This article introduces the paper "Experimental and Theoretical Studies on the Effect of Die Temperature on the Quality of the Products in High-Pressure Die-Casting Process."
1. Overview:
- Title: Experimental and Theoretical Studies on the Effect of Die Temperature on the Quality of the Products in High-Pressure Die-Casting Process
- Authors: Mohammad Sadeghi, Jafar Mahmoudi
- Year: 2012
- Published in: Advances in Materials Science and Engineering
- Keywords:
- Die temperature
- High-pressure die-casting (HPDC)
- A380 alloy
- Numerical simulation
- Experimental observation
- ProCAST software
- Ladder frame
2. Research Background:
- Social/Academic Context:
- High-pressure die-casting (HPDC) process has been widely used to manufacture a large variety of products with high dimensional accuracy and productivities.
- It has a much faster production rate in comparison to other methods and it is an economical and efficient method for producing components with low surface roughness and high-dimensional accuracy.
- All major aluminum automotive components can be processed with this technology [1-7].
- Although HPDC has a considerably higher speed than other metal forming processes, due to complexity of the process and the number of variables, optimization of the process is essential.
- In particular, there are issues related to control of:
- Die temperature
- Solidification of the components
- Quality control of the castings
- Development or use of a coherent and integrated system
- The mechanical properties of a die-cast product are principally related to:
- Die temperature
- Metal velocity at the gate
- Applied casting pressure [4]
- Combination of:
- Die temperature
- Fluidity of the molten metal
- Geometrical complexity of the parts
- Cooling rate during die casting
affect the integrity of a cast component.
- Thermal profile of the die during operation is another important factor in the production of high-quality components.
- Too high temperature of the die will lead to longer solidification which consequently prolongs the cycle time.
- A cold die will contribute to a number of surface defects [3, 8, 9].
- Limitations of Existing Research:
- In many of these works, the geometry of the part is simple and there are few researches on very complex part in industry.
- Necessity of Research:
- The aim of this work is optimization of process parameters in die casting of a complex automotive component named ladder frame by simulation.
3. Research Objectives and Research Questions:
- Research Objective:
- Die temperature in high-pressure die casting of A380 alloy is optimized by experimental observation and numerical simulation.
- Core Research Question:
- What is the effect of die temperature on the quality of the products in high-pressure die-casting process?
- What is the proper die temperature for this alloy?
- Research Hypothesis:
- It is shown that the proper die temperature for this alloy is above 200°C.
4. Research Methodology:
- Research Design:
- Combined experimental observation and numerical simulation.
- Experimental measurements of die temperature and melt temperature.
- Numerical simulation using ProCAST software.
- Verification of simulation results by experimental measurements.
- Data Collection Method:
- Experimental Data:
- Die temperatures at the initial step and the final filling positions were measured.
- The difference between these values was calculated.
- Melt temperature was measured by thermocouple and Laser pyrometer (model chy 110) at the die surface.
- Experiments were conducted at die temperatures of "150°C, 200°C, and 250°C".
- Simulation Data:
- ProCAST software was used to simulate the fluid flow and solidification step of the part.
- Material properties of the alloy were extracted from the software database and are shown in Table 1.
- Initial and boundary conditions used in the simulation are given in Table 2.
- Experimental Data:
- Analysis Method:
- Numerical Simulation:
- Governing equations for mass balance, momentum balance, and energy balance (enthalpy formulation) were solved using ProCAST software.
- Free surface modeling is achieved with a scalar variable, Φ.
- Two deferent mesh sizes were used and simulation results were compared at these two mesh sizes to ensure mesh independency of the results.
- Experimental Verification:
- The results were verified by experimental measurements.
- Numerical Simulation:
- Research Subject and Scope:
- Material: A380 material.
- Part Geometry: Ladder frame (one part of the new motor EF7) with a very complicated geometry (Figure 1).
- Process: High-pressure die casting (HPDC).
- Die Temperatures: "150°C, 200°C, and 250°C".
- Melt Temperature: Initial melt temperature of "680°C", shot sleeve speed of "3 m/s", and speed melt in gate of "55 m/s" for the ladder frame were assumed.
- Machine: IDRA1600 die-cast machine.
5. Main Research Results:
- Core Research Results:
- It is shown that the proper die temperature for this alloy is above 200°C.
