International Journal of Metalcasting volume 15, pages839–851 (2021)Cite this article
- 175 Accesses
- 1 Citations
- Metrics
Abstract
The demand for producing essential cast parts and the design requirements for superior engineering performance have increased in recent years. Sand cores used in conventional aluminum cast parts are harmful to the environment, which limits their application. Utilizing water-soluble cores in the aluminum casting industry is expected to be an environmentally friendly approach due to recyclability of the salt cores. In this study, water-soluble salt cores were made from chloride- and/or carbonate-containing salts in various amounts. The salts were melted and cast into steel molds to obtain salt cores. The salt cores were subjected to three-point bending tests to determine their mechanical strength, the melting points were determined with thermal analyses, and the water solubility was measured at room temperature and 50 °C. A maximum bending strength of 17.19 MPa, a maximum melting point of 776 °C and a maximum water solubility of 89 g salt/100 ml water were obtained for the samples with compositions of 75% KCl–25% K2CO3 and 25% Na2CO3–75% K2CO3, respectively. Fractographs of the samples used in bending tests were taken by a still camera in macro mode, and from these fractured surfaces, scanning electron microscopy studies were performed. The X-ray diffraction pattern of the sample exhibiting optimal properties (28.3% Na2CO3 and 71.7% K2CO3) also showed that K2CO3, NaKCO3 and KNaCO3 phases were present in the structure, as expected. An actual casting process with aluminum die casting of an automotive part was also performed. The diecast aluminum part was subjected to a leak-proof test, and X-ray images were used to check for porosity in the part.
Introduct
There is an increasing demand for components that can provide increased performance, efficient designs and complex internal passages. Although conventional sand core technology is used in a multitude of casting techniques to meet these needs, it has achieved limited success in processes that utilize pressures, such as low-pressure casting and, especially, high-pressure die casting (HPDC).
The cores used in aluminum gravity die casting and lowpressure die casting are sand based and can be produced by cold box, hot box or shell methods. In high-pressure (injection) die casting, steel cores are often used, which makes the design step a constraining factor in the production of complex-shaped parts. The difficulty in the mechanical cleaning of sand cores after casting is that it is time intensive, results in energy losses and suffers from surface quality deterioration and deformation; in addition, the burnt sand core contains organic compounds that form hazardous waste, posing a serious problem in the industry. To overcome all these problems, in this study, the use of recyclable salt cores in the casting of low-melting-temperature metals or alloys is discussed.
Inorganic-based salt core production has been performed since the twentieth century. The use of salt-based cores in foundries began in the 1970s and became widespread in the production of aluminum diesel engine pistons in the 1990s.1,2 Inorganic salt cores have been made possible by the use of gravity die casting and low- and high-pressure casting methods, as well as the sintering of dry compacted salt powders.2–6 The salt cores were used in casting aluminum, low-meltingtemperature magnesium, zinc and other metal parts.7 Salt cores with refractory additions of alumina, glass fiber and composite cores were also studied, and it was reported that additions had a tendency to increase the mechanical strength of the cores.8 Salt cores coated with refractory coatings and infiltrated with silica were studied to assess the mechanical strength and surface quality, and the findings indicated that the surfaces and salt cores were of high quality.6,9 The raw salt-containing materials can be composed of carbonate, chloride, sulfate, bromide and phosphates of alkali metals. These salts are also listed in the literature as a lost or expendable core material when they are used in casting processes because they are soluble in water.10
The main advantages of salt cores are as follows:
- Salt cores have sufficient strength for use in gravity, high-pressure and low-pressure die casting technologies.
- They are subject to easy core removal after casting.
- Their use reduces the costs of complex-shaped parts, and they have short cycle times in production compared with traditional sand-cored production.
- Salt cores allow more design freedom to create complex designs.
- They can reduce weight due to their thin-walled designs.
- Salt cores reduce the amount of machining after casting.
- The core is environmentally friendly; it does not generate waste, and the related compounds can be fed back into the system.
The production of salt cores can occur by three methods:
a. Squeezing
b. Shooting or blowing with a binder
c. Casting of molten salt
In the casting method, the salt and ingredients to be used are melted in a crucible and poured into a core mold. Casting can be performed by the gravity casting technique, as well as by injection molding.11,12 Because of their high density, the cores dissolve less in water in this method than in other methods. The volume shrinkage during solidification of the salt core is quite high. In addition, the produced cores can absorb moisture as they sit before use.1,9 Currently, the salt cores for engine pistons, engine block water jackets and valve body parts can be cast by this method. Especially in the casting of low-melting-point metals, such as aluminum and magnesium, all core production methods can be used. The design of thin-walled parts is preferred in gravity casting production due to the short cycle times in production and the reduced amount of machining after casting compared with especially sandcored casting methods. With the development of simulation software in recent years, the preproduction risk zones of these cores, the amount of air trapped in the mold and the stress zones can be seen at the design stage, and necessary interventions can be made.5,7,12–1
Paper Summary:
This paper introduction was written based on the ['EFFECTS OF COMPOSITION ON THE PHYSICAL PROPERTIES OF WATER-SOLUBLE SALT CORES'] published by ['International Journal of Metalcasting'].
