The content of this introduction paper is based on the article "EXPERIMENTAL EVALUATION, DIAGNOSIS, AND PREDICTION OF THE IMPACTS OF POWER QUALITY DISTURBANCES IN IE2, IE3, AND IE4 CLASS EFFICIENCY MOTORS." published by [UFPA/ITEC / PPGEE].
![Figure 2-1 - Induction Motor components [2].](https://castman.co.kr/wp-content/uploads/Figure-2-1-Induction-Motor-components-2-png.webp)
1. Overview:
- Title: EXPERIMENTAL EVALUATION, DIAGNOSIS, AND PREDICTION OF THE IMPACTS OF POWER QUALITY DISTURBANCES IN IE2, IE3, AND IE4 CLASS EFFICIENCY MOTORS.
- Author: JONATHAN MUÑOZ TABORA
- Year of publication: 2024
- Journal/academic society of publication: UFPA/ITEC / PPGEE
- Keywords: Voltage variation, voltage unbalance, harmonics, temperature, efficiency classes, permanent magnet motors, predictive maintenance.
2. Abstract:
Electric motors remain the largest end-use of electricity in the world and a fundamental part of the industrial sector. In addition, with technological advances, their applications have expanded into new categories such as electric vehicles, transportation, and navigation, among others. Europe has started to upgrade to IE4 efficiency motor classes, and it is expected that other regions will follow the transition to higher efficiency motor classes. In some regions, the operating voltage may differ from the nominal voltage according to IEC 60038-2009. This, together with other disturbances such as unbalance and voltage harmonics, can affect the performance of these new technologies. In this context, significant efforts have been made in predictive maintenance to improve existing techniques with new proposals that increase their effectiveness in diagnosing the health of rotating machines in the presence of different disturbances present in SEPs. This work evaluates the impact of voltage variations, voltage harmonics, and different percentages of under and over-voltage unbalances on the temperature and performance of low-power induction motors of IE2, IE3, and IE4 classes. The study includes technical, economic, statistical, and thermal analysis to obtain important indicators related to energy consumption, efficiency, power factor, and temperature. In the search for innovative and complementary techniques, this study also presents a new Electric Motor Degradation Indicator (EMDI) based on frequency domain analysis of electric motor current waveforms for the diagnosis of rotating machinery integrity. The results show that under ideal operating conditions, the permanent magnet motor of the IE4 class has a better performance in terms of power consumption and temperature, but it has a non-linear characteristic. Then, in the presence of certain disturbances, the scenario changes, with lower performance compared to squirrel-cage induction motors under the same operating conditions. The analysis performed will allow to identify and quantify the impact of the different perturbations present in the electrical power systems on the performance of the new electric motor technologies to be introduced. Regarding the proposed motor health diagnostic indicator, the results presented strongly support the effectiveness of the proposed approach in facilitating the implementation of predictive maintenance practices. Another important contribution of this thesis is that its results will form the basis for the implementation of a new regulation for the introduction of minimum efficiency requirements for electric motors in Honduras.
3. Introduction:
In 2015, the Paris Agreement represented a significant global step in addressing climate change. Since then, it has driven the implementation of policies and regulations focused on energy efficiency, playing a key role in achieving environmental goals and promoting sustainable practices internationally. In this context, Induction motors (IMs) represent an important category for energy savings with about 53% of the world's final electrical energy consumption [1].
4. Summary of the study:
Background of the research topic:
Electric motors remain the largest end-use of electricity in the world and a fundamental part of the industrial sector. With technological advances, their applications have expanded into new categories such as electric vehicles, transportation, and navigation, among others. Europe has started to upgrade to IE4 efficiency motor classes, and it is expected that other regions will follow the transition to higher efficiency motor classes. In some regions, the operating voltage may differ from the nominal voltage according to IEC 60038-2009. This, together with other disturbances such as unbalance and voltage harmonics, can affect the performance of these new technologies.
Status of previous research:
Significant efforts have been made in predictive maintenance to improve existing techniques with new proposals that increase their effectiveness in diagnosing the health of rotating machines in the presence of different disturbances present in SEPs.
Purpose of the study:
This work evaluates the impact of voltage variations, voltage harmonics, and different percentages of under and over-voltage unbalances on the temperature and performance of low-power induction motors of IE2, IE3, and IE4 classes. The study includes technical, economic, statistical, and thermal analysis to obtain important indicators related to energy consumption, efficiency, power factor, and temperature. In the search for innovative and complementary techniques, this study also presents a new Electric Motor Degradation Indicator (EMDI) based on frequency domain analysis of electric motor current waveforms for the diagnosis of rotating machinery integrity.
Core study:
The results show that under ideal operating conditions, the permanent magnet motor of the IE4 class has a better performance in terms of power consumption and temperature, but it has a non-linear characteristic. Then, in the presence of certain disturbances, the scenario changes, with lower performance compared to squirrel-cage induction motors under the same operating conditions. The analysis performed will allow to identify and quantify the impact of the different perturbations present in the electrical power systems on the performance of the new electric motor technologies to be introduced. Regarding the proposed motor health diagnostic indicator, the results presented strongly support the effectiveness of the proposed approach in facilitating the implementation of predictive maintenance practices. Another important contribution of this thesis is that its results will form the basis for the implementation of a new regulation for the introduction of minimum efficiency requirements for electric motors in Honduras.
5. Research Methodology
Research Design:
The effects of voltage harmonics, voltage unbalance, and voltage magnitude variations were evaluated using the test benches shown in Figure 1-9 and Figure 1-10. The bench comprises a three-phase alternating current (AC) programmable source (1), in which different voltages applied to the IE2, IE3 and IE4 Class Induction motors (4) were configured. The induction motors input parameters were measured using a class “A” power-quality analyzer (2), and an electromagnetic brake (3) was used as the electric load.
Data Collection and Analysis Methods:
The tests were conducted at the Amazon Energy Efficiency Center (CEAMAZON) of the Federal University of Pará (UFPA). At first, the induction motors were subjected to a perfect three-phase sine voltage of 220 V for 1 h and 10 min so that they reached their thermal equilibrium, and, in a second moment:
- The value of each voltage harmonic (2nd, 3rd, 5th, and 7th) increased by 2% every 10 minutes until it reached 25%;
- Each motor was individually subjected to 1 hour and 10 minutes of 1%, 3%, and 4% NEMA voltage unbalance until thermal equilibrium was restored;
- The LSPMM was supplied with a nominal voltage of 220V (1.00 p.u.), which was used as the base voltage to define the undervoltage and overvoltage values per unit. The LSPMM was then subjected to VV conditions of 0.90, 0.95, 1.0, 1.05 and 1.10 p.u. with loads ranging from 0% to 125%.
Research Topics and Scope:
This work presents a series of methodologies aimed at analyzing the performance of 0.75 kW output power electric motors in the presence of different disturbances present in current electrical systems, such as voltage variation, voltage harmonics and voltage unbalance, in order to establish conclusions and guidelines to be considered by specialists in the substitution between technologies.
6. Key Results:
Key Results:
- The IE4 class permanent magnet motor shows the lowest currents, consumption, and operating temperature, as well as quieter operation, but with a higher percentage of harmonic distortion and a lower power factor compared to the IE3 class motor at the same load.
- The analyzed negative sequence harmonics (2nd and 5th) are individually more harmful than the analyzed positive sequence harmonic of 7th order.
- The third zero-sequence harmonic did not produce significant variations in electric motors, where the parameters showed variations around their initial values.
- The combination of all the harmonics turns out to be more harmful than any single harmonic analyzed, of which the second harmonic had the largest contribution.
- The models can be used to estimate the temperature increase based on the harmonic present for the analyzed power.
- The developed model reliably represents the performance of the motor under non-ideal conditions, such as in the presence of the negative sequence voltage harmonic.
- The proposed indicator has been successfully validated under different disturbances commonly found in electrical systems that motors may encounter in real operating conditions.
