This introduction paper is based on the paper "The Evolution of Dilatant Shear Bands in High Pressure Die Casting for Al-Si Alloy" published by "Preprints.org".
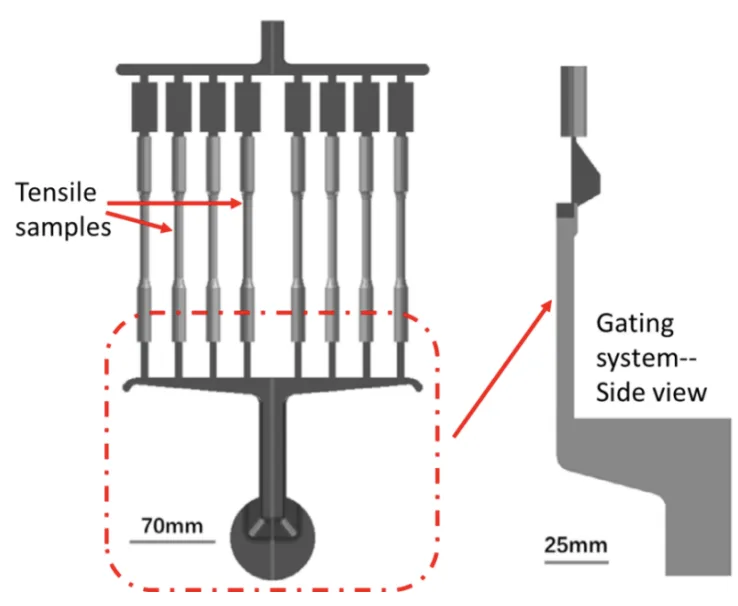
1. Overview:
- Title: The Evolution of Dilatant Shear Bands in High Pressure Die Casting for Al-Si Alloy
- Author: JINGZHOU LU, ewan lordan, Kun Dou
- Year of publication: 2024
- Journal/academic society of publication: Preprints.org (Not peer-reviewed version)
- Keywords: Shear bands; Segregation; Defects; Aluminium alloys; High pressure die casting
2. Abstract:
Bands of interdendritic porosity and positive macrosegregation are commonly observed in pressure die castings, with previous studies demonstrating their close relation to dilatant shear bands in granular materials. Despite recent technological developments, the micromechanism governing dilatancy in the high pressure die casting (HPDC) process for alloys between liquidus and solidus temperature region is still not fully understood. To investigate the influence of fluid flow and the size of externally solidified crystals (ESCs) on the evolution of dilatant shear bands in HPDC, various filling velocities were trialled to produce HPDC samples of Al8SiMnMg alloy. This study demonstrates that crystal fragmentation is accompanied by a decrease in dilatational concentration, thus producing an indistinct shear band. Once crystal fragmentation stagnates, the enhanced deformation rate associated with a further increase in filling velocity (from 2.2 ms-1 to 4.6 ms-¹) localises dilatancy into a highly concentrated shear band. The optimal piston velocity is 3.6 ms-1, under which the average ESC size reaches the minimum and the average yield stress and overall product of strength and elongation reaches the maximum value of 144.6 MPa and 3.664 GPa%, respectively. By adopting the concept of force chain buckling in granular media, the evolution of dilatant shear bands in equiaxed solidifying alloys can be adequately explained based on further verification with DEM-type modelling in OpenFOAM. Three mechanisms for ESC enhanced dilation are presented, elucidating previous reports relating the presence of ESCs to the subsequent shear band characteristics. By applying the physics of granular materials to equiaxed solidifying alloys, unique opportunities are presented for process optimization and microstructural modelling in HPDC.
3. Introduction:
High pressure die casting (HPDC) is highlighted as a crucial manufacturing process for light metals due to its high productivity, dimensional accuracy, and superior mechanical properties. However, the injection phase in HPDC is characterized by intense turbulence resulting from rapid filling speeds and narrow in-gates. The J factor [Eq.1], as defined by the VanRens equation, is introduced as a critical parameter indicating the initial flow regime, with significant implications for product quality.
The paper notes that intensive melt shearing during injection significantly influences the morphology and distribution of coarse externally solidified crystals (ESCs) in the final microstructure. Previous research is cited, indicating that filling velocity affects crystal fragmentation and re-melting, and ESCs' presence influences the rheology of the solidifying alloy and the characteristics of defect bands.
