This introduction paper is based on the paper "Influence of Zr, Cr and Sc alloying on the microstructure and mechanical properties of a Al-Mg-Si casting alloy" published by "Technische Universität Darmstadt".
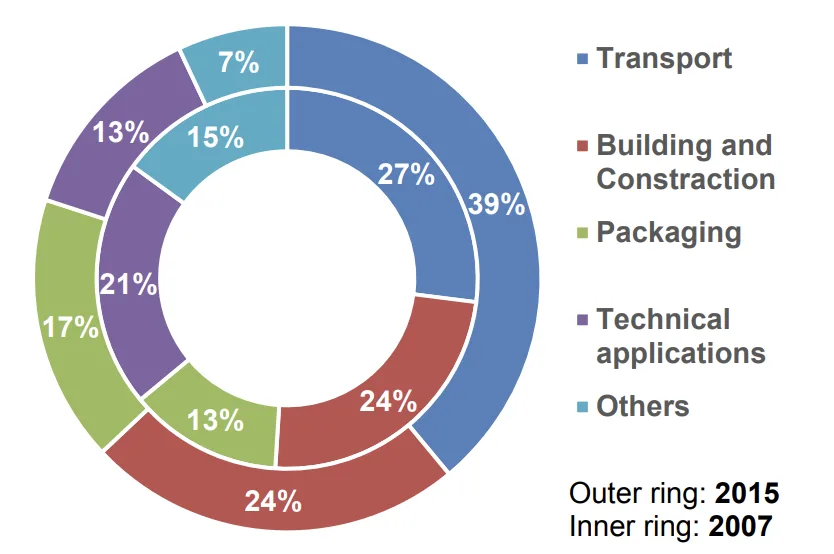
1. Overview:
- Title: Influence of Zr, Cr and Sc alloying on the microstructure and mechanical properties of a Al-Mg-Si casting alloy
- Author: Prach Olena, M.Sc.
- Year of publication: 2021
- Journal/academic society of publication: Technische Universität Darmstadt
- Keywords: Al-Mg-Si casting alloy, Zirconium, Chromium, Scandium, Microstructure, Mechanical properties, High-Pressure Die Casting (HPDC)
2. Abstract:
In the present work, new Al-Mg-Si-Mn casting alloys with the addition of Sc, Cr and Zr were developed and mechanical properties along with the microstructure were studied. Differential Scanning Calorimetry studies of the Al-Mg-Si-Mn alloys determined the eutectic melting temperature of 595°C, with additions of Cr, Zr, and Sc not changing the alloy solidification behaviour. Minor additions of Cr, Zr and Sc did not essentially change the microstructure, primarily consisting of α-Al and α-Al15(Mn,Fe)3Si2 phase, but produced a slight modification of the interlamellar spacing. Al3Zr and Al7Cr intermetallic phases were observed in Sc-free alloys, while Al3Sc and Al3Zr phases were observed in Sc-containing alloys. Zr, Cr and Sc mainly enriched the solid solution. Microhardness and nanohardness measurements showed consistent trends within alloy groups. Additions of Zr or Zr+Cr did not significantly increase yield and tensile strength over the base alloy, while Sc additions significantly increased tensile properties. The SZ11 alloy (Sc+Zr) showed comparable results to the S2 (Sc-only) alloy. Artificial aging (T5) from the as-cast state did not lead to precipitation strengthening in the base alloy. Sc-free alloys responded best to T5 at 225°C, while Sc-containing alloys benefited most at 325°C due to nano-dispersed Al3Sc precipitates. High-temperature solution treatment (T6) led to spheroidization of fibrous eutectic, degrading strength but increasing ductility. Unexpectedly, HPDC alloys showed a positive ductility response to the T6 regime.
3. Introduction:
Light-weight Al-alloys are increasingly important for energy saving and fuel efficiency in the transportation sector. Al-Mg-Si wrought alloys (6xxx series) are widely used due to their excellent strength potential via precipitation hardening. While Al-Si cast alloys dominate over 90% of aluminum castings, Al-Mg-Si casting alloys are less common but are gaining traction in automotive and aerospace for their good castability, corrosion resistance, and mechanical properties in the as-cast state.
The aim of this thesis is to improve the mechanical properties of the commercially available alloy Magsimal®59 by alloying with Sc, Cr, and Zr. Scandium addition is known to significantly increase strength via Al3Sc precipitates and grain refinement, but its high cost limits its use. Zirconium offers improved workability and is cheaper, while Chromium is used for grain structure control and toughness.