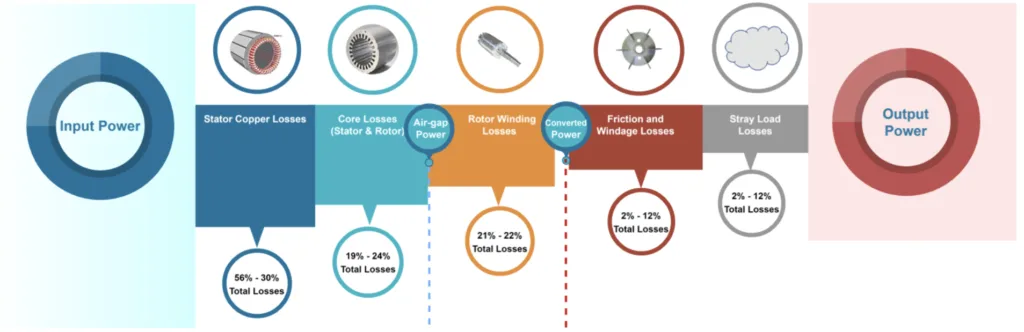
![Figure 2-3 - Typical fraction of losses in 50-Hz, four-pole squirrel cage induction motors for (a) Losses
variation as a function of output power [8]; (b) Losses variation as a function of load [9].](https://castman.co.kr/wp-content/uploads/image-1775-1024x425.webp)
![Figure 2-5 – Permanent magnet motors: (a) Surface mounted permanent magnet motor (SPM)[22] [23]; (b) Interior permanent magnet motor (IPM) [22] [24].](https://castman.co.kr/wp-content/uploads/image-1776-1024x769.webp)
![Figure 2-6 - Structure of a four-pole LSPMM [28]](https://castman.co.kr/wp-content/uploads/image-1777-1024x690.webp)
![Figure 2-7 - Typical rotor configurations for LSPMM’s :(a) Spoke rotor; (b) W Type magnetic circuit
structure; (c) Swastika magnetic circuit structure; (d) V-type magnetic circuit structure; (e) U-type
magnetic circuit structure; (f) Series-type magnetic circuit structure [29], [30].](https://castman.co.kr/wp-content/uploads/image-1778-1024x678.webp)
![Figure 2-8 – Starting torque in LSPMM and SCIM: (a) Starting behavior of torque components for
LSPMM´s [31]; (b) Torque behavior for IM and LSPMM during starting [26].](https://castman.co.kr/wp-content/uploads/image-1779-1024x329.webp)
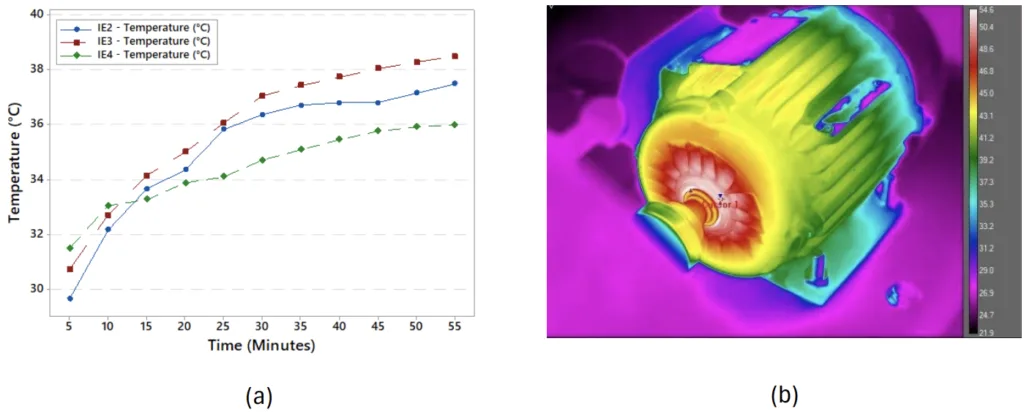
Figure Name List:
- Figure 1-1 - Energy efficiency classes classification and consumption
- Figure 1-2 - Countries with MEPS for electric motors in 2024.
- Figure 1-3 - Methodology for literature review based on the PRISMA statement.
- Figure 1-4 - Publications related to electric motors in recent years.
- Figure 1-5 - Distribution of publications related to energy forecasting worldwide.
- Figure 1-6 - Distribution of studies by subject area.
- Figure 1-7 - Thematic map of keywords separated by relevant categories.
- Figure 1-8 - Publications related to electric motors diagnosis in the last 20 years.
- Figure 1-9 - General test setup for the power quality disturbances tests.
- Figure 1-10 - General test setup for the electric motor degradation index tests.
- Figure 1-11- Thermographic images of the LSPMM
- Figure 2-1 - Induction Motor components [2]…….
- Figure 2-2 - Distribution of motor losses and percentage of losses for 0.75 kW – 160 kW IM's.
- Figure 2-3 - Typical fraction of losses in 50-Hz, four-pole squirrel cage induction motors
- Figure 2-4 - Impact of possible areas of improvement for induction motor performance
- Figure 2-5 - Permanent magnet motors
- Figure 2-6 - Structure of a four-pole LSPMM [28]…
- Figure 2-7 - Typical rotor configurations for LSPMM's
- Figure 2-8 Starting torque in LSPMM and SCIM
- Figure 2-9 Comparison between IE2, IE3 and IE4 efficiency class motors
- Figure 2-10 - Consumption in IE2, IE3 and IE4 class motors
- Figure 2-11 - Temperature rise for IE2, IE3 & IE4 IM's classes
- Figure 3-1-Additional Negative and zero sequence losses in induction motors.
- Figure 3-2 - Flowchart of methodology used to obtain the results from the measurements.
- Figure 3-3 - Current increase for 2nd, 3rd, 5th, 7th and all harmonic order combined for induction motors
- Figure 3-4 - Total current harmonic distortion (THDI) variation for 2nd, 3rd, 5th, 7th and all harmonic order combined for induction motors
- Figure 3-5 - Reactive power increase for 2nd, 3rd, 5th, 7th and all harmonic order combined for induction motors
- Figure 3-6 - Power factor decrease for 2nd, 3rd, 5th, 7th and all harmonic order combined for induction motors
- Figure 3-7-Temperature rise in the presence of voltage harmonics of 2nd, 3rd, 5th, 7th and all harmonic order combined for induction motors
- Figure 3-8 - Thermographic images of the LSPMM in presence of 2ndvoltage harmonics in frontal and lateral view
- Figure 3-9 - Thermographic images of the LSPMM in presence of 5th voltage harmonics in frontal and lateral view
- Figure 3-10 - Correlation matrix between temperature and input parameters in IE2 class SCIM
- Figure 3-11 - Temperature regression versus motor input parameters for IE2 class SCIM
- Figure 3-12 - Correlation matrix between temperature and input parameters in IE3 class SCIM
- Figure 3-13 - Temperature regression versus motor input parameters for IE3 class SCIM
- Figure 3-14 - Correlation matrix between temperature and input parameters in IE4 class LSPMM
- Figure 3-15 - Temperature regression versus motor input parameters for IE4 class LSPMM
- Figure 3-16 Incremental Impact of Voltage distortion on Temperature
- Figure 3-17 - Temperature as a function of 2nd voltage harmonic
- Figure 3-18 - Adjusted coefficient of determination (adjusted R2) for generated models presented in Table 2.
- Figure 3-19 - Line-start permanent magnet motor simulation on FEMM
- Figure 3-20 - Density flux plot for (a) Nominal conditions; (b) 2nd voltage harmonics and (c) 5th voltage harmonics.
- Figure 3-21- Quarter section of motor illustrating the areas with convection boundary conditions.
- Figure 3-22 - Temperature distribution (in Kelvin) in the motor from the FEMM thermal simulation for
- Figure 3-23 - Comparison between the model and measured temperature for 25% voltage harmonic distortion of 2nd and 5th order harmonics.
- Figure 4-1 - Power derating curve for Induction Motors
- Figure 4-2 - The Complex Voltage Unbalance Factor Diagram [13].
- Figure 4-3 - Induction motor subjected to voltage unbalance
- Figure 4-4 - Voltage Unbalance supply on a delta-connected IM and the resulting positive
- Figure 4-5 - Induction motor voltages when subjected to voltage unbalance
- Figure 4-6 - Positive and negative sequences for impedances for IE2, IE3 and IE4 Class motors
- Figure 4-7 - Flowchart of methodology used to obtain the results from the measurements.
