This article introduces the paper ['General manufacturing route for medical devices'] presented at the ['Metallic Biomaterials Processing and Medical Device Manufacturing']
1. Overview:
- Title: General manufacturing route for medical devices
- Author: Yu Sun, Sen Yu and Gui Wang
- Publication Year: 2021
- Publishing Journal/Academic Society: Metallic Biomaterials Processing and Medical Device Manufacturing, Elsevier Ltd.
- Keywords: Manufacturing process, medical devices, metal industry, casting, forming, heat treatment, joining, titanium alloys
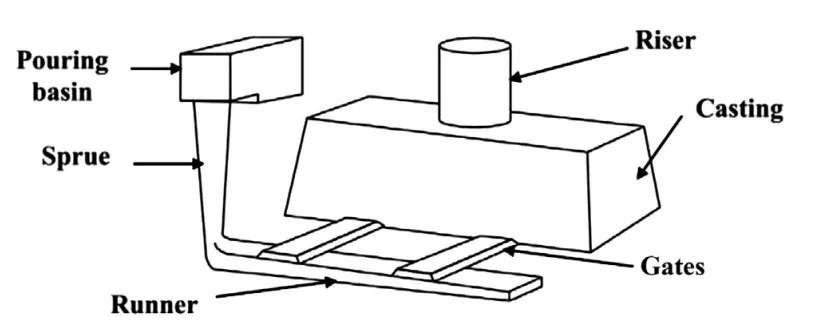
2. Research Background:
Background of the Research Topic:
Manufacturing is fundamental to the secondary industry, transforming raw materials into finished goods. The medical device industry utilizes a wide array of manufacturing processes to create products ranging from simple surgical tools to complex medical systems. These processes are adapted from the metal industry to produce components from biomaterials. Modern manufacturing integrates all intermediate steps from product design to component integration.
Status of Existing Research:
In the metal industry, manufacturing routes typically involve solidifying molten metal and then mechanically shaping it. Heat and plastic deformation significantly influence the mechanical properties of metals. Understanding the science behind manufacturing processes is crucial for producing high-quality, economical parts and establishing effective techniques, particularly in mold design and casting practice.
Necessity of the Research:
This chapter addresses the major manufacturing processes for medical devices, focusing on the route from raw material to primary shape. It emphasizes casting, forming, heat treatment, and joining, highlighting the underlying scientific principles essential for quality and cost-effective production in the medical device sector. A detailed example of primary manufacturing processing for titanium alloys is included.
3. Research Purpose and Research Questions:
Research Purpose:
The purpose of this chapter is to elucidate the general manufacturing routes for medical devices, with a focus on metal processing. It aims to provide a handbook-level understanding of the major manufacturing processes, including casting, forming, heat treatment, and joining, relevant to the production of medical devices.
Key Research:
The key research areas covered in this chapter are:
- Metal casting fundamentals and processes, including metal flow, solidification, and defect formation.
- Metal forming processes, encompassing rolling, forging, extrusion, and drawing, along with the effect of temperature.
- Heat treatment methods and their impact on microstructure and properties.
- Welding techniques for joining materials in medical device manufacturing.
- Specific manufacturing processes for titanium alloy tubes and wires.
Research Hypotheses:
As a handbook chapter, it does not explicitly state research hypotheses. However, the underlying premise is that a thorough understanding of these manufacturing processes is essential for producing high-quality medical devices from metallic biomaterials.
4. Research Methodology
Research Design:
This chapter employs a descriptive and explanatory approach, outlining the fundamental principles and processes involved in manufacturing medical devices from metallic materials. It provides a structured overview of various manufacturing techniques, focusing on metal casting and forming.
Data Collection Method:
This chapter synthesizes existing knowledge and principles in materials science and manufacturing engineering. It draws upon established theories and practices in the field to describe and explain the manufacturing routes.
Analysis Method:
The chapter uses a descriptive analysis method, breaking down complex manufacturing processes into fundamental steps and principles. It utilizes figures and examples to illustrate key concepts and mechanisms, such as solidification in casting (Fig. 3.2), shrinkage during casting (Fig. 3.5), and microstructure evolution during hot rolling (Fig. 3.11).
Research Subjects and Scope:
The scope of this chapter is focused on the general manufacturing routes for medical devices, specifically addressing metal casting, metal forming, heat treatment, and welding. The primary subjects are metallic biomaterials and the manufacturing processes used to shape them into medical components. The chapter also includes a specific focus on titanium alloys as an example material.
