This article introduces the paper "Effect of melt cleanliness on the formation of porosity defects in automotive aluminium high pressure die castings".
1. Overview:
- Title: Effect of melt cleanliness on the formation of porosity defects in automotive aluminium high pressure die castings
- Authors: C. Tian, J. Law, J. van der Touw, M. Murray, J.-Y. Yao, D. Graham, D. St. John
- Year of Publication: 2002
- Journal/Conference: Journal of Materials Processing Technology 122 (2002) 82-93
- Keywords:
- Porosity
- Casting porosity
- High pressure die casting
- Melt cleanliness
- Inclusions
2. Research Background:
- Social/Academic Context of Research Topic:
- Porosity is a major quality problem in cast automotive components produced by high pressure die casters.
- Porosity leads to leaking problems, surface defects, and machining problems.
- High pressure die casting porosity is classified into gas porosity, shrinkage porosity, and flow porosity, all intrinsic to the process.
- Melt cleanliness, specifically inclusions and dissolved hydrogen, is suspected to affect porosity formation.
- Die casters observe increased porosity when using 100% returns (scrap) without adequate treatment, sometimes leading to "porosity outbreaks" where up to 80% of castings fail quality requirements.
- Limitations of Existing Research:
- Existing research has not fully explored the link between melt cleanliness and porosity in high pressure die castings under industrial production conditions.
- The specific mechanisms by which melt cleanliness affects porosity in this context are not completely understood.
- Necessity of Research:
- To identify the cause of porosity outbreaks in industrial settings.
- To investigate the link between molten metal quality and the quality of high pressure die castings.
- To provide insights for preventing porosity and improving casting quality by controlling melt cleanliness.
3. Research Objectives and Research Questions:
- Research Objective:
- To experimentally investigate the effect of melt cleanliness on the formation of porosity defects in automotive aluminium high pressure die castings under actual industrial production conditions.
- Core Research Question:
- Does melt cleanliness, specifically the level of inclusions in the melt, affect the probability of rejection due to excessive porosity in critical locations of high pressure die castings?
- Research Hypothesis:
- The probability of rejection due to excessive porosity in critical locations of high pressure die castings increases as the number of inclusions in the melt increases.
4. Research Methodology
- Research Design:
- Experimental investigation conducted under actual industrial production conditions at Nissan Casting Australia Pty Ltd. (NCAP).
- Three types of experiments were performed: small-scale batch experiments, large-scale batch experiments, and large-scale consecutive trials.
- Melt cleanliness was varied by using normal melts, dirty melts (100% returns), and melts made of returns and ingots.
- Data Collection Methods:
- Porosity levels were determined using a real-time X-ray radiographic inspection method.
- Inclusion content in the melt was measured using LiMCA II (liquid metal cleanliness analyser) for particles greater than 20 µm.
- PODFA (porous disc filtration apparatus) was used to collect inclusions for type identification.
- Machine operating parameters (gate velocity, fill time, cycle time, die surface temperature) were monitored in large-scale consecutive trials.
- Analysis Methods:
- Statistical analysis using logistic regression to determine the relationship between inclusion level and reject rate.
- Microscopic examination (optical microscopy, SEM, TEM) of inclusions collected by PODFA to identify their types.
- Porosity index (volume of porosity) was estimated from microscopic X-ray examinations.
- X-ray index (averaged X-ray grades) was calculated to assess overall porosity.
- Research Subjects and Scope:
- Automotive aluminium high pressure die castings, specifically a 'TA Transmission Case' casting (ADC12 alloy).
- Experiments were conducted at a 1250 t locking-force UBE high pressure die casting machine at NCAP.
- Melt cleanliness was the primary variable, while other parameters were kept consistent with normal production conditions.
5. Key Research Findings:
- Core Research Findings:
- The probability of rejection due to excessive porosity increased as the number of inclusions in the melt increased.
- A statistically significant correlation was found between inclusion level and reject rate (p < 0.05).
- The relationship between inclusion level and reject rate was fitted to a logistic equation.
- Inclusions in the melt were identified as mainly amorphous oxides, oxide films, and sludge particles.
- Castings made from dirty melt showed increased porosity levels at most locations compared to normal castings.
