This introduction paper is based on the paper "Improving the Mechanical Properties of Salt Core through Reinforcing Fibers" published by "Journal of Sensor Science and Technology".
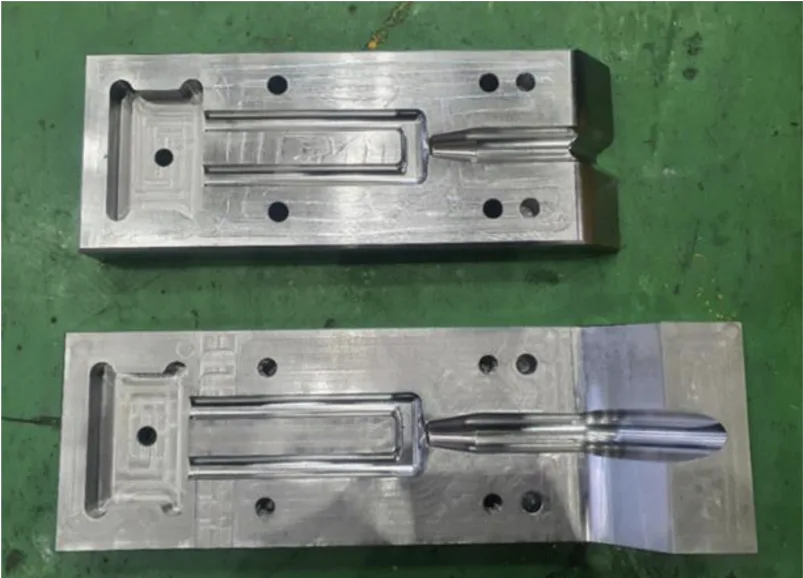
1. Overview:
- Title: Improving the Mechanical Properties of Salt Core through Reinforcing Fibers
- Author: Ahrom Ryu, Soyeon Yoo, Min-Seok Jeon, Dongkyun Kim, Kiwon Hong, Sahn Nahm, and Ji-Won Choi
- Year of publication: 2023
- Journal/academic society of publication: Journal of Sensor Science and Technology (Vol. 32, No. 3, pp. 159-163)
- Keywords: Salt core, Reinforcing fiber, Bending strength, Eco-friendly, High-pressure die casting
2. Abstract:
Salt cores have attracted considerable attention for their application to the casting process of electric vehicle parts as a solution to ecological issues. However, the salt core still has low mechanical strength for use in high-pressure die casting. In this study, we investigated the improvements in the bending strength of KCl-based salt cores resulting from the use of reinforcing materials. KCl and Na2CO3 powders were used as matrix materials, and glass fiber and carbon fiber were used as reinforcing materials. The effects of carbon fiber and glass fiber contents on the bending strength properties were investigated. Here, we obtained a new fiber-reinforced salt core composition with improved bending strength for high-pressure die casting by adding a relatively small amount of glass fiber (0.3 wt%). The reinforced salt core indicates the improved properties, including a bending strength of 49.3 Mpa, linear shrinkage of 1.5%, water solubility rate of 16.25 g/min.m² in distilled water, and hygroscopic rate of 0.058%.
3. Introduction:
Aluminum high-pressure die-casting (HPDC) alloys are widely used in electronics and automotive industries due to their high strength, stiffness, good formability, favorable weight ratio, and corrosion resistance. For manufacturing parts with complex internal geometries and high-quality requirements, salt-core-based casting processes have been proposed as an alternative to traditional sand casting. This process uses a salt material as a temporary core that can be easily dissolved after metal solidification, allowing for precise creation of complex internal features and better surface finish. Salt cores offer advantages like high strength, dimensional accuracy, casting removability, humidity resistance, and recyclability. However, challenges remain for mass production, including the inherent low strength of salt core materials, vulnerability to humidity, deformation during solidification, and difficulty in core extraction. Conventional salt cores are composed of inorganic salts (e.g., KCl, NaCl, CaCO3, Na2CO3, Na2SO4), which are brittle, do not provide reinforcement, and are prone to shrinkage and cracking, leading to reduced strength. Therefore, enhancing the mechanical strength of salt cores is essential.