5. Main Research Results:
Key Research Results:
- Metal Casting: Detailed explanation of metal casting as a manufacturing process, covering fundamentals such as fluid flow (fluidity, pouring temperature, gating system), solidification (nucleation, crystal growth, grain structure), heat transfer, and formation of casting defects (shrinkage, segregation). Different casting processes like investment casting and ingot casting are described (Fig. 3.7, Fig. 3.8, Fig. 3.9).
- Metal Forming: Comprehensive overview of metal forming processes, including rolling (flat rolling, profile rolling, ring rolling, thread rolling), forging (closed-die, open-die), extrusion (positive, reverse, lateral), and drawing. The effect of temperature (cold, warm, hot working) on metal forming is discussed (Fig. 3.10, Fig. 3.11, Fig. 3.12, Fig. 3.13, Fig. 3.14, Fig. 3.15, Fig. 3.16, Fig. 3.17, Fig. 3.18, Fig. 3.19, Fig. 3.20, Fig. 3.21).
- Heat Treatment: Explanation of heat treatment processes (normalizing, annealing, quenching, tempering) and their effects on microstructure and properties of metallic materials (Fig. 3.22, Fig. 3.23).
- Welding: Description of welding as a joining process, including fusion welding, weld zones (base metal, weld metal, HAZ), and factors affecting weld quality (Fig. 3.24, Fig. 3.25). Specific considerations for welding titanium tubes are provided.
- Titanium Alloy Processing: Specific manufacturing routes for titanium alloy tubes and wires are discussed, including extrusion (perforated extrusion, back squeeze) and rolling of tubes, and drawing of wires (Fig. 3.26, Fig. 3.27, Fig. 3.28, Fig. 3.29).
Data Interpretation:
- Fluidity in Casting: Fluidity is determined by viscosity, surface tension, and solidification pattern. Higher superheat and mold surface characteristics influence metal flow capability.
- Solidification and Grain Structure: Solidification occurs via nucleation and crystal growth, leading to grain structures that affect casting properties. Cooling rate influences dendrite structure (Fig. 3.4).
- Shrinkage and Porosity: Shrinkage during solidification can lead to porosity, which can be mitigated by casting design and directional solidification. Table 3.1 shows solidification shrinkage of metals.
- Temperature in Forming: Temperature significantly affects metal forming. Cold working increases strength but reduces ductility, while hot working allows for greater shape change due to dynamic recrystallization (Fig. 3.11).
- Heat Treatment Effects: Heat treatment processes like annealing, normalizing, quenching, and tempering are used to modify microstructure and mechanical properties, such as hardness and strength (Fig. 3.23).
- Welding Zones: Fusion welding creates distinct zones (base metal, weld metal, HAZ) with varying microstructures and properties. Welding parameters and material properties influence the HAZ characteristics (Fig. 3.24).
Figure Name List:
- Figure 3.1 Schematic illustration of a typical riser-gated casting.
- Figure 3.2 (A) Illustration of solidification and temperature distribution in the solidifying metal and (B) a well-developed dendritic structures casting.
- Figure 3.3 grain structure of as cast meta ls (A) a pure zinc showing typical combination of columnar grains from the mold wall and equiaxed grains in the center, (B) as cast grain for magnesium can be refined by adding an inoculant (C) during the casting process.
- Figure 3.4 (A) Temperature distribution during the casting solidification and (B) coarse dendritic structures with large spacing between dendrite arms result from a slow cooling rate.
- Figure 3.5 illustration of three-stage shrinkage during casting.
- Figure 3.6 Schematic of (A) microsegregation, (B) typical macrosegregation pattern in a steel ingot.
- Figure 3.7 Classification of casting processes.
- Figure 3.8 The investment-casting process.
- Figure 3.9 Schematics of an ingot casting process and development of typical grain structures.
- Figure 3.10 The schematic diagram for stress-strain curve of a low-carbon steel.
- Figure 3.11 Schematic illustration of microstructure evolution during the hot rolling process.
- Figure 3.12 Grain structure comparison between a machined and rolled bolt.
- Figure 3.13 Schematic illustration of rolling process.
- Figure 3.14 Closed-die forging with flash. (A) Schematic diagram with flash terminology. (B) Forging sequence in closed-die forging of connecting rods.
- Figure 3.15 Open-die forging.
- Figure 3.16 The basic principles of metal extrusion.
- Figure 3.17 The relationship between force and displacement for positive and reverse extrusion.
- Figure 3.18 Process of drawing.