The main objectives include increasing knowledge of Sc-, Zr-, and Cr-containing Al-Mg-Si alloys, investigating the effects of single additions of Sc and Zr, and exploring the possibility of full or partial Sc substitution by Zr and/or Cr to achieve similar mechanical properties and precipitation behaviour.
4. Summary of the study:
Background of the research topic:
Aluminum alloys are critical for lightweighting in various industries, especially transportation, to reduce fuel consumption and emissions. Al-Mg-Si alloys, known for their heat-treatability and good balance of properties, are primarily used as wrought products. However, there is a growing interest in developing high-performance Al-Mg-Si casting alloys, particularly for high-pressure die casting (HPDC), to combine complex shape capabilities with good mechanical performance. Optimizing these alloys through microalloying with elements like Zr, Cr, and Sc can enhance their microstructure and mechanical properties.
Status of previous research:
Previous research has established the benefits of Al-Mg-Si systems, including commercial casting alloys like Magsimal®59, Hydronalium 511, and Aural11, which offer good mechanical properties in the as-cast state. The effects of individual additions of Sc (significant strengthening, grain refinement), Zr (improved workability, Al3Zr precipitates), and Cr (grain structure control, toughness) to aluminum alloys are known, primarily from studies on wrought alloys or other Al alloy systems. However, comprehensive studies on Al-Mg-Si casting alloys, especially HPDC variants, with combined additions of these elements, and particularly focusing on Sc substitution, are limited. Thermodynamic modeling and phase diagram calculations are crucial for understanding phase formation in these complex multi-component alloys.
Purpose of the study:
The main goal of this research is to improve the mechanical properties of a commercial Al-Mg-Si casting alloy (Magsimal®59) through systematic alloying with Scandium (Sc), Zirconium (Zr), and Chromium (Cr). Specific objectives include:
- To investigate the influence of individual and combined additions of Sc, Zr, and Cr on the microstructure and mechanical properties of the Al-Mg-Si base alloy.
- To explore the potential for partial or full substitution of expensive Scandium with more economical Zirconium and/or Chromium while maintaining or enhancing mechanical performance.
- To understand the precipitation behaviour and strengthening mechanisms in these newly developed alloys in both as-cast and heat-treated conditions.
Core study:
The core of this study involved the development and investigation of new Al-Mg-Si-Mn casting alloys based on the Magsimal®59 composition, with systematic additions of Zr, Cr, and Sc, individually and in combination. These alloys were produced by high-pressure die casting (HPDC). The research focused on:
- Microstructural Characterization: Comprehensive analysis of the as-cast and heat-treated microstructures using Differential Scanning Calorimetry (DSC), optical microscopy, Scanning Electron Microscopy (SEM) with Energy Dispersive Spectrometry (EDS), and Transmission Electron Microscopy (TEM). This included identification of constituent phases, intermetallic compounds (e.g., Al15(Mn,Fe)3Si2, Al3Zr, Al7Cr, Al3Sc), eutectic morphology (Mg2Si), Dendrite Arm Spacing (DAS), and Interlamellar Spacing (ILS).
- Mechanical Property Evaluation: Assessment of mechanical properties including microhardness, macrohardness (Brinell), nanohardness (of α-Al matrix and eutectic regions, and intermetallic phases), and tensile properties (yield strength, ultimate tensile strength, elongation) in both as-cast and various heat-treated states (T5 and T6 regimes).
- Heat Treatment Response: Investigation of the alloys' response to different artificial aging (T5 from as-cast state at 125-325°C) and solution treatment followed by artificial aging (T6 regime, including study of outgassing phenomena) heat treatments.
- Thermodynamic Calculations: Utilization of Thermo-Calc software to predict phase diagrams and understand phase formation in the developed multicomponent alloys.
5. Research Methodology
Research Design:
The research was designed to systematically investigate the influence of alloying elements Zr, Cr, and Sc on a base Al-Mg-Si-Mn alloy (commercial Magsimal®59). A series of experimental alloys were developed with varying concentrations of these elements, individually and in combination (details in Table 3.6). All alloys were produced using High-Pressure Die Casting (HPDC) to ensure conditions relevant to industrial application. The study compared the developed alloys against the base alloy in as-cast and various heat-treated conditions (T5 and T6).
