21(st) century. Magnesium alloys 2000 Mat Sci Forum 350(3):19-28
- [7] Friedrich H, Schumann S (2001) Research for a "new age of magnesium" in the automotive industry. J Mater Process Technol 117:276-281
- [8] Schuman S (2005) The paths and strategies for increased magnesium application in vehicles. Mat Sci Forum 488-489:1-8
- [9] Dieringa H, Kainer KU (2007) Magnesium-der zukunftswerkstoff für die automobilindustrie. Mat-wiss U Werkstofftech 38(2):91-95
- [10] Tang B, Wang Xs, Li SS, Zeng DB, Wu R (2005) Effects of Ca combined with Sr additions on microstructure and mechanical properties of AZ91D. Mater Sci Technol 21(29):574-578
- [11] Michalek JJ, Papalambros PY, Skerlos SJ (2004) A study of fuel efficiency and emission policy impact on optimal vehicle design decisions. J Mech Des 126(6):1062-1070
- [12] Medraj M, Parvez A (2007) Analyse the importance of Magnesium-aluminium-strontium alloys for more fuel-efficient automobiles. Automotive 45-47
- [13] Aichinger HM (1996) Reduced fuel consumption through weight-saving in passenger vehicles-importance of steel as a lightweight material. Stahl Und Eisen 116(6):71
- [14] Kurihara Y (1994) The role of aluminum in automotive weight-reduction. 2. JOM J Miner Metals Mater Society 46(2):33-35
- [15] Das S (2003) Magnesium for automotive applications: primary production cost assessment. JOM J Miner Metals Mater Society 55(11):22-26
- 16 Emission control, Automotive World 4:10-15
- [17] Aghion E, Bronfin B, Eliezer D (2001) The role of the magnesium industry in protecting the environment. J Mater Process Technol 117(3):381-385
- 18 Annual Report. Int. Magnesium Association
- [19] Kammer C (2001) Magnesium Taschenbuch. Aluminium, Verlag, Germany p 1
- [20] Brown B (2007) Magnesium application in the short term. http://www.magnesium.com/W3/data-bank/article.php?mgw=199&magnesium-286
- [21] Commission of the European Communities (2007), Results of the review of the Community Strategy to reduce CO2 emissions from passenger cars and light-commercial vehicles, {SEC(2007) 60} {SEC(2007) 61}, COM(2007) 19 final
- [22] United Nations (February 2007), Kyoto protocol reference manual on accounting of emissions and assigned amounts
- [23] Price on Magnesium and Aluminium (2007) http://www.lightmetals.org/e/documents/LMTinretospect.pdf
- [24] Hakamada M, Furuta T, Chino Y, Chen Y, Kusuda H, Mabuchi M (2007) Life cycle inventory study on magnesium alloy substitution in vehicles. Energy 32(8):1352-1360
- [25] Fitch P, Cooper JS (2005) Life-cycle modeling for adaptive and variant design. Res Eng Design 15(4):216-228
- [26] Das S (2000) The life-cycle impacts of aluminum body-in-white automotive. JOM J Miner Metals Mater Society 50(8):41-44
- [27] Tkachenko VG, Maksimchuk IN, Volosevich PY, Lashuk NK, Malka AN, Friezel VV (2006) Creep resistance and long-term strength of structural magnesium alloys. High Temp Mater Proc 25(1-2):97-107
- [28] Pekguleryuz MO, Kaya AA (2003) Creep resistant magnesium alloys for powertrain applications. Adv Eng Mater 5(12):866-878
- [29] Baril E, Labelle P, Pekguleryuz MO (2003) Elevated temperature Mg-Al-Sr: Creep resistance, mechanical properties, and microstructure. Jom-Journal of the Minerals Metals & Materials Society 55(11):A34-A39
- [30] Aghion E, Bronfin B, Von Buch F, Schumann S, Friedrich H (2003) Newly developed magnesium alloys for powertrain applications. Jom-J Miner Metals Mater Society 55(11):A30-A33