Drawing upon previous studies, the authors state that the rheology of equiaxed solidifying alloys can be interpreted as cohesionless compacted granular materials. The phenomenon of Reynolds’ dilatancy is mentioned, where increased shear stress in alloys leads to volumetric expansion and the formation of shear bands. The paper emphasizes the importance of HPDC process parameters, particularly the intensification stage and thermal conditions, in influencing shear band formation. The study aims to explore the influence of flow conditions on band characteristics, focusing on the implications of force chain buckling on dilatant shear banding and presenting three novel mechanisms for ESC enhanced dilation in HPDC. The influence of filling velocities on dilatant shear band evolution and crystal morphology will be discussed.
4. Summary of the study:
Background of the research topic:
The study addresses the common occurrence of interdendritic porosity and positive macrosegregation in pressure die castings. Previous research has established a close relationship between these defects and dilatant shear bands, phenomena well-documented in granular materials. Despite advancements in HPDC technology, the micromechanism governing dilatancy in alloys within the liquidus-solidus temperature range during HPDC remains incompletely understood.
Status of previous research:
Prior investigations utilizing vane rheometry and direct shear cells have indicated that the rheology of equiaxed solidifying alloys can be modeled as cohesionless compacted granular materials [12,13]. These studies have shown that grains in such assemblies respond to compressive and shear loading by rearranging into regions of contraction and dilation. In alloys like Al-7Si-0.3Mg and Mg-9A1-0.7Z, increased shear stress leads to volumetric expansion (Reynold's dilatancy) [14], ultimately localizing into shear bands. Research also suggests that HPDC parameters influence shear band characteristics [8,12,16,17]. Tordesillas' work on stress-dilatancy in granular assemblies through discrete element simulation (DEM) highlights cyclic jamming-unjamming events and force chain buckling as underlying mechanisms [18,19].
Purpose of the study:
This research aims to investigate the influence of fluid flow and the size of externally solidified crystals (ESCs) on the evolution of dilatant shear bands during the HPDC process. Specifically, the study seeks to elucidate the micromechanisms of ESC-enhanced dilation in HPDC by applying the concept of force chain buckling from granular materials to equiaxed solidifying alloys.
Core study:
The core of this study involves experimental HPDC of Al8SiMnMg alloy, employing various filling velocities to produce samples. The research examines the evolution of dilatant shear bands under different flow conditions and analyzes the resulting crystal morphology. The study adopts the concept of force chain buckling in granular media to explain the observed phenomena and uses DEM-type modeling in OpenFOAM for verification. The research further proposes three novel mechanisms for ESC-enhanced dilation in HPDC, aiming to provide insights for process optimization and microstructural modeling in HPDC.
5. Research Methodology
Research Design:
The research employs an experimental design involving High Pressure Die Casting (HPDC) of Al8SiMnMg alloy. Samples were produced using a Frech 4500 kN locking force cold chamber HPDC machine with varying filling velocities: 2.2 ms-1, 3.6 ms-1, and 4.2 ms-1. Tensile samples were created according to ASTM standards. DEM-type modelling using OpenFOAM was utilized for verification of proposed mechanisms.
Data Collection and Analysis Methods:
- Tensile Testing: Tensile tests were performed using an Instron 5500 universal electromechanical testing system, adhering to ASTM standard E8/E8M, to assess mechanical properties.
- Microstructure Characterization: Samples were analyzed using optical microscopy and scanning electron microscopy (SEM) to observe etched microstructures. Keller's reagent was used for etching. High contrast SEM micrographs were used for grain size measurements and analyzed with Fiji/ImageJ software. EDX mapping was used to highlight eutectic fraction.
- Thermographic Data: A FLIR T650sc infrared camera was used to monitor die temperature, ensuring a steady-state die temperature during the experiments. FLIR Tools software was used for analysis.
- Image Analysis: Fiji/ImageJ software was used for image processing, including binarization of SEM micrographs to differentiate grains and matrix, and for estimating the normalized width of the Si enrichment region.
- DEM-type modelling: OpenFOAM v5.0 platform was used to model melt flow and ESC motion, using Navior-Stokes equations, Standard k-epsilon equations and DPMFoam.
Research Topics and Scope:
The research focuses on:
- The evolution of dilatant shear bands in HPDC of Al-Si alloy.
- The influence of different filling velocities on dilatant shear band characteristics.
- The role of externally solidified crystals (ESCs) in enhancing dilatancy.
- Investigation of force chain buckling as a mechanism for dilatant shear band formation in equiaxed solidifying alloys.
- Validation of proposed mechanisms using DEM-type modelling in OpenFOAM.