Data Collection and Analysis Methods:
- Casting: Alloys were prepared using a Frech DAK 450-54 cold chamber HPDC machine. Master alloys (AlCr20, AlZr15, AlSc2) were used for additions.
- Chemical Analysis: Spark emission spectroscopy (Ametek Spectromaxx) for composition control.
- Differential Scanning Calorimetry (DSC): Performed using a NETZSCH device to determine phase transformation temperatures (e.g., melting, solidification).
- Microstructural Characterization:
- Optical Microscopy and Scanning Electron Microscopy (SEM - TESCAN Mira3) with Energy Dispersive Spectrometry (EDS) for phase identification, morphology, distribution, Dendritic Arm Spacing (DAS), and Interlamellar Spacing (ILS) using ImageJ software.
- Electron Probe Microanalysis (EPMA - JEOL JXA-8100) for detailed elemental mapping.
- Transmission Electron Microscopy (TEM - Philips CM20) for observing fine precipitates and dispersoids.
- Mechanical Testing:
- Hardness: Brinell hardness, Vickers microhardness (Zwick Roell), and nanoindentation (iNano, G200 with Berkovich tip) using LC and CSM modes.
- Tensile Tests: Uni-axial tensile tests at room temperature on an Instron 5967 machine according to ASTM E8_E8M_13a.
- Heat Treatment: T5 (artificial aging from as-cast state at 125°C, 175°C, 220°C, 325°C) and T6 (solution treatment at 480-570°C, water quenching, followed by artificial aging at 175°C, 225°C, 325°C). Outgassing effects during ST were also studied.
- Thermodynamic Calculations: Thermo-Calc software (TCAl2: Al-alloys v2.1 database) was used to calculate phase diagrams and predict phase formation.
Research Topics and Scope:
The research focused on Al-Mg-Si-Mn casting alloys, specifically the Magsimal®59 base composition, modified with additions of Zirconium (0.1-0.2 wt.%), Chromium (0.1-0.3 wt.%), and Scandium (0.1-0.2 wt.%), as well as their combinations (e.g., Cr+Zr, Sc+Zr). The scope covered:
- Investigation of phase transformations and solidification behavior using DSC.
- Detailed microstructural analysis (phases present, their morphology, size, distribution, elemental segregation) in the as-cast state. Identified phases include α-Al, Mg2Si eutectic, α-Al15(Mn,Fe)3Si2, Al3Zr, Al7Cr, and Al3Sc.
- Quantification of microstructural features like DAS, ILS, and volume fraction of phases.
- Evaluation of mechanical properties (various hardness scales, tensile strength, yield strength, elongation) in the as-cast state.
- Study of the response to heat treatments:
- T5 aging: aging kinetics and effect on hardness and tensile properties.
- T6 regime: effect of solution treatment temperature on outgassing, microstructure, and subsequent aging response on hardness and tensile properties.
- Correlation of microstructure with mechanical properties.
- Assessment of the potential for Sc substitution by Zr and/or Cr.
6. Key Results:
Key Results:
As-cast state:
- DSC: The eutectic melting temperature of the Al-Mg-Si-Mn alloys was determined to be around 595°C. Additions of Cr, Zr, and Sc (single or dual) did not significantly alter the alloy solidification behavior.
- Microstructure: The main phases were α-Al (equiaxed, globular-rosette morphology, DAS ~10-12 µm) and α-Al15(Mn,Fe)3Si2. Additions of Cr, Zr, and Sc slightly modified the interlamellar spacing (ILS) of the Mg2Si eutectic.
- Sc-free alloys: Al3Zr (orthogonal, ~13 µm in Z2) and Al7Cr intermetallic phases were observed depending on Zr/Cr content.
- Sc-containing alloys: Al3Sc (irregular shape, near α-Al15(Mn,Fe)3Si2) was observed, particularly in S2 (0.2 wt.% Sc). With Zr addition, Al3Zr phase was also present (e.g., SZ11, SZ21, with larger Al3Zr in SZ21).
- Zr, Cr, and Sc primarily enriched the solid solution. Mn and Cr were partly in primary particles and partly in solid solution.
