This introductory paper is the research content of the paper "Influence of process parameters and heat treatment on self-piercing riveting of high-strength steel and die-casting aluminium" published by Elsevier.
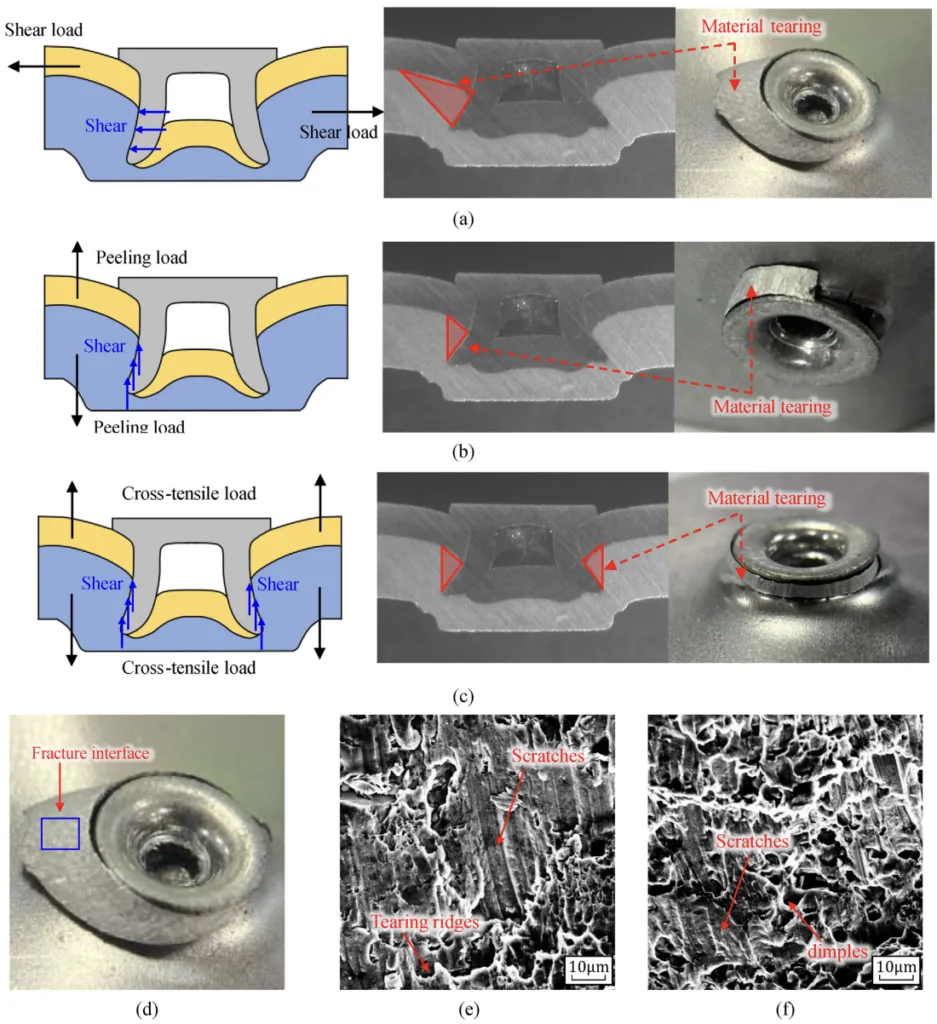
1. Overview:
- Title: Influence of process parameters and heat treatment on self-piercing riveting of high-strength steel and die-casting aluminium
- Author: Chao Wang, Zhanpeng Du, Aiguo Cheng, Zhicheng He, Hailun Tan, Wanyuan Yu
- Publication Year: 2023
- Published Journal/Society: Journal of Materials Research and Technology
- Keywords: Self-piercing riveting, Die-casting aluminium, Cracking mechanism, Joinability, Mechanical response
2. Abstract
The application of steel/die-casting aluminum alloy is an inevitable trend in the development of automotive lightweight technology. The joining process of self-piercing riveting (SPR) is the key technology to guarantee the collision safety for the body. However, the crackings on joint button can be easily found owing to the low ductility of die-casting aluminum. This paper aims to investigate cracking mechanism and improve the SPR joinability by exploring methods of cracking inhibition. Parametric study is performed to explore the effects of heat treatment, process parameters on crack inhibition and forming quality of SPR with steel/die aluminum alloy. The results show that SPR joinability can be improved by larger elongation and lower yield strength by proper heat treatments, i.e., AlSi10MnMg-T6 and AlSi10MnMg-T7. Meanwhile, the depth and diameter of the die are the main factors affecting cracking generation and forming quality. Similar to the upsetting process, tangential tensile stress is generated on the bottom surface in the riveting process, it leads to cracking generation on the bottom surface. This paper further studies the effects of heat treatment and stack direction on joint quality and mechanical response of SPR joints. Tearing failure of the lower sheet is the main factor causing failure of steel-aluminium joint (steel is the top sheet). The heat treatment mainly affects the energy absorption value and has a relatively small effect on the peak force. The mechanical properties of the steel-aluminium joints are superior to those of aluminium-steel joints (aluminium is the top sheet).