- Figure 4-8 - Line and average current for VU in IE4 LSPMM with
- Figure 4-9 - Average Current for under and over voltage unbalance conditions for
- Figure 4-10 - Power Factor (a-c) and Positive-Phase sequence voltage variation (d-e) with Under and Over Voltage Unbalance
- Figure 4-11 - Total power variation with Under and Over Voltage Unbalance for
- Figure 4-12 - Current Total Harmonic Distortion for under and over voltage unbalance conditions for
- Figure 4-13 - Frame Temperature with 1% under voltage
- Figure 4-14 - Frame Temperature with 1% over voltage
- Figure 4-15-Temperature increase in IE2, IE3 and IE4 class IM's with
- Figure 4-16 - Correlation matrix for IE3 Class SCIM motor parameters in the presence of VU with
- Figure 4-17 - Correlation matrix for IE4 Class LSPMM motor parameters in the presence of VU with
- Figure 4-18 - Temperature for the IE4 Class LSPMM
- Figure 4-19 - Residuals versus fitted or predicted temperature values.
- Figure 4-20 - Adjusted coefficient (Adjusted R²) for generated models presented in Table 7
- Figure 5-1 - Steps toward the implementation of energy efficiency actions on induction motor policies.
- Figure 5-2 - Methodology flowchart.
- Figure 5-3 - Speed variation for IE2, IE3 & IE4 Class motors in presence of 2nd, and combined 2nd, 3rd, 5th and 7th voltage harmonics.
- Figure 5-4 - Speed variation for IE2, IE3 & IE4 Class motors in presence of 5th and 7th voltage harmonics.
- Figure 5-5 - Harmonic currents present in IM´s with harmonic voltage distortion of
- Figure 5-6 - Speed variation for IE2, IE3 & IE4 Class motors in presence of 0%-4% Voltage Unbalance Conditions with under and over voltages;
- Figure 5-7 Fifth harmonic currents variations for phases a-b-c for the IE3 Class motor for
- Figure 5-8 - Fifth harmonic currents variations for phases a-b-c for the IE4 Class motor for
- Figure 5-9 - Seventh harmonic currents variations for phases a-b-c for the IE3 Class motor for
- Figure 5-10 - Seventh harmonic currents variations for phases a-b-c for the IE4 Class motor for
- Figure 5-11 - Phase “a” harmonic current variation for 4% Voltage unbalance with undervoltage for
- Figure 5-12 - Phase “a” harmonic current variation for 4% Voltage unbalance with overvoltage for
- Figure 6-1 - Image of Table 1 of the IEC 60038-2009 standard in relation to allowable voltages in power systems worldwide
- Figure 6-2 - Three-phase nominal voltage by region for a nominal 220 V LSPMM in a delta connection.
- Figure 6-3 - Line-start permanent magnet
- Figure 6-4 - Experimental input current as a function of load for 0.75 kW
- Figure 6-5 - Methodology flowchart.
- Figure 6-6 - Experimental input current as a function of load at different voltage magnitudes.
- Figure 6-7 - LSPMM under VV conditions
- Figure 6-8 - Experimental power factor as a function of load under VV conditions.
- Figure 6-9 - Ridgeline plot of power factor under VV conditions for the LSPMM.
- Figure 6-10 - Contour plots for power factor variation with power and load for IE4 Class motor with
- Figure 6-11 - Experimental efficiency as a function of load under VV conditions.
- Figure 6-12 - Frame temperature variation in the LSPMM under VV conditions. Frontal temperature with
- Figure 6-13 - Frame temperature variation in the LSPMM under VV conditions. Lateral temperature with
- Figure 6-14 - Measured absolute temperature under VV conditions
- Figure 6-15 - Correlation matrix between voltage magnitude and input parameters in the LSPMM for
- Figure 6-16 - Consumption as a function of voltage magnitude under different load conditions.
- Figure 6-17 - Representation of the time-of-use tariff pricing scheme considered in the economic analysis.
- Figure 6-18 - Payback for the initial cost of a new motor by changing the LSPMM voltage supply level
- Figure 7-1 - Graphical representation of the Electric Motor Degradation Index (EMDI) methodology.
- Figure 7-2-General test setup.
- Figure 7-3-Methodology Flowchart.
- Figure 7-4-EMDI calculation in dB for the nominal voltage operation condition and loading varying from 30% to 125% of nominal for
- Figure 7-5-Single phasing triggered in IE3 Class motor to evaluate the EMDI.
- Figure 7-6-EMDI calculation in dB for a single phase-loss in the IE3 Class motor.
- Figure 7-7-Input current variation as a function of load in VV conditions.
- Figure 7-8 - EMDI calculation in VV conditions for nominal load condition.
- Figure 7-9 - Pumping System at the Federal University of Pará
- Figure 7-10- Voltage magnitude variation for the electric motor input.
- Figure 7-11- Measured input line currents as a function of time.
- Figure 7-12-Electric motor diagnosis indicator comparison in VV conditions.
- Figure 10-1-IE2 Class induction motor nameplate.
- Figure 10-2 - IE2 Class induction motor parameters.
- Figure 10-3- IE3 Class induction motor nameplate.
- Figure 10-4-IE2 Class induction motor parameters.
- Figure 10-5-IE4 Class line-start permanent magnet motor nameplate.
7. Conclusion:
The results showed that the presence of voltage harmonics may result in amplification of current harmonics in electric motors for distortion percentages greater than 8% as well as in significant variations of other harmonic currents in the analyzed electric motors including negative and positive sequence harmonics, which ends up increasing the total harmonic distortion rate of the network. It was also observed how these new harmonics presented higher percentages for the higher efficiency motor analyzed (line-start permanent magnet motor).
This chapter also presented how the voltage unbalance results in an increase in the current total harmonic distortion for the three technologies, with higher percentages for the LSPMM. Finally, from the results presented, it is possible to establish some general guidelines that may be considered as recommendations:
- Replacing old/non-efficient electric motors with higher efficiency motors results in better economic benefits for the end user.
- New technologies can represent a challenge for electric utilities mainly in terms of power quality and large-scale uses.
- The study also recommends that consideration be given to oversized motors, given their prevalence in industry and the impact of oversizing on motor efficiency.
- Regulatory institutions must also observe the power quality impacts of higher efficient motors, so that manufacturers implement solutions to the challenges that the implementation of new technologies in induction motors can bring to the electric power systems.
8. References:
- [1] International Energy Agency (IEA), "Publications." Accessed: Aug. 15, 2019. [Online]. Available: https://www.iea-4e.org/publications
- [2] "Plano Nacional de Eficiência Energética - Plano Nacional de Eficiência Energética - Ministério de Minas e Energia." Accessed: Mar. 08, 2020. [Online]. Available: http://www.mme.gov.br/web/guest/secretarias/planejamento-e-desenvolvimento-energetico/publicacoes/plano-nacional-de-eficiencia-energetica
- [3] IEC 60034-30-1:2014, “Rotating electrical machines - Part 30-1: Efficiency classes of line operated AC motors (IE code)." Accessed: Aug. 15, 2019. [Online]. Available: https://webstore.iec.ch/publication/136
- [4] OFFICIAL DIARY OF THE UNION, “INTERMINISTERIAL ORDINANCE N° 1, OF 29 JUNE 2017 - National Press." Accessed: Mar. 08, 2020. [Online]. Available: http://www.in.gov.br/materia
- [5] A. Anibal, B. Rob, B. Conrad U., D. Martin, and H. William, “Motor MEPS Guide, 1st Edition Zurich Switzerland, February." 1st Edition Zurich Switzerland, Feb. 2009. Accessed: May 27, 2020. [Online]. Available: https://www.motorsystems.org/files/otherfiles/0000/0100/meps_guide_feb2009.pdf
- [6] F. J. T. E. Ferreira, B. Leprettre, and A. T. de Almeida, "Comparison of Protection Requirements in IE2-, IE3-, and IE4-Class Motors,” IEEE Transactions on Industry Applications, vol. 52, no. 4, pp. 3603-3610, Jul. 2016, doi: 10.1109/TIA.2016.2545647.