- Hardness: Within alloys with the same primary alloying element (e.g., Z1-Z2, S1-S2), mean microhardness and nanohardness were similar. Sc-containing alloys generally showed higher hardness. Additions of Zr or Zr+Cr did not lead to a significant increase in macro/micro hardness over the base M59. Sc and Sc+Zr additions led to the highest macrohardness (e.g., SZ21 and SCZ ~15% harder than M59). Nanohardness of α-Al and eutectic regions increased with alloying, with Sc and Sc+Zr additions showing the highest eutectic hardness.
- Tensile Properties: Additions of Zr or Zr+Cr did not significantly increase yield strength. Alloying with Sc significantly increased tensile properties (YS, UTS, Elongation). 0.1 wt.% Sc was sufficient for solid solution enrichment; further Sc addition did not lead to more strengthening. The SZ11 alloy (Sc+Zr) showed comparable tensile results to the S2 (Sc-only) alloy.
Heat treated state:
- T5 Aging (from as-cast):
- Base alloy (M59) did not show significant precipitation strengthening.
- Sc-free alloys showed a good response at 225°C.
- Sc-containing alloys showed the greatest benefit at 325°C, with nano-dispersed Al3Sc precipitates observed (e.g., S1, S2 alloys after aging at 225°C/325°C).
- S2 alloy (0.2 wt.% Sc) achieved the highest YS and UTS at 325°C.
- T6 Regime (Solution Treatment + Aging):
- High-temperature solution treatment (ST > 520°C) led to spheroidization of fibrous Mg2Si eutectic, causing a strong degradation of tensile/yield strengths but an increase in ductility.
- Outgassing (blistering) was observed at ST temperatures ≥ 520°C for the base alloy.
- Hardness after ST was lower than as-cast, but increased after aging.
- For the base alloy, T6 (ST at 570°C + AA at 175°C) resulted in hardness comparable to T5, with YS increasing from 164 MPa (as-cast) to 200 MPa. For S2 alloy, YS increased from 194 MPa (as-cast) to 220 MPa. Elongation was generally lower after T6 compared to as-cast due to blistering at high ST temperatures.
- Low ST temperatures (e.g., 480°C) did not dissolve Mg2Si effectively, resulting in poor aging response.
- Al3Zr, Al3Sc, and Al7Cr primary intermetallics were not significantly affected by ST at 520°C.
- Comparison: HPDC alloys showed an unexpected positive response to the T6 regime in terms of ductility if blistering could be controlled. T5 treatment, especially for Sc-containing alloys at 325°C, offered significant strength improvements. The combination of Al3Sc and Mg2Si precipitation hardening provides a complex scenario for optimizing heat treatment.
![Figure 2.5 Graphical illustration of a) hot-chamber, b) cold-chamber die casting
machine[32]](https://castman.co.kr/wp-content/uploads/image-2222-1024x447.webp)
![Figure 2.6 a) Structural zone formation in castings [36], b) dendritic arms [36], c) SEM image of dendrites in Al-Mg-Si alloys (present work), d) SEM image of aluminum dendrites in the fractured surface of a tensile test bar of the Al-MgSi alloy (present work).](https://castman.co.kr/wp-content/uploads/image-2223-1024x880.webp)
![Figure 6.17 Microstructure of the AlMg5Si2Mn HPDC alloy and 3D modelling of theMg2Si eutectic in the a)as-cast and b,c) heat-treated state. From [171]](https://castman.co.kr/wp-content/uploads/image-2224-1024x540.webp)
Figure Name List:
- Figure 2.1 Fields of the application of Al alloys in 2007 and 2015 as for comparison, adapted from [22].
- Figure 2.2 World aluminum production, adopted from [18].
- Figure 2.3 Semi-product of aluminum alloys, adapted from [22].
- Figure 2.4 Classification of the casting techniques. Adopted from [31]
- Figure 2.5 Graphical illustration of a) hot-chamber, b) cold-chamber die casting machine[32]
- Figure 2.6 a) Structural zone formation in castings [36], b) dendritic arms [36], c) SEM image of dendrites in Al-Mg-Si alloys (present work), d) SEM image of aluminum dendrites in the fractured surface of a tensile test bar of the Al-Mg-Si alloy (present work).
- Figure 2.7 SEM image of the Al-Mg-Si-Sc-Zr alloy with the EDX maps of Mg, Si, Sc, Zr and composition vs distance along the line [45].
- Figure 2.8 Morphology of the Mg2Si eutectic in the a) as-cast Al-Mg2Si alloy and b) after solution treatment at 575°C [49].