3. Research Background:
Background of the research topic:
- Lightweighting is an urgent demand for the automotive industry to achieve energy saving and emission reduction [1].
- Hybrid use of aluminum and high-strength steel in body-in-white (BIW) is a practical method for lightweighting [2,3].
- Die-casting aluminium parts can reduce vehicle weight [2,3].
Status of previous research:
- Resistant spot welding (RSW) is unsuitable for joining steel-aluminum sheets [4].
- Self-piercing riveting (SPR) is a key joining process for aluminum and mixed-material lightweight structures [5].
- Previous studies have investigated the effects of process parameters (sheet thickness, rivet length, die geometry) on SPR joint quality and strength [6,7,8,9,10,11,12,13].
- Cracking in die-casting aluminum bottom sheets is a significant challenge, affecting corrosion resistance and joint strength [14-17].
- Existing methods to reduce cracking include process parameter optimization, adding ductile materials, and new SPR processes (F-SPR, L-SPR, TA-SPR) [15,19,20,21,22,23,24,25,26,27,28,29,30,31,32,33,34].
- Heat treatment can affect the mechanical properties of casting aluminum alloys [35,36,37].
Need for research:
- Limited research exists on the combined influence of process parameters and heat treatments on cracking and forming quality.
- It's unclear how to select versatile rivets and dies for low-ductility die-casting aluminum.
- Comprehensive consideration of the combined effects of process parameters and heat treatment is lacking.
- The impacts of both heat-treated and non-heat-treated materials need investigation.
4. Research purpose and research question:
Research purpose:
- To investigate the cracking mechanism in SPR of steel/die-casting aluminum.
- To improve SPR joinability by exploring methods of cracking inhibition.
- To solve the crackings for die-casting aluminium part using suitable process parameters and heat treatment.
- To explore the effect of heat treatment and stack direction on mechanical response.
Core research:
- Effects of rivet length, die diameter, die depth, and heat treatments on joint quality.
- Analysis of cracking generation mechanisms using microscopy.
- Effects of heat treatment and stack direction on the mechanical response of SPR joints.
5. Research methodology
- Research Design: Parametric study, experimental investigation.
- Materials: High-strength steel HC340/590DP (1.6 mm thick), die-casting aluminum AlSi10MnMg and JDA1b (3.0 mm thick). Chemical compositions are detailed in Table 1. Material properties are in Table 3.
- Heat Treatments: Three heat treatment conditions for AlSi10MnMg (T5, T6, T7) were used, as listed in Table 2.
- Riveting Details: Servo SPR system (EPRESS GmbH), load-control mode, 80 kN max riveting force, 100 mm/s riveting speed. Semi-tubular rivets made of boron steel (H5). Three die types (flat die I, flat die II, pip die) with varying parameters (Table 5, Fig. 2).
- Experimental Setup: Aluminum as the bottom sheet. Detailed analysis scheme in Table 4.
- Data Collection:
- Riveting experiments with varying parameters (rivet length, die diameter, die depth, heat treatment).
- Metallurgical microscopy and scanning electron microscopy (SEM) analysis.
- Quasi-static tests (shear, peeling, cross-tension) using a universal testing machine (ETM105D) at 3 mm/min.
- Analysis Method:
- Joint quality evaluation: Forming quality (height of rivet head, undercut, bottom thickness, remaining thickness - Fig. 3(a), Table 6) and appearance quality (cracking grades - Fig. 4).
- Joinability matrixes (Fig. 6).
- Analysis of cracking mechanisms.
- Comparison of mechanical properties (peak force, energy absorption).
6. Key research results:
Key research results and presented data analysis:
- Joinability: SPR joinability can be improved by larger elongation and lower yield strength through heat treatments (AlSi10MnMg-T6, AlSi10MnMg-T7) (Fig. 8).
- Die Depth and Diameter: The depth and diameter of the die significantly affect cracking generation and forming quality (Fig. 9). Larger depth and diameter improve forming quality but increase cracking risk.
- Rivet Length: Rivet length has a relatively small influence on cracking generation. Proper rivet length (6.0-6.5 mm) can improve forming quality.
