This article introduces the paper "Improving Quality in Mega-Casted Products: Identification of contributors to geometrical variation".
1. Overview:
- Title: Improving Quality in Mega-Casted Products: Identification of contributors to geometrical variation
- Authors: Paul Adam, David Hermez
- Year of Publication: 2024
- Journal/Conference: Chalmers University of Technology, Master's thesis in Production Engineering
- Keywords: HPDC, Megacasting, Geometrical variation, Distortions
2. Research Background:
The increasing global demand for environmentally friendly automotive manufacturing necessitates lightweighting techniques to address the weight increase associated with electric vehicle (EV) batteries. Volvo Cars is investing in large-scale casting (Mega-casting) using High-Pressure Die Casting (HPDC) to simplify assembly, improve efficiency, and enhance product quality. However, mega-casting presents challenges related to geometrical variation. While existing research focuses on minor defects like surface imperfections or porosity, this study concentrates on larger defects impacting dimensional accuracy.
3. Research Objectives and Questions:
- Research Objective: To identify the contributors to geometrical variation in the HPDC process, specifically within mega-casting, and propose solutions for improved product quality.
- Key Research Questions:
- What factors contribute to geometrical variation in mega-casted products/parts?
- What are the most critical contributing factors?
- Research Hypothesis: The hypothesis was that design is the root cause of geometrical variation, with variations in thickness leading to residual stresses that affect the accuracy of the final shape.
4. Research Methodology:
- Research Design: A mixed-methods approach combining qualitative and quantitative research methods was employed.
- Data Collection Methods: A literature review was conducted. Eleven professionals in the HPDC field were interviewed. Production tests were performed at a foundry.
- Analysis Methods: Qualitative analysis of expert interviews utilized Affinity Mapping. Quantitative analysis included correlation studies of measurement and process data, and analysis of Volvo Mega-casting production data to assess geometrical variation.
- Subjects and Scope: The study focused on the HPDC process, particularly mega-casting, excluding surface defects, porosity, and machining.
5. Main Research Findings:
- Key Findings: Design, particularly variations in wall thickness inducing residual stresses, was identified as the primary cause of geometrical variation. A method was found to successfully reduce geometrical variation in some instances; however, this led to secondary issues such as sticking to the trim-press. A Design of Experiments (DoE) was suggested for future studies to systematically optimize influential parameters.
- Statistical/Qualitative Analysis Results: Expert interviews and data analysis revealed that gating system, die design, die temperature, melt temperature, alloy composition, vacuum-assisted casting, soldering during ejection, quenching (including media, rate, and orientation), and trimming all impact geometrical variation. The influence of vacuum-assisted casting on geometrical variation remained inconclusive.
- Data Interpretation: Analysis of Volvo Mega-casting data highlighted specific areas with significant geometrical variation.
- Figure List and Description: Numerous figures and tables visually presented simulation results, expert insights, and data analysis results.
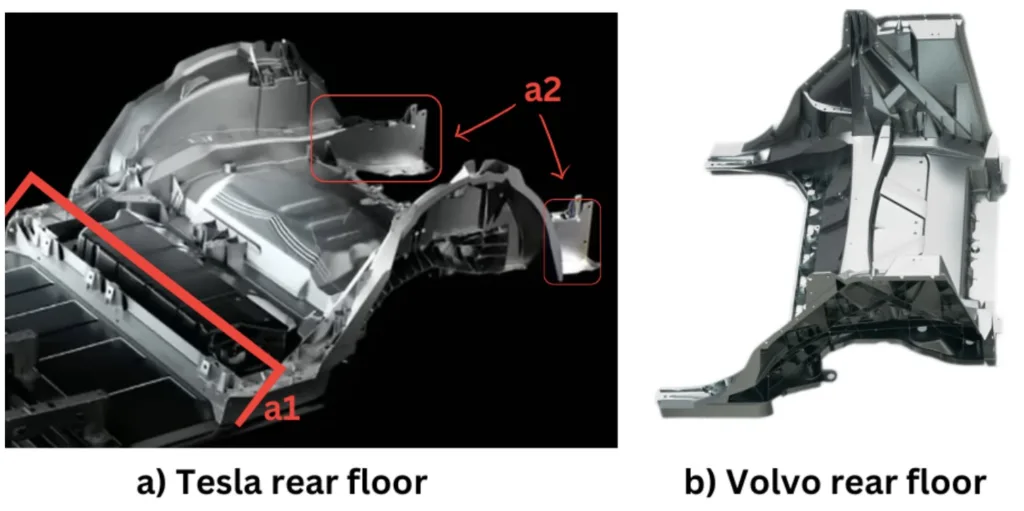
6. Conclusion and Discussion:
- Summary of Key Findings: Design flaws, especially thickness variations leading to residual stresses, were the root cause of geometrical variation. Various process parameters interact in complex ways to influence this variation.
