This article introduces the paper "Effects of die-casting defects on the blister formation in high-pressure die-casting aluminum structural components".
1. Overview:
- Title: Effects of die-casting defects on the blister formation in high-pressure die-casting aluminum structural components
- Authors:
- Bartłomiej Dybowski
- Andrzej Kiełbus
- Łukasz Poloczek
- Publication Year: 2023
- Journal/Conference: Engineering Failure Analysis
- Keywords:
- Blistering
- High pressure die casting
- Aluminum Alloys
- Heat treatment
- Microscopic characterization
2. Research Background:
- Social/Academic Context of Research Topic:
- High-pressure die casting (HPDC) is a widely used process for mass production of thin-walled nonferrous metal parts requiring tight dimensional tolerances and good surface finish [1].
- HPDC is crucial for automotive structural components like shock towers and A, B, C-pillars, demanding high mechanical properties, specifically high ductility (UTS > 180 MPa, YS > 130 MPa, A5 > 10%).
- Heat treatment is often essential to achieve the required ductility in HPDC aluminum structural components.
- However, heat treatment can induce blistering on the surface, which is unacceptable in final products and leads to component rejection, reducing production efficiency [15].
- Limitations of Existing Research:
- Previous studies on new Al-Si-Cu-Mn-Fe HPDC alloys showed that while strength properties are satisfactory, plastic properties are insufficient for structural elements.
- Even with optimal alloy chemical composition and no initial blisters, heat treatment does not guarantee improved strength properties [7].
- Further research is needed to understand the relationship between specific die-casting defects and blister formation to develop effective mitigation strategies.
- Necessity of Research:
- Blistering during heat treatment of HPDC aluminum components is a significant issue in the automotive industry, causing production losses and quality concerns [15].
- Understanding the effect of specific casting defects on blister formation is crucial for developing strategies to minimize or eliminate blistering and improve the reliability and efficiency of HPDC processes for structural components.
- This research is necessary to identify the types of casting defects that initiate blistering and to provide insights for process optimization to reduce these defects.
3. Research Objectives and Research Questions:
- Research Objective:
- To present the effect of die-casting defects in AlSi10MnMg alloy structural components on the possibility of blister formation during heat treatment.
- To identify the types of casting defects that act as initiation sites for blistering in HPDC aluminum structural components.
- Core Research Questions:
- How do different types of die-casting defects in AlSi10MnMg alloy structural components affect the formation of blisters during heat treatment?
- What are the characteristics of casting defects that initiate blister formation in hot and cold areas of HPDC components?
- Research Hypothesis:
- Blister formation in heat-treated HPDC AlSi10MnMg alloy structural components initiates at casting defects that create microstructural discontinuities.
- Different types of casting defects, such as cold flakes, porosity, cold drops, cold shots, and oxide films, have varying effects on blister formation depending on their location and characteristics.
4. Research Methodology
- Research Design:
- Case study of a commercial 9.5 kg shock tower casting made of AlSi10MnMg HPDC alloy.
- Comparison of samples from hot areas (near the gating system) and cold areas (away from the gating system) of the casting.
- Analysis of samples in the as-cast state and after T7 heat treatment (solution heat treatment and overaging).
- Data Collection Methods:
- Microstructure observations:
- Light Microscopy (LM) and Scanning Electron Microscopy (SEM) for structural research.
- Energy-Dispersive X-Ray Spectroscopy (EDS) for microstructural components microanalyses.
- Metallographic specimens prepared using a typical procedure in non-etched micro-sections.
- EDM (electrical discharge machining) was used to cut blisters in half for examination.
- Casting process simulations:
- MAGMAsoft commercial software was used for liquid alloy injection simulations and flow analysis within the die.
- Simulation of melt velocity and temperature during mold filling.
- Casting surface observations:
- Visual inspection of casting surfaces after heat treatment to identify blister locations and characteristics.
- Microstructure observations:
- Analysis Methods:
- Qualitative analysis of microstructure to identify casting defects and their characteristics in relation to blister formation.