- Cold flow surface defects occur at final filling positions predicted by the software at die temperature of "150°C" (Figure 5).
- Shrinkage defects occurred at the final solidification positions are shown in Figure 12, which were predicted by the software.
- The verified model interestingly represented the correct location of the porosity defects in the castings.
- Statistical/Qualitative Analysis Results:
- Melt Temperature Variation:
- The results show that the die temperature varies from "150 to 250°C", while the melt temperature varies between "660°C and 680°C" (Figure 2).
- Table 3 shows melt temperature at outset injection in shot sleeve and at end injection final filling position.
- At die temperature "150°C", Melt temperature °C at outset injection was "670, 669, 671" and Melt temperature °C at end injection was "650, 649, 652".
- At die temperature "200°C", Melt temperature °C at outset injection was "675, 676, 674" and Melt temperature °C at end injection was "664, 666, 663".
- At die temperature "250°C", Melt temperature °C at outset injection was "679, 680, 679" and Melt temperature °C at end injection was "671, 670, 668".
- Melt Temperature Reduction:
- The difference of two melt temperature curves at the initial and end of the process at "250°C, 200°C, and 150°C are 9.5°C, 10°C, and 19.5°C, respectively" (Figure 3).
- Defect Observation:
- Figure 5 shows typical examples of cold flow surface defects in pieces produced in a die with temperature of "150°C".
- Gas porosities caused by entrapped air during metal injection are illustrated in Figure 7.
- Shrinkage defects occurred at the final solidification positions are shown in Figure 12.
- Melt Temperature Variation:
- Data Interpretation:
- There is a break point in the curve of end injection at die temperature of "200°C".
- Defects are more probable at die temperatures less than "200°C".
- With regard to this break point, it can be seen that the normal die temperature for this alloy is "200°C".
- Maximum temperature depends on the die cooling system and optimized cycle time for production of a specific part.
- Comparison of the experimental and simulation results indicates that defects in the pieces are placed at the predicted places by simulation.
- Figure Name List:
- FIGURE 1: Geometry of ladder frame product.
- FIGURE 2: Melt temperatures at die entrance and start injection versus die temperatures.
- FIGURE 3: Melt temperatures at the end of the die and end injection versus die temperatures.
- FIGURE 4: Reduction of melt temperature at various die temperatures at the initial and the end of injection.
- FIGURE 5: Cold flow surface defects at final filling positions.
- FIGURE 6: positions of added overflows to the mold.
- FIGURE 7: Some porosity defects.
- FIGURE 8: Velocity vectors of the melt at the three holes in the front of the gate.
- FIGURE 9: Steps filled die by the melt and show End points.
- FIGURE 10: Flow pattern of melt with die temperature (a) 150°C and (b) 250°C in same time. Time al = b1, a2 = b2, and a3 = b3.
- FIGURE 11: Hot spots at the end of solidification step, which are susceptible to casting defects.
- FIGURE 12: Defects occurred in final solidification positions.