- [7] International Energy Agency (IEA), "Energy Efficiency 2018 - Analysis and outlooks to 2040 - en - OECD." Accessed: Aug. 15, 2019. [Online]. Available: http://www.oecd.org/publications/energy-efficiency-2018-9789264024304-en.htm
- [8] P. Waide and C. Brunner, “Energy-Efficiency Policy Opportunities for Electric Motor-Driven Systems," Jan. 2011.
- [9] J. Fong, F. J. T. E. Ferreira, A. M. Silva, and A. T. de Almeida, “IEC61800-9 System Standards as a Tool to Boost the Efficiency of Electric Motor Driven Systems Worldwide," Inventions, vol. 5, no. 2, Art. no. 2, Jun. 2020, doi: 10.3390/inventions5020020.
- [10] A. T. de Almeida, F. J. T. E. Ferreira, and J. Fong, "Perspectives on Electric Motor Market Transformation for a Net Zero Carbon Economy,” Energies, vol. 16, no. 3, Art. no. 3, Jan. 2023, doi: 10.3390/en16031248.
- [11] "WEG Uso Eficiente da Energía Elétrica." Accessed: Mar. 08, 2020. [Online]. Available: https://d335luupugsy2.cloudfront.net/cms/files/92176/1580492002Cartilha_Weg_versaoWE3_INTERATIVA.pdf
- [12] R. Werle, C. U. Brunner, and R. Tieben, “Swiss motor efficiency program EASY: results 2010 - 2014,” p. 14.
- [13] F. J. T. E. Ferreira and A. T. de Almeida, “Induction motor downsizing as a low-cost strategy to save energy," Journal of Cleaner Production, vol. 24, pp. 117-131, Mar. 2012, doi: 10.1016/j.jclepro.2011.11.014.
- [14] "Optimized Rewinding of Oversized Induction Motors | IEEE Conference Publication | IEEE Xplore." Accessed: Feb. 10, 2024. [Online]. Available: https://ieeexplore.ieee.org/document/10238885
- [15] ANEEL, “CALL N°. 002/2015 PRIORITY ENERGY EFFICIENCY PROJECT: ‘ENCOURAGING THE REPLACEMENT OF ELECTRIC MOTORS: PROMOTING ENERGY EFFICIENCY IN THE DRIVING POWER SEGMENT.” Accessed: Mar. 08, 2020. [Online]. Available: https://www.aneel.gov.br/sala-de-imprensa-exibicao/-/asset_publisher/XGPXSqdMFHrE/content/chamada-de-projeto-para-incentivar-substituicao-de-motores-eletricos-e-prorrogada/656877?inheritRedirect=false
- [16] "National Electric Energy Agency ANEEL." Accessed: Apr. 04, 2020. [Online]. Available: https://www.aneel.gov.br/
- [17] A. T. D. Almeida, F. J. T. E. Ferreira, and A. Quintino, "Technical and economical considerations on super high-efficiency three-phase motors,” in 48th IEEE Industrial Commercial Power Systems Conference, May 2012, pp. 1–13. doi: 10.1109/ICPS.2012.6229618.
- [18] WEG, "See+." Accessed: Mar. 08, 2020. [Online]. Available: https://www.weg.net/see+/pages/regua.jsp
- [19] H. Abusaada and A. Elshater, “Notes on Developing Research Review in Urban Planning and Urban Design Based on PRISMA Statement,” Social Sciences, vol. 11, no. 9, Art. no. 9, Sep. 2022, doi: 10.3390/socsci11090391.
- [20] D. Moher, A. Liberati, J. Tetzlaff, and D. G. Altman, “Preferred reporting items for systematic reviews and meta-analyses: the PRISMA statement," BMJ, vol. 339, p. b2535, Jul. 2009, doi: 10.1136/bmj.b2535.
- [21] U.S. Department of Energy, Energy Efficiency & Renewable Energy, "Premium Efficiency Motor Selection and Application Guide – A Handbook for Industry," Energy.gov. Accessed: Aug. 15, 2019. [Online]. Available: https://www.energy.gov/eere/amo/downloads/premium-efficiency-motor-selection-and-application-guide-handbook-industry
- [22] F. J. T. E. Ferreira, G. Baoming, and A. T. de Almeida, "Reliability and Operation of High-Efficiency Induction Motors,” IEEE Transactions on Industry Applications, vol. 52, no. 6, pp. 4628-4637, Nov. 2016, doi: 10.1109/TIA.2016.2600677.
- [23] A. Hassanpour Isfahani and S. Vaez-Zadeh, "Line start permanent magnet synchronous motors: Challenges and opportunities,” Energy, vol. 34, no. 11, pp. 1755–1763, Nov. 2009, doi: 10.1016/j.energy.2009.04.022.
- [24] M. G. Kahrisangi, A. H. Isfahani, S. Vaez-Zadeh, and M. R. Sebdani, "Line-start permanent magnet synchronous motors versus induction motors: A comparative study," Front. Electr. Electron. Eng., vol. 7, no. 4, pp. 459-466, Dec. 2012, doi: 10.1007/s11460-012-0217-8.
- [25] A. T. de Almeida, F. J. T. E. Ferreira, and G. Baoming, "Beyond Induction Motors—Technology Trends to Move Up Efficiency,” IEEE Transactions on Industry Applications, vol. 50, no. 3, pp. 2103–2114, May 2014, doi: 10.1109/TIA.2013.2288425.
- [26] F. J. T. E. Ferreira, A. M. Silva, V. P. B. Aguiar, R. S. T. Pontes, E. C. Quispe, and A. T. de Almeida, "Overview of Retrofitting Options in Induction Motors to Improve Their Efficiency and Reliability," in 2018 IEEE International Conference on Environment and Electrical Engineering and 2018 IEEE Industrial and Commercial Power Systems Europe (EEEIC/ICPS Europe), Jun. 2018, pp. 1-12. doi: 10.1109/EEEIC.2018.8493887.
- [27] M. GWOŹDZIEWICZ and L. ANTAL, “INVESTIGATION OF LINE START PERMANENT MAGNET SYNCHRONOUS MOTOR AND INDUCTION MOTOR PROPERTIES, Prace Naukowe Instytutu Maszyn, Napędów i Pomiarów Elektrycznych, Politechniki Wrocławskiej." Prace Naukowe Instytutu Maszyn, Napędów i Pomiarów Elektrycznych, Politechniki Wrocławskiej., 2010. [Online]. Available: https://pdfs.semanticscholar.org/e9ce/18be7c97cf70342b3135d9cd8364e14538bb.pdf
- [28] C. Debruyne, S. Derammelaere, J. Desmet, and L. Vandevelde, “Comparative study of the influence of harmonic voltage distortion on the efficiency of induction machines versus line start permanent magnet machines,” in 2012 IEEE 15th International Conference on Harmonics and Quality of Power, Hong Kong, China: IEEE, Jun. 2012, pp. 342-349. doi: 10.1109/ICHQP.2012.6381217.
- [29] V. P. B. Aguiar, R. S. T. Pontes, and F. J. T. E. Ferreira, “Technical and Economic Evaluation of Efficiency Improvement after Rewinding in Low-Power Induction Motors: A Brazilian Case," Energies, vol. 11, no. 7, Art. no. 7, Jul. 2018, doi: 10.3390/en11071701.
- [30] H. Kim, Y. Park, H.-C. Liu, P.-W. Han, and J. Lee, “Study on Line-Start Permanent Magnet Assistance Synchronous Reluctance Motor for Improving Efficiency and Power Factor,” Energies, vol. 13, no. 2, Art. no. 2, Jan. 2020, doi: 10.3390/en13020384.
- [31] C. Debruyne, “Impact of voltage distortion on energy efficiency of induction machines and line start permanent magnet machines,” dissertation, Ghent University, 2014. Accessed: Aug. 15, 2019. [Online]. Available: http://hdl.handle.net/1854/LU-4383637
- [32] İ. Tarımer, “Investigation of the Effects of Rotor Pole Geometry and Permanent,” 1, vol. 90, no. 2, pp. 67-72, 2009, doi: 10.5755/j01.eee.90.2.10512.