- Comparison of defect types and blister formation in hot and cold areas of the casting.
- Correlation of casting defects with blister locations and sizes.
- Analysis of simulation results to understand melt flow and temperature distribution during casting.
- Research Subjects and Scope:
- Material: Commercial AlSi10MnMg HPDC alloy.
- Component: 9.5 kg shock tower casting produced on an ITALPRESSE 2700 machine.
- Focus: Die-casting defects (cold flakes, porosity, cold drops, cold shots, oxide films) and their effect on blister formation during T7 heat treatment.
- Areas of investigation: Hot areas (near gating system) and cold areas (away from gating system) of the casting.
5. Key Research Findings:
- Core Research Findings:
- The blistering process begins at casting defects, which create microstructural discontinuities.
- If gases are present in a discontinuity, they expand during solution treatment, forming surface blisters.
- Different casting defects lead to blisters of varying sizes and locations.
- The largest blisters form on cold flakes, mainly in casting areas near the gating system.
- Smaller blisters form on porosity - both gas and shrinkage porosity.
- Cold drops, cold shots, and thin oxide films act as blistering sites, primarily in areas away from the gating system.
- Statistical/Qualitative Analysis Results:
- Blister Location: Most blistering occurs near the gating system in hot areas [Fig. 3]. In contrast, only a few blisters occur in cold areas [Fig. 4a].
- Blister Size: Blisters present in hot areas are separate from others and larger than those in cold areas [Fig. 4b]. Large blisters in hot areas can be over 5 mm in size, while small blisters in cold areas are lower than 2 mm.
- Defect Types and Location:
- Hot Areas: Characterized by large particles with different microstructure than the alloy in their surrounding area (cold flakes) [Fig. 8c, Fig. 9]. Also present are a few singular pores [Fig. 8a], Si eutectic phase's single large separations, intermetallic phases, and thick a-Al dendrites [Fig. 8b].
- Cold Areas: Gas and shrinkage porosity are higher compared to hot areas [Fig. 10a]. Long discontinuities and thin layers are present near the casting wall edge. Fine, circular, and elongated particles (cold drops) [Fig. 11a, b]. Oxide thin films are also found [Fig. 11c, d].
- Microstructure under Blisters: The AlSi10MnMg alloy microstructure under the blisters center differs from the alloy further from it [Fig. 16a], indicating blistering begins at wide, flat alloy microstructure discontinuities.
- Data Interpretation:
- Cold flakes: Act as primary sites for large blister formation in hot areas due to their flat shape, large size, and discontinuity with the matrix, trapping gases.
- Porosity: Contributes to smaller blister formation in both hot and cold areas. Spherical pores need higher pressure to form blisters [10], but interconnected, elongated micro-shrinkage pores increase blister risk.
- Cold drops, cold shots, oxide films: Initiate smaller blisters in cold areas, often associated with porosity and laminations, due to lower alloy temperature and semi-solid flow.
- Blister Shape: Blisters in hot areas are often semicircular with a flat bottom edge parallel to the casting wall [Fig. 13], indicating formation at flat discontinuities like cold flakes.
- Figure Name List:
- Fig. 1. Shock tower casting scheme.
- Fig. 2. Liquid alloy temperature during the injection at different mold filling stages (a, b).
- Fig. 3. Shock tower casting surface's blisters distribution.
- Fig. 4. Blisters on the heat-treated casting surface in (a) a cold area (area 2E in Fig. 3) and (b) a hot area (area 10G in Fig. 3).
- Fig. 5. As-cast AlSi10MnMg alloy microstructure, LM: (a) cold area, (b) hot area.
- Fig. 6. Intermetallic phases in as-cast AlSi10MnMg alloy, SEM: (a) platelet-like and (b) polygonal.
- Fig. 7. Heat-treated AlSi10MnMg alloy microstructure, SEM: (a) spheroidized Si and (b) intermetallic phases.