4. Summary of the study:
Background of the research topic:
Salt cores are increasingly important in HPDC for creating complex internal geometries in cast parts, particularly for automotive applications. However, their inherent low mechanical strength poses a significant limitation for their use, especially under the high pressures of die casting. Traditional salt materials are brittle and susceptible to cracking.
Status of previous research:
Previous efforts to improve salt core strength included optimizing manufacturing processes to enhance filling density and uniformity, and using simulations to understand core properties. Various reinforcing materials like aluminum borate whiskers, alumina powder, and silica powder have been explored, but these often result in limited strength improvements or adversely affect the liquidity of the molten salt. Reinforcing fibers, such as glass fibers, have shown promise in ceramic matrix composites and have been studied for KNO3-based salt cores, demonstrating improved bending strength and reduced hygroscopic rates. However, high fiber content can lead to decreased liquidity and casting defects.
Purpose of the study:
This study aimed to improve the mechanical properties, particularly the bending strength, of KCl-based salt cores by incorporating inexpensive glass fibers and carbon fibers as reinforcing materials. The research investigated the effects of varying fiber content on bending strength, linear shrinkage, water solubility, and hygroscopic rate. Furthermore, the study sought to analyze the morphology and crack microstructures of the reinforced salt cores using scanning electron microscopy (SEM) to understand the strengthening mechanisms and to identify an optimized composition, particularly focusing on achieving significant strength improvement with ultra-low (0.3 wt%) glass fiber content.
Core study:
The core of this study involved the fabrication of KCl-based salt cores (matrix: KCl-60 mol%Na2CO3 with MgCl2) reinforced with different amounts of glass fibers or carbon fibers (ranging from 0.1 wt% to 0.7 wt%). These fabricated salt cores were then subjected to a series of tests to evaluate their mechanical and physical properties. Specifically, bending strength, linear shrinkage rate, water solubility rate, and hygroscopic rate were measured. The microstructure of the fractured surfaces of the salt cores, particularly the unreinforced and the 0.3 wt% glass fiber reinforced samples, was analyzed using SEM to observe the effects of fiber reinforcement.
5. Research Methodology
Research Design:
The study employed an experimental research design. It involved the systematic preparation of salt core samples with varying compositions of reinforcing fibers (glass and carbon) and subsequent characterization of their mechanical and physical properties to determine the effects of these reinforcements.
Data Collection and Analysis Methods:
- Raw Materials: Potassium chloride (KCl, 99% purity) and sodium carbonate (Na2CO3, 99% purity) were used as matrix materials. MgCl2 was also part of the matrix. Glass fibers (average particle size 20 µm, diameter 3 µm) and carbon fibers (average particle size 100 µm, diameter 7.2 µm) were used as reinforcing materials.
- Fabrication: A mixture of KCl, Na2CO3, MgCl2 (molar ratio 30:60:10 respectively), and reinforcing fibers (0.1 wt% to 0.7 wt%) was dried, melted in an alumina crucible at 750 °C, stirred for 10 minutes, and then poured into a preheated (220 °C) SKD61 steel mold. After cooling for 55 seconds, the salt core was removed and cooled to room temperature.
- Bending Strength: Assessed using a three-point bending method on a universal testing machine (DUT-3000CM) with a constant pressure head speed of 2 mm/min and a load of 980 N.
- Linear Shrinkage Rate (L): Calculated using the formula
L = (l1-l2)/l1 × 100%
, where l1 is the designed length (12 mm) and l2 is the actual length of the sample. - Water Solubility Rate (K): Determined by immersing cylindrical salt cores in 23±2 °C distilled water and calculated using
K = m / (sxt)
, where m is mass, s is total surface area, and t is dissolution time. - Hygroscopic Rate (φ): Calculated using
φ = (m1-m0)/m0 × 100%
, where m0 is the original mass and m1 is the mass after 1 day exposure to 60% relative humidity in a humidity and temperature controller. - Microstructure Analysis: Observed using a scanning electron microscope (SEM, Inspect 50, FEI, USA) on platinum-sputtered fractured surfaces of the salt cores.