- [33] T. J. E. Miller, "Synchronization of Line-Start Permanent-Magnet AC Motors,” IEEE Transactions on Power Apparatus and Systems, vol. PAS-103, no. 7, pp. 1822-1828, Jul. 1984, doi: 10.1109/TPAS.1984.318630.
- [34] A. Chama, A. Sorgdrager, and R.-J. Wang, “Analytical synchronization analysis of line-start permanent magnet synchronous motors,” Progress In Electromagnetics Research M, vol. 48, pp. 183-193, Jun. 2016, doi: 10.2528/PIERM16050311.
- [35] "Design and Analysis of a Hybrid Permanent Magnet Assisted Synchronous Reluctance Motor Considering Magnetic Saliency and PM Usage - IEEE Journals & Magazine." Accessed: May 16, 2020. [Online]. Available: https://ieeexplore.ieee.org/document/8115172
- [36] M. J. Melfi, S. D. Rogers, S. Evon, and B. Martin, “Permanent Magnet Motors for Energy Savings in Industrial Applications," in 2006 Record of Conference Papers - IEEE Industry Applications Society 53rd Annual Petroleum and Chemical Industry Conference, Sep. 2006, pp. 1-8. doi: 10.1109/PCICON.2006.359695.
- [37] A. Takahashi, S. Kikuchi, K. Miyata, and A. Binder, “Asynchronous Torque of Line-Starting Permanent-Magnet Synchronous Motors,” IEEE Transactions on Energy Conversion, vol. 30, no. 2, pp. 498-506, Jun. 2015, doi: 10.1109/TEC.2014.2361836.
- [38] C. Vavra, “Understanding permanent magnet motors," Control Engineering.
- [39] A. T. de Almeida, J. Fong, H. Falkner, and P. Bertoldi, “Policy options to promote energy efficient electric motors and drives in the EU," Renewable and Sustainable Energy Reviews, vol. 74, pp. 1275-1286, Jul. 2017, doi: 10.1016/j.rser.2017.01.112.
- [40] A. De Almeida, J. Fong, C. U. Brunner, R. Werle, and M. Van Werkhoven, “New technology trends and policy needs in energy efficient motor systems - A major opportunity for energy and carbon savings," Renewable and Sustainable Energy Reviews, vol. 115, p. 109384, Nov. 2019, doi: 10.1016/j.rser.2019.109384.
- [41] F. J. T. E. Ferreira and A. T. de Almeida, “Induction motor downsizing as a low-cost strategy to save energy," Journal of Cleaner Production, vol. 24, pp. 117-131, Mar. 2012, doi: 10.1016/j.jclepro.2011.11.014.
- [42] "Minimum Energy Performance Standards (MEPS) – Policies," IEA. Accessed: Jul. 26, 2020. [Online]. Available: https://www.iea.org/policies/333-minimum-energy-performance-standards-meps
- [43] "IEC 60034-7:2020 | IEC Webstore." Accessed: Feb. 11, 2024. [Online]. Available: https://webstore.iec.ch/publication/64225
- [44] S. Singh and A. Singh, "Steady-state Performance Assessment of Induction Motor under Unbalanced Voltage Condition,” Electric Power Components and Systems, vol. 41, Oct. 2013, doi: 10.1080/15325008.2013.817492.
- [45] D. Zhang, R. An, and T. Wu, “Effect of Voltage Unbalance and Distortion on the Loss Characteristics of Three Phase Cage Induction Motor,” IET Electric Power Applications, vol. 12, Oct. 2017, doi: 10.1049/iet-epa.2017.0464.
- [46] A. B. F. Neves, M. V. B. de Mendonça, A. de L. Ferreira Filho, and G. Z. Rosa, "Effects of voltage unbalance and harmonic distortion on the torque and efficiency of a Three-Phase Induction Motor," in 2016 17th International Conference on Harmonics and Quality of Power (ICHQP), Oct. 2016, pp. 943-948. doi: 10.1109/ICHQP.2016.7783350.
- [47] W. Abu-Elhaija and A. Muetze, “A voltage unbalance factor coding technique for three-phase induction motors,” International Transactions on Electrical Energy Systems, vol. 28, no. 6, p. e2554, 2018, doi: 10.1002/etep.2554.
- [48] E. Quispe, “Efectos del desequilibrio de tensiones sobre la operación del motor de inducción trifásico. Énfasis en la caracterización del desequilibrio de tensiones y el efecto sobre la potencia nominal," 2012. doi: 10.13140/RG.2.1.3406.7287.
- [49] NEMA MG1-2016, “Motors and Generators." Accessed: Aug. 15, 2019. [Online]. Available: https://www.nema.org/Standards/Pages/Motors-and-Generators.aspx
- [50] "IEEE Recommended Practice for Monitoring Electric Power Quality,” IEEE Std 1159-2019 (Revision of IEEE Std 1159-2009), pp. 1–98, Aug. 2019, doi: 10.1109/IEEESTD.2019.8796486.
- [51] "Power Quality Indices and Objectives,” e-cigre. Accessed: Apr. 04, 2020. [Online]. Available: https://e-cigre.org/publication/261-power-quality-indices-and-objectives
- [52] Ching-Yin Lee, “Effects of unbalanced voltage on the operation performance of a three-phase induction motor,” IEEE Transactions on Energy Conversion, vol. 14, no. 2, pp. 202-208, Jun. 1999, doi: 10.1109/60.766984.
- [53] M. Kostic, "Effects of Voltage Quality on Induction Motors' Efficient Energy Usage," Induction Motors - Modelling and Control, Nov. 2012, doi: 10.5772/51223.
- [54] P. Gnaciński, “Gnacinski P. Thermal loss of life and load-carrying capacity of marine induction motors. Energy Conversion and Management, vol. 78: 574-583, Febr. 2014,” Energy Conversion and Management, vol. 78, pp. 574-583, Feb. 2014, doi: 10.1016/j.enconman.2013.11.023.
- [55] A. H. Bonnett, "The impact that voltage and frequency variations have on AC induction motor performance and life in accordance with NEMA MG-1 standards," in Conference Record of 1999 Annual Pulp and Paper Industry Technical Conference (Cat. No.99CH36338), Seattle, WA, USA: IEEE, 1999, pp. 16-26. doi: 10.1109/PAPCON.1999.779341.
- [56] Yaw-Juen Wang, “Analysis of effects of three-phase voltage unbalance on induction motors with emphasis on the angle of the complex voltage unbalance factor,” IEEE Transactions on Energy Conversion, vol. 16, no. 3, pp. 270-275, Sep. 2001, doi: 10.1109/60.937207.
- [57] E. El-Kharashi, M. El-Dessouki, J. G. Massoud, A. W. Farid, and M. A. Al-Ahmar, "The use of the current complex factor to determine the precise output energy of the induction motor," Electric Power Systems Research, vol. 154, pp. 23–36, Jan. 2018, doi: 10.1016/j.epsr.2017.08.008.
- [58] A. L. Ferreira Filho, J. A. A. Cormane, D. C. Garcia, M. V. C. Costa, M. A. G. Oliveira, and F. A. do Nascimento, "Analysis of the complex voltage unbalance factor behavior resulting from the variation of voltage magnitudes and angles,” in Proceedings of 14th International Conference on Harmonics and Quality of Power ICHQP 2010, Sep. 2010, pp. 1–7. doi: 10.1109/ICHQP.2010.5625315.
- [59] A. I. Adekitan, "A New Definition of Voltage Unbalance Using Supply Phase Shift,” J Control Autom Electr Syst, vol. 31, no. 3, pp. 718-725, Jun. 2020, doi: 10.1007/s40313-020-00579-8.
