This article introduces the paper "Effect of Addition of Grain Refiner and Modifier on Microstructural and Mechanical Properties of Squeeze Cast A356 Alloy" presented at the "Transactions of the Indian Institute of Metals"
1. Overview:
- Title: Effect of Addition of Grain Refiner and Modifier on Microstructural and Mechanical Properties of Squeeze Cast A356 Alloy
- Authors: Reeturaj Tamuly, Amit Behl, Hemant Borkar
- Publication Year: 2022
- Publishing Journal/Academic Society: Transactions of the Indian Institute of Metals
- Keywords: Squeeze casting, Grain refiner, Modifier, A356 alloy
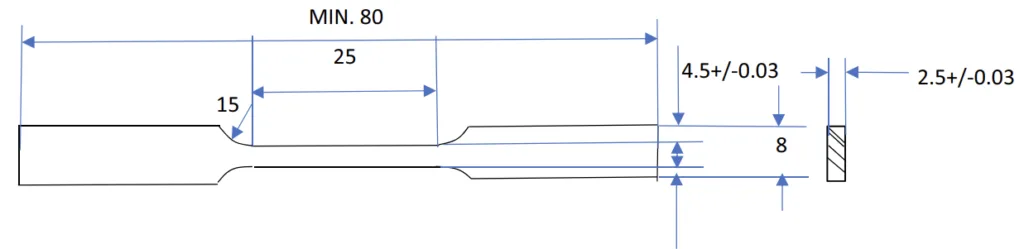
2. Research Background:
In industries such as automobile, aerospace, and defense, Aluminum-Silicon (Al-Si) alloys, particularly grade A356, are extensively utilized due to their low density combined with advantageous properties including high strength, excellent castability, superior thermal conductivity, and good corrosion and wear resistance. Prior research has demonstrated that the mechanical properties of gravity die-cast Al-Si alloys can be enhanced through the incorporation of grain refiners like boron and titanium, and modifiers such as strontium. Squeeze casting, a pressure-assisted casting technique, is also known to improve the mechanical properties of aluminum alloys.
However, existing research presents limitations in the comprehensive study of squeeze casting applied to cast Al-alloys that are both grain refined and modified using master alloys. This necessitates further investigation into the effects of these combined processes. Therefore, this research is crucial to explore the influence of squeeze casting in conjunction with grain refinement and modification on Al-Si alloys.
3. Research Purpose and Research Questions:
Research Purpose:
This study aims to investigate the effect of adding Aluminum-Titanium-Boron (Al-Ti-B) alloys as a grain refiner, and the combined effect of Al-Ti-B with varying levels of Strontium (Sr) as a microstructural modifier, on the squeeze cast A356 Al-Si alloy. The research further analyzes the impact of T6 solution heat treatment on the microstructure and mechanical properties of these squeeze cast alloys.
Key Research Questions:
- How does the addition of Al-Ti-B grain refiner influence the microstructure and mechanical properties of squeeze cast A356 alloy?
- What is the combined effect of Al-Ti-B grain refiner and Sr modifier on the microstructure and mechanical properties of squeeze cast A356 alloy?
- How does T6 solution heat treatment affect the microstructure and mechanical properties of squeeze cast A356 alloy with and without grain refiner and modifier additions?
Research Hypotheses:
The central hypothesis is that the addition of grain refiner and modifier will lead to an improvement in the mechanical properties of the squeeze cast A356 alloy. Furthermore, it is hypothesized that the application of heat treatment will further augment these enhanced mechanical properties.
4. Research Methodology
Research Design:
The research employed an experimental design to systematically evaluate the effects of grain refiner and modifier additions, as well as heat treatment, on the microstructure and mechanical properties of squeeze cast A356 alloy.
Data Collection Method:
The study utilized a combination of advanced microscopy and mechanical testing techniques for data collection:
- Optical Microscopy: Used to analyze the general microstructure and grain size.
- Scanning Electron Microscopy (SEM): Employed for high-resolution imaging of microstructural features, including the morphology of Si particles and intermetallic phases.
- Energy Dispersive Spectroscopy (EDS): Integrated with SEM to determine the elemental composition of microstructural constituents.
- Tensile Testing: Conducted using a universal testing machine to quantify mechanical properties such as Yield Strength, Tensile Strength, and percentage Elongation.
Analysis Method:
The collected data was analyzed using both qualitative and quantitative methods:
- Microstructural Analysis: Qualitative assessment of grain morphology, Secondary Dendrite Arm Spacing (SDAS), and Si particle characteristics from microscopy images. Quantitative measurement of SDAS was also performed.