Research Topics and Scope:
The research focused on:
- Investigating the effect of varying concentrations (0.1 wt% to 0.7 wt%) of glass fibers and carbon fibers on the bending strength of KCl-based salt cores.
- Evaluating other critical properties of glass fiber reinforced salt cores, including linear shrinkage, water solubility rate, and hygroscopic rate.
- Analyzing the microstructure of unreinforced and glass fiber reinforced salt cores to understand the reinforcement mechanisms.
- Optimizing the glass fiber content to achieve improved mechanical properties, specifically targeting a low concentration (0.3 wt%).
6. Key Results:
Key Results:
- The addition of both glass fibers and carbon fibers significantly increased the bending strength of the KCl-based salt cores compared to unreinforced cores (which had a bending strength of 22 MPa).
- A maximum bending strength of 49.3 MPa was achieved with the addition of 0.3 wt% glass fiber.
- For the salt core reinforced with 0.3 wt% glass fiber, the following properties were observed:
- Linear shrinkage: 1.5%
- Water solubility rate: 16.25 g/min·m² in distilled water
- Hygroscopic rate: 0.058%
- The linear shrinkage rate of the salt cores tended to increase with increasing glass fiber content, ranging from 1.03% for unreinforced cores to 4.08% for cores with 0.7 wt% glass fiber.
- The hygroscopic rate also increased with glass fiber content, from 0.036% for unreinforced cores to 0.122% for cores with 0.7 wt% glass fiber. However, for glass fiber content up to 0.3 wt%, the hygroscopic rate remained below 0.1%.
- The addition of glass fibers generally increased the dissolution time (reduced water solubility rate). Samples containing 0.7 wt% glass fiber showed the lowest water solubility. The KCl-based salt core reinforced with 0.3 wt% glass fiber completely dissolved in room-temperature water after 6 hours, demonstrating good water solubility for practical applications.
- SEM analysis revealed that unreinforced salt cores exhibited a relatively loose intergranular adhesion and small micro-holes. In contrast, the salt core reinforced with 0.3 wt% glass fiber showed a more compact microstructure. The glass fibers were well embedded in the salt matrix, which can impede crack propagation. Additionally, these fibers can act as foreign crystal nuclei, leading to an increased nucleation rate of grains and hindering columnar crystal growth, thereby contributing to higher strength.