1. Overview:
- Title: EFFECTS OF COMPOSITION ON THE PHYSICAL PROPERTIES OF WATER-SOLUBLE SALT CORES
- Author: Cihan Cantas, Bedri Baksan
- Publication Year: 2020
- Publishing Journal/Academic Society: International Journal of Metalcasting
- Keywords: salt core, water solubility, bending strength, microstructure characteristics, macrostructure characteristics
2. Abstracts
The demand for producing essential cast parts and the design requirements for superior engineering performance have increased in recent years. Sand cores used in conventional aluminum cast parts are harmful to the environment, which limits their application. Utilizing water-soluble cores in the aluminum casting industry is expected to be an environmentally friendly approach due to recyclability of the salt cores. In this study, water-soluble salt cores were made from chloride- and/or carbonate-containing salts in various amounts. The salts were melted and cast into steel molds to obtain salt cores. The salt cores were subjected to three-point bending tests to determine their mechanical strength, the melting points were determined with thermal analyses, and the water solubility was measured at room temperature and 50 °C. A maximum bending strength of 17.19 MPa, a maximum melting point of 776 °C and a maximum water solubility of 89 g salt/100 ml water were obtained for the samples with compositions of 75% KCl–25% K2CO3 and 25% Na2CO3-75% K2CO3, respectively. Fractographs of the samples used in bending tests were taken by a still camera in macro mode, and from these fractured surfaces, scanning electron microscopy studies were performed. The X-ray diffraction pattern of the sample exhibiting optimal properties (28.3% Na2CO3 and 71.7% K2CO3) also showed that K2CO3, NaKCO3 and KNaCO3 phases were present in the structure, as expected. An actual casting process with aluminum die casting of an automotive part was also performed. The diecast aluminum part was subjected to a leak-proof test, and X-ray images were used to check for porosity in the part.
3. Research Background:
Background of the Research Topic:
In contemporary manufacturing, the pursuit of intricate cast components with enhanced engineering performance is paramount. Conventional sand cores, while widely utilized in aluminum casting, present environmental concerns that impede their broader application. Water-soluble salt cores emerge as a promising, eco-conscious alternative, primarily due to their inherent recyclability. This research delves into the fabrication and characterization of water-soluble salt cores derived from chloride- and carbonate-based salts, exploring their potential in die casting applications.
Status of Existing Research:
The utilization of inorganic salt cores dates back to the twentieth century, gaining traction in foundries during the 1970s and becoming prevalent in aluminum diesel engine piston production in the 1990s [1, 2]. The advent of gravity die casting, low-pressure, and high-pressure die casting techniques, alongside advancements in sintering dry compacted salt powders [2-6], facilitated the development of inorganic salt cores. These cores have been employed in casting aluminum, low-melting-temperature magnesium, zinc, and other metals. Prior research has explored salt cores with refractory additions such as alumina, glass fiber, and composites, noting a tendency for increased mechanical strength with such additions [7]. Studies on salt cores coated with refractory materials and infiltrated with silica have also been conducted to evaluate mechanical strength and surface quality, demonstrating high quality surfaces and salt cores [6, 9]. Raw materials for salt cores encompass carbonates, chlorides, sulfates, bromides, and phosphates of alkali metals, recognized as expendable core materials due to their water solubility [10]. Salt cores offer several advantages, including sufficient strength for gravity, high-pressure, and low-pressure die casting; ease of removal post-casting; reduced costs for complex parts; shorter production cycles; greater design freedom; potential for weight reduction through thin-walled designs; and minimized post-casting machining. Furthermore, they are environmentally benign, generating no waste as related compounds can be recycled back into the system. Production methods include squeezing, shooting or blowing with a binder, and casting of molten salt.
Necessity of the Research:
Conventional sand core technology, while meeting certain demands, faces limitations in pressure-intensive processes like low-pressure and high-pressure die casting (HPDC). Mechanical removal of sand cores is labor-intensive, energy-consuming, and can compromise surface quality. Burnt sand cores also contain organic compounds, posing hazardous waste issues. This study addresses these challenges by investigating recyclable salt cores for casting low-melting-temperature metals and alloys, aiming to overcome the environmental and efficiency drawbacks of traditional sand cores.
