This introductory paper is the research content of the paper ["INNOVATIVE COOLING SOLUTIONS OF HPDC TECHNOLOGY"] published by [Multidiszciplináris Tudományok].
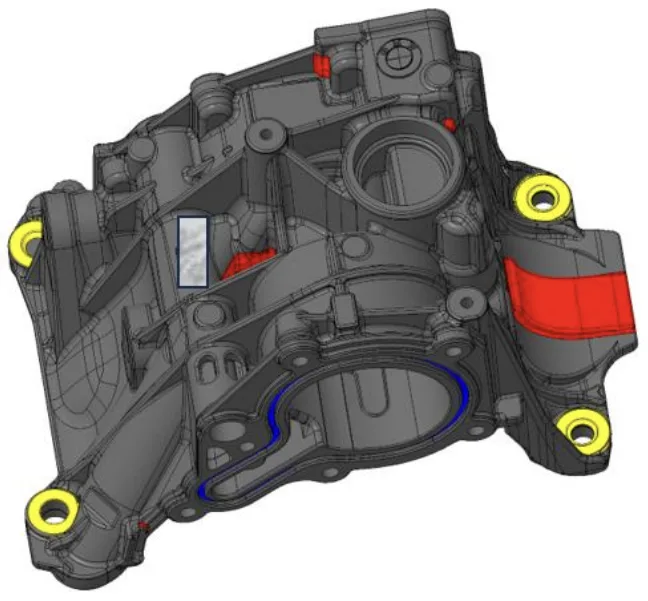
1. Overview:
- Title: INNOVATIVE COOLING SOLUTIONS OF HPDC TECHNOLOGY
- Author: Zoltán Ferenc Bratu, János Péter Erdélyi, Dániel Molnár
- Publication Year: 2024
- Published Journal/Society: Multidiszciplináris Tudományok, 14. kötet, 3. szám
- Keywords: HPDC, 3D printed sliders, laser cusing, cooling technology
2. Abstract
In High Pressure Die Casting (HPDC), the so-called sliders are moving components of the mould, that can form cavities, holes, and undercuts. Sliders differ greatly from fixed- and moving mould halves regarding cooling and thermal balance. Sliders can also be used to improve local heat dissipation in different areas. They are equipped with cooling holes through which the hole-forming cores, which penetrate deep into the mould cavity, can be tempered. As the industry produces increasingly complex castings, the cooling systems for the various moulds, inserts and cavities have evolved accordingly. This has resulted in innovative solutions and developments in the cooling of moulds and mould inserts, such as the use of 3D-printed metal inserts with improved heat dissipation. This article compares the cooling differences between traditionally cooled and 3D-printed sliders. We investigate cooling efficiency and tool temperatures at different cooling intensities through simulation experiments. Furthermore, at the end of the solidification phase, we examine the mold temperatures and the heat extracted for different molds and cooling intensities.
3. Research Background:
Background of the research topic:
High pressure die casting is a rapidly developing industry.
Status of previous research:
One of the most important development trends is to reduce the casting cycle time and the amount of lubricant applied (ASM Metals Handbook, 1998; Butler, 2005; Andresen, 2005). One means of achieving these objectives is using various innovative cooling techniques for moulds to achieve more drastic cooling (Cho et al., 2014; Jarfors et al., 2021).
Need for research:
Not explicitly stated in the provided text, but implied: The need exists to improve cooling efficiency and reduce cycle times in HPDC, particularly for complex castings.
4. Research purpose and research question:
Research purpose:
To compare the cooling differences between traditionally cooled and 3D-printed sliders in HPDC.
Core research:
- Investigate cooling efficiency and tool temperatures at different cooling intensities.
- Examine the mold temperatures and the heat extracted for different molds and cooling intensities at the end of the solidification phase.
5. Research methodology
The research employed simulation experiments using the commercially available Magma casting simulation software (www.magmasoft.de). The experimental geometry was a single-cavity die-casting mould with two side sliders, one top slider, and one fixed side obliquely moving slider. The enclosing dimensions of the mould are 876 x 783 x 687 mm. The complexity of the casting under test is illustrated in Figure 1. Cooling of the mould was provided by oil and water cooling circuits using a Reglopast cooling and heating unit (www.regloplas.com). The material of the sliders is 1.2343 (ESU HRC47) hot-worked steel (uddenholm.com).