- [60] M. T. Jonathan, E. Ortiz de Matos, T. M. Soares, M. E. de L. Tostes, and J. C. Paye, "Fifth & Seventh Harmonic Effects on the Performance of IE2, IE3 & IE4 Induction Motor Classes,” in Proceedings of the 13th Latin-American Congress on Electricity Generation and Transmission - CLAGTEE 2019, Santiago, Chile, Oct. 2019, p. 6. [Online]. Available: http://www.clagtee2019.pucv.cl/2019/book.html
- [61] M. T. Jonathan, T. M. Soares, M. E. de L. Tostes, E. Ortiz de Matos, and C. E. Moreira, "Impactos do 50 Harmônico na Temperatura de Motores Elétricos Classes IE2, IE3 e IE4.," in Conferência Brasileira sobre Qualidade da Energia Elétrica (CBQEE), São Paulo, Brazil, Sep. 2019, p. 6. [Online]. Available: http://sbqee.org.br/cbqee/
- [62] A. T. de Almeida, F. J. T. E. Ferreira, and J. A. C. Fong, “Standards for Super-Premium Efficiency class for electric motors," in Conference Record 2009 IEEE Industrial Commercial Power Systems Technical Conference, May 2009, pp. 1–8. doi: 10.1109/ICPS.2009.5463983.
- [63] C. Debruyne, L. Vandevelde, and J. Desmet, “Harmonic effects on Induction and Line Start Permanent Magnet Machines,” in International Conference on Energy Efficiency in Motor Driven Systems (EEMODS 2013), Rio de Janeiro, RJ, Brazil, Oct. 2013.
- [64] T. Zawilak and J. Zawilak, “MINIMIZATION OF HIGHER HARMONICS IN LINE-START PERMANENT MAGNET SYNCHRONOUS MOTOR,” Przeglad Elektrotechniczny, vol. 84, Jan. 2008.
- [65] E. Vera, “Optimal design of line-start permanent magnet synchronous motors of high efficiency. Electric power. Ecole Centrale de Lille, 2015. English. NNT: 2015ECLI0022. tel-01308575," 2015.
- [66] F. Ferreira, M. V. Cistelecan, and A. de Almeida, "Voltage Unbalance Impact on the Performance of Line-Start Permanent-Magnet Synchronous Motors.," Nantes, France, 2009.
- [67] F. Kalluf, C. Pompermaier, M. V. F. da Luz, and N. Sadowski, “Braking torque analysis of the single phase line-start permanent magnet synchronous motor," The XIX International Conference on Electrical Machines - ICEM 2010, 2010, doi: 10.1109/ICELMACH.2010.5608211.
- [68] A. Kumar and A. Srivastava, "Performance Comparison of Two Different Rotor Topologies of Line Start Permanent Magnet Synchronous Motors,” Engineering Technology, vol. 5, p. 8.
- [69] Mingji Liu, Zhi Han, Yawei Pei, and Pengfei Shi, “Optimization of permanent magnet motor air-gap flux density based on the non-uniform air gap,” in Proceedings 2013 International Conference on Mechatronic Sciences, Electric Engineering and Computer (MEC), Dec. 2013, pp. 3422-3426. doi: 10.1109/MEC.2013.6885604.
- [70] A. Sorgdrager, R.-J. Wang, and A. J. Grobler, “Transient performance optimisation of line-start permanent magnet synchronous motors using Taguchi regression rate method," Jan. 2017.
- [71] X. Zeng, L. Quan, X. Zhu, L. Xu, and F. Liu, "Investigation of an Asymmetrical Rotor Hybrid Permanent Magnet Motor for Approaching Maximum Output Torque,” IEEE Transactions on Applied Superconductivity, vol. 29, no. 2, pp. 1–4, Mar. 2019, doi: 10.1109/TASC.2019.2893708.
- [72] F. J. T. E. Ferreira, J. Alberto, and A. T. de Almeida, "Voltage Unbalance Impact on Coil-Side Temperature Rise in a Delta-Connected, Dual-Winding Induction Motor,” in 2020 IEEE International Conference on Industrial Technology (ICIT), Feb. 2020, pp. 925-930. doi: 10.1109/ICIT45562.2020.9067201.
- [73] "IEEE Recommended Practice for Monitoring Electric Power Quality,” IEEE Std 1159-1995, pp. i-, 1995, doi: 10.1109/IEEESTD.1995.79050.
- [74] E. C. de Lima, J. M. de C. Filho, and J. S. de Sá, “Diagnosis of induction motors operating under distorted and unbalanced voltages," in 2016 17th International Conference on Harmonics and Quality of Power (ICHQP), Oct. 2016, pp. 786-791. doi: 10.1109/ICHQP.2016.7783368.
- [75] E. F. Fuchs, D. J. Roesler, and M. A. S. Masoum, “Are harmonic recommendations according to IEEE and IEC too restrictive?," IEEE Transactions on Power Delivery, vol. 19, no. 4, pp. 1775-1786, Oct. 2004, doi: 10.1109/TPWRD.2003.822538.
- [76] A. Munoz R. and G. Nahmias C., “Mechanical vibration of three-phase induction motors fed by nonsinusoidal currents," in 3rd International Power Electronic Congress. Technical Proceedings. CIEP '94, Aug. 1994, pp. 166–172. doi: 10.1109/CIEP.1994.494416.
- [77] X. Song, J. Hu, H. Zhu, and J. Zhang, “Effects of the Slot Harmonics on the Stator Current in an Induction Motor with Bearing Fault,” Mathematical Problems in Engineering. Accessed: Jun. 16, 2020. [Online]. Available: https://www.hindawi.com/journals/mpe/2017/2640796/
- [78] "Static air-gap eccentricity fault diagnosis using rotor slot harmonics in line neutral voltage of three-phase squirrel cage induction motor,” ResearchGate. Accessed: Jun. 15, 2020. [Online]. Available: https://www.researchgate.net/publication/306417959_Static_air-gap_eccentricity_fault_diagnosis_using_rotor_slot_harmonics_in_line_neutral_voltage_of_three-phase_squirrel_cage_induction_motor
- [79] M. Kordestani, A. A. Safavi, and M. Saif, "Harmonic Fault Diagnosis in Power Quality System Using Harmonic Wavelet," Jul. 2017. doi: 10.1016/j.ifacol.2017.08.2370.
- [80] "Fault diagnosis and condition monitoring of electrical machines - A Review | Request PDF," ResearchGate. Accessed: Jun. 16, 2020. [Online]. Available: https://www.researchgate.net/publication/224713187_Fault_diagnosis_and_condition_monitoring_of_electrical_machines_-_A_Review
- [81] W. Li and C. Mechefske, "Induction motor fault detection using vibration and stator current methods," Insight - Non-Destructive Testing and Condition Monitoring, vol. 46, pp. 473–478, Aug. 2004, doi: 10.1784/insi.46.8.473.39379.
- [82] IEC 60034-7:1992, ““Classification of types of constructions and mounting arrangements (IM Code))." Accessed: Aug. 15, 2019. [Online]. Available: https://webstore.iec.ch/publication/145
- [83] L. Aarniovuori, M. Niemelä, J. Pyrhönen, W. Cao, and E. B. Agamloh, “Loss Components and Performance of Modern Induction Motors," in 2018 XIII International Conference on Electrical Machines (ICEM), Sep. 2018, pp. 1253-1259. doi: 10.1109/ICELMACH.2018.8507189.
- [84] H. O. Mirzamani and A. L. Choobari, "Study of harmonics effects on performance of induction motors," in Proceedings of the 4th WSEAS international conference on Applications of electrical engineering, in AEE'05. Prague, Czech Republic: World Scientific and Engineering Academy and Society (WSEAS), Mar. 2005, pp. 389–394.
- [85] H. G. Beleiu, V. Maier, S. G. Pavel, I. Birou, C. S. Pică, and P. C. Dărab, “Harmonics Consequences on Drive Systems with Induction Motor," Applied Sciences, vol. 10, no. 4, Art. no. 4, Jan. 2020, doi: 10.3390/app10041528.
- [86] C. Debruyne, J. Desmet, S. Derammelaere, and L. Vandevelde, "Derating factors for direct online induction machines when supplied with voltage harmonics: A critical view," in 2011 IEEE International Electric Machines Drives Conference (IEMDC), May 2011, pp. 1048–1052. doi: 10.1109/IEMDC.2011.5994745.