4. Research Purpose and Research Questions:
Research Purpose:
This study aims to evaluate the impact of varying salt compositions on the physical properties of water-soluble salt cores. The ultimate goal is to identify optimal salt core formulations suitable for die casting applications, enhancing both process efficiency and environmental sustainability.
Key Research:
The key research objectives are to characterize and optimize the following properties of water-soluble salt cores:
- Mechanical Strength: Quantifying the bending strength to ensure structural integrity during casting.
- Melting Point: Determining the melting temperature to ensure compatibility with casting alloys and process temperatures.
- Water Solubility: Assessing the solubility in water for efficient and residue-free core removal after casting.
- Microstructure and Macrostructure Characteristics: Analyzing the internal structure and surface features to understand their influence on physical properties.
- Performance in Aluminum Die Casting: Validating the practical applicability of salt cores through an actual aluminum die casting process.
Research Hypotheses:
The central hypotheses guiding this research are:
- Altering the compositional ratios of chloride- and carbonate-based salts will significantly affect the mechanical strength, melting point, and water solubility of the resulting salt cores.
- Through systematic variation and analysis of salt compositions, an optimal formulation can be identified that maximizes bending strength, melting point, and water solubility for enhanced die casting performance.
5. Research Methodology
Research Design:
This research employed an experimental design focused on compositional variation. Salt cores were formulated using different weight percentages of sodium chloride (NaCl), potassium chloride (KCl), sodium carbonate (Na2CO3), and potassium carbonate (K2CO3). Double, triple, and quadruple mixtures were created with 25% weight differences to systematically explore a range of compositions, as detailed in Table 1 of the original paper.
Data Collection Method:
A comprehensive suite of experimental techniques was utilized to characterize the physical properties of the salt cores:
- Bending Strength: Three-point bending tests were conducted using a Shimadzu AG-IS 250 universal strength testing machine to measure the mechanical strength at room temperature. A constant crosshead speed of 2 mm/s with a 1 kN load cell was maintained.
- Melting Point Determination: Thermal analyses were performed using Differential Scanning Calorimetry (DSC, PerkinElmer Diamond DSC) for compositions with melting points up to 725 °C, and Thermogravimetric Analysis (TG/DTA, PerkinElmer TG/DTA 6300) for higher melting points. Samples were tested in copper pans.
- Water Solubility: Water solubility was measured using deionized water on a heated magnetic stirrer at 50 °C with a 1500 rpm mixer speed. Saturation limits were determined by testing multiple samples until undissolved salt remained.
- Fractography: Macrographs of fractured samples from bending tests were captured using a Canon EOS 40D digital camera. Scanning Electron Microscopy (SEM, Jeol JSM-5600LV) and X-ray Diffraction (XRD, PANalytical XRD) were employed for detailed microstructure analysis.
- Aluminum Die Casting: An actual casting process was conducted using aluminum die casting of an automotive part to validate the practical application of the salt cores. Leak-proof and X-ray porosity tests were performed on the die-cast part.
Analysis Method:
The collected data were subjected to rigorous analysis to derive meaningful conclusions:
- Statistical Optimization: Minitab 17 statistical software was used to optimize salt core composition for maximum melting point and water solubility, considering bending strength as a key factor.
- Analysis of Variance (ANOVA): ANOVA was employed to assess the effects of individual salt components (NaCl, KCl, Na2CO3, K2CO3) on bending strength and water solubility.
- Microstructural Analysis: SEM images were analyzed to characterize fracture surfaces and dendritic solidification patterns. XRD patterns were used to identify crystalline phases present in the salt core compositions.
Research Subjects and Scope:
The research focused on water-soluble salt cores composed of chloride- and carbonate-based salts, specifically NaCl, KCl, Na2CO3, and K2CO3. The scope was limited to compositions suitable for casting low-melting-point alloys, particularly aluminum alloys used in automotive components. The study investigated a range of binary, ternary, and quaternary salt mixtures to identify formulations with enhanced physical properties for die casting applications.
6. Main Research Results:
Key Research Results:
The experimental investigation yielded several key findings regarding the physical properties of water-soluble salt cores with varying compositions:
- Maximum Bending Strength: A composition of 75% KCl–25% K2CO3 (Sample 1) exhibited the highest bending strength of 17.19 MPa, as shown in Table 1 and Figure 4.
- Maximum Melting Point: The highest melting point of 776 °C was achieved with a 25% Na2CO3-75% K2CO3 mixture (Sample 30), as detailed in Table 1.