- X-ray indices increased when dirty experimental melt was used.
- Rejected castings were not directly associated with machine operating parameter deviations.
- Statistical/Qualitative Analysis Results:
- Logistic regression analysis showed a statistically significant relationship between inclusion content (x) and the probability of rejection (p(x)), fitted by the equation: p(x) = ey(x) / (1 + ey(x)), where y(x) = α + βx.
- For combined data, the fitted equation was y(x) = -4.08 + 0.0617x.
- For small-scale batch experiments: y(x) = -2.98 + 0.0500x.
- For large-scale consecutive experiments: y(x) = -5.02 + 0.0818x.
- 95% confidence intervals for the fitted equations were provided (Figures 3-5).
- Data Interpretation:
- Increased inclusion content in the molten metal increases the likelihood of porosity defects leading to casting rejection.
- Melt cleanliness is a critical factor influencing the quality of high pressure die castings in terms of porosity.
- The statistical relationship suggests a probabilistic effect of inclusions on porosity, likely due to the random distribution of inclusions and the complex nature of their interaction with porosity formation.
- Figure Name List:
- Fig. 1. A TA Transmission Case casting.
- Fig. 2. An X-ray radiograph showing the porosity in a specific location of a casting.
- Fig. 3. Reject rate vs. number of inclusions in the melts. Data obtained from the small-scale batch experiments.
- Fig. 4. Reject rate vs. number of inclusions in the melt. Data obtained from the large-scale consecutive and batch experiments. The sizes of the circles indicate the number of castings made for the corresponding data points.
- Fig. 5. Reject rate vs. number of inclusions in the melt. Combined data from the consecutive and batch experiments. The size of the circles indicates the number of castings made for the corresponding data points.
- Fig. 6. Schematic drawings of the TA Transmission Case that show the zones where X-ray examinations were performed. There are 10 positions in zones A and D, three in B and five in C, respectively.
- Fig. 7. Porosity index (mm³, averaged from three castings) of: (a) normal castings; (b) castings made from a dirty melt, at locations where porosity must be controlled according to prescribed standards ('zone' and 'position' denote specific locations in the castings).
- Fig. 8. The difference in porosity index between normal castings and castings made from a dirty melt.
- Fig. 9. X-ray indices of three experimental and six normal castings.
- Fig. 10. Cycle time of: (a) all castings; (b) rejected castings made in the consecutive large-scale experiments. The prolonged cycle times are associated with minor stops.
- Fig. 11. Average gate velocities of: (a) all castings; (b) rejected castings made in the consecutive large-scale experiments.
- Fig. 12. Fill time of: (a) all castings; (b) rejected castings made in the consecutive large-scale experiments.
- Fig. 13. Inclusions found in a filter cake formed from filtering a dirty melt (~80,000 particles greater than 20 µm/kg of molten metal) with PoDFA. Top: optical image; bottom: backscattered electron image (the bright phase is a sludge particle, the black particles are amorphous oxides).
