This article introduces the paper 'Low Solution Temperature Heat Treatment of AlSi9Cu3(Fe) High-Pressure Die-Casting Actual Automotive Components' published by 'Journal of Materials Engineering and Performance'.
1. Overview:
- Title: Low Solution Temperature Heat Treatment of AlSi9Cu3(Fe) High-Pressure Die-Casting Actual Automotive Components
- Author: Silvia Cecchel, Andrea Panvini, and Giovanna Cornacchia
- Publication Year: 2018
- Publishing Journal/Academic Society: Journal of Materials Engineering and Performance, ASM International
- Keywords: blisters, heat treatment, high-pressure die-casting, non-ferrous alloys, porosity, secondary aluminum alloys


2. Abstracts or Introduction
In the realm of high-pressure die-casting (HPDC), a significant limitation arises from the inability to apply high-temperature heat treatments to components due to the formation of surface blisters. This phenomenon not only compromises surface quality but also detrimentally affects mechanical properties. This paper addresses this challenge by investigating the efficacy of a low solution temperature T6 heat treatment specifically tailored for HPDC AlSi9Cu3 alloy.
The research explores the use of very low solution temperatures, specifically below 450 °C, in conjunction with a subsequent aging process at 165 °C, to mitigate blister formation. These low solution temperatures were combined with industrially relevant treatment times, ranging from 1 to 16 hours, to ensure practical applicability.
The study was conducted on samples extracted from actual automotive castings, allowing for the evaluation of typical production-related defects. Comprehensive property analysis was performed using visual inspection, microstructural observations, image analysis, hardness measurements, tensile testing, and fractography to ascertain the treatment's effectiveness.
3. Research Background:
Background of the Research Topic:
The imperative to reduce automotive emissions has driven the adoption of lightweight materials, particularly aluminum alloys, in vehicle manufacturing, as documented in (Ref 1, 2). High-pressure die casting (HPDC) stands out as the predominant manufacturing method for high-volume production of light alloy components (Ref 8, 9).
However, a critical drawback of HPDC is the inherent porosity resulting from rapid metal die filling and solidification, trapping air within the casting (Ref 10). This porosity precludes the use of conventional high-temperature heat treatments due to surface blistering (Ref 11), limiting the achievable mechanical properties of HPDC components.
Status of Existing Research:
To circumvent the limitations of HPDC, alternative technologies like semisolid metal and rheocasting processes have been explored to enhance component integrity (Ref 12, 13). While gravity casting offers superior mechanical performance, its slow production cycle and weight limitations render it unsuitable for high-volume automotive applications (Ref 14-19). Vacuum-assisted HPDC represents an advancement, minimizing gas porosity and enabling heat treatment (Ref 21).
Prior research by Lumley et al. (Ref 10, 44-46) demonstrated the feasibility of heat-treating HPDC Al-Si-X alloys at lower solution temperatures (< 500 °C) and shorter times (~ 15 min) in laboratory settings to avoid blistering. Pabel et al. (Ref 47) investigated various heat treatment conditions for Al Si9Cu3(Fe)(Zn) alloy, including natural and artificial aging combinations, to optimize mechanical properties.
Necessity of the Research:
Despite advancements in vacuum HPDC, a cost-effective solution for enhancing the mechanical properties of secondary aluminum alloys produced via conventional HPDC remains crucial. Secondary AlSi9CuX alloys are extensively used in automotive applications due to their favorable mechanical properties and high-temperature performance, despite their recycled content (Ref 22, 23). This study addresses the industrial constraints of batch uniformity and longer treatment times prevalent in foundry furnaces, investigating the feasibility of low solution temperature T6 heat treatments for conventional HPDC AlSi9Cu3 alloys in a practical industrial context.
4. Research Purpose and Research Questions:
Research Purpose:
The primary objective of this research is to evaluate the effectiveness of a low solution temperature T6 heat treatment in enhancing the mechanical properties of conventional HPDC AlSi9Cu3 alloy components, specifically focusing on mitigating surface blistering.
Key Research:
This study centers on determining if very low solution temperatures (< 450 °C), combined with industrially applicable treatment times (1 to 16 hours) and a subsequent aging step at 165 °C, can achieve significant strengthening in AlSi9Cu3 alloy without inducing relevant blistering. The research explores the optimal combination of solution temperature and time within these constraints to maximize mechanical properties.