- Cracking Mechanism: Tangential tensile stress generated on the bottom surface during riveting leads to cracking (Fig. 11, Fig. 12, Fig. 13, Fig. 14, Fig. 15).
- Stack Direction: Steel-aluminum joints (steel top, aluminum bottom) have superior mechanical properties compared to aluminum-steel joints (Fig. 20).
- Heat Treatment Effects: Heat treatment mainly affects energy absorption, with a smaller effect on peak force (Fig. 20).
- Failure Mode: Tearing failure of the lower sheet is the main factor causing failure of steel-aluminium joint (steel is the top sheet).
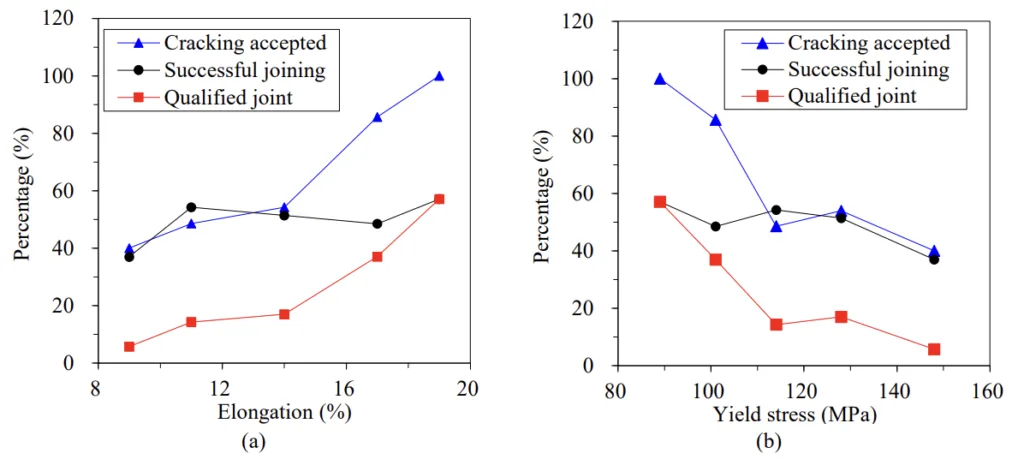
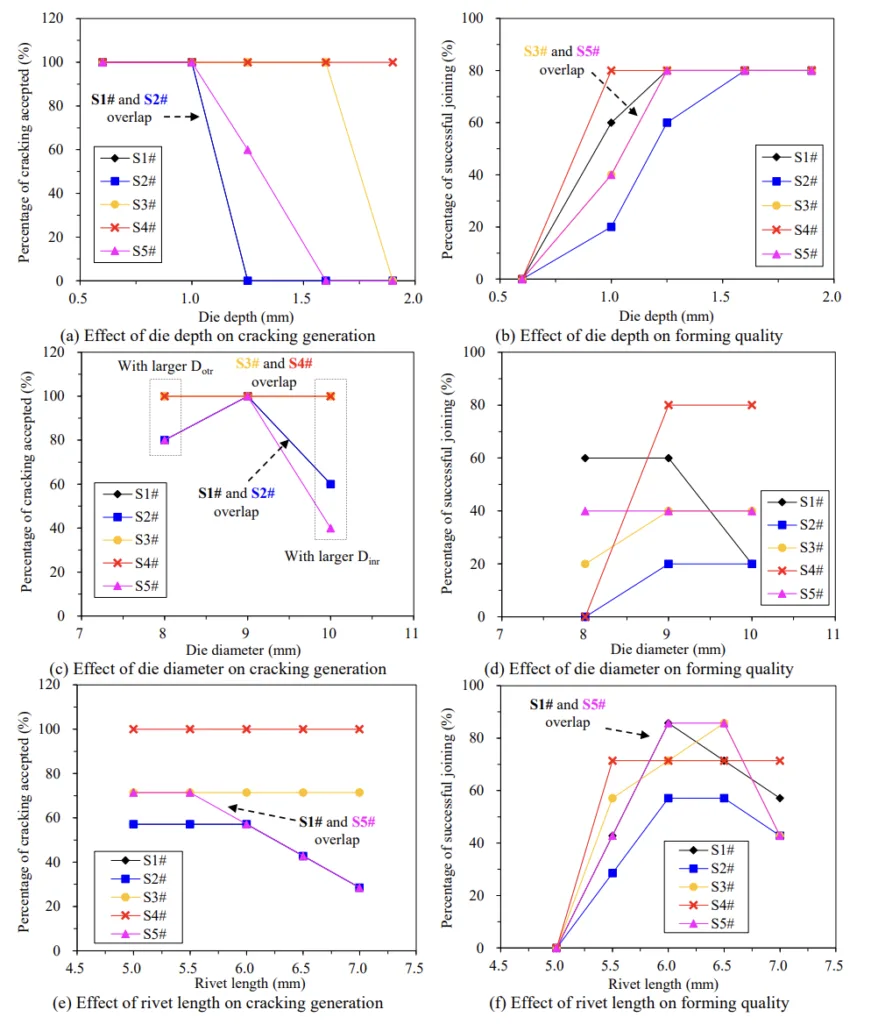
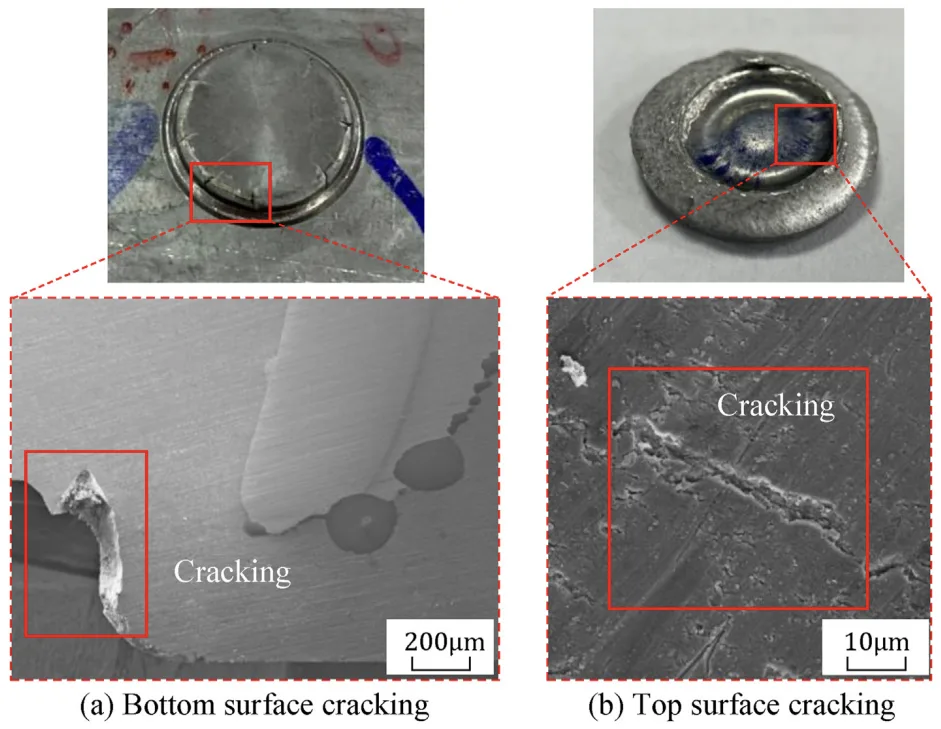
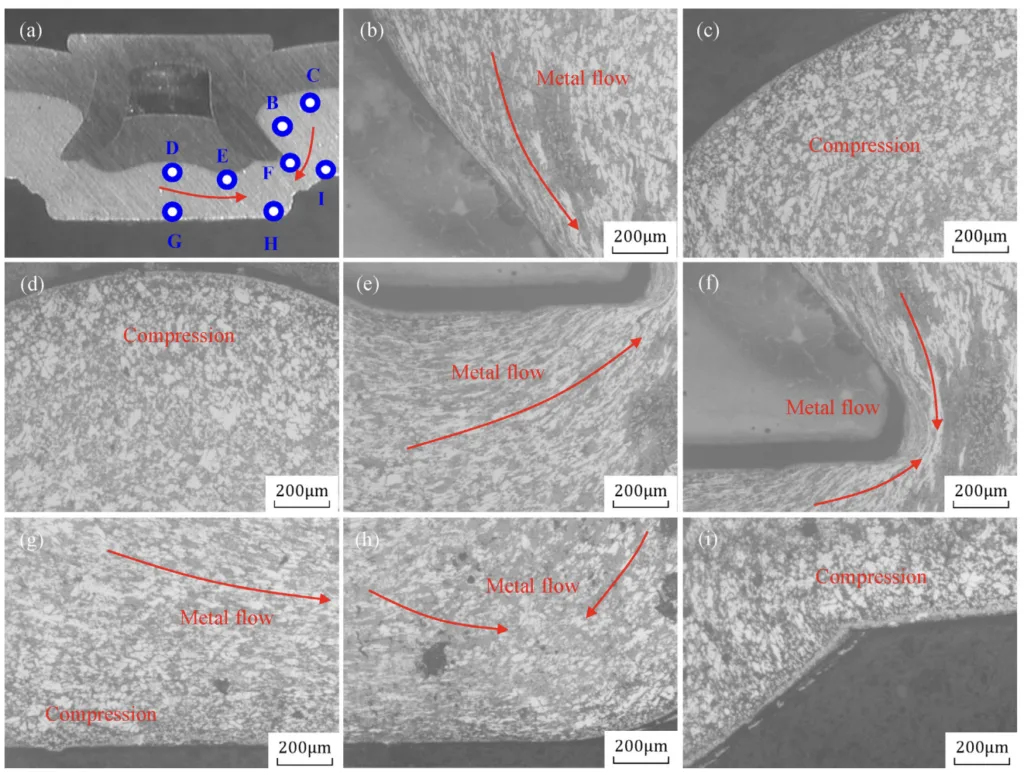
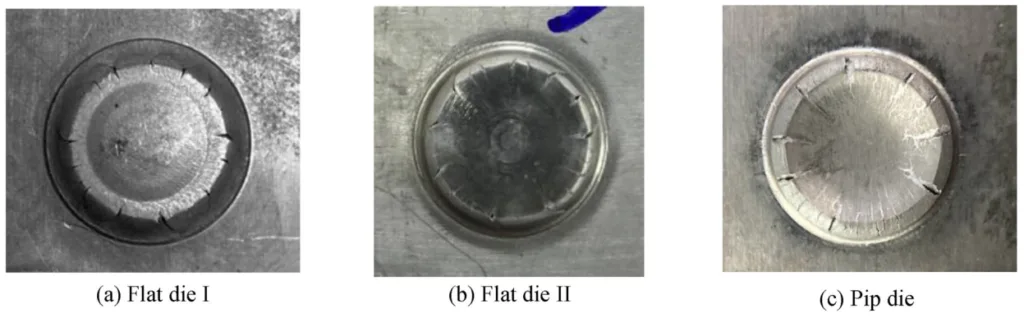
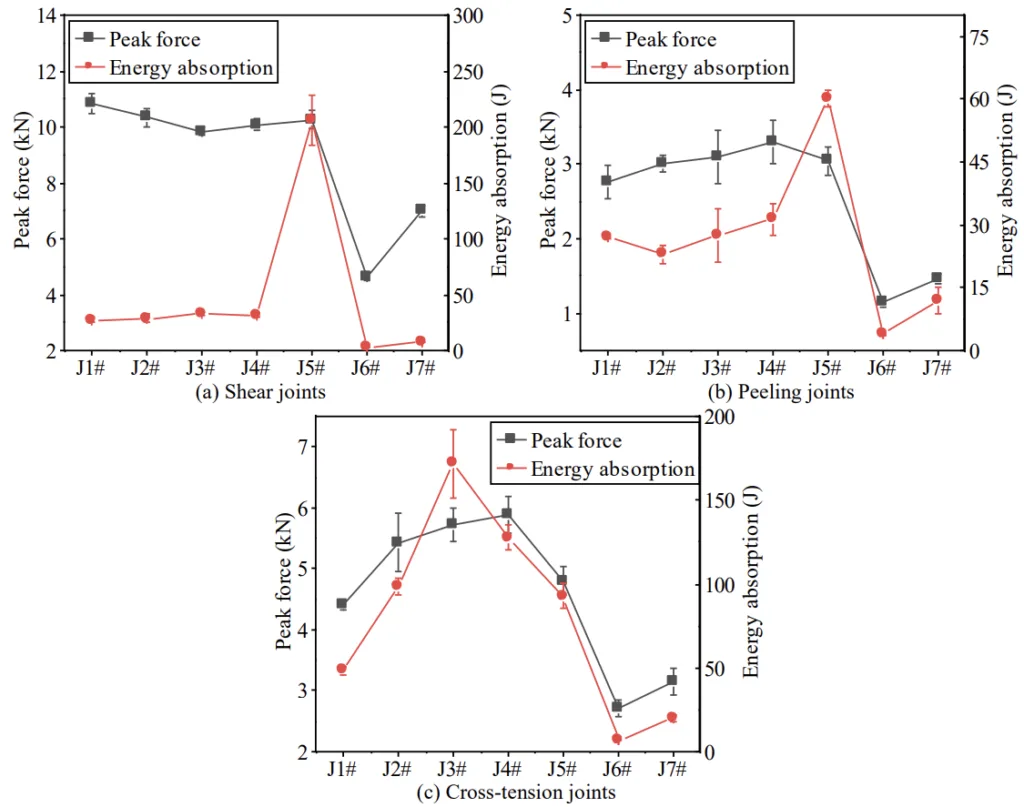
List of figure names:
- Fig. 1 Self-piercing riveting equipment.