- Maximum Water Solubility: Sample 30 (25% Na2CO3-75% K2CO3) also demonstrated the highest water solubility, reaching 89 g salt/100 ml water (Table 1).
- Optimal Composition (Statistical Analysis): Statistical optimization using Minitab 17 identified an optimal composition of 28.3% Na2CO3 and 71.7% K2CO3. This formulation yielded a calculated melting point of 756.4 °C, a water solubility of 81.36 g/100 ml, and a bending strength of 3.35 MPa. Experimental validation of this optimal composition resulted in a melting temperature of 760 °C, water solubility of 89.5 g/100 ml, and bending strength of 5.26 MPa, closely aligning with computational predictions.
- Phase Identification: XRD analysis of the optimal composition (28.3% Na2CO3 and 71.7% K2CO3) confirmed the presence of K2CO3, NaKCO3, and KNaCO3 phases (Figure 11), as anticipated.
- Aluminum Die Casting Validation: Successful aluminum die casting of an automotive part was achieved using the developed salt cores, demonstrating their practical applicability in industrial settings. The die-cast aluminum part passed leak-proof tests and exhibited acceptable porosity levels based on X-ray inspection.
Analysis of presented data:
- Table 1 systematically presents the compositional design, bending strength, maximum solubility, and melting points for all tested salt core samples, providing a comprehensive dataset for comparative analysis.
- Figure 4 graphically illustrates the bending strength of each sample, highlighting the superior mechanical performance of specific compositions.
- Figure 5 displays the mean effects plot for bending strength, revealing the individual contributions of NaCl, KCl, Na2CO3, and K2CO3 to the overall strength of the salt cores.
- Figure 6 shows the solubility of pure salts in water at various temperatures, demonstrating the temperature dependence of solubility for different salt components.
- Figure 7 presents a solubility-density diagram for the NaCl-Na2CO3-K2CO3 ternary system, visualizing the solubility behavior across compositional variations.
- Figure 8 illustrates the mean effects plot for solubility, indicating the influence of each salt component on the water solubility of the cores.
- Figure 9 provides fractographs of salt cores with different compositions, offering visual insights into fracture behavior and microstructure.
- Figure 10 presents SEM micrographs of the fractured optimized composition salt core, revealing detailed microstructural features.
- Figure 11 shows the XRD pattern of binary K2CO3 and Na2CO3 mixtures, confirming the phase composition of the optimized salt core.
- Figure 17 displays X-ray photographs of a cast part, demonstrating the successful application of salt cores in producing complex geometries with acceptable internal quality.
Figure Name List:
- Figure 1. Core casting mold design (all measures are in mm)16.
- Figure 2. SAE 1040 steel core molds.
- Figure 3. Porosity in chloride-containing sample (Sample #29).
- Figure 4. Bending strength of the samples.
- Figure 5. Mean effects plot for the bending strength.
- Figure 6. Solubility of pure salts in water at various temperatures (g/100 ml water).
- Figure 7. Solubility-density diagram of the NaCI-Na2CO3-K2CO3 triple system.
- Figure 8. Mean effects plot for the solubility of salts.
- Figure 9. Fractographs of salt cores with different compositions.
- Figure 9. continued
- Figure 10. SEM micrographs of the fractured optimized composition salt core (28.3% Na2CO3 and 71.7% K2CO3).
- Figure 11. XRD pattern of binary K2CO3 and Na2CO3 mixtures.
- Figure 12. The salt core and aluminum cast part under laboratory conditions.
- Figure 13. Photographs of the salt core cast into the steel die and the cast salt core in the mold.
- Figure 14. The cast salt core.
- Figure 15. Gravity die casting of aluminum with a salt core.
- Figure 16. Cross-sectional view of a cast part with a salt core.
- Figure 17. X-ray photographs from different sections of a cast part.
