This introductory paper is the research content of the paper ["Effects of Cooling Rate on Solidification Structure and Performance of ADC12 Alloy"] published by [Special Casting & Nonferrous Alloys].
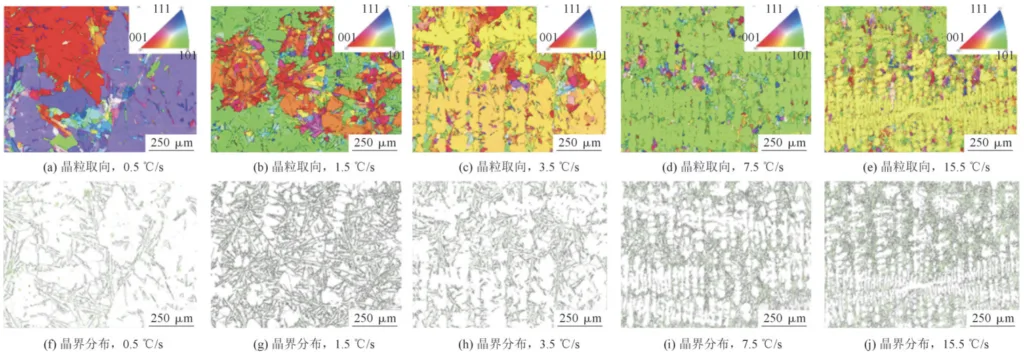
1. Overview:
- Title: Effects of Cooling Rate on Solidification Structure and Performance of ADC12 Alloy
- Author: CHENG Yugang, LI Junchen, ZHENG Daoyou, ZHAO Kui, QIAN Qijia, WANG Wenquan, WANG Kun
- Publication Year: 2025
- Publishing Journal/Academic Society: Special Casting & Nonferrous Alloys
- Keywords: Directional Solidification, Cooling Rate, ADC12 Aluminum Alloy, Dendrite, Mechanical Properties
2. Abstracts / Introduction
Abstract: Effects of cooling rate on solidification structure evolution and mechanical properties of ADC12 aluminum alloy were investigated through directional solidification experiments. The results indicate that as the cooling rate increases, the dendrite spacing of ADC12 aluminum alloy shows a downward trend and the grain orientation tends to be consistent. When the cooling rate is ≥1.5 °C/s, the downward trend slows down significantly. With the cooling rate of 15.5 °C/s, the distance between dendrite arms in the cross and longitudinal section is 18.28 and 18.14 µm, respectively. Grain refinement is helpful to improving the mechanical properties and hardness of alloy, where the tensile strength, elongation and microhardness of ADC12 aluminum alloy reach 280.89 MPa, 1.76% and 98.35 HV, respectively. SEM results reveal that the fracture surface of ADC12 aluminum alloy is transformed from brittle fracture to ductile/brittle mixed fracture as the dendrite spacing decreases, and the amounts of dimples on the fracture are increased.
3. Research Background:
Background of the Research Topic:
In the context of achieving "dual carbon" strategic goals and the development of new energy vehicles as a strategic emerging industry, hybrid electric vehicles, utilizing Dedicated Hybrid Transmissions (DHT), are crucial. DHT变速箱 aluminum alloy housings, often made of ADC12 casting aluminum alloy, face challenges due to their large size and susceptibility to deformation during heat treatment. Consequently, heat treatment strengthening is often avoided, relying on direct casting. Furthermore, variations in cooling rates across different sections of the DHT housing, due to uneven thickness, lead to significant differences in mechanical properties.
Status of Existing Research:
Existing research indicates that dendrite spacing, a key factor influencing the mechanical properties of aluminum alloy castings, is primarily affected by the cooling rate. Generally, a higher cooling rate results in smaller dendrite arm spacing and improved material mechanical properties [1-5]. Studies on single crystal high-temperature alloys and DZ22 high-temperature alloys have shown that increased cooling rates lead to reduced dendrite spacing and more compact solidification structures [9, 10].
Necessity of the Research:
Despite existing research on the relationship between cooling rate and microstructure in other alloys, there is a lack of comprehensive studies specifically focusing on the relationship between cooling rate and performance in ADC12 aluminum alloy. Therefore, this research aims to investigate the effects of cooling rate on the solidification structure evolution and mechanical properties of ADC12 alloy through directional solidification experiments. This study is intended to provide a reference for optimizing the preparation process of aluminum alloys.