- [87] S. X. Duarte and N. Kagan, “A Power-Quality Index to Assess the Impact of Voltage Harmonic Distortions and Unbalance to Three-Phase Induction Motors,” IEEE Transactions on Power Delivery, vol. 25, no. 3, pp. 1846–1854, Jul. 2010, doi: 10.1109/TPWRD.2010.2044665.
- [88] H. O. Mirzamani and A. L. Choobari, “Study of harmonics effects on performance of induction motors," 2005.
- [89] "519-2014 - IEEE Recommended Practice and Requirements for Harmonic Control in Electric Power Systems." Accessed: May 15, 2020. [Online]. Available: https://standards.ieee.org/standard/519-2014.html
- [90] M. Kordestani, M. Saif, M. E. Orchard, R. Razavi-Far, and K. Khorasani, “Failure Prognosis and Applications—A Survey of Recent Literature,” IEEE Transactions on Reliability, pp. 1–21, 2019, doi: 10.1109/TR.2019.2930195.
- [91] S. M. K. Zaman and X. Liang, “An Effective Induction Motor Fault Diagnosis Approach Using Graph-Based Semi-Supervised Learning," IEEE Access, vol. 9, pp. 7471-7482, 2021, doi: 10.1109/ACCESS.2021.3049193.
- [92] F. J. T. E. Ferreira, A. T. de Almeida, J. F. S. Carvalho, and M. V. Cistelecan, "Experiments to observe the impact of power quality and voltage-source inverters on the temperature of three-phase cage induction motors using an infra-red camera," in 2009 IEEE International Electric Machines and Drives Conference, May 2009, pp. 1311–1318. doi: 10.1109/IEMDC.2009.5075373.
- [93] J. T. Allan, "The effect of voltage variation on the operation of induction motors,” Transactions of the South African Institute of Electrical Engineers, vol. 20, no. 6, pp. 137–155, Jun. 1929.
- [94] "Power savings obtained from supply voltage variation on squirrel cage induction motors | IEEE Conference Publication | IEEE Xplore." Accessed: Apr. 19, 2023. [Online]. Available: https://ieeexplore.ieee.org/document/4763392
- [95] "Investigation of voltage and frequency variation on induction motor core and copper losses | IEEE Conference Publication | IEEE Xplore." Accessed: Apr. 19, 2023. [Online]. Available: https://ieeexplore.ieee.org/document/7934894
- [96] E. B. Agamloh, S. Peele, and J. Grappe, "A comparative analysis of voltage magnitude deviation and unbalance on standard and premium efficient induction motors,” in Conference Record of 2012 Annual IEEE Pulp and Paper Industry Technical Conference (PPIC), Jun. 2012, pp. 1–8. doi: 10.1109/PPIC.2012.6293004.
- [97] "The impact that voltage and frequency variations have on AC induction motor performance and life in accordance with NEMA MG-1 standards." Accessed: Sep. 15, 2022. [Online]. Available: https://ieeexplore.ieee.org/document/779341
- [98] A. H. Bonnett, "The impact that voltage and frequency variations have on AC induction motor performance and life in accordance with NEMA MG-1 standards," in Conference Record of 1999 Annual Pulp and Paper Industry Technical Conference (Cat. No.99CH36338), Jun. 1999, pp. 16-26. doi: 10.1109/PAPCON.1999.779341.
- [99] N. Mendes et al., “ANN for Motor Loading Diagnosis under Voltage Variation Conditions,” in 2023 IEEE Kansas Power and Energy Conference (KPEC), Apr. 2023, pp. 1-6. doi: 10.1109/ΚΡEC58008.2023.10215414.
- [100] J. M. Tabora, L. C. D. S. Júnior, M. E. de L. Tostes, E. O. de Matos, and U. H. Bezerra, "Efficient Electric Motors Performance Under Voltage Variation Conditions,” in 2023 IEEE Kansas Power and Energy Conference (KPEC), Apr. 2023, pp. 1–6. doi: 10.1109/ΚΡEC58008.2023.10215475.
- [101] M. Kostic, M. Ivanovic, and S. Minic, “Reduction of electric energy consumption in induction motor drives by setting supply voltage," in 2012 2nd International Symposium On Environment Friendly Energies And Applications, Jun. 2012, pp. 128-133. doi: 10.1109/EFEA.2012.6294073.
- [102] K. Zhao, L. Cheng, C. Zhang, D. Nie, and W. Cai, “Induction motors lifetime expectancy analysis subject to regular voltage fluctuations," in 2017 IEEE Electrical Power and Energy Conference (EPEC), Oct. 2017, pp. 1–6. doi: 10.1109/EPEC.2017.8286230.
- [103] W. Wang and Z. Lu, “Analysis of Model Predictive Current-Controlled Permanent Magnet Synchronous Motor Drives with Inaccurate DC Bus Voltage Measurement," Energies, vol. 13, no. 2, Art. no. 2, Jan. 2020, doi: 10.3390/en13020353.
- [104] H.-J. Lee and J.-G. Shon, “Improved Voltage Flux-Weakening Strategy of Permanent Magnet Synchronous Motor in High-Speed Operation," Energies, vol. 14, no. 22, Art. no. 22, Jan. 2021, doi: 10.3390/en14227464.
- [105] A. Sikora, A. Zielonka, and M. Woźniak, “Minimization of Energy Losses in the BLDC Motor for Improved Control and Power Supply of the System under Static Load," Sensors, vol. 22, no. 3, Art. no. 3, Jan. 2022, doi: 10.3390/s22031058.
- [106] A. Sikora and M. Woźniak, “Impact of Current Pulsation on BLDC Motor Parameters,” Sensors, vol. 21, no. 2, Art. no. 2, Jan. 2021, doi: 10.3390/s21020587.
- [107] "World Energy Outlook 2019 - Analysis," IEA. Accessed: Jun. 10, 2022. [Online]. Available: https://www.iea.org/reports/world-energy-outlook-2019
- [108] D. F. de Souza, F. A. M. Salotti, I. L. Sauer, H. Tatizawa, A. T. de Almeida, and A. G. Kanashiro, “An assessment of the impact of Brazilian energy efficiency policies for electric motors,” Energy Nexus, vol. 5, p. 100033, Mar. 2022, doi: 10.1016/j.nexus.2021.100033.
- [109] J. M. Tabora et al., “Virtual Modeling and Experimental Validation of the Line-Start Permanent Magnet Motor in the Presence of Harmonics," Energies, vol. 15, no. 22, Art. no. 22, Jan. 2022, doi: 10.3390/en15228603.
- [110] F. J. T. E. Ferreira, G. Baoming, and A. T. de Almeida, “Stator Winding Connection-Mode Management in Line-Start Permanent Magnet Motors to Improve Their Efficiency and Power Factor,” IEEE Transactions on Energy Conversion, vol. 28, no. 3, pp. 523-534, Sep. 2013, doi: 10.1109/TEC.2013.2270084.
- [111] J. M. Tabora, M. E. de Lima Tostes, E. O. de Matos, and U. H. Bezerra, "Voltage Unbalance amp; Variations Impacts on IE4 Class LSPMM," in 2021 14th IEEE International Conference on Industry Applications (INDUSCON), Aug. 2021, pp. 940-946. doi: 10.1109/INDUSCON51756.2021.9529505.
- [112] J. M. Tabora, F. V. Vieira Bezerra, T. M. Soares, E. Ortiz de Matos, M. E. de Lima Tostes, and U. Holanda Bezerra, "Electric Motor Degradation Indicator in Non-Ideal Supply Conditions," in 2023 IEEE Workshop on Power Electronics and Power Quality Applications (PEPQA), Oct. 2023, pp. 1–5. doi: 10.1109/PEPQA59611.2023.10325777.
- [113] D. López-Pérez and J. Antonino-Daviu, “Application of Infrared Thermography to Failure Detection in Industrial Induction Motors: Case Stories,” IEEE Transactions on Industry Applications, vol. 53, no. 3, pp. 1901–1908, May 2017, doi: 10.1109/TIA.2017.2655008.