- Implications for process optimization and microstructural modeling in HPDC.
6. Key Results:
Key Results:
- Dilatant Shear Bands and Filling Velocity: Bands of positive macrosegregation were observed across all tested filling velocities. Dilatational concentration initially decreased as velocity increased from 2.2 ms-1 to 3.6 ms-1, then increased again at 4.2 ms-1, indicating a transition from localized to global dilation and back to localized dilation.
- Optimal Piston Velocity: The optimal piston velocity was identified as 3.6 ms-1. At this velocity, the average ESC size reached a minimum, while average yield stress (YS) and the product of strength and elongation reached maximum values (144.6 MPa and 3.664 GPa%, respectively).
- ESC Size and Dilatancy: Crystal fragmentation was found to correlate with a decrease in dilatational concentration. An increase in filling velocity initially reduced average ESC size but further increases did not significantly alter ESC size, though in-cavity solidified grain size was reduced.
- Force Chain Buckling and ESC Enhanced Dilation Mechanisms: The study proposed and illustrated three novel mechanisms for ESC enhanced dilation in HPDC, based on the concept of force chain buckling. These mechanisms are graphically illustrated in Figure 8 and include:
- 'Stacking faults' due to large ESCs reducing contact points and increasing interstitial fluid.
- ESCs acting as pivots in outermost band regions due to transverse lift forces.
- Large ESCs dislodging force chain segments due to high energy dissipation upon collision in turbulent flow.
- Model Validation: DEM-type simulations in OpenFOAM corroborated the proposed mechanisms, accurately predicting ESC aggregation and dilatant shear band evolution.
Figure Name List:
- Figure 1. Casting region with gating system and 8 tensile samples HPDC tensile.
- Figure 2. Shot profile highlighting filling velocities used to produce HPDC tensile specimens.
- Figure 3. Infrared image and the temperature readings during various cycles of the HPDC process.
- Figure 4. Dilatant shear bands observed in HPDC samples produced with filling velocities of 2.2 ms-1 (top row), 3.6 ms-1 (middle row) and 4.2 ms-¹ (bottom row). Typical macrostructure of etched samples from the centre of the gage section are shown (left) and corresponding EDX maps highlighting eutectic fraction are shown (right).
- Figure 5. Optical micrographs taken from zone A, showing how dilatancy varies with filling velocities of (i) 2.2 ms-¹, (ii) 3.6 ms-¹, and (iii) 4.2 ms-¹. Outlined in (ii) is a potential force chain that has persisted through deformation. The bulk filling direction is out of the page.
- Figure 6. Typical high contrast secondary electron SEM micrographs used to obtain average ESC and in-cavity solidified grain size (Table.1), for filling velocities of (i) 2.2 ms-¹, (ii) 3.6 ms-¹ and (iii) 4.2 ms-1.
- Figure 7. The yield stress, elongation and ultimate tensile stress of various tensile samples.
- Figure 8. Graphical illustration highlighting the three mechanisms governing ESC enhanced dilation within the shear band: (i) 'Stacking faults' introduced by the presence of ESCs along the force chain; (ii) ESCs located on the outermost regions of the band effectively acting as pivots; (iii) ESCs propelled by highly turbulent flow conditions, potentially dislodging crystals from the force chain. σ denotes the major principle stress axis.
- Figure 9. (i) Calculation domain and mesh for the model, (ii) The fluid velocity distribution of melt, (iii) The ESC motion and velocity distribution in the tensile sample during filling.
- Figure 10. The ESCs aggregation tendency in the tensile sample during filling.
7. Conclusion:
The study concludes that the evolution of dilatant shear bands in equiaxed solidifying alloys during HPDC can be effectively explained by adopting the concept of force chain buckling from granular materials. Fluid flow and grain size are identified as significant factors influencing dilatancy, thereby controlling dilatational concentration and the extent of segregation within shear bands. The maximum dilatancy was observed at a filling speed of 2.2 ms-¹, associated with a larger average ESC size. Increasing filling velocity initially promoted crystal fragmentation, reducing dilatational concentration and indistinct shear bands, up to a critical J-factor. However, excessively high filling velocities led to increased deformation rate, increased dilatational concentration, and distinct shear bands, while also refining in-cavity solidified grains due to atomization. The optimal piston velocity of 3.6 ms-1 was found to minimize ESC size and maximize mechanical properties. The research proposes three novel mechanisms for ESC-enhanced dilation and validates these with DEM simulations, offering valuable insights for optimizing HPDC processes and microstructure modeling. The application of granular material physics to equiaxed solidifying alloys opens new avenues for process optimization and microstructural control in HPDC.