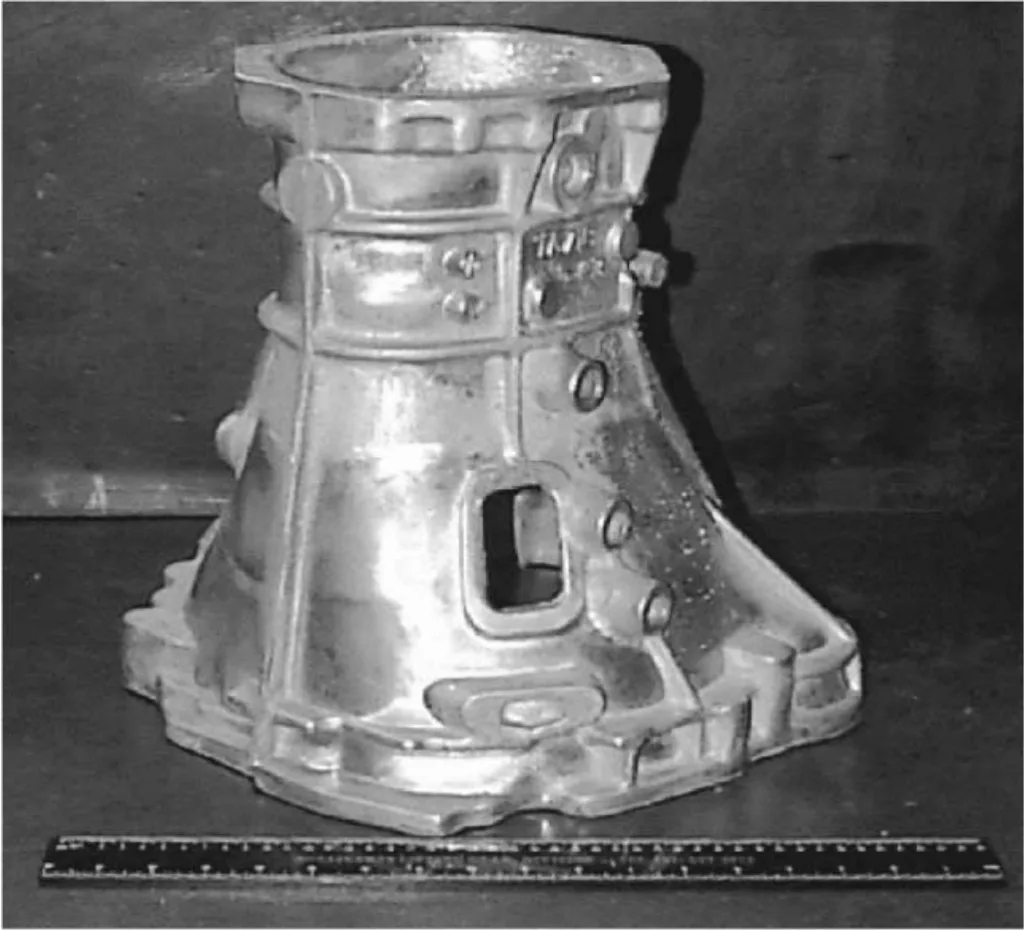
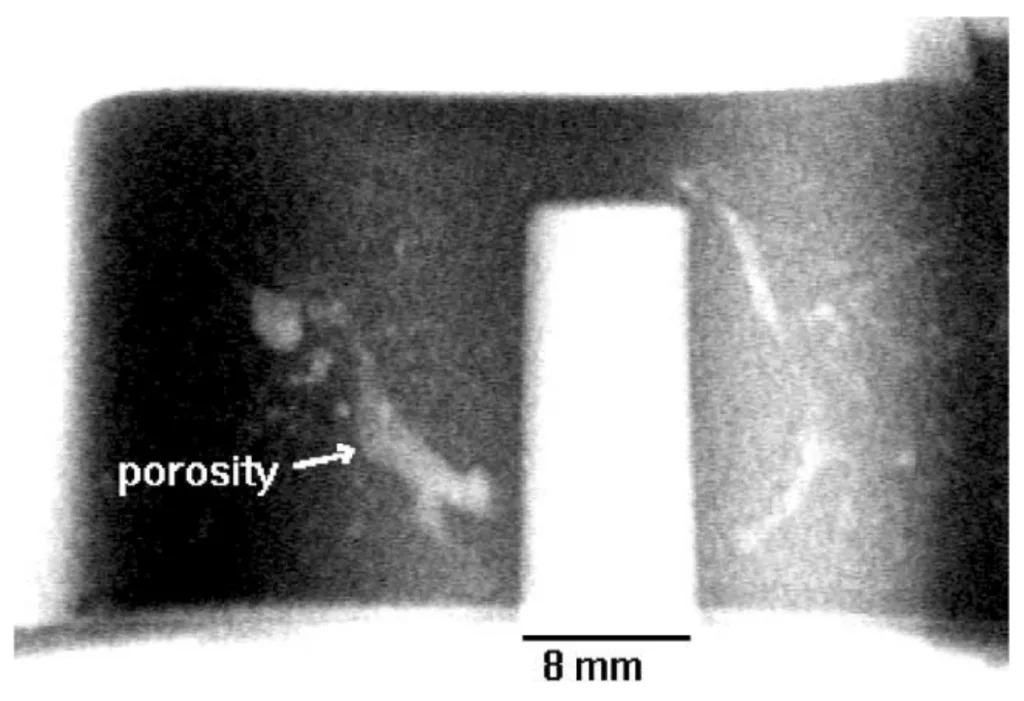
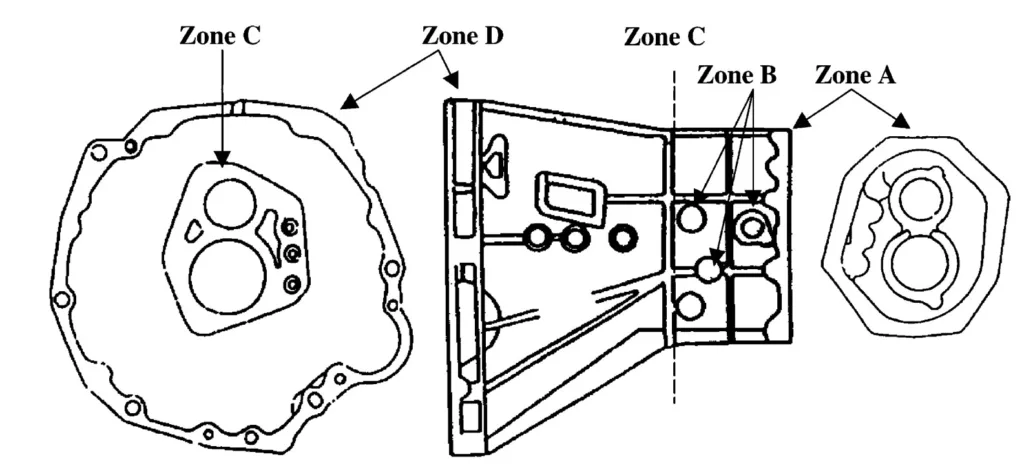
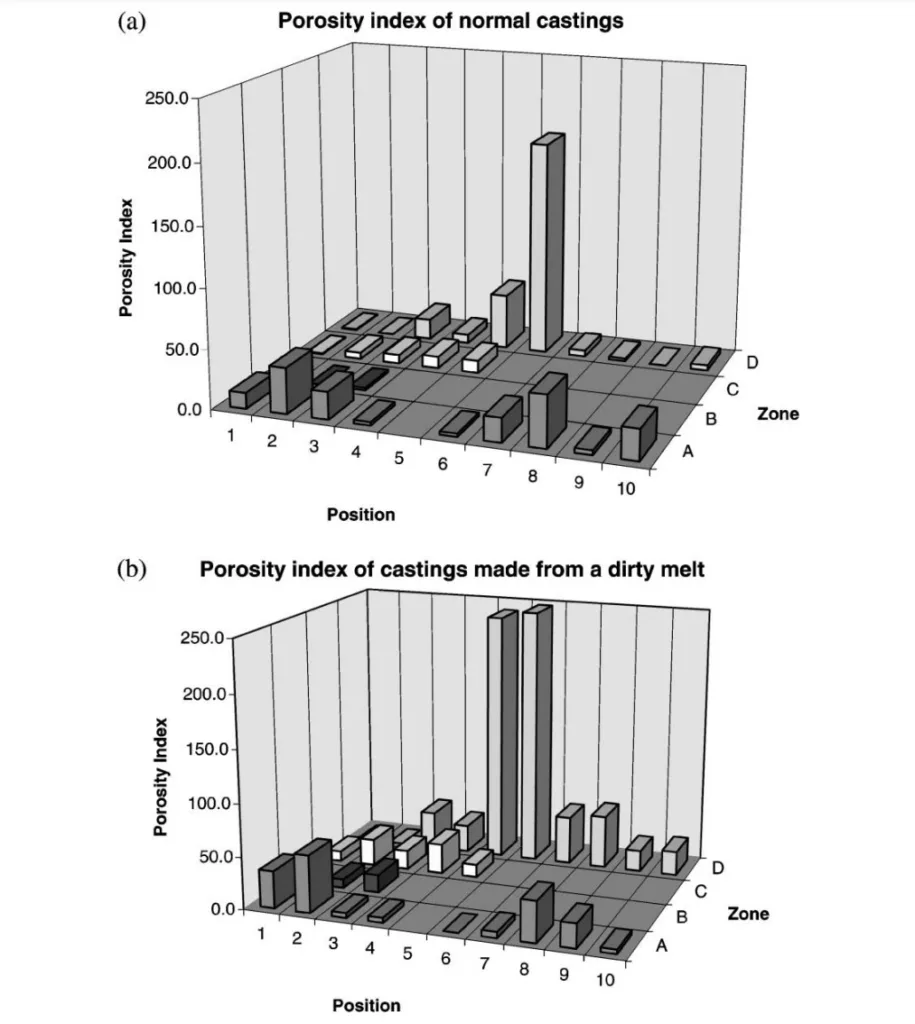
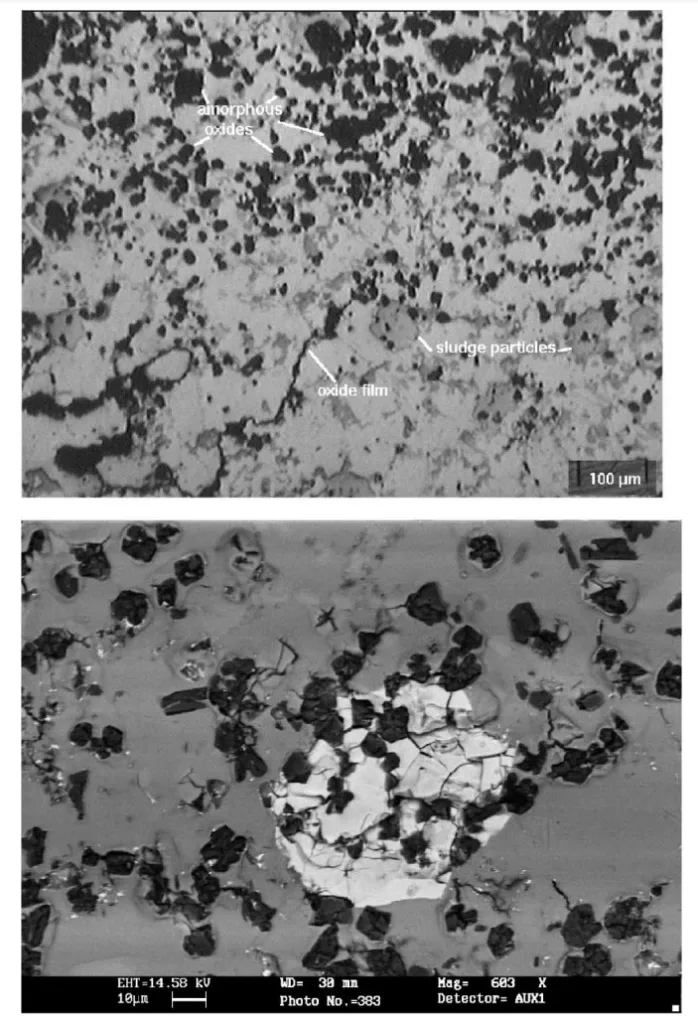
6. Conclusion and Discussion:
- Summary of Key Findings:
- This study experimentally confirmed that melt cleanliness, specifically the inclusion content, significantly affects porosity formation and the reject rate of automotive aluminium high pressure die castings.
- Increased inclusion levels in the melt lead to a higher probability of casting rejection due to excessive porosity.
- The inclusions were identified as primarily amorphous oxides, oxide films, and sludge particles.
- Statistical analysis established a logistic relationship between inclusion content and reject rate.
- Academic Significance of Research:
- Provides quantitative experimental evidence for the link between melt cleanliness and porosity in high pressure die castings under industrial conditions.
- Offers a statistical model to predict the probability of rejection based on inclusion levels.
- Contributes to a better understanding of the mechanisms by which melt cleanliness influences porosity formation in this specific casting process.
- Practical Implications:
- Emphasizes the importance of controlling melt cleanliness in high pressure die casting to minimize porosity defects and reduce reject rates.