- Figure 2.9 Schematic representation of a strengthening mechanisms in Al. Adopted from [50]
- Figure 2.10 Different types of solid solutions a) Substitutional and b) interstitial solid solution. Adapted from [55].
- Figure 2.11 Crystallographic relationships between matrix and second phase. a) coherency with strained, but continuous, lattice planes across the boundary, b) semicoherent, c) incoherent equilibrium precipitate. Adapted from [54,66]
- Figure 2.12 Schematic illustration of interaction mechanisms between dislocations and precipitates: particle looping and particle cutting. Adapted from [71].
- Figure 2.13 Strength vs size of particles, adopted from [50,51].
- Figure 3.1 a)Ternary Al-Mg-Si diagram with the pseudobinary line (red) and an experimentally established an invariant line of L → (Al) + Mg2Si (black curved line), b) binary Al-Mg2Si phase diagram, showing an influence of excess Mg [94] and c) Al-Mg-Si Liquidus surface [88].
- Figure 3.2 Binary phase diagram a) Al-Mg2Si, the investigated alloy is marked with arrow, adapted from [87] and b) calculated Al-5Mg-2Si-(0…2.0)Mn phase diagram.
- Figure 3.3 a) Al-Sc phase diagram [120], b) Al-rich side of Al-Sc diagram calculated by Thermo-Calc.
- Figure 3.4 Scheme of the L12-type structure of Al3Sc precipitates
- Figure 3.5 a) SEM image of Al3Sc particle found in Al-2Sc master alloy [123], b) TEM bright-field image of the Al3Sc particle in Al-0.7Sc alloy [116] and c) TEM bright-field image of Al3Sc precipitates [111].
- Figure 3.6 a) Al-rich side of Al-Zr diagram and b) variety of the crystal structures [130].
- Figure 3.7 TEM images of a) bright and b) dark-field of Al-Mg-Si-Zr wrought alloy after annealing [111]
- Figure 3.8 Bright field TEM images of the Al3(Sc,Zr) nanoparticles, a) [114], b) [135], c) [128]
- Figure 3.9 Calculated phase diagrams of the investigated alloys, AlMg5Si2Mn with additions of a)Zr, b) Cr and Zr
- Figure 3.10 Phase diagrams of the investigated alloys, AlMg5Si2Mn with additions of a) Sc, b) Sc and Zr, c )Sc, Cr and Zr.
- Figure 3.11 a) Typical temperature regions for solution heat treatment and precipitation hardening [13] and b) Precipitation sequence of the investigated alloys, adapted from [50]
- Figure 4.1 a) As-caste plate with gating system and overflow directly after withdrawing from the HPDC machine and b) after removal of the casting system.
- Figure 4.2 a) Schematic illustration of the indentation imprint and its diagonals measurement and b) Image of a microhardness imprint on a polished surface
- Figure 4.3 Schematic illustration of a load displacement curve
- Figure 4.4 Schematic illustration of the tensile test samples
- Figure 5.1 DSC curve of the base alloy in as-cast state.
- Figure 5.2 a) DSC heating and cooling curves of the Sc free alloys, b) enlarged DSC traces for these alloys in a range of 590-600°C.
- Figure 5.3 DSC heating and cooling curves of the Sc containing alloys
- Figure 5.4 Cross section of the plate with the corresponding microstructures.
- Figure 5.5 SEM image of a base alloy: a) an overview of a microstructure, b) Mn- containing intermetallic phase.
- Figure 5.6 SEM image of the base alloy and EMPA maps of the dendritic area
- Figure 5.7 SEM micrographs of the Sc free alloys
- Figure 5.8 EMPA maps of the distribution of the Zr in a)Z1 alloy and b) Z2 alloy
- Figure 5.9 EMPA maps of the distribution of the Zr and Cr in a)CZ11 alloy and b) CZ12 alloy
- Figure 5.10 SEM micrographs of the Sc-containing alloys
- Figure 5.11 SEM images and EMPA maps of the dendritic area of a) S1, b) S2 alloys in as-cast state
- Figure 5.12 SEM images and EMPA maps of the dendritic area of a) SZ11, b) SZ21 alloys in as-cast state
- Figure 5.13 SEM image of the Mn-containing phase in the base alloy. a) polished sample, b) fracture surface and c) Mn-containing phase in Sc-containing alloy.