8. References:
- 1. T. Kaneuchi, H. Nakano, Effect of J-value for internal quality of HPDC products at various casting alloys, in: Japan Die Cast. Congr. Trans., 2008: pp. 131-136.
- 2. T. Kaneuchi, K. Motegi, T. Imamura, Properties of castings produced by high vacuum die cast process, in: Japan Die Cast. Congr. Trans., 2004: pp. 277-282.
- 3. Y. Yamada, H. Yoshii, S. Mochizuki, Evaluation of J factor and leakage quality for high pressure die casting applied to closed-deck type cylinder block, SAE Tech. Pap. (2011).
- 4. E. Koya, M. Nakagawa, S. Kitagawa, J. Ishimoto, Y. Nakano, N. Ochiai, Research of Atomization Phenomena in HPDC-Step 1 Feature of Gas Porosity Dispersion and Photography of Atomized Flow, SAE Tech. Pap. 2018–April (2018) 1–8. doi:10.4271/2018-01-1392.
- 5. E. Koya, M. Nakagawa, S. Kitagawa, J. Ishimoto, Y. Nakano, N. Ochiai, Atomization in High-Pressure Die Casting - Step 2 Simulation of Atomized Flow of Molten Aluminum by LES-VOF Method, SAE Tech. Pap. 2018-April (2018) 1–10. doi:10.4271/2018-01-1393.
- 6. S. Otarawanna, C.M. Gourlay, H.I. Laukli, A.K. Dahle, Agglomeration and bending of equiaxed crystals during solidification of hypoeutectic Al and Mg alloys, Acta Mater. 58 (2010) 261-271. doi:10.1016/j.actamat.2009.09.002.
- 7. H.R. Kotadia, N. Hari Babu, H. Zhang, S. Arumuganathar, Z. Fan, Solidification behavior of intensively sheared hypoeutectic Al-Si alloy liquid, Metall. Mater. Trans. A Phys. Metall. Mater. Sci. 42 (2011) 1117–1126. doi:10.1007/s11661-010-0516-8.
- 8. H. Cao, M. Wessén, Characteristics of microstructure and banded defects in die cast AM50 magnesium components, Int. J. Cast Met. Res. 18 (2005) 377–384. doi:10.1179/136404605225023216.
- 9. M. Wu, X. Li, Z. Guo, S.Xiong, Effects of process parameters on morphology and distribution of externally solidified crystals in microstructure of magnesium alloy die castings, China Foundry. 15 (2018) 139–144. doi:10.1007/s41230-018-7242-z.
- X. Li, Z. Guo, S. Xiong, Influence of melt flow on the formation of defect band in high pressre die casting of AZ91D magnesium alloy, Mater. Charact. 129 (2017) 344–352.
- C.M. Gourlay, H.I. Laukli, A.K. Dahle, Defect band characteristics in Mg-Al and Al-Si high-pressure die castings, Metall. Mater. Trans. A Phys. Metall. Mater. Sci. 38 (2007) 1833–1844. doi:10.1007/s11661-007-9243-1.
- A.K. Dahle, D.H. StJohn, Rheological behaviour of the mushy zone and its effect on the formation of casting defects during solidification, Acta Mater. 47 (1998) 31–41. doi:10.1016/S1359-6454(98)00342-5.
- AZ91 magnesium alloy, Acta Mater. 56 (2008) 3403–3413. doi:10.1016/j.actamat.2008.03.020.
- C.M. Gourlay, A.K. Dahle, Dilatant shear bands in solidifying metals, Nature. 445 (2007) 70–73. doi:10.1038/nature05426.
- S. Otarawanna, C.M. Gourlay, H.I. Laukli, A.K. Dahle, The thickness of defect bands in high-pressure die castings, Mater. Charact. 60 (2009) 1432–1441. doi:10.1016/j.matchar.2009.06.016.
- H. Gjestland, S. Sannes, J. Svalestuen, H. Westengen, Optimizing the Magnesium Die Casting Process to Achieve Reliability in Automotive applications, SAE Tech. Pap. Ser. SAE 2005-0 (2005). doi:10.4271/2005-01-0333.
- S. Otarawanna, H.I. Laukli, C.M. Gourlay, A.K. Dahle, Feeding mechanisms in high-pressure die castings, Metall. Mater. Trans. A Phys. Metall. Mater. Sci. 41 (2010) 1836-1846. doi:10.1007/s11661-010-0222-6.