4. Research Purpose and Research Questions:
Research Purpose:
The purpose of this research is to investigate the effect of cooling rate on the solidification structure evolution and mechanical properties of ADC12 alloy through directional solidification experiments, aiming to provide a basis for optimizing the preparation process of aluminum alloys.
Key Research:
This research focuses on:
- Investigating the evolution of solidification structure of ADC12 aluminum alloy under different cooling rates.
- Analyzing the effect of cooling rate on the dendrite spacing of ADC12 alloy.
- Evaluating the mechanical properties (tensile strength, elongation, microhardness) of ADC12 alloy solidified at different cooling rates.
- Examining the fracture morphology of ADC12 alloy under different cooling rates.
5. Research Methodology
Research Design:
Directional solidification experiments were conducted to simulate different cooling rates experienced by DHT housing sections. Five cooling rates (0.5 °C/s, 1.5 °C/s, 3.5 °C/s, 7.5 °C/s, and 15.5 °C/s) were selected based on AnyCasting software simulations of DHT casting.
Data Collection Method:
- Optical Microscopy: Axio-Scope.A1型 optical microscope was used to observe the microstructure after etching with Kroll’s reagent (HF+4%HNO₃ water solution).
- X-ray Diffraction (XRD): D8 Advance X-ray diffractometer (CuKα) was used for phase analysis.
- Scanning Electron Microscopy (SEM): PhenomXL scanning electron microscope was used for microstructure observation and phase identification.
- Mechanical Testing: Instron universal testing machine was used to evaluate tensile strength, elongation, and microhardness.
Analysis Method:
- EDS (Energy Dispersive Spectrometry): EDS point analysis was performed to analyze the composition of intermetallic compounds.
- Image analysis software: Software was used to measure dendrite arm spacing and grain size.
- Formula (2) and (3): Formula (2) $D = \sqrt{S/\pi}$ was used to calculate equivalent grain size (D), and Formula (3) $l = L/(N-1)$ was used to calculate dendrite arm spacing (l).
Research Subjects and Scope:
The research subject was commercial ADC12 aluminum alloy. The scope of the study involved investigating the effects of five different cooling rates (0.5 °C/s, 1.5 °C/s, 3.5 °C/s, 7.5 °C/s, and 15.5 °C/s) on the solidification structure and mechanical properties of this alloy.
6. Main Research Results:
Key Research Results:
- Microstructure Evolution: As the cooling rate increased, the dendrite spacing of ADC12 aluminum alloy decreased, and the grain orientation became more consistent. At cooling rates ≥1.5 °C/s, the reduction in dendrite spacing slowed down. At 15.5 °C/s, the transverse dendrite arm spacing was 18.28 µm, and the longitudinal spacing was 18.14 µm.
- Mechanical Properties: Grain refinement improved the mechanical properties and hardness. At a cooling rate of 15.5 °C/s, the tensile strength, elongation, and microhardness (HV) of ADC12 aluminum alloy reached 280.89 MPa, 1.76%, and 98.35 HV, respectively.
- Fracture Surface: SEM analysis showed that the fracture surface of ADC12 aluminum alloy transitioned from brittle fracture to ductile/brittle mixed fracture as dendrite spacing decreased, with an increase in dimples on the fracture surface.
- Phase Composition: ADC12 alloy mainly consisted of α-Al, eutectic Si, and Al₂Cu. Intermetallic compounds identified included α-Al₁₅(Fe,Mn)₃Si₂, Al₂Cu, 富Si phase, and β-AlFeSi phase.
Analysis of presented data:
- Figure 3: XRD patterns (Fig.3) show that as the cooling rate increases, the diffraction peak intensity of the (200) plane of α-Al decreases, while the (220) plane intensity increases, indicating a change in grain orientation.
- Figure 4: Grain orientation and grain boundary distribution maps (Fig.4) illustrate that at lower cooling rates (0.5 °C/s and 1.5 °C/s), grains are larger and randomly oriented. As cooling rate increases, grains become finer and more oriented, with a shift from <001> and <101> to <220> orientation at 15.5 °C/s. Grain boundary density also increases with cooling rate.
- Figure 5: Microstructure images (Fig.5) show that at lower cooling rates, the microstructure consists of coarse dendrites and eutectic phases. With increasing cooling rate, dendrite size decreases, and the microstructure becomes finer.
- Figure 7: Dendrite arm spacing (Fig.7) decreases with increasing cooling rate, following a negative correlation.
- Figure 8: Mechanical properties (Fig.8) including tensile strength, elongation, and hardness increase with increasing cooling rate.