- Figure 3.19 Schematic showing the mechanism of straight-knife shearing.
- Figure 3.20 Bending in the V-die.
- Figure 3.21 Progression of metal flow in drawing a cup from a flat blank.
- Figure 3.22 1 Local magnification of iron-carbon phase diagram.
- Figure 3.23 Schematic diagram of the main annealing processes: (A) deformed state, (B) recovered, (C) partially recrystallized, (D) fully recrystallized, (E) grain growth, and (F) abnormal grain growth.
- Figure 3.24 Features of a typical fusion-weld zone in arc welding.
- Figure 3.25 Grain structure in (A) a deep weld and (B) a shallow weld; note that the grains in the solidified weld metal are perpendicular to their interface with the base metal. (C) Weld bead on a cold-rolled nickel strip produced by a laser beam. (D) Microhardness (HV) profile across a weld bead.
- Figure 3.26 Schematic diagram of solid ingot perforation and extrusion process.
- Figure 3.27 Schematic diagram of pipe reverse extrusion.
- Figure 3.28 Schematic diagram of the working principle of skew rolling perforating machine.
- Figure 3.29 Principle of high-pressure hot gas forming.
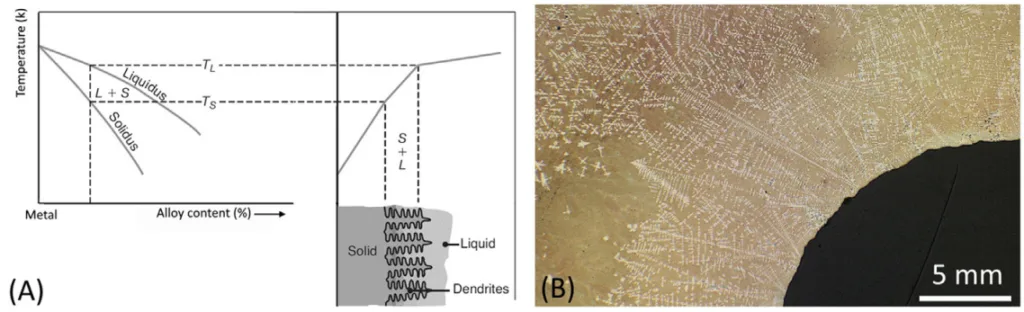
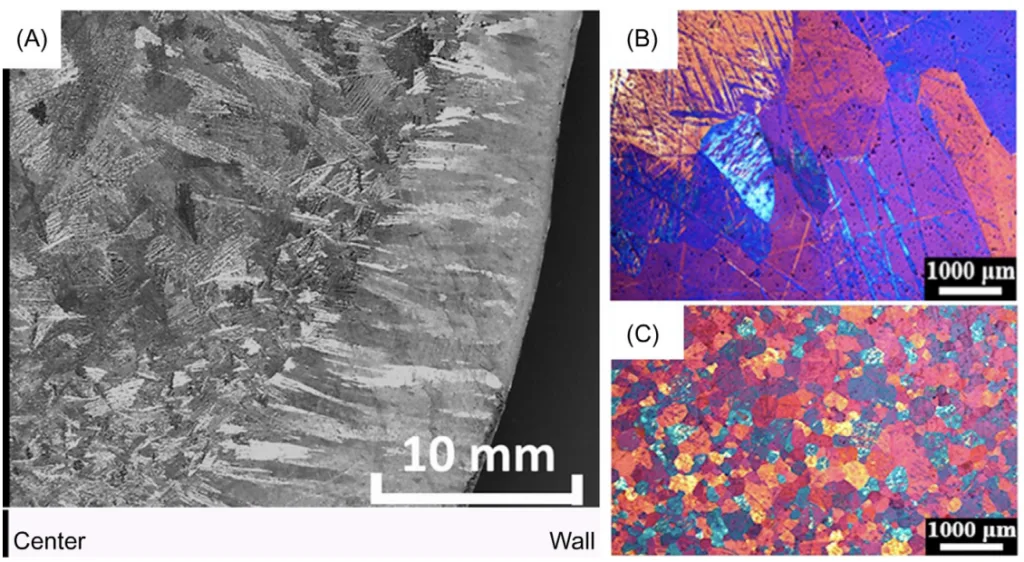
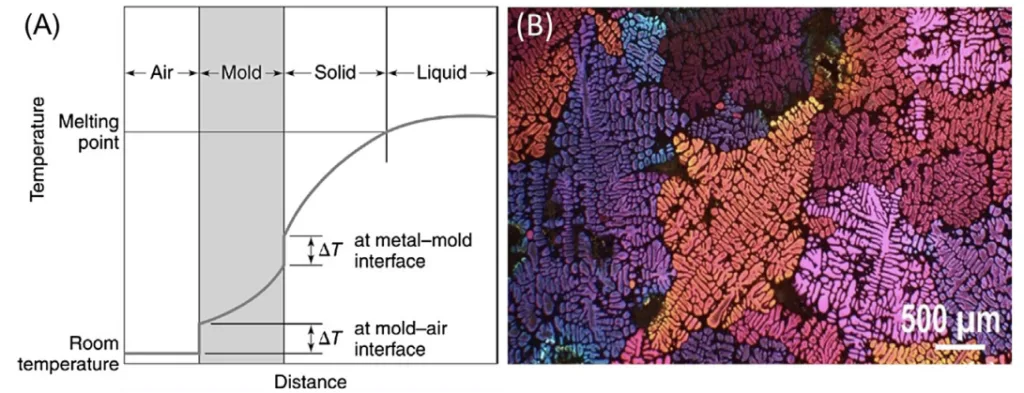

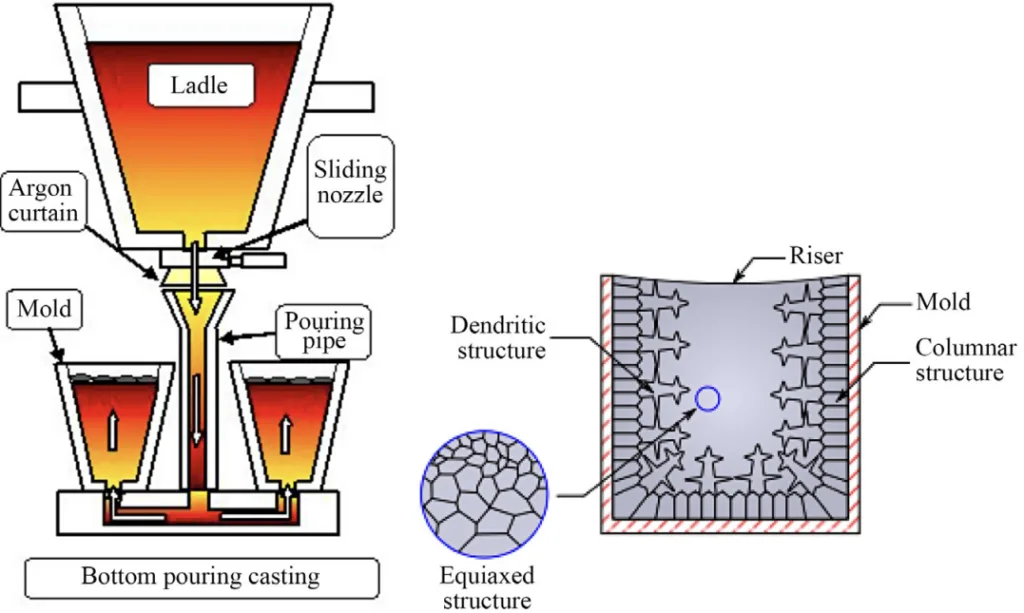
6. Conclusion:
Summary of Main Results:
This chapter provides a comprehensive overview of the general manufacturing routes for medical devices, focusing on metal casting, forming, heat treatment, and welding. It details the fundamental principles, processes, and influencing factors for each manufacturing technique. Specific examples, such as titanium alloy processing, illustrate the practical application of these methods in medical device manufacturing. The chapter emphasizes the importance of understanding material behavior and process parameters to achieve desired product quality and performance.
Academic Significance of the Research:
The chapter serves as a valuable resource for experts and researchers in the field of medical device manufacturing and materials science. It consolidates essential knowledge on various manufacturing processes, providing a structured framework for understanding and further research in this domain. It highlights the scientific principles underlying each process, promoting a deeper understanding of manufacturing metallurgy.
Practical Implications:
For practitioners in the medical device industry, this chapter offers practical guidance on selecting and optimizing manufacturing processes for metallic components. It provides insights into process parameters, defect control, and material selection, aiding in the production of high-quality, reliable medical devices. The detailed descriptions of casting, forming, heat treatment, and welding techniques offer a foundation for process design and improvement.
Limitations of the Research
As a handbook chapter, it provides a broad overview and does not delve into highly specific or cutting-edge research topics. The depth of coverage for each process is limited by the scope of a single chapter. It serves as an introduction and reference point rather than an exhaustive study of each manufacturing method.