- Mechanical Property Analysis: Statistical analysis of tensile test data to determine average values and trends in Yield Strength, Tensile Strength, and Elongation.
Research Subjects and Scope:
The research focused on A356 aluminum alloy processed via squeeze casting. The scope included:
- Alloy Compositions: Baseline A356 alloy, A356 with Al-5Ti-1B grain refiner (750 ppm Ti, 150 ppm B), and A356 with Al-5Ti-1B grain refiner combined with Al-10Sr modifier at two levels (200 ppm Sr and 300 ppm Sr).
- Processing Conditions: Squeeze casting process with controlled parameters and T6 heat treatment applied to selected samples.
- Characterization: Comprehensive microstructural and mechanical property evaluation of all alloy compositions in both as-cast and heat-treated conditions.
5. Main Research Results:
Key Research Results:
- Squeeze Casting Effect: Squeeze casting significantly reduced the Secondary Dendrite Arm Spacing (SDAS) of the A356 alloy by 50%, from 45(± 2) μm to 26(± 2) µm.
- Grain Refinement Effect: The addition of Al-Ti-B grain refiner altered the α-Al phase morphology from dendritic to globular and further decreased the SDAS to 20(± 3) µm. However, the reduction in SDAS due to grain refiner was limited (6(± 1) µm), possibly due to the fading effect of the grain refiner.
- Combined Grain Refinement and Modification Effect: The combined addition of Al-Ti-B grain refiner and Sr modifier induced changes in the morphology of Si particles and Fe-based intermetallics. The average SDAS remained around 20(± 3) µm for both 200 ppm and 300 ppm Sr additions, indicating Sr's limited influence on SDAS. However, Sr was effective in modifying the morphology of Si particles.
- Heat Treatment Effect: T6 heat treatment led to spheroidization and coarsening of eutectic Si, and precipitation of hardening phases (Mg₂Si and Fe-based intermetallics).
- Mechanical Properties - Non-Heat-Treated: Addition of grain refiner alone resulted in a decrease in tensile strength (from 205 MPa to 172.667 MPa), yield strength (from 110.6 MPa to 109.3 MPa), and % elongation (from 10% to 6.33%), potentially due to the fading effect of the grain refiner. The combined addition of grain refiner and modifier improved yield strength compared to grain refiner alone.
- Mechanical Properties - Heat-Treated: Heat treatment improved both tensile strength and yield strength across all alloy compositions but reduced % elongation. The highest yield strength of 193 MPa was achieved for the heat-treated A356 + Al-5Ti-1B + Al-10Sr (300 ppm Sr) alloy.
Statistical/Qualitative Analysis Results:
- SDAS Reduction: Squeeze casting achieved a 50% reduction in SDAS. Grain refiner further reduced SDAS by a smaller margin.
- Tensile Properties (Non-Heat-Treated): Base A356 alloy exhibited a tensile strength of 205 MPa, yield strength of 110.6 MPa, and 10% elongation. With grain refiner, these values decreased. With combined grain refiner and modifier, yield strength recovered, and elongation improved with 300 ppm Sr.
- Tensile Properties (Heat-Treated): Heat-treated base A356 alloy showed a tensile strength of 235 MPa, yield strength of 184 MPa, and 8.16% elongation. Heat-treated alloys with grain refiner and modifier showed varying tensile properties, with the highest yield strength achieved in the 300 ppm Sr modified alloy.
Data Interpretation:
The results indicate that squeeze casting is effective in refining the microstructure of A356 alloy. Grain refinement further enhances microstructural refinement but may lead to a reduction in tensile properties in the as-cast condition, possibly due to grain refiner fading. The addition of Sr modifier partially modifies the Si particle morphology and, in combination with grain refiner, can improve yield strength. T6 heat treatment is crucial for maximizing strength in all alloy compositions, although it reduces ductility.