- A. Tordesillas, J. Shi, T. Tshaikiwsky, Stress-dilatancy and force chain evolution, Int. J. Numer. Anal. Meth. Geomech. 35 (2011) 264-292.
- A. Tordesillas, Force chain buckling, unjamming transitions and shear banding in dense granular assemblies, Philos. Mag. 87 (2007) 4987–5016. doi:10.1080/14786430701594848.
- E. Lordan, J. Lazaro-Nebreda, Y. Zhang, Z. Fan, Effective Degassing for Reduced Variability in High-Pressure Die Casting Performance, JOM. (2018). doi:10.1007/s11837-018-3186-4.
- F. Radjai, D. Wolf, M. Jean, J.J. Moreau, F. Radjai, D. Wolf, M. Jean, J. Jacques, M. Bimodal, Bimodal Character of Stress Transmission in Granular Packings To cite this version : HAL Id : hal-01407369 Bimodal Character of Stress Transmission in Granular Packings, (2016) 0-4.
- D. walker, A. tordesillas, On Reynolds' Dilatancy and Shear Band Evolution: a New Perspective, Int. J. Bifurc. Chaos. 23 (2013) 1330034. doi:10.1142/S0218127413300346.
- M. Oda, J. Konishi, S. Nemat-Nasser, Experimental micromechanical evaluation of the strength of granular materials: Effects of particle rolling, Stud. Appl. Mech. 7 (1983) 21–30. doi:10.1016/B978-0-444-42192-0.50009-8.
- K. Iwashita, M. Oda, Micro-deformation mechanism of shear banding process based on modified distinct element method, Powder Technol. 109 (2000) 192–205. doi:10.1016/S0032-5910(99)00236-3.
- T.S. Majmudar, R.P. Behringer, Contact force measurements and stress-induced anisotropy in granular materials, Nature. 435 (2005) 1079–1082. doi:10.1038/nature03805.
- H.I. Laukli, C.M. Gourlay, A.K. Dahle, Migration of crystals during the filling of semi-solid castings, Metall. Mater. Trans. A Phys. Metall. Mater. Sci. 36 (2005) 805-818. doi:10.1007/s11661-005-1011-5.
- H.I. Andersson, L. Zhao, M. Barri, Torque-coupling and particle-turbulence interactions, J. Fluid Mech. 696 (2012) 319-329. doi:10.1017/jfm.2012.44.
- C. Bi, S. Xiong, X. Li, Z. Guo, Development of a Fluid-Particle Model in Simulating the Motion of External Solidified Crystals and the Evolution of Defect Bands in High-Pressure Die Casting, Metall. Mater. Trans. B Process Metall. Mater. Process. Sci. 47 (2016) 939–947. doi:10.1007/s11663-016-0591-3.
- X. Li, W. Yu, J. Wang, S. Xiong, Influence of melt flow in the gating system on microstructure and mechanical properties of high pressure die casting AZ91D magnesium alloy, Mater. Sci. Eng. A. 736 (2018) 219-227. doi:10.1016/j.msea.2018.08.090.
- I. Graco, Atomization Concept and Theory, 1995.
- K. Dou, E. Lordan, Y. Zhang, A. Jacot, Z. Fan. A complete computer aided engineering (CAE) modelling and optimization of high pressure die casting (HPDC) process. Journal of Manufacturing Processes, 2020. doi.org/10.1016/j.jmapro.2020.10.062.
- K. Dou, E. Lordan, Y. Zhang, A. Jacot, Z. Fan. A novel approach to optimize mechanical properties for aluminium alloy in High pressure die casting (HPDC) process combining experiment and modelling. Journal of Materials Processing Technology, 2021. doi.org/10.1016/j.jmatprotec.2021.117193.
- Bi, C., Xiong, S., Li, X. et al. Development of a Fluid-Particle Model in Simulating the Motion of External Solidified Crystals and the Evolution of Defect Bands in High-Pressure Die Casting. Metall Mater Trans B 47, 939–947 (2016). https://doi.org/10.1007/s11663-016-0591-3.
9. Copyright:
- This material is a paper by "JINGZHOU LU, ewan lordan, Kun Dou". Based on "The Evolution of Dilatant Shear Bands in High Pressure Die Casting for Al-Si Alloy".
- Source of the paper: doi: 10.20944/preprints202410.0105.v1
This material is summarized based on the above paper, and unauthorized use for commercial purposes is prohibited.
Copyright © 2025 CASTMAN. All rights reserved.