7. Future Follow-up Research:
- Directions for Follow-up Research
Further research could explore advanced variations and optimizations within each manufacturing process discussed, such as additive manufacturing integration with casting or forming, novel heat treatment strategies for specific biomaterials, and advanced welding techniques for dissimilar metal joining in medical devices. - Areas Requiring Further Exploration
Areas requiring further exploration include the application of Industry 4.0 technologies in medical device manufacturing, in-depth studies on the biocompatibility and long-term performance of materials processed using these routes, and the development of sustainable and cost-effective manufacturing solutions for the medical device industry.
8. References:
- J. Campbell, Casting, second ed., Elsevier, Butterworth-Heinemann, 2003.
- B. Cantor, K. O'Reilly, Solidification and Casting, CRC Press, 2002.
- K. Serope, S.R. Schmid, Manufacturing Engineering and Technology, seventh ed., P&C ECS, 2013.
- K.R. Ravi, R.M. Pillai, K.R. Amaranathan, B.C. Pai, M. Chakraborty, Fluidity of aluminum alloys and composites: a review, J. Alloy. Compd. 456 (2008) 201–210.
- P.R. Beeley, R.F. Smart, Investment Casting, Maney Publishing for IOM3, the Institute of Materials, Minerals and Mining, 1995.
- J. Campbell, Complete Casting Handbook Metal Casting Processes, Metallurgy, Techniques and Design, second ed., Elsevier, 2015.
- F. Herlach, Solidification and Crystallization, John Wiley & Sons, 2004.
- C. Beckermann, Macrosegregation, ASM Handbook, Volume 15: Casting, ASM Handbook Committee, 2008, pp. 348-352. https://doi.org/10.1361/asmhba0005216.
- R. Mehrabian, M. Keane, M.C. Flemings, Interdendritic fluid flow and macrosegregation; influence of gravity, Metall. Trans. 1 (1979) 1209–1220.
- H. Fredriksson, U. Åkerlind, Materials Processing During Casting, John Wiley & Sons Ltd, 2012.
- T. Altan, G. Ngaile, G. Shen, Cold and Hot Forging: Fundamentals and Applications, ASM International, 2004.
- T.A. Perkins, T.J. Kronenberger, J.T. Roth, Metallic forging using electrical flow as an alternative to warm/hot working, J. Manuf. Sci. Eng 129 (2007) 84–94.
- M. Spittel, T. Spittel, Metal Forming Data of Ferrous Alloys - Deformation Behaviour, Springer, Berlin Heidelberg, 2009.
- J.L. Duncan, Geometric and Mechanics Models of Sheet Forming Processes, Elsevier Inc, 2002.
- K. Styles, A. Bichard, Working Drawings Handbook, Taylor and Francis, 2012.
- C.N.A. Kumar, R. Deivanathan, Effect of aluminium alloy and mild steel on the productivity in sheet metal forming processes, Appl. Mech. Mater 234 (2012) 64–68.
- S.C. Babu, V.S.S. Kumar. 2012. Experimental studies on incremental forming of stainless steel AISI 304 sheets. Proc. IMechE Part B J. Eng. Manufacture 226 (7) 1224-1229.
- W.H. Sillekens, G. Kurz, R.J. Werkhoven, Magnesium forging technology: state-of-the-art and development perspectives, in: L. Katgerman, F. Soetens (Eds.), 11th International Aluminium Conference - INALCO 2010 New Frontiers in Light Metals, IOS Press © 2010 The authors and IOS Press, 2010.
- Z. Feng, L. Chai, Z. Chen, T. Jin, G. Shi, Y. Jin, et al., Forging technology and microstructure and mechanical properties of a novel high temperature titanium alloy resistant to 650°C, in: Y. Han (Ed.), High Performance Structural Materials. CMC 2017, Springer, 2018.
- T.P. Wang, K.M. Qi, Metal Plastic Processing-Rolling Theory and Process, Metallurgical Industry Press, 2001.
- M.P. Dixit, U.S. Dixit, Modeling of Metal Forming and Machining Processes, Springer, London, 2008.
- B.R. Song, Rolling Technology, Metallurgical Industry Press, 2014.
- H. Tschaetsch, Extrusion, Metal Forming Practise, Springer, Berlin, Heidelberg, 2006.
- L. Katgerman, F. Soetens, A.R. Eivani, A.J. den Bakker, J. Zhou, J. Duszczyk, An Investigation of Dynamic Recrystallization During Hot Extrusion of Al-4.5Zn-1Mg Alloy, IOS Press, 2010.