- Academic Significance: The study provides novel insights and knowledge for improving the quality of mega-castings.
- Practical Implications: The findings underscore the need for design optimization considering geometrical variation from the outset, emphasizing the importance of optimizing the quenching process and improving the trimming process.
- Limitations: The study's scope was limited by time constraints and resource limitations. Simulation analysis was partially hindered, and in-depth statistical analysis was restricted. Human factors and post-casting processes were excluded.
7. Future Research:
- Future Research Directions: A Design of Experiments (DoE) should be conducted to identify optimal combinations of process parameters to minimize geometrical variation. Further simulation studies are needed to analyze the influence of design and process parameters on geometrical variation.
- Areas Requiring Further Exploration: Research should focus on the trimming process, the impact of human factors, and the integration with subsequent processes.
8. References Summary:
- [1] V. C. S. AB, (Accessed on 01/25/2024), n.d.
[Online]. Available: %7Bhttps: //www.media.volvocars.com/se/sv-se/media/pressreleases/294589/ photos%7D. - [2] K. Wärmefjord, J. Hansen, and R. Söderberg, “Challenges in geometry assurance of megacasting in the automotive industry”, Journal of Computing and Information Science in Engineering, 2023.
- [3] D. Carlisle, Mega-casting trends for automotive manufacturers | ducker carlisle, (Accessed on 01/25/2024), n.d.
[Online]. Available: %7Bhttps://www.duckercarlisle. com/mega-casting-trends-for-automotive-manufacturers/%7D. - [4] R. Stumpf. “Why volvo will start ‘mega-casting’ its new electric vehicles”. (2022),
[Online]. Available: https://www.popsci.com/technology/volvoto-start-mega-casting/. (accessed: 25.01.2024). - [5] K. Wärmefjord, R. Söderberg, A. Dagman, and L. Lindkvist, “Geometrical variation mode effect analysis (gvmea) for split lines”, Procedia CIRP, vol. 92, pp. 94–99, 2020, 16th CIRP Conference on Computer Aided Tolerancing (CIRP CAT 2020), issn: 2212-8271. doi: https://doi.org/10.1016/ j.procir.2020.05.165.
[Online]. Available: https://www.sciencedirect. com/science/article/pii/S2212827120309264. - [6] B. Schleich, K. Wärmefjord, R. Söderberg, and S. Wartzack, “Geometrical variations management 4.0: Towards next generation geometry assurance”, Procedia CIRP, vol. 75, pp. 3–10, 2018, The 15th CIRP Conference on Computer Aided Tolerancing, CIRP CAT 2018, 11-13 June 2018, Milan, Italy, issn: 2212-8271. doi: https://doi.org/10.1016/j.procir.2018.04.078.
[Online]. Available: https://www.sciencedirect.com/science/article/ pii/S2212827118305948. - [7] G. K. Sigworth and R. J. Donahue, “The metallurgy of aluminum alloys for structural high-pressure die castings”, International Journal of Metalcasting, vol. 15, no. 3, pp. 1031–1046, 2021.
- [8] F. Bonollo, N. Gramegna, and G. Timelli, “High-pressure die-casting: Contradictions and challenges”, JOM: the journal of the Minerals, Metals Materials Society, 2015-05. doi: 10.1007/s11837-015-1333-8.
- [9] F. Casarotto, A. Franke, and R. Franke, “6 - high-pressure die-cast (hpdc) aluminium alloys for automotive applications”, in Advanced Materials in Automotive Engineering, J. Rowe, Ed., Woodhead Publishing, 2012, pp. 109–149, isbn: 978-1-84569-561-3. doi: https://doi.org/10.1533/9780857095466.109.
[Online]. Available: https://www.sciencedirect.com/science/article/ pii/B9781845695613500065. - [10] M. Tiryakio¯glu and G. Totten, “Quenching aluminum components in water: Problems and alternatives”, ASM Proceedings: Heat Treating, pp. 156–165, 1998-01.
- [11] F. Peti, G. Lucian, S. Ioan, and C. Cristian, “Studies concerning the design of the runner, gate and venting systems in the case of the high pressure die casting technology”, ANNALS OF THE ORADEA UNIVERSITY. Fascicle of Management and Technological Engineering., vol. XIX (IX), 2010/2, 2010-09. doi: 10.15660/AUOFMTE.2010-2.1926.
