P. Jelínek, E. Adámková*
Department of Metallurgy and Foundry Engineering, VŠB-Technical University of Ostrava,
- listopadu 2172/15, 708 33 Ostrava – Poruba, Czech Republic
*Corresponding author. E-mail address: eliska.adamkova@vsb.cz
Received 04.03.2014; accepted in revised form 30.03.2014
Abstract
Development of salt cores prepared by high-pressure squeezing and shooting with inorganic binders has shown a high potential of the given technology even for high-pressure casting of castings. Strength, surface quality of achieved castings, and solubility in water become a decisive criterion. The shape and quality of grain surface particularly of NaCl – cooking salts that can be well applied without anticaking additives has shown to be an important criterion. Thus the salt cores technology can cover increasingly growing demands for casting complexity especially for the automobile industry.
Korea
무기 바인더를 사용한 고압 압착 및 촬영에 의해 준비된 솔트 코어의 개발은 주물의 고압 주조에서도 주어진 기술의 높은 잠재력을 보여주었습니다. 달성된 주물의 강도, 표면 품질 및 물에 대한 용해도가 결정적인 기준이 됩니다.
특히 NaCl의 곡물 표면의 모양과 품질은 고결 방지 첨가제 없이 잘 적용될 수 있는 요리 용 소금이 중요한 기준이 되는 것으로 나타났습니다. 따라서 솔트 코어 기술은 특히 자동차 산업에서 주조 복잡성에 대한 증가하는 수요를 충족시킬 수 있습니다.
Keywords: Innovative foundry technologies and materials, Product development, Salt cores, High-pressure die casting, Squeezinginjection
Introduction
Classic metal cores used for high-pressure casting of castings cannot entirely cover increasingly growing demands for shape complexity of castings especially for automobile industry [1, 2]. Therefore the interest in development of soluble cores (Verlorene Kerne, Lost Cores) that would also enable at the same time the closed technological cycle is growing.
This prerequisite is met by cores from inorganic salts soluble in water. But the application of them is limited above all by strength properties and both under low temperatures (primary strength) and under increased temperatures too.
On the other hand it is also limited by casting conditions – injecting of metal into the mould (the rate in ingates, post-pressure, laminar filling, gating system). According to some authors the salt cores are suitable for lower filling rates (under 35 m/s) with limited post-pressure, i.e. ideal e.g. for the „rheocasting“ technology [3].
The contribution deal with development of salt cores by way of high-pressure squeezing and shooting with use of alkali silicate binders and their applications on test high-pressure cast castings.
Korea
주조의 고압 주조에 사용되는 고전적인 금속 코어는 특히 자동차 산업에서 주조의 모양 복잡성에 대한 증가하는 수요를 완전히 충족 할 수 없습니다 [1, 2]. 따라서 폐쇄 된 기술주기를 동시에 가능하게하는 가용성 코어 (Verlorene Kerne, Lost Cores) 개발에 대한 관심이 증가하고 있습니다.
이 전제 조건은 물에 용해되는 무기 염의 코어로 충족됩니다. 그러나 이들의 적용은 무엇보다도 강도 특성과 저온 (1 차 강도) 및 고온에서도 제한됩니다. 다른 한편으로, 그것은 또한 주조 조건에 의해 제한됩니다.
금형에 금속 주입 (인 게이트의 속도, 후압, 층상 충전, 게이팅 시스템). 일부 저자에 따르면 소금 코어는 후압이 제한된 낮은 충전 속도 (35m / s 미만)에 적합합니다. "rheocasting"기술 [3].
이 공헌은 알칼리 규산염 바인더를 사용한 고압 압착 및 사격을 통한 소금 코어의 개발과 테스트 고압 주조 주조에 대한 적용을 다룹니다.