Research Hypotheses:
The central hypothesis is that it is possible to employ solubilization temperatures below 450 °C for extended durations within a T6 treatment to achieve strengthening in AlSi9Cu3 alloy without causing detrimental blistering. It is further hypothesized that extending the solution treatment time at these lower temperatures will promote homogenization and improve the aging response, leading to enhanced mechanical properties.
5. Research Methodology
Research Design:
The research employed an experimental design involving systematic variation of solution treatment parameters within a T6 heat treatment cycle. Preliminary low-temperature solution treatments (< 450 °C) with varying times (1, 2, 4, 8, 16 h) were conducted to assess hardness response and microstructural changes. Based on these preliminary findings, a set of T6 heat treatments were designed, combining selected solution temperatures (430, 450, and 490 °C) and times (4, 8, and 0.25 h for 490°C) with a constant artificial aging treatment at 165 °C for varying durations (1, 2, 4, 8, 16 h).
Data Collection Method:
Samples for analysis were extracted from actual HPDC automotive components made of secondary AlSi9Cu3 alloy (EN AC 46000). The following methods were used for data collection:
- Visual Inspection: Surface quality was assessed through visual checks to detect blistering after solution treatments.
- Microstructural Observations: Optical microscopy was used to examine microstructural changes before and after solution treatments, focusing on silicon fragmentation and spheroidization.
- Hardness Tests: Vickers hardness HV60 tests were performed to quantify the effect of heat treatments on alloy hardness, following ASTM E 18-03 procedures (Ref 48).
- Tensile Tests: Cylindrical die-cast tensile specimens were tested according to UNI EN ISO 6892-1:2009 standards to evaluate yield strength (σy), ultimate tensile strength (σm), and elongation (A%).
- Fractography: Scanning electron microscopy (SEM) was used to examine fracture surfaces of tensile samples and orthogonal cross-sections to analyze fracture mechanisms and microstructural features.
- Energy Dispersive Spectroscopy (EDS): Semiquantitative chemical analysis using EDS was performed to characterize intermetallic phases.
- Image Analysis: LAS 4.0 software was used for intermetallic image analysis on orthogonal cross-sections to quantify intermetallic volume, size, roundness, and porosity.
Analysis Method:
Collected data were analyzed to determine the influence of different solution treatment parameters on the mechanical properties and microstructure of the AlSi9Cu3 alloy. Hardness-time curves were plotted to assess the kinetics of solution treatment. Tensile test results were compared to evaluate the improvement in mechanical properties, and the Quality Index (QI) (Ref 52) was calculated to compare overall metallurgical quality. Microstructural images and fractography were analyzed to correlate property changes with microstructural evolution, including silicon spheroidization, intermetallic phase morphology, and porosity characteristics. Image analysis provided quantitative data on intermetallic and porosity features to support qualitative observations.
Research Subjects and Scope:
The research focused on secondary AlSi9Cu3 alloy (EN AC 46000) commonly used in automotive components. Samples were extracted from industrially produced HPDC automotive castings to ensure relevance to real-world production conditions. The scope of the study was limited to investigating low solution temperature T6 heat treatments and their impact on blistering and mechanical properties, specifically yield strength, tensile strength, elongation, and hardness.
6. Main Research Results:
Key Research Results:
The study successfully demonstrated that low solution temperature T6 heat treatments, with solution temperatures below 450 °C, can be effectively applied to HPDC AlSi9Cu3 alloy components without causing significant blistering. The optimum heat treatment condition identified was a solution treatment at 430 °C for 4 hours followed by aging at 165 °C for 8 hours. This treatment resulted in a yield strength increase of approximately 50 MPa, a doubling of ductility, and the highest Quality Index value, representing a 50% improvement over the as-cast condition. Hardness measurements indicated a gradual decrease with increasing solution times at both 430 °C and 450 °C, suggesting progressive intermetallic solubilization and silicon fragmentation. Tensile test results confirmed improved mechanical resistance for all heat-treated samples compared to the as-cast condition, with yield strength and ultimate tensile strength increasing with solution temperature.
Analysis of presented data:
- Hardness-time curves (Fig. 2 & 4): Showed a decrease in hardness with increasing solution time, indicating silicon spheroidization and intermetallic solubilization. Hardness increased after aging, confirming age hardening response.
- Optical Microscopy (Fig. 3): Revealed microstructural changes, including fragmentation and spheroidization of silicon phases after heat treatment, and homogenization of the alloy.