- [12] M. Iqbal, “Gating design criteria for sound casting”, 2014.
[Online]. Available: https://api.semanticscholar.org/CorpusID:195176629. - [13] M. E. Mehtedi, T. Mancia, P. Buonadonna, L. Guzzini, E. Santini, and A. Forcellese, “Design optimization of gate system on high pressure die casting of alsi13fe alloy by means of finite element simulations”, Procedia CIRP, vol. 88, pp. 509–514, 2020, 13th CIRP Conference on Intelligent Computation in Manufacturing Engineering, 17-19 July 2019, Gulf of Naples, Italy, issn: 2212-8271. doi: https://doi.org/10.1016/j.procir.2020.05.088.
[Online]. Available: https://www.sciencedirect.com/science/article/pii/ S2212827120304108. - [14] R. Svenningsson and H. Svensson, “Residual stresses in high pressure die castings”, RISE, SWECAST, Tech. Rep. 2013-004, 2013, p. 39.
- [15] “Residual stress analysis applied to hpdc aluminium components: A case study”, La metallurgia italiana : rivista mensile della Associazione fra gli industriali metallurgici italiani, vol. 11-12, no. 113, 2021, issn: 0026-0843.
- [16] P. Hofer, E. Kaschnitz, and P. Schumacher, “Distortion and residual stress in high-pressure die castings: Simulation and measurements”, JOM, vol. 66, pp. 1638–1646, 2014-09. doi: 10.1007/s11837-014-1118-5.
- [17] J. Campbell, “Chapter 10 - the 10 rules for good castings”, in Complete Casting Handbook (Second Edition), J. Campbell, Ed., Second Edition, Boston: Butterworth-Heinemann, 2015, pp. 535–638, isbn: 978-0-444-63509-9. doi: https : / / doi . org / 10 . 1016 / B978 - 0 - 444 - 63509 - 9 . 00010 - 8.
[Online]. Available: https : / / www . sciencedirect . com / science / article / pii / B9780444635099000108. - [18] CFD Investigation of Quench Media and Orientation Effects on Structural Stress Induced in the Intense Quenching Processes for Aluminum Cylinder Heads, vol. Heat Treat 2017: Proceedings from the 29th Heat Treating Society Conference and Exposition, Heat Treating Conference Proceedings, 2017-10, pp. 411–421. doi: 10 . 31399 / asm . cp . ht2017p0411. eprint: https : / / dl . asminternational.org/heat-treating/proceedings-pdf/HT2017/84130/ 411/669057/ht2017p0411.pdf.
[Online]. Available: https://doi.org/10. 31399/asm.cp.ht2017p0411. - [19] Y. Wang and C. Lee, “Design and optimization of conformal cooling channels for increasing cooling efficiency in injection molding”, Applied Sciences, vol. 13, p. 7437, 2023-06. doi: 10.3390/app13137437.
- [20] T. Kim, K. Jin, N. Kim, and B. Kim, Numerical analysis and optimal design to reduce residual stresses and deformations of die casting baseplate after ejection - journal of mechanical science and technology, 2015-07.
[Online]. Available: https : / / link . springer . com / article / 10 . 1007 / s12206 - 015 - 0625 - 9#citeas. - [21] H. Dini, N.-E. Andersson, and A. Jarfors, “Effect of process parameters on distortion and residual stress of high-pressure die-cast az91d components”, International Journal of Metalcasting, vol. 12, 2017-11. doi: 10.1007/s40962- 017-0186-z.
- [22] G. Campatelli and A. Scippa, “A heuristic approach to meet geometric tolerance in high pressure die casting”, Simulation Modelling Practice and Theory, vol. 22, pp. 109–122, 2012, issn: 1569-190X. doi: https://doi.org/10.1016/ j.simpat.2011.11.003.
[Online]. Available: https://www.sciencedirect. com/science/article/pii/S1569190X11001808. - [23] C. El, A. Bouayad, and M. Alami, “The effect of mold and pouring temperature on hardness and microstructure of a hpdc hyper- eutectic aluminum alloy”, International Journal of Engineering research and technology, vol. Volume 4, pp 1162–1165, 2015-03.
- [24] Z. Niu, G. Liu, T. Li, and S. Ji, “Effect of high pressure die casting on the castability, defects and mechanical properties of aluminium alloys in extralarge thin-wall castings”, Journal of Materials Processing Technology, vol. 303, p. 117 525, 2022, issn: 0924-0136. doi: https : / / doi . org / 10 . 1016 / j . jmatprotec.2022.117525.