- Fig. 8. Casting defects in shock tower casting hot areas, LM: (a) porosity, (b) externally solidified crystals (ESC), (c) cold flake, and (d) discontinuity on the flake edge.
- Fig. 9. Cold flake in the AlSi10MnMg alloy microstructure, LM.
- Fig. 10. Casting defects in shock tower casting cold areas, SEM: (a) porosity, (b) cold shuts and laminations (b-d).
- Fig. 11. Casting defects in as-cast shock tower casting cold areas, SEM: cold drops (a, b), thin oxide films (c, d).
- Fig. 12. EDS chart obtained from the thin films shown in Fig. 11c.
- Fig. 13. A blister formed at the discontinuity parallel to the casting wall edge, LM.
- Fig. 14. A blister formed at the discontinuity lying under the angle to the casting wall edge, LM.
- Fig. 15. Surface characteristics observed on a blister, SEM: (a) flat surface in the center, (b) rough surface at the edges.
- Fig. 16. Different alloy microstructure, LM: (a) in the blister's center shown in Fig. 13, (b) secondary cracks under the blister shown in Fig. 14.
- Fig. 17. Non-expanded discontinuity, LM: (a) at the blister edge, (b) cold flake far from the casting edge.
- Fig. 18. Cold drops, SEM: (a) at blister edge, (b) at blister formed by alloy porosity.
- Fig. 19. Large blisters in the shock tower cold area, LM.
- Fig. 20. Blisters formed at the AlSi10MnMg alloy porosity, SEM: a) separated gas pore, b) connected gas pores, c) shrinkage porosity.
- Fig. 21. Shock tower casting's cold areas, SEM: (a) semi-spherical blister, (b) expanded thin discontinuities.
- Fig. 22. Expanded discontinuities, SEM: (a) formed at flat cold drops, (b) formed at spherical ones.
- Fig. 23. Needle-like cold drops in the shock tower cold area, SEM: (a) as-cast, (b) heat-treated.
- Fig. 24. Blisters formed by thin oxide film, SEM.
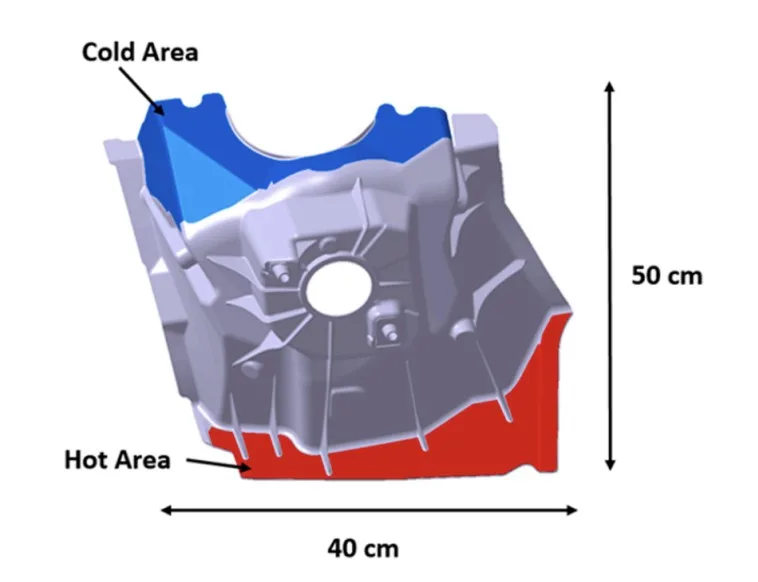
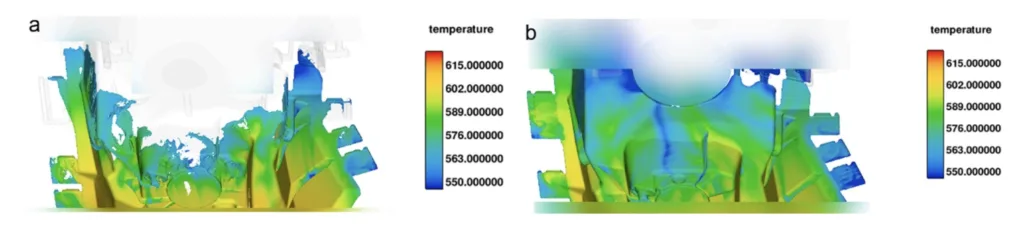
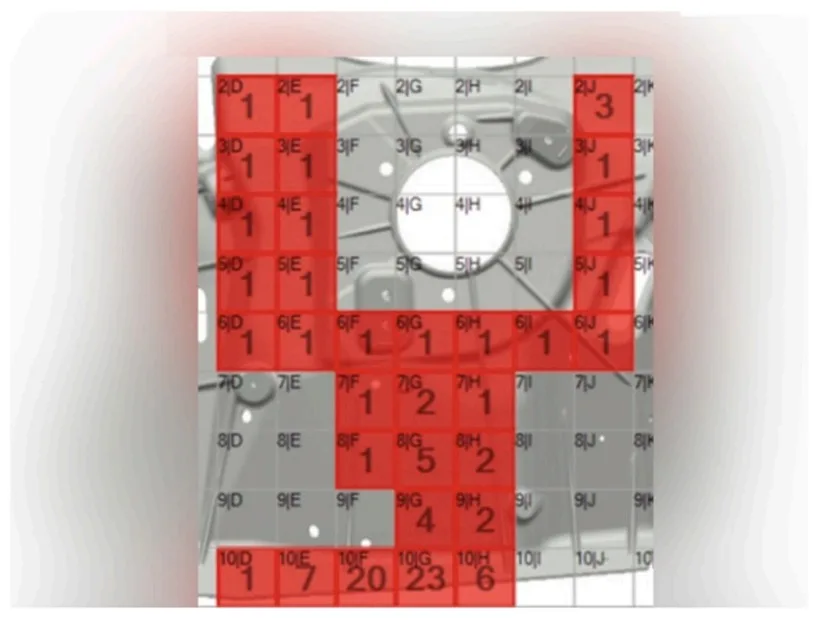
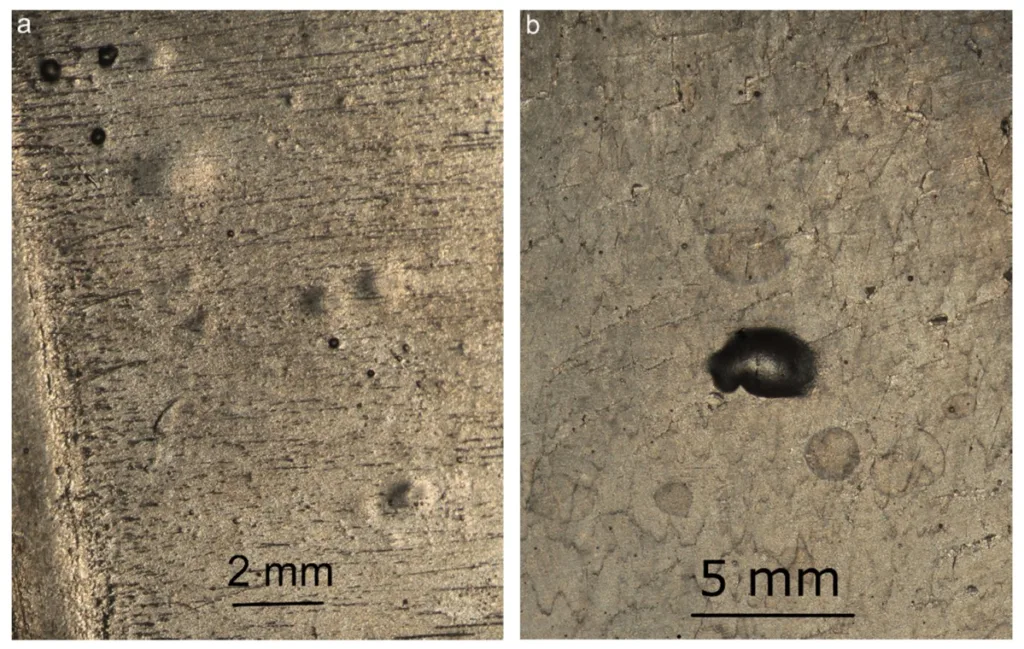
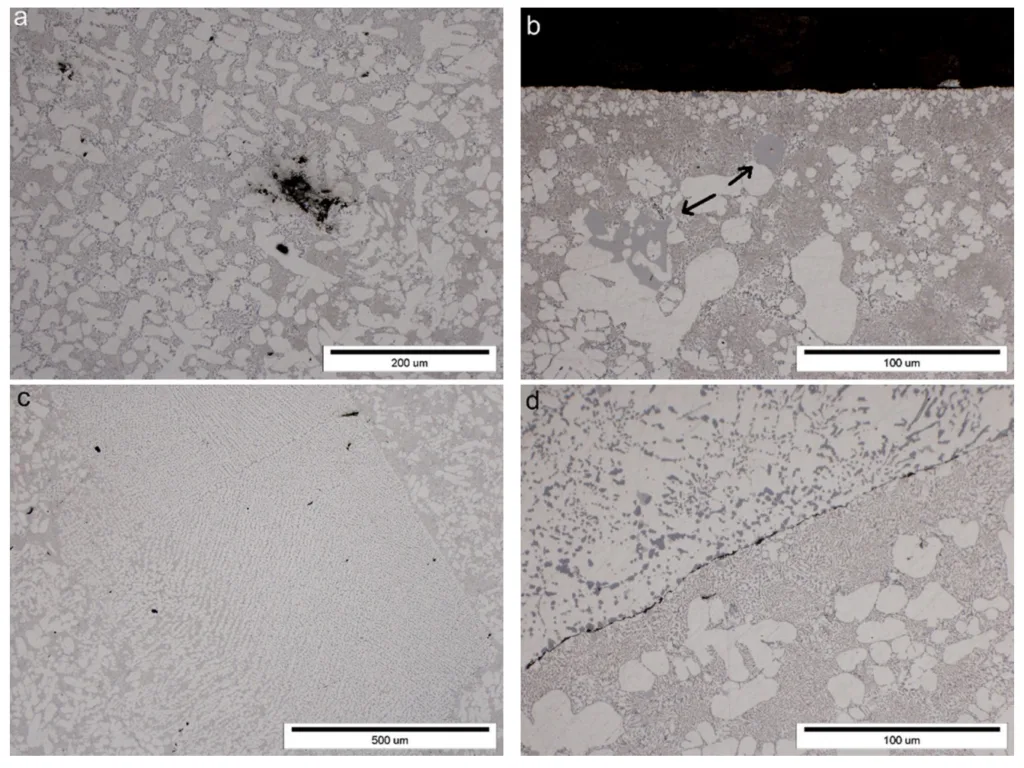
6. Conclusion and Discussion:
- Summary of Main Results:
- Blister formation in HPDC AlSi10MnMg alloy is initiated by casting defects that create microstructural discontinuities.
- Cold flakes are the most detrimental defects, causing large blisters in hot areas and reducing alloy ductility.
- Porosity, cold drops, cold shots, and oxide films also contribute to blistering, especially in cold areas, resulting in smaller blisters.
- Blistering is more pronounced in hot areas near the gating system due to the prevalence of large cold flakes.
- Academic Significance of Research:
- This research provides a detailed analysis of the relationship between specific die-casting defects and blister formation in HPDC aluminum structural components.
- It identifies cold flakes as the primary cause of large blisters and highlights the role of other defects like porosity, cold drops, and oxide films in blister initiation.
- The findings contribute to a better understanding of the blistering mechanism in HPDC alloys and the critical role of casting defects in this phenomenon.