- Tensile Test Curves (Fig. 5): Demonstrated improved tensile properties after T6 treatments, with variations depending on solution temperature.
- SEM Analysis (Fig. 6 & 7): Showed fracture surfaces and orthogonal cross-sections, revealing intermetallic phases and porosity. Rosette-shaped Fe-Mn particles were observed on fracture surfaces (Table 4).
- EDS Analysis (Table 3 & 4): Provided compositional data of intermetallic phases.
- Image Analysis (Table 5): Quantified intermetallic features, showing a decrease in intermetallic dimension and roundness with increasing solution temperature, and an increase in porosity dimension after heat treatment.
Figure Name List:
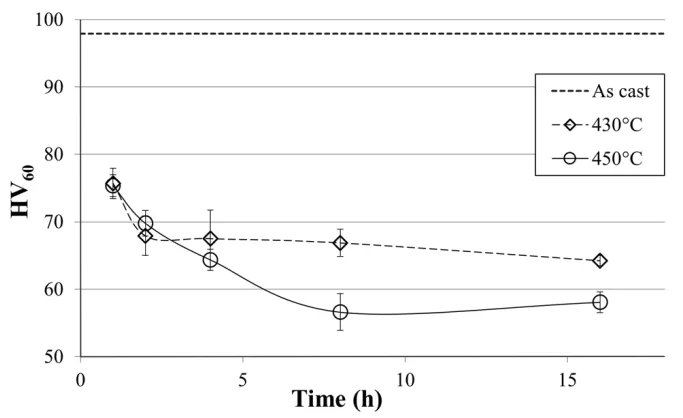
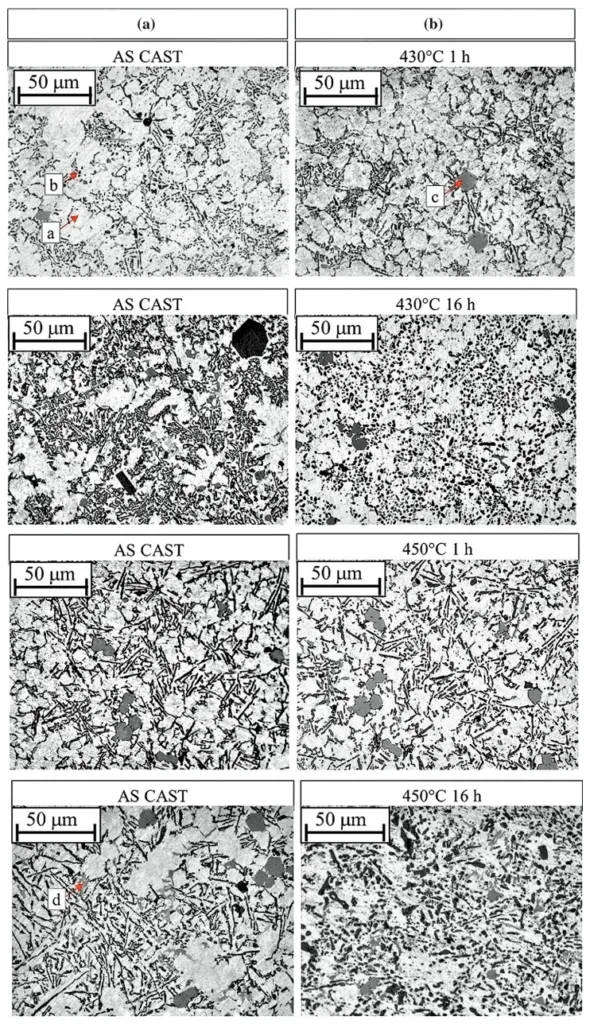
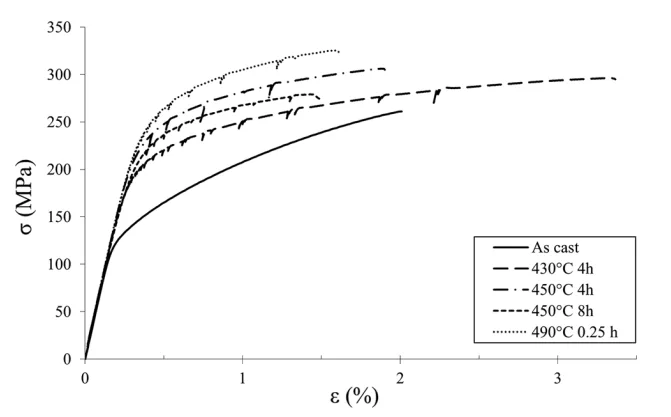
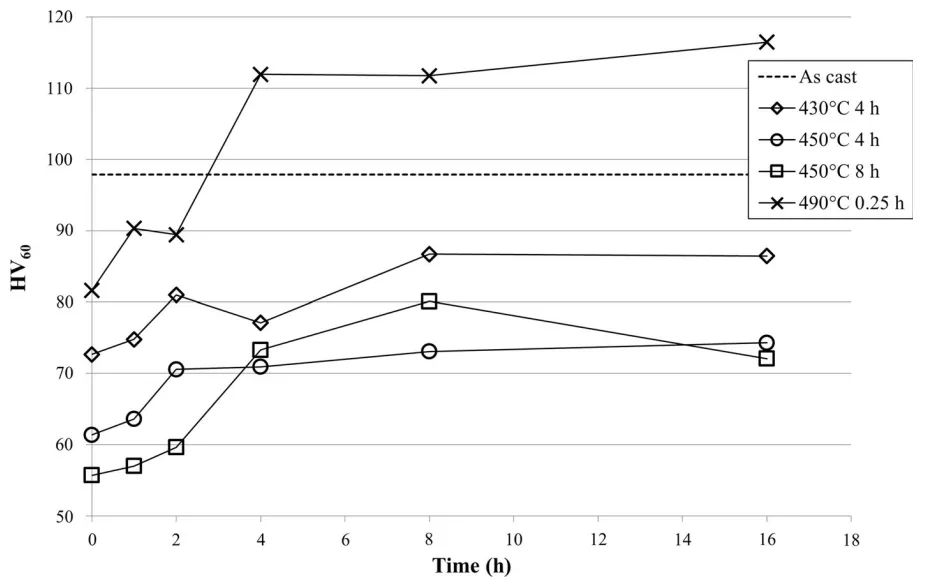
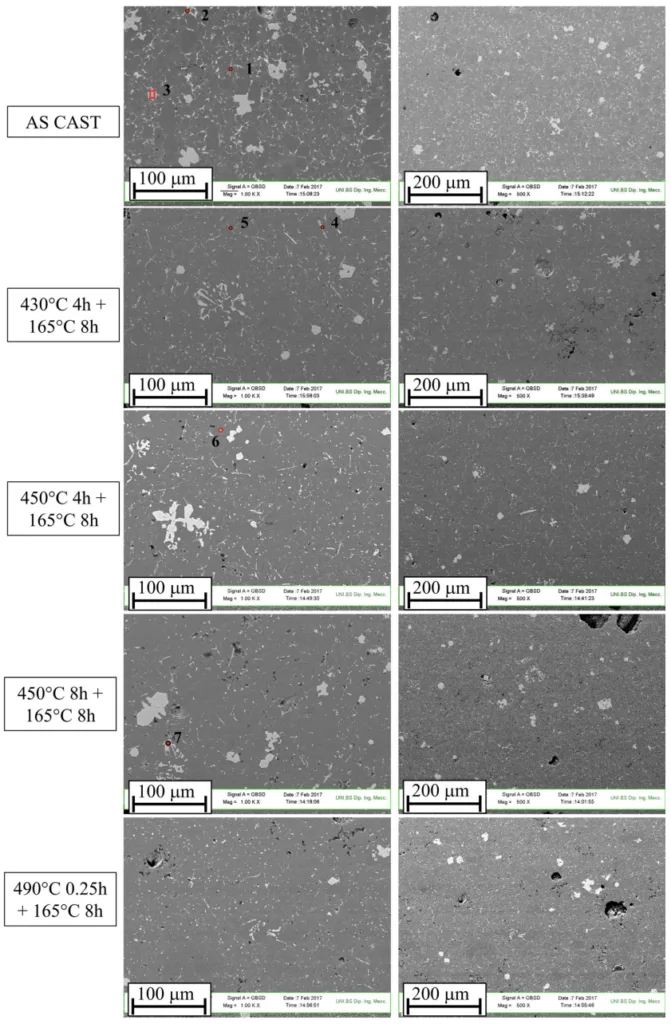
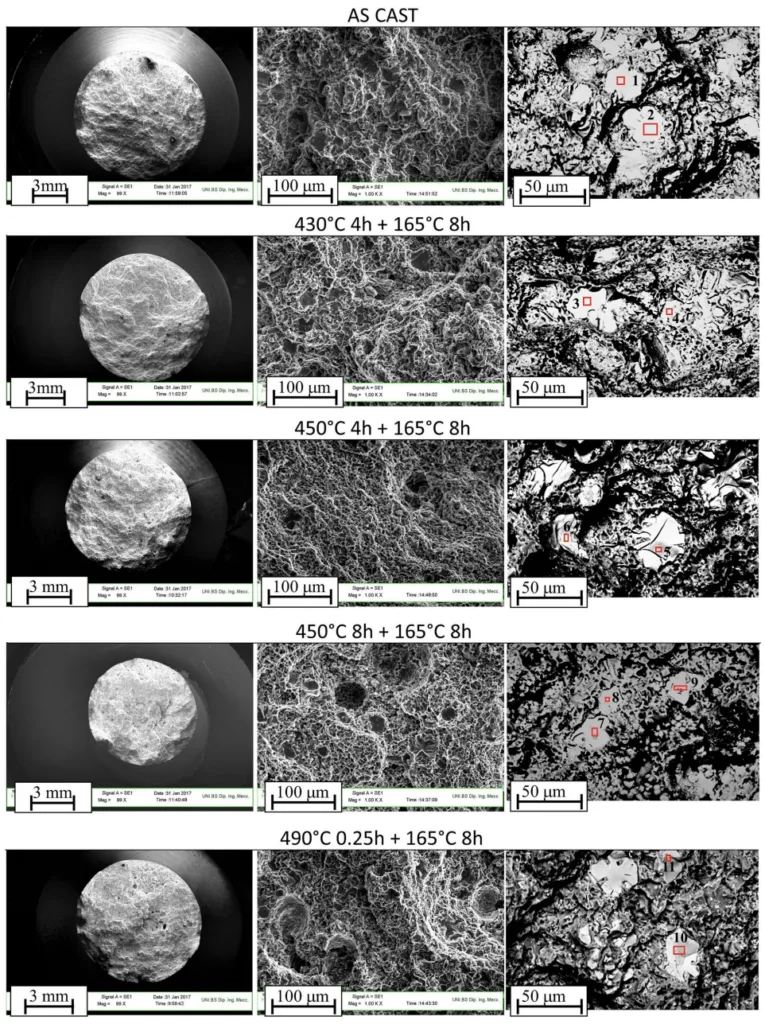
- Fig. 1 Experimental solution treatment parameters (left) and experimental T6 heat treatment conditions selected (right)