- Figure 5.14 SEM images of the alloys with coarse Cr-, Zr- containing phases [159]
- Figure 5.15 SEM micrograph and EDS elemental mapping of the Al7Cr and Al3Zr intermetallic phases in the CZ33 alloy [159].
- Figure 5.16 TEM bright-field images of the a-c) base alloy with the β and β' precipitates in the base alloy.
- Figure 5.17 TEM bright-field images of the a- b) Mn-containing dispersoids in the base alloy and Al3Sc precipitates observed in b)S1 and c)S2 alloys
- Figure 5.18 a) Cross section of the plate and b) volume fraction of the α-Al and eutectic close to the edge region and in the middle part of the plate, ILS for the middle region plotted for M59, Z2 and S2 alloys.
- Figure 5.19 a) Macro- and b) micro-hardness of the Sc-free alloys and Sc-containing alloys in as-cast state
- Figure 5.20 Microstructure of investigated alloy with indent in a) α-Al matrix and b) eutectic as an example, nanohardness measurements of the c) α-Al matrix and eutectic.
- Figure 5.21 Images of the α-Al15(Mn,Fe)3Si2 intermetallic phase with the corresponding load-displacement and hardness-displacement curves.
- Figure 5.22 Images of the a) Al7Cr and b) Al3Zr intermetallic phases with the corresponding hardness-displacement curves.
- Figure 5.23 Load–displacement and hardness-displacement curves for the α- Al15(Mn,Fe)3Si2, Al3Zr and Al7Cr primary phases.
- Figure 5.24 Tensile properties of the investigated alloys a) yield strength b) ultimate tensile stress and c) elongation to failure in as-cast state.
- Figure 5.25 Typical SEM morphology of the fracture surface of the as-cast alloys processed by HPDC, a) macroscopic fracture of the tensile bar for the base alloy, b) pores on the fracture surface for the base alloy, c) the enlarged fracture surface of the Sc-free alloy Al3Zr and Al7Cr intermetallics in the d) CZ22 and e) SZ12 alloys.
- Figure 5.26 Effect of the change in the interlamellar space on the a) yield strength and b) elongation.
- Figure 6.1 Microhardness as a function of a time at a) 125, b) 175, c) 225 and d) 325°C.
- Figure 6.2 Tensile properties of the a) base alloy (black line) and Z2 (blue line), b) S2 (green line) as a function of aging temperature for 3hours.
- Figure 6.3 Tensile properties as a function of aging time after AA at 325°C.
- Figure 6.4 Tensile properties as a function of chemical composition after 3 hours of AA a) 225°C b) 325°C
- Figure 6.5 Tensile properties as a function of artificial aging for 3 hours at 225°C and 325°C a-b) yield stress, c-d) ultimate tensile stress and e-f) elongation to failure.
- Figure 6.6 TEM bright-field images of the M59 alloy after artificial aging a-b) at 175ºC; c-d) at 325ºC
- Figure 6.7 TEM bright-field images of the Sc-containing alloys after artificial aging: a) S1 after 225ºC, b) S1 325ºC, c) S2 225ºC, d) S2 325ºC
- Figure 6.8 a) Hardness across the plate after the heat treatment and as-cast state. AA at 175°C (24 hours) and b) surface tensile samples of the base alloy and after different solution-treatment schedules.
- Figure 6.9 Structure after solution treatment at different temperatures during 1h [172].
- Figure 6.10 Hardness-time curves for the base alloy aged at 175°C following the solution treatment procedures at 570 and 480°C. The black curve represents results after AA directly from as-cast state.
- Figure 6.11 Microstructure of the M59 alloy in a) as-cast state and after solution treatment at b) 480°C, c) 520°C, d) 570°C.
- Figure 6.12 SEM images of the a) Z2, b) S2 and c) CZ33 alloys after ST at 520°C during 3h [172].
- Figure 6.13 Stress-strain curves for the base and S2 alloys after high temperature T6 regime (ST570°C+AA175°C).
- Figure 6.14 Tensile properties as a function of chemical composition after ST520+AA225 and ST520+AA325 (marked with red symbols).
- Figure 6.15 TEM bright-field images taken along 〈001〉Al axis of the M59 alloy after the solution treatment without aging at a-b) 520 ºC and c-d) 570ºC*.