- Figure 9: Fracture morphology images (Fig.9) show a transition from brittle fracture with cleavage surfaces at low cooling rates to a mixed ductile/brittle fracture with increased dimples at higher cooling rates.
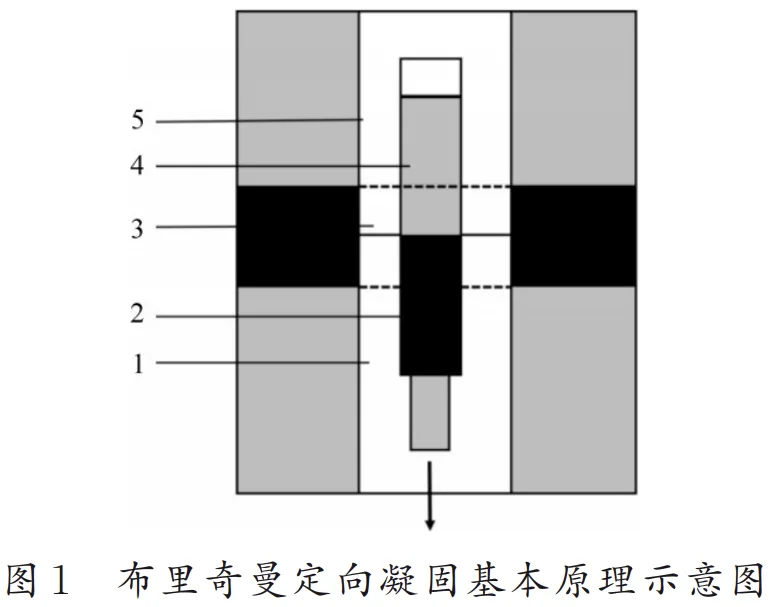
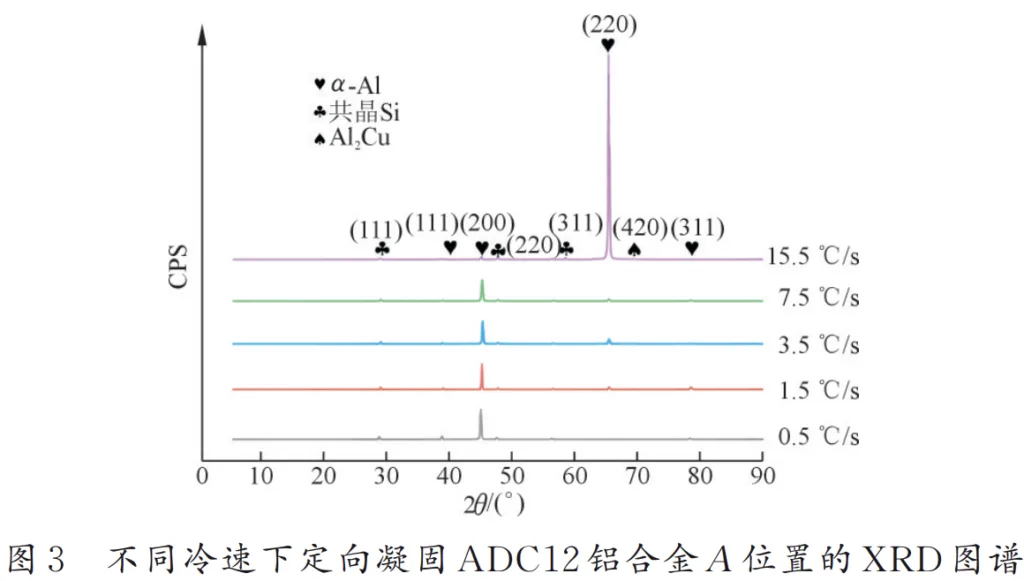
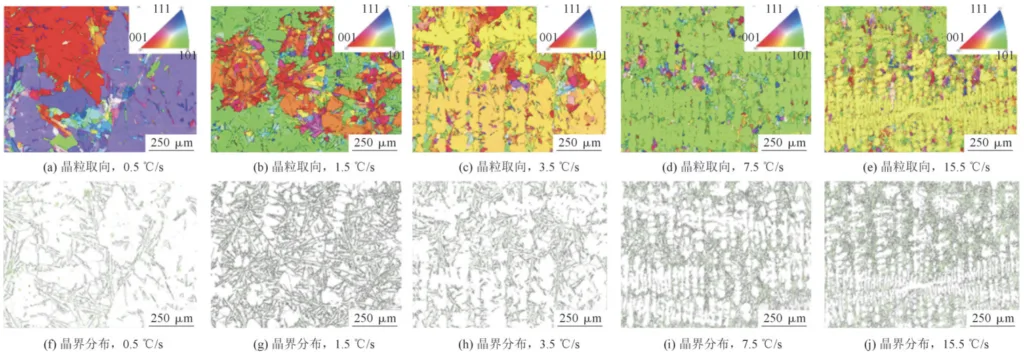
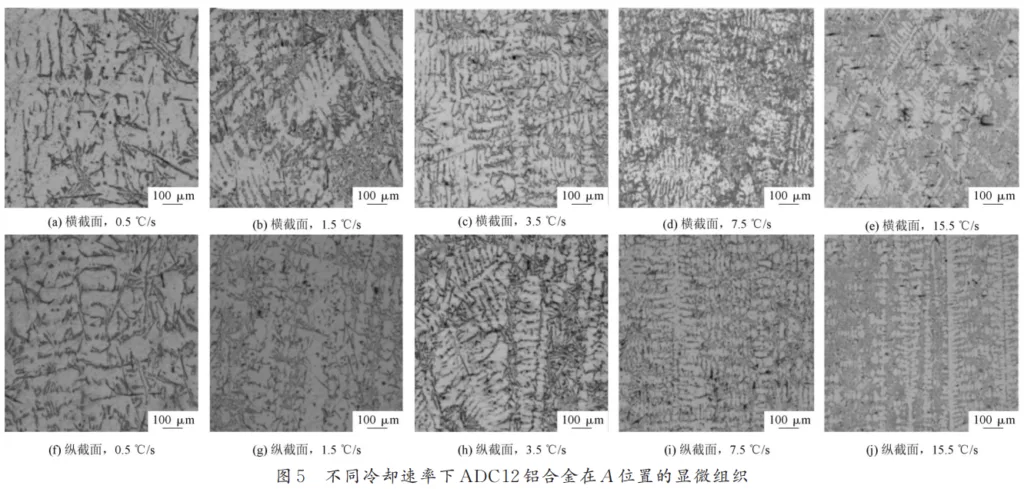
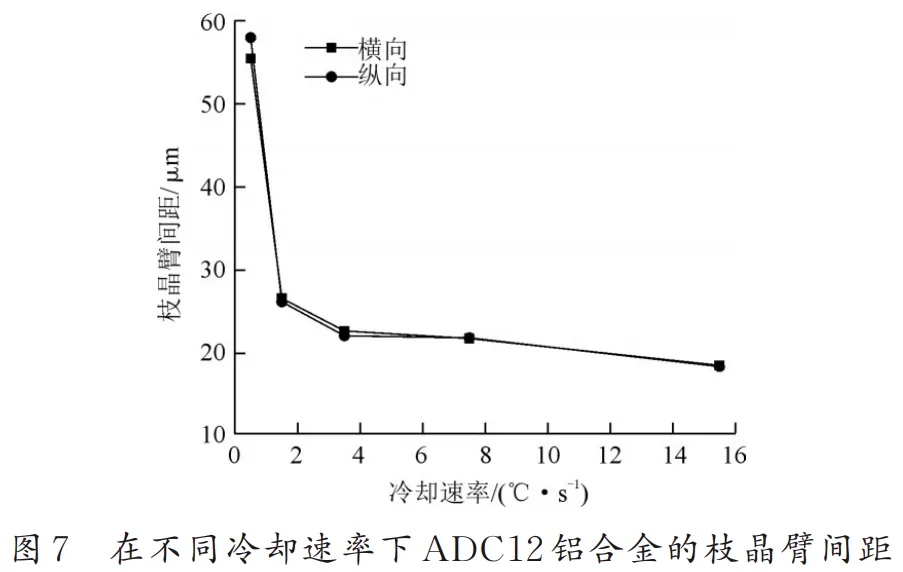
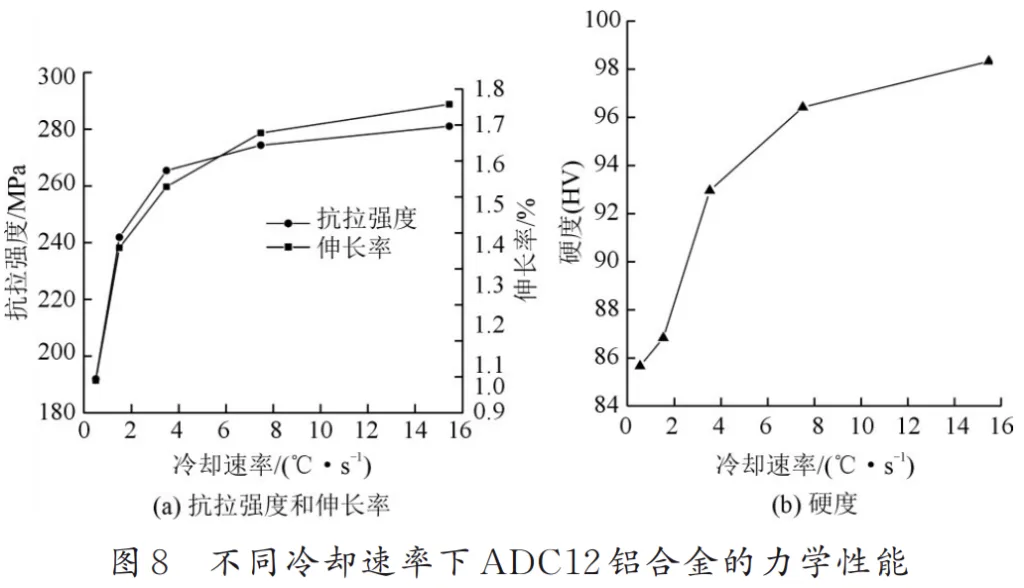
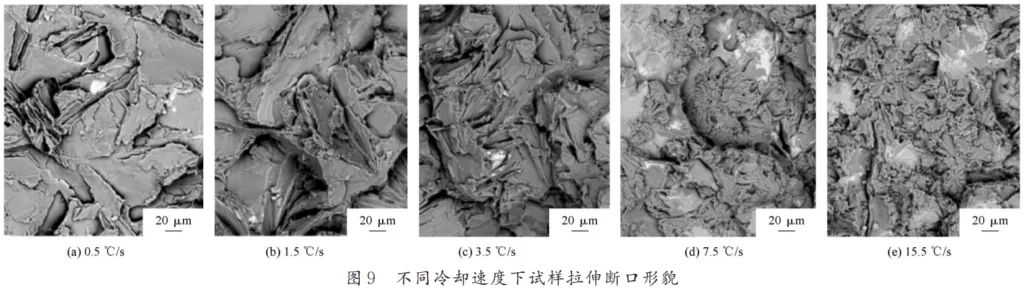
Figure Name List:
- Fig.1 Basic principle of Bridgman directional solidification
- Fig.2 Sampling positions and dimensions of directional solidified ADC12 aluminum alloy
- Fig.3 XRD patterns of directionally solidified ADC12 aluminum alloy at position A under different cooling rates
- Fig.4 Grain orientation and grain boundary distribution at position A under different cooling rates
- Fig.5 Microstructure of ADC12 aluminum alloy at position A under different cooling rates