- Fig. 2 Hardness-time curves for alloy EN AC 46000 solutionized at different time-temperature conditions
- Fig. 3 Optical micrograph 500x magnification on the same section of an EN AC 46000 sample as-cast (A) and solution-treated at 430 and 450 °C (B). In detail, a-Al-dendrites (a), Al-Si-Al2Cu-eutectic (b), primary Al15 (Mn, Fe,Cr)3Si2 (c) and Al₂Cu (d)
- Fig. 4 Hardness-time curves for alloy EN AC 46000 aged at 165 °C following different solution treatment procedures
- Fig. 5 Comparison of tensile test curves for alloy EN 46000 aged at 165 °C for 8 h following different solution treatment procedures
- Fig. 6 SEM on the orthogonal cross section of the tensile samples
- Fig. 7 SEM on the fracture surfaces of the tensile samples
- Fig. 8 Results of intermetallics mapping on SEM investigation on the section orthogonal to the axis of the tensile samples
7. Conclusion:
Summary of Key Findings:
This study conclusively demonstrates the feasibility of employing low solution temperature T6 heat treatments for HPDC secondary AlSi9Cu3 alloy. Solubilization temperatures below 450 °C, combined with industrially relevant times, effectively strengthened the alloy without inducing significant blistering. The optimal T6 treatment identified, involving a 430 °C/4h solution and 165 °C/8h aging, yielded substantial improvements in yield strength (~50 MPa increase), ductility (doubled), and overall Quality Index (~50% increase).
Academic Significance of the Study:
This research contributes to the scientific understanding of heat treatment response in HPDC aluminum alloys, particularly secondary alloys. It demonstrates that effective strengthening can be achieved at lower solution temperatures than conventionally used, expanding the processing window for heat-treatable HPDC components. The study provides valuable insights into the relationship between low-temperature solution treatment parameters, microstructural evolution (silicon spheroidization, intermetallic phase transformation), and resulting mechanical properties.