The experiments involved comparing original cast material sliders with experimentally optimized 3D printed sliders. The 3D printed sliders were made using laser cusing, with the same material quality as the original cast sliders (1.2343 (ESU HRC47)). Figure 2-3 show the cooling system in the original cast material sliders. Figure 4-7 show the cooling system of the 3D printed backdrop. Figure 8 and Figure 9 show the structure of each cooling system imported from the 3D mould designs.
Simulation tests were carried out to investigate:
- The temperature conditions during filling and solidification.
- The amount of heat dissipated during the solidification phase.
- The position and morphology of the shrinkage cavities formed in the casting.
Material properties, initial conditions, and boundary conditions corresponded to real production conditions. Table 1 illustrates the main parameters of the four simulation calculations performed, varying cooling type (SLM for 3D printed, Conv. for conventional) and heat transfer coefficient.
6. Key research results:
Key research results and presented data analysis:
- Figure 10 shows the slider temperatures for different simulated versions. The conventional slider temperatures are 40-50°C higher than the 3D printed slider temperatures.
- Figures 11-12 show the mould temperatures simulated with each version. The mould temperatures for conventional cooling and 3D printed sliders show a difference of 20-40°C. For the most intense cooling, the temperature differences range from 40-80°C.
- Figure 13 shows the location and extent of the shrinkage cavities. The volume of shrinkage cavities is ~103 mm³ for conventionally cooled sliders, and ~90, ~70, and ~50 mm³ for 3D printed sliders with increasing cooling intensity.