- Fig.6 SEM morphologies of intermetallic compound in ADC12 aluminum alloy at different cooling rates
- Fig.7 Dendrite arm spacing of ADC12 aluminum alloy at different cooling rates
- Fig.8 Mechanical properties of ADC12 aluminum alloy at different cooling rates
- Fig.9 Tensile fracture morphologies of specimens at different cooling rates
7. Conclusion:
Summary of Key Findings:
This study demonstrates that increasing the cooling rate during directional solidification of ADC12 aluminum alloy refines the microstructure, reduces dendrite spacing, and enhances mechanical properties. Specifically, increasing the cooling rate to 15.5°C/s resulted in significant grain refinement, improved tensile strength, elongation, and hardness, and altered the fracture mode from brittle to mixed ductile/brittle.
Academic Significance of the Study:
This research provides quantitative data on the relationship between cooling rate, solidification structure, and mechanical properties of ADC12 aluminum alloy. It contributes to a deeper understanding of the solidification behavior of ADC12 alloy under varying cooling conditions and validates the theoretical relationship between cooling rate and dendrite spacing.
Practical Implications:
The findings suggest that controlling and increasing the cooling rate during the casting of ADC12 aluminum alloy components, such as DHT housings, can effectively improve their mechanical performance. This is crucial for applications requiring high strength and reliability without relying on post-casting heat treatments.
Limitations of the Study and Areas for Future Research:
The study focused on a limited range of cooling rates and directional solidification. Future research could explore:
- The effects of even higher cooling rates.
- The influence of cooling rate on other properties like fatigue and corrosion resistance.
- Optimization of casting processes to achieve desired cooling rates in complex ADC12 alloy components.
- Numerical simulation to predict microstructure and properties based on cooling rate variations in real castings.