Practical Implications:
The findings offer a practically viable and more affordable approach to heat treating HPDC secondary AlSi9Cu3 alloy components. By eliminating the need for vacuum-assisted HPDC or high-temperature solution treatments, this low-temperature T6 process can be readily implemented in conventional foundry settings, enhancing the mechanical performance and expanding the application range of HPDC aluminum components, especially in the automotive sector.
Limitations of the Study and Areas for Future Research:
While this study provides significant insights, further research is warranted to optimize the low-temperature T6 treatment for various HPDC component geometries and alloy compositions. Long-term performance evaluation, including fatigue and creep behavior of components treated with the optimized parameters, is recommended. Further investigation into the precise mechanisms of intermetallic phase transformation and porosity evolution during low-temperature solution treatment would also be beneficial.
8. References:
- 1. H. Helms and U. Lambrecht, The Potential Contribution of Light-Weighting to Reduce Transport Energy Consumption, Int. J. Life Cycle Assess., 2007, 12, p 58-64
- 2. J. Hirsch, Automotive Trends in Aluminium-The European Perspec-tive, Mater. Forum, 2004, 28, p 15-23. http://citeseerx.ist.psu.edu/viewdoc/download?doi=10.1.1.606.9561&rep=rep1&type=pdf
- 3. S. Das, The Life-Cycle Impacts of Aluminum Body-in-White Auto-motive Material, JOM, 2000, 52, p 41-44
- 4. J. Kasai, Life Cycle Assessment, Evaluation Method for Sustainable Development, JSAE Rev., 1999, 20, p 387-393. https://doi.org/10.1016/S0389-4304(99)00013-2
- 5. S. Cecchel and D. Ferrario, Numerical and Experimental Analysis of a High Pressure Die Casting Aluminum Suspension Cross Beam for Light Commercial Vehicles, La Metall. Ital., 2016, 108, p 41-44
- 6. L. Wang, D. Apelian, and M.M. Makhlouf, Optimization of Aluminum Die. Casting Alloys for Enhanced Properties, Mater. Sci. Forum, 2009, 618-619, p 601-605
- 7. M.M. Makhlouf, D. Apelian, and L. Wang, Microstructures and Prop-erties of Aluminum Die Casting Alloys, North American Die Casting Association, Rosemont, 1998
- 8. D.R. Gunasegaram and A. Tharumarajah, Impacts of High-Pressure Diecasting Process Parameters on Greenhouse Gas Emissions, Metall. Mater. Trans. B, 2009, 40, p 605-614
- 9. European Aluminium Association (IOP Publishing Physics Web, 2013). http://european-aluminium.eu/media/1329/environmental-profile-re port-for-the-european-aluminium-industry.pdf. Accessed Apr 2013
- R.N. Lumley, R.G. O'Donnell, D.R. Gunasegaram, and M. Givord, Heat Treatment of High-Pressure Die Castings, Metall. Mater. Trans. A, 2007, 38A, p 2564-2574
- E.J. Vinarcik, High Integrity Die Casting Processes, Wiley, New York, 2003
- D.H. Kirkwood, M. Suéry, P. Kapranos, H.V. Atkinson, and K.P. Young, Semi-solid Processing of Alloys, Springer, Berlin, 2010
- S. Capuzzi, G. Timelli, A. Fabrizi, and F. Bonollo, Influence of Ageing Heat Treatment on Microstructure and Mechanical Properties of a Secondary rheOCast. AISi9Cu3(Fe) Alloy, Mater. Sci. Forum, 2015, 828, p 212-218
- T.P. Fisher, Technology of Gravity Die Casting, Newnes, Oxford, 1968
- ASM Metals Handbook, vol. 15, 10th edn., Casting, (ASM, Metals Park, 1990)
- J. Campbell, R. A. Harding, Casting Technology, 2000, in TALAT 2.0 cd-rom, EAA, Bruxelles
- J. Campbell, Castings, Butterworth Heinemann Ltd, Oxford, 1991, p 273-275