8. Figures:
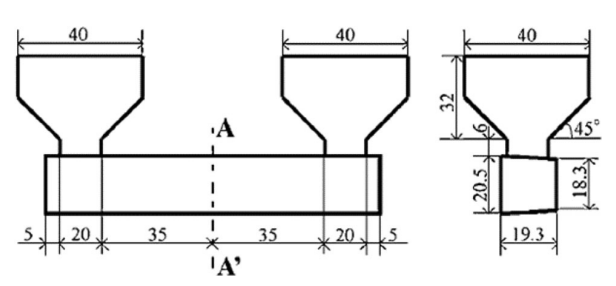
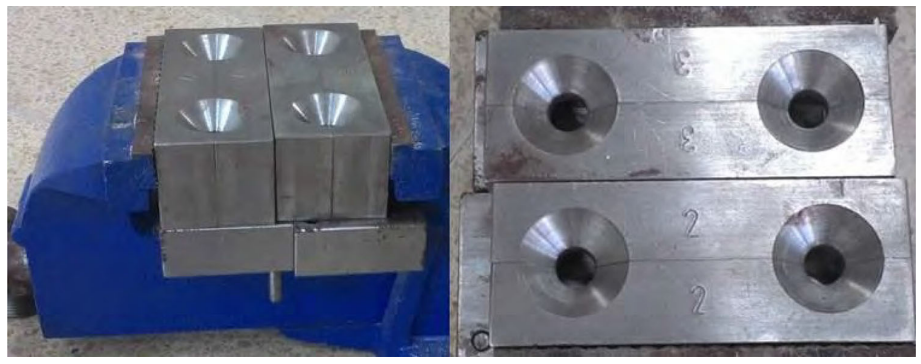
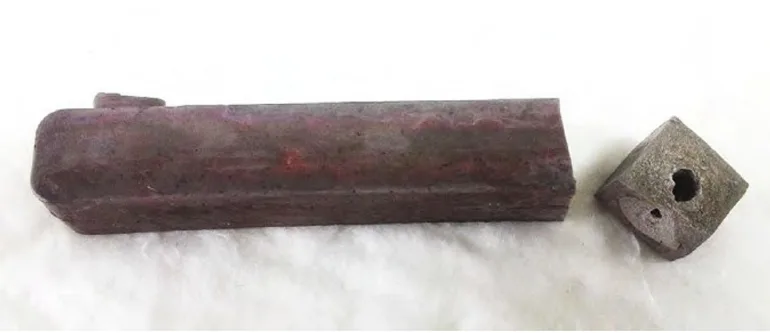
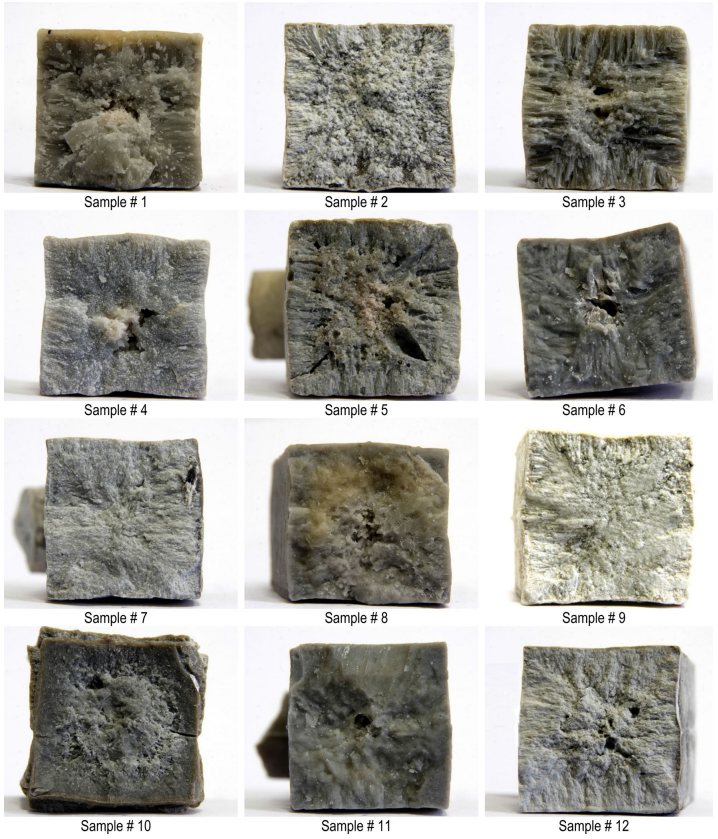
Optimization of Salt Core Composition
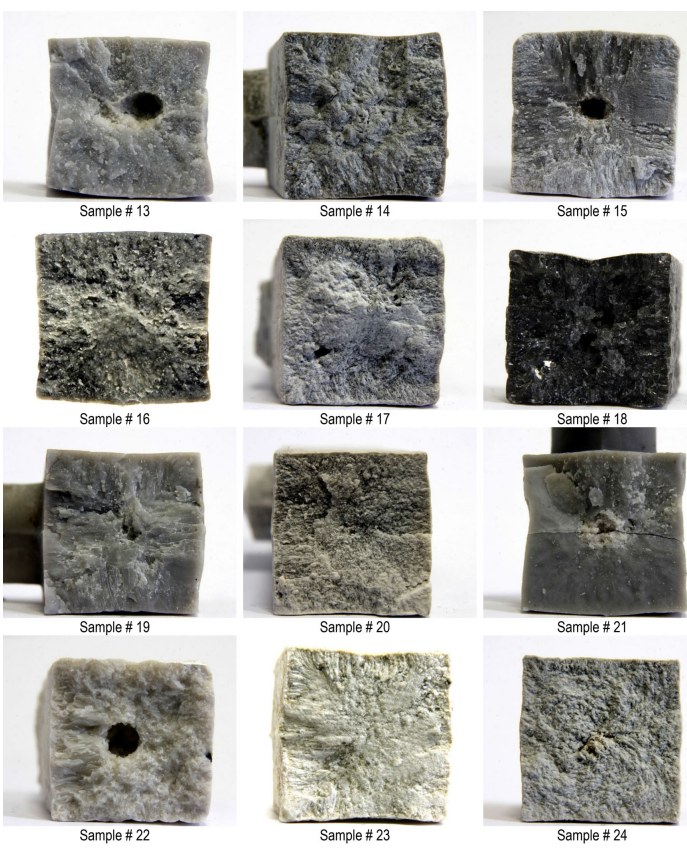
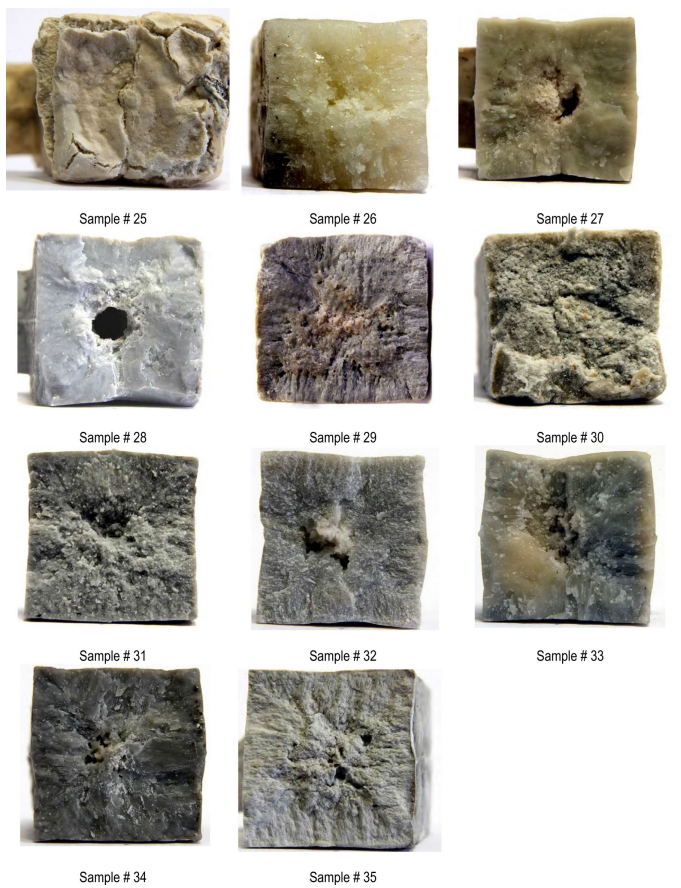
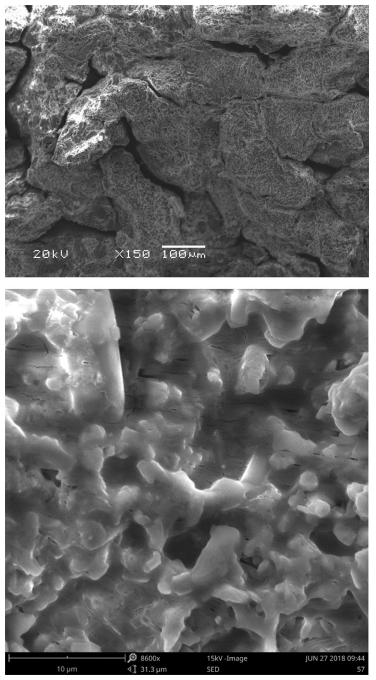
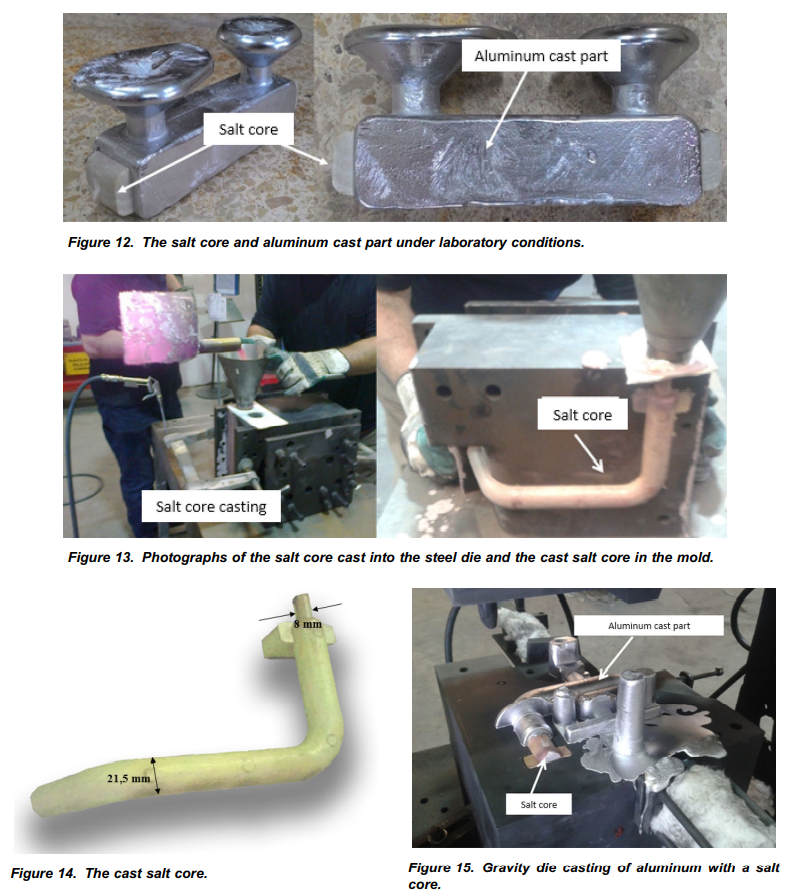
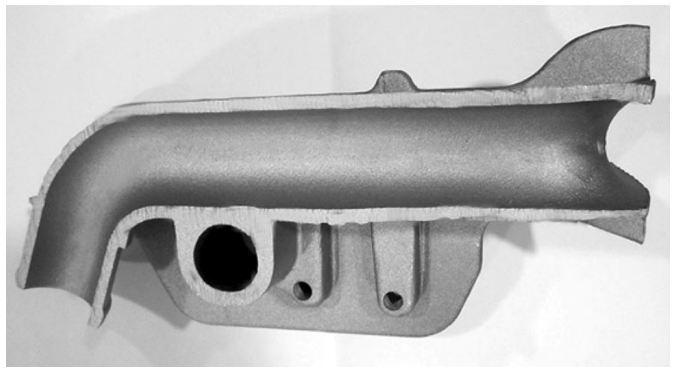
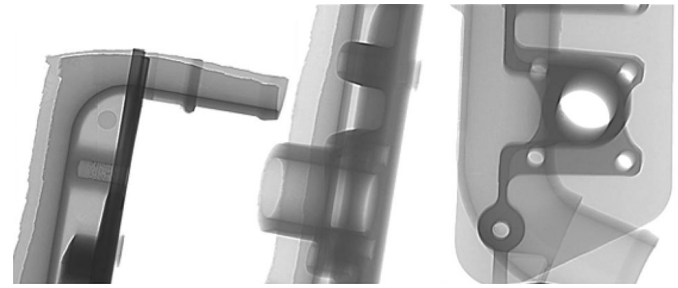
7. Conclusion:
Summary of Key Findings:
This study concludes that the composition of water-soluble salt cores significantly influences their physical properties. Cores with high chloride content (KCl, NaCl) exhibit greater brittleness compared to carbonate-containing cores (K2CO3, Na2CO3), potentially due to larger dendritic structures that promote crack propagation. For applications requiring robust salt cores, carbonate-based formulations are preferable. Chloride-containing cores also demonstrate higher shrinkage ratios (1-3%) than carbonate cores (0.3-0.5%). Furthermore, carbonate cores are more hygroscopic than chloride cores, necessitating immediate use or humidity protection post-production. Despite these considerations, the study demonstrates that salt cores, particularly carbonate-based compositions, possess sufficient strength for injection molding processes, offering an advantage over steel cores for complex part geometries. Optimal salt core formulations for die casting applications should prioritize carbonate components to achieve a balance of high strength, water solubility, and melting point.
Academic Significance of the Study:
This research provides a comprehensive dataset and analysis of the physical properties of water-soluble salt cores across a wide range of compositions. It significantly contributes to the fundamental understanding of how salt composition affects core performance in die casting. The findings offer valuable insights for material selection and formulation strategies in the development of advanced water-soluble cores.