- Practical Implications:
- Minimizing cold flake formation is crucial for reducing blistering in HPDC AlSi10MnMg alloy structural components, especially in hot areas.
- Process optimization strategies should focus on:
- Maintaining high shot sleeve temperature and minimizing alloy residence time to reduce cold flake formation.
- Implementing obstacles in the gating system to break down large flakes [17].
- Regular holding furnace maintenance and dosing tap cleaning to reduce cold flakes.
- Optimizing lubrication system, vacuum system, and shot profile settings to minimize gas entrapment and porosity [19].
- Controlling mold cooling to reduce solidification rate in cold areas and minimize cold drops and cold shuts.
- Limitations of Research:
- The study is based on a single case study of a shock tower casting, and findings may be specific to this component geometry and production process.
- The research is primarily qualitative, focusing on microscopic observations and defect characterization rather than quantitative statistical analysis of blister formation and defect frequency.
- Further research is needed to quantify the relationship between defect size, type, and blister severity across different HPDC components and alloys.
7. Future Follow-up Research:
- Directions for Future Research:
- Quantitative analysis of the correlation between different types and sizes of casting defects and the probability and size of blister formation.
- Investigation of the effect of varying heat treatment parameters (temperature, time) on blister formation in relation to different casting defect types.
- Development and validation of process optimization strategies to specifically target and reduce the formation of cold flakes and other blister-inducing defects in HPDC.
- Study of different alloy compositions and their susceptibility to blister formation in relation to casting defects.
- Areas Requiring Further Exploration:
- The precise mechanism of gas entrapment and expansion within different types of casting defects during heat treatment.
- The influence of mold design and gating system on the formation and distribution of cold flakes and other defects.
- The effectiveness of real-time defect detection and process control methods for reducing blister formation in HPDC production.
8. References:
- [1] F. Bonollo, N. Gramegna, G. Timelli, High-pressure die-casting: contradictions and challenges, JOM 67 (2015) 901-908, https://doi.org/10.1007/s11837-015-1333-8.
- [2] S. Ji, Y. Wang, D. Watson, Z. Fan, Microstructural evolution and solidification behavior of Al-Mg-Si alloy in high-pressure die casting, Metall. Mater. Trans. A 44 (2013) 3185-3197, https://doi.org/10.1007/s11661-013-1663-5.
- [3] M. Jolly, L. Katgerman, Modelling of defects in aluminium cast products, Prog Mater Sci. 123 (2022), 100824, https://doi.org/10.1016/j.pmatsci.2021.100824.
- [4] A. Zhang, Z. Guo, Q. Wang, S. Xiong, Multiphase-field modelling of hydrogen pore evolution during alloy solidification, IOP Conf Ser Mater Sci Eng. 861 (2020), 012021, https://doi.org/10.1088/1757-899X/861/1/012021.
- [5] P. Zhang, Z. Li, B. Liu, W. Ding, Effect of chemical compositions on tensile behaviors of high pressure die-casting alloys Al-10Si-yCu-xMn-zFe, Mater. Sci. Eng. A 661 (2016) 198-210, https://doi.org/10.1016/j.msea.2016.03.032.
- [6] P. Zhang, Z. Li, B. Liu, W. Ding, Tensile properties and deformation behaviors of a new aluminum alloy for high pressure die casting, J Mater Sci Technol. 33 (2017) 367-378, https://doi.org/10.1016/j.jmst.2016.02.013.
- [7] S. Seifeddine, D. Poletaeva, M. Ghorbani, A. Jarfors, Heat treating of high pressure die cast components: challenges and possibilities, in: Light Metals 2014, Springer International Publishing, Cham, 2014, pp. 183-188, https://doi.org/10.1007/978-3-319-48144-9_32.
- [8] X.G. Hu, Q. Zhu, S.P. Midson, H.V. Atkinson, H.B. Dong, F. Zhang, Y.L. Kang, Blistering in semi-solid die casting of aluminium alloys and its avoidance, Acta Mater. 124 (2017) 446-455, https://doi.org/10.1016/j.actamat.2016.11.032.