- [31] Pekguleryuz MO, Baril E, Labelle P, Argo D (2003) Creep resistant Mg-Al-Sr alloys. J Adv Mater 35(3):32-38
- [32] Grieve DJ (2001) Magnesium Die Castings. http://www.tech.plym.ac.uk/sme/mech330/magcast.htm
- [33] Bavarian Motor Works (2007) Magnesium fosters rebirth of an automotive engine. International magnesium association: The global voice for magnesium (May):1-3
- [34] AIST (2007) New technology for increasing the application for magnesium alloys. http://www.aist.go.jp/aist_e/latest_research/2001/20011203/20011203.html
- [35] Robots 4 welding (2007) Welding magnesium. http://www.robots4welding.com/magnesium-welding-automation.htm
- [36] Kulekci MK, Şik A, Kaluç E (2007) Effects of tool rotation and pin diameter on fatigue properties of friction stir welded lap joints. Int J Adv Manuf Technol DOI 10.1007/s00170-006-0901-z
- [37] Chi CT, Chao CG (2007) Characterization on electron beam welds and parameters for AZ31B-F extrusive plates. J Mater Process Technol 182(1-3):369-373
- [38] Liu LM, Wang SX, Zhu ML (2006) Study on TIG welding of dissimilar Mg alloy and Cu with Fe as interlayer. Sci Technol Weld Join 11(5):523-525
- [39] Chang WS, Kim HJ, Noh JS, Bang HS (2006) The evaluation of weldability for AZ31B-H24 and AZ91C-F Mg alloys in friction stir welding. Key Eng Mater 321-323:1723-1728
- [40] Welding Magnesium (2007) http://www.robots4welding.com/magnesium-welding-automation.htm
- [41] Huang ZH, Guo XF, Zhang ZM (2006) Effects of alloying on microstructure and mechanical property of AZ91D magnesium alloy. Rare Met Mater Eng 35(3):363-366
- [42] Garmo EPD, Black JT, Kohser RA (1997) Magnesium and magnesium alloys. Materials and processes in manufacturing (8th Edition). Wiley, USA, pp 182-184
- [43] Novotny S, Geiger M (2003) Process design for hydroforming of lightweight metal sheets at elevated temperatures. J Mater Process Technol 138:594-599
- [44] Haferkamp H, Boehm R, Holzkamp U, Jaschik C, Kaese V, Niemeyer M (2001) Alloy development, processing and applications in magnesium lithium alloys. Mater Trans 42(7):1160–1166
- [45] Sreejith PS, Ngoi BKA (2000) Dry machining: machining of the future. J Mater Process Technol 101:287-291
- [46] ASM Handbook vol. 2, 1961, p. 1081
- [47] Report (2001) "Magnesium in the aerospace industry", NFPA: National fire protection association. Ref: ANM-112N-04-07, Rev.c.USA
- [48] Shi ZM, Song GL, Atrens A (2006) Influence of anodising current on the corrosion resistance of anodised AZ91D magnesium alloy. Corros Sci 48(8):1939-1959
- [49] Niu LY, Jiang ZH, Li GY, Gu CD, Lian JS (2006) A study and application of zinc phosphate coating on AZ91D magnesium alloy. Surf Coat Technol 200(9):3021-3026
- [50] Polmear IJ (1994) Magnesium alloys and applications. Mater Sci Technol 10(1):1-14
- [51] Magnesium Pure and Alloys, Norsk Hydro Report
- [52] Mg application in automotive industry (2007) http://www.avisma.ru/mg/eng/03-2.htm
9. Copyright:
- This material is Mustafa Kemal Kulekci's paper: Based on "Magnesium and its alloys applications in automotive industry".
- Paper Source: DOI 10.1007/s00170-007-1279-2
This material was summarized based on the above paper, and unauthorized use for commercial purposes is prohibited.
Copyright © 2025 CASTMAN. All rights reserved.