Practical Implications:
The identification of optimal salt core compositions, particularly the 28.3% Na2CO3 and 71.7% K2CO3 mixture, offers immediate practical benefits for the die casting industry. These formulations enable the production of complex aluminum parts with enhanced efficiency and reduced environmental impact through the use of recyclable, water-soluble cores. The study validates the feasibility of using these salt cores in industrial aluminum die casting applications, providing a pathway for adopting more sustainable core technologies.
Limitations of the Study and Areas for Future Research:
While this study provides valuable insights, it primarily focused on low-melting-temperature aluminum alloys. Further research is recommended to explore the applicability of water-soluble salt cores for casting high-melting-temperature alloys and metals. Investigating the incorporation of refractories and/or binders into salt core formulations could also expand their application range and enhance their properties for more demanding casting conditions.
References
- [1]P. Jelinek et al., Development of Foundry Cores Based on Inorganic Salts. Materiali in Tehnologije 47(6), 689–693 (2013)
- [2]Y. Kaneko, A.M., New developments in water soluble salt cores for die casting, in 6th SDCE International Die Casting Congress (1970, The Society of Die Casting Engineers Inc.: Cleveland, Ohio, USA)
- [3]Yamada, Y., Yaokawa, J., Yoshii, H., Anzai, K., Noda, Y., Developments and Application of Expendable Salt Core Materials for High Pressure Die Casting to Apply Closed-Deck Type Cylinder Block, in JSAE-Report. 2007, Society of Automotive Engineers Japan. p. 1–5
- [4]P. Zhou et al., Microstructures and performance of CaO-based ceramic cores with different particle size distributions for investment casting. Mater. Res. Express. 5(2), 025202 (2018)Article Google Scholar
- [5]B. Fuchs, H. Eibisch, C. Korner, Core viability simulation for salt core technology in high-pressure die casting. Int. J. Metalcast. 7(3), 39–45 (2013). https://doi.org/10.1007/BF03355557CAS Article Google Scholar
- [6]M. Merchán et al., Research on coatings and infiltration to strengthen ceramic lost cores used in high-pressure die casting processes. Int. J. Metalcast. 13(3), 597–603 (2019). https://doi.org/10.1007/s40962-018-00301-0CAS Article Google Scholar
- [7]R. Huang, B. Zhang, Study on the composition and properties of salt cores for zinc alloy die casting. Int. J. Metalcast. 11(3), 440–447 (2017). https://doi.org/10.1007/s40962-016-0086-7Article Google Scholar
- [8]S. Tu et al., Fabrication and characterization of high-strength water-soluble composite salt core for zinc alloy die castings. Int. J. Adv. Manuf. Technol. 95(1), 505–512 (2018)Article Google Scholar
- [9]P. Jelinek et al., Advances in technology of soluble cores for die castings. Arch. Found. Eng. 15(2), 29–34 (2015)CAS Article Google Scholar
- [10]P. Jelínek, E. Adámková, Lost cores for high-pressure die casting. Arch. Found. Eng. 14(2), 101–104 (2014)Article Google Scholar
- [11]H. Michels, M. Bünck, A. Bührig-Polaczek, Suitability of lost cores in rheocasting process. Trans. Nonferr. Met. Soc. China 20, s948–s953 (2010)Article Google Scholar
- [12]P.P. Zhou et al., Optimization of the injection molding process for development of high performance calcium oxide -based ceramic cores. Mater. Res. Express. 5(2), 1 (2018)Google Scholar
- [13]Lagler, M., Use of Simulation to Predict the Viability of Salt Cores in HPDC Process. Die Casting Engineer, 2013(July), p. 16–17
- [14]H.I. Kurt, Optimization of tensile strength of Al Alloys with Mg and Ti. El-Cezeri J. Sci. Eng. 4(1), 1 (2017)Google Scholar
- [15]H.I. Kurt, I.H. Guzelbey, S. Salman, An experimental study of investigating the relationships between structures and properties of al alloys included with high Mg and high Ti. Int. J. Mater. Prod. Technol. 56(3), 271–283 (2018)CAS Article Google Scholar
- [16]J. Yaokawa et al., Strength of salt core composed of alkali carbonate and alkali chloride mixtures made by casting technique. Mater. Trans. 48(5), 1034–1041 (2007)CAS Article Google Scholar
- This material is "Cihan Cantas, Bedri Baksan"'s paper: Based on "EFFECTS OF COMPOSITION ON THE PHYSICAL PROPERTIES OF WATER-SOLUBLE SALT CORES".
- Paper Source: https://doi.org/10.1007/s40962-020-00511-5