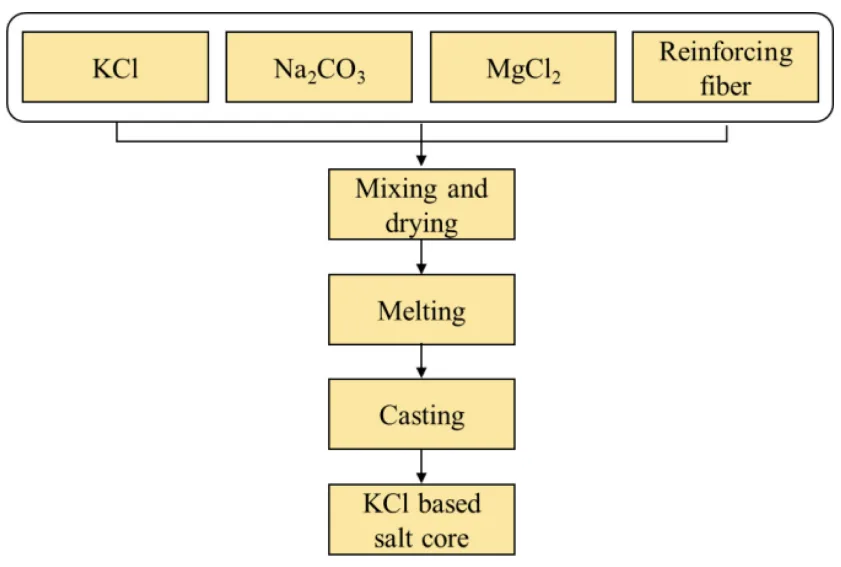

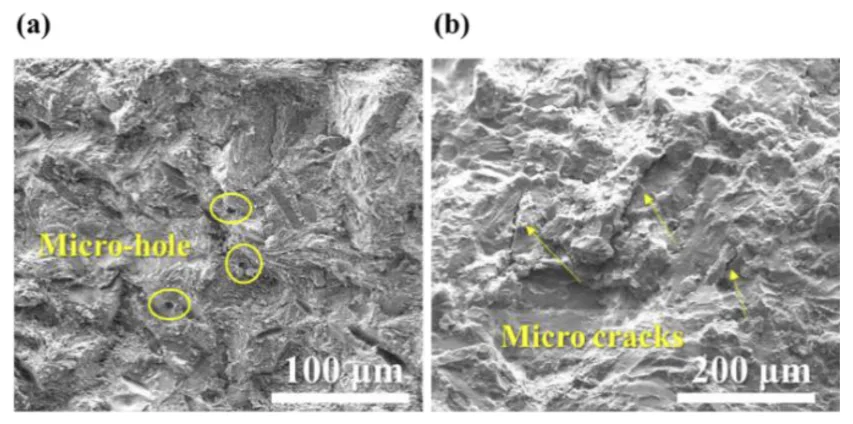
Figure Name List:
- Fig. 1. SEM morphologies of the (a) glass fibers and (b) carbon fibers.
- Fig. 2. Preparation process of KCl-based salt core.
- Fig. 3. SKD61 steel salt core mold.
- Fig. 4. Effect of the content of reinforcing fibers on the bending strength of KCl-based salt cores.
- Fig. 5. Water soluble experiments of the KCl-based salt core reinforced by 0.3 wt% glass fiber in room temperature: (a) 0 h, (b) 2 h, (c) 4 h, (d) 6 h.
- Fig. 6. SEM micrographs of the fractured salt core: (a) unreinforced, (b) with 0.3 wt% glass fiber
7. Conclusion:
This study successfully demonstrated that the mechanical properties of KCl-based salt cores can be significantly improved by incorporating reinforcing fibers. Both glass and carbon fibers were effective in enhancing bending strength by inhibiting crack propagation. Notably, the addition of a very small amount (0.3 wt%) of glass fiber resulted in a substantial increase in bending strength, achieving values up to 49 MPa (from an initial 22 MPa for unreinforced cores). The investigation of the fractured surface microstructure confirmed the reinforcing effect. Furthermore, key properties such as water solubility rate, hygroscopic rate, and shrinkage of the glass fiber reinforced KCl-based salt core were characterized, providing valuable data for their application in high-pressure die casting. The enhanced bending strength makes these reinforced salt cores more suitable for demanding casting processes.
8. References:
- [1] J. Bedmar, B. Torres, and J. Rams, "Manufacturing of Aluminum Matrix Composites Reinforced with Carbon Fiber Fabrics by High Pressure Die Casting, Mater., Vol. 15, No. 9, pp. 3400(1)-3400(18), 2022.
- [2] S. O. Akinwamide, O. J. Akinribide, and P. A. Olubambi, "Microstructural evolution, mechanical and nanoindentation studies of stir cast binary and ternary aluminium based composites, J. Alloys Compd., Vol. 850, pp. 156586(1)-156586(3), 2021.
- [3] S. O. Akinwamide, B. T. Abe, O. J. Akinribide, B. A. Obadele, and P. A. Olubambi, "Characterization of microstructure, mechanical properties and corrosion response of aluminium-based composites fabricated via casting-a review,J. Adv. Manuf. Technol., Vol. 109, pp. 975-991, 2020.
- [4] J. Weise, J. Hilbers, F. Handels, D. Lehmhus, M. Busse, and M. Heuser, "New Core Technology for Light Metal Casting, Adv. Eng. Mater., Vol. 21, No. 4, p. 1800608, 2019.