- Suggests that monitoring and reducing inclusion levels in the molten metal can improve the quality and productivity of automotive component manufacturing.
- Provides a basis for developing melt treatment strategies to mitigate porosity outbreaks and ensure consistent casting quality.
- Limitations of Research:
- The study focused on a specific casting geometry (TA Transmission Case) and experimental conditions at NCAP.
- Generalization of the results to other casting geometries or different operating parameters should be approached with caution.
- The logistic equation represents an empirical relationship and may not fully capture the complex theoretical relationship between inclusion content and porosity.
- The study primarily considered the total number of inclusions greater than 20 µm as an independent variable, while other attributes of inclusions (type, shape, spatial distribution) and dissolved hydrogen were not fully investigated.
7. Future Follow-up Research:
- Directions for Follow-up Research:
- Further investigation into the specific mechanisms by which different types of inclusions (amorphous oxides, oxide films, sludge particles) contribute to porosity formation.
- Exploring the combined effects of inclusion content and dissolved hydrogen on porosity in high pressure die castings.
- Applying the findings to other casting geometries and alloys to assess the generalizability of the results.
- Developing and evaluating industrial-scale melt treatment methods to effectively reduce inclusion levels and improve melt cleanliness.
- Areas Requiring Further Exploration:
- Quantitative analysis of the spatial distribution of inclusions in castings and its correlation with porosity distribution.
- Investigating the influence of inclusion characteristics (wetting behavior, shape) on pore nucleation and growth.
- Modeling the fluid dynamics and solidification processes in high pressure die casting considering the presence and characteristics of inclusions.
8. References:
- [1] K. Hooper, Private communications, 1997.
- [2] D.E. Groteke, Influence of SNIF treatment on characteristics of aluminum foundry alloys, AFS Trans. 93 (1985) 953–960.
- [3] K.J. Brondyke, P.D. Hess, Interpretation of vacuum gas test results for aluminum alloys, Trans. TMS-AIME 230 (1964) 1542-1546.
- [4] E.L. Rooy, E.F. Fischer, Control of aluminum casting quality by vacuum solidification tests, AFS Trans. 76 (1968) 237-240.
- [5] D.E. Groteke, Testing for molten metal cleanliness, Die Casting Engr. (September/October 1996) 18–26.
- [6] P.N. Anyalebechi, Analysis and thermodynamic prediction of hydrogen solution in solid and liquid multicomponent aluminum alloys, Light Met. (1998) 827-842.
- [7] C.E. Ransley, H. Neufeld, The solubility of hydrogen in liquid and solid aluminum, J. Inst. Met. 74 (1948) 599-620.
- [8] C. Tian, J. Law, M. Murray, Unpublished work, 1998.
- [9] Properties of cast aluminum alloys, in: ASM Handbook Committee (Eds.), Metals Handbook, Vol. 2, 9th Edition: Properties and Selection: Nonferrous Alloys and Pure Metals, American Society for Metals, Metals Park, OH, 1979, pp. 152-179.
- [10] R.I.L. Guthrie, D.A. Doutre, On line measurements of inclusion in liquid metals, in: Proceedings of the International Seminar on Refining and Alloying of Liquid Aluminum and Ferro-alloys, Trondheim, Norway, 1985, pp. 145-163.
- [11] D. Doutre, B. Gariépy, J.P. Martin, G. Dubé, Aluminium cleanliness monitoring: methods and applications in process development and quality control, Light Met. (1985) 1179–1195.
- [12] P. McCullagh, J.A. Nelder, Generalized Linear Models, Chapman & Hall, London, 1983.
- [13] P. Miller, CSIRO Internal Reports, CSIRO Manufacturing Science and Technology, Clayton, Vic., 1997.
9. Copyright:
- This material is based on the paper by C. Tian, J. Law, J. van der Touw, M. Murray, J.-Y. Yao, D. Graham, D. St. John: Effect of melt cleanliness on the formation of porosity defects in automotive aluminium high pressure die castings.
- Paper Source: https://doi.org/10.1016/S0924-0136(01)01229-8
This material is a summary based on the above paper, and unauthorized use for commercial purposes is prohibited.
Copyright © 2025 CASTMAN. All rights reserved.