- Fig. 2 Appearance and dimension parameters of the rivets and dies.
- Fig. 3 Schematic illustration of forming quality.
- Fig. 4 Schematic illustration of appearance quality.
- Fig. 5 Geometric dimensions of SPR joints and quasi-static test.
- Fig. 6 Joint quality with varied rivet and die combinations.
- Fig. 7 The central cross-sectional profile of SPR joints of S4#.
- Fig. 8 Joint quality with varied elongation and yield stress.
- Fig. 9 Effect of parameters of the rivet and die on joint quality.
- Fig. 10 Selection of dimensional parameters of the die: (a) depth and (b) diameter.
- Fig. 11 Characteristics of the two types of cracks on bottom sheet.
- Fig. 12 Three regions based on the degree of deformation.
- Fig. 13 Metallographic graphs of the cross-section of the SPR joint.
- Fig. 14 Cracking characteristics of three types dies.
- Fig. 15 Schematic illustration of bottom surface cracking: (a) piercing (b) flaring, and (c) danger zone and safety zone.
- Fig. 16 The cross-section profile, appearance quality, and forming quality of SPR joints (unit: mm).
- Fig. 17 Static failure modes for the SPR joints under quasi-static tests.
- Fig. 18 The failure mechanism and micromorphology of the joints: (a) shear joints, (b) peeling joints, (c) cross-tension joints, (d) macro fracture, (e) magnified view of joint J2#, and (f) magnified view of joint J4#.
- Fig. 19 Bottom sheet fracture of the cross-tension test: (a) macro fracture, (b) magnified area of joint J1#, (c) magnified area of joint J2#, and (d) magnified area of joint J5#.
- Fig. 20 The mechanical properties of SPR joints with different heat treatments and stack direction.
7. Conclusion:
Summary of key findings:
- SPR joinability is improved by larger elongation and lower yield strength achieved through heat treatment.
- Die depth and diameter are key factors influencing cracking and forming quality.
- Cracking is caused by tangential tensile stress on the bottom surface.
- Steel-aluminum joints have better mechanical properties than aluminum-steel joints.
- Heat treatment primarily affects energy absorption, not peak force.
- Tearing failure of the lower sheet is the main factor causing failure of steel-aluminium joint (steel is the top sheet).
The research provides a detailed understanding of the cracking mechanism in SPR of steel/die-casting aluminum joints.
It offers practical guidance for selecting appropriate process parameters and heat treatments to improve joinability and prevent cracking.
The findings contribute to the advancement of lightweight automotive manufacturing by enabling reliable joining of steel and die-casting aluminum.
8. References:
- [1] Duan LB, Xiao NC, Hu ZH, Li GY, Cheng AG. An efficient lightweight design strategy for body-in-white based on implicit parameterization technique. Struct Multidiscip O 2016;55:1927–43.
- [2] Niu ZC, Liu GY, Li T, Ji SX. Effect of high pressure die casting on the castability, defects and mechanical properties of aluminium alloys in extra-large thin-wall castings. J Mater Process Technol 2022;303:117525.
- [3] Lou M, Li YB, Wang Y, Wang B, Lai XM. Influence of resistance heating on self-piercing riveted dissimilar joints of AA6061-T6 and galvanized DP590. J Mater Process Technol 2014;214:2119–26.
- [4] Li DZ, Chrysanthou A, Patel I, Williams G. Self-piercing riveting-a review. Int J Adv Manuf Technol 2017;92:1777–824.
- [5] Sun X, Khaleel M. Performance optimization of self-piercing rivets through analytical rivet strength estimation. J Manuf Process 2005;7:83–93.
- [6] Zhao H, Han L, Liu YP, Liu XP. Quality prediction and rivet/die selection for SPR joints with artificial neural network and genetic algorithm. J Manuf Process 2021;66:574–94.
- [7] Wang DF, Kong DW, Xie C, Li SH, Zong L. Study on the effect of rivet die parameters on joint quality of self-piercing riveting employed 3D modeling and MCDM method. Int J Adv Manuf Technol 2022;119:8227–41.
- [8] Zhao H, Han L, Liu YP, Liu XP. Analysis of joint formation mechanisms for self-piercing riveting (SPR) process with varying joining parameters. J Manuf Process 2022;73:668–85.