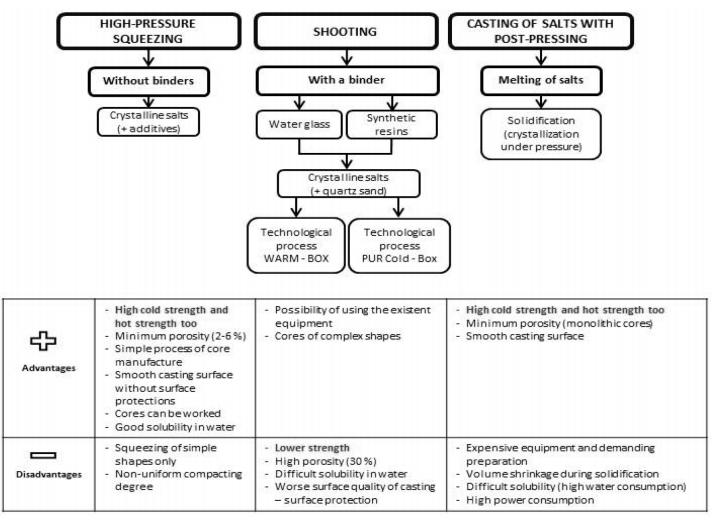
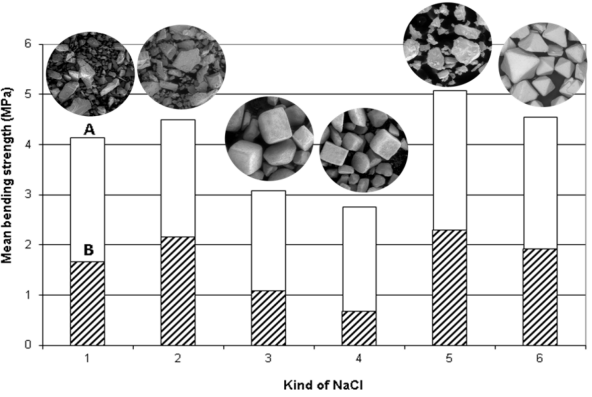
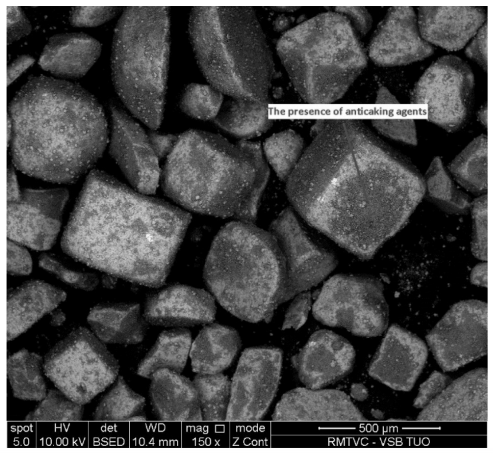
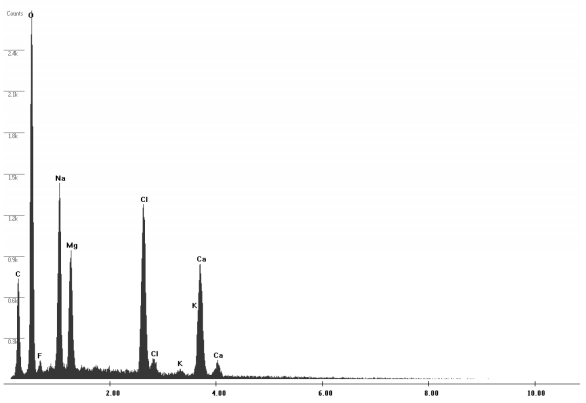
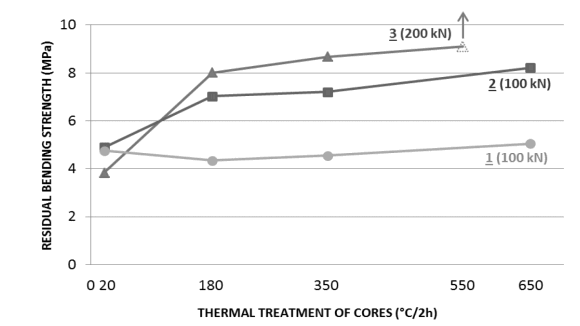
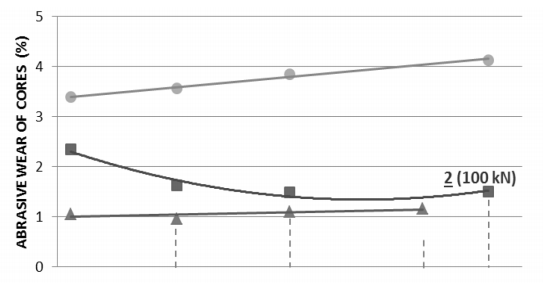
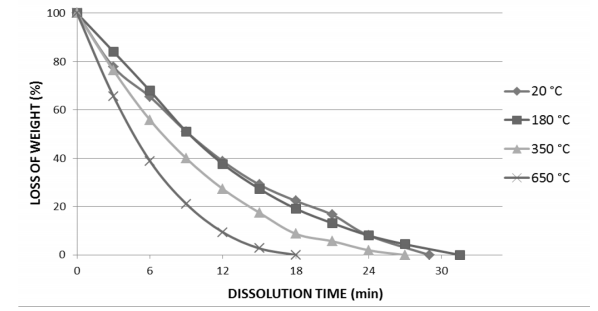
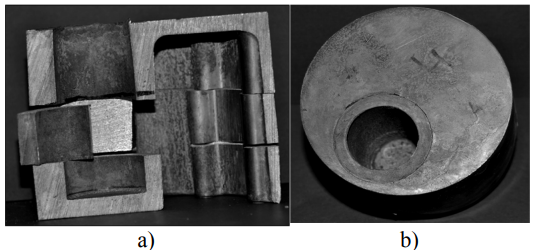
References
[1] Brůna, M., Sládek, A. & Kucharčík, L. (2012). Formation of porosity in Al-Si alloys. Archives of Foundry Engineering.
12(1), 5-8. DOI: 10.2478/v10266-012-0001-5.
[2] Lichý, P., Bednářová, V. & Elbel, T. (2012). Casting routes for porous metals production. Archives of Foundry
Engineering. 12(1), 71-74. DOI: 10.2478/v10266-012-0014-0.
[3] Michels, H., Bűnck, M. & Bűhrig – Polaczek, A. (2010). Suitability of lost cores in rheocasting process. Transactions
of Nonferrous Metals Society of China. 20, 948-953. DOI: 10.1016/S1003-6326(10)60612-7.
[4] Kallien, L., Bőhnlein, Ch., Dworak, A. & Műller, B. (2013). Ergebnisse aus dem Forschungsprojekt 3-D-Freiform –
medienführende Kanäle im Druckguss. Giesserei Praxis. 100(12), 36-43.
[5] Jelínek, P., Mikšovský, F., Beňo, J. & Adámková, E. (2013). Development of Foundry Cores Based on Inorganic Salts.
Materials and technology. 47(6), 689-693. ISSN: 1580-2949, 1580-3414.
[6] Adámková, E., Jelínek, P., & Študentová, S. (2013). Application of cooking salts in manufacture of water soluble
cores for high pressure die casting (Aplikace kuchyňských solí při výrobě vodou rozpustných jader odlitků tlakového
lití). Materials and technology. 61(11-12), 689-693. ISSN: 1580-2949, 1580-3414.
[7] Jelínek, P., Mikšovský, F., & Adámková, E. (2012). Influencing the strength characteristics of salt cores soluble in
water (Ovlivňování pevnostních charakteristik solných ve vodě rozpustných jader). Slévárenství. 60(3-4), 85-89. ISSN:
0037-6825.
[8] Fuchs, B., Eibisch, H. & Körner, C. (2013). Core viability simulation for salt core technology in high – pressure die
casting. International Journal of Metalcasting. 7(3), 39-45. ISSN: 1939-5981.