- [9] H. Zhao, Y. Bai, X. Ouyang, P. Dong, Simulation of mold filling and prediction of gas entrapment on practical high pressure die castings, Trans. Nonferrous Met. Soc. Chin. 20 (2010) 2064-2070, https://doi.org/10.1016/S1003-6326(09)60418-0.
- [10] O. Ozhoga-Maslovskaja, E. Gariboldi, J.N. Lemke, Conditions for blister formation during thermal cycles of Al-Si-Cu-Fe alloys for high pressure die-casting, Mater Des. 92 (2016) 151-159, https://doi.org/10.1016/j.matdes.2015.12.003.
- [11] H. Toda, P.C. Qu, S. Ito, K. Shimizu, K. Uesugi, A. Takeuchi, Y. Suzuki, M. Kobayashi, Formation behaviour of blister in cast aluminium alloy, Int. J. Cast Met. Res. 27 (2014) 369-377, https://doi.org/10.1179/1743133614Y.0000000123.
- [12] H. Kang, H. Jang, S. Oh, P. Yoon, G. Lee, J. Park, E. Kim, Y. Choi, Effects of solution treatment temperature and time on the porosities and mechanical properties of vacuum die-casted and T6 heat-treated Al-Si-Mg alloy, Vacuum 193 (2021), 110536, https://doi.org/10.1016/j.vacuum.2021.110536.
- [13] H. Cao, Q. Sun, Q. Pu, L. Wang, M. Huang, Z. Luo, J. Che, Effect of vacuum degree and T6 treatment on the microstructure and mechanical properties of Al-Si-Cu alloy die castings, Vacuum 172 (2020), 109063, https://doi.org/10.1016/j.vacuum.2019.109063.
- [14] H.J. Kang, P.H. Yoon, G.H. Lee, J.Y. Park, B.J. Jung, J.Y. Lee, C.U. Lee, E.S. Kim, Y.S. Choi, Evaluation of the gas porosity and mechanical properties of vacuum assisted pore-free die-cast Al-Si-Cu alloy, Vacuum 184 (2021), 109917, https://doi.org/10.1016/j.vacuum.2020.109917.
- [15] R.N. Lumley, R.G. O'Donnell, D.R. Gunasegaram, M. Givord, Heat treatment of high-pressure die castings, Metall. Mater. Trans. A 38 (2007) 2564-2574, https://doi.org/10.1007/s11661-007-9285-4.
- [16] P.W. Cleary, J. Ha, M. Prakash, T. Nguyen, Short shots and industrial case studies: understanding fluid flow and solidification in high pressure die casting, Appl Math Model. 34 (2010) 2018-2033, https://doi.org/10.1016/j.apm.2009.10.015.
- [17] D.R. Gunasegaram, M. Givord, R.G. O'Donnell, B.R. Finnin, Improvements engineered in UTS and elongation of aluminum alloy high pressure die castings through the alteration of runner geometry and plunger velocity, Mater. Sci. Eng. A 559 (2013) 276-286, https://doi.org/10.1016/j.msea.2012.08.098.
- [18] W.G. Walkington, Die casting defects: causes and solutions, NADCA, 1997.
- [19] X.P. Niu, B.H. Hu, I. Pinwill, H. Li, Vacuum assisted high pressure die casting of aluminium alloys, J. Mater. Process Technol. 105 (2000) 119-127, https://doi.org/10.1016/S0924-0136(00)00545-8.
9. Copyright:
*This material is summarized based on the paper: "Effects of die-casting defects on the blister formation in high-pressure die-casting aluminum structural components" by Bartłomiej Dybowski, Andrzej Kiełbus, and Łukasz Poloczek.
*Paper Source: https://doi.org/10.1016/j.engfailanal.2023.107223
This summary is based on the above paper and is prohibited from unauthorized use for commercial purposes.
Copyright © 2025 CASTMAN. All rights reserved.