[Online]. Available: https://www.sciencedirect. com/science/article/pii/S0924013622000371. - [25] X. Dong, X. Zhu, and S. Ji, “Effect of super vacuum assisted high pressure die casting on the repeatability of mechanical properties of al-si-mg-mn die-cast alloys”, Journal of Materials Processing Technology, vol. 266, pp. 105–113, 2019.
- [26] O. Köser, J. Rückert, and P. Ubl, Part ejection in magnesium high pressure die casting, 2021.
- [27] S. Ueda, S. Sannakanishi, H. Shiga, M. K. Faiz, and M. Yoshida, “Evaluation of ejection force for die castings by fem thermal stress analysis with elastoplastic-creep model”, Materials Transactions, vol. 63, no. 2, pp. 217–223, 2022.
- [28] A. Monroe and P. Sanders, “The need for a new approach to soldering in high pressure die casting”, International Journal of Metalcasting, vol. 15, no. 2, pp. 391–397, 2021.
- [29] Z. Chen, “Formation and progression of die soldering during high pressure die casting”, Materials Science and Engineering: A, vol. 397, no. 1-2, pp. 356–369, 2005.
- [30] M. M. Makhlouf and D. Apelian, “Casting characteristics of aluminum die casting alloys”, 2002-02. doi: 10.2172/792701.
[Online]. Available: https: //www.osti.gov/biblio/792701. - [31] B. Zabala, C. Raone, A. Igartua, et al., “Evaluation hpdc lubricant spraying for improved cooling and die protection”, 2016-06.
- [32] D. Mehdi, “Effect of silicon content on the mechanical properties of aluminum alloy”, International Research Journal of Engineering and Technology, vol. 2, pp. 1326–1330, 2015-07.
- [33] D. S. MacKenzie, “Quenching of aluminum alloys”, in Aluminum Science and Technology, K. Anderson, J. Weritz, and J. G. Kaufman, Eds., vol. 2A, ASM International, 2018, pp. 438–461. doi: 10.31399/asm.hb.v02a.a0006506.
[Online]. Available: https://dl.asminternational.org/handbooks/editedvolume/10/chapter/117748/Quenching-of-Aluminum-Alloys. - [34] S. MacKenzie, HTM Journal of Heat Treatment and Materials, vol. 75, no. 1, pp. 23–34, 2020. doi: doi:10.3139/105.110401.
[Online]. Available: https: //doi.org/10.3139/105.110401. - [35] G. E. Totten, C. E. Bates, and N. Clinton, Handbook of quenchants and quenching technology. ASM international, 1993.
- [36] H. Tensi and P. Stitzelberger-Jacob, “Effects of rewetting on the cooling of quenched aluminum specimens”, HTM, Haerterei-Tech. Mitt, vol. 43, no. 3, pp. 148–155, 1988.
- [37] H. M. Tensi, P. Stitzelberger-Jakob, and G. E. Totten, “Surface rewetting of aluminum.”, Advanced materials & processes, vol. 156, no. 6, H15–H15, 1999.
- [38] Y. Lei, H. Zhao, W. Bai, Q. Xu, and Z. Han, “Microstructure, mechanical properties and residual stress of high vacuum die casting alsi10mgmn alloys with different spray quenching”, Journal of Materials Processing Technology, vol. 325, p. 118 284, 2024, issn: 0924-0136. doi: https : / / doi . org / 10 . 1016 / j . jmatprotec . 2024 . 118284.
[Online]. Available: https : / / www . sciencedirect.com/science/article/pii/S0924013624000025. - [39] R. D. Lopez-Garcia, I. Medina-Juárez, and A. Maldonado-Reyes, “Effect of quenching parameters on distortion phenomena in aisi 4340 steel”, Metals, vol. 12, no. 5, 2022, issn: 2075-4701. doi: 10.3390/met12050759.
[Online]. Available: https://www.mdpi.com/2075-4701/12/5/759. - [40] L. T. Blessing and A. Chakrabarti, DRM: A design reseach methodology. Springer, 2009.
- [41] Mega casting, n.d.
[Online]. Available: https://www.media.volvocars.com/ global/en-gb/media/photos/327230/mega-casting-8.
Copyright:
This summary is based on the master's thesis "Improving Quality in Mega-Casted Products: Identification of contributors to geometrical variation" by Paul Adam and David Hermez.
Unauthorized commercial use is prohibited.
Copyright © 2025 CASTMAN. All rights reserved.