- [9] Karathanasopoulos N, Pandya KS, Mohr D. An experimental and numerical investigation of the role of rivet and die design on the self-piercing riveting joint characteristics of aluminum and steel sheets. J Manuf Process 2021;69:290–302.
- [10] Liu YP, Li H, Zhao H, Liu XP. Effects of the die parameters on the self-piercing riveting process. Int J Adv Manuf Technol 2019;105:3353–68.
- [11] Du ZP, Duan LB, Jing LJ, Cheng AG, He ZC. Numerical simulation and parametric study on self-piercing riveting process of aluminium-steel hybrid sheets. Thin-Walled Struct 2021;164:107872.
- [12] Du ZP, Wei BL, He ZC, Cheng AG, Duan LB, Zhang G. Experimental and numerical investigations of aluminium- steel self-piercing riveted joints under quasi-static and dynamic loadings. Thin-Walled Struct 2021;169:108277.
- [13] Zhang XL, He XC, Xing BY, Wei WJ, Lu JW. Quasi-static and fatigue characteristics of self-piercing riveted joints in dissimilar aluminium-lithium alloy and titanium sheets. J Mater Res Technol 2020;9:5699–711.
- [14] Wang XY, Fang YD, Zhan ZF. A crack detection and evaluation method for self-piercing riveting. IMECE 2018;52170:V012T11A06.
- [15] Jäckel M, Grimm T, Niegsch R, Drossel W. Overview of current challenges in self-pierce riveting of lightweight materials. ICEM 2018;2:384–9.
- [16] Hu K, Jiang L, Zhan ZF, Wu F. Crack detection and evaluation method for self-piercing riveting button images based on BP neural network. IMECE 2021;85581:V004T04A21.
- [17] Ang HQ. An overview of self-piercing riveting process with focus on joint failures, corrosion issues and optimisation techniques. Chin J Mech Eng-En 2021;34:1–25.
- [18] Zhao XZ. Research on applying the self-pierce riveting (SPR) for die casting aluminum alloys. Purdue University; 2019. Dr.
- [19] Li DZ, Han L, Lu ZJ, Thornton M, Shergold M. Influence of die profiles and cracks on joint buttons on the joint quality and mechanical strengths of high strength aluminium alloy joint. Adv Mater Res 2012;548:398–405.
- [20] Jäckel M, Coppieters S, Hofmann M, Vandermeiren N, Landgrebe D. Mechanical joining of materials with limited ductility: analysis of process-induced defects. AIP Conf Proc 2017;1896:110009.
- [21] Neuser M, Kappe F, Busch M, Grydin O, Bobbert M. Joining suitability of cast aluminium for self-piercing riveting. IOP Conf Ser Mater Sci Eng 2021;1157:012005.
- [22] Neuser M, Kappe F, Ostermeier J, Krüger JT, Bobbert M. Mechanical properties and joinability of AlSi9 alloy manufactured by twin-roll casting. Adv Eng Mater 2022;24:2200874.
- [23] Liu YC, Wang G, Weiler J. Joining magnesium die casting using self-piercing riveting with a rivet receiver. SAE Techni Paper 2021:2021010275.
- [24] Drossel WG, Jaeckel M. New die concept for self-pierce riveting materials with limited ductility. Key Eng Mater 2014;611–612:1452–9.
- [25] Yang BX, Ma YW, Shan H, Niu SZ, Li YB. Friction self-piercing riveting (F-SPR) of aluminum alloy to magnesium alloy using a flat die. J Magnesium Alloys 2021;10:1207–19.
- [26] Li YB, Wei ZY, Wang ZZ, Li YT. Friction self-piercing riveting of aluminum alloy AA6061-T6 to magnesium alloy AZ31B. J Manuf Sci E-T Asme 2013;135:061007.
- [27] Ma YW, Yang BX, Hu SQ, Shan H, Geng Ph, Li YB, et al. Combined strengthening mechanism of solid-state bonding and mechanical interlocking in friction self-piercing riveted AA7075-T6 aluminum alloy joints. J Mater Sci Technol 2022;105:109–21.
- [28] Han SL, Li ZY, Wang ZY, Li Y. Review on joining processes of magnesium alloy sheets. Int J Adv Manuf Technol 2022;118:2787–803.
- [29] Ma YW, He GZ, Lou M, Li YB, Lin ZQ. Effects of process parameters on crack inhibition and mechanical interlocking in friction self-piercing riveting of aluminum alloy and magnesium alloy. J Manuf Sci E-T Asme 2018;140:101015.