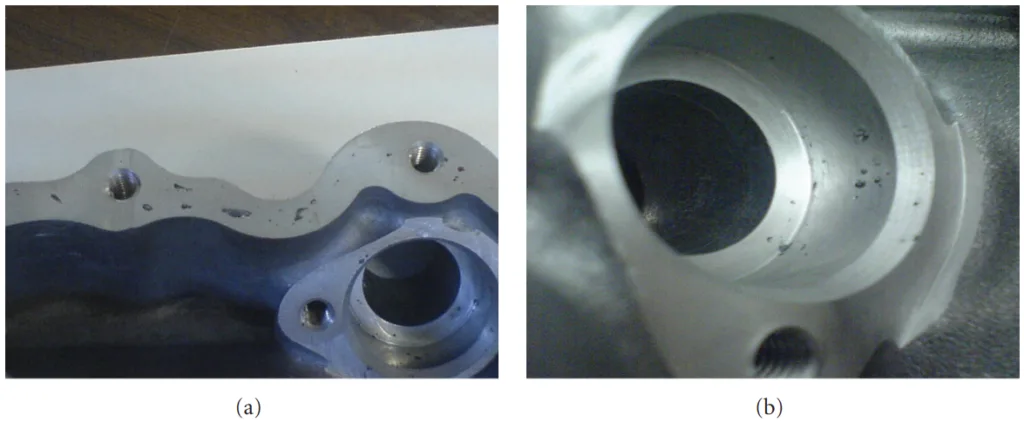
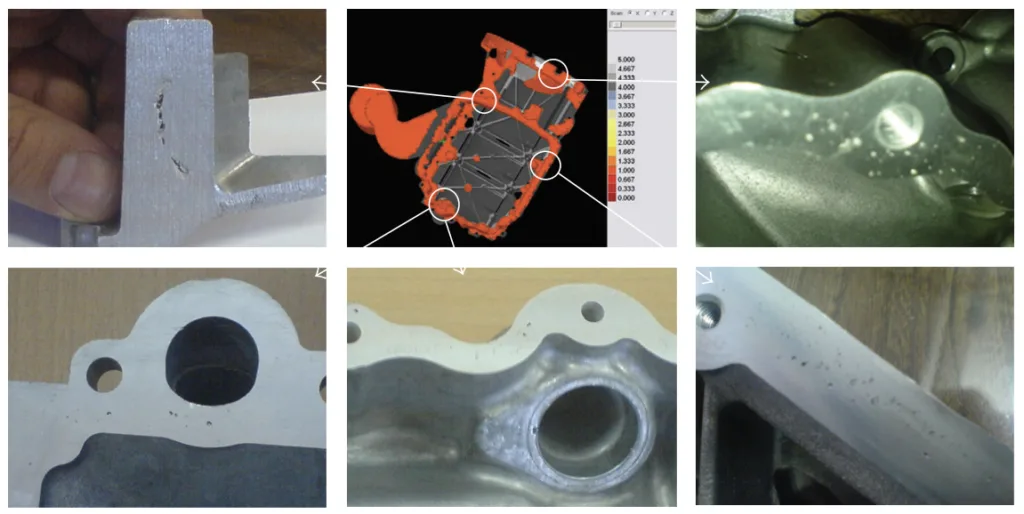
6. Conclusion and Discussion:
- Summary of Main Results:
- Comparison of the experimental and simulation results indicates that defects in the pieces are placed at the predicted places by simulation.
- Optimum die temperature for A380 alloy for H13 die material is around "200°C".
- If the die temperature is reduced from the optimum temperature range, probability of cold flow defects and air porosities increase.
- Determination of optimized places of overflows by simulation led to decrease of some casting defects such as cold shots and air porosities.
- Academic Significance:
- This study experimentally and theoretically determined the optimal die temperature for high-pressure die casting of A380 alloy.
- The research highlights the importance of die temperature control in achieving high-quality die-cast products.
- The use of numerical simulation (ProCAST software) is validated as an effective tool for optimizing die casting processes and predicting defect locations.
- Practical Implications:
- For manufacturing components using A380 alloy and H13 die material in HPDC, maintaining a die temperature of around "200°C" is recommended to minimize defects and ensure product quality.
- The findings suggest that die casters should carefully control and monitor die temperature to avoid cold flow defects and air porosities, especially when using die temperatures below 200°C.
- Numerical simulation can be used to optimize die design and process parameters, particularly in determining effective locations for overflows to mitigate defects.
- Limitations of Research:
- The study focused on a specific alloy (A380) and part geometry (ladder frame).
- The optimal die temperature may vary for different alloys, die materials, and component designs.
- Further research may be needed to investigate the influence of other process parameters and die cooling system designs.
7. Future Research:
- Future Research Directions:
- Further research is recommended to investigate the effect of die temperature on other aluminum alloys and different component geometries in HPDC.
- Optimization of die cooling systems to maintain a uniform die temperature and improve cycle time could be explored.
- Further studies could investigate the influence of other process parameters such as injection speed and pressure in conjunction with die temperature.
- Areas for Further Exploration:
- Investigating the effect of different die materials on the optimal die temperature.
- Exploring advanced simulation techniques to predict and mitigate other types of casting defects.
- Conducting economic analysis to determine the optimal balance between die temperature, cycle time, and product quality in HPDC.