- [114] A. Mahami, C. Rahmoune, T. Bettahar, and D. Benazzouz, "Induction motor condition monitoring using infrared thermography imaging and ensemble learning techniques,” Advances in Mechanical Engineering, vol. 13, no. 11, p. 16878140211060956, Nov. 2021, doi: 10.1177/16878140211060956.
- [115] M. Manana, A. Arroyo, A. Ortiz, C. J. Renedo, S. Perez, and F. Delgado, “Field winding fault diagnosis in DC motors during manufacturing using thermal monitoring,” Applied Thermal Engineering, vol. 31, no. 5, pp. 978–983, Apr. 2011, doi: 10.1016/j.applthermaleng.2010.11.023.
- [116] G. Singh, T. C. Anil Kumar, and V. N. A. Naikan, “Fault diagnosis of induction motor cooling system using infrared thermography,” in 2016 IEEE 6th International Conference on Power Systems (ICPS), Mar. 2016, pp. 1–4. doi: 10.1109/ICPES.2016.7584040.
- [117] M. Ghods, J. Faiz, A. A. Pourmoosa, and S. Khosrogorji, “Analytical Evaluation of Core Losses, Thermal Modelling and Insulation Lifespan Prediction for Induction Motor in Presence of Harmonic and Voltage Unbalance," International Journal of Engineering, vol. 34, no. 5, pp. 1213–1224, May 2021, doi: 10.5829/ije.2021.34.05b.14.
- [118] J. M. Tabora, M. E. De Lima Tostes, E. O. De Matos, U. H. Bezerra, T. M. Soares, and B. S. De Albuquerque, “Assessing Voltage Unbalance Conditions in IE2, IE3 and IE4 Classes Induction Motors," IEEE Access, vol. 8, pp. 186725–186739, 2020, doi: 10.1109/ACCESS.2020.3029794.
- [119] J. Muñoz Tabora, M. E. de Lima Tostes, E. Ortiz de Matos, T. Mota Soares, and U. H. Bezerra, "Voltage Harmonic Impacts on Electric Motors: A Comparison between IE2, IE3 and IE4 Induction Motor Classes," Energies, vol. 13, no. 13, Art. no. 13, Jan. 2020, doi: 10.3390/en13133333.
- [120] W. R. Finley, M. M. Howdowanec, and W. G. Holter, "Diagnosing motor vibration problems," in Conference Record of 2000 Annual Pulp and Paper Industry Technical Conference (Cat. No.00CH37111), Jun. 2000, pp. 165-180. doi: 10.1109/PAPCON.2000.854217.
- [121] V. Climente-Alarcon, J. A. Antonino-Daviu, F. Vedreño-Santos, and R. Puche-Panadero, "Vibration Transient Detection of Broken Rotor Bars by PSH Sidebands,” IEEE Transactions on Industry Applications, vol. 49, no. 6, pp. 2576–2582, Nov. 2013, doi: 10.1109/TIA.2013.2265872.
- [122] I. Ibrahim, R. Silva, M. H. Mohammadi, V. Ghorbanian, and D. A. Lowther, “Surrogate-Based Acoustic Noise Prediction of Electric Motors,” IEEE Transactions on Magnetics, vol. 56, no. 2, pp. 1-4, Feb. 2020, doi: 10.1109/TMAG.2019.2945407.
- [123] S. Sathyan, U. Aydin, and A. Belahcen, “Acoustic Noise Computation of Electrical Motors Using the Boundary Element Method," Energies, vol. 13, no. 1, Art. no. 1, Jan. 2020, doi: 10.3390/en13010245.
- [124] M. Liu, K. W. han, J. Hu, W. Xu, and J. Rodriguez, “Model Predictive irect Speed ontrol With Torque Oscillation Reduction for PMSM rives,” IEEE Transactions on Industrial Informatics, vol. 15, no. 9, pp. 4944–4956, Sep. 2019, doi: 10.1109/TII.2019.2898004.
- [125] . Saito, M. Kuroishi, and H. Nakai, “Vibration Prediction Method of Electric Machines by using Experimental Transfer Function and Magnetostatic Finite Element nalysis,” J. Phys.: Conf. Ser., vol. 744, p. 012088, Sep. 2016, doi: 10.1088/1742-6596/744/1/012088.
- [126] G. . Stone, M. K. W. Stranges, and . G. unn, “ ommon Questions on Partial ischarge Testing: A Review of Recent Developments in IEEE and IEC Standards for Offline and Online Testing of Motor and Generator Stator Windings,” IEEE Industry Applications Magazine, vol. 22, no. 1, pp. 14–19, Jan. 2016, doi: 10.1109/MIAS.2015.2458337.
- [127] G. . Stone, H. G. Sedding, and . han, “Experience With Online Partial-Discharge Measurement in High-Voltage Inverter-Fed Motors,” IEEE Transactions on Industry Applications, vol. 54, no. 1, pp. 866–872, Jan. 2018, doi: 10.1109/TIA.2017.2740280.
- [128] B. Hu et al., “ Partial ischarge Study of Medium-Voltage Motor Winding Insulation Under woLevel Voltage Pulses With High v/ t,” IEEE Open Journal of Power Electronics, vol. 2, pp. 225–235, 2021, doi: 10.1109/OJPEL.2021.3069780.
- [129] I. Zamudio-Ramirez, R. A. Osornio-Rios, J. A. Antonino-Daviu, H. Razik, and R. de J. omeroTroncoso, “Magnetic Flux nalysis for the ondition Monitoring of Electric Machines: Review,” IEEE Transactions on Industrial Informatics, vol. 18, no. 5, pp. 2895–2908, May 2022, doi:10.1109/TII.2021.3070581.
- [130] E. L. Bonaldi, L. E. de L. de Oliveira, J. G. B. da Silva, G. Lambert-Torresm, and L. E. B. da Silva, Predictive Maintenance by Electrical Signature Analysis to Induction Motors. IntechOpen, 2012. doi:10.5772/48045.
- [131] J. Antonino- aviu, “Electrical Monitoring under Transient onditions: New Paradigm in Electric Motors Predictive Maintenance,” Applied Sciences, vol. 10, no. 17, Art. no. 17, Jan. 2020, doi:10.3390/app10176137.
- [132] . houdhary, . Goyal, S. L. Shimi, and . kula, “ ondition Monitoring and Fault iagnosis of Induction Motors: Review,” Arch Computat Methods Eng, vol. 26, no. 4, pp. 1221–1238, Sep. 2019, doi: 10.1007/s11831-018-9286-z.
- [133] T. Ince, S. Kiranyaz, L. Eren, M. skar, and M. Gabbou , “Real-Time Motor Fault Detection by 1-D onvolutional Neural Networks,” IEEE Transactions on Industrial Electronics, vol. 63, no. 11, pp. 7067–7075, Nov. 2016, doi: 10.1109/TIE.2016.2582729.
- [134] B. G. Joung, W. J. Lee, . Huang, and J. W. Sutherland, “ evelopment and pplication of a Method for Real Time Motor Fault etection,” Procedia Manufacturing, vol. 49, pp. 94–98, Jan. 2020, doi:10.1016/j.promfg.2020.07.002.
- [135] M. Şimşir, R. Bayır, and Y. Uyaroğlu, “Real-Time Monitoring and Fault Diagnosis of a Low Power Hub Motor Using Feedforward Neural Network,” Computational Intelligence and Neuroscience, vol. 2016, p. e7129376, Dec. 2015, doi: 10.1155/2016/7129376.
- [136] H. Zhang, B. Ge, and B. Han, “Real-Time Motor Fault iagnosis Based on T N and ttention,” Machines, vol. 10, no. 4, Art. no. 4, Apr. 2022, doi: 10.3390/machines10040249.
9. Copyright:
- This material is a paper by "JONATHAN MUÑOZ TABORA". Based on "EXPERIMENTAL EVALUATION, DIAGNOSIS, AND PREDICTION OF THE IMPACTS OF POWER QUALITY DISTURBANCES IN IE2, IE3, AND IE4 CLASS EFFICIENCY MOTORS.".
- Source of the paper: [N/A]
This material is summarized based on the above paper, and unauthorized use for commercial purposes is prohibited.
Copyright © 2025 CASTMAN. All rights reserved.