- Figure 6.16 TEM bright-field images taken along 〈001〉Al axis showing the Al3Zr dispersoids in Z2 alloy after solution treatment Z2 alloy at 520ºC during 1.5h
- Figure 6.17 Microstructure of the AlMg5Si2Mn HPDC alloy and 3D modelling of theMg2Si eutectic in the a)as-cast and b,c) heat-treated state. From [171]
- Figure 6.18 Comparative stress strain curves for the base alloy and S2 alloy after T6 regime and in as-cast state (dashed lines).
- Figure 6.19 Tensile properties of the M59, Z2 and S2 alloys after different heat treatment regimes.
- Appendix A.1 Casting cycle for cold-chamber die casting [32] (This is a figure in the appendix)
- Appendix A.5 SEM-images of the base alloy after artificial aging at a) 175ºC and b) 325 ºC [SC31]. (This is a figure in the appendix)
- Appendix A.6 Comparative stress-strain curves for the a) alloys with a single addition and b-c) with combined additions in the as-cast state. (This is a figure in the appendix)
7. Conclusion:
The study successfully developed new Al-Mg-Si-Mn casting alloys with Sc, Cr, and Zr additions and characterized their microstructure and mechanical properties.
As-cast state:
- The eutectic melting temperature was consistently ~595°C, unaffected by the minor alloying additions.
- Microstructure consisted of α-Al, Mg2Si eutectic, and α-Al15(Mn,Fe)3Si2 phase. Sc-free alloys could form Al3Zr and Al7Cr, while Sc-containing alloys formed Al3Sc and Al3Zr. These additions slightly modified interlamellar spacing.
- Zr, Cr, and Sc additions primarily enriched the solid solution.
- Hardness (micro, nano) was consistent within alloy groups, with Sc-containing alloys generally harder.
- Zr or Zr+Cr additions did not significantly improve yield/tensile strength over the base alloy. Sc additions, however, markedly increased tensile properties. The SZ11 (Sc+Zr) alloy showed comparable performance to the S2 (Sc-only) alloy, suggesting potential for Sc substitution.
Heat treated state:
- Artificial aging (T5) of the base alloy from as-cast did not lead to precipitation strengthening.
- Sc-free alloys responded well to T5 at 225°C, while Sc-containing alloys benefited most from T5 at 325°C, forming nano-dispersed Al3Sc precipitates.
- The initial step of T6 (high-temperature solution treatment) caused spheroidization of the fibrous eutectic, degrading strength but increasing ductility. Full T6 treatment of the base alloy showed no significant improvement in mechanical properties.
- HPDC alloys, unexpectedly, showed a positive ductility response to the T6 regime.
Overall, alloying with Sc, or Sc combined with Zr, offers significant improvements in mechanical properties for Al-Mg-Si HPDC alloys. The specific heat treatment (T5 vs. T6) must be chosen based on the desired balance of strength and ductility, with T5 at elevated temperatures (e.g., 325°C for Sc-alloys) being promising for strength, and T6 potentially for ductility.
8. References:
- [1] Constellium, Going Full Circle: The Life-Cycle of Aluminium, n.d. https://www.constellium.com/sites/default/files/constellium_-_life_cycle_of_aluminium.pdf.
- [2] Hydro, Aluminium – about Hydro and resource efficiency, 2012. https://www.hydro.com/en-DE/products-and-services/services/remelting-and-recycling/.
- [3] Hydro, Aluminum, environment and society, 2012. www.hydro.com.
- [4] O.M. Barabash, T.N. Legkaya, N.P. Korzhova, O. V. Sulzhenko, Thermodynamic analysis and experimental study of composite structure formation: In eutectic alloys α-Al + Mg2Si, Powder Metall. Met. Ceram. 39 (2000) 458–461. doi:10.1023/A:1011314406064.
- … (The list continues as in the paper, up to [177] and beyond if present in the original document). For brevity, only the first few are listed here as an example. The full list from pages 124-132 of the dissertation would be included in the actual WordPress output.
9. Copyright:
- This material is a paper by "Prach Olena, M.Sc.". Based on "Influence of Zr, Cr and Sc alloying on the microstructure and mechanical properties of a Al-Mg-Si casting alloy".
- Source of the paper: urn:nbn:de:tuda-tuprints-172138
This material is summarized based on the above paper, and unauthorized use for commercial purposes is prohibited.
Copyright © 2025 CASTMAN. All rights reserved.