- Figures 14-17 show the heat balances of the different simulated versions. The energy extracted by the tempering circuits when using the conventional sliders is 413.71 kJ. With the 3D printed sliders, the system can extract 548.19 kJ, 637.79 kJ, and 807.37 kJ of energy, respectively. The difference between the results of the 3D printed sliders with the most powerful cooling and the conventional sliders is 49%.
- Figures 18-21 show the thermal scales of the simulated versions, classified by each cooling channel of the mould. The energy dissipated by the unconventional sliders is shown in Figure 19.
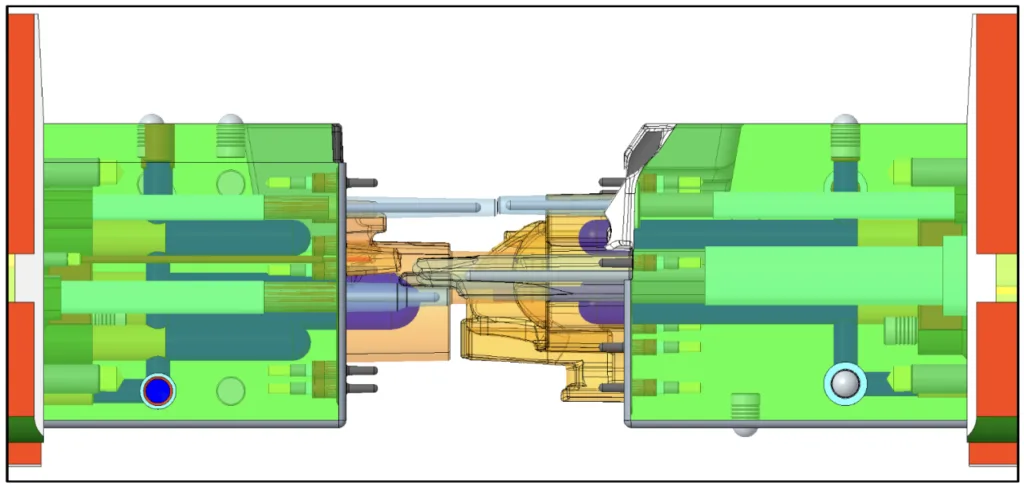

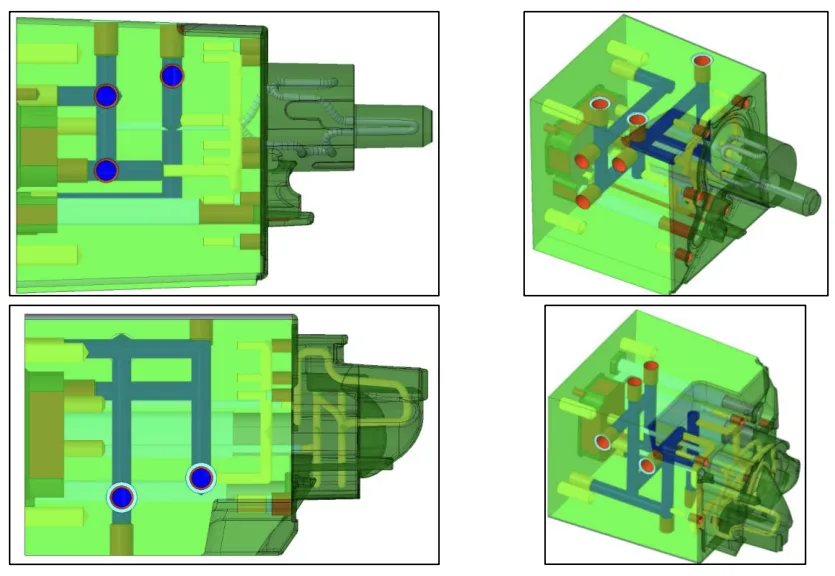
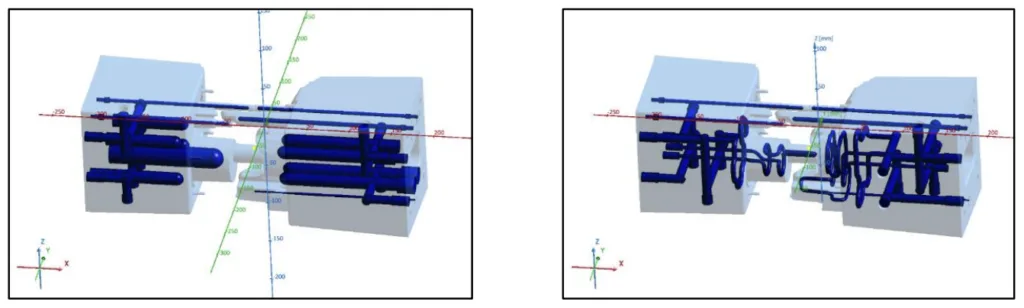
Figure 9. Cooling system of the 3D printed sliders
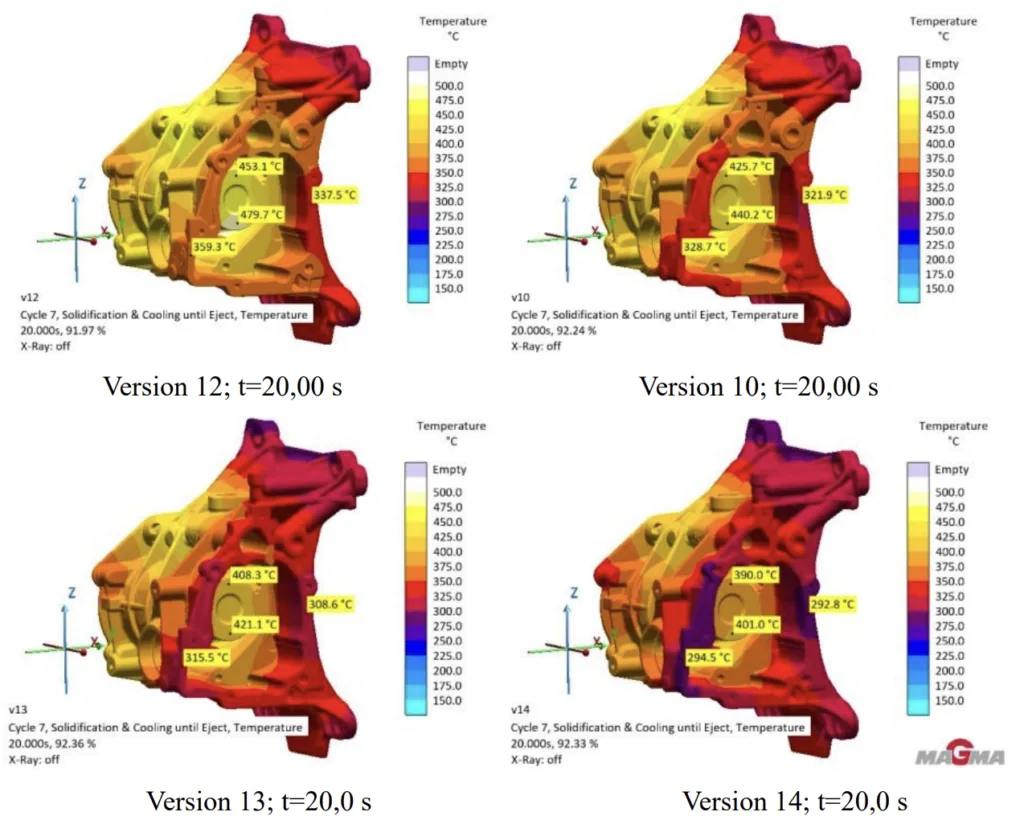

List of figure names:
- Figure 1. Geometry of the tested casting
- Figure 2. Cooling system in the sliders
- Figure 3. Cooling system in the sliders
- Figure 4-7. Cooling system of the 3D printed sliders
- Figure 8. Cooling system of the conventional sliders
- Figure 9. Cooling system of the 3D printed sliders
- Figure 10. Calculated slider temperatures for each version at the time points studied scale: T=150,0-450,0°C
- Figure 11. Calculated casting temperatures for each version at the time points considered, view A, Scale: T=150.0-500.0°C
- Figure 12. Casting temperatures calculated for each version at the time points under investigation, view B, Scale: T=150.0-500.0°C
- Figure 13. Shrinkages calculated for each version shrinkage scale: 0.0-100.0%
- Figure 14. The heat balance of version 12
- Figure 15. The heat balance of version 10
- Figure 16. The heat balance of version 13
- Figure 17. The heat balance of version 14
- Figure 18. Heat balance of version 12 broken down by cooling channels
- Figure 19. Heat balance of version 10 broken down by cooling channels
- Figure 20. Heat balance of version 13 broken down by cooling channels
- Figure 21. Heat balance of version 14 broken down by cooling channels
7. Conclusion:
Summary of key findings:
The 3D printed sliders, due to their larger specific surface area, dissipate more heat compared to conventional sliders. This results in lower slider and mold temperatures, and a higher cooling efficiency. The use of 3D printed sliders also leads to a reduction in the formation of shrinkage cavities. The heat dissipation is significantly higher (up to 49% difference) with 3D-printed sliders compared to conventional sliders.
The research demonstrates the superior cooling performance of 3D-printed sliders in HPDC. This has significant practical implications for the industry, as it can lead to reduced cycle times, lower lubricant usage, and improved casting quality.
8. References:
- [1] ASM Metals Handbook (1998). Casting. Volume 15. ASM International, USA.
- [2] Butler, W. (2005). The next generation of die casting machines. Die Casting Engineer, 1/2005, USA.
- [3] Andresen, B. (2005). Die Casting Engineering. Marcel Dekker, USA
- [4] Cho, J. I. et al. (2014). The relationship between dendrite arm spacing and cooling rate of Al-Si casting alloys in high pressure die casting. International Journal of Metalcasting, 8, 49–55. https://doi.org/10.1007/BF03355571
- [5] Jarfors, A. E. et al. (2021). On the use of conformal cooling in high-pressure die-casting and semisolid casting. Technologies - Manufacturing Technologies, 9(2), 39. https://doi.org/10.3390/technologies9020039
- [6] https://www.regloplas.com
- [7] https://uddeholm.com
- [8] Gibson, I. et al. (2021). Hybrid additive manufacturing. In Additive Manufacturing Technologies (pp. 347-366). Springer, Cham. https://doi.org/10.1007/978-3-030-56127-7_12
- [9] https://www.magmasoft.de
9. Copyright:
- This material is a paper by "[Zoltán Ferenc Bratu, János Péter Erdélyi, Dániel Molnár]": Based on "[INNOVATIVE COOLING SOLUTIONS OF HPDC TECHNOLOGY]".
- Source of paper: https://doi.org/10.35925/j.multi.2024.3.17
This material was created to introduce the above paper, and unauthorized use for commercial purposes is prohibited. Copyright © 2025 CASTMAN. All rights reserved.