8. References:
- [1] 张丁非,兰伟,丁培道,等.AZ91镁合金的凝固冷却速度与二次枝晶间距的定量关系研究[J]. 材料工程,2007(4):23-26.
- [2] 张炳荣,王斯勇,王一民,等.重力铸造铝合金发动机缸盖的二次枝晶间距研究[J].铸造技术,2008(11):1546-1 549.
- [3] MIGF, LIU XY, ZHU Z J, et al. Effects of chill casting processes on secondary dendrite arm spacing and densification of Al-Si-Mg alloy [J]. Transactions of Nonferrous Metals Society of China, 2007, 17(5):1012-1 017.
- [4] KALKA M, ADAMIEC J. Complex procedure for the quantitative description of an Al - Si cast alloy microstructure [J]. Materials Characterization, 2006, 56(4-5):373-378.
- [5] 孙小平,石路,管仁国,等.铝合金晶粒细化的研究进展与发展趋势[J].有色矿冶,2010,26(5):32-35.
- [6] 康永飞,李浩,白朴存,等.冷却速率对复杂铝合金铸件组织的影响[J].铸造,2020,69(1):40-45.
- [7] MALEKAN M, NAGHDALIS, ABRISHAMIS, et al. Effect of cooling rate on the solidification characteristics and dendrite coher-ency point of ADC12 aluminum die casting alloy using thermal analy-sis[J]. Journal of Thermal Analysis and Calorimetry, 2016, 124(2): 601-609.
- [8] 王孝国,李秋书,郭璐,等.区熔式定向凝固技术对7075铝合金微观组织和硬度的影响研究[J].热加工工艺,2019,48(13): 26-29,33.
- [9] 冯小辉,李应举,杨院生,等.单晶高温合金凝固组织演化数值模拟与预测[J].钢铁研究学报,2011,23(S2):365-368.
- [10]顾林喻,刘忠元,史正兴,等,高梯度快速定向凝固下DZ22高温合金的显微偏析[J].中国有色金属学报,1996(2):112-115.
- [11]喻亮,刘远,严宇龙,等.热轧变形量对含0.5%B的6063铝合金晶粒取向、织构及再结晶的影响[J].热加工工艺,2024,53(15): 121-125.
- [12]武雅璐,武建国,李秋书,等.定向凝固条件下铝合金力学性能和导电性研究[J].热加工工艺,2016,45(21):69-73.
- [13]林嘉华.铝合金凝固过程空间界面传热与枝晶生长数值模拟的研究[D].广州:华南理工大学,2019.
- [14]汪鹏程,柳飞洪,闫赛飞,等,低过热度倾斜板流变压铸对ADC12组织及力学性能的影响[J].特种铸造及有色合金,2022,42(5): 540-545.
- [15] SAZIANA S, ZAIDI MO, HOSSEIN A B, et al. Mechanical properties and microstructures of a modified Al-Si-Cu alloy prepared by thixoforming process for automotive connecting rods [J]. Journal of Materials Research and Technology, 2020, 10: 1086-1102.
- [16] SAMATS, OMAR M Z, BAGHDADI A H, et al. Mechanical properties and microstructures of a modified Al-Si-Cu alloy prepared by thixoforming process for automotive connecting rods [J]. Journal of Materials Research and Technology, 2020, 10:1 086-1102..
- [17]胡汉起,金属凝固原理(第2版)[M].北京:机械工业出版社,2000.
- [18]朱锐祥、稀土元素(Ce La Sm)对压铸铝合金组织与性能的影响[D].合肥:合肥工业大学,2019.
- [19]赵丽红,毕涛,低压铸造铝合金车轮轮辋断裂分析及结构优化[J].特种铸造及有色合金,2022,42(1):119-121.
- [20]张钧林.材料科学基础[M].北京:化学工业出版社,2006.
- [21]车家宝,廖敦明,孙飞,等.铝合金铸件凝固过程二次枝晶臂间距模拟计算[J].铸造,2020,69(4):382-387.
9. Copyright:
- This material is "[CHENG Yugang, LI Junchen, ZHENG Daoyou, ZHAO Kui, QIAN Qijia, WANG Wenquan, WANG Kun]"'s paper: Based on "[Effects of Cooling Rate on Solidification Structure and Performance of ADC12 Alloy]".
- Paper Source: DOI:10.15980/j.tzzz.T20230459
This material was created to introduce the above paper, and unauthorized use for commercial purposes is prohibited.
Copyright © 2025 CASTMAN. All rights reserved.