- S. Schleg, D. P. Kamicki, Guide to casting and moulding processes, 2000, Engineered casting solutions
- J.R. Brown, Non-ferrous Foundryman's Handbook, Butterworth, Oxford, 1999
- G. Timelli, O. Lohne, L. Arnberg, and H.I. Laukli, Effect of Solution Heat Treatments on the Microstructure and Mechanical Properties of a Die-Cast AlSiMgMn Alloy, Metall. Mater. Trans. A, 2008, 39A, p 1747-1758
- P.S. Cheng, Y. Chu, B. Ueda, Y. Yasuhara, T. Deguchi, X. Yan, Development of Heat Treatment Processes of A Ductile Casting Alloy for High Vacuum Die Cast Automotive Structural Components, NADCA Die Casting congress & exposition 2015, 2015
- G. Vicario, I. Anza, I. Crespo, P. Eguizabal, F. Saenz de Tejada, European Patent No. EP2865773
- G. Vicario, I. Anza, I. Crespo, A. Abuin, F. Saenz de Tejada, European patent No. EP2865774
- S. Cecchel, G. Cornacchia, and A. Panvini, Cradle-to-Gate Impact Assessment of a High-Pressure Die-Casting Safety-Relevant Automo-tive Component, JOM, 2016, 68, p 2443-2448. https://doi.org/10. 1007/s11837-016-2046-3
- S. Cecchel, D. Chindamo, E. Turrini, C. Carnevale, G. Cornacchia, M. Gadola, A. Panvini, M. Volta, D. Ferrario, and R. Golimbioschi, Impact of Reduced Mass of Light Commercial Vehicles on Fuel Consumption, Sci. Total Environ., 2018, 613–14, p 409-417. https://doi.org/10.1016/ j.scitotenv.2017.09.081
- S. Cecchel, D. Chindamo, M. Collotta, G. Cornacchia, A. Panvini, G. Tomasoni, and M. Gadola, Lightweighting in Light Commercial Vehicles: Cradle-to-Grave Life Cycle Assessment of a Safety-Relevant Component, IJLCA, 2018, https://doi.org/10.1007/s11367-017-1433-5
- S. Cecchel, D. Ferrario, A. Panvini, and G. Cornacchia, Lightweight of a Cross Beam for Commercial Vehicles: Development, Testing and Validation, Mater. Des., 2018, 149, p 122-134. https://doi.org/10.1016/ j.matdes.2018.04.021
- S. Cecchel, M. Collotta, G. Cornacchia, A. Panvini, and G. Tomasoni, A Comparative Cradle-to Gate Impact Assessment: Primary and Secondary Aluminum Automotive Components Case, La Metall. Ital., 2018, 2, p 46-55
- J. Gautheir, P.R. Louchez, and F.H. Samuel, Heat treatment of 319.2 Aluminum Automotive: Part 1: Solution Heat Treatment, Cast Met., 1994, 8(2), р 91-106
- M.H. Mulazimoglu, N. Tenekedjiev, B.M. Closset, and J.E. Gruzleski, Studies on the. Minor Reactions and Phases in Strontium-Treated Aluminium-Silicon Casting Alloys, J. Cast Met., 1993, 6(1), p 16-18
- F.H. Samuel, A.M. Samuel, and H.W. Doty, Factors Controlling the Type and Morphology of Cu-Containing Phases in 319 Al Alloy, AFS Trans., 1996, 104, p 893-901
- P.N. Anyalebechi, Analysis of the Effects of Alloying Elements on Hydrogen Solubility in Liquid. Aluminum Alloys, Scr. Metall. Mater., 1995, 33(8), p 1209-1216
- C.H. Cacers, M.B. Djurdjevic, T.J. Stockwell, and J.H. Sokolowski, The Effect of Cu Content on the Level of Microporosity in Al-Si-Cu-Mg Casting Alloys, Scr. Mater., 1999, 40(5), p 631-637
- S.G. Shabestari and H. Moemeni, Effect of Copper and Solidification Conditions on the Microstructure and Mechanical Properties of Al-Si-Mg Alloys, J. Mater. Process. Technol., 2004, 153-154, p 193-198
- J. Czikel, G. Sabath, and G. Schindelbacher, Studien zur Gießtechnik von Prüfstäben im Druckgießverfahren und zu den Eigenschaften der Legierung GD-AlSi9Cu3, Giesserei Rundschau, 1987, 4, p 7-11
- N. Zazi, Effect of Heat Treatments on the Microstructure, Hardness and Corrosion Behavior of Nondendritic AlSi9Cu3 (Fe) Cast Alloy, Mater. Sci., 2013, 19, p 258-263