Figure Name List:
- Fig. 1 Tensile test specimen (all dimensions are in mm)
- Fig. 2 Optical images of a as-received A356 alloy b squeeze cast A356 alloy
- Fig. 3 Optical images of grain refined alloy samples using Al-5Ti-1B at only one magnification (750 ppm Ti,150 ppm B)
- Fig. 4 Optical images of grain refined and modified alloy samples a using Al-5Ti-1B and Al-10Sr (750 ppm Ti, 150 ppm B and 200 ppm Sr; b using Al-5Ti-1B and Al-10Sr (750 ppm Ti,150 ppm B and 300 ppm Sr)
- Fig. 5 Optical images of heat-treated samples a using Al-5Ti-1B (750 ppm Ti,150 ppm B); b using Al-5Ti-1B and Al-10Sr (750 ppm Ti,150 ppm B and 200 ppm Sr); c using Al-5Ti-1B and Al-10Sr (750 ppm Ti,150 ppm B and 300 ppm Sr)
- Fig. 6 SEM images of heat-treated samples showing spheroidized Si particles a at lower magnification b at higher magnification
- Fig. 7 EDS analysis of (mention alloy composition) showing the presence of Mg₂Si particles and Fe-based intermetallics after heat treatment process
- Fig. 8 SEM images of grain-refined alloy samples using Al-5Ti-1B a α-Al and Si eutectic phase b unmodified Si particles in eutectic zone
- Fig. 9 SEM images of alloy samples a using Al-5Ti-1B showing Si particles b using Al-5Ti-1B and Al-10Sr showing partial modification of Si particles c using Al-5Ti-1B and Al-10Sr showing α-Al and Si eutectic phase at lower magnification d using Al-5Ti-1B and Al-10Sr showing partially modified Si particles in eutectic zone at lower magnification (750 ppm Ti,150 ppm B,300 ppm Sr)
- Fig. 10 BSE image of grain refined and modified squeeze cast A356 alloy samples a A356 + Al-5Ti-1B(750 ppm Ti and 150 ppm B) + Al-10Sr (200 ppm Sr) b A356 + Al-5Ti-1B(750 ppm Ti and 150 ppm B) + Al-10Sr (300 ppm Sr) c Spectrum 10 indicating the brighter region d EDX analysis showing the presence of Fe intermetallic
- Fig. 11 Microstructural images of A356 alloy samples a Optical image of unmodified A356alloy showing presence of Fe-based β-phase needles b Optical image of Sr-modified alloy showing Fe-based α-phase intermetallic with Chinese script morphology
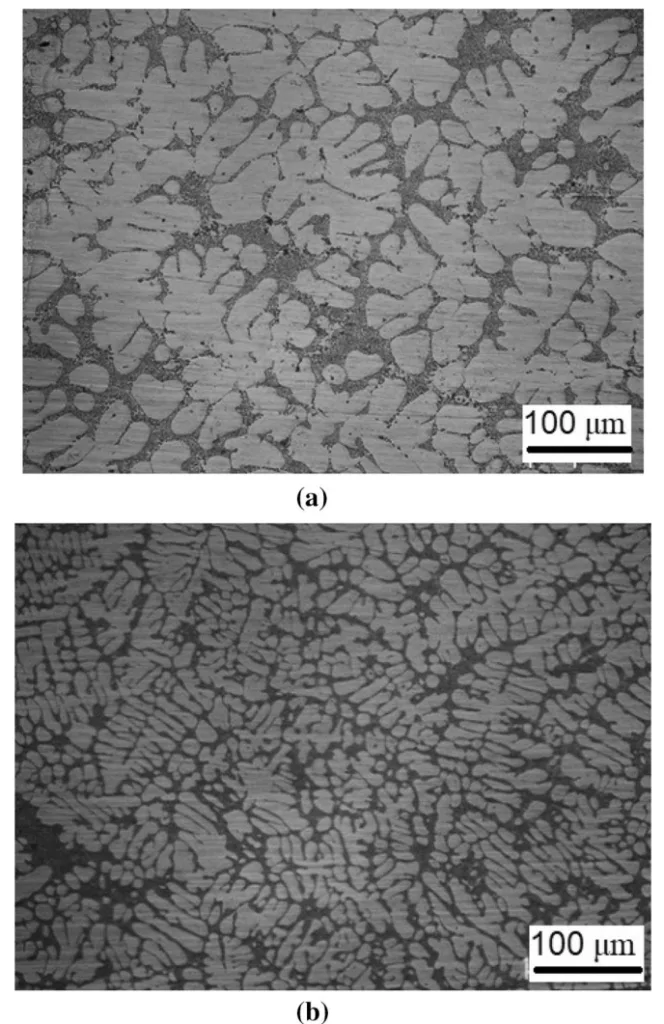
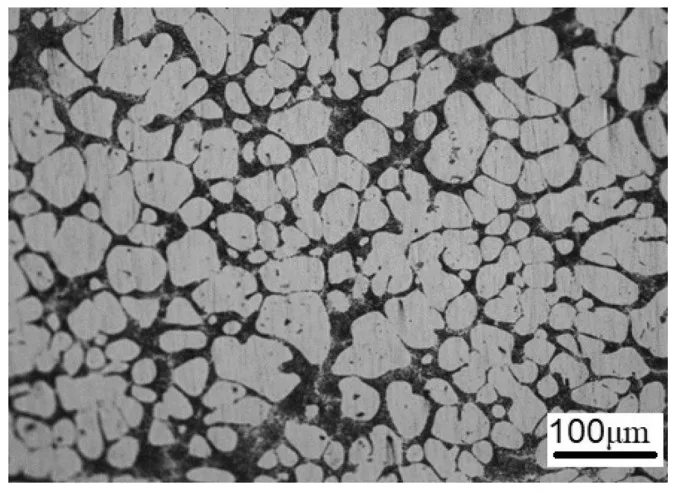
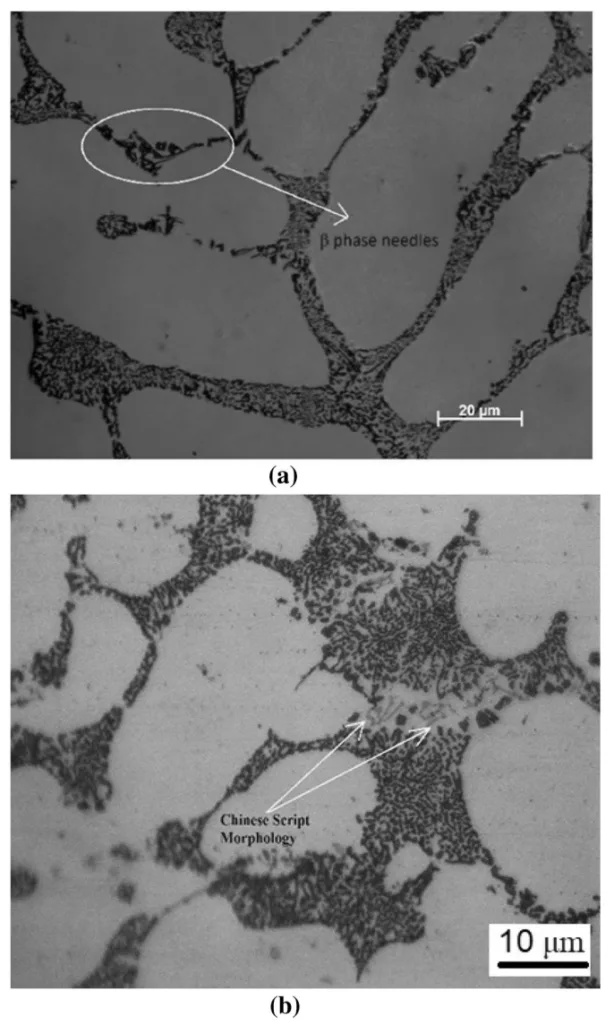
6. Conclusion and Discussion:
Summary of Main Results:
This research conclusively demonstrates the significant impact of squeeze casting, grain refinement using Al-Ti-B, modification with Sr, and T6 heat treatment on the microstructure and mechanical properties of A356 aluminum alloy. Squeeze casting effectively refines the microstructure by reducing SDAS. Grain refiner addition further refines the α-Al phase, while Sr modification alters Si particle morphology. T6 heat treatment induces spheroidization of eutectic Si and precipitation hardening, leading to enhanced strength.
Academic Significance of the Research:
This study contributes valuable insights into the synergistic effects of squeeze casting, grain refinement, and modification on Al-Si alloys. It provides a detailed microstructural and mechanical property characterization, enhancing the understanding of phase transformations and strengthening mechanisms in squeeze cast, grain refined, and modified A356 alloy. The findings are significant for materials science and engineering, particularly in the context of aluminum alloy processing and optimization.
Practical Implications:
The practical implications of this research are substantial for the die casting industry. The study highlights the potential of combining squeeze casting with grain refinement and modification to produce high-performance A356 alloy components. The optimized processing parameters and alloy compositions identified can be directly applied to improve the mechanical properties of cast components for automotive, aerospace, and other engineering applications, particularly where high strength and lightweight are critical requirements. The research also underscores the importance of T6 heat treatment as a crucial post-casting process for achieving peak mechanical properties.
Limitations of the Research:
The study acknowledges certain limitations, including the potential fading effect of the grain refiner, which may have limited the extent of microstructural refinement and property enhancement in some conditions. The partial modification observed with Sr suggests a need for further optimization of Sr content. Additionally, the relatively high quench temperature used in the T6 treatment may have impacted ductility, indicating a need for further investigation into quench sensitivity and optimization of cooling rates.