- Dorel Banabic, Advanced Methods in Material Forming, Springer,, Berlin, Heidelberg, 2007.
- George E. Totten, Steel Heat Treatment, Taylor and Francis, 2006.
- M.I. Khan, Welding Science and Technology, New Age International, 2007.
- B.K. Choudhary, J. Christopher, D.P. Rao Palaparti, E. Isaac Samuel, M.D. Mathew, Influence of temperature and post weld heat treatment on tensile stress-strain and work hardening behaviour of modified 9Cr-1Mo steel, Mater. Des 52 (2013) 58-66.
- K.E. Thelning, Steel and Its Heat Treatment, Butterworth-Heinemann, 2013.
- R.M. Mahamood, E.T. Akinlabi, Non-contact welding technologies: fusion welding, Advanced Noncontact Cutting and Joining Technologies. Mechanical Engineering Series, Springer, Cham, 2018.
- R. Timings, Fabrication and Welding Engineering, Taylor and Francis, 2008.
- P.T. Houldcroft, R. John, Welding and Cutting: A Guide to Fusion Welding and Associated Cutting Processes, Elsevier, Woodhead Publishing, 2001.
- R.W. Messler, Welding as a Joining Process, Elsevier Inc, 2004.
- G.F. Deyev, Surface Phenomena in Fusion Welding Processes, Taylor and Francis, 2010.
- V.Y. Osadchy, A.S. Vavilin, V.G. Zimovec, A.P. Kolikov, The technology and equipment of the pipe production, internet engineering, Moscow, 2002 (in Russian).
- S.B. Bodlani, S.C.K. Yuen, G.N. Nurick, The energy absorption characteristics of square mild steel tubes with multiple induced circular hole discontinuities-part 1: experiments, J. Appl. Mech 76 (2009) 041012.
- S.D. Hu, B. Ye, L.X. Li, Materials properties of thick-wall cold-rolled welded tube with a rectangular or square hollow section, Constr. Build Mater 25 (2011) 2683-2689.
- R.S. Saluja, V. Singh. 2019. Subjective factors consideration in the selection of welding technique for welded tube manufacturing. In: R. Narayanan, S. Joshi, U. Dixit (Eds.). Advances in Computational Methods in Manufacturing. Lecture Notes on Multidisciplinary Industrial Engineering, Springer, Singapore.
- A. Kumar, M. Sapp, J. Vincelli, M.C. Gupta, A study on laser cleaning and pulsed gas tungsten arc welding of Ti-3Al-2.5V alloy tubes, J. Mater. Process Tech. 210 (2009) 64-71.
- A. Kumar, Mool C. Gupta, Surface preparation of Ti-3Al-2.5V alloy tubes for welding using a fiber laser, Opt. Lasers Eng 47 (2009) 1259–1265.
- B. Ren, G. Tao, P. Wen, C. Du, Study on weldability window and interface morphology of steel tube and tungsten alloy rod welded by explosive welding, Int. J. Refractory Met. Hard Mater 84 (2019) 105005.
- H. Pan, Z. Wang, Y. Hui, C. Yang, X. Deng, C. Bao, Product Design and Production Practice of 700MPa High Strength Hot Rolled Strip for Auto Axle Tube, Springer International Publishing, 2016.
- S. Yuan, Development and trends in internal high pressure forming, Metal Form. Technol. 21 (4) (2003) 32-34.
- R. Neugebauer, A. Sterzing, F. Schieck. Opportunities for progressive applications by means of integrating and combining various technologies with hydroforming, Tube Hydroforming Technology-Proceedings Tubehydro, Harbin, 2007, pp. 65-69.
- X. Long, L. Shuyu, A new type of rod and tubular high-power ultrasonic-focused radiator, J Nanjing Univ. (Nat. Sci.) 05 (2012) 544-552.
- H. Hosseinabadi, S.S.A. Goodarzi, A coupled stream function-finite element analysis for wire drawing processes, Int. J. Adv. Manuf. Technol 57 (2011) 917–926.
9. Copyright:
- This material is "Yu Sun, Sen Yu and Gui Wang"'s paper: Based on "General manufacturing route for medical devices".
- Paper Source: https://doi.org/10.1016/B978-0-08-102965-7.00003-5
This material was summarized based on the above paper, and unauthorized use for commercial purposes is prohibited.
Copyright © 2025 CASTMAN. All rights reserved.