This introductory paper is the research content of the paper ["Improving Die Casting Melt Quality and Casting Results with Melt Quality Analysis and Filtration"] published by [Metaullics Systems Co. L.P.].
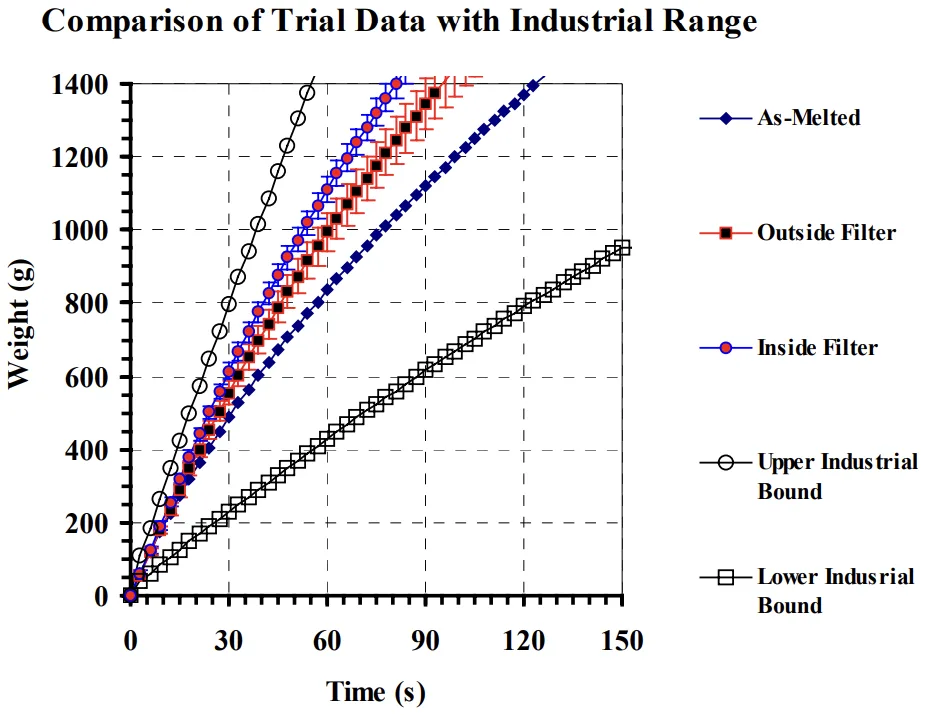
1. Overview:
- Title: Improving Die Casting Melt Quality and Casting Results with Melt Quality Analysis and Filtration
- Author: Dr. David V. Neff
- Publication Year: Not explicitly stated in the provided text.
- Published Journal/Society: Not explicitly stated, but references suggest presentations at AFS (American Foundry Society) conferences.
- Keywords: Aluminum castings, melt quality, inclusions, filtration, bonded particle filter, die casting, machinability, scrap reduction.
2. Abstract
The use of aluminum castings in automotive applications continues to expand at a significant pace. High volume requirements are served by high pressure, low pressure, permanent mold, and precision sand casting processes. The engineered requirements for these applications demand a high degree of casting integrity, which begins with the aluminum alloy melt conditions. Information is presented in this paper on several shop floor and laboratory methods of evaluating melt quality cleanliness, especially with respect to inclusions, and the benefits to be derived from sustained-usage, in-furnace filtering systems employing the bonded particle filter. Substantial gains can be made in reduction of machining defects, improved surface finish, increased elongation, reduced leakers, and overall scrap reduction---all with minimal cost, effort, and risk utilizing bonded particle filtration.
3. Research Background:
Background of the research topic:
The growth in aluminum casting production, particularly for automotive applications (engine components, structural components, wheels), has driven the need for higher casting properties.
Status of previous research:
Filtration processes are commonly used in aluminum shape casting operations. Bonded particle filters have emerged as the preferred choice for in-furnace applications (Neff, 1995).
Need for research:
Higher property requirements demand excellent metal quality and stringent control of inclusions and hydrogen content to minimize porosity. It is often not practical to provide absolute point-of-pour filtration in pressure diecasting, gravity diecasting, permanent mold processes, and high volume sand casting.
4. Research purpose and research question:
Research purpose:
To demonstrate the effectiveness of bonded particle filtration in improving melt quality and casting results. To present shop floor and laboratory methods for evaluating melt cleanliness.
Core research:
Evaluation of melt cleanliness using various techniques (Prefil, PodFA, K-Mold, etc.) and the impact of bonded particle filtration on casting quality parameters (machinability, scrap reduction, mechanical properties).