7. Future Follow-up Research:
Directions for Follow-up Research:
Future research should focus on addressing the identified limitations and further optimizing the alloy composition and processing parameters. Key directions include:
- Optimizing Sr Content: Investigating the optimum Sr content to achieve full modification of Si particles and maximize mechanical properties without adverse effects.
- Boron Content Optimization: Further research into the role and optimal content of Boron in Al-Ti-B grain refiners to mitigate fading effects and enhance grain refinement efficiency.
- Quench Temperature Optimization: Exploring the effect of lower quench temperatures during T6 heat treatment to improve ductility while maintaining high strength.
- Sr:B Ratio Effect: Detailed study of the Sr:B ratio to determine the optimal balance for effective Sr modification and grain refinement in squeeze cast A356 alloys.
Areas Requiring Further Exploration:
- Fading Mechanism: In-depth investigation into the fading mechanism of Al-Ti-B grain refiners in squeeze casting conditions to develop strategies for mitigating this effect.
- Heat Treatment Parameter Optimization: Systematic optimization of T6 heat treatment parameters, including solutionizing temperature and time, quenching rate and media, and aging temperature and time, to achieve the best combination of strength and ductility.
- Effect of Other Modifiers: Exploring the use of alternative or combined modifiers in conjunction with grain refiners to achieve superior microstructural control and mechanical properties in squeeze cast A356 alloys.
8. References:
- Davies J R, Associates, Aluminium and Aluminium Alloys. ASM International, ASM World Headquarter, Material Park, Novelty, OH (1993)
- Jakob O, Svensson I L, Pascal L, and Dimitri D, Characterisation and investigation of local variations in mechanical behaviour in cast aluminium using gradient solidification, Digital Image Correlation and finite element simulation. Mater Design (1980-2015) 56 (2014): 755
- Kumar, P., and J. L. Gaindhar. "DAS, Solidification Time and Mechanical Properties of Al-11% Si Alloy V-Processed Castings (97-09)." Transactions of the American Foundrymen's Society 105 (1997): 635-638.
- Goulart, Pedro R., José E. Spinelli, Wislei R. Osório, and Amauri Garcia. "Mechanical properties as a function of microstructure and solidification thermal variables of Al-Si castings." Materials Science and Engineering: A 421, no. 1-2 (2006): 245-253.
- Seifeddine, Salem, Sten Johansson, and Ingvar L. Svensson. "The influence of cooling rate and manganese content on the β-Al5FeSi phase formation and mechanical properties of Al-Si-based alloys." Materials Science and Engineering: A 490, no. 1-2 (2008): 385-390.
- Ceschini, Lorella, Iuri Boromei, Alessandro Morri, Salem Seifeddine, and Ingvar L. Svensson. "Microstructure, tensile and fatigue properties of the Al-10% Si-2% Cu alloy with different Fe and Mn content cast under controlled conditions." Journal of Materials Processing Technology 209, no. 15-16 (2009): 5669-5679.
- Caceres, C. H., C. J. Davidson, J. R. Griffiths, and Q. G. Wang. "The effect of Mg on the microstructure and mechanical behavior of Al-Si-Mg casting alloys." Metallurgical and materials transactions A 30, no. 10 (1999): 2611-2618.
- Stadler, F., H. Antrekowitsch, W. Fragner, H. Kaufmann, E. R. Pinatel, and Peter J. Uggowitzer. "The effect of main alloying elements on the physical properties of Al-Si foundry alloys." Materials Science and Engineering: A 560 (2013): 481-491.
- Sritharan, T., and H. Li. "Influence of titanium to boron ratio on the ability to grain refine aluminium-silicon alloys." Journal of Materials Processing Technology 63, no. 1-3 (1997): 585-589.
- Jones, G. Pcarson, and J. Pearson. "Factors affecting the grain-refinement of aluminum using titanium and boron additives." Metallurgical Transactions B 7, no. 2 (1976): 223-234.
- Mayes, C. D., D. G. McCartney, and G. J. Tatlock. "Influence of microstructure on grain refining performance of Al-Ti-B master alloys." Materials science and technology 9, no. 2 (1993): 97-103.
- Mohanty, P. S., and J. E. Gruzleski. "Grain refinement mechanisms of hypoeutectic Al Si alloys." Acta materialia 44, no. 9 (1996): 3749-3760.
- Spittle, J. A. "Grain refinement in shape casting of aluminium alloys." International Journal of Cast Metals Research 19, no. 4 (2006): 210-222.