- [30] Durandet Y, Deam R, Beer A, Song W, Blacket S. Laser assisted self-pierce riveting of AZ31 magnesium alloy strips. Mater Des 2010;31:S13–6.
- [31] Deng L, Lou M, Li YB, Carlson BE. Thermally assisted self- piercing riveting of aluminum AA6061-T6 to ultra-high strength steels. Inter Manuf Sci Eng Conf 2018;51364:V002T04A36.
- [32] Yang BX, Ma YW, Shan H, Li YB. A comparative study of self- piercing riveting and friction self-piercing riveting of cast aluminum alloy Al-Si7Mg. J Manuf Sci E 2023;145:0011003.
- [33] Klein T, Kirov G, Ucsnik S. Self-piercing riveting of medium- and high-strength Al and Mg alloy sheets enabled by in- process electric resistance heating. J Manuf Sci E-T Asme 2021;143:034502.
- [34] Deng L, Lou M, Li YB, Carlson BE. Thermally assisted self- piercing riveting of AA6061-T6 to ultrahigh strength steel. J Manuf Sci E-T Asme 2019;141:101006.
- [35] Mallick PK. Materials, design and manufacturing for lightweight vehicles. Woodhead publishing; 2020.
- [36] Zhao X, Meng D, Zhang JY, Han QY. The effect of heat treatment on die casting aluminum to apply self-pierce riveting. Int J Adv Manuf Technol 2020;109:2409–19.
- [37] Yarcu S, Huebner S, Yilkiran D, Brunotte K, Behrens BA, Schuchardt T, et al. Clinching of heated aluminum die casting. Congr Ger Acad Assoc Prod Tech 2021:85–93.
- [38] Haque R. Quality of self-piercing riveting (SPR) joints from cross-sectional perspective: a review. Arch Civ Mech Eng 2018;18:83–93.
- [39] Xie ZQ, Yan WM, Yu C, Mu TT, Song LL. Improved shear strength design of cold-formed steel connection with single self-piercing rivet. Thin-Walled Struct 2018;131:708–17.
- [40] Li DZ, Han L, Chrysanthou A, Shergold M, Williams G. The effect of setting velocity on the static and fatigue strengths of self-piercing riveted joints for automotive applications. TMS Annual Conference 2014:557–64.
- [41] Han L, Thornton M, Li DZ, Shergold M. Effect of setting velocity on self-piercing riveting process and joint behaviour for automotive applications. SAE Technical Paper 2010. 2010-01-0966.
- [42] Zhao H, Han L, Liu YP, Liu XP. Modelling and interaction analysis of the self-pierce riveting process using regression analysis and FEA. Int J Adv Manuf Technol 2021;113:159–76.
- [43] Ma YW, Lou M, Li YB, Lin ZQ. Effect of rivet and die on self- piercing rivetability of AA6061-T6 and mild steel CR4 of different gauges. J Mater Process Technol 2018;251:282–94.
- [44] Kajtoch J. Strain in the upsetting process. Metall Foundry Eng 2007;33:51–61.
- [45] Sahin M, Cetinarslan CS, Akata HE. Effect of surface roughness on friction coefficients during upsetting processes for different materials. Mater Des 2007;28:633–40.
- [46] Lin SY. An investigation of die-workpiece interface friction during the upsetting process. J Mater Process Technol 1995;54:239–48.
- [47] Lin YC, Chen MS. Numerical simulation and experimental verification of microstructure evolution in a three- dimensional hot upsetting process. J Mater Process Technol 2009;209:4578–83.
- [48] Lin YC, Chen MS, Zhong J. Numerical simulation for stress/ strain distribution and microstructural evolution in 42CrMo steel during hot upsetting process. Comput Mater Sci 2008;43:1117–22.
- [49] Kim C, Min KM, Choi H, Kim HJ, Lee MG. Development of analytical strength estimator for self-piercing rivet joints through observation of finite element simulations. Int J Mech Sci 2021;202:106499.
- [50] Huang ZC, Zhou ZJ, Jiang YQ. Effect of shot peening on static and fatigue properties of self-piercing riveting joints. J Mater Res Technol 2022;18:1070–80.
9. Copyright:
- This material is a paper by "Chao Wang, Zhanpeng Du, Aiguo Cheng, Zhicheng He, Hailun Tan, Wanyuan Yu": Based on "Influence of process parameters and heat treatment on self-piercing riveting of high-strength steel and die-casting aluminium".
- Source of paper: https://doi.org/10.1016/j.jmrt.2023.09.187
This material was created to introduce the above paper, and unauthorized use for commercial purposes is prohibited. Copyright © 2025 CASTMAN. All rights reserved.