5. Research methodology
The research employs a combination of laboratory evaluations and production-scale experiments in die casting foundries.
- Research Design: Comparative studies (filtered vs. unfiltered metal), and evaluations of different filter configurations.
- Data Collection:
- Reduced Pressure Test (Figure 2)
- Alscan (hydrogen measurement)
- Qualiflash (fluidity test, Figure 3)
- Prefil Footprinter (real-time analysis of metal cleanliness, Figure 4)
- PodFA (metallographic examination, Figure 5)
- Mechanical Testing (using a multiple test bar mold, Figure 6)
- Tatur Test (shrinkage and porosity, Figure 7)
- K-Mold (macro-cleanliness, Figure 8)
- Analysis Method: Quantitative and semi-quantitative analysis of melt cleanliness, fluidity, mechanical properties, and defect rates. Comparison of results with industry standards.
- Research Scope: Focus on in-furnace filtration using bonded particle filters, primarily in the context of die casting.
6. Key research results:
Key research results and presented data analysis:
- Prefil Results: Filtered metal showed cleanliness comparable to the best 'clean metal' industry standard (Figure 9a). Production foundry results also showed significant improvement with filtration (Figure 9b).
- PodFA Results: The 8 grit bonded particle filter showed improved results compared to a 20 ppi ceramic foam filter (Figure 10). Filtration after flux injection further improved metal quality (Figure 11).
- K-Mold Results: Clear distinction between filtered and unfiltered metal in both laboratory (Figure 12a) and production (Figure 12b) settings.
- Tatur Test Results: Filtered material showed a 3% difference in pipe volume and a 10% higher feeding distance (Table 1).
- Mechanical Properties: Significant improvement in elongation for filtered samples, while tensile and yield strength were not greatly affected (Table 2).