- Schumacher, P. "Nucleation Mechanisms during Grain Refinement of Al-Si-Alloys." Giesserei-Rundschau 50 (2003): 228-230.
- Mohanty, P. S., F. H. Samuel, and J. E. Gruzleski. "Studies on addition of inclusions to molten aluminum using a novel technique." Metallurgical and Materials Transactions B 26, no. 1 (1995): 103-109.
- Nafisi, Shahrooz, and Reza Ghomashchi. "Boron-based refiners: implications in conventional casting of Al-Si alloys." Materials Science and Engineering: A 452 (2007): 445-453.
- Lu, L., and A. K. Dahle. "Effects of combined additions of Sr and AlTiB grain refiners in hypoeutectic Al-Si foundry alloys." Materials Science and Engineering: A 435 (2006): 288-296.
- Limmaneevichitr, C., and W. Eidhed. "Fading mechanism of grain refinement of aluminum-silicon alloy with Al-Ti-B grain refiners." Materials Science and Engineering: A 349, no. 1-2 (2003): 197-206
- Ghomashchi, Reza. "The evolution of AlTiSi intermetallic phases in Ti-added A356 Al-Si alloy." Journal of Alloys and Compounds 537 (2012): 255-260.
- Lee, Choongdo. "Effect of Ti-B addition on the variation of microporosity and tensile properties of A356 aluminium alloys." Materials Science and Engineering: A 668 (2016): 152-159.
- Sokolowski, J. H., C. A. Kierkus, B. Brosnan, and W. J. Evans. "Formation of Insoluble Ti (Al, Si) 3 Crystals in 356 Alloy Castings and Their Sedimentation in Foundry Equipment: Causes, Effects and Solutions (00-21)." Transactions of the American Foundrymen's Society 108 (2000): 491-496
- Birol, Y. "Grain refinement of pure aluminium and Al-7Si with Al-3B master alloy." Materials Science and Technology 28, no. 3 (2012): 363-367.
- Couture, A. A. F. S. "Iron in aluminum casting alloys-a literature survey." International cast metals journal 6, no. 4 (1981): 9-17.
- Kori S. Auradi A V, Murty B S, and Chakraborty M. Poisoning and fading mechanism of grain refinement in Al-7Si alloy. In: Proceedings of 3rd international conference on advanced materials processing (ICAMP-3), 387-393. Processing (ICAMP-3), Melbourne, Australia, 2004.
- Haro-Rodríguez, Sergio, Rafael E. Goytia-Reyes, Dheerendra Kumar Dwivedi, Víctor H. Baltazar-Hernández, Horacio Flores-Zúñiga, and María J. Pérez-López. "On influence of Ti and Sr on microstructure, mechanical properties and quality index of cast eutectic Al-Si-Mg alloy." Materials & Design 32, no. 4 (2011): 1865-1871.
- Crosley, Phillip Bernard, and L. F. Mondolfo. "The modification of aluminum-silicon alloys." Mod Cast 49, no. 3 (1966): 99-100.
- Lu, Shu-Zu, and A. Hellawell. "The mechanism of silicon modification in aluminum-silicon alloys: Impurity induced twinning." Metallurgical Transactions A 18, no. 10 (1987): 1721-1733.
- Qiu, D., J. A. Taylor, M. X. Zhang, and P. M. Kelly. "A mechanism for the poisoning effect of silicon on the grain refinement of Al-Si alloys." Acta Materialia 55, no. 4 (2007): 1447-1456.
- Liao, Hengcheng, and Guoxiong Sun. "Mutual poisoning effect between Sr and B in Al-Si casting alloys." Scripta materialia 48, no. 8 (2003): 1035-1039.
- Timpel, M., N. Wanderka, R. Schlesiger, T. Yamamoto, N. Lazarev, D. Isheim, G. Schmitz, S. Matsumura, and J. Banhart. "The role of strontium in modifying aluminium-silicon alloys." Acta Materialia 60, no. 9 (2012): 3920-3928.
- Nogita, Kazuhiro, Stuart David McDonald, and Arne Kristian Dahle. "Effects of boron-strontium interactions on eutectic modification in Al-10 mass% Si alloys." Materials Transactions 44, no. 4 (2003): 692-695.
- Chatterjee S, Some observations on the effect of pressure on the solidification of Al-Si eutectic alloys. (1973).
- Chatterjee S, Effects of pressure on the solidification of some commercial aluminium-base casting alloys. (1972).
- Chadwick, G. A., and Tai Man Yue. "Principles and applications of squeeze casting." Metals and materials Bury St Edmunds 5, no. 1 (1989): 6-12.