- [5] M. Gromada, A. Świeca, M. Kostecki, A. Olszyna, and R. Cygan, "Ceramic cores for turbine blades via injection moulding, J. Mater. Process Technol., Vol. 220, pp. 107-112, 2015.
- [6] H. Khandelwal and B. Ravi, "Effect of Binder Composition on the Shrinkage of Chemically Bonded Sand Cores, Mater. Manuf. Process., Vol. 30, No. 12, pp. 1465-1470, 2015.
- [7] P. Jelinek, E. Adamkov, F. Miksovsky, and J. Beno, "Advances in Technology of Soluble cores for Die Castings, Arch. Foundry Eng., Vol. 15, pp. 29-34, 2015.
- [8] P. P. Zhou, G. Q. Wu, Y. Tao, X. Cheng, J. Q. Zhao, and H. Nan, "Optimization of the injection molding process for development of high performance calcium oxide -based ceramic cores, Mater. Res. Express, Vol. 5, No. 2, p. 025208, 2018.
- [9] R. Huang and B. Zhang, "Study on the Composition and Properties of Salt Cores for Zinc Alloy Die Casting, Int. J. Metalcasting, Vol. 11, pp. 440-447, 2017.
- [10] M. Lagler, “Use of Simulation to predict the Viabilirt of Salt Cores in the HPDC Process-Shot Curve as a Decisive Criterion, Die Casitng Eng., Vol. 57, No. 4, pp. 16-17, 2013.
- [11] B. Fuchs, H. Eibisch, and C. Körner, "Core Viability Simulation for Salt Core Technology in High-Pressure Die Casting, Int. J. Metalcasting, Vol. 7, pp. 39-45, 2013.
- [12] J. Yaokawa, K. Anzai, Y. Yamada, H. Yoshii, and H. Fukui, "Castability and Strength of Potassium Chloride-Ceramic Composite Salt Cores, J. Japan Foundry Eng., Vol. 76, No. 10, pp. 823-829, 2004.
- [13] J. Beòo, E. Adámkov, F. Mikovsk, and P. Jelínek, "Development of composite salt cores for foundry applications, Mater. Technol., Vol. 49, No. 4, pp. 619-623, 2015.
- [14] J. Yaokawa, D. Miura, K. Anzai, Y. Yamada, and H. Yoshii, "Strength of Salt Core Composed of Alkali Carbonate and Alkali Chloride Mixtures Made by Casting Technique, Mater. Trans., Vol. 48, No. 5, pp. 1034-1041, 2007.
- [15] F. Liu, S. Tu, X. Gong, G. Li, W. Jiang, X. Liu, and Z. Fan, "Comparative study on performance and microstructure of composite water-soluble salt core material for manufacturing hollow zinc alloy castings, Mater. Chem. Phys., Vol. 252, p.123257, 2020.
- [16] X. Gong, W. Jiang, F. Liu, Z. Yang, F. Guan, and Z. Fan, "Effects of glass fiber size and content on microstructures and properties of KNO3-based water-soluble salt core for high pressure die casting, Int. J. Metalcasting, Vol. 15, pp. 520-529, 2021.
- [17] S. Tu, F. Liu, G. Li, W. Jiang, X. Liu, and Z. Fan, “Fabrication and characterization of high-strength water-soluble composite salt core for zinc alloy die castings, Int. J. Adv. Manuf. Tech, Vol. 95, pp. 505-512, 2018.
9. Copyright:
- This material is a paper by "Ahrom Ryu, Soyeon Yoo, Min-Seok Jeon, Dongkyun Kim, Kiwon Hong, Sahn Nahm, and Ji-Won Choi". Based on "Improving the Mechanical Properties of Salt Core through Reinforcing Fibers".
- Source of the paper: http://dx.doi.org/10.46670/JSST.2023.32.3.159
This material is summarized based on the above paper, and unauthorized use for commercial purposes is prohibited.
Copyright © 2025 CASTMAN. All rights reserved.