- Qualiflash Results: Strong advantage in metal fluidity with filtered metal in both laboratory and production settings (Figure 13a).
- Machinability and Scrap Reduction: Significant improvements in various foundries, including hardspot elimination, reduced leakers, extended tool life, and reduced scrap (Table 3).
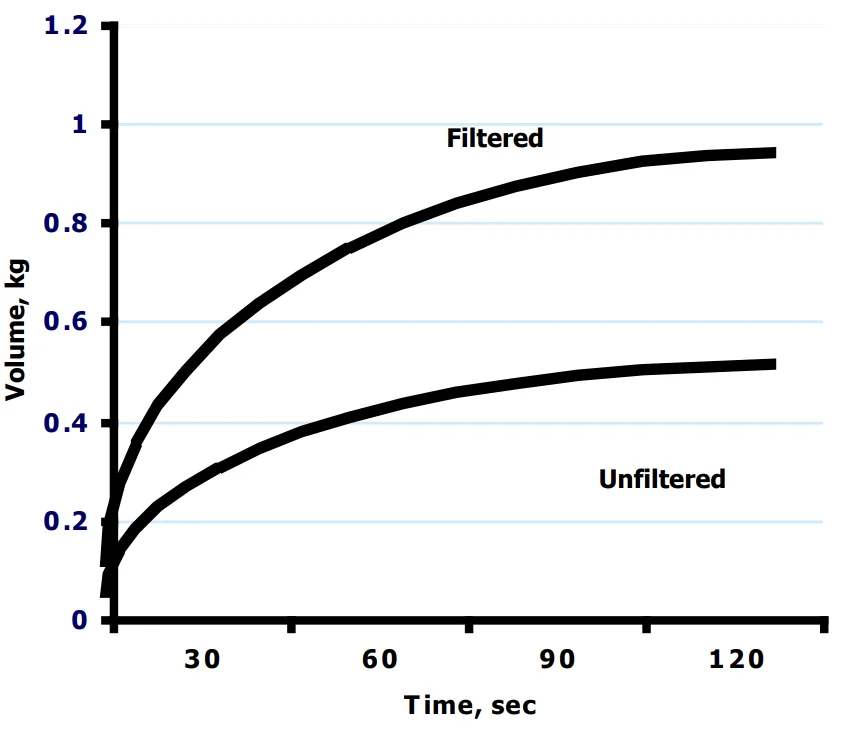
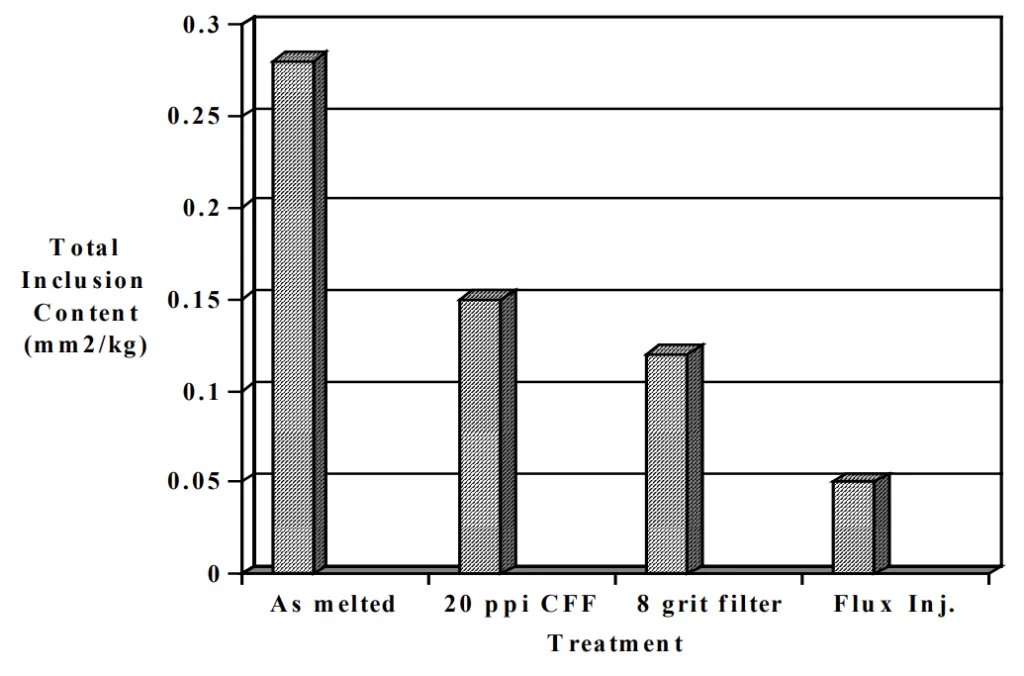
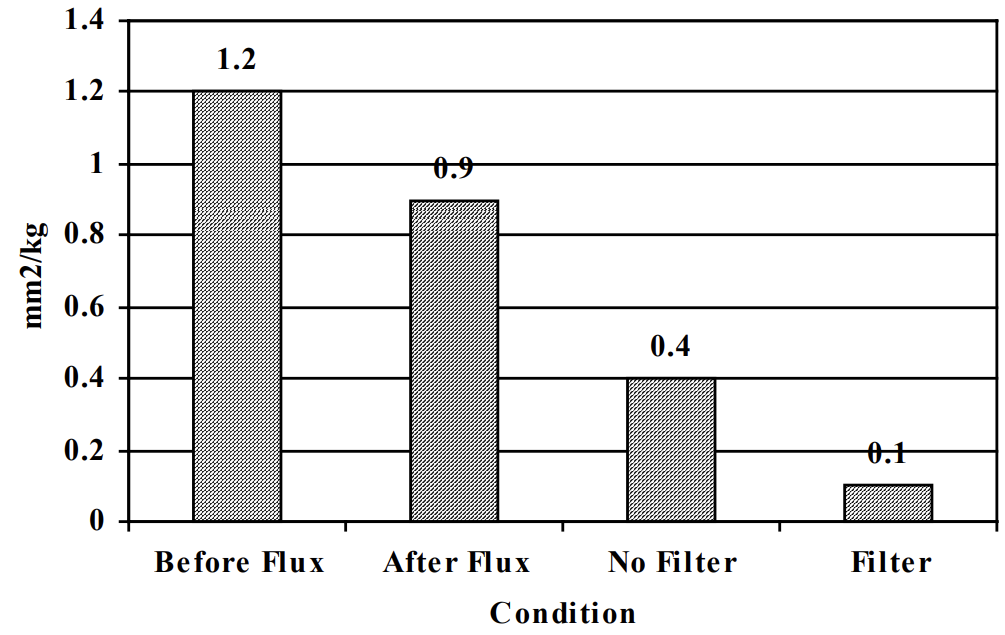
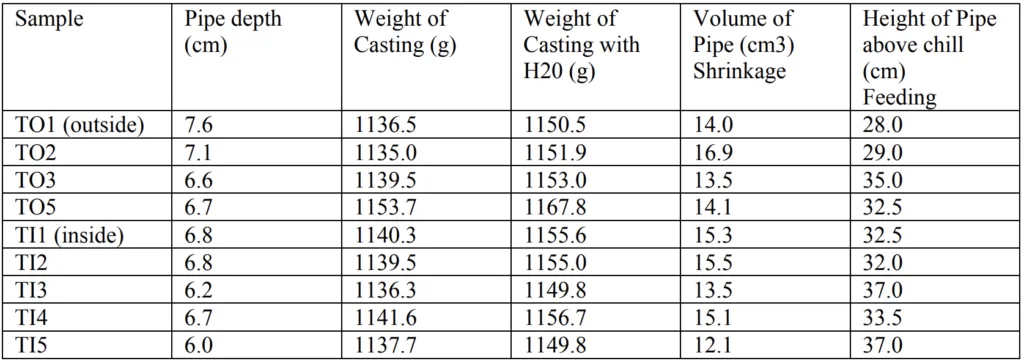
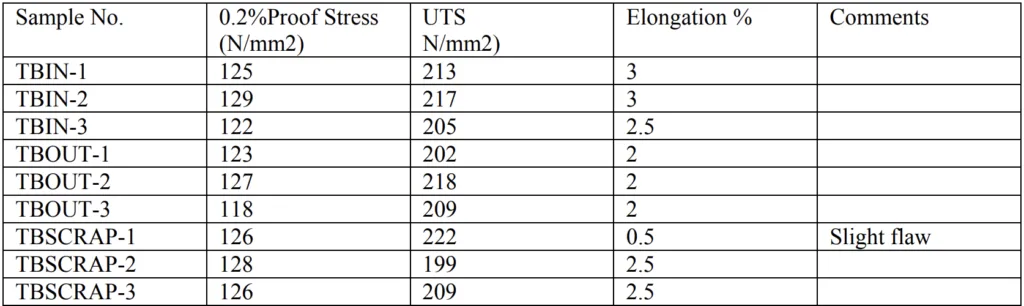
List of figure names:
- Figure la: Vertical Gate Filters are placed in the outlet well or dipwell of a casting furnace.
- Figure 1b: A box filter is useful in crucible furnaces our dipwells of other furnace types.
- Figure 2: The Reduced Pressure Test is the most common tool used by foundries and diecasters to assess metal quality.
- Figure 3: The Qualiflash test measures molten metal fluidity semi-quantitatively.
- Figure 4: The Prefil Footprinter provides real-time analysis of metal cleanliness relative to accumulated industry data. (N-Tec)
- Figure 5: The PodFA test is a common method to evaluate metal cleanliness using metallography on the collected sample.
- Figure 6: A multiple test bar mold is used to cast specimens for mechanical testing. (N-Tec)
- Figure 7: The Tatur test measures shrinkage and porosity. (N-Tec).
- Figure 8: The K-Mold is a simple shop-floor, real-time test which evaluates macro-cleanliness.
- Figure 9a:The Prefil curve demonstrates improved fluidity with the filter compared with
- Figure 9b: Production foundry Prefil results verify benefits of filtration.
- Figure 10: PodFA results show improvement of 8 grit bonded particle filter over 20 ppi ceramic foam filter.
- Figure 11: PodFA results show further improvement by filtration after flux injection.
- Figure 12a: Laboratory K-mold results after continuous re-use of the same metal.