- B.A. Parker, D.S. Saunders, and J.R. Griffiths, the Quantitative. Evaluation of Microstructure of a Strontium-Modified Al-Si-Mg. Alloy Following Prolonged Solution Treatment, Met. Forum, 1982, 5(1), p 48-53
- P.A. Rometsch, L. Arnberg, and D.L. Zhang, Modelling Dissolution of Mg2Si and Homogenisation in Al-Si-Mg Casting Alloys, Int. J. Cast Met. Res., 1999, 12, p 1-8
- D.J. Bryant, The Effects of Preaging Treatments on Aging Kinetics and Mechanical Properties in AA6111 Aluminum Autobody Sheet, Metall. Mater. Trans. A, 1999, 30A, р 1999-2006
- G.C. Weatherley, A. Perovic, N.K. Mukhopadhyay, D.J. Lloyd, and D.D. Perovic, The Precipitation of the Q Phase in an AA6111 Alloy, Metall. Mater. Trans. A, 2001, 32A, p 213-218
- J.A. Taylor, D.H. St. John, L.H. Zheng, G.A. Edwards, J. Barresi, and M.J. Couper, Solution treatment effects in Al-. Si-Mg casting alloys: part 1-intermetallic phases, Alum. Trans., 2001, 4-5, p 95-110
- J.A. Taylor, D.H. John, and M.J. Couper, Solution Treatment Effects in Al-. Si-Mg Casting Alloys: Part 1-Intermetallic Phases, Alum. Trans., 2001, 4-5, p 111-124
- S.N. Singh, B.P. Bardes, and M.C. Flemings, Solution Treatment of Cast Al-4.5 pct Cu Alloy, Metall. Trans., 1970, 1, p 1383-1388
- R.N. Lumley, R.G. O'Donnell, D.R. Gunasegaram, and M. Givord, Blister Free Heat Treatment of High Pressure Die-Casting Alloys, Mater. Sci. Forum, 2006, 519–521, p 351-358
- R.N. Lumley, R.G. O'Donnell, D.R. Gunasegaram, and M. Givord: Heat Treatment of Aluminium Alloy High Pressure Die Casting, International Patent Application, PCT/AU2005/001909. 2004-12-23
- R.N. Lumley, R.G. O'Donnell, D.R. Gunasegaram, T. Kittel-Sherri, M. Gershenzon, A.C. Yob, and I.J. Polmear, The Role of Alloy
- T. Pabel, G.F. Geier, H. Rockenschaub, and M. Hopfinger, Improved mechanical properties of the high pressure die casting alloy AlSi9Cu3 (Fe)(Zn) as a result of the combination of natural and artificial ageing, Int. J. Mat. Res. (formerly Z. Metallkd.), 2007, 98–6, p 516-520
- AMERICAN SOCIETY FOR TESTING AND MATERIALS. Stan-dard test methods for Rockwell hardness and Rockwell superficial hardness of metallic materials. ASTM Standard E: 18 03 2003
- L. Backerud, G. Chai, and J. Tamminen, Solidification Characteristics of Aluminum Alloys, Vol 2, Foundry Alloys, AFS, New York, 1990
- F. Paray and J.E. Gruzleski, Microstructure-Mechanical Property Relationships in a 356 Alloy. Part II: Mechanical Properties, Cast Met., 1994, 7, p 153-163
- E. Sjölander and S. Seifeddine, The Heat Treatment of Al-Si-Cu-Mg Casting Alloys, J. Mater. Process. Technol., 2010, 210, p 1249-1259
- S.P. Midson, C.A. Dallmann, J.A. Brennan, T6 Heat Treating of Strontium Modified, Low-Iron Conventional Die Castings, NADCA Die Casting congress & exposition 2015, 2015
- A.M. Samuel and F.H. Samuel, A Metallographic Study of Porosity and Fracture Behavior in Relation to the Tensile Properties in 319.2 End Chill Castings, Metall. Mater. Trans. A, 1995, 26A, p 2359-2372
9. Copyright:
- This material is "Silvia Cecchel, Andrea Panvini, and Giovanna Cornacchia"'s paper: Based on "Low Solution Temperature Heat Treatment of AlSi9Cu3(Fe) High-Pressure Die-Casting Actual Automotive Components".
- Paper Source: https://doi.org/10.1007/s11665-018-3478-4
This material was summarized based on the above paper, and unauthorized use for commercial purposes is prohibited.
Copyright © 2025 CASTMAN. All rights reserved.