- Dong, J. X., P. A. Karnezis, G. Durrant, and B. Cantor. "The effect of Sr and Fe additions on the microstructure and mechanical properties of a direct squeeze cast Al-7Si-0.3 Mg alloy." Metallurgical and materials transactions A 30 (1999): 1341.
- Okada, S., N. Fujii, A. Goto, S. Morimoto, and T. Yasuda. "Development of a full automatic squeeze casting machine." AFS Transactions 82 (1982): 135.
- Shivkumar, S., S. Ricci, B. Steenhoff, D. Apelian, and G. Sigworth. "An experimental study to optimize the heat treatment of A356 alloy." AFS Transactions 97 (1989): 791.
- Guodong, Wan Lil Luo Jirong1 Lan, and Qionghua L, Mechanical properties and microstructures of squeezed and cast hypereutectic A390 alloy [J]. J Huazhong Univ Sci Technol (Nat Sci Edition) 8 (2008).
- Ma, Z., E. Samuel, A. M. A. Mohamed, A. M. Samuel, F. H. Samuel, and H. W. Doty. "Influence of aging treatments and alloying additives on the hardness of Al-11Si-2.5 Cu-Mg alloys." Materials & Design 31 (2010): 3791.
- Ma Z, Samuel E, Mohamed A MA, Samuel A M, Samuel FH, and Doty H W. Parameters controlling the microstructure of Al-11Si-2.5 Cu-Mg alloys. Mater Design 31(2010): 3791.
- Abou El-khair, M. T. "Microstructure characterization and tensile properties of squeeze-cast AlSiMg alloys." Materials Letters 59, no. 8-9 (2005): 894-900
- Mulazimoglu M H, Electrical conductivity studies of cast Al-Si and Al-Si-Mg alloys Ph.D. Thesis, 1988, McGill University, Montreal, PQ, Canada.
- H.J Li, S. Shivkumar, X.J. Luo and D. Apelian: "Influence of Modification on The Solution Heat Treatment Response of Cast Al-Si-Mg Alloys", Cast Metals, Vol. 1, 1989, pp. 227-234
- I. Kovacs, J. Lendvai and E. Nagy: "Mechanism of Clustering in Supersaturated Solid Solutions AI-Mg2Si Alloys. "Acta Metallurgica, Vol.20, 1972, pp. 975-983.
- Gupta A K and Lloyd D J, In: Aluminum alloys, their physical and mechanical properties (ICAA3), L. Arnberg, O. Lohne, E. Nes and N. Ryum, eds. The Norwegian Institute of Technology, Trondheim, 2 (1992), 21.
- Kashyap, K. T., and T. Chandrashekar. "Effects and mechanisms of grain refinement in aluminium alloys." Bulletin of Materials Science 24, no. 4 (2001): 345-353.
- Cooper P, Hardman A, Boot D, and Burhop E, Characterisation of a new generation of grain refiners for the foundry industry." In: LIGHT METALS-WARRENDALE-PROCEEDINGS-, 923-928. TMS, 2003.
- Lu L, and Arne K. Dahle, Effects of Sr and B interactions in hypoeutectic Al-Si foundry alloys. Light metals (2006): 807.
- Spittle J A, Grain refinement in shape casting of aluminium alloys (2006): 210.
- Wang, Tongmin, Hongwang Fu, Zongning Chen, Jun Xu, Jing Zhu, Fei Cao, and Tingju Li. "A novel fading-resistant Al-3Ti-3B grain refiner for Al-Si alloys." Journal of alloys and compounds 511, no. 1 (2012): 45-49.
- Gazanion F, Grant Chen X, and Dupuis C, Studies on the sedimentation and agglomeration behavior of Al-Ti-B and Al-Ti-C grain refiners." In Materials science forum, 396, p 45-52. Trans Tech Publications Ltd, 2002.
- Schneider W, Kearns M A, McGarry M J, and Whitehead A J, A comparison of the behaviour of AlTiB and AlTiC grain refiners. In: Essential readings in light metals, p 400-408. Springer, Cham, 2016.
- Talaat M M, Salah S, Ezz S, and El-Sayed M. El-Banna. GRAIN REFINEMENT OF A1-3 AND 5% Si ALLOYS.
- Zamkotowicz Z, Stuczynski T, Augustyn B, Lech-Grega M, and Wezyk W, Investigation of grain refinement fading in hypoeutectic aluminium-silicon alloys. In: LIGHT METALS-WARRENDALE-PROCEEDINGS-, p 807-816. TMS, 2004.