8. References:
- [1] M. S. Dargusch, G. Dour, N. Schauer, C. M. Dinnis, and G. Savage, "The influence of pressure during solidification of high pressure die cast aluminium telecommunications components," Journal of Materials Processing Technology, vol. 180, no. 1-3, pp. 37-43, 2006.
- [2] Z. W. Chen and M. Z. Jahedi, "Die erosion and its effect on soldering formation in high pressure die casting of aluminium alloys," Materials and Design, vol. 20, no. 6, pp. 303-309, 1999.
- [3] P. W. Cleary, J. Ha, M. Prakash, and T. Nguyen, "3D SPH flow predictions and validation for high pressure die casting of automotive components," Applied Mathematical Modelling, vol. 30, no. 11, pp. 1406-1427, 2006.
- [4] K. J. Laws, B. Gun, and M. Ferry, "Effect of die-casting parameters on the production of high quality bulk metallic glass samples," Materials Science and Engineering A, vol. 425, no. 1-2, pp. 114-120, 2006.
- [5] D. McBride, T. N. Croft, and M. Cross, "A coupled finite volume method for the computational modelling of mould filling in very complex geometries," Computers & Fluids, vol. 37, no. 2, pp. 170–180, 2008.
- [6] C. C. Tai and J. C. Lin, “The optimal position for the injection gate of a die-casting die," Journal of Materials Processing Technology, vol. 86, no. 1-3, pp. 87–100, 1998.
- [7] S. W. Youn, C. G. Kang, and P. K. Seo, "Thermal fluid/solidification analysis of automobile part by horizontal squeeze casting process and experimental evaluation," Journal of Materials Processing Technology, vol. 146, no. 3, pp. 294-302, 2004.
- [8] J. X. Zhou, L. L. Chen, D. M. Liao, and R. X. Liu, "High pressure diecasting module of InteCAST software and its applications," Journal of Materials Processing Technology, vol. 192-193, pp. 249-254, 2007.
- [9] S. Yue, G. Wang, F. Yin, Y. Wang, and J. Yang, “Application of an integrated CAD/CAE/CAM system for die casting dies," Journal of Materials Processing Technology, vol. 139, no. 1-3, pp. 465-468, 2003.
- [10] A. Kermanpur, S. Mahmoudi, and A. Hajipour, "Numerical simulation of metal flow and solidification in the multi-cavity casting moulds of automotive components," Journal of Materials Processing Technology, vol. 206, no. 1-3, pp. 62-68, 2008.
- [11] S. Schneiderbauer, S. Pirker, C. Chimani, and R. Kretz, "Studies on flow characteristics at high-pressure die-casting," in Proceedings of the 3rd International Conference on Advances in Solidification Processes.
- [12] M. F. V. T. Pereira, M. Williams, and W. B. du Preez, "Reducing non value adding aluminium alloy in production of parts through high pressure die casting," in Proceedings of the Light Metals Conference, 2010.
- [13] J. K. Rai, A. M. Lajimi, and P. Xirouchakis, "An intelligent system for predicting HPDC process variables in interactive environment," Journal of Materials Processing Technology, vol. 203, no. 1-3, pp. 72-79, 2008.
- [14] B. S. Sung and I. S. Kim, "The molding analysis of automobile parts using the die-casting system," Journal of Materials Processing Technology, vol. 201, pp. 635-639, 2008.
- [15] V. Ilotte, "Die casting for chassis components," in Proceedings of the 4th International High Tech Die Casting Conference, Montichiari, Italy, April 2008.
- [16] Z. Brown, C. Barnes, J. Bigelow, and U. S. Contech, "Squeeze cast automotive applications and design considerations," in Proceedings of the 4th International High Tech Die Casting Conference, Montichiari, Italy, April 2008.
- [17] J. P. Papai, Contact heat transfer coefficients in aluminum alloy die casting: an experimental and numerical investigation? [Ph.D. thesis], The Ohio State University, 1994.
9. Copyright:
- This material is based on the paper by Mohammad Sadeghi and Jafar Mahmoudi: Experimental and Theoretical Studies on the Effect of Die Temperature on the Quality of the Products in High-Pressure Die-Casting Process.
- Paper Source: https://doi.org/10.1155/2012/434605
This material is a summary of the above paper and is prohibited from unauthorized use for commercial purposes.
Copyright © 2025 CASTMAN. All rights reserved.