- Figure 12b: Production diecaster K-Mold results show excellent results on 380 alloy.
- Figure 13a: Laboratory results with Qualiflash show significant improvement with the box filter.
7. Conclusion:
Summary of key findings:
Bonded particle filtration significantly improves metal fluidity, elongation, and overall metal cleanliness. These improvements lead to better die fill, fewer feeding defects, reduced microporosity, improved machinability, and reduced scrap rates.
- Academic significance: The research provides quantitative and qualitative evidence of the effectiveness of bonded particle filtration using various established testing methods.
- Practical implications: The use of bonded particle filters in-furnace can significantly improve casting quality and reduce costs in die casting operations.
8. References:
- [1] Neff, D., "continuous, Sustained, “Re-useable” Filtration Systems for Aluminum Foundries and Diecasters, Proceedings, 4th International Conference on Molten Aluminum Processing, AFS, Orlando, November, 1995, р.121
- [2] Law, J., Tian, C., Murray, M., “Experiences in the Measurement of Molten Metal Quality in a High Pressure Diecasting Foundry", Transacations, NADCA 1999, p.235
- [3] Evans, C., Willmert, W., “Qualiflash as it Relates to Filtration and Degassing for Foundry and Extrusion Alloys" Proceedings, Fifth International Conference, Molten Aluminum Processing, AFS, Orlando, November, 1998, p. 349
9. Copyright:
- This material is a paper by "Dr. David V. Neff": Based on "Improving Die Casting Melt Quality and Casting Results with Melt Quality Analysis and Filtration".
- Source of paper: [DOI URL] Not provided in the text.
This material was created to introduce the above paper, and unauthorized use for commercial purposes is prohibited. Copyright © 2025 CASTMAN. All rights reserved.