- Wang, Tongmin, Yuanping Zheng, Zongning Chen, Yufei Zhao, and Huijun Kang. "Effects of Sr on the microstructure and mechanical properties of in situ TiB2 reinforced A356 composite." Materials & Design 64 (2014): 185-193.
- Tan, Pan, Yi Yang, Yudong Sui, Qudong Wang, and Yehua Jiang. "The influence of Al-10Sr or/and Al-5Ti-1B on microstructure and mechanical properties of Al-12Si-4Cu-2Ni-0.8 Mg alloys." Journal of Alloys and Compounds 809 (2019): 151856.
- Samuel A M, Doty H W, Valtierra S, and Samuel F H, Effect of grain refining and Sr-modification interactions on the impact toughness of Al-Si-Mg cast alloys. Mater Design (1980-2015) 56 (2014) 264.
- Kori S A, Auradi V, Murty B S, Chakraborty M, Poisoning and fading mechanism of grain refinement in Al-7Si alloy. In: Proceedings of 3rd international conference on advanced materials processing (ICAMP-3), p 387-393. Processing (ICAMP-3), Melbourne, Australia, 2004.
- Mohanty, P. S., and J. E. Gruzleski. "Mechanism of grain refinement in aluminium." Acta Metallurgica et Materialia 43, no. 5 (1995): 2001-2012.
- Iqbal, N., N. H. Van Dijk, S. E. Offerman, M. P. Moret, L. Katgerman, and G. J. Kearley. "Real-time observation of grain nucleation and growth during solidification of aluminium alloys." Acta Materialia 53, no. 10 (2005): 2875-2880.
- Murty, B. S., S. A. Kori, and M. Chakraborty. "Grain refinement of aluminium and its alloys by heterogeneous nucleation and alloying." International Materials Reviews 47, no. 1 (2002): 3-29
- Greer A L, Quested T E, and Spalding JE, Modelling of grain refinement in directional solidification. In: LIGHT METALS-WARRENDALE-PROCEEDINGS-, p 687-694. TMS, 2002
- Emadi D, Whiting 1 V, Sahoo M, Sokolowski J H, Burke P, and Hart M. Optimal heat treatment of A356. 2 alloy. In LIGHT METALS-WARRENDALE-PROCEEDINGS-, p 983-990. TMS, 2003.
- Croucher T, and Butler D, Polymer quenching of aluminum castings. In 26th National SAMPE Symposium, p 527-535. 1981.
- Totten G E, and Mackenzie D S Aluminum quenching technology: a review. In: Materials science forum, 331, p 589-594. Trans Tech Publications Ltd, 2000.
- Sverdlin, A. V., G. E. Totten, and G. M. Vebster. "Polyalkyleneglycol base quenching media for heat treatment of aluminum alloys." Metallovedenie i Termicheskaya Obrabotka Metallov 6 (1996): 17-19.
- Senatorova O G, Sidelnikov V V, Mihailova I F, Fridlyander I N, Bedarev A S, Spector JI, Tihonova LA Low distortion quenching of aluminium alloys in polymer medium. In: Materials science forum, 396, p 1659-1664. Trans Tech Publications Ltd, 2002.
- Beitz, H. Non-combustible water-based quenchants in forging shops for automotive parts-latest development. In: 1 st international automotive heat treating conference, p 106-109. 1998.
- Zhang, D. L., and L. Zheng. "The quench sensitivity of cast Al-7 wt pct Si-0.4 wt pct Mg alloy." Metallurgical and Materials Transactions A 27, no. 12 (1996): 3983-3991.
- Mohamed AMA, and Samuel FH A review on the heat treatment of Al-Si-Cu/Mg casting alloys. Heat treatment-conventional and novel applications (2012): 55–72.
- Wahyuningtyas P, Syahrial A Z, Putra W N, and Utomo B W. Effect of T6 on mechanical properties of TiB and Sr modified ADC12/SiC composite produced by stir casting. In: E3S web of conferences, 130, 01023. EDP Sciences, 2019.
9. Copyright:
This material is Reeturaj Tamuly, Amit Behl, Hemant Borkar's paper: Based on "Effect of Addition of Grain Refiner and Modifier on Microstructural and Mechanical Properties of Squeeze Cast A356 Alloy".
Paper Source: https://doi.org/10.1007/s12666-022-02607-4
This material was summarized based on the above paper, and unauthorized use for commercial purposes is prohibited.
Copyright © 2